«Красфан»: гранды сибирской фанеры
Фанера известна человечеству с древности. Говорят, ее использовали в победоносной армии Александра Македонского для изготовления прочных щитов, способных успешно противостоять рубящим и колющим ударам противника. Так это или нет, судить историкам, но факт остается фактом: притом что технология производства вот уже много лет остается по сути неизменной, материал востребован на рынке, а сферы его применения и объемы потребления со временем только преумножаются. Поэтому мы посещаем фанерные заводы в разных регионах страны, знакомясь с особенностями их работы.
Так и случилось при посещении красноярской выставки «Эксподрев-2021»: стоило уважаемым коллегам из Сибирского государственного университета науки и технологий имени академика Михаила Федоровича Решетнёва, вырастившего не одно поколение специалистов для ЛПК, предложить экскурсию на предприятие «Красфан», мы тут же собрались и отправились в Сосновоборск.
В зеленом и тихом пригороде Красноярска даже трудно заподозрить присутствие крупного завода. И тем не менее на улице Заводской, больше напоминающей тенистую хвойную аллею, обнаружилась проходная на предприятие, которое, несмотря на внушительные размеры, занимает лишь малую часть площади прежнего индустриального гиганта. Но обо всем по порядку.
Предыстория и история
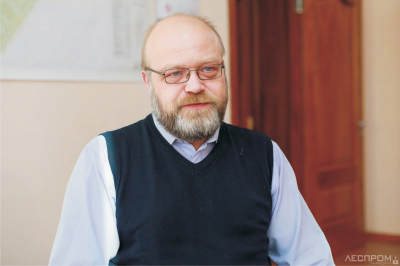
Как можно узнать из многочисленных открытых источников, в 70-х годах ушедшего века на этом месте успешно работал огромный Красноярский завод автомобильных прицепов (1976–1990 гг.), который был градообразующим предприятием Сосновоборска и фактически положил начало истории этого молодого города, отстоящего всего на 30 км от столицы края.
Основание завода было связано с интенсивным развитием в СССР производства автопоездов, строительством крупных производств грузовых автомобилей и тракторов (кстати, ставший в дальнейшем КамАЗом завод в 1960-е годы планировали построить в Красноярском крае – в рамках реализации проекта «создания Сибирского комплекса заводов по производству большегрузных автомобилей», не больше ни меньше) и необходимостью организации массового производства прицепной техники для них. В 1970 году были изданы распоряжение Совета Министров СССР и приказ Министерства автомобильной промышленности СССР, а 11 марта 1972 года состоялась закладка первого кубометра бетона в блок литейных цехов.
Завод был объявлен комсомольской стройкой. Молодые строители очередного гиганта советской промышленности не только возводили корпуса, но и высаживали саженцы хвойных пород, со временем вокруг завода выросли стройные зеленые «улицы» соснового бора.
В 1977 году на заводе изготовили тысячный полуприцеп, а в 1988 году заводчане отпраздновали выпуск 200-тысячного полуприцепа и тысячного рефрижератора. В это время среднесуточный темп производства составлял 103 полуприцепа, 19 сельскохозяйственных прицепов, 38 прицепов к легковому автомобилю и два рефрижератора. На заводе работали около 10,5 тыс. человек!
А дальше… наступили «лихие» девяностые: сперва предприятие преобразовали в Сосновоборский машиностроительный завод (1990–1991 гг.), затем оно было приватизировано и стало называться ЗАО «Бесотрал» (1991–2001 гг.), а с 2001 года – Красноярский завод прицепной техники. Это был целый производственный комплекс, на котором, помимо сборки прицепной техники и запчастей для специализированного автотранспорта, осуществлялось инструментальное, кузнечное и сталелитейное производство. Постепенно усугубляющиеся проблемы со сбытом готовой продукции стали приводить к периодическим задержкам заработной платы. В ноябре 2006 года было введено конкурсное управление и предприятие выставили на продажу, а в 2009 году завод-гигант ликвидировали. Однако для нашей истории это печальное событие не конец, а скорее начало.
