Искать пути оптимизации производства сейчас особенно важно
Павловский ДОК реализовал метановый проект
Прошло четыре года, с тех пор как журналисту «ЛесПромИнформ» довелось побывать на одном из ведущих предприятий холдинга «Алтайлес» – Павловском ДОКе и детально ознакомиться с технологией изготовления MDF на самом современном оборудовании*. Жизнь не стоит на месте, производство постоянно совершенствуется и модернизируется, и за несколько лет на комбинате произошло немало изменений.
Воспользовавшись любезным приглашением руководства холдинга, мы получили возможность снова побывать на производственной площадке, чтобы узнать о сегодняшнем дне и планах Павловского ДОКа, сделав акцент на новшествах.
Обратить недостатки в выгоду
Рачительность проистекает из внимательности. В этом я наглядно убедился на комбинате, который вместе с его руководством мы обошли кругом и потом еще прошли насквозь: если что-то где-то неправильно работает или даже не так лежит, это сразу примечает заинтересованный взгляд, а потом недочет не просто устраняется – сначала становится возможностью для улучшения, затем эффективной рационализацией. Идеи порой весьма просты, а повод для их внедрения – вынужденная необходимость, но результаты впечатляют и наводят на мысль: у этой компании есть чему поучиться.
Измерить и взвесить
Что же нового на заводе?
Одна из недавно реализованных на Павловском ДОКе новаций встречает нас в буквальном смысле слова на входе, точнее, на въезде. Рамка для сканирования и измерения входящего древесного сырья групповым методом – это, по сути, аналог сканера, которые используются на лесопильных предприятиях для приемки древесины. Только здесь замеряется не каждое бревно, а сразу вся лесовозная машина.
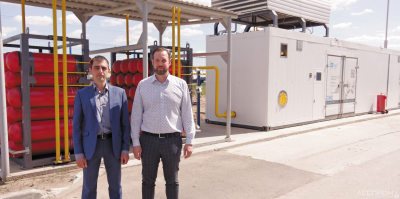
«Первое, что мы хотим вам продемонстрировать, это новая система учета древесины, – начал рассказ генеральный директор холдинга "Алтайлес" Иван Михайлович Ключников. – При открытии завода мы рассчитывали ограничиться исключительно весовым методом приемки, но практика показала, что погрешность очень большая. Поэтому, увидев на одном предприятии отрасли эту технологию, решили использовать у себя».
Пока систему отлаживают, но первые очевидные плюсы уже есть. «Прежде всего мы добились стабильности измерений, – отметил директор ДОКа Алексей Абакирович Гильманов. – Теперь данные о приходящем сырье корректны и достаточно точны, независимо от того, когда была заготовлена древесина, месяц назад или совсем недавно».
При весовом способе оценки сырья измерения зависят от многих факторов. В том числе от периода заготовки – зимой и летом, да и просто от раза к разу влажность древесины существенно разнится, соответственно меняется общий вес груженой машины, «кубометры» тоже получаются разные. Новая технология помогла сделать процесс учета прозрачным, а измерения – корректными и точными.
Пропускной пункт работает круглые сутки. И хотя пропускная способность очень большая, до восьмидесяти единиц автотранспорта в сутки, обслуживает его один оператор-диспетчер в смену. Поставщик оборудования – компания «Интерфейс» из Сыктывкара. «Они собирают эту рамку из устройств – камер, сканеров и других – разных производителей, металлоконструкции делают сами, – пояснил глава холдинга. – Качество измерений нас устраивает, но мы всегда готовы к усовершенствованиям».
На метане и дешево, и безопасно
«Еще одна новая тема, которую мы развиваем на этом предприятии холдинга, это так называемый метановый проект, – продолжил рассказ Иван Ключников. – Идея очень простая. Мы работаем в малолесном регионе, и при концентрации сырья того или иного качества на перерабатывающих производствах неизбежно сталкиваемся с очень большим пробегом машин и серьезными затратами топлива. Тут надо как-то сэкономить!
К решению проблемы мы двигались постепенно. С самого начала работы комбината активно наращивали автопарк: сначала приобрели пять, потом 10, затем 50 и 70 автомашин… Конечно же, думали об их эффективном использовании. Когда наши лесовозы стали накатывать по 300 тыс. км в год – а с учетом загрузки этих машин это хорошей показатель, – стали решать, что делать дальше. Постепенно перевели автопарк на круглосуточный режим работы, организовав транспортную цепочку таким образом, чтобы использовать их наиболее рентабельно. Дальше действовали в направлении оптимизации затрат на топливо: подбирали более экономичные автомобили (работали на КамАЗах, МАЗах, Volvo), различные колесные формулы (так появился тип прицепов с четвертой, вынесенной, осью при наиболее экономически эффективной формуле 4х2). Логичным следующим этапом развития стал переход на метан.
