Новое = хорошо забытое старое
Пора задействовать отечественные разработки и технологии
Введение санкций вызвало в России серьезные проблемы с экспортом продукции ЛПК и импортом оборудования и технологий, поэтому резонно обратиться к отечественным технологиям, которые нередко превосходят аналогичные зарубежные и по техническим показателям, и по стоимости.
К огромному сожалению, в течение 30 лет после развала СССР такие разработки не желали финансировать ни государство, ни бизнес. Но сейчас, как говорится, жареный петух клюнул и, вроде бы, появилась надежда, что наконец-то обратят внимание и на отечественные технологии. В их числе разработки московского регионального отделения Международной академии наук экологии и безопасности жизнедеятельности (МАНЭБ).
Задачи, которые нужно решать
В лесной отрасли усугубляется проблема очистки леса от пораженных короедом, поваленных и обгорелых деревьев. Нередко такие участки находятся в зоне защитных лесов, где возможны только санитарные рубки. А ведь подобные лесные ресурсы можно и нужно эффективно использовать.
Это соображение, а также законодательно закрепленная необходимость утилизировать древесные отходы предприятий ЛПК подсказали в качестве выхода производство топливных гранул (пеллет). Однако в России ввиду огромных запасов природного газа и его относительной дешевизны использование древесных пеллет ограничено индивидуальными потребителями и котельными малой мощности в удаленных от газопроводов районах.
Поскольку Европа взяла курс на использование биотоплива и возобновляемые источники энергии, логичным вариантом реализации пеллет стал экспорт. Основные поставщики пеллет в Европу – это США и Канада. У России есть ряд преимуществ по логистике и затратам перед странами Северной Америки, однако, как ни парадоксально, американские гранулы, доставляемые в ЕС за десятки тысяч километров, были и остаются дешевле российских.
Разработка технологии производства пеллет, стоимость которых ниже, чем американских аналогов, стала главной задачей инвестиционного проекта. Для этого предполагалось выпускать пеллеты повышенной калорийности из древесных отходов после санитарной очистки леса.
Цели проекта:
- Разработка, изготовление и опытно-промышленная эксплуатация пеллетного завода по переработке отходов лесопользования производственной годовой мощностью 30 тыс. т древесно-угольных пеллет с повышенной теплотворной способностью 23,0 МДж/ кг (5000 ккал/кг).
- Изготовление и продажа оборудования древесно-угольных пеллетных заводов для переработки древесных отходов при очистке охранных лесов Центрального и Северо-Западного района Российской Федерации.
- Организация производства и экспорта древесно-угольных пеллет в страны Европейского союза.
Реализация проекта в Центральном и Северо-Западном регионах обусловлена прежде всего их близостью к Балтийскому морю. Использование сырья от санитарных рубок леса для производства пеллет не позволяет организовывать крупные заводы. Оптимально строительство пеллетных заводов производственной мощностью 30 тыс. т в год при радиусе очистки леса от больных, поваленных и обгорелых деревьев 50 км.
Предложенная технологическая схема пеллетного завода предусматривает следующие технологические операции:
- санитарную рубку пораженных короедом, упавших и обгорелых деревьев, обработку древесной массы и разделение ее на деловую древесину и порубочные отходы, переработку порубочных отходов в древесную щепу;
- вывоз из леса деловой древесины и древесной щепы на промышленную площадку пеллетного завода;
- использование деловой древесины для производства древесно-строительной продукции и складирование опилок для производства потребительских древесных пеллет – для отопления индивидуальных домов;
- складирование древесной щепы из отходов санитарной рубки леса;
- пиролизную обработку древесной щепы с получением мелкофракционного древесного угля, жидкого топлива, электрической и тепловой энергии;
- подготовку сырья для производства древесно-угольных пеллет путем смешивания древесной щепы и мелкофракционного древесного угля с последующим их совместным помолом для получения древесно-угольной смеси фракцией 0–2 мм;
- изготовление древесно-угольных пеллет;
- изготовление светлых древесных потребительских пеллет.
Развитие проекта
Апробацию на уровне экспериментальных исследований прошли следующие элементы:
- пиролизный реактор в составе экспериментальной пиролизной установки, г. Москва, ООО «Фирма «РОСТ-Л», 2010 год;
- устройство гидравлической очистки отходящих газов топочного устройства, г. Люберцы, Московская обл., ООО «Фирма РОСТ-Л», 2001–2005 годы;
- пеллетная установка Evol 500 (Польша) на лесозаводе ИП «Егошин И. И.», пос. Виноградово, Московская обл., 2013 год.
