Древесные плиты − 2009: теория и практика
В стенах Санкт-Петербургской государственной лесотехнической академии им. С. М. Кирова 18−19 марта 2009 года прошла XII научно-практическая конференция «Древесные плиты: теория и практика». Конференция собрала около 70 участников − представителей российских деревообрабатывающих производств, а также компаний, которые так или иначе связаны с отечественной плитной промышленностью.
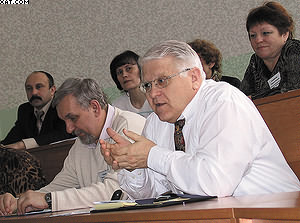
Директор-представитель Modul Systeme Engineering AG
Янош Дерьвари
Конференцию открыл генеральный директор ЗАО «ВНИИДРЕВ» (г. Балабаново) Александр Шалашов, представив обзор современного состояния российской древесно-плитной промышленности. В течение последних пяти лет Россия активно наращивала объемы производства древесных плит, и в 2008 году их было произведено 7,9 млн м3 (без учета фанеры). Мировой финансовый кризис в прошлом году на объемах производства древесных плит не сказался, так как большинство наших производителей ориентированы на внутренний рынок. Из-за девальвации рубля в этом году ожидается резкое снижение импорта древесных плит и мебели. Рынок мебели в течение последних пяти лет в России ежегодно прирастал на 10%. С учетом этого обстоятельства «ВНИИДРЕВ» прогнозирует сохранение благоприятных условий для роста объемов производства древесных плит в стране.
Несмотря на кризис, продолжается реализация ряда проектов. Реконструированы три завода по выпуску ДСтП в Томске, Сыктывкаре и Смоленской области, оснащенные линиями СПБ-110. Начат проект реконструкции в Вологодской области − в Шексне. Всего сейчас в стадии строительства или освоения находится 10 новых заводов по производству ДСтП общей мощностью 2450 тыс. м3 в год; 7 заводов по выпуску MDF на 1600 тыс. м3 в год; 2 завода, производящих ДВП, на 152 тыс. м в год и один завод по производству OSB (ООО «Сыктывкарский завод ОСП») мощностью 400 тыс. м в год.
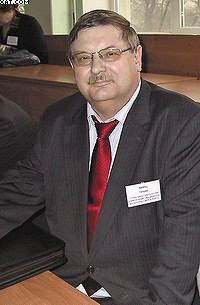
Глава представительства
Siempelkamp в России Генрих Хванц
Александр Шалашов также отметил: из семи линий ДСтП, которые были введены в эксплуатацию в течение последних двух лет, пять − б/у. Высказанное докладчиком сомнение в том, что оборудование 1980-х годов выпуска позволит инвесторам создавать конкурентоспособную с точки зрения себестоимости продукцию, вызвало в зале оживленную дискуссию. Часть присутствующих согласилась с докладчиком. Ведь демонтированное с зарубежных предприятий оборудование, которое ввозится в нашу страну, устарело морально; кроме того, его физическое состояние тоже нередко оставляет желать лучшего. Такие производственные линии не только проигрывают современному оборудованию по производительности и расходу сырья на единицу продукции. Зачастую их работа вредна для окружающей среды. К тому же при запуске такого оборудования весьма велики производственные риски. Противоположную точку зрения высказал директор-представитель немецкой компании Modul Systeme Engineering AG, которая занимается продажей оборудования б/у и его предпродажной подготовкой, Янош Дерьвари. Он обратил внимание присутствующих на объем инвестиций, которые требуются для запуска завода с б/у оборудованием. Капитальные вложения в подобный проект на 50%, а то и на порядок ниже, чем в проект с новым оборудованием. Следовательно, и срок окупаемости проекта меньше, и кредитная нагрузка ниже. Янош Дерьвари заверил, что оборудование, прошедшее предпродажную подготовку, при правильной эксплуатации гарантированно отработает в течение всего срока возврата инвестиций проекта.
Далее Александр Шалашов отметил, что ожидаются опережающие темпы роста мощностей предприятий, выпускающих плиты MDF, по сравнению с мощностями производств по выпуску ДСтП. Оптимальным для рынка считается соотношение объемов производства MDF и ДСтП 1:3. По данным Минпромторга России, в Перечень приоритетных инвестиционных проектов РФ в области освоения лесов включено 10 проектов по выпуску MDF общей мощностью 2200 тыс. м в год и 9 проектов по выпуску ДСтП суммарной мощностью 2500 тыс. м. Интересно, что в тот же перечень вошли 22 проекта строительства заводов по изготовлению OSB суммарной мощностью 6,9 млн м в год, что как минимум в три раза превышает прогнозируемую емкость рынка на 2015 год. По официальным данным, за 2008 год спрос на OSB в РФ составил 200 тыс. м. При этом дефицит OSB на рынке сохраняется, он привел к росту стоимости этого материала более чем в два раза. Дефицит составил около 80 млн м и покрывался за счет импорта из Канады и Польши.