Для большинства крупных транспортных компаний это уже вполне рабочая схема, но в нашей отрасли пока нет. Были отдельные попытки внедрения машин на газе, но возникали проблемы увязки с сетью заправок. Мы воспользовались тем, что на Павловском ДОКе хорошие технические условия для подключения газа, ведь наш холдинг один из самых крупных газовых потребителей в крае. Сделали необходимые расчеты и решили построить на территории ДОКа собственную газовую заправку – для машин этого и других заводов холдинга».
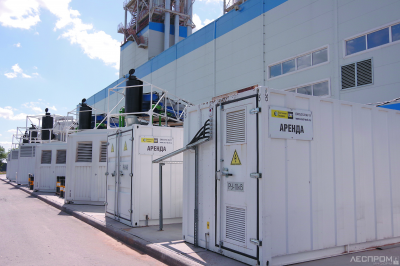
Тем временем в поле зрения появилась новенькая, с иголочки, заправочная станция, сооруженная позади основного производственного корпуса, вдоль магистральной дороги, с которой на нее то и дело заезжали тоже новые и нарядные грузовики Scania.
«Фактически мы организовали тут своеобразный логистический центр заправки топливом своих грузовиков, организовали сообщение с другими комбинатами, – показывает на очередной "причаливающий борт" Иван Ключников. – Проект был реализован за 2021 год, и в начале 2022-го заправочную станцию запустили. Параллельно под этот проект мы заказали новые машины, но… Сначала поставка задерживалась из-за проблемы с электронными чипами, дефицит которых образовался в эпоху пандемии, с декабря по февраль ее решали, а в феврале произошло то, что формирует нашу сегодняшнюю реальность. И тогда нам объявили, что в ближайшем обозримом будущем машины не поставят.
Но не зря говорят, что кризис – это время возможностей. Как только закрылась одна дверь, тут же открылась другая: у российских транспортных компаний тоже возникла проблема – сильно упали объемы магистральных грузоперевозок, а потому резко сократилась потребность в расширении автопарка. И они начали реализовывать излишки машин на рынке. У одной компании мы перекупили по привлекательной цене 14 грузовиков, которые позволили нам запустить свой проект. Потребовалось дополнительно приобрести прицепы к грузовикам, обратились к одному из российских производителей, которых за последние годы стало немало, и в марте услышали, что получим желаемое уже в конце апреля. Вопрос был решен!
Что касается выбора машин. Разумеется, планируя всю эту затею, мы глубоко изучили тему и сделали ставку на автомобили, которые, во-первых, выпускаются полностью оборудованными для работы на метане, а во-вторых, компанией, с большим опытом такого производства. Оценены были эффективность и многочисленные нюансы эксплуатации. Поэтому мы ориентировались на определенные модели конкретного производителя.
Построенная заправка может обслуживать до 20 машин. На старте проекта мы планировали купить 11 тягачей, но так вышло, что их чуть больше. За год реализации мы разобрались, где еще можем извлечь выгоду от их использования, и добавили машин на газе на эти задачи. В частности, на доставку готовой плиты нашим клиентам в Сибири.
Пока мы не намерены полностью обеспечить грузооборот компании за счет метановых машин, они обслуживают те направления, которые считаются регулярными. Многие перевозки материалов, компонентов разовые, и нет смысла выделять на них какие-то машины из нового парка, заменять газовыми имеющиеся у нас обычные дизельные грузовики».
Газовые машины конструктивно почти ничем не отличаются от дизельных – разве что на месте топливных баков установлены баллоны. Для их эксплуатации нужно, по сути, изучить правила безопасности и порядок заправки топливом на новой станции.
«Тут есть свои нюансы, – говорит Алексей Гильманов. – Партнерская организация из Барнаула обучает наших специалистов – как водителей, так и операторов, обслуживающих газовую заправочную станцию».
