Добрые дела мастеров своего дела
На каких только предприятиях отрасли не побывали корреспонденты «ЛесПромИнформ» за 20 лет! Исходные «вводные» для таких визитов бывают самыми разными: персональное приглашение руководства или масштабная PR-акция, «подсказка» со стороны поставщиков оборудования или обнаруженная на отраслевом мероприятии взаимная заинтересованность, а то и просто случайная встреча с кем-то из сотрудников. Признаюсь честно: на завод «ДДМ-Строй» я самым нахальным образом напросился – а директор компании была слишком деликатна, чтобы отказать.
Все дело в том, что мне очень и сразу понравилось название компании, точнее, то, как расшифровывается аббревиатура ДДМ: Добрых дел мастер. Ну разве можно придумать что-то более располагающее для бизнеса по созданию деревянных домов?
Немного фактов для начала
Производственная площадка «ДДМ-Строй» располагается в подмосковном городке Протвино. По пути из Москвы специалист отдела маркетинга и PR Иван Круговцев дал несколько необходимых пояснений о «ДДМ-Строй».
Компания работает с 2005 года, специализируясь на изготовлении клееного бруса, а также на производстве домокомплектов из него, строительстве домов и малых архитектурных форм (беседки, бани и т. д., на которые сейчас существует большой спрос) по индивидуальным заказам.
Комплект деталей дома из клееного бруса – это своего рода конструктор, готовый для самостоятельной сборки на объекте. К нему прилагается детальная документация для сборки. Все элементы домокомплекта идеально соединяются между собой, обеспечивая быструю и качественную сборку. Дома чаще всего строятся «под ключ», то есть заказчик получает готовый дом со всеми инженерными коммуникациями и финишной отделкой, остается только завезти мебель. При строительстве врезка балок перекрытий и стропил осуществляется при минимальном использовании крепежа. Проекты домов разрабатывают в специальной конструкторской программе Cadwork (Германия) профессиональные архитекторы, технологи и конструкторы, на все работы и продукцию предоставляется трехлетняя гарантия.
Для постоянного проживания в средней полосе России рекомендуется дом из клееного бруса толщиной 212 мм. Для временного проживания в теплое время, а также в южных регионах будет достаточно толщины бруса 168 мм. Для небольшой бани – достаточно 125 мм. Качественный клееный брус (гарантия составляет 25 лет) производится на заводе из сосны и ели, реже – кедра. Наиболее распространенные сечения: 186(h) х212, 186(h)х254, 186(h)х125, 186(h)х168, 270(h)х205, 270(h)х250, 140(h)х125, 140(h)х168, 140(h)х212.
За разговором время и сотня километров дороги пролетели незаметно – обогнув жилые кварталы Протвино, мы въехали в промзону.
Предприятие над коллайдером
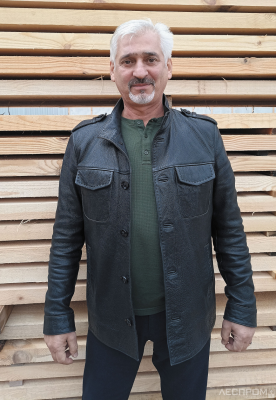
У ворот завода нас уже ждал директор производства Акиф Исмаилов. Начиная экскурсию, он то ли в шутку, то ли всерьез упомянул, что где-то на глубине, в толще земли под промплощадкой проходит огромное кольцо коллайдера… А почему бы и нет, если город Протвино (еще не так давно – «закрытый») был основан в 1960 году для обеспечения амбициозного проекта НИИ Физики высоких технологий? И раньше на площадке, часть которой сегодня занимает завод «ДДМ», располагалась большая база строительно-монтажного управления, которое усердно трудилось над созданием как строго засекреченных объектов, так и жилья для работающих на них людей. Во все стороны разбегались железнодорожные пути, по которым сюда приходило сырье, а уходила – строительная продукция.
В какой-то мере «ДДМ-Строй» – продолжатель этой традиции, только в сегменте деревянного домостроения. И продукцию свою отправляет уже по автодорогам, а на открытой площадке над остатками многоколейного ж/д-тупика царит башенный кран – на заводе он «отвечает» за все внецеховые перемещения, от выгрузки сырья, перемещения сушильных пакетов и склеенного бруса до отправки готовых домокомплектов потребителям.
