GT: Жизнь в зеленом цвете
Признаюсь, всегда считал название петербургской компании Green Tools, совсем недавно сокращенное до GT, данью популярности европейской «зеленой повестке», не особенно задумываясь о смысле: какие вообще отношения могут связывать режущий инструмент и экологию? И только визит на предприятие помог расставить все точки над i…
Незадолго до Нового года бренд отметил пятилетие. Однако история работы в области дереворежущего инструмента началась гораздо раньше.
Коротко о главном
GT – отечественный производитель режущего инструмента для деревообрабатывающей, мебельной и других отраслей промышленности. Сегодня в ассортименте компании насчитывается более 900 наименований только стандартных позиций осевого и насадного инструмента в HM и PCD-вариантах и дисковых пил с HM и PCD-режущими элементами. Отдельное направление деятельности – проектирование и производство инструмента любой сложности по индивидуальному заказу.
Производство укомплектовано оборудованием компаний Vollmer Werke Maschinenfabrik GmbH, J. Schneeberger Maschinen AG, E. Zoller GmbH & Co KG, Haas Automation Inc, Kirschner Maschinenbau GmbH и др. Для изготовления инструмента используются материалы от Tigra GmbH, Bestar Stahlhandelsgesellschaft Remscheid mbH, De Beers Group и других европейских компаний.
Среди потребителей инструмента GT компании из самых разных сфер лесопереработки: Segezha Group, «Илим Тимбер», «Игирма Груп», «Евразия Холдинг», «Алмаз», Волгодонский комбинат древесных плит, «Акватон», Nextform, «Невский ламинат», «Первая мебельная фабрика», IKEA, «Стандарт Сити», Mizantin, «Ставрос», «Арбор Нова», «Леор», Grand Fasad, «Кухонный завод» и многие другие.
Помимо предприятий ЛПК, инструмент под маркой GT применяется в авиа-, авто-, приборо-, машиностроении.
В штате компании 57 человек, в том числе 45 занято в производстве. Остальные – это отдел закупок, техотдел, финансовый отдел и управление. Предприятие работает в режиме 24/7, в три смены.
Официальные представительства компании есть в Москве, Нижнем Новгороде, Пензе, Ростове-на-Дону, Хабаровске, Петрозаводске. 17 дилеров по России, а также в Белоруссии и Казахстане.
«Что в имени тебе моем?»
Официальным днем рождения GT считается 16 декабря 2016 года.
«Это дата регистрации предприятия, – рассказывает заместитель генерального директора ООО "Грин Тулс" Екатерина Попова. – Тогда был создан наш бренд и его символ. С этим связана целая история! Долго думали-гадали, как назвать фирму и каким должен быть ее логотип. Рисовали самые разные варианты – их было очень много, устроили такой общий мозговой штурм. И тут вспомнили про своего питомца по имени Зеленый – это большая и, в полном соответствии с именем, зеленая игуана. Вот так – "зеленый" (green) плюс "инструменты" (tools) – и родилось название, а следом и изображение свернувшейся в кольцо игуаны.
Зеленый попал к нам маленьким и был рядом всегда, переезжал из офиса в офис вместе с нами, стал свидетелем всего происходящего в компании. Этот ящер прожил долгую жизнь – 16 лет, по человеческим меркам, говорят, около ста, но, к сожалению, в прошлом году умер. А сейчас в большом террариуме посреди кабинета живет его преемник – Зеленый-второй. Так совпало, что вскоре после ухода нашей игуаны мы узнали о подобном животном, которое пытаются пристроить в добрые руки. Конечно, мы его забрали, это полноценный сотрудник нашего предприятия и всеобщий любимец».
Путь к алмазной фрезе
Площадь производственной площадки компании примерно 1000 м2, здание находится в аренде. В нем производственный цех, склад продукции под отгрузку, техотдел и несколько административных помещений.
Над зоной въезда сделан козырьком настил – там организован своеобразный открытый кабинет директора, откуда он в окружении выставочных образцов компании может следить за процессом производства в цеху. Именно туда я и направился, чтобы узнать у учредителя и директора GT Дмитрия Соколова, как и с чего все началось.
«Как и многие другие, бизнес я начинал с продаж, и было это – страшно подумать – 22 года тому назад. Почему именно режущий инструмент? Наверное, в этом сыграл свою роль вуз, но вообще я с детства связан с деревообработкой: примерно в 10 лет я попал в столярную мастерскую, где занимались художественной резкой по древесине, вот с этого, наверное, и началась моя к ней любовь. Отучился в училище на мастера-краснодеревщика. Много работал на мебельных фабриках, окончил Лесотехническую академию (специализация – технологии деревообработки). По большому счету основной костяк компании состоит из ее выпускников.
Ну а потом так сложилось, что именно это направление стало развиваться: сначала продажи, потом потихоньку занялись сервисом… Расположенный в Санкт-Петербурге сервисный центр по заточке, восстановлению и ремонту пил и фрез стал известен далеко за пределами Северной столицы. И постепенно я приходил к пониманию того, что на тех станках, которые задействованы в обслуживании инструмента, его можно и производить.
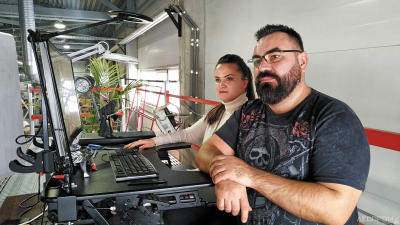
Мы долгое время представляли в России немецкую компанию AKE, обеспечивая сервис и продажи ее инструмента. В принципе, до сих пор остаемся партнерами, но дальше – больше мне хотелось заниматься именно изготовлением продукции. Всегда интереснее самому производить что-то новое, чем продавать сделанное другими.
