Фрезерование древесных плитных материалов и композитов на четырехсторонних станках
Выбор режущего инструмента
В 1920 году Армин Бернер из немецкой компании Gubisch установил на рейсмусовом станке два боковых шпинделя, расширив спектр его функции, – так появился первый четырехсторонний продольно-калевочный станок. Сегодня четырехсторонние станки серьезно изменились за счет совершенствования конструкции, однако первоначальный состав узлов сохранился.
Четырехсторонние станки используются на деревообрабатывающих и мебельных предприятиях, выпускающих различные погонажные столярно-строительные изделия и полуфабрикаты (двери, элементы декора, отделки и т. п.), а также детали мебели из цельной массивной древесины и древесных плитных материалов (ДСтП, ДВП, MDF, HDF, OSB, фанеры и других, включая материалы на основе пластиков и композиты).
Все модели состоят из следующих обязательных элементов:
- станины с рабочим и фуговальным столами;
- продольных направляющих линеек (правых и левых);
- механизма подачи (концентрированного или распре- деленного);
- прижимных механизмов (чаще пневматических) для заготовок: боковых и вертикальных;
- фрезерных агрегатов (горизонтальных и вертикальных шпинделей);
- системы управления.
Любой четырехсторонний станок можно рассматривать как комбинацию механизмов фрезерных станков, установленных на одной станине согласно последовательности выполнения операций по обработке деталей. На подобных станках последовательно обрабатываются четыре продольные поверхности заготовки, что и предопределило их название.
По исполнению четырехсторонние станки условно подразделяются на три основные группы:
1. Легкие, с шириной обработки деталей, как правило, до 180 мм. Предназначены преимущественно для производства простейших профильных погонажных столярно-строительных изделий (наличников, брусков, плинтусов и т. д.). Скорость подачи от 6 до 36 м/мин (кинематическая); 4–7 шпинделей.
2. Средние, с шириной обработки до 250 мм. Применяются для фрезерования строительного погонажа из древесины и древесных материалов, брусьев, досок и т. д. Скорость подачи от 8 до 80 м/мин; 4–12 шпинделей.
3. Тяжелые и сверхтяжелые, с шириной обработки 400–2600 мм. Используются для обработки большепролетных строительных балок, стенового клееного бруса и других деталей с большим поперечным сечением, в том числе широких и толстых клееных щитов для стен и перекрытий. Скорость подачи от 20 до 1600 м/мин; 1–6 шпинделей.
Рассмотрим станки первой и второй группы, которые в основном предназначены для получения погонажных изделий разного назначения из разнообразных материалов (рис. 1). Если обработке древесины на четырехсторонних продольно-фрезерных станках посвящено немало статей и книг, то информации о фрезеровании древесных материалов и композитов на их основе крайне мало.
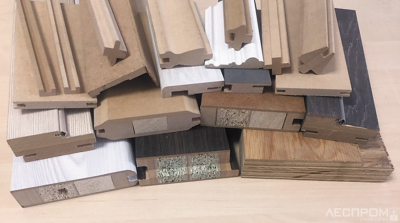
Производительность станков и качество получаемой продукции определяют следующие факторы (по степени значимости):
- оснащение и состояние технологического оборудования (мощность и число шпинделей, изношенность, наличие вибрации);
- правильный выбор режущего инструмента;
- состояние и физико-механические свойства (плотность) обрабатываемого материала;
- совершенствование технологии и возможность фрезерования нескольких заготовок одновременно;
- механизация и автоматизация технологического процесса (в частности, загрузки и разгрузки);
- правильно работающая система аспирации;
- квалификация обслуживающего персонала.
Минимальное число шпинделей, а также их невысокая мощность существенно уменьшают производительность оборудования, а изношенность и сильная вибрация на шпинделях снижают качество фрезерованных поверхностей и стойкость режущего инструмента, что также сказывается на производительности процесса из-за простоев оборудования, связанного с его частыми заменами.