В 2006 году правительству Красноярского края был представлен инвестиционный проект строительства в Сосновоборске предприятия по глубокой переработке древесины для включения его в перечень приоритетных. У владельцев ОАО «Красноярский завод прицепной техники» собственники новообразованного ООО «Енисейский фанерный комбинат» в январе 2007 года приобрели промышленную площадку – производственные и подсобные корпуса общей площадью около 260 тыс. м2, подъездные железнодорожные пути, электрическую подстанцию (общая площадь земельного участка, на котором расположены структуры комбината, 75 га).
В феврале 2008 года предприятие было включено в перечень приоритетных инвестиционных проектов в области освоения лесов, и летом 2008 года началось строительство. Кризис 2008–2009 годов и сложности с финансированием, связанные с изменением позиции основного инвестора, привели к тому, что сроки реализации проекта были сдвинуты, и все же 27 мая 2011 года состоялся пуск в эксплуатацию первой производственной линии.
Инвестиции в комбинат, открывшийся в 2009 году, составили около $15 млн. Проектная мощность предприятия – 350 тыс. м3 фанеры и 100 тыс. м3 шпона в год. Приобретенное зарубежное оборудование позволяло создать на предприятии более 600 рабочих мест. На полную мощность комбинат должен был выйти в 2012 году, но…
Деятельность Енисейского фанерного комбината в городе Сосновоборск была приостановлена Роспотребнадзором: в ходе административного расследования установлено «превышение предельно допустимой концентрации уровня миграции в воздушную среду метанола и формальдегида выпускаемой продукции». Сосновоборский городской суд, отреагировав на иск этой организации, принял решение остановить деятельность предприятия и реализацию его продукции до устранения нарушений.
В ноябре 2014 года ООО «Енисейский фанерный комбинат» было признано банкротом. К тому времени у предприятия накопились долги по зарплате на сумму почти 25 млн руб. Имущество комбината продали за 554,5 млн рублей. В 2016 году было создано ООО «Красфан». Для восстановления производства фанеры компания привлекла инвесторов и приобрела с торгов бывший Енисейский фанерный комбинат.
Как вспоминал в интервью «Комсомольской правде» директор «Красфана» Максим Замыслов, «ЕФК проработал с запуска в 2011 году до 2014 года. После банкротства завода почти 500 человек остались без работы, около трех лет помещения простаивали. В 2016 году ООО «Красфан» выкупило производственные площадки и начало восстанавливать производства. Все находилось в плачевном состоянии, но вложились, модернизировали…»
Оперативно, меньше чем за год, предприятие возобновило выпуск фанеры: к марту 2017 года компания «Красфан» произвела первые 450 м3 продукции по полному технологическому циклу.
Сегодня на производстве ООО «Красфан» работает больше 400 человек.
Начнем с сырья
Предприятие занимает всего один из многих цехов прежнего мегазавода прицепов, и, чтобы попасть «на технологию», нужно миновать еще несколько таких же, но пустых и гулких циклопических помещений, которые запросто могли бы служить самолетными ангарами. Наш проводник, главный технолог предприятия Сергей Мурашов, логично решил начать экскурсию с истоков. То есть со склада сырья.
«Мы перерабатываем древесину всех пород, которые произрастают в крае, кроме осины, – рассказал он по пути туда. – Существует даже такая отраслевая аббревиатура СКЛЕП. Ничего страшного, хоть и звучит мрачновато: сосна, кедр, лиственница, ель, пихта, – то есть все хвойные породы, которые используются в производстве фанеры. Ну и, разумеется, береза тоже активно идет в дело». Технологический процесс начинается традиционно для деревообрабатывающего предприятия – с приемки сырья (расчетная вместимость биржи 45 тыс. м3, реальное заполнение на момент посещения – около 10 тыс. м3).