В 2015–2017 годах были запланированы следующие работы:
- Строительство и опытно-промышленная эксплуатация первой очереди пеллетного завода производственной мощностью 6000 т в год для отработки технологических и экономических параметров производства с целью строительства второй очереди производственной мощностью 30 тыс. т в год.
- Строительство и опытно-промышленная эксплуатация второй очереди завода древесно-угольных пеллет (2016–2017) для организации производства и продажи на российском и мировом рынке комплектного оборудования пеллетных заводов.
- Организация санитарной рубки леса в Московской области с последующим производством древесно-угольных пеллет для реализации на российском и зарубежных рынках.
- Проведение исследований и организация производства жидкого биодизельного топлива из древесных отходов.
Результаты
Древесно-угольные пеллеты относятся к возобновляемым источникам энергии.
По стоимостным и потребительским свойствам древесно-угольные пеллеты, изготавливаемые в автоматизированных пиролизных установках, призваны заменить в системах отопления индивидуальных домов ископаемый уголь, дизельное топливо, сжиженный газ, электроэнергию.
Кроме того, они могут заменить древесные пеллеты. Если калорийность древесных пеллет 4300 ккал/ кг, то древесно-угольных – больше 5000 ккал/кг, то есть на 20% выше, поэтому следует ожидать повышенного спроса на них. Высокая рентабельность производства древесно-угольных пеллет связана еще и относительно низкой стоимостью логистики.
Кроме экономической выгоды эксплуатации пиролизных установок, следует учитывать экологическую выгоду от очистки леса от погибших деревьев. В стоимостном выражении экономическую выгоду от очистки леса учесть не представляется возможным.
В чем уникальность производственного оборудования?
Пиролизная установка работает в автономном режиме, без задействования внешних источников тепловой и электрической энергии. Для обслуживания пиролизной установки требуется всего пять человек в смену.
Вместо цикличного ручного углевыжигания используется автоматизированное получение древесного угля в пиролизном реакторе нового типа. Сушка опилок и щепы осуществляется за счет тепловой энергии отходящих газов при нагреве пиролизного реактора. Для низкотемпературного пиролиза высушенных древесных отходов используется тепло от сжигания пиролизной жидкости в термическом генераторе и тепло отходящих горячих газов газомоторного электроагрегата. Электроэнергия для нужд производства вырабатывается за счет использования в газомоторном и дизельных электроагрегатах высококалорийного пиролизного газа и светлой пиролизной жидкости.
Прочность и сохранение формы древесно-угольных пеллет достигаются оптимальными температурой нагрева и давлением прессования смеси измельченных опилок и древесного угля. При производстве возможна добавка клеящих веществ.
При производства 3000 т древесно-угольных пеллет расход древесных опилок составляет 70% объема пеллет, или 2100 т в год, а расход древесного угля – 30% объема пеллет, или 900 т в год.
В настоящее время использование древесных отходов для производства новых полезных продуктов весьма актуальная задача. В леспромхозах при переработке древесины отходы составляют до 50%. Правительство Московской области выделяло на очистку подмосковного леса немалые суммы. Переработка бросового сырья может обеспечить большой экономический и экологический эффект.
Блок-схема производства древесно-угольных пеллет
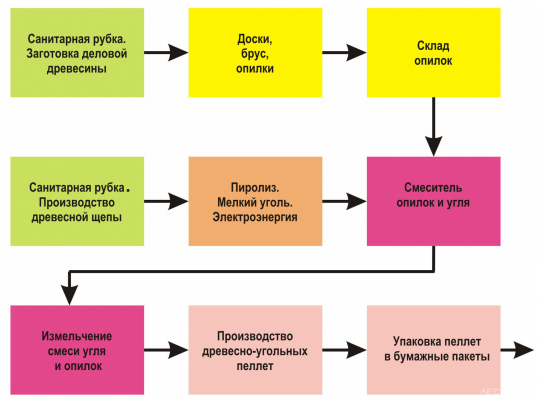
На участке, выделенном для санитарной рубки леса, заготавливают деловую древесину и древесные отходы – тонкомеры, комли, вершинки, толстые сучья. Длинномерную деловую древесину грузят на автомашину, оснащенную гидравлическим подъемником, и доставляют на лесозавод для производства досок, бруса, реек и другой товарной продукции из дерева. Образовавшиеся при этом опилки направляют в цех производства древесно-угольных пеллет.
С делянки древесные отходы самосвалами вывозят на лесозавод для производства древесной щепы. Как вариант близ дорог из древесных отходов получают щепу размером 0–12 мм с помощью тракторных щепорезов марки WCH, которые соединяют с тракторным валом отбора мощности. Ножи приводятся во вращение двигателем трактора. Такая версия удобна для использования в труднодоступных районах. Для опытно-промышленной проверки технологии заготовки леса выбраны щепорезы тракторные WCH250TP с диаметром загрузки 250 мм.
