Шпон и фанера как сырье для предприятий малого бизнеса
Производство шпона, кроме пиленого, не под силу малому бизнесу, поскольку требует дорогостоящего оборудования – это лущильный либо строгальный станок, оборудование для проварки или пропарки сырья, сушильные камеры, многоэтажный горячий пресс и др. А вот выпуск готовых изделий на основе шпона и фанеры, а также переработка отходов этих материалов могут стать серьезным источником доходов для активных предпринимателей.
Напомним, шпон – тонкие листы древесины, которые могут быть получены тремя способами: лущением, строганием и пилением. Этот материал активно используется в производстве разнообразной продукции и востребован на рынке.
Продукция из древесного шпона
Лущеный шпон (чаще березовый, толщиной 1–2 мм) используется в основном для производства фанеры. Строганый шпон толщиной 0,6–1,0 мм из древесины твердолиственных пород предназначен для облицовывания мебельных щитов, филенчатых дверей и других декоративных работ. Пиленый шпон толщиной до 6 мм применяется в качестве верхних планок паркетных досок или как облицовочный материал.
Сегодня для производства одного из самых распространенных древесных материалов – ламинированных древесно-стружечных плит (ЛДСП) широко используется так называемый синтетический шпон – пропитанная синтетической смолой текстурная бумага.
В производстве фанеры доля сухого кускового лущеного шпона составляет примерно 10–15% общего объема шпона. Его склеивают в форматные листы для среднего слоя фанеры или поставляют на рынок как товарную продукцию.
Наиболее распространенные изделия из этого полуфабриката – плоскоклееные или гнутоклееные детали мебели (рис. 1). Технические требования к таким заготовкам устанавливает ГОСТ 21178.
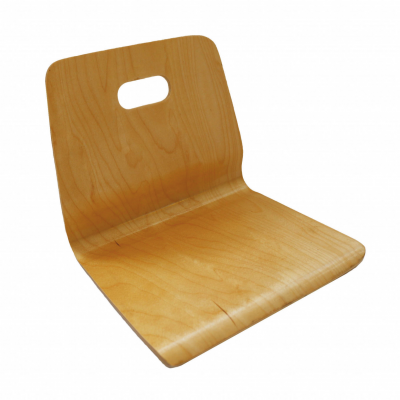
Подобные детали мебели изготавливаются в следующем порядке.
Из пакета шпона рабочий подбирает на столе пачки шпона примерно одной ширины для прирубки на заданную черновую длину на станке поперечной резки шпона. При изготовлении узких деталей для торцовки пачек шпона используют настольный торцовочный станок с шириной пиления до 300 мм.
После формирования заготовок черновой ширины на средние листы заготовок наносится клей. Сборка пакетов выполняется на столе пресса. После выдержки клееные заготовки проходят послепрессовую обработку для получения готовой детали. На ленточно-пильном станке заготовка опиливается по контуру, на фрезерном станке выполняется по копиру чистовое фрезерование, а на сверлильном станке делаются требуемые отверстия и пазы.
Для создания цеха по обработке кускового лущеного шпона необходимо следующее оборудование.
1. Для поперечной резки пачек шпона используются специальные гильотинные ножницы, например QFS 850 немецкой фирмы Kuper (рис. 2). Пачка шпона укладывается на стол станка, фиксируется прижимной балкой и обрезается в размер при вертикальном движении ножа. Длина реза определяется по двум параллельным измерительным линейкам, закрепленным на рабочем столе.
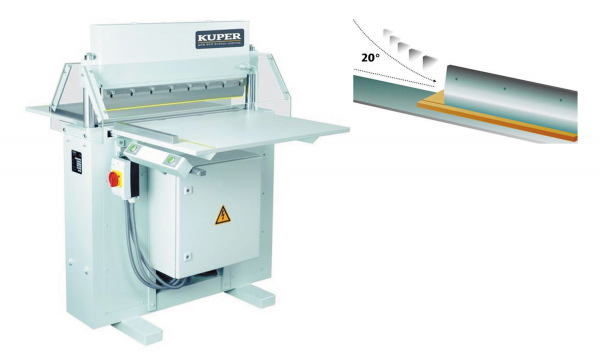
Направление реза поперечное, ширина реза до 850 мм;
макс. толщина пачки 60 мм;
общая мощность 3,5 кВт;
габаритные размеры 1,12 х 0,6 м
2. Для продольного пиления пачек шпона предназначены специальные станки, но они слишком тяжелые и дорогостоящие для малого производства. При длине черновых заготовок до 800 мм используют тот же станок Kuper. Для более длинных заготовок можно приспособить ручную электропилу с направляющей шиной требуемой длины.
3. Для нанесения клея на узкие, до 300 мм, заготовки подойдет вальцовый станок КН-3 (рис. 3), а на более широкие шпоновые заготовки – станок Ш2В. Наиболее широко сегодня используются клеи ПВА.