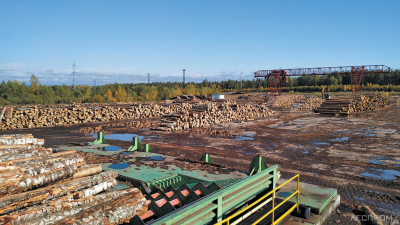
«Сортименты поступают разной длины: на собственной заготовке мы заказываем 5,4 и 2,7 м, а когда покупаем у сторонних лесозаготовителей, они, как правило, 6-метровые. Раскладываются по штабелям, с учетом длины, диаметра, породы и сортности. Отдельный штабель, самый дальний от производственного корпуса, формируется из неликвидов (это значит, либо диаметр бревна меньше допустимых 15–16 см, либо наличествует большая кривизна или гниль)».
Перевалку сырья на бирже, а также внутрицеховые перемещения обеспечивают мощные, но юркие погрузчики Liebherr.
Круглые лесоматериалы принимаются поштучно: штабель раскатывается, приходят контролеры и с двух сторон проводят точковку, определяя диаметр и сортность. По результатам этой точковки данные заносятся в систему 1С и становятся основой как для приемки, так и для формирования всей дальнейшей документации.
«После того как лес рассортировали и оформили на складе, поступает команда на подачу в производство, допустим, березы: берется ранее сформированный березовый штабель и подается на раскатной стол, – рассказывает Сергей Николаевич. – В месяц мы перерабатываем около 10 тыс. м3, то есть 120 тыс. м3 древесины в среднем за год. Готовой продукции на 1 октября 2021 года выпустили 25 тыс. м3 фанеры, на следующий год закладываем в план 35 тысяч. Да, полезный выход относительно небольшой, тому много причин, одна из которых – особенности установленного на заводе американского оборудования: оно дюймовое, рассчитано на американские древесные породы и выпуск более толстого шпона – минимальной толщиной 2,4 мм (чуть меньше 0,01 дюйма). Нам пришлось перенастраивать его, удалось уменьшить этот показатель до 2,2 мм. Собираемся купить новый станок для долущивания, он должен существенно повысить полезный выход.
Также за три первых квартала года из отходов основного производства произведено 1000 м3 брусков, 1000 м3 карандашей пиленых (их с удовольствием берут на штакетники) и 100 т топливных брикетов».
Подготовка к лущению шпона
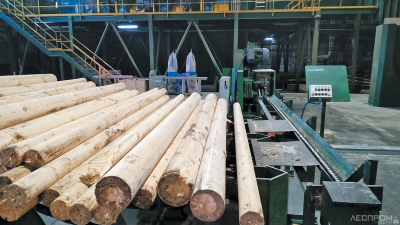
Транспортером фанерный кряж подается в цех на окорку и раскряжевку. Пройдя «жернова» двухроторного станка Valon Kone (Финляндия), окоренное сырье анализируется сканером сортиментов с распределением по пяти группам диаметра.
Линия раскряжевки USNR, по словам главного технолога завода, «стопроцентная американка»: с помощью трех дисковых пил бревно торцуется и пилится пополам. Сканер со специальными датчиками «считывает кубатуру»: расписывает сырье по породам, диаметрам и длинам, передавая в компьютерную систему всю базовую информацию и формируя отчеты.
На участке работают три оператора посменно, два через два. Сейчас завод загружен не полностью, поэтому пока работа идет только в дневные смены.
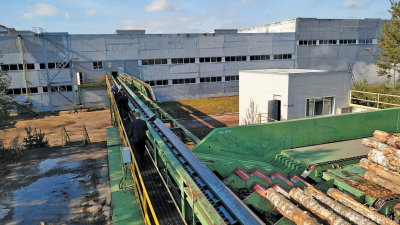
Перед лущением осуществляется гидротермическая обработка древесного сырья. «По американо-канадской технологии, примененной на нашем заводе, лес не пропаривают в бассейнах, а прогревают горячей водой в специальных туннелях, – Сергей Николаевич демонстрирует целый ряд внушительных бетонных секций, вся система управляется с пульта, параметры процесса выводятся на компьютерный дисплей. – Принцип душевой кабины: в эти камеры загружают чураки, а сверху подается горячая вода. Все время нагревать проточную воду – довольно дорогое удовольствие, поэтому организован процесс циркуляции: пройдя через штабель, вода отдает тепло и уходит через отверстия в полу туннеля по стоку в бассейн, после механической очистки по трубам подается наверх в теплообменник, нагревается и снова поступает в туннель.