При производительности 10 м3/ч с помощью одного щепореза можно заготовить 30 тыс. т древесной щепы в год. Древесные отходы или щепу фракции 0–12 мм загружают в щеповоз и доставляют на склад пиролизного завода для естественной сушки под навесом. Со склада древесную щепу с помощью скребковых конвейеров транспортируют на линию загрузки пиролизных реакторов.
На производственной площадке монтируется пиролизная установка для переработки древесной щепы в древесный уголь. Из каждой тонны древесной щепы в результате термохимического разложения образуется 250 кг мелкофракционного древесного угля. После охлаждения с помощью шнекового конвейера уголь транспортируют в лопастной смеситель, куда одновременно подают опилки или щепу. Смесь опилок и древесного угля измельчают до фракции 0–2 мм и после сушки до оптимальной влажности направляют в приемный бункер пеллетной установки. За счет давления и температуры 100°С в матрице пеллетной установки формируются древесно-угольные пеллеты повышенной калорийности. Шнековый конвейер подает их в бункер для охлаждения. Затем пеллеты поступают на линию расфасовки.
Приготовление древесного угля
Для производства древесно-угольных пеллет требуется мелкофракционный древесный уголь, получаемый из щепы на пиролизной установке конструкции ООО «РОСТ-Л» (рис. 2).
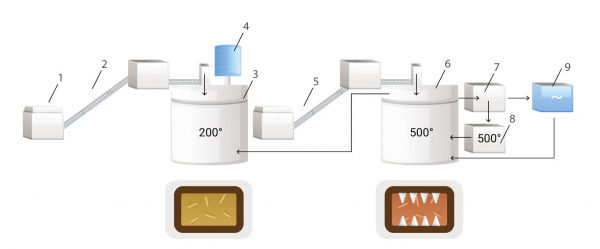
Для получения 900 т древесного угля необходимо термически обработать 3600 т древесной щепы. Щепу загружают в бункер щепы с подвижным основанием, вместимость которого должна соответствовать суточной производительности пиролизной установки – 100 м3. Из бункера щепу транспортируют по наклонному шнековому конвейеру в камеру сушки пиролизной установки (овальной формы, площадь сечения 2,65 м2, высота 3 м – так достигается большой объем камеры – 8 м3 с минимальным расстоянием внутреннего слоя щепы от металлической стенки корпуса). Сушка происходит за счет пропускания сквозь слой щепы бескислородных газов, нагретых до 400°С, на выходе их температура 200°С. Интенсификация сушки обеспечивается за счет активации отходов ворошителями.
Корпус камеры сушки, изготовленный из нержавеющей стали, помещается в теплоизолированную оболочку из красного кирпича. Камера оборудована устройством очистки и утилизации тепла отходящих в атмосферу газов.
Высушенная и термически обработанная щепа при температуре не ниже 200°С непрерывно подается по наклонному шнековому конвейеру во внутреннюю полость пиролизного реактора. Сухие отходы нагреваются до температуры 400–450°С за счет контакта с горячими металлическими стенками реактора, выполненными из термостойкой стали. Для интенсификации пиролиза используются вращающиеся лопасти двух активаторов, которые расположены на верхней крышке камеры, по краям корпуса пиролизного реактора.
К внутренней поверхности реактора приварены продольные призмы с отверстиями, через которые пиролизный газ из нижней зоны поступает в коллектор. Металлический корпус пиролизного реактора помещен в наружную теплоизолированную камеру. В полость между ними подаются горячие бескислородные газы.
В блоке охлаждения и сепарации пиролизный пар охлаждается и разделяется на синтетическое жидкое топливо и сухой пиролизный газ. Из одной тонны древесной щепы можно получить 200 кг пиролизной жидкости и 350 кг пиролизного газа.
Часть жидкого топлива сжигают в термическом генераторе с образованием бескислородных газов, нагретых до 500°С. Пиролизный газ поступает в газомоторную мини-ТЭЦ для выработки электрической и тепловой энергии. Выхлопные газы газомоторного электроагрегата (500°С) подаются в полость между внешней оболочкой и пиролизной камерой.
В блоке охлаждения и сепарации образовавшийся в пиролизном реакторе жидкогазовый пиролизный пар охлаждается и разделяется на синтетическое жидкое топливо и сухой пиролизный газ. Блок охлаждения и сепарации пиролизного пара состоит из трех последовательно установленных осадительных камер, с помощью которых выделяют три вида пиролизной жидкости (рис. 3).