В погоне за энергией
«Главная выгода метанового проекта – это, конечно, значительная экономия затрат на топливо, – объясняет Иван Ключников. – От идеи заправлять свои машины на единственной газовой станции в Барнауле мы пришли к необходимости строительства собственной. Инвестиции оказались не такими уж большими, а кроме того, мы приобрели опыт взаимодействия с компаниями, которые занимаются оформлением техподсоединения и т. п. Все это, как выяснилось, вполне можно сделать в рабочем порядке.
Опыт пригодился и при подключении газопоршневых установок – это еще одно новшество, которое появилось после пуска основного производства. Таким образом мы смогли преодолеть проблему с электроэнергией. Ведь одна из главных сложностей, с которыми сталкиваешься при строительстве нового завода, инфраструктурная. Еще обсуждая проект с администрацией, мы обозначали, что нуждаемся как минимум в 10 МВт электроэнергии, и получили ответ: “Без проблем, рядом есть подстанция, вам хватит – обратитесь к энергетикам, они все предоставят”. Однако, начав строительство в конце 2015 года, к моменту запуска технологии мы смогли постепенно получить только 6,4 МВт. Это были настоящие тиски. Мы уже далеко продвинулись в строительстве без вариантов сдать назад, когда и столкнулись с монополией, повлиять на которую было решительно невозможно. Обещание модернизировать подстанцию до того, как завод заработает, отодвигалось бесконечно, и волей-неволей пришлось искать альтернативное решение. И оно было найдено: используя газ, мы вырабатываем электроэнергию на комбинате – 8 МВт. По такой схеме работают многие газовые компании, организаторы тепличных хозяйств и другие. В ЛПК примеров не припомню. Но у нас не было другого выхода.
Что мы сделали: подписали со специализированной компанией договор аренды контейнерных газопоршневых установок и мощной батареи на 1 МВт, плюс еще один договор с организацией, квалифицированный персонал которой, имея все необходимые допуски, занялся обслуживанием этой техники. Расчет простой – стоимость генерации одного киловатта электроэнергии у нас складывается из стоимости затраченного газа и услуг двух этих фирм, и она получилась вполне конкурентоспособной. Что называется, "в рынке". При этом огромный плюс такой схемы – это, как говорят профессионалы, "уход в остров", то есть возможность автономности, независимости от сторонней подстанции, которая, надо признать, сделала нам немало сюрпризов. Например, могли позвонить и вежливо сообщить: “Вы знаете, мы отключаемся, а включим, когда все, что надо, закончим”. Как такой подход сочетать с нуждами постоянно действующего большого производства? Это приводило к большому количеству простоев, а во сколько обходится простой плитного завода, страшно сказать… Не говоря уже о проблемах, связанных с негативным влиянием отключений энергии на оборудование.
Мощности наших установок немного не хватает, для того чтобы работать на максимуме нагрузки, но, если чуть сбавить обороты, завод может полностью отключиться от внешней сети. Так что с точки зрения производственной безопасности это "островное" решение – просто супер!
Мы рассматриваем вариант как модернизации за свой счет действующей электроподстанции, так и строительства новой, с тем чтобы получить дополнительную энергию для обеспечения топовых нагрузок. Но тут тоже есть свои нюансы. Договариваться сложно, однако и полностью перейти на использование контейнерных установок не получится, поскольку это оборудование с двигателями, которые могут потребовать ремонта, а на этот случай нужно иметь какой-то резерв. Вот его нам сегодня, пожалуй, не хватает».
«Газопоршневые установки позволяют нам не только работать в автономном энергорежиме, но и сгладить скачки электроэнергии, которые по ГОСТу допустимы в Россетях. Для частного потребителя они проявляются в мигании лампочки, и больше никаких проблем, а вот для завода потеря электричества даже на доли секунды критична – это неизбежная остановка оборудования с высоким энергопотреблением. Разгон оборудования занимает очень много времени – от 15 минут до двух часов, в зависимости от того, где произошел скачок напряжения. Один час простоя обходится нам дороже 150 тыс. руб., так что при вынужденной остановке каждую минуту завод несет колоссальные потери. Да и капремонт техники требует затрат», – поддерживает Алексей Гильманов.
«Работа в режиме stop and go изматывает, – добавляет Иван Ключников, – вся линия останавливается, а только начинаем разгонять, опять встает… Это и для персонала тяжело, и частотники все время горели, а у нас запасных не было. Теперь проблем нет – постоянно работает своя распределительная подстанция из газопоршневых установок, энергия подается всем основным потребителям, технологическим участкам».
Независимость как норма
Но вернемся к результатам реализации метанового проекта.