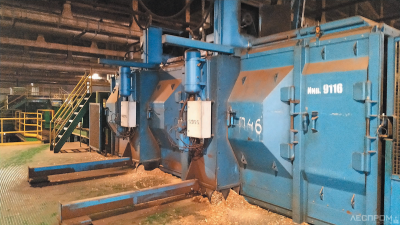
Два раза в год, весной и осенью, бассейн с водой обрабатывают химикатами (каустиком), потери воды за счет испарения восполняются свежей.
Режим нагрева один для всех пород древесины. Летом воду нагревают до 35°С, зимой – до 45°С. В центре чурака всегда 20 градусов. Камер для ГТО достаточное количество, поэтому мы можем позволить себе не спешить и использовать мягкий режим пропарки – в течение суток (24 часа)».
По завершении прогрева чураки подаются на лущильный станок.
Участок лущения
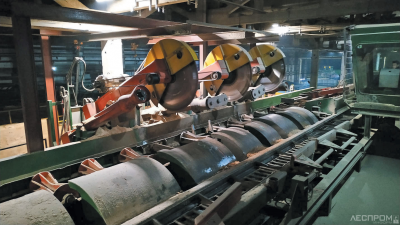
Лущение, пожалуй, основополагающий процесс в фанерном производстве. За него отвечает двухшпиндельный лущильный станок производства COE, подразделения концерна USNR (М296, США). В дальнейшем для расширения производства планируется установка еще одного лущильного станка – от компании «Лидермаш» (КНР).
На подающем конвейере шпон проходит через сканер, который производит расчет оптимальной резки ленты шпона. Одновременно со сканером работает влагомер шпона, осуществляющий его предварительную подсортировку по влажности. После сканера и влагомера шпон поступает на роторные ножницы раскроя шпона Raute.
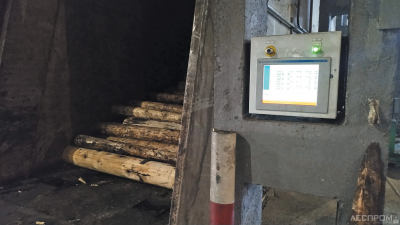
Полученный сырой шпон уходит на конвейер-накопитель. Неформатный попадает на нижний этаж установки – там стоят работницы, которые его собирают. Форматный шпон на верхних этажах распределяется на две стопы – ядро и заболонь – и поступает на стопоукладку. Со стопоукладки отправляется на промежуточный склад. На складе формируется партия для последующего высушивания в определенном режиме.
Кстати. Оборудование марки Raute, хорошо знакомой нам по другим производствам, на «Красфане», как это ни удивительно, вовсе не финское, а производства канадской Durand-Raute Industries Ltd., входящей в глобальную Raute Group. «Когда к нам в гости приезжали представители Raute, они эти станки даже не узнали, – с улыбкой вспомнил Сергей Мурашов. – Дескать, нет, мы такое не выпускаем.
Для запуска фанерного завода в 2011 году в Канаде была приобретена полностью сформированная готовая производственная линия. Она там ни дня не проработала, была впоследствии разобрана и привезена к нам. На планах и чертежах это выглядит так, будто кусок более крупного производства вырезан и целиком перемещен в Сосновоборск, где занимает площадку 400 м длиной и 75 м шириной. Вот так нам и досталось немало экзотических для России, и для Сибири, машин».
Как на любом фанерном производстве, после лущения от чураков остаются «карандаши» – срединная часть в виде тонкого цилиндра. «Мы стали перерабатывать их в брусок квадратного сечения, поставили для этого специальный станок, – главный технолог демонстрирует машину. – Полученный брус реализуем потребителям для последующего изготовления мебельного щита и создания малых архитектурных форм.