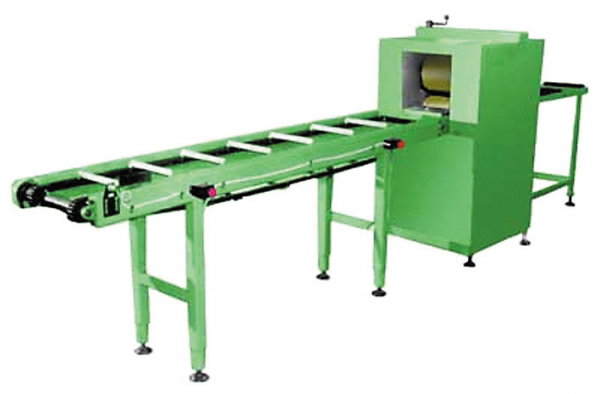
Скорость подачи заготовок 24,2 м/мин;
ширина клеенаносящих роликов 300 мм;
диаметр наносящих роликов 165 мм;
мощность электродвигателей 1,1 кВт
4. Для склеивания используется вакуумный пресс (рис. 4). Это головное оборудование цеха представляет собой конструкцию со столешницей над герметичной коробкой. Сверху установлена откидная рамка с эластичной пленкой. В столешнице сделаны отверстия, а коробка через патрубок связана с системой отсоса воздуха.
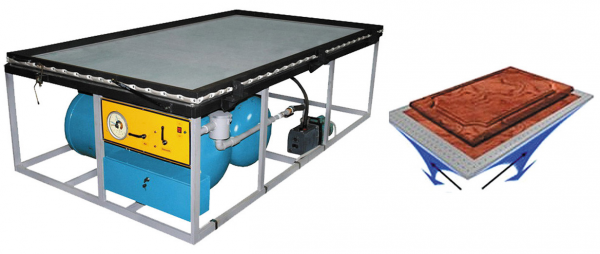
Мощность системы 1,5 кВт;
давление прессования 0,1 МПа;
габариты 3400 х 1550 х 1050 мм
Склеивать в прессе можно как плоскоклееные, так и гнутоклееные заготовки, например гнутые мебельные фасады. Для гнутоклееных заготовок нужна матрица (шаблон), повторяющая контуры детали.
Верхняя рамка опускается и герметично фиксируется над столешницей. После включения вакуумного насоса под пленкой создается разряжение и она плотно прижимается к шаблону, обеспечивая заданную форму будущего изделия. Пленка играет роль пуансона, а усилие прижима обеспечивается перепадом давления снаружи и внутри пресса.
Вакуумные прессы также широко применяются для облицовывания шпоном или синтетическими пленками мебельных щитов, в том числе с фрезерованным декоративным рисунком.
Предприниматели часто приобретают только вакуум-насос, а все остальное изготавливают собственными силами. В качестве пленки используют обычную пленку ПВХ или силиконовую.
В зависимости от вида профиля гнутоклееных заготовок расход сухого шпона на 1 м3 составляет 2–3 м3, жидкого клея – примерно 120 кг/м3. Для деталей глубокого профиля можно использовать устройство с шаблоном и гибкой лентой (рис. 5), в которых при движении пуансона вниз проклеенные полосы шпона плотно прижимаются к шаблону.
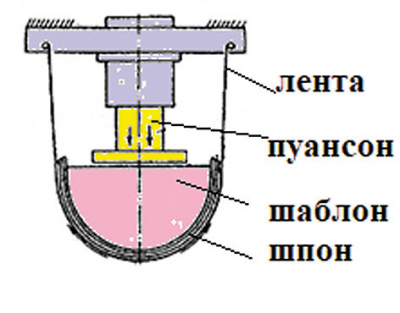
5. Для механической обработки клееных деталей используется сначала ленточно-пильный столярный станок, например, марки ЛС-40, на котором выполняется черновая опиловка заготовок. Чистовое фрезерование осуществляется концевыми фрезами на фрезерном столе или насадными фрезами на промышленных фрезерных станках – российском Ф-4 или импортных производства EcoWood (рис. 6), Ostermann и др.
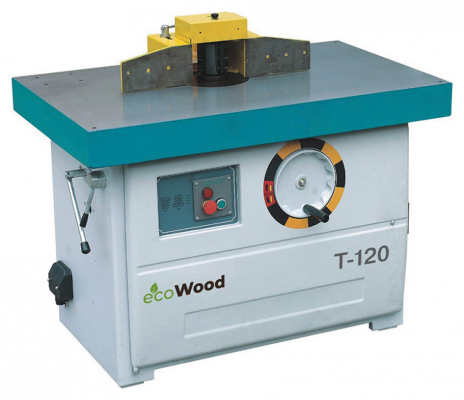
Рабочая высота 120 мм; мощность 4 кВт; вес 325 кг
6. Для вторичной механической обработки заготовок, то есть сверления отверстий и выборки пазов в деталях, используется сверлильно-пазовальный станок, например российский СВПГ или LBM компании Robland (рис. 7).