Мощные шпиндели или их большое число на станке позволяют повысить производительность фрезерования за счет возможности обработки лицевых поверхностей погонажа не одним, а минимум двумя шпинделями (черновое и чистовое фрезерование) с повышением качества готовой продукции.
При этом особое значение имеет форма сечения обрабатываемого профиля. Величина (глубина) снимаемого при обработке припуска может ограничиваться мощностью привода одного шпинделя, что не позволит удалить припуск за один проход, поэтому иногда целесообразно предусмотреть на станке по два шпинделя для каждой стороны заготовки. Сложные и большие профили с поднутрением (недоступные для горизонтальной или вертикальных фрез), могут быть обработаны универсальными шпинделями, с возможностью поворота (больше двух степеней свободы). Обработка на четырехстороннем станке за один проход нескольких деталей (брусков, наличников, галтелей, раскладок, штапиков и т. п.) обеспечивается с помощью пильного шпинделя с мощным приводом, от 11 кВт. Конструктивно это может быть предпоследний или последний шпиндель на станке.
В зависимости от стоимости и стойкости режущего инструмента, физико-механических свойств плитных древесных материалов и композитов, стабильной точности профиля, объемов производства однотипного погонажа, наличия заточного участка и прочего целесообразно использовать следующий режущий инструмент (в порядке стойкости при обработке):
- насадные цельные затылованные фрезы из инструментальной стали (HSS), в том числе составные;
- насадные цельные и составные напайные фрезы с пластинами из HW (рис. 2);
- насадные фрезы, в том числе составные и фуговальные головы со сменными HW-пластинами (рис. 3);
- ножевые головы с фуговальными ножами и профильными бланкетами из HSS и HW (рис. 4);
- насадные фуговальные напайные фрезы и головы с зубьями из DP (PSD);
- насадные фуговальные фрезы со сменными зубьями из DP (PSD) (рис. 5);
- насадные профильные напайные, в том числе составные фрезы из DP (PSD) (рис. 6).
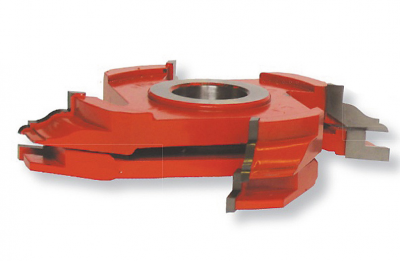
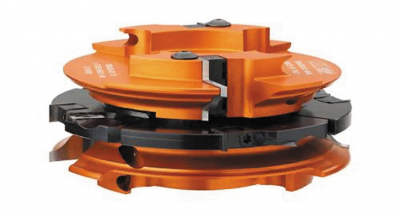
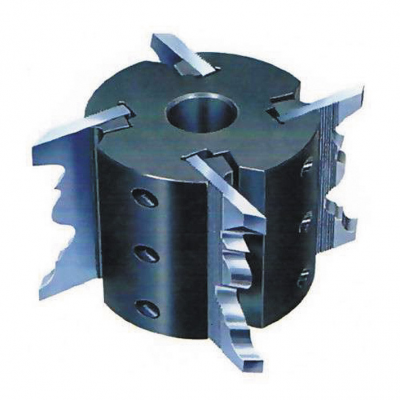

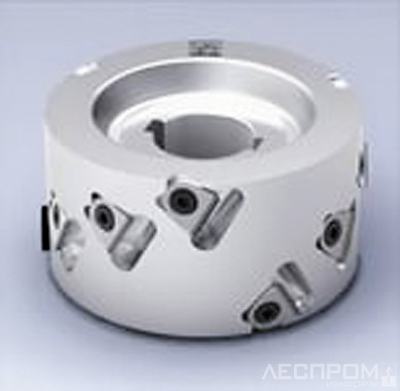
Монолитные (цельные) фрезы изготавливаются из инструментальной стали (твердость не ниже HRC 58-62) одновременно с режущей частью, которую затем затачивают. Их небольшой эксплуатационный ресурс связан с невозможностью замены режущих элементов (зубьев) по мере износа. Чаще всего их используют для фрезерования мягколиственных пород и мягких пластиков, а для обработки плитных материалов и композитов они почти непригодны из-за нестойкости. Основное их преимущество – низкая стоимость.