Вот машина заезжает на заправку. Процессом управляет один оператор, в дальнейшем руководство предприятия рассчитывает перейти на полностью автоматическую заправку автомобилей. Колонка выглядит почти стандартно, но, если на обычной заправке в окошечке видно, как набегают литры топлива, тут можно наблюдать динамику в кубометрах. Заправка одной машины занимает обычно от 13 до 20 минут, и за это время, по словам руководителя комбината, бак от 18–25% наполняется до 100%.
«Заправочная станция состоит из расположенного в контейнере основного модуля компрессорной установки (где природный газ магистрального давления превращается в компримированный, то есть сжатый до высокого давления), включающей насос, компрессор и абсорберы (где из газа удаляется влага), – и аккумуляторной установки, где хранится подготовленный объем газа. Это позволяет нам запасать газ для заправки от 3 до 5 машин, в зависимости от того, оснащены они дополнительными баллонами или нет. Грузовики в базовой комплектации могут проехать не больше 500 км, мы оснащаем их дополнительными баллонами, что увеличивает запас хода до 900–1000 км. С нынешним плечом доставки это очень важно», – рассказывает Алексей Гильманов.
«Наша машина может на одной заправке сделать рейс за низкосортной древесиной, например, на границу с Казахстаном, – поясняет Иван Ключников. – Поскольку общей инфраструктуры под заправку газа в регионе нет, без собственной станции это было бы проблематично. Экономический эффект проекта мы еще продолжаем оценивать, поскольку май был первым месяцем полноценной работы машин и заправочной станции в рамках метанового проекта, но уже сейчас можно сказать, что экономия в сравнении с традиционной заправкой примерно в два раза. Цифра может в дальнейшем корректироваться, потому что сервис таких газовых машин, как наши, дороже, чем обычных дизельных, но основная выгода проекта была связана с созданием своей заправочной станции – мы исходим из цены метана не на сторонней станции, а на нашей. Как крупный потребитель газа Павловский ДОК покупает его по специальной цене. В итоге двукратная экономия на топливе».
Срок окупаемости проекта – не более 2,5 лет. В отличие от многих компаний, «Алтайлес» сделал ставку на отечественное оборудование. И не прогадал, особенно с учетом текущей ситуации. Как по основным инвестициям, так и по обслуживанию станции в будущем это серьезная экономия.
По словам директора комбината, есть и еще один аспект, о котором не следует забывать, – экологический. Недаром метан все шире используется на городском общественном транспорте. Дело даже не в том, что страна богата газом, объем выбросов газового двигателя существенно ниже, чем дизельного, а тем более ДВС. Газовые грузовики «Алтайлеса» строго соответствуют стандарту «Евро-6».
Технология имеет множество степеней защиты, поэтому автомобили на метане можно считать вполне безопасными. Специалисты оценивают безопасность такого транспорта даже выше, чем работающего на традиционных видах топлива.
«Технология применения метана в качестве автомобильного топлива развивается, в крупных городах все больше такси, автобусов и грузовых машин работают на газе, – согласен Иван Ключников. – Качество оборудования и обеспечивающей безопасность запорно-сбросной арматуры неуклонно повышается, а значит, оно будет распространяться все шире. И наш выбор верный и своевременный.
Противники газового транспорта обычно приводят такой аргумент: приедете на заправку – и будете час стоять и ждать, пока баллоны заполнят. Действительно, это один из основных факторов, который тормозит развитие метановой темы в России. Вот, сейчас на заправочную станцию пришла машина из Бобровки, это за Барнаулом, заправилась за считаные минуты и уже отправилась в сторону Камня-на-Оби. Это произошло, пока мы разговаривали, стоя рядом, даже и не заметили. И процесс не останавливается круглые сутки, а управление очередью полностью контролируется.
Проект предполагает расширение, и рядом с действующей станцией отведено место для такого же контейнерного модуля. Если мы увидим, что загрузка станции серьезно повысилась, то, во избежание простоев, сможем оперативно ввести его в строй.
Хочу еще раз подчеркнуть: ничего уникального в газе как автомобильном топливе нет. Особенность нашего проекта в другом – никто или почти никто не делает всю инфраструктуру “под себя", в основном пользователи метановой техники довольствуются заправками вдоль дорог. Вот они-то и сталкиваются с теми минусами, о которых говорят сторонники использования традиционного топлива. А мы смогли их избежать и даже обернуть в плюсы. Зная необходимые мощности, мы понимали, что обеспечим загрузку станции и при этом будем полностью независимы».