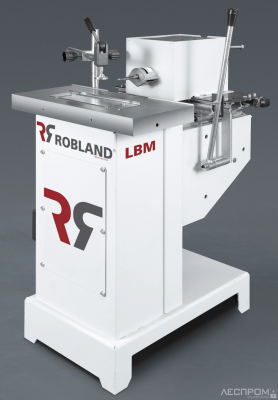
Размеры стола 600 x 300 мм; частота вращения шпинделя 3000 об/ мин;
мощность двигателя 2,2 кВт;
габариты станка 860 x 600 x 1100 мм;
вес 150 кг
Помимо основных станков, потребуются межстаночные связи (приемные и подающие столы), заточное оборудование, стружкоотсос. Затраты на оборудование не превысят 2,7 млн рублей.
Производительность цеха будет определяться производительностью головного оборудования – вакуумного пресса. При цикле прессования 30 мин и объеме загрузки 10 деталей производительность составит 20 деталей в час.
Мебельные изделия из фанеры
Фанера считается лучшим древесным материалом, превосходящим по свойствам не только прочие древесные плиты, но и массивную древесину. За счет взаимно перекрестного направления волокон в смежных слоях шпона и упрессовки в горячем прессе получается материал более прочный и изотропный, в сравнении с исходным сырьем.
Применение фанеры для изготовления изделий мебели дает определенные преимущества по сравнению с использованием пиломатериалов (массивной древесины):
- Толщина деталей может быть в 1,5–2 раза меньше.
- Раскрой плит большого формата позволяет найти оптимальную схему раскроя материала на заготовки при минимальных потерях древесины. 3. Не требуется вырезка дефектов.
- Из листов фанеры легко выпиливаются широкие заготовки любой формы.
- Шлифованные лицевые поверхности фанеры упрощают подготовку деталей к отделке.
В России много предприятий, производящих фанеру, и это не дефицитный материал. Толщина листов составляет от 3 до 40 мм, стандартные размеры квадратных листов – 1220, 1525, 1800, 2440, 2500 мм. Выпускается также фанера с соотношением сторон 1:2 (например, 1220 х 2440 мм). Кроме полноформатных листов, на рынке можно найти фанеру малых форматов (переобрез), которая значительно дешевле.
По качеству фанера подразделяется на четыре сорта, при этом сорт каждого листа обозначается дробью, например, 3/4 означает, что лицевой слой 3-го сорта, а оборотный слой – 4-го сорта. Основная используемая порода – береза, встречается также хвойная фанера (наружные слои из соснового шпона). Основные марки фанеры следующие: ФК – на карбамидных клеях, для использования в помещении и ФСФ – на фенольных клеях, для наружного использования.
Для мебельных щитовых деталей подойдет фанера толщиной 10–20 мм, для задней стенки тумб и шкафов можно использовать тонкую фанеру, 3–4 мм (рис. 8). При толщине меньше 16 мм соединения деталей на шкантах или евровинтах (конфирматах) представляет сложность, лучше использовать другие типы, например на прямых шипах либо шипах «ласточкин хвост».
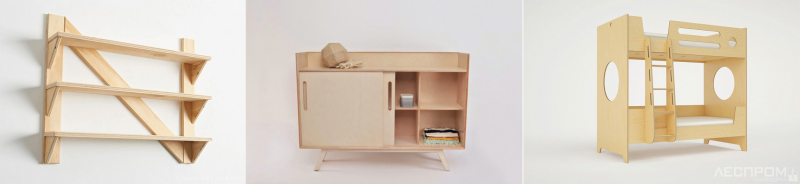
Для фанеры низших сортов (4/4) характерно наличие сучков или заплаток, поэтому рентабельнее приобретать фанеру более высоких сортов. К недостаткам наиболее распространенной березовой фанеры следует отнести нечеткий текстурный рисунок.
Технологический процесс состоит из следующих операций. С подстопного места листы фанеры подаются на стол универсального круглопильного станка для раскроя на черновые заготовки. Для дополнительного раскроя на криволинейные заготовки возможно использование ленточно-пильного станка. Чистовое фрезерование, получение фигурных деталей и профильных кромок выполняется на фрезерном станке с нижним шпинделем. При установке шипорезной каретки с его помощью можно формировать шипы и проушины для столярных соединений. Присадочные работы осуществляются на многошпиндельном сверлильном станке, а выборка пазов – на пазовальном. Для шлифования мелких деталей подходит тарельчато-ленточный станок, а для крупных щитовых – ленточный шлифовальный. На участке отделки необходим поворотный стол для нанесения на детали лакокрасочных материалов методом распыления и стеллажи для сушки покрытий. Сборка изделий выполняется на столярных столах.