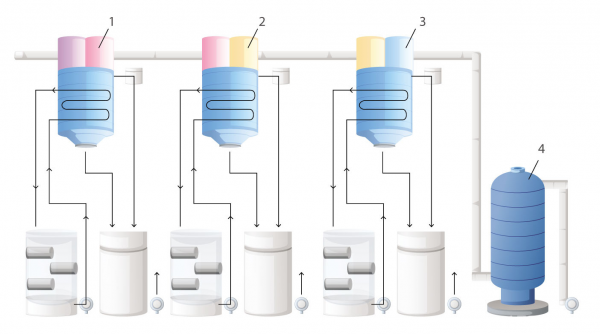
В первой камере при 280–350°С из пиролизных паров выделяется тяжелая фракция пиролизной жидкости (мазут), во второй камере при 210–280°С – средняя фракция пиролизной жидкости (керосин), а в третьей камере при 140–210°С – легкая фракция пиролизной жидкости (бензин). Пиролизные пары тяжелой фракции (150 т) поступают в генератор тепловой энергии, обеспечивающий подачу в нагревательную камеру горячих, 400–450°С, бескислородных газов. При этом генератор тепловой энергии одновременно с источником тепловой энергии используется в качестве фильтра для улавливания твердых частичек и сажи, загрязняющих пиролизную жидкость.
Среднюю и легкую фракции пиролизной жидкости заливают в цистерны и используют в качестве топлива для дизельной электростанции, которая снабжает пиролизный завод электроэнергией. Также их можно продавать в качестве печного топлива по цене 10 руб./л. После определенной обработки из легкой и средней фракции пиролизной жидкости можно получить моторное топливо Евро 4 для реализации. Отделенный от пиролизной жидкости пиролизный газ поступает в газгольдер, где охлаждается до 40°С и освобождается от влаги, после чего направляется в газомоторный электроагрегат для выработки электрической энергии. В результате термохимической обработки 3600 т древесной щепы образуется 1,26 млн м3 пиролизного газа. При калорийности пиролизного газа 23 МДж/ м3 и расходе 60 м3 на 100 кВт·ч мощности может быть получено 2 млн кВт·ч электрической энергии. Горячие выхлопные газы поступают в кирпичную камеру для дополнительного нагрева металлических корпусов пиролизного реактора.
Технологическая схема сепарации пиролизного пара почти не отличается от схемы сепарации нефти при получении бензина, керосина, мазута и может стать основой новой технологии переработки нефти с производством бензина, керосина, мазута, которая будет значительно дешевле применяемой сейчас на нефтеперерабатывающих заводах.
Древесный уголь, образующийся в реакторе, выгружается из камеры пиролиза с помощью шнекового конвейера с водяной рубашкой, после охлаждения смешивается с опилками и используется для производства древесно-угольных пеллет.
Наряду с мелкофракционным углем можно получать кусковой древесный уголь. Для этого входная и выходная задвижки специального пиролизного реактора выполняются диаметром 300 мм, а на загрузочном узле устанавливается решетка с ячейкой 100 х 100 мм. Кусковой древесный уголь упаковывается в пакеты по 5 кг. Отсев угля фракции менее 20 мм направляется в смеситель и используется для производства древесно-угольных пеллет.
Производство пеллет с использованием гранулятора EVOL
Опилки и древесный уголь измельчали до фракции 0–2 мм с помощью электрической дробилки SG 40 (производство Китай–Германия) с циклоном молоткового типа подходят для переработки щепы, опилок, стружки.
Подготовленная в определенной пропорции смесь опилок и древесного угля с помощью шнекового питателя загружается в приемный бункер пеллетной установки, откуда по наклонному шнековому конвейеру поступает в камеру дополнительного помола. Затем смесь под давлением заполняет ячейки матрицы, нагревается до 100°С и выдавливается в виде гранул – пеллет (рис. 4).