Два цеховых помещения, управление, сушильный комплекс, котельная, погрузочно-разгрузочная площадка, открытый склад для хранения сырья и готовой продукции и отдельно стоящая покрасочная камера – вот, собственно, и все. Продуманно и компактно. Вся территория предприятия контролируется системой видеокамер, а технологические процессы, где только возможно, автоматизированы.
Ну что же, пора смотреть производство.
Пройдемся по технологии
«Вот здесь мы в самом начале пути, – директор производства начал рассказ на участке приемки сырья. – Ежемесячно на завод приходит примерно 800 м3 древесного сырья. Мы закупаем пиломатериалы строго по своим особым техническим условиям (сырая доска с сечением 50х150 и 50х200, габариты – 55х207 и 55х157 мм соответственно), поставки осуществляются в основном из Вологодской, Костромской, Нижегородской и Владимирской областей.
Работники на приемке доски проверяет соответствие полученного сырья техническим условиям предприятия: каждую партию перебирают, оценивают геометрию и имеющиеся пороки, отсортировывают выбраковку.
«Все поставщики работают с нами более 10 лет, все требования давно знают, поэтому процент брака невысок и всегда удается достаточно легко и быстро разбираться со спорными вопросами. По каждой поставке составляется акт – и направляется поставщику, чтобы он принял решение: заменить “выпадающий” объем в следующий раз или как-то иначе поступить к обоюдному согласию. Например, мы можем приобрести некондицию по более низкой цене: поскольку сами занимаемся возведением домов, она может пригодиться в ходе строительства», – пояснил Акиф Ибрагимович.
Годные для дальнейшей обработки доски укладываются в штабели на специальные калиброванные прокладки и готовятся к сушке в сушильном комплексе. Он состоит из двух камер конвективного Drywood FA-10 объемом по 100 м3 каждая. Установка работает в автоматическом режиме, управляется с помощью компьютера.
Пиломатериалы естественной влажности проходят 6 фаз сушки, это так называемый «мягкий» режим: вначале древесину разогревают до 55 градусов, далее, согласно специальной программе, пиломатериал автоматически проходит несколько стадий увлажнения и сушки. Продолжительность цикла различается, в зависимости от сезона: в зимний период он составляет 12–14 дней, в летний – от 6 до 8 суток. Влажность досок на выходе – 12(+-2)%. Соответствие заданным режимам оператор регулярно фиксирует в специальном журнале: во сколько происходят переходы с одной фазы на другую, какая температура в этот момент и так далее.
Сушильные камеры установлены в 2005 году и вот уже 17 лет, благодаря своевременному и добросовестному обслуживанию, успешно функционируют. Тепло для их работы (помимо этого, получаемая тепловая энергия используется для отопления всех производственных и иных помещений предприятия в холодное время года) поступает от собственной котельной.
Производство полностью безотходное: все дефекты пиломатериалов, которые вырезаются после их сушки, а также прочие древесные отходы производства становятся топливом для котлов. Отходы (кусковые по транспортеру или в биг-бэгах, опилки – через систему аспирации) поступают в бункер-накопитель, а уже из него шнековой подачей направляется в систему горения. Котел на предприятии – Кировского завода, мощность 1мВт. Так как процесс сушки древесины непрерывный, котельная работает в режиме 24/7. Котельщики работают посменно и следят за показателями на приборах в процессе сушки и днем, и ночью.
По завершении цикла сушки пиломатериал поступает в первый цех, который работники между собой называют цехом клееной заготовки: заходит в него доска, а выходит уже склеенный брус для производства деталей домокомплекта.
Здесь каждую доску сначала строгают и калибруют по заданному размеру (например, 197 х 47) на 6-шпиндельном калево-фрезерном станке BL 6–23.
Далее происходит распределение на еловые и сосновые пиломатериалы.
На отдельной площадке аккумулируется двухсуточный объем доски, необходимый для обеспечения полноценной работы смены.
Следующий этап – два торцовочных поста со станками Stromab PS 600/P. Визуальный контроль позволяет отследить и изъять из процесса некондицию – наряду с торцовкой операторы удаляют вскрывшиеся при первой строжке дефекты (согласно специальной инструкции), после чего раскладывают заготовки на поддонах по сортности: первый сорт пойдет на внешние ламели (по ТУ минимальная длина ламели – 30 см), второй – внутрь бруса.