Форматные обрезки идут на прокладки для разделения слоев в штабелях. Другие отходы деревообработки сжигаются в котельной предприятия, оснащенной котлоагрегатами Бийского котельного завода, а вырабатываемое тепло используется для работы горячего пресса, сушильных комплексов, нагрева технологической воды для туннелей ГТО.
Сухие отходы, которые образуются при ребросклеивании, и форматные обрезки измельчаются в рубительной машине и становятся биотопливом».
Немного о биотопливе
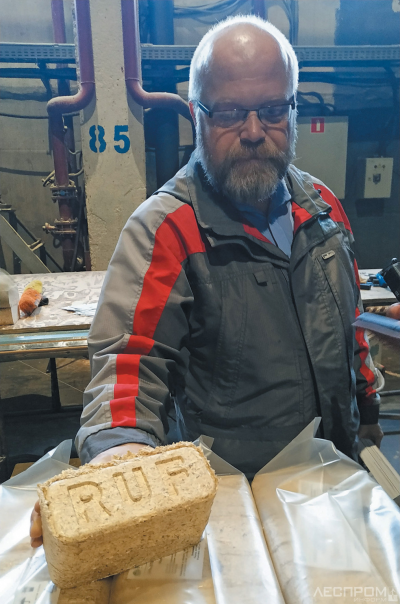
Чуть в стороне от основной линии стоит брикетная установка RUF 400, производящая в час 400 брикетов, что соответствует 345 кг. Сырьем служат твердые древесные отходы всех пород, используемых в основном производстве. Прессование происходит без связующих, брикет формируется за счет давления и нагрева. Брикеты на комбинате выпускаются с 2019 года, получены все необходимые сертификаты. Продукция успешно продается в Новосибирской и Томской областях, других регионах России. Руководство предприятия рассматривает возможность установки еще одной аналогичной линии, пскольку наращивание мощностей предприятия неизбежно приведет к образованию дополнительных объемов древесных отходов, которые можно превратить в продукцию с высокой добавленной стоимостью.
Сушим, чиним, клеим
Сушильные установки предприятия, как и станок для лущения шпона, изготовлены американской компанией COE. Это три параллельно расположенные проходные 14-секционные линии, управляемые системой Sequoia Sentry производства компании Ventek Inc. (США), которая позволяет при измерении влажности вносить поправку на толщину и температуру шпона.
Отдельно сушатся как форматный, так и неформатный шпон, который потом пойдет на внутренние слои фанеры. Для внешней «рубашки» производится ручная сортировка форматного шпона с разделением на два, три и четыре сорта. Работники визуально обнаруживают сучки, трещины и другие подобные дефекты, которые устраняются на участке оптимизации, оснащенном шпонопочиночными станками производства завода «Пролетарская свобода» (Ярославль). Как гласит немецкая поговорка, «хорошо поставленная заплатка бережет все платье», и в фанерном производстве вовремя и качественно заделанные дефекты позволяют получить продукцию более высокого класса. Ярославские станки, простые и эффективные, успешно справляются с этой задачей.
Неформатный шпон подается на линию ребросклеивания от уже упомянутой канадской «дочки» Raute. По словам Сергея Мурашова, в мире всего семь таких станков: «Сюда подается неформатный шпон, формируется ребро, перерубается, вдоль волокон ребро в ребро соединяется с получением полноформатного шпона». Казалось бы, все просто, но визуально процесс завораживает, как текущая вода, за которой можно наблюдать бесконечно.
Итак, дефекты удалены, получены полноформатные листы шпона. Пора клеить фанеру.
«Существуют разные способы клеенанесения, – к прессам главный технолог подходит издалека. – На нашем заводе представлены три: распыление – завод приобрел для этой технологии американскую линию, их всего две в мире – в Южной Африке и у нас, но сейчас она не работает, – самый распространенный в Европе контактный способ нанесения вальцами и налив».