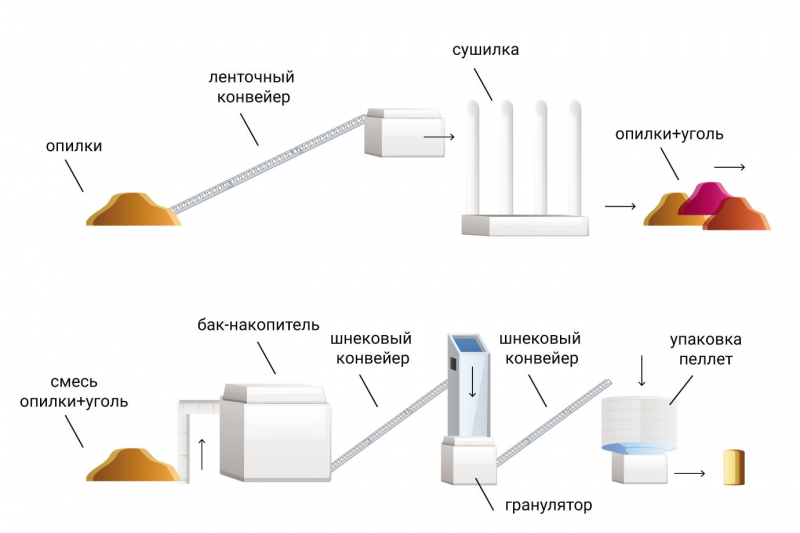
В грануляторе Evol 500 матрица с длиной ячеек 38 мм.
ООО «РОСТ-Л» совместно с ИП «Егошин И. И.» провели эксперимент по получению древесно-угольных пеллет из смеси опилок и древесного угля в соотношении 2:1 по массе.
Сырые опилки от деревообрабатывающих линий складировали на бетонном полу в цехе производства пеллет. Рабочие вручную насыпали опилки на ленточный конвейер, по которому они поступали в дробилку, а затем в пневматическую сушилку с подогревом за счет сжигания обрезков древесины. Высушенные опилки выгружались через пылеуловитель на бетонный пол.
Отсев древесного угля (три мешка) от углевыжигательного комплекса, принадлежащего сторонней коммерческой фирме, после измельчения в дробилке и сушки сложили рядом с сухими опилками.
Опилки и древесный уголь в пропорции 2:1 смешивали вручную, лопатой. Такой способ получения смеси не оптимален из-за пыления угля при дроблении и неравномерного перемешивания.
Смесь измельченного древесного угля (33% по массе) и древесных опилок (64% по массе) загружали в смесительный бак с помощью всасывающего шланга – продуктопровода. Общий объем смеси составил 35 пластмассовых ведер вместимостью 30 л, то есть 1050 л, или примерно 1 м3.
Из смесительного бака древесно-угольная смесь с помощью шнекового конвейера поступала в гранулятор, где измельченные опилки склеивались за счет нагревания содержащегося в них лигнина и древесно-угольная смесь спрессовывалась в ячейках.
Поначалу, при низкой температуре, удалось получить черные пеллеты требуемого качества. Однако после нагрева матрицы гранулятора выше 100°С пеллеты длиной 38 мм стали разрушаться. Эксперимент был остановлен, поскольку необходимо было заменить матрицу другой, с длиной ячеек 15 мм.
Сжигание древесно-угольных пеллет в пеллетном котле
Для определения потребительского эффекта древесно-угольных пеллет их сжигали в пеллетном котле, оборудованном системой автоматического сжигания с дистанционным управлением в пос. Белоозерский Московской области. Пеллетный котел обеспечивал теплом коттедж площадью 200 м2. Эффект оценивался по скорости нагрева воды в системе отопления. Если при сжигании в котле древесных пеллет температура в системе отопления коттеджа достигала 60°С за 20 минут, то при использовании древесно-угольных пеллет – за 10 минут.
Предварительные результаты применения древесно-угольных пеллет показали возможность создания новой технологии и оборудования для массового использования в системах отопления индивидуальных жилых домов. Кроме того, древесно-угольные пеллеты могут служить топливом для малых котельных жилищно-коммунальных хозяйств и небольших производственных фирм.
При этом возможна полная автоматизация системы отопления, без постоянного дежурства и диспетчерского контроля.
Новые потребительские свойства продукции
Древесно-угольные пеллеты производятся из древесных опилок и древесного угля. В качестве сырья для получения древесного угля используется низкосортная древесина и древесные отходы, что исключает затраты на окорку. По калорийности древесно-угольные пеллеты на 20% превосходят древесные, поэтому при переходе на них возможно снижение затрат на логистику и увеличение объемов экспорта. При совершенствовании технологии производства и применении клеящих веществ, например 5% молотой кукурузы, содержание древесного угля в составе пеллет может быть увеличено. В результате калорийность древесно-угольных пеллет повысится до 6000 ккал/кг, следовательно, стоимость их перевозки снизится в 1,5 раза.
Повышение калорийности древесно-угольных пеллет позволит продлить период использования объема разовой загрузки бункера пеллетного котла, что существенно повысит удобство его эксплуатации.
Автор выражает благодарность президенту МАНЭБ, профессору, д. т. н. Г. М. Золотареву за консультации при подготовке статьи.
Текст Сергей Передерий