Сильная сторона AKE – лесопиление. Но мы мыслили гораздо шире и ассортиментный ряд производителя нам не совсем подходил. Развитие пошло в ином направлении, и как конкурентов мы рассматриваем совсем другие компании. В Европе производителей инструмента огромное количество, и выбрать кого-то одного в партнеры, чтобы "покрыть” все рыночные сегменты, не получается. А когда у тебя много поставщиков – это тоже неудобно. Вот, представьте, с крупного мебельного предприятия поступает комплексный заказ на разные типы инструмента и ты начинаешь его в кучку собирать: срок обработки заказа (только обработки, еще до предложения компании и тем более изготовления продукта!) что у немцев, что у итальянцев составляет 3–4 недели, затем разработка чертежей и так далее… Очень долго, а ведь никто ждать не хочет. Для сравнения: мы стараемся по предложению укладываться в три дня, на чертежи – максимум неделя.
Я пришел к необходимости создания полноценного собственного производства еще и потому, что зависеть от кого бы то ни было в определенных ситуациях бывает, мягко говоря, некомфортно. Простой пример: поступает крупный заказ, большие деньги вложены, размещаешь его за границей, долго и нервно ждешь, а потом выясняется, что на предприятии заказчика оборудование не работает или работает, но не должным образом. И в этот момент выясняется, что добросовестной техподдержки с той стороны практически нет, а ответ производителя на твои запросы, по сути, вежливый вариант фразы “это ваши проблемы, решайте сами”. И ты остаешься виноватым перед заказчиком, твоя репутация страдает.
Да и зачем покупать со стороны то, что мы способны делать сами ничуть не хуже? Когда зависишь только от себя и сам отвечаешь за все, по-другому относишься к делу. Да и к тебе иначе относятся.
Сердцем полноценного инструментального производства является механический участок, где начинается жизнь металлической болванки, становящейся корпусом инструмента. Все остальное делается на сервисных станках, равно пригодных как для изготовления нового инструмента, так и для обслуживания б/у. Главное было организовать механический участок, а там заработало и все остальное.
Конечно, перейти от сервиса инструмента к производству было не просто. Прежде чем сделать этот ответственный шаг, пришлось объездить немало заводов Европы, поучаствовать во всех ведущих отраслевых выставках, начиная с ганноверской Ligna в 2005 году (кстати, мы познакомились с земляками из GT именно в Ганновере. – Прим. авт.), чтобы изучить, как работают ведущие производители. Надо было "дозреть" до понимания, что ничего сверхсложного в этом процессе нет, и решиться начать.
А еще – научить сотрудников конструированию. Наши инженеры-технологи приобрели богатый опыт, в том числе в Германии, они буквально своими руками освоили это дело, стали уникальными специалистами, знают процесс изнутри и делятся знаниями с поступающими к нам на работу людьми.
Мы на каждом этапе технологии до мелочей понимаем, что и как нужно делать – от выбора материалов и конструкторских разработок до отгрузки готовых изделий. Достаточно сказать, что с запуском собственного производства количество рекламаций клиентов уменьшилось во много раз. А те, что случаются, оперативно и успешно решаются, что пополняет наш опыт и дает новый толчок для усовершенствований и развития.
На сегодня мы изготавливаем полный набор применяемого в индустрии режущего инструмента, кроме ленточных пил: дисковые пилы (диаметр стандартно до 600 мм, опционально до 800 мм), концевые и насадные фрезы (диаметр насадного инструмента до 350 мм) в широком ассортименте – с твердосплавными и алмазными напайками, сменными ножами и пр. С действующим станочным парком мы способны собственными силами производить очень большой набор изделий, в том числе сложных и для самых разных отраслей, например, для оконных производств или деревянного домостроения. Мы наработали такую обширную производственную базу, что создание даже самого нестандартного инструмента не вызывает у нас больших проблем.
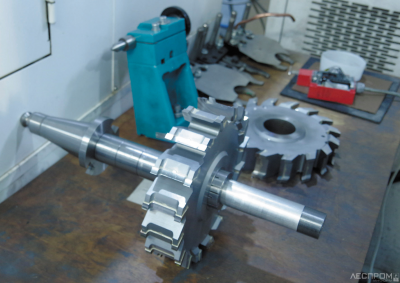
В чем наша особенность как производителя? Наш рынок сбыта – это только Российская Федерация и страны СНГ. Мы производим и реализуем внутри страны. Что это значит? Во-первых, мы быстро отвечаем на запросы, во-вторых, нет никаких проблем с логистикой при доставке. Нет и рисков, связанных с недобросовестностью поставщиков, поскольку все делаем сами и материалы всегда в наличии. Но самое главное, конечно, что в разы быстрее изготавливаем продукцию. Если срок исполнения заказа известным европейским производителем составляет 30 недель, то мы аналогичную заявку полностью отработаем за 5–6 недель!
Понятно, что покупатели привыкли к определенным стандартам качества, так или иначе связанным с брендами производителей инструмента. Порой приходится сталкиваться с определенным недоверием, но оно проходит после первой покупки и опробования нашего инструмента на производстве. А дальше включается простая логика: материалы те же, оборудование и технологические процессы те же, квалификация работников на одинаковом уровне, значит, и инструмент как минимум не хуже. Ну и не будем забывать о доступности сервиса.