Какой инструмент будет эффективнее, долговечнее и дешевле в эксплуатации при обработке плитных древесных материалов и композитов на четырехстороннем продольно-фрезерном станке?
Из всей гаммы режущего HW-инструмента наиболее эффективен (по стойкости) и доступен (по стоимости) твердосплавный напайный, однако у него есть несколько недостатков. Так, при переточке параметры профиля детали изменяются, что усложняет сборку сопрягаемых изделий из деталей разных партий. Сменные HW-пластины избавляют от этих недостатков, однако, по сравнению с напайным, стойкость такого инструмента ниже, а стоимость (в том числе эксплуатационные расходы) выше.
Алмазный инструмент используется для фрезерования натуральной твердолиственной древесины, ДСтП, MDF, HDF, фанеры, OSB. Его целесообразно использовать при выпуске погонажа из плитных материалов больше 15 тыс. п. м. в месяц. Наиболее эффективен алмазный инструмент для фрезерования плит MDF, при обработке плит ДСтП, OSB, фанеры или композитных переклееных заготовок на их основе его эффективность ниже. Современные рыхлые плиты ДСтП содержат большое количество минеральных включений, добавляемых в клеевые системы вместо дорогой древесной муки. Однако их абразивные свойства отрицательно сказываются на стойкости инструмента.
Использование более жестких сменных пластинок вместо универсальных может увеличить стойкость насадных фрез на 25–30%.
Плотность обрабатываемого материала также существенно сказывается на стойкости инструмента, а следовательно, и производительности оборудования, и конечно, на качестве получаемой поверхности. Чем плотнее материал, тем выше должна быть твердость режущих элементов.
Основные требования, предьявляемые к твердосплавным фрезам для обработки древесных материалов и пластиков изложены в ГОСТ Р 52419–2005 «Фрезы насадные, оснащенные твердым сплавом, для обработки древесных материалов и пластиков. Технические условия».
Совершенствования технологии и возможность фрезерования нескольких заготовок одновременно (если позволяет конфигурация станка и установленная мощность шпинделей) позволяет значительно повысить производительность оборудования без снижения качества за счет одновременного фрезерования сразу нескольких заготовок (рис. 7) как по ширине, так и по толщине, с дальнейшим разделением их на последних шпинделях.
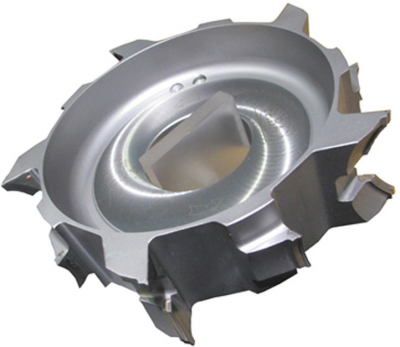
В себестоимости продукции стоимость режущих инструментов составляет около 3%. Это означает, что увеличение периодов стойкости режущих инструментов в современных условиях менее эффективно, чем повышение скорости подачи и других параметров резания и производительности обработки. Например, повышение стойкости инструмента на 50% снижает затраты только на 1%, тогда как увеличение скорости подачи на 20% обеспечивает их сокращение на 15%. Алмазный инструмент, в отличие от стального и твердосплавного, лучше работает при максимальной скорости подачи.
Механизация и автоматизация технологического процесса обработки (в частности, загрузки и разгрузки) заготовок на четырехсторонних станках позволяют повысить их производительность, уменьшить долю тяжелого ручного труда, увеличить выработку продукции на одного работающего, что в итоге снизит ее себестоимость.
Наряду с улучшением условий труда правильно организованная аспирация (особенно стационарная) на производстве способствует повышению стойкости режущего инструмента, а в конечном итоге и производительности технологического потока. Высокая квалификация обслуживающего персонала и достойная оплата труда, безусловно, тоже положительно влияют на производительность станков.
Текст Владимир Падерин