На очереди – зарезка вертикальных мини-шипов (от 9 до 11 мм), которая производится на шипорезных станках Weili FS-18H с двух сторон бездефектных отрезков досок строго по распределенным раньше сортам.
Потом ламели поступают на автоматическую линию бесконечного сращивания F-A01, где склеиваются в ламели с использованием ПВА-клея Д4. Если планируются стандартные изделия, то сращивают и обрезают заготовки по 12,5 м, однако под какой-то конкретный проект, где возможны различные сечения и длины деталей, начальник цеха Александр Саперов готов оперативно переустановить параметры под заданные в чертежах размеры балки: допустим, склеить 20 ламелей длиной 8,5 метров, 10 по 11 метров и еще сколько-то по 9 метров... На предприятии стараются избегать появления ненужных отходов.
По завершении сращивания делается чистовая острожка полученных ламелей на четырехстороннем станке Leadermac. На этом этапе, перед закладкой заготовок в пресс для склеивания бруса наибольшее внимание уделяется чистоте и правильной размерности острожки пласти.
На выходе из четырехстороннего станка строганые ламели попадают в клеенаносящую машину, из которой ламели с нанесенным на них связующим попадают в пресс для склейки бруса.
Склеивание бруса в прессе VESP 12000/250 (длина 12,5 м – соответственно, такова и максимально допустимая длина бруса) также производится по заданию, определяемому текущим проектом (если это не накопительная – на склад – склейка). Цель – получить строго необходимое количество бруса того или иного размера. Давление в прессе поддерживается автоматически, продолжительность склеивания варьирует в зависимости от окружающей атмосферы: например, в недавней летней жаре брус в прессе выдерживали около 25 минут, в более прохладное время – 35, зимой (когда температура в этой части цеха составит 9–12 градусов), по словам Акифа Исмаилова, его могут прессовать и час: руководством по продолжительности и другим параметрам операторам служат специальные режимные карты.
На выходе из пресса – готовый клееный брус, которому предстоит дальнейшая обработка во втором цехе с получением различных деталей домокомплекта.
Для склеивания бруса используется как двухкомпонентная ЭПИ-клеевая система P.I. Bond (класс водостойкости D-5, состав не содержит формальдегида, меламина, фенола и толуола, что подтверждено необходимыми сертификатами) японской компании Oshika, так и однокомпонентный пенополиуретановый клей из Голландии.
К связующим на предприятии предъявляются очень высокие требования: качественный клей в отвержденном состоянии должен быть химически нейтрален, не разлагаться, не выделять никаких токсичных соединений. Соответствие этим критериям, равно, как и соблюдение на заводе правильных режимов склейки строго контролирует поставщик клея: на протяжении всей производственной деятельности компания «ДДМ-Строй» приобретает у одной и той же компании – Concept Smart. Ежемесячно проводятся независимые испытания качества склейки бруса. Также компания «ДДМ» сама ежегодно сдает образцы своей продукции на независимые испытания с центральный СЭС, чтоб быть уверенными в качестве и экологичности своей продукции.
Выдержанный не менее двух суток (чтобы клей надежно схватился) брус передается в цех производства деталей, где в зависимости от назначения будущего изделия, подвергается делению, строжке или профилированию: если из него впоследствии планируется выпуск балки, его строгают с 4 сторон, а если стеновые элементы дома, его профилируют на станке Leadermac. Если необходимо уменьшить сечение, клееный брус отправляют на ленточно-делительный станок Italmac MC 2H.
И вот теперь начинается процесс священнодействия, по отношению к которому все предыдущие операции являлись только подготовкой: брус попадает в универсальный домостроительный комплекс Hundegger K2i для нарезки деталей будущего дома. В компьютер высокоточного и производительного станка с ЧПУ уже внесены все данные по текущему заказу в виде файла, созданного конструктором в специальной программе CadWork. Оператору остается только следить за тем, как точная и высокопроизводительная машина изготавливает составные части домокомплекта.
Начальник цеха подбирает для обработки оптимальный инструмент, исходя из данных проекта. Он находится в постоянном контакте с конструкторами, готовыми помочь в отдельных сложных моментах.
Как только изготавливается первая деталь комплекта, начальник цеха вместе с оператором проверяет все размеры на соответствие прописанным конструкторами в проекте – ведь от геометрии, габаритов и точности соединений деталей зависит качество всего домокомплекта в целом. И только после этого дается «добро» на производство остальных деталей.
