«Механика-Транс»
Инженер здесь главный человек
Производство твердого биотоплива из древесных отходов, пожалуй, самая молодая отрасль лесопромышленного комплекса – в России ее история насчитывает не более двух десятков лет. А потому и изготовлением оборудования для биотопливной промышленности занимается в основном молодежь. При этом у каждого разработчика такого оборудования свой подход и к технологиям производства биотоплива, и к выстраиванию бизнеса.
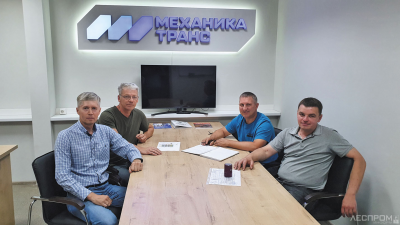
Логотип «Механика-Транс», одной из компаний – производителей машин для лесной промышленности, в последние годы все чаще попадается мне на глаза при посещении пеллетных и брикетных заводов в Республике Коми. Очевидно, предприниматели из нашего региона при выборе биотопливного оборудования нашли для себя некий стандарт. Интересно было узнать причины такого решения, большинство владельцев заводов обосновали его качеством оборудования, действительно позволяющего стабильно, с заявленной мощностью производить пеллеты или брикеты.
В июле 2022 года я приехал на производственную площадку ООО «НПО "Механика-Транс"» в Йошкар-Оле и встретился с заместителем директора компании Андреем Алметовым.
– Андрей Николаевич, в какой области специализируется ваше предприятие?
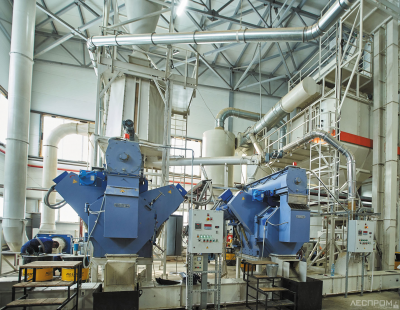
– Мы позиционируем себя как производителя биотопливного оборудования, в первую очередь пеллетных заводов. А вообще изготавливаем для деревообрабатывающих предприятий участки измельчения сырья, сортировки щепы, пневмосистемы, транспортеры, занимаемся механизацией котельных на древесном топливе и многим другим. Кроме того, наше предприятие выпускает оборудование для переработки мусора и торфа, а также для производства древесной муки.
С 2022 года мы стали серийно выпускать просеиватели щепы производительностью до 300 м3/ч, измельчители коры, рубительные машины мощностью до 15 м3/ч. Сейчас идет разработка машины мощностью 40 м3/ч.
– И как давно «Механика-Транс» на этом рынке?
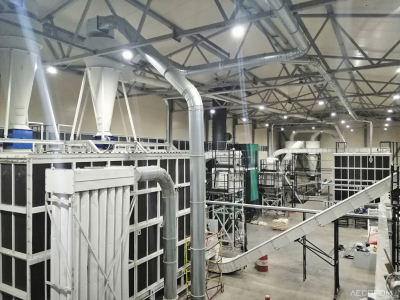
– 2022 год для нас юбилейный – компании 15 лет. ООО «НПО "Механика-Транс"» было основано в 2007 году. Основали его Юрий Созонов, ныне директор компании, Алексей Нефедов, технический директор, и я. И все эти 15 лет, мы руководим компанией вместе и непосредственно участвуем в разработках новых изделий, производстве, запуске заводов…
Начинали мы сложно, на энтузиазме, в арендованном гараже. Первыми небольшими заказами компании были конвейеры – шнековые, ленточные, скребковые. Также участвовали в механизации производственных участков, изготавливали транспортеры для лесопромышленных предприятий, кстати, отсюда слово «Транс» в названии компании.
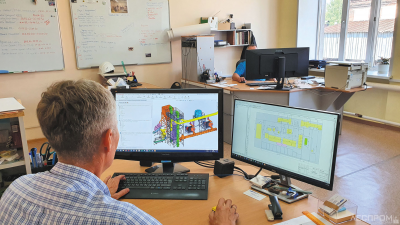
Следующим этапом стал выпуск пеллетных линий небольшой мощности – до 2 т/ч, а сегодня заводы производительностью до 10 т/ч стали для нас нормой. Например, наш самый большой проект, реализованный для предприятия ООО «Ангара Лес» в городе Кодинске Красноярского края, это пеллетная линия мощностью 8 т/ч с двумя линиями сушки.
Сейчас наши проекты есть по всей стране, от Калининграда до Южно-Сахалинска. Предприятие выпускает оборудование с повышенным запасом прочности, срок его эксплуатации 15 лет и больше. Это оборудование тяжелого класса, и до недавнего времени его поставляли в Россию исключительно иностранные компании.
– Что означает аббревиатура НПО в названии компании?