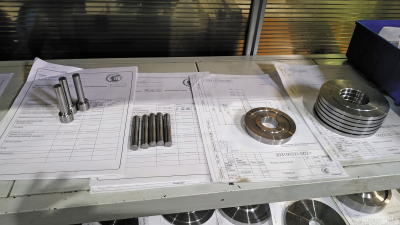
Активное развитие станочного парка началось примерно три года назад. Не могу сказать, что сейчас он полностью укомплектован, – всегда хочется лучшего, более современного и эффективного, поэтому продолжаем развиваться в этом направлении. В скором времени на площадке появятся новые машины, и, когда они будут включены в производственный цикл, все заработает, я надеюсь, что производительность и обороты вырастут раза в два. А себестоимость продукции за счет этого удастся снизить, что наверняка понравится клиентам».
Театр начинается с вешалки…
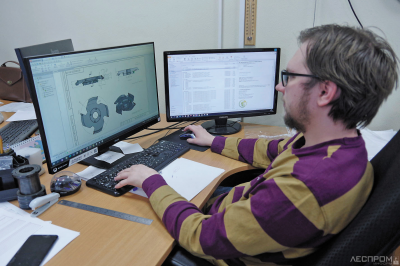
«Клиент предоставляет нам техзадание, причем это может быть набор показателей и размеров, эскиз или просто определенный запрос: "Надо то-то для того-то, что можете предложить?" Это задание поступает в технический отдел, технологи садятся за работу и на основе полученных данных разрабатывают проект, создают техническую модель и подробные чертежи с учетом технологии, оборудования и инструмента, с помощью которых будет изготовлено изделие, потом это все обязательно обсуждается и согласовывается с заказчиком. Получилось ли именно то, чего он хотел, и, с другой стороны, правильные ли пожелания высказал, исходя из потребностей своего производства? Заказов приходит до десяти в день, объем работы у технологов очень большой», – рассказывает Екатерина Попова.
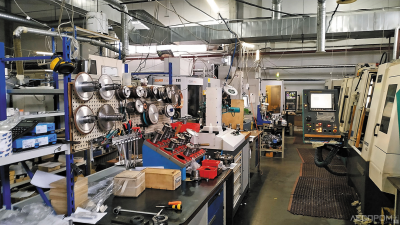
Прямо под окнами вынесенного в отдельный кабинет на втором этаже техотдела расположен склад. Небольшой, и вот почему.
«Склад готовых изделий стараемся сильно не раздувать, потому что это все-таки вложение серьезных оборотных средств. На складе для текущих продаж поддерживается запас самых востребованных типоразмеров и инструмента базового уровня. Допустим, стандартный алмазный подрез диаметра 120, мы сразу делаем партию 100–150 штук, чтобы, помимо текущих заказов, создать складской запас, они продаются как горячие пирожки, а при особенностях оборудования наиболее рентабельно именно серийное производство. Так же и с нестинговыми фрезами», – пояснил Дмитрий Соколов.
«В последний раз мы делали инструмент именно для склада в начале первой волны коронавируса. И все. Остальное время загрузка такова, что только успевай отрабатывать заказы», – добавил бренд-менеджер Артем Озолин.
Но склад – это своеобразный финиш в производственной гонке. А мы с Дмитрием Соколовым тем временем подошли к ее старту, он любезно согласился провести экскурсию последовательно по всем участкам производства – дисковых пил, спиральных фрез и алмазного инструмента.
Изготовление дисковых пил
Рассказывает Дмитрий Соколов:
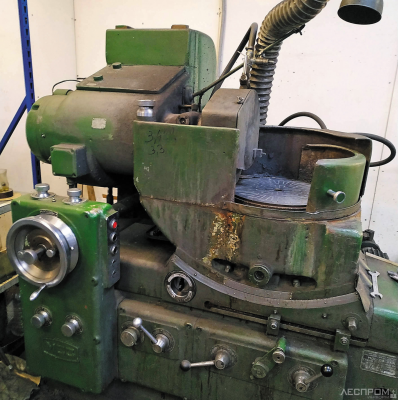
– Что касается дисковых пил, на предприятии совмещены функции производства и сервисного обслуживания – мы изготавливаем эти пилы как в стандартных сериях, так и под заказ, а кроме того, восстанавливаем инструмент клиентов, который требует замены напаек, ремонта, доработки посадочных отверстий.
Изготовление любого продукта, в том числе новой пилы, начинается с разработки конструкторской документации: технолог готовит комплект, состоящий из техзадания, чертежей (клиент эти чертежи утверждает) и маршрутного листа. Только после этого запускается производство.
Прежде чем изготовить пилу, надо подготовить корпус. Корпуса вырезаются из поставляемого компанией Bestar, Германия, листового металла – эту операцию мы отдали на аутсорсинг, партнер выполняет раскрой под наши текущие потребности (как пояснил директор GT, «необходимости в организации собственного участка для вырезания заготовок нет – при текущей загрузке такая установка будет работать, скажем, 20 минут в день; гораздо рачительнее и проще поручить эту задачу партнеру, предоставив ему металл и чертежи». – Прим. авт.).