Линия заделки и доработки – тот участок, где готовая деталь приобретает свой итоговый законченный вид. Работники внимательно осматривают ее, если обнаруживают смоляной кармашек, заделывают его вставкой-лодочкой (или пробку на место сучка, при этом стараясь попасть в годовые кольца: ведь помимо эксплуатационных свойств, большое значение в деревянном доме имеет эстетическая сторона). При необходимости нарезают фаски и подшлифовывают поверхности.
Далее детали передают на обработку антисептиком, что обеспечит их сохранность на период монтажа и первичной эксплуатации. «Мы используем состав Neomid 46 Bio, он эффективен от 3 до 6 месяцев, концентрация подбирается разная, в зависимости от ожидаемых условий работы на площадке заказчика: 1 к 10, 1 к 12, стандарт – 1 к 19», – пояснил начальник производства. Также обрабатываются торцы – составом от растрескивания Renner.
После этой финальной операции детали (каждая из которых маркируется этикеткой с собственным номером – что совершенно необходимо, ведь в проекте может быть, допустим, 1100 деталей) проходят проверку отделом технического контроля. Формируется транспортный пакет, который упаковывают в полиэтиленовую пленку и стягивают полипропиленовой лентой. Каждую упаковку подписывают названием проекта, нумеруют и сопровождают упаковочным листом с указанием наименований и количества деталей, находящихся внутри.
С помощью башенного крана готовый «конструктор» брусового дома отгружается на автотранспорт для доставки клиенту.
По сути, осталось упомянуть только два производственных участка. Один из них – отдельно стоящая, утепленная покрасочная камера, которую оборудовали недавно, следуя за набирающим популярность трендом на крашеные строения – беседки, качели, навесы и так далее. В работе используется краска на водной основе или масло для наружных или внутренних работ в зависимости от назначения детали в проекте. Детали перед покраской дополнительно шлифуют.
Еще один участок – сервисный. «Стараемся по максимуму выполнять все сервисные и ремонтные работы своими силами, – рассказал Акиф Исмаилов. – Для этого организована ремонтная бригада: слесарь, электрик, заточник. Заточной участок оснащен всем необходимым оборудованием, весь режущий инструмент точим сами на станках Jeffer и ТчН-8. Кроме круглых пил диаметром 800 для станка Hundegger – их отдаем на сервис в стороннюю организацию. Впрочем, это случается не так часто, кроме того, у нас есть “обменный фонд” из четырех таких пил, позволяющий всегда найти из запаса замену той, что нуждается в заточке».
Персонал предприятия составляет около 40 человек, из них 4 ИТР. Производственные мощности компактного завода – при двухсменной работе около 500 м3 готового бруса в месяц, то есть в среднем 5–6 домов.
Слово директору
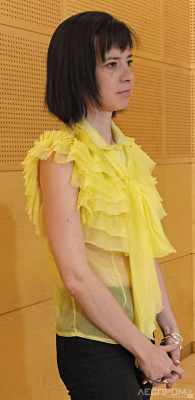
О прошлом, настоящем и будущем «ДДМ-Строй» и рынка деревянного домостроения в целом мы поговорили с генеральным директором компании Верой Вавиловой. Встреча состоялась «на полях» выставки «Лесдревмаш», поэтому стиль интервью невольно получился телеграфным.
– Давайте начнем с того, когда, как и почему возникло ваше производство бруса?
– Судьба предприятия довольно обычная для постсоветского времени: в СССР там, где сейчас располагаются наши цеха, была крупная строительная база, ж\д-ветка позволяла принимать вагоны. В начале 90-х это предприятие развалилось и территорию выкупили в частную собственность. Владелец разделил ее на участки – один из них мы и купили со стоящим там зданием. Построили еще одно, котельную, сушильный комплекс и дальше стали развивать производство. Ездили по выставкам, выбирали и приобретали оборудование. Запуск – в 2006 году.
Изначальные планы были немного другими, задумывались о выпуске мебельного щита и деревянных окон, но впоследствии было принято решение сосредоточиться на клееном брусе и домостроении из него. Соответствующим образом было перекомплектовано производственное оборудование.
– Как бы вы обозначили основные конкурентные преимущества производства «ДДМ»?