– Научно-производственное объединение. 25% коллектива – это сотрудники конструкторского бюро и АСУ. Конструкторское бюро разрабатывает новые изделия, модернизирует созданное и занимается исследованиями в области оптимизации производственных процессов. То есть для нас самые важные сотрудники – это разработчики, инженеры, поэтому со временем в компании и появился полноценный конструкторский отдел. Сейчас это мощная команда инженеров, проектирующая заводы под ключ. Благодаря коллективу конструкторов компания «Механика-Транс» выполняет нестандартные заказы, находит технические решения сложных задач.
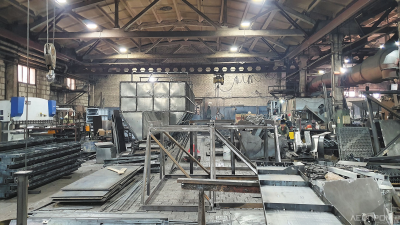
Конечно, у нас есть собственная производственная площадка – 5 тыс. м2. Своими силами выполняем почти все виды работ – лазерная резка и гибка металла, сварочные работы и механообработка, покраска и сборка.
В отделе АСУ работают 11 специалистов: программисты, схемотехники, электромонтажники. В электроцехе есть возможность для отладки изготавливаемой системы АСУ, это позволяет сократить время пусконаладочных работ, выявить ошибки монтажа и программирования. Вся АСУ запускается в тестовом режиме и только после этого отгружается заказчику.
– Как строятся отношения с заказчиками оборудования?
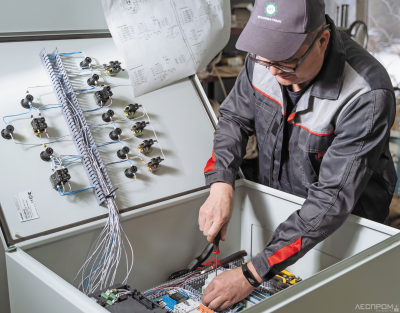
– В качестве первого шага мы проводим предпроектные работы, создаем своего рода техническое решение. Для этого наш специалист выезжает на площадку заказчика, где формируется техническое задание.
Далее ищем оптимальное техническое решение задач с учетом особенностей сырья и существующей производственной инфраструктуры. У нас индивидуальный подход к каждому клиенту.
Затем согласовываем перечень оборудования, мощности, стоимость и технологическое описание. Причем на этапе проектирования мы предоставляем 3D-визуализацию будущего завода. После этого подписывается договор на поставку.
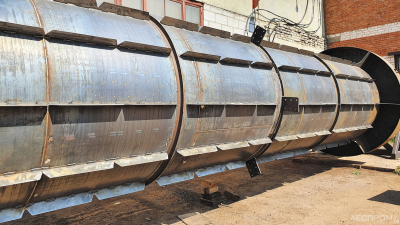
Изготовление оборудования, в зависимости от загруженности производства и сложности линии, занимает от двух месяцев до года. Основная часть делается под заказ на каждый проект. На складе готовой продукции, как правило, хранится только типовое оборудование: шлюзовые перегрузчики, дробилки, вентиляторы и т. п.
Помимо заводов под ключ, немалая часть сделок – это поставки единичного оборудования и отдельных участков. «Механика-Транс» производит молотковые дробилки, все виды транспортеров, сепараторы, бункеры, механизированные склады, пневмосистемы и другое оборудование, применяемое в деревообработке.
– Как выстроен технологический процесс?
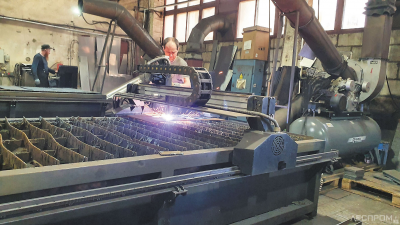
– Конструкторская документация передается на участок заготовок, где используются токарные, фрезерные и ленточнопильные станки, установки лазерной и плазменной резки. Заготовки распределяются между бригадами. После сварки, сборки и испытаний оборудование грунтуется, окрашивается в фирменные цвета и на складских площадках дожидается отгрузки. Минимизировать ошибки при отгрузке помогает разработанная компанией система штрихкодирования изготавливаемого оборудования.
В производстве оборудования применяются надежные комплектующие. Нет цели сэкономить, упростить. Всегда в приоритете качество, максимальный ресурс работы, долговечность и эффективность.
Мы не гонимся за количеством реализованных проектов. Пусть это будут 4–6 линий гранулирования или брикетирования в год, главное, что все они сейчас успешно работают.
– На брикетном заводе в Коми я наблюдал, как специалист вашей компании удаленно, из Йошкар-Олы, подключался к оборудованию и контролировал параметры его работы. Расскажите об этом подробнее.