Огонь под контролем
Мы огибаем основной производственный корпус Павловского ДОКа и вдали видим поднимающиеся в небо клубы черного дыма. Как выясняется, это плановое мероприятие одной из соседних фирм, и разговор переключается на пожарную охрану – для Алтайского края это острая проблема, а у «Алтайлеса» в ленточных борах довольно большая аренда. Как обстоят дела с лесными пожарами в этом году?
«Этот год по горимости очень напряженный, – отвечает руководитель холдинга. – Пожаров много, территории были охвачены большие. Пожарная служба холдинга ликвидировала несколько крупных лесных пожаров. Один произошел в Угловском районе (возгорание было вызвано грозой) и бушевал в течение 14 дней: огнем пройдено более 3 тысяч гектаров – такого в Алтайском крае не было 12 лет. Всего с начала пожароопасного сезона на арендованной холдингом территории произошло 252 лесных пожара на площади 7764 га. Лесные пожары – большая проблема, и без охраны оставлять боры ни в коем случае нельзя. Противопожарная деятельность у нас в холдинге построена системно. Структурно компания состоит из отдельных юрлиц, владеющих лесохозяйственными участками, и на каждом таком участке есть элементы специальной инфраструктуры в составе пожарно-наблюдательных вышек, пунктов сосредоточения пожарного инвентаря и спецтехники, которая используется для борьбы с огнем. Мы не «изобретали велосипед», на Алтае система пожарных вышек создана давно, число их велико и аналогов по России я не знаю. Конечно, в регионе используется и авиационный мониторинг, но основной контроль осуществляется именно с помощью системы вышек.
Мы развиваем систему мониторинга с использованием камер видеонаблюдения. Это позволяет точно определять расположение пожара, не задействуя сотрудника на самой вышке. Мы предлагали в крае внедрить программное обеспечение, позволяющее устанавливать точные координаты, расстояние до пожара, и взять на себя расходы, хотя это и дорогостоящая техника.
Работа на пожарно-наблюдательной вышке (ПНВ) очень тяжелая, особенно на юге, где летом температура выше 40°С. Единственный выход – установка на вышках видеокамер и дистанционный мониторинг территории с пульта слежения. Компании "Лесохранитель" и "Лесной дозор" разработали две подходящие технологии, которые позволяют не просто наблюдать за происходящим при довольно высоком разрешении "картинки", но и определять характер дыма, а также замерять расстояние до его источника и устанавливать координаты, исходя из привязки камеры. Такие устройства намного упрощают пожарную охрану, и мы предлагали внедрить эту технологию в крае, и взять на себя расходы, хотя это дорогостоящая техника. От Минприроды требовалось только создать центральный диспетчерский пункт, в котором специалисты будут отслеживать ситуацию и решать, куда и какие силы направлять для тушения. Но взаимопонимания достичь не удалось – нам объяснили, что раз мы заключили договор как лесопользователи, то сами должны обеспечивать пожарную безопасность на арендованных и сопредельных территориях. В итоге мы взяли на вооружение несколько упрощенную в сравнении с предлагаемой разработчиками схему – отказались от использования специального программного обеспечения, но установили в этом году камеры по всему лесному фонду – в основном на своих ПНВ. Так отпала необходимость в "вышкарях", как называют пожарных наблюдателей на вышках, а у тех, кто сегодня следит за пожарной обстановкой, радикально изменились условия труда: они несут вахту в комфортных условиях отдельного кабинета, наблюдая за происходящим на экране. По сети Internet на пульт транслируется высококачественное изображение.
По факту нам удается устранять все возгорания. Но если возникает необходимость дополнительной помощи, то стягивается техника с соседних предприятий холдинга.
К реализации проекта по развитию системы камер слежения мы приступили в 2021 году, и скоро подавляющее большинство предприятий холдинга полностью перейдет на эту модель. Что далеко ходить – прямо над нами, на корпусе 54-метровой башни сепаратора, закреплена автоматизированная камера, контролирующая ситуацию в близлежащем ленточном бору».