– Во-первых, это полный цикл производства. Во-вторых, собственная сушка древесного сырья. Мы сами сушим доску для производства клееного бруса, это очень важно. То есть полностью несем все гарантии перед покупателем, а сами можем быть уверены в том, что качество нашей сушки соответствует уровню остальных технологических этапов.
И наконец, ЧПУ-станок Hundegger, который позволяет сделать множество различных зарезок. Тем самым он позволяет нам расширять ассортимент продукции, благодаря его широким возможностям мы можем делать и стропильные системы, и балки, и сложнейшие варианты зарезок, на которые способен не каждый завод (случается, коллеги привозят нам свои полуфабрикаты на доработку именно «под Hundegger»). Фактически это сердце нашего предприятия сегодня.
Включив в технологическую цепочку Hundegger вместо прежнего Stromab, мы вышли на совершенно новый уровень: если прежде мы могли выпускать добротные, но достаточно обычные, стандартизированные домокомплекты, то теперь готовы делать проекты практически любой сложности и в максимально возможной заводской готовности. Это ведь не только стены, но и перекрытия, стропила, фермы, ограждения… И все это, любые деревянные детали по проекту на 100% подготовлены на заводе для быстрого эффективного монтажа на месте размещения дома. Что это значит? Совершенно другое качество сборки, минимизация влияния человеческого фактора. Строителям не нужно ничего продумывать и придумывать, включать инженерную мысль – достаточно правильно и четко собрать по номерам, указанным в чертеже, из деталей готовый «конструктор».
– Сделанный клееный брус вы полностью используете для производства собственных домокомлпектов или его можно купить «на кубометры» и строить потом самому?
– Несколько лет назад мы отказались от практики продажи клиентам бруса и домокомплектов. Сейчас договор заключается не на покупку домокомплекта, а на строительство дома – то есть с обязательным условием его возведения силами нашей компании.
Отдельно, без сборки мы продаем только отдельные виды продукции – например, силовую клееную балку или стропильные системы. Да и то в единичных случаях. В основном же: готовый домокомплект с нашим монтажом.
Оптимизации бизнес-процессов способствует то, что у нас таким образом разработан сортамент продукции, что на входе только два сечения доски, из которых мы можем делать до 40 различных сечений бруса. Брус типовых сечений клеится постоянно, на склад. При получении заказа брус из этого оперативного запаса идет в обработку по данным, указанным в проекте.
Единовременно в работе находится около 30 проектов.
– Как ваш бизнес пережил последние несколько лет, которые вряд ли можно назвать обычными и спокойными? Что вообще происходило и происходит на рынке деревянного строительства?
– Это точно. Пандемия вызвала всплеск интереса к деревянному домостроению в 2021 году. Бум обращений в компании, очередь на строительство… и дефицит стройматериалов.
Ситуация понятная: сходить некуда, поехать некуда, все строятся на своих участках – иной раз по несколько домов. И мы невольно расслабились: стеновой клееный брус и стандартные домокомплекты из него достаточно простая для производителя продукция – знай себе делай да отгружай – заказов на год вперед, все прекрасно. Но продолжалось это очень недолго.
Правда, вместе с бумом жилищного строительства наступило полное затишье на рынке коммерческих объектов. Рестораны, гостиницы, кафе – все было закрыто, бизнесмены приостановили все свои проекты и мы работали только для физлиц.
Вот на такой волне мы вошли в 2022 год. И примерно в марте почувствовали, что нервная система покупателей не выдержала: людей подкосили произошедшие события и они, что называется, «сели на деньги»: нам стали уклончиво говорить «мы подумаем», «мы подождем», «сейчас неразумно тратить» и тому подобное. Вектор поменялся до наоборот: от «надо срочно строить» год назад до «проживем и так».
Однако, согласно поговорке, не было бы счастья – да несчастье помогло. Вынужденно стал развиваться внутренний туризм: коронавирус вроде отменили, можно ехать – а некуда, только по родной стране. Есть желающие, есть средства, но как выясняется, отдыхать-то у нас негде. Все «мощности» этого сектора давно распределены и заняты, желаемого комфорта возросшему количеству потенциальных путешественников предоставить не получается.