По словам генерального директора ЗАО «ВНИИДРЕВ», тревожной выглядит ситуация на рынке синтетических смол для производства древесных плит. Учитывая темпы роста объемов производства плит в предыдущие годы, к 2015 году потребление всех видов формальдегидных смол для изготовления древесных плит, фанеры и пленки может вырасти до 2,1−2,3 тыс. т в год. Дефицит смол при этом может составить 600−800 тыс. т в год.
Доклад выступившего далее председателя оргкомитета конференции, профессора ЛТА Адольфа Леоновича был посвящен производственным стратегиям в период финансового кризиса, которые могли бы использовать заводы, занимающиеся выпуском ДСтП и MDF. Предложено две стратегии: для крупных производств (мощностью более 350 тыс. м в год) и для заводов малой мощности (менее 150 тыс. м продукции в год). Стратегической целью для крупных производств, работающих на современном высокопроизводительном оборудовании, является освоение проектных мощностей или хотя бы сохранение уже достигнутого уровня производительности. Достичь этого можно путем снижения себестоимости продукции и, соответственно, её рыночной цены. Для снижения себестоимости продукции докладчик предложил два метода уменьшения расхода связующего как одного из основных компонентов в структуре себестоимости.
Суть первого заключается в добавлении в карбамидоформальдегидную смолу (КФС) модификатора «Скар-Лет 104 Ультра». Испытания показали, что добавление модификатора позволяет добиться сразу нескольких положительных моментов: повысить качество плиты, уменьшить её плотность, сократить цикл прессования на 10−15%, а также уменьшить расход КФС на 1,5−2,5 кг при добавлении 1 кг модификатора на 1 м готовой продукции (то есть приблизительно на 10%). Правда, внедрение этого метода на производстве потребует наличия свободной площади и финансовых вложений примерно 100−150 тыс. руб.
Суть второго метода состоит в ограничении впитывания смолы стружкой. Поскольку часть смолы впитывается торцевой поверхностью стружки и при горячем прессовании не вступает в контакт с соседними древесными частицами, прочностные характеристики плиты не ухудшаются. Для того чтобы ограничить впитывание смолы стружкой, её можно обработать парафином в количестве 0,5−0,8% от массы абсолютно сухой древесины и подсушить. При этом парафин расплавится и впитается в стружку. При последующем нанесении связующего расход КФС сократится на 5−15%, а готовая продукция приобретет повышенную водостойкость. Реализация этого метода требует от 200 до 400 тыс. руб.
Что касается заводов малой мощности, здесь наилучшей стратегией будет диверсификация производства и освоение новых рыночных ниш.
Представитель компании «Фаэтон» (СПб.) Алексей Кузнецов рассказал об использовании древесных плит в деревянном строительстве. Как известно, наиболее широко древесные плиты применяются в каркасно-панельном домостроении. Одним из преимуществ этой технологии является низкая себестоимость квадратного метра жилья − от 14 до 18 тыс. руб. «Фаэтон» поставляет в Россию производственные комплексы немецкой компании Weinmann (Homag Group). Докладчик также объявил объем инвестиций: на закупку производственной линии мощностью 50−70 домов в год потребуется около 1 млн евро; линия мощностью до 1000 домов в год обойдется инвесторам в 10 млн евро. C 2003 года в России было построено 17 крупных домостроительных комбинатов (мощностью от 100 до 700 домов в год), работающих по каркасно-панельной технологии Weinmann. Технология производства состоит из восьми основных операций:
- изготовления деревянного каркаса;
- обшивки плитным материалом внутренней стороны стены каркаса;
- переворота каркаса и заполнения его теплоизолятором;
- обшивки плитным материалом внешней стороны стены каркаса;
- транспортировки элемента на вертикальный склад;
- установки в элементе окон и дверей;
- оштукатуривания внешней стороны стены;
- выдержки готового элемента на вертикальном складе.
Далее следует отгрузка и доставка элемента заказчику на панелевозе.
Начальник лаборатории ОАО «Витебскдрев» (Белоруссия) Иван Грошев рассказал о возможностях использования текстильных отходов в технологии производства древесно-волокнистых плит мокрым способом. Для изготовления нового материала, который назвали органо-синтетическая волокнистая плита − ОСВПт, в качестве основного сырьевого компонента в «Витебскдрев» использовали отходы стрижки искусственного меха, так называемый стригальный кноп, которого на ОАО «БелФа» (Белоруссия) ежегодно образуется около 2 тыс. т. При содержании текстильных отходов в плите ОСВПт 35% её плотность составляет 940−950 кг/м3, прочность на изгиб − 20−22 МПа, разбухание − 15%. За счет введения текстильных отходов в древесно-волокнистую массу удалось добиться упрощения и удешевления технологии производства ДВП, а также улучшить физико-механические характеристики готовой продукции.