Алексей Гильманов считает, что вопросы пожарной безопасности актуальны не только в лесах, где предприятие ведет заготовку древесины, но и на производстве. «На Павловском ДОКе организована добровольная пожарная бригада. В каждом цехе, помимо общей интегрированной системы водного тушения, есть порошковые огнетушители. За одним из сотрудников закреплены обязанности пожарного техника – он обеспечивает работоспособность заводской системы пожаротушения, не реже чем раз в неделю проводит учебные тревоги с имитацией тушения пожара: при участии работников цеха разматывают рукава, подгоняют машину с водой, подключают пожарные гидранты – выполняется все необходимое, кроме подачи воды. Люди постоянно практикуются в локализации и ликвидации очагов возгорания, которые мы моделируем на разных производственных участках. А когда завод остановлен, проводятся полноценные учения, с реальным тушением пожара», – рассказывает директор.
Мелочей на эффективном производстве не бывает
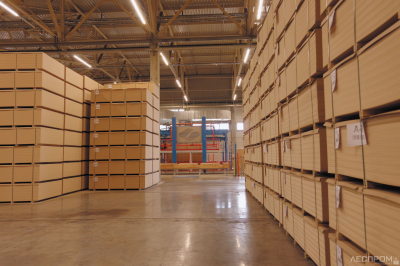
Интересуясь новинками последних лет, нельзя было не пройти по основной технологической цепочке, чтобы обсудить, что изменилось на производстве со времени его запуска. Первое нестандартное решение, примененное на комбинате, оказалось на бирже сырья.
«У нас не очень большая биржа сырья, сейчас ее площадь100 на 100 м, – демонстрирует площадку Алексей Гильманов. – Но, нам не нужно аккумулировать огромный запас древесины на заводе, поскольку холдинг использует более 40 промежуточных складов, служащих своего рода буфером между заготовкой и перерабатывающими производствами. Поэтому максимальная вместимость биржи 25 тыс. м3, за счет дополнительного поля теоретически ее можно нарастить до 50 тыс. м3. В среднем площадка используется наполовину – поддерживаем запас балансов 10–12 тыс. м3, что позволяет гарантированно работать 7–10 дней, с учетом подвоза щепы с лесопильных заводов. В межсезонье, из-за проблем с дорогами, создаем запас побольше».
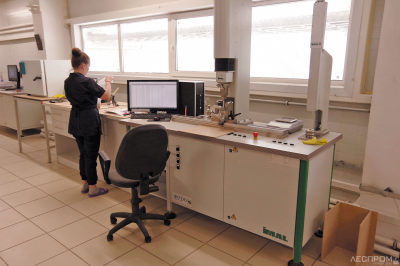
На бирже сырья работают мощные перегружатели, и на манипуляторе одного из них заметно необычное устройство.
«Да, это наша находка, – поясняет Иван Ключников, заметив мой интерес. – Дело в том, что мы заготавливаем древесину в очень перестойных лесах, а для них характерны стволы большого диаметра – иногда настолько большого – до 92 см, что они просто не помещаются в рубительную машину, принимающую до 54 см. Было найдено простое, но эффективное решение – специальный захват на перегружателе, который раскалывает самые толстые бревна – и тогда их можно перерабатывать в рубилке.
Все заводы холдинга давно и успешно используют технику Liebherr, это отличные машины с огромным эксплуатационным ресурсом и высоконадежные. Планируем установить здесь еще один перегружатель этой компании. Вообще, мы стараемся оптимизировать и схему работы перегружательной техники. Например, на комбинате работают всего два погрузчика и два штабелера – и это для перемещения и круглого леса, и сыпучих материалов. Есть еще пять вилочных погрузчиков – это считается немного. Чтобы уйти от использования перегружателей, допустим, на перевалке щепы, процесс организован так, что щеповоз разгружается сразу в силосы, каждый вмещает 2,5 тыс. плотных м3. Активно внедряем шнеки, ковшовые элеваторы, системы транспортеров».
Аспирационную систему на комбинат поставила австрийская компания, но все трубы сделаны в России, как заметил директор предприятия. «Вообще по возможности стараемся привлекать отечественных поставщиков и, что можем, делаем своими силами. Эта практика оправдала себя на этапе монтажа и пуска производства, поэтому завод обошелся достаточно бюджетно, придерживаемся ее и сейчас, когда это стало гораздо важнее», – подчеркнул Алексей Гильманов.
На участке размола и осмоления подготовлена площадка для установки второго реактора. «Это когда нарастим объем производства до 320 тыс. м3, – объясняет директор. – Пока тут хранятся ингредиенты для связующего и готовая смола. Сейчас производство на 60% обеспечено собственной смолой, которая изготавливается на месте из приобретаемого концентрата.