С полученных стальных полуфабрикатов после лазерной резки нужно удалить связанные с высокотемпературной обработкой выплески металла и другие несовершенства, которые мешают дальнейшей работе. Кроме того, необходима дополнительная шлифовка поверхности. Мы шлифуем поверхность по всему диаметру будущей пилы, поскольку возможна разнотолщинность продольного листового проката по сечению, которая имеет значение для свесов на сторону при напайке зубьев, выравниваем полотно и заодно придаем ему более презентабельный вид, устраняя все поверхностные дефекты. Для этой операции применяется раритетный станок, выпушенный Московским станкостроительным заводом в далеком 1957 году, как ни удивительно, по точности обработки, до 5 микрон, он может дать фору многим современным машинам. При этом станок с автоматической подачей, реализован магнитный стол, на котором удерживается заготовка, массивная станина, вращение вала в бронзовых втулках без использования подшипников… Сравнивая с современными моделями, мы отметили, что в этой области технологии если и шагнули куда-то, то не вполне вперед: конструкции стали облегченными, а точность понизилась.
После обработки на этом станке полотно приобретает безукоризненный вид. Но это далеко не все. Для того чтобы оно стало корпусом пилы, ему нужно придать геометрическую ровность и внутреннее напряжение. Напряжение – один из основных параметров дисковой пилы, при его нарушении она не будет работать должным образом. Внутреннее напряжение пилы это, по сути, реакция пилы на внешние изменения, она должна быть стабильной и позволять пиле удерживать заданную геометрическую форму, для того чтобы обеспечить наиболее ровный рез. А ведь именно этого мы и ждем от качественного инструмента.
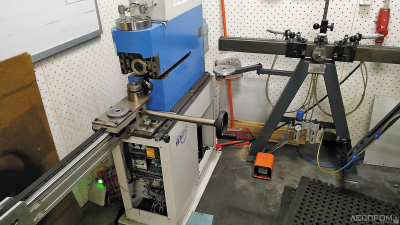
Мы производим замеры на специальном устройстве производства компании AKE путем изгиба полотна и его реакции на этот изгиб. Для разных типов обработки древесины требуются разные напряжения, соответственно, если мы понимаем, что пила недонапряжена, требуется придать ей дополнительное напряжение. Делается это с помощью вальцовочного автомата. Для того чтобы пилу заданного диаметра напрячь на нужное количество единиц, следует прокатать одно или два вальцовочных кольца на определенном расстоянии от центра пилы с установленным гидравлическим усилием. Разработанные методики позволяют сделать это достаточно точно. Устройство это тоже немецкое, фирмы MumTec.
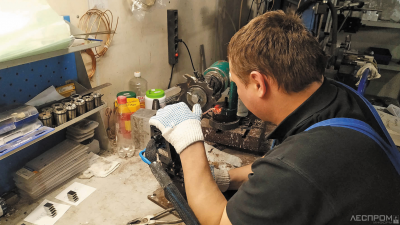
Если после этого все же требуется более точная подгонка, проводится ручная рихтовка на наковальне. Это тонкая работа, которую могут выполнять только опытные специалисты очень высокого класса. Мы своих обучали в Германии, и только через несколько лет они могут выдавать прогнозируемые результаты.
После всех обработок проводится финальный контроль. Разработаны специальные нормативы, по которым производится проверка. Если точность соответствует заявленной в проектных чертежах, пила готовится дальше.
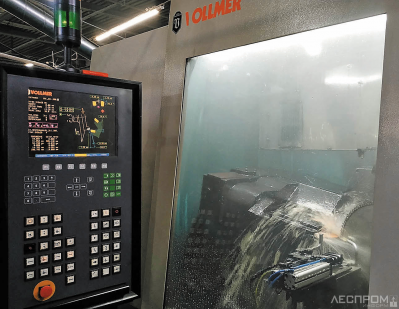
На подготовленный корпус напаиваются зубья. Делается это на установке компании Kirschner Maschinenbau GmbH, Германия. Процесс пайки автоматизирован, ТВЧ-нагрев наиболее щадящий как для твердого сплава, так и для корпуса – в компьютер заложены температура и продолжительность нагрева, а также время отпуска. Все процессы контролируются при помощи пирометрического устройства, обеспечивающего обратную связь на компьютер для поддержания либо прекращения процесса. Используем твердый сплав компании Tigra, припой и флюсы – немецкой компании Brazetec.
Почему так важен пирометрический контроль? Повышенная температура при работе со спекаемыми материалами (твердыми сплавами и поликристаллическим алмазом) может привести к растрескиванию, а точное выдерживание параметров позволяет выпускать долговечный и износостойкий инструмент.
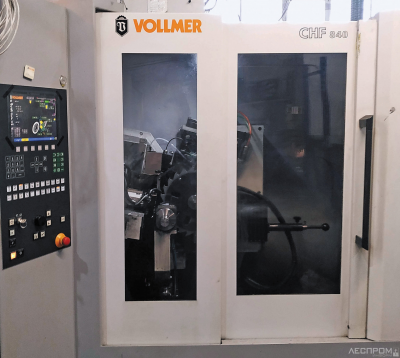
Необходимо удалить последствия напайки зубьев – побежалость, следы флюса и припоя с помощью пескоструйной обработки.
Следующий этап – заточка зубьев из твердого сплава выполняется на группе станков компании Vollmer. Мы разделяем станки по типу заточки: одни работают по передней грани, другие – по задней и отдельный станок – по боковой грани. Что это нам дает? Возможность в разы увеличить объем выпускаемого инструмента. Минимум перенастроек приводит к увеличению поточности.
Конечно, есть станки, работающие в универсальном режиме, но они, как правило, не используются для изготовления новых пил, а применяются в сервисных работах.