Теперь мы можем своим глазами проследить, как сухой шпон по транспортеру попадает в клеевую завесу, так происходит нанесение связующего на поверхность. Излишки клея стекают на сито, просеиваются и через систему подогрева возвращаются обратно в систему для использования. В производстве применятся клей на основе формальдегидной смолы марки СФЖ 3014 Н. Поставки осуществляют «Метадинеа» и «УралХимПласт», два российских завода, которые производят смолу, подходящую для наливного метода нанесения.
Для передачи клеевого слоя с одного листа на другой (подпрессовки) нужен холодный пресс: набранные пакеты шпона поступают в него, оттуда на загрузочную этажерку, которой подаются в горячий пресс (на «Красфане» два сорокаэтажных пресса производства американской фирмы Spartech). По завершении прессования установка автоматически раскрывается, толкатель выталкивает фанеру на загрузочной этажерке, и установка складывается, так же автоматически.
Давление в прессе 14 MПа. Температура при рабочем режиме – 115°С.
Осталось сделать форматную обрезку: две параллельно стоящие циркулярные пилы задают размер по ширине, подобным образом другая пара пил задает размер по длине.
Полученная фанера проверяется на наличие внутренних пустот при помощи ультразвукового сканера Fagus Grecon. Главный технолог считает его морально устаревшим: «В этом году будем покупать новый!»
Дальше готовые листы поступают в карманы сортировки, формируются пакеты, которые выравниваются и обвязываются полиэстеровой лентой. Готово, можно складировать.
Ламинирование фанеры
А мы планомерно приближаемся к завершению технологической цепочки и ее новейшему пополнению – линии ламинирования фанеры. Оборудование китайского производства, эксплуатируется с мая 2021 года.
«Но, прежде чем заниматься покрытием поверхности полученной фанеры, ей нужно задать однородную толщину, – поясняет Сергей Николаевич. – Фактически мы делаем калибрование – качество поверхности в данном случае вторично, в приоритете отклонение по толщине – важно избегать разнотолщинности: разница между двумя точками не должна превышать 0,2 мм. Для этого листы фанеры пропускают через линию шлифования. Потом из них формируются пакеты, которые и поступают на ламинирование».
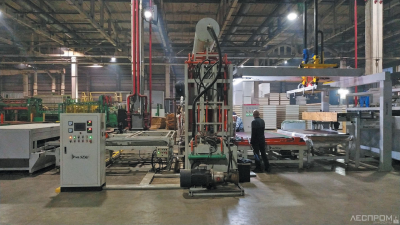
Линию ламинирования обслуживают трое: оператор у пульта управления и два человека на подаче пленки – лист фанеры подается автоматически, а пленка, как более хрупкий материал, уже вручную. В качестве теплоносителя в установке используется термомасло. Давление ламинирования – 4,6 МПа. По словам главного технолога, поначалу, используя установку, пробовали разные режимы: «При температуре 160 градусов цикл прессования продолжался около 60 секунд, сейчас применяем мягкий, щадящий режим – температуру снизили до 130, время увеличилось до 120 секунд. Для отверждения пленки этого достаточно. При охлаждении происходит полимеризация».
Пленку на основе фенолоформальдегидных смол «Красфан» закупает у ООО «Новел Групп» из Самарской области (это крупнейший в Российской Федерации производитель фенольных пленок), причем заказывать приходится резаную, в листах, поскольку использование пленки в рулоне невозможно технологически.
Из каждой партии готовых ламинированных листов отбирается образец для тестирования (механического и химического) качества отверждения.
Готовые пакеты фанеры отправляются на склад готовой продукции, расположенный по соседству. Вместе с другой готовой продукцией предприятия, там они будут ждать «попутной машины» для отправки потребителю.
