Зашкаливающая маржинальность лесозаготовки, или чем станок лучше напильника
Лесозаготовительный сектор в России, казалось бы, состоялся: рынок поделен и вовсю идет укрупнение бизнеса, используется самая современная техника, производители предоставляют сногсшибательный по скорости и охвату сервис. Все, кажется, на высоком уровне – для человека, не имеющего отношения к отрасли...
Лет семь назад на одной международной выставке производитель профессиональной техники задал мне вопрос: «У вас в России что, нет цепных пил?» Я даже не сразу нашелся, что ответить, – вроде, есть… Да и газ у нас не везде, и отапливаемся дровами… Тут он меня сразил вторым вопросом: «Почему же тогда в вашей стране нет профессионального оборудования для заточки цепного инструмента?» Хм! Как человек интересующийся, я стал факультативно (работаю в деревообработке, а лесозаготовка – все же отдельная сфера) изучать «матчасть». Благо, есть где получить информацию из первых рук. Побывал и на лесозаготовительных участках, и на легендарном чемпионате по рубке, пообщался с операторами – а в итоге, честно говоря, был шокирован.
Создалось обоснованное впечатление, что в лесозаготовительном бизнесе уровень маржинальности, который перекочевал из 1990-х годов, настолько высок, что предприниматели, приобретая технику за миллионы евро(!), не понимают и по некоторым причинам не хотят понимать, что ствол дерева пилит цепная пила, а все остальное – это вспомогательная техника, которая доставляет инструмент к дереву.
На вопрос, почему в этой сфере никому нет дела до заточки пильных шин, ответ у всех один: «Норморасход инструмента хозяина устраивает, а у нас и других забот хватает». Парадоксально, но факт: у подавляющего большинства лесозаготовителей подготовка инструмента организована на пещерном уровне. А значит, дорогостоящая техника работает неэффективно, владельцы не только тратятся на ремонты, запчасти и лишнее топливо, но и недополучают кубатуру.
Как это происходит на практике? Сейчас заточку инструмента выполняют прямо на делянке, где ведется заготовка: на бытовом ручном устройстве это делает и без того загруженный мастер участка или оператор валочной машины.
И при этом все операторы в один голос утверждают: после того, как заточной круг бытового станка коснется цепной пилы, она уже никогда не будет работать как новая. Именно поэтому многие операторы считают необходимым несколько раз за смену выскочить из машины и напильником подточить цепь. Такой способ эффективен, только если у оператора есть навык заточки. Кроме того, за требующиеся для заточки минимум 10–20 минут (которые валочная машина стоимостью около €500 тыс. простаивает), хозяин недополучает 3–6 «кубов» пиловочника. При этом валочная машина из-за лишних простоев и неэффективности работы недорубает в смену около 5 м3, что за год выливается в 2400 м3 недополученной древесины, а это еще примерно 14 млн рублей.
Почему качество заточки на бытовом станке низкое? Причины те же, что и в случае заточки любым профессиональным многозубым инструментом.
Заточка осуществляется вручную, поэтому неизбежен разброс по размерам и геометрии. Зуб – ограничитель подачи или вовсе не затачивается или затачивается на глаз, то есть произвольно. При работе заточенного таким образом инструмента нагрузка на зубья распределяется неравномерно, и объективно пила пилит плохо; при этом оператор валочной машины вынужден увеличивать давление на пильный узел, что приводит к ускоренному износу звездочек, шин и гидромоторов, а также к удлинению и последующему разрыву пильной цепи. Ремонтировать такую цепь бесполезно. При этом пользователи, как ни странно – отмечая быстрый износ шин, вместо того чтобы озаботиться повышением качества заточки инструмента (то есть устранить причину износа) – заказывают у поставщиков усиленные шины, которые, понятно, дороже обычных.
Из-за отсутствия охлаждения зоны заточки зуб перегревается (часто это видно невооруженным глазом: металл синеет) и становится хрупким. В результате стойкость инструмента снижается в разы.
Сравним норморасход режущего инструмента на одну валочную машину (привожу реальный пример – см. табл.).
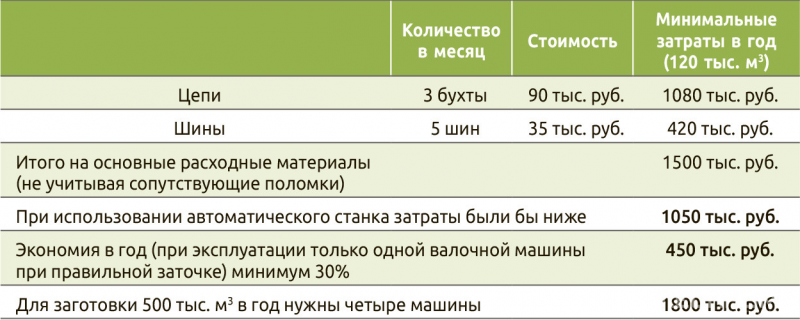
Как следует из приведенных цифр, при эксплуатации четырех валочных машин автоматический профессиональный заточной станок окупается за год.
Некоторые предприятия смогли снизить затраты и добиться вдвое меньшего норморасхода, но таких – единицы.
Казалось бы, очевидно: проблема требует решения. Но у нас «хвост виляет собакой», и сотрудники разного уровня на местах по тем или иным причинам не хотят оптимизировать процесс, а руководитель, как ни странно, ничего не может с этим поделать.
В «коварном» зарубежье все по-другому: на автоматических станках затачивают все цепные пилы для валочных машин и почти все – для ручного инструмента. Например, в Германии эксплуатируется примерно 1000 таких профессиональных станков. А в Финляндии их около шестидесяти. Работа там строится на том, что конечный пользователь платит за аренду цепей, т. е. ему привозят партию готового к работе инструмента и через неделю забирают в заточку, привозя новую партию. Тем самым конечный пользователь сосредотачивается на выполнении основной задачи бизнеса, при этом работая оптимально (и значит: профессионально) подготовленным инструментом. Да-да, замена которого осуществляется на машине за пару минут.
В России такое оборудование тоже есть, правда, в единственном экземпляре: в профессиональном сервисном центре компании «Инструментальный мир» (г. Ковров). Причем компания занимается заточкой только ручного инструмента, а местные лесозаготовители работать с ней отказались по причинам, указанным выше.
Как ни крути, если в отрасли не стремятся считать деньги и минимизировать лишние расходы, значит, уровень маржинальности там зашкаливает. Но так будет не всегда. Уже сейчас довольно просто оптимизировать многие рабочие моменты для сохранения конкурентоспособности. Так не пора ли об этом задуматься?
Текст
Андрей Фёдоров, отдел сбыта по России ООО «Фолльмер Рус»