Основные марки заточных станков: CX100, CHD250, CHF840. Самый интересный в этой линейке станок CHD250 позволяет работать в автоматическом режиме с роботизированной сменой инструмента. Оператор набирает входящую палету, вмещающую до 40 пил, каждую пилу заносит под определенным номером в программу, туда же забивает количество зубьев и необходимые углы заточки. Палета закатывается в приемный магазин роботизированной подачи и запускается в работу. Участие оператора больше не требуется, и станок может, допустим, за ночную смену обработать все 40 пил в соответствии с заданием. Если при автоматической проверке каждого изделия на соответствие по диаметрам, угловым параметрам станок обнаруживает несоответствие, то «отказная» пила откладывается в сторону, на отдельную палету, но при этом весь процесс не тормозится. Готовые пилы размещаются на третьей палете, и на этом процесс фактически завершается.
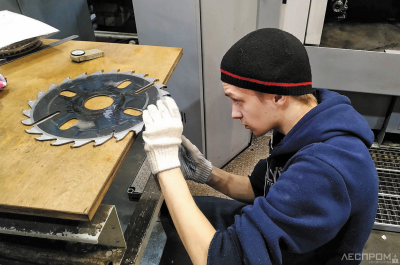
Станок самостоятельно перенастраивается с заточки по передней грани на заточку по задней и наоборот, для этого установлены два круга на шпинделе. В зависимости от выбранной программы зубьям можно придать любую форму, которая применяется в нашей промышленности: прямая заточка, трапециевидная, косозубая, заточка на одну сторону и на обе…. И это все в автоматическом режиме.
Последняя операция – заточка по боковой грани выполняется на станке Vollmer CHF840.
При необходимости проводится доработка посадки. Если требуется высокоточная посадка, то она выполняется на координатно-расточном станке, как правило, для стандартной точности посадки обычно более чем достаточно простого чистового посадочного фрезерования. Однако некоторые операции, например, скользящую посадку, этот станок не производит, тогда применяется электроэрозия на ЧПУ-станке. Этот метод позволяет обрабатывать заготовки пакетно: допустим, если нужно сделать 20 одинаковых по параметрам пил, мы можем «зарядить» все 20 штук в один пакет, выровнять по базовой посадке и подать в станок, получив на выходе изделия с высокой точностью обработки.
Потом каждая пила отправляется на очередной замер по биениям геометрической ровности и прочности. Если все в порядке, пилы маркируются – прямо на диск наносится логотип или имя клиента, для того чтобы его можно было легко идентифицировать. Заказчикам это нравится – получается персонализированный инструмент.
Маркированный лазером инструмент покрывается специальным консервирующим составом для защиты от коррозии, упаковывается и снабжается тут же распечатываемыми табличками, содержащими основную информацию о продукте – артикул, типовые размеры. После этого он готов для передачи клиенту.
На упаковке мы не экономим. Например, фрезы отправляются заказчику в удобных фанерных ящичках с выгравированными на крышке данными об инструменте, позволяющими клиенту в следующий раз быстро и легко заказать аналогичный следующий, просто назвав артикул или характеристики.
Изготовление спиральных фрез
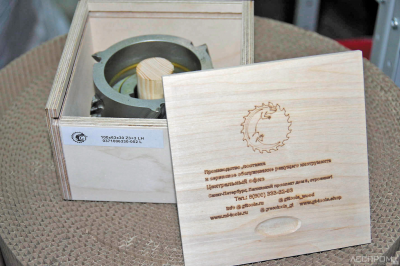
Первая операция при производстве спиральных средств – это резка твердосплавного металлического прута (в соответствии с разработанными технологом картами раскроя, для обеспечения оптимального раскроя у нас есть специальная программа). Прутки от поставщика поступают стандартной длины 330 мм и разного диаметра. Прут нарезается по длине с учетом всех поступивших заказов таким образом, чтобы минимизировать неделовой остаток, из прута длиной меньше 50 мм сделать фрезу невозможно.
Резка производится тонким кругом с алмазным покрытием в водном охлаждающем слое – заготовка постоянно находится под действием охлаждающей жидкости на основе немецкого концентрата, рез получается идеально ровный и идеально чистый. Настроечная линейка позволяет резать в размер максимально точно. Станок классический, работает у нас около 10 лет, это оборудование еще из тех времен, когда оно делалось с прицелом на вечность. Конечно, если бережно поддерживать его в надлежащем состоянии.
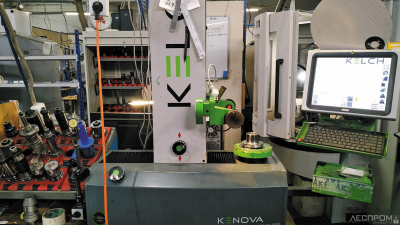
Полученные заготовки нужной длины поступают на участок шлифования. Порой им требуется дополнительная обработка вроде обнижения диаметра (рабочего либо диаметра хвостовика), в зависимости от потребности заказчика.
У нас внедрена система учета движения заказа на базе 1С и мониторинг рабочего времени, делающие рабочий процесс оптимальным.
На каждом станке установлен терминал, с помощью которого можно идентифицировать начало и завершение обработки, а также установить, на каком станке и какой оператор ее выполнил. Эти данные используются для аналитики и выстраивания очередности выполнения заказов в современной цифровой системе управления производством.