Продукция и планы
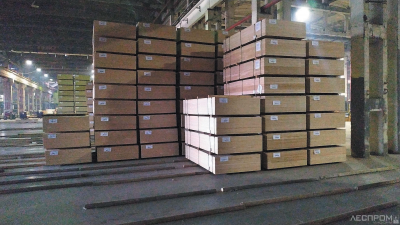
Если прежде выпускаемая предприятием продукция реализовывалась главным образом внутри страны, то в последнее время все больше поставок осуществляется на экспорт: Германия, Дания, Англия, Греция, Израиль, Египет…
«У нас ведь не очень большой завод, – с улыбкой замечает главный технолог. – Но, в принципе, мы можем полностью обеспечить потребности Красноярского края в фанере. Что, собственно, и делаем».
По словам Сергея Мурашова, имеющаяся территория позволяет думать о путях дальнейшего развития и у собственника много вероятных сценариев, рассматривалось собственное лесопиление, производство ДСП и другие, но пока окончательного решения нет. Из ближних и конкретных перспектив стоит отметить собственный лесопитомник предприятия для выращивания саженцев с закрытой корневой системой, его должны запустить в этом году.
Качество и безопасность
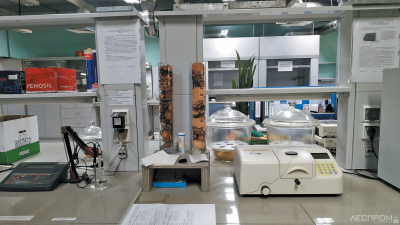
Финальным пунктом нашего путешествия по заводу «Красфан» стала полностью оснащенная лаборатория службы контроля качества, в которой проводятся все необходимые анализы продукции с определением физико-механических показателей, плотности, влажности и испытания на изгиб, скалывание, выделение формальдегида. Также отслеживаются вязкость и расход связующих, качество смолы, поступающей от поставщиков.
Как рассказала начальник лаборатории Юлия Владимировна Залюбовская, класс эмиссии формальдегида для хвойной фанеры – Е0,5, для лиственной – Е1. Это хорошие показатели, однако на предприятии ведется планомерная работа по их снижению.
Российские и международные сертификаты получены на все основные виды продукции: хвойную, березовую и лиственничную фанеру, ламинированную фанеру, топливные брикеты.
Забота о безопасности и экологии для работников предприятия не пустой звук или модная тема – это и залог успешной реализации выпускаемой продукции, и реальная возможность сохранить родной Сосновоборск таким же зеленым…
Редакция благодарит Михаила Баяндина (СибГУ им. М. Ф. Решетнёва) и Александра Тамби (ассоциация «Лестех») за помощь в организации поездки.
Справка
Площадь Сосновоборска – 2664 га, общая протяженность улиц и проездов – 72,1 км. На 1 января 2018 года на одного жителя приходилось 23,7 кв. м общей площади жилых помещений. Средний возраст сосновоборца – почти 39 лет. Официальный уровень безработицы – 0,7%. Предприятия: Красноярская ТЭЦ-4, ООО «Красфан», ООО «Завод холодильного оборудования "Айсберг"», Красноярский завод полимерной упаковки «Европласт».
«АиФ»
Справка
Заготовка древесины
ООО «Красфан» арендует лесные участки в границах нескольких лесничеств Красноярского края: Емельяновском (46887 га), Балахтинском (62006 га), Сухобузимском (102461 га), Козульском (139548 га), где ведется лесозаготовительная деятельность в виде как сплошных, так и выборочных рубок.
Собственная заготовка ведется с помощью сортиментных комплексов, приобретенных в лизинг.
Древесное сырье вывозится из леса и доставляется на предприятие автомобильным транспортом.
Справка
Основные виды продукции ООО «Красфан»:
Фанера влагостойкая марки ФСФ общего назначения (формат 1220 х 2440 мм) с наружными слоями из хвойных пород и лиственных пород (береза), шлифованная и нешлифованная, фанера строительная, фанера ламинированная, брикеты древесные топливные, а также отходы лесопереработки (оточка цилиндрическая – «карандаш», дрова, топливная древесная щепа и т. д.).
Текст и фото Леспроминформ