И тут весы качнулись в другую сторону: к нам (и думаю, эта ситуация характерна для всех домостроителей) начали возвращаться наши «коммерческие» заказчики. Мы активно строим общественные бассейны, СПА, полноценные зоны отдыха, мини-гостиницы, рестораны. Много различных объектов в регионах, особенно в тех, где тепло. Ведь из клееного бруса можно построить фактически что угодно – и все будет красиво, функционально. А кроме того, такие сооружения быстровозводимы, достаточно бюджетны, экологичны и визуально очень привлекательны для туристов-горожан.
Но было бы упрощением считать, что только это направление формирует рынок сегодня. Есть и вторая сторона спроса. Это частные заказчики, а именно те из наших любимых физлиц, у кого уже есть на личных участках дома и которым – опять таки в силу вынужденного пребывания внутри страны – хочется что-то в своем владении улучшить. Заказывают малые архитектурные формы: садовые павильоны, стекленные беседки, барбекю-зоны и так далее.
Расширению использования нашей продукции на внутреннем рынке может способствовать и еще одна тема. В современных условиях клееный брус может быть востребован как конструкционный материал: силовые конструкции, стропильные системы, балки и перекрытия – отличные варианты применения этого материала, при грамотном проектировании и правильном распределении нагрузок.
Многие спрашивают, что будет дальше. Наш прогноз таков: в 2023 году продолжится спрос на коммерческие объекты из деревянных конструкций. Алтай и другие регионы Сибири, Камчатка и Дальний Восток, Поволжье и южные регионы России – они развиваются и представляют тем больший интерес в туристическо-рекреационной сфере, чем более комфортабельные условия для путешественников будут в них созданы. Отельеры и рестораторы сейчас, за счет относительно недорогих заемных средств, стараются расширить свои возможности варианты предложения. Да, это специфическая категория заказчиков, с ними нужно учиться работать, возможно, перестраивать свой маркетинг. Этим заказчикам важно строгое соблюдение всех норм, сроки окупаемости объектов и т. п., но именно они в ближайшее время смогут обеспечить сбыт производственно-строительным компаниям и развитие рынка деревянного домостроения в целом.
Что касается физлиц, то у представителей так называемого среднего класса интерес к строительству индивидуальных домов из древесных материалов не угас и не угаснет – но подход к ним понадобится. Наверное, лучшим решением станут пакетные предложения, включающие и банковские услуги. Проведенный нами опрос показал, что около 2% – это тот уровень кредитных ставок, который позволит вернуть на рынок домов из клееного бруса большую часть семейных покупателей.
– Поговорим о географии продаж? Вот в каком аспекте: сейчас вкус к производству клееного бруса ощутили во всех, наверное, «лесных» регионах. А значит, на том или ином уровне оно уже там существует. А если есть местные производители бруса и местные домостроители, найдется ли в регионах место для подмосковной компании «ДДМ-Строй»?
– Вы знаете, деревянное строительство – такая особенная сфера, где очень хорошо работает сарафанное радио. То есть информация передается в личном общении от заказчика к заказчику и, допустим, клиент в Магадане, в частном владении которого нужно построить не только дом, но и все прочие вспомогательные строения, у нас появляется потому, что прежде его знакомый имел опыт сотрудничества с нами в центральной России – и ему понравилось. Или вот строили и во Владивостоке: казалось бы, удивительно, лесной край, рядом Иркутск, но там существует несколько строительных компаний, с которыми у нас давние прекрасные отношения – им очень нравится и наша продукция, и наш подход к работе. Нравится настолько, что они готовы переплачивать за доставку из Подмосковья, но возводят у себя наши домокомплекты. Похожая история есть и в Воронежской области. И, несмотря на то, что мы обычно берем сборку на себя, мы доверяем своим друзьям и партнерам и продолжаем такое взаимодействие.
Возвращаясь к вопросу о географии продаж: это, без преувеличения, вся страна. Строим и на Камчатке, и под Москвой (до 80%). Рынок этот велик и места хватит всем.
Был опыт работы на экспорт – например, в Швейцарии и Франции. Заказчикам очень нравилось и нравится все, что мы делаем, сотрудничали около двух лет и до сих пор мы постоянно на связи, люди хотят, но… Пандемия приостановила эту работу, и сегодняшняя ситуация, к сожалению, ей тем более не способствует. Но мы, конечно, верим в то, что рано или поздно все придет в норму. И лучше – рано.
Текст и фото Максим Пирус