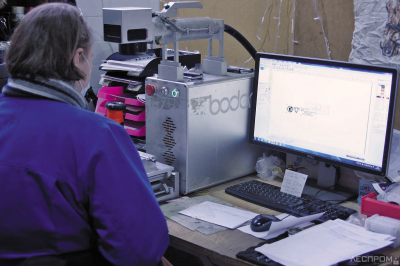
Шлифование твердосплавных заготовок производится на станках швейцарской компании Schneeberger и немецкой Vollmer. Точность обработки до одного микрона.
Результат работы проверяется с помощью станции оперативного оптического контроля. Измерение осуществляется как по светотеневой копии, так и камерой. Для того чтобы обеспечить максимальную точность и удобство эксплуатации, мы используем в зажимах инструмента гидравлические патроны.
После того как фрезы того или иного вида изготовлены, заказ поступает на участок маркировки, упаковки и далее на склад для отгрузки клиенту.
По соседству с участком, где наносится лазерная маркировка, расположена балансировочная машина Tool Dynamic немецкой компании Haimer.
Изготовление алмазных фрез
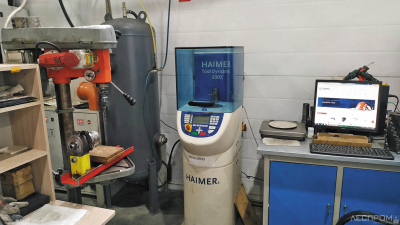
Алмазные фрезы составляют наибольшую часть в структуре выпуска компании. Изготавливаются как концевые, так и насадные фрезы, как прямые, так и профильные. В том числе сборные для сложных конструкций, например, для паркетного, мебельного или дверного производства. Для их производства требуется самый большой пакет инженерно-конструкторской документации: отдельный чертеж на токарную заготовку, отдельный на фрезерование и еще один чертеж готовой фрезы с указанием углов резания и других необходимых параметров.
Заготовки для алмазных фрез поставляются на завод в виде дисков диаметром 60 мм.
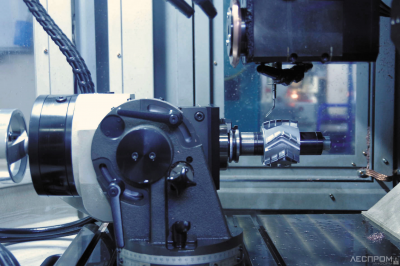
Производство алмазных фрез – многоступенчатый процесс. Токарная обработка выполняется на ЧПУ-станке, фрезерование – на пятиосевом ЧПУ-центре. Все машины работают в режиме повышенной точности, и достигается весьма достойное качество изделий. Качество токарной обработки такое высокое, что после нее изделие даже не нуждается в дополнительной шлифовке, а направляется на фрезерование, а затем на участок пайки. Процесс аналогичен изготовлению напайных HW-фрез.
После того как напаяны зубья и удалены следы пайки, фреза поступает на участок электроэрозии.
Для изготовления алмазных фрез задействовано много станков Vollmer, часть их работают у нас уже давно, но некоторые поступили на предприятие в последние месяцы. В частности, Vollmer VGrind 360, купленный у производителя в Германии, один из самых производительных агрегатов такого типа на рынке. Этот станок с генератором удвоенной мощности способен качественно и быстрее аналогичных станков обрабатывать любой профиль, и концевых профильных, и насадных профильных и прямых фрез диаметром от 3 до 20 мм.
Процесс полностью автоматизирован и не требует участия человека, за исключением внесения в компьютер изначальных параметров обработки и общего контроля за процессом. Технический уровень и производительность оборудования позволяют выпускать инструмент высокого качества сериями и крупными сериями.
Стоит обратить внимание на заточку зубьев прямой фуговальной фрезы. Это фреза нашей разработки, на которую получен патент. Ее отличает специальная форма стружкоотводящих канавок, которая улучшает обтекание зубьев набегающим потоком воздуха, меняя его с турбулентного на ламинарный и направляя стружку в сторону аспирационной системы. Зубья установлены под большим аксиальным углом (54 градуса), верхняя кромка зуба непрямая, с радиусом двойной кривизны, и при проецировании на плоскость получается идеально прямая линия. Заточить подобный профиль без применения 5-осевого станка невозможно. А VGrind очень хорошо и быстро справляется с такой задачей. Если клиенту требуется заточка на более острые углы, это мы тоже сделаем без проблем.
По факту заточки проводится операционный контроль на измерительных приборах и необходимая балансировка.
Когда продукт полностью готов, остается всего одна технологическая операция – технический контроль. Для выполнения этой функции на предприятии установлена измерительная установка компании Zoller. Причем одна из топовых версий, с возможностью лазерного измерения и создания 3D-модели инструмента с проверками абсолютно всех угловых и линейных параметров в автоматическом режиме.
По итогам проверок на паспорте изделия ставится штамп ОТК с фамилией проверяющего – и товар готов. Процесс завершен.
Производство профильных ножей
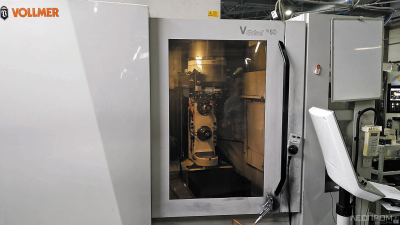
Кроме основных производственных линий, на предприятии есть несколько участков для осуществления других процессов. Один из них изготовление профильных сменных ножей. Технология производства изделий с нанесением профиля по задней грани достаточно универсальная, получила широкое распространение за счет экономической и технологической составляющих: деревообработчику не нужно держать на предприятии двадцать различных типов фрез для выпуска 20 типов продукции – достаточно одного набора голов и 20 комплектов сменных ножей! Разумеется, ножи в разы, а то и в десятки раз дешевле новых фрез.