Для создания мебельного цеха требуется следующее оборудование:
- Для раскроя листов фанеры на черновые заготовки необходим универсальный круглопильный станок (типа Ц-6) с параллельной направляющей и перпендикулярным упором для выполнения продольных и перпендикулярных резов. Скошенные кромки выполняются на станке с наклоняемым пильным диском, например, станке Ostermann S2.
- Для получения непрямолинейных заготовок служит ленточно-пильный столярный станок ЛС-40 (Кировский станкостроительный завод) или станок с наклонным столом Ostermann BS 40.
- Для фрезерных работ рекомендуется отечественный станок широкого профиля ФСШ-1АК или импортный EcoWood T100 без шипорезной каретки. В простейшем варианте все фрезерные работы можно выполнять на фрезерном столе с погружным фрезером.
- Для сверления нескольких отверстий за одну установку заготовки используются присадочные станки, например Ostermann 21. Как минимум достаточно электродрели с набором сверл и шаблонов.
- Пазы формируются на специальном сверлильно-пазовальном станке типа СВПГ или на фрезерном столе, за несколько проходов пазовальной фрезой.
- Для шлифовальных работ желательны два станка: тарельчато-ленточный, например, Holzmann BT46 (рис. 9), – для малых деталей, ленточный плоскошлифовальный типа ШлПС-6РМ Кировского станкостроительного завода (рис. 10) – для сравнительно больших щитовых деталей.
- Для отделки деталей оптимально нанесение ЛКМ с помощью пневматического краскораспылителя, например, компании Wagner (рис. 11).
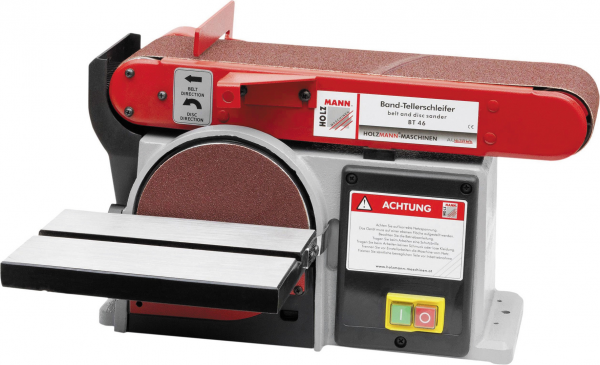
Мощность двигателя 250 Вт;
частота вращения 90 об/мин;
размер стола 150 x 230 мм;
диаметр шлиф. круга 150 мм;
масса брутто 19 кг
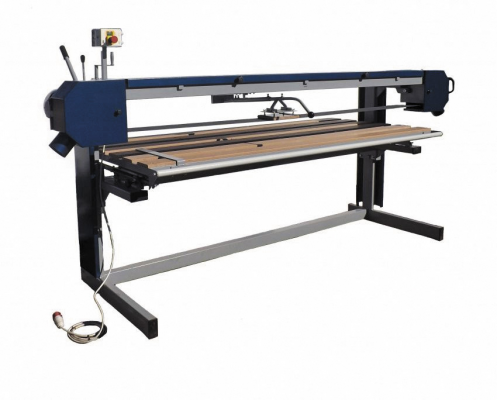
Длина стола 2400 мм;
ширина стола 1000 мм;
общая мощность 3 кВт;
вес 360 кг
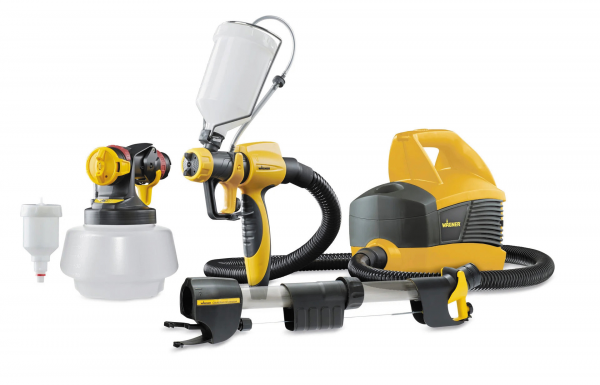
Flexio Extra Kit Мощность 630 Вт;
производительность 0,4 л/мин;
вес нетто 3,3 кг;
емкость бака 1,8 л
Распылитель предназначен для нанесения ЛКМ на водной основе и оснащен встроенным регулятором ширины факела.
Ориентировочная стоимость комплекта нового основного и вспомогательного оборудования (межстаночные связи, столы, заточной станок, стружкоотсос, стеллаж для сушки деталей после отделки) составляет 2 млн рублей.
Текст Владимир Волынский