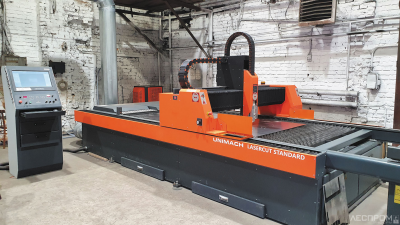
– Да, действительно, одной из отличительных особенностей наших заводов является автоматическая система управления производством, разработанная специалистами «Механики-Транс». Другими словами, заводом может управлять один оператор. Система контролирует более 300 параметров, хранит десятилетний архив событий, оснащена функцией удаленного доступа и видеонаблюдения. На АСУ приходится существенная часть стоимости завода, но многолетний опыт показал, что это оправданно на 100%. Просто необходимо решить: вы хотите работать по старинке или максимально автоматизировать производство и исключить ошибки, связанные с человеческим фактором? Программисты компании постоянно совершенствуют АСУ. С 2020 года появились новые опции и возможности программы. Наши специалисты могут удаленно вносить изменения в программное обеспечение и дополнять действующую систему новыми «фишками».
– Проблема биотопливных заводов – пожары. Вы предлагаете какие-то решения или это забота владельца завода?
– Очень важный вопрос. К сожалению, при производстве пеллет и брикетов возгорание оборудования не редкость. Поэтому несколько лет назад в типовых предложениях пеллетных заводов от «Механики-Транс» появилась опция «Система искро- и пожарообнаружения и гашения». В последнее время при подписании договора на поставку нового завода мы настаиваем на включении таких систем в основной список оборудования. Причем если раньше мы устанавливали такую систему на двух точках, то теперь контролируется не меньше шести точек.
Кроме системы искрообнаружения и тушения, мы применяем систему тушения возгорания собственной разработки. Ее эффективность подтвердил многолетний опыт. Принцип действия основан на контроле температуры на входе и выходе из барабана и в основном циклоне перед дымососом. На каждую точку контроля устанавливается определенный порог предупреждения. При приближении рабочей температуры к этому порогу всплывает окно «Опасный режим»: тушить – «да» или «нет». Если оператор видит, что процесс сушки контролируемый, он нажимает «нет» и сушка продолжается. А если он игнорирует всплывшее окно и не сообщает системе о своем решении, сушка продолжается, но предупреждение остается на мониторе. При дальнейшем критическом повышении температуры процесса и превышении пороговых аварийных значений АСУ автоматически останавливает сушку. Электропривод открывает вентиль на углекислотном баллоне, и 30 кг углекислоты подаются в барабан и циклон. Кислород вытесняется, температура в барабане резко падает, снижается интенсивность горения или оно прекращается. Задача оператора – оценить ситуацию и принять меры для прекращения горения. На случай продолжения горения установлен второй баллон, с ручным приводом. Подача углекислоты дает оператору возможность оценить ситуацию и действовать в соответствии с обстановкой.
Барабанная сушка – пожароопасный процесс. При разборе обстоятельств и причин возгораний в 100% случаев установлено нарушение технологического процесса. Например: прекратилась подача влажного сырья в барабан – температура на выходе растет – возможно возгорание. Во избежание этого на подающие в барабан шнеки мы устанавливаем редукторы с большим запасом по крутящему моменту. Устанавливаем в бункере-ворошителе сырья перед сушкой ультразвуковые датчики измерения уровня загрузки, так как флажковые периодически зависают. Если все же датчик завис: АСУ видит, что бункер не пополняется больше указанного времени, и всплывает окно предупреждений: «Проверь состояние датчика уровня». Используем и другие способы контроля технологического процесса.
Персонал должен внимательно следить за состоянием внутренней поверхности труб сушки и барабана. Мелкодисперсная пыль во влажной среде налипает на них, поэтому необходимо регулярно осматривать оборудование и чистить его. Для уменьшения налипания мы изготавливаем линии сушки и циклоны из нержавеющей стали, стали использовать и дымососы из нержавейки. Устанавливаем датчики вибрации на вентиляторы, дымососы, молотковые дробилки. Датчики сигнализируют о повышении уровня вибрации и необходимости осмотра и чистки. Предусматриваем аварийные сбросы сырья и прочее. В общем, работаем над снижением пожароопасности процесса и контролем максимального числа параметров.
– Как повлияли санкции, введенные в 2022 году против России, на деятельность компании?
– К сожалению, это давление мы заметили. Теперь нет возможности укомплектовывать вентиляторы электродвигателями, а транспортеры – мотор-редукторами из Евросоюза. Но мы нашли им замену на отечественном рынке. Есть трудности с поставками электроники для АСУ. Подобные проблемы с рядом других комплектующих.
Несмотря на запрет экспорта российских пеллет, никто из наших клиентов, заключивших договор, не отказался от сделки.
У нас нет упаднического настроения – поступают заказы на пеллетные и брикетные заводы, брикеты пользуются спросом на внутреннем рынке, также заказывают линии производства древесной муки, транспортные системы. Времена сложные, но большой конструкторский задел и возможности диверсификации производства позволяют нашей компании смотреть в будущее с надеждой.
Текст и фото Андрей Кривошеин