Рядом мы запускаем участок щепомойки для удаления различных минеральных включений. Перед заводом была поставлена задача наладить производство тонкой плиты, чтобы составить конкуренцию ДВП. Много времени и сил потратили на освоение подготовки щепы для нового процесса – удаление инородных фракций. Отчасти удалось справиться с помощью системы специальных магнитов, а окончательно решить проблему поможет щепомойка. И если на других заводах тоньше 5 мм MDF не берутся делать, то мы выпускаем плиты толщиной 3–4 мм и готовы предложить 2,5 мм».
На этапе формирования основной производственной линии завода были выбраны три поставщика. «Покупали мы все сами, по техническим заданиям производителя линии прессования, это позволило нам в дальнейшем проектировать системы с отдельными компаниями по своему выбору: например, сжатый воздух, пневмотранспорт и другие. Сейчас мы можем в рамках общей концепции развивать технологическую линию. Вот, в частности, недавно подписали контракт с компанией, которая к маю будущего года поставит нам пресс для ламинирования. Это очень достойного качества линия с высоким количеством тактов – 180 циклов в минуту», – сообщил Иван Ключников.
«Автоматической линии упаковки, как таковой, на заводе пока нет, – продолжает экскурсию по следующему участку Алексей Гильманов. – Мы решили последовать китайской концепции и просто поставили несколько упаковочных столов. Работали 10–12 человек плюс начальник, который руководил и водителями погрузчиков. Но после консультаций со специалистами Федерального центра компетенций удалось так перекомпоновать оборудование линии, что сегодня на участке со всем справляются всего два сотрудника. Разумеется, после ввода линии ламинирования концепция участка будет полностью пересмотрена. А запустить ее планируем к осени следующего года».
Склад готовой продукции завода занимает без малого 14 тыс. м3 и совмещен с зоной отгрузки. Как рассказал Алексей Гильманов, там планируют разместить автоматизированную линию загрузки: на площадке из листового металла и фторопласта будет формироваться блок из пакетов с MDF, а после этого вся площадка целиком будет заезжать в контейнер или автофургон. После цикла загрузки пустая площадка будет «выдергиваться» обратно.
«Мы должны были получить это оборудование еще в конце апреля, но из-за возникших проблем срок поставки перенесли на лето», – говорит директор комбината.
В отлично оборудованной заводской лаборатории, по словам директора холдинга, «можно исследовать что угодно: и воду, и технологическую щепу, и все компоненты связующего, и, разумеется, каждую партию готовой продукции – клиент должен быть уверен, что приобретает качественную, апробированную продукцию». Оборудование выбрали итальянской компании, ведущего эксперта в этой области. «Постепенно приближаемся к полному, глубокому анализу готовой плиты, – комментирует Иван Ключников. – Скоро от итальянских партнеров поступит новое измерительное устройство – профилометр, который позволит усовершенствовать контроль готовой продукции за счет отслеживания плотности плиты после пресса в режиме онлайн. Сейчас мы доставляем образец с линии в лабораторию, тратим немало времени на проверку качества, после чего даем обратную связь на производство, тем самым зачастую добиваемся возможности работать быстрее, повышая эффективность. А с помощью нового устройства можно будет прямо на линии контролировать параметры продукции, останется только следить, чтобы профилеметр, грубо говоря, не наврал. ».
Алексей Гильманов добавляет, что оценка качества разных плит сейчас занимает от 15 до 30 минут. «Профилометр будет делать эту важнейшую операцию в режиме реального времени, и в каждый момент мы будем знать, качественную мы делаем плиту или нужно срочно внести какие-то коррективы в процесс.
Кроме того, рассматриваем коммерческие предложения по установке сканера для сыпучих материалов. Хотим отслеживать расход топливной биомассы, чтобы точно понимать, какой объем в какой период времени мы используем для выработки тепла. Сейчас у нас, кроме геометрических, методов измерения древесных отходов нет», – рассказал директор комбината.
Модернизация: быть или не быть?
Умение преодолевать проблемы говорит в том числе и о том, что на предприятии без них не обходится.