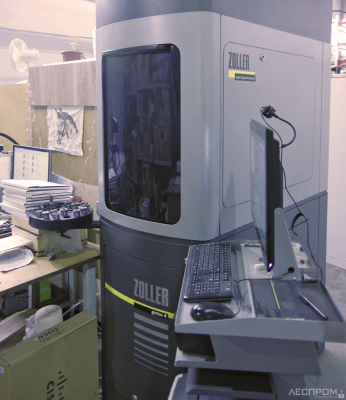
В этом процессе, как обычно, все начинается с разработки чертежей, которые после согласования с клиентом идут в работу, но для ножей мы сразу изготавливаем на специальной машине с ЧПУ высокоточный пластиковый шаблон. В автоматическом режиме. Зачем это нужно? Шаблон – это расходник, который при постоянном использовании через какое-то время вследствие скольжения по металлу неизбежно снашивается. Зачастую к нам обращаются с просьбой изготовить новый. Иногда клиенты хотят внести в профиль ножа какие-то изменения, и для этого тоже легко сделать из пластика новую болванку.
Раньше на изготовление вручную металлического шаблона у опытного заточника уходило несколько часов. А теперь, при наличии исходных данных в программе, перевыпустить шаблон – дело двух минут. Следовательно, наш заточник может через две минуты приступать к профилированию заказанных изделий по такому шаблону.
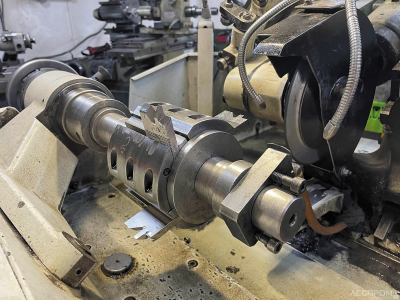
Профилирование предварительно нарезанных заготовок бланкетных ножей нужной длины выполняется по выбранному шаблону на станке Weinig Randomat. Для этого заготовка устанавливается в голову, аналогичную той, с которой потом будет работать клиент, а в идеале – в предоставленную им голову. Принцип работы станка очень похож на используемый для изготовления дубликата ключа по образцу: устанавливаются оригинал и заготовка, а потом машина по шаблону в точности повторяет профиль изделия.
Кстати о профильных ножах. Нередко клиенты считают, что достаточно установить в голову фрезы новые профильные ножи, чтобы получить полностью готовый к работе продукт. А это не совсем так. Ножи необходимо дозаточить. Ведь при ручной установке неизбежны некоторые неточности – аксиальные либо радиальные. Выставить ножи точно «в ноль», как они были изначально заточены, почти невозможно. А если проточить их после установки еще раз по шаблону, получится инструмент, который будет работать идеально, качественно и долго.
Сервис и перспективы
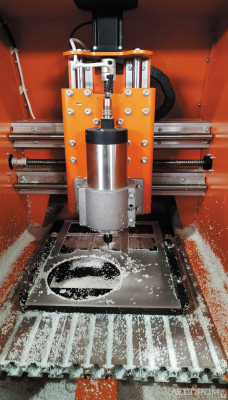
Как уже упоминалось, GT занимается не только изготовлением нового режущего инструмента. В сервисном обслуживании инструмента наших клиентов надо отметить, что мы не ограничиваемся затачиванием и ремонтом инструмента собственного изготовления, а обслуживаем изделия других производителей. С тем же качеством и тем же ответственным отношением, по тем же расценкам, что и для своих пил и фрез. Заказчикам удобнее получать все услуги в одном месте, и мы это хорошо понимаем. Нам важно сохранить уважение клиента к компании, а также к ее продукции и услугам.
Одно из новых направлений деятельности, которое мы активно развиваем последние 3–4 месяца, – производство насадных фрез с напайками из твердого сплава. Обычно все производители идут от твердого сплава к алмазу, мы пошли немного в обратную сторону, и это позволило дозагрузить мощности по оборудованию, которые бывают свободны, но, главным образом, это отклик на просьбы наших клиентов. Получать такой инструмент из-за границы сейчас становится все сложнее, играют роль цены и сроки поставки.
А для высокоскоростных линий мы освоили ряд новых продуктов, как профильных изделий, так и прямой строжки, радиусовки. Наш инструмент успешно может работать на скоростях до 150 м/мин.
Обучение
В компании действует специальная программа обучения, это добровольная помощь клиентам при сервисе инструмента. Они отправляют к нам на обучение своих заточников, это бесплатная программа.
Классическая программа занимает примерно три дня, за это время начинающие могут получить первичные навыки заточки, а имеющие определенный опыт – повысить квалификацию. Обычно мы рекомендуем два таких этапа с разрывом минимум год.
Как это делается. Мы не отрываем своих специалистов от работы для проведения формальных «лекций», а, наоборот, прикрепляем обучаемых к определенному оператору, и обучение происходит в процессе работы. Хотя мы даем и некоторые теоретические знания, поскольку есть ряд важных моментов, которые нужно понимать, прежде чем подойти к станку.
Обучаемые сначала смотрят, как выполняют работу наши сотрудники, потом им самим предоставляется возможность попробовать те или иные операции, а на третий, «выпускной», день они сами начинают работать под присмотром наставника. Работники получают знания и опыт и благодарны нам за такую возможность, как и их работодатели. Уже около 40 компаний воспользовались этой услугой. Единственное условие для участия в этой программе – компания должна быть нашим клиентом.
В нашей компании в полной мере развит институт наставничества, более опытные операторы помогают новичкам осваивать станок или группу станков, а поскольку текучка кадров у нас минимальная, люди работают подолгу, это требуется не так часто, как при освоении новых процессов и технологий в случае приобретения современного оборудования.
Тренд на бренд
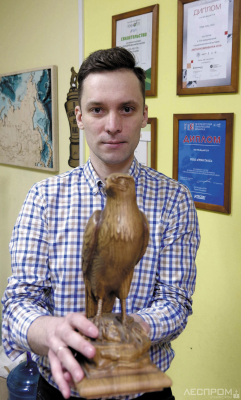
«Наши высокоточные и высококачественные станки позволяют добиваться результатов на уровне лучших европейских стандартов, например, затачивать алмазные фрезы с допуском 2–3 микрона, – с гордостью говорит бренд-менеджер Артём Озолин. – Самое дорогое в современном производстве – стоимость эксплуатации оборудования. И с нашим уровнем технологий мы ориентированы на выпуск качественного инструмента, а не бюджетного, дешевого.
Фрезы выпускаем как под заказ клиентов, так и в стандартном исполнении, по достаточно обширному каталогу. Работая с клиентом, мы не стремимся продать ему то, что у нас есть, а стараемся максимально точно понять его потребности и предложить решение существующих проблем. Поэтому понятия "стандартный" и "индивидуальный" для нас весьма размытые: технологи предприятия к каждому заказу относятся как к эксклюзивному, чтобы обеспечить качественную работу инструмента на предприятии заказчика.
Вся наша продукция брендированная – с логотипом GT, кроме того, мы заказываем специальные деревянные ящички для упаковывания фрез с вырезанными на корпусе чертежами помещаемых внутрь инструментов. То есть даже упаковке продукции уделяем большое внимание.
Качество должно проявляться во всем, тут нет мелочей. И добротно изготовленный инструмент из качественного металла, на лучших станках не должен потом болтаться в каких-то никудышных картонках. Для бланкетных ножей мы приобрели вакууматоры, и упаковываем их в пленку с помощью вакуума. Инструмент должен дойти до клиента в целости и сохранности.
Наверное, сейчас, какую заметную на российском рынке компанию ни назови, окажется, что мы с ней так или иначе пересекались, работали, работаем или собираемся работать. Причем за счет мощной технической и технологической базы наша компания не ограничивается изготовлением режущего инструмента только для деревообработки, мы можем предоставить инструмент для обработки почти любого материала, в том числе различных пластиков, цветных и черных металлов, чугуна, слоистых материалов – карбона и т. п. Под конкретную задачу мы можем разработать и изготовить фрезы любого назначения».
Сегодня и завтра
Конечно, после детального осмотра технологических участков нельзя было не поинтересоваться у директора предприятия основными производственными показателями.
«Объем производства наших спиральных фрез составляет около 30 000 единиц в год, постоянно растут продажи алмазного инструмента: в 2018 году – 500 единиц, в 2019-м – 1500, в 2020-м – 2000, в 2021-м – 2500. Для нашего рынка это, пожалуй, немного, но, как вы можете судить, мы не останавливаемся на достигнутом.
Что касается дисковых пил, продаем их примерно 3000 штук в год, – рассказал Дмитрий Соколов. – Потенциал предприятия значительно выше, и мы готовы удовлетворить все потребности наших действующих и потенциальных заказчиков. Начали работать с маркет-плейсами, продукция успешно продается на Ozon.
В 2022 году при поддержке Фонда содействия инновациям станочный парк предприятия пополнится еще несколькими единицами оборудования, запуск которых поможет вывести производство на новый уровень. Ожидается поставка трех новых машин, в том числе для лазерной резки алмазных зубьев, которая сейчас осуществляется методом электроэрозии. Лазер действует в сто раз быстрее, мы сможем существенно повысить производительность и точность процесса, вместе с тем понизив себестоимость.
География поставок инструмента – вся страна. Если конкретнее, то по алмазному инструменту это по большей части Центральная Россия, Поволжье, где сосредоточено огромное количество мебельных предприятий с новым современным оборудованием, для которого требуется инструмент соответствующего уровня. Но, разумеется, есть клиенты и в Северо-Западном регионе, Сибири, на Дальнем Востоке.
Так исторически сложилось, что наши спиральные фрезы больше реализуются локально, из Петербурга. Недавно развиваемое направление по изготовлению инструмента для строжки ориентировано в основном на рынок Карелии – такая вот региональная особенность. Постепенно будем продвигать дальше.
А дисковые пилы представлены очень широко во всех регионах, где занимаются деревообработкой.
GT имеет представительства в других городах, что позволяет компании максимально приблизиться к заказчику. Представители GT знают специфику своего региона и потребности предприятий, готовы проконсультировать и продемонстрировать инструмент, оказать оперативную поддержку и сервисные услуги и в самые короткие сроки организовать доставку продукции в любую точку России и ближнего зарубежья.
Что касается планов на будущее, их очень много. Будем и дальше внедрять принципы Индустрии 4.0, наращивая автоматизацию и цифровизацию процессов. Будем продвигать отечественный продукт, снижать себестоимость с сохранением качества, чтобы стать более конкурентоспособными. Будем осваивать новые виды продукции для новых видов применения. Мы высоко ценим своих партнеров и заказчиков за их доверие, и, уверен, совместными усилиями внесем весомый вклад в развитие отечественной промышленности!»
Текст и фото Максим Пирус