«Особенность нашего 9-футового пресса в высокой скорости прессования – 1,5 м/с, а значит, в отличие от большинства подобных устройств (у конкурентов скорость пресса обычно 0,8 м/с), он может работать на тонкой плите. Если удлинить пресс на пять метров, можно дополнительно повысить его производительность. Технически мы полностью готовы к модернизации линии прессования, но, к сожалению, с этим пока есть проблемы, – рассказывает директор холдинга. – В начале 2021 года специалисты Павловского ДОКа назвали мероприятия, реализация которых позволит повысить эффективность работы предприятия на 20%, то есть с 250 тыс. до 320 тыс. м3 MDF в год – это значительный прирост, в той рыночной ситуации просто необходимый, – и просчитали их стоимость. Мы начали проект, заказали оборудование. По сути, вопрос был только в том, когда останавливать завод для проведения пусконаладочных работ: учитывая установленные сроки доставки оборудования, хотели сделать это в апреле. Планировалось удлинение пресса (для чего были заказаны дополнительные рамы, нагревательные плиты, лента удлинения), а также модернизация системы размола. На данный момент мы получили все необходимые детали устройства, но, в отсутствие специалистов компании-поставщика, не можем приступить к монтажу – ведь оборудование нужно не только собрать, но и запустить.
Помимо этого, модернизация предполагала оптимизацию энергетического центра. В ходе производства образуется большой объем мелкой фракции – это бракованное волокно, остатки коры после окорки и прочее. Для ее утилизации рассматривались два возможных варианта: установка дополнительной горелки на оборудование энергоцентра и строительство дополнительного котла. Котел будет работать только на мелкой фракции, подаваемой шнековыми транспортерами, что позволит минимизировать использование внутризаводского транспорта. Вырабатываемых 4 МВт тепла будет достаточно для обеспечения всей инфраструктуры завода даже во время плановых остановок.
Процесс пошел, но с горелкой ничего не получилось, потому что поставка совпала по времени с обострением международных отношений и производители наглухо закрылись от любых контактов. А вот котельное оборудование мы получили, и работа в этом направлении продолжается. Единственная сложность этого проекта, как и модернизации основной технологической линии, в электрооборудовании: мы используем электрошкафы компании, чья продукция сейчас под санкциями. Ввезти их пока проблематично, но мы, что называется, на низком старте и надеемся, что в ближайшем будущем удастся найти решение». Энергоцентр суммарно должен вырабатывать 70 МВт тепловой энергии.
«А вот еще идея! – оживился Иван Ключников. – В силу особенностей технологии размола заводу требуется много пара и вместе с тем образуется очень большой объем конденсата. К моменту запуска комбината у нас не было соответствующих мощностей для очистки воды. Но со временем была приобретена установка химической и биологической очистки, после прохождения которой воду можно снова использовать.». «Мы показали вам несколько проектов, реализованных за последнее время конкретно на этом комбинате, – завершил экскурсию Иван Ключников, – но те или иные задумки, когда больше, когда меньше, мы постоянно осуществляем на всех предприятиях холдинга. Развитие не прекращается. Ведь в сегодняшней ситуации как никогда важно досконально просчитывать, изучать возможности оптимизации и усовершенствования производства».
Автор выражает благодарность помощнику генерального директора по связям с общественностью лесной холдинговой компании «Алтайлес» Ольге Лисице за приглашение на предприятия и помощь в подготовке статьи
Справка
ООО «Павловский ДОК» (с. Павловск, Павловский район Алтайского края). Входит в состав лесного холдинга «Алтайлес». Дата образования OOO – 5 мая 2015 года. Уставный капитал – 20 млн рублей.
Самый крупный проект холдинга, реализованный с нуля. Завод введен в эксплуатацию в 2020 году (торжественное открытие состоялось 25 июня 2019 года). Инвестиции составили более 7 млрд рублей. Мощность линии по производству MDF – 250 тыс. м3 в год. Продукция реализуется под брендом «АлтайДекор».
В качестве сырья используется низкосортная древесина, а также щепа с лесопильных комбинатов компании, расположенных в Рубцовске и Камне-на-Оби. Производство полностью безотходное. Оборудование – Siempelkamp, Holtec, Buttner, Andritz, Polytechnik и др. 30-метровый пресс Siempelkamp ContiRoll позволяет выпускать плиты форматов 2440×1220, 2440×1830, 2620×2070, 2800×2070 мм и толщиной 2,5–40 мм. Класс эмиссии карбамидоформальдегидной смолы – Е1.
Согласно финансовой отчетности за 2021 год, выручка выросла до 5,3 млрд руб. (189%), чистая прибыль выросла до 1,6 млрд руб. (287%).
5 марта 2020 года директором ДОКа стал Алексей Гильманов, ранее руководивший на предприятии отделом производства.
Текст Максим Пирус