Иван Грошев также сообщил об интересных исследованиях, касающихся возможности использования отходов коврового (ткацкого кнопа) и обувного производства (подносков) в технологии изготовления ДСтП. Эти отходы, если нужно, измельчают и добавляют к древесной стружке. Полученный в ходе испытаний материал, в составе которого было 40% отходов меха, имел высокую прочность при изгибе. Кроме того, на «Витебскдрев» изучалась возможность использования текстильных отходов для создания разного рода защитных покрытий для древесных плит. Чтобы получить ворсовое покрытие, на предприятии разработали и запатентовали специальное устройство воздушного нанесения защитных покрытий и композиционные смеси с добавкой из цветных коротковолокнистых отходов. Плиты с таким ворсовым покрытием могут быть с успехом использованы как при производстве мебели, так и в строительстве.
Представитель компании «Азия-Абразив» Олег Мургало предложил рекомендации, которые помогут производителям снизить затраты при шлифовании древесных плит:
- Правильно подбирать и хранить шлифовальные материалы − это продлевает срок их службы. Можно добиться снижения затрат при шлифовании, правильно выбрав тип абразивной ленты, тип шва ленты, а также марку графитового полотна. Если при шлифовании возникают повышенные нагрузки, то нужно использовать ленты на синтетической основе. На промежуточном шлифовании лучше использовать утюжки с подложкой из фетра или латекса, а на финишном − из мягкого полиуретана или фетра. На утюжок шлифовального станка следует устанавливать графитовое полотно марки HD. Хранить шлифленту лучше в транспортной упаковке и в хорошо вентилируемом помещении.
- При производстве плит следует стремиться к минимальному припуску на шлифование. Проблемы качества лучше решать с помощью формстанций и пресса, а не линии шлифования. С увеличением припуска на шлифование повышается расход шлифовальных материалов и износ оборудования.
- Позволит снизить затраты и свое-временная замена шлифленты и утюжков. Изношенный утюжок приводит к получению брака и повышению износа ленты, а иногда и к её разрыву.
- Четвертый совет очевиден, но от этого не менее полезен: работать нужно на правильно настроенном оборудовании.
Олег Мургало отметил, что 98% шлифовальных материалов, которые используются в отечественной плитной промышленности, поставляются из-за рубежа. В России остался лишь Белгородский абразивный завод, который производит шлифленту. Все остальные предприятия занимаются только нарезкой и склейкой абразивных материалов. Российские потребители шлифовальных материалов зачастую не знают, какой современный абразивный материал в какой ситуации лучше использовать и как правильно им пользоваться. Докладчик дал подробные рекомендации по рабочим нагрузкам и величинам съема материала в зависимости от зернистости шлифлент, по настройке шлифовального оборудования и методам устранения дефектов, возникающих при шлифовании древесных плит.
Руководитель московского бюро Electronic Wood Systems GmbH (Германия) Михаил Корабельников рассказал об измерительных системах, необходимых в производстве древесных плит. Для определения степени влажности фирма EWS выпускает ряд приборов, в которых используются разные методы измерения: в Micro-Scan − микроволновый метод, в MT-Scan − инфракрасный, а в MC-Scan − метод измерения электрического сопротивления. В двух первых системах применяется бесконтактный способ. В последней − контактный.
Mass-Scan предназначена для online-измерения качества насыпки ковра в производстве MDF. В ней используется метод рентгеновского излучения.
Система измерения толщины, которая так и называется Thick-Scan, используется для контроля качества плит после пресса. С её помощью проверяется соответствие продукции заданной толщине и разнотолщинность. Здесь применяется контактный способ измерения с помощью плавающих роликов. У роликов, которые и являются датчиками толщины, есть так называемый механизм памяти положения. Благодаря этому механизму, по словам докладчика, повышение скорости перемещения измеряемых панелей слабо сказывается на росте динамических нагрузок − ударов, вибраций, а также предотвращается подскакивание роликов при столкновении с краем следующей плиты. Thick-Scan совершает минимум движений и обеспечивает точность измерений в пределах 0,02 мм. Для пористых плитных материалов существует система под названием Thick-Scan L, в которой используется бесконтактный способ измерения с помощью лазера.
Система Ultra-Scan применяется для обнаружения расслоений внутри панелей. Она также используется для контроля качества плит на выходе пресса. В Ultra-Scan для измерений используется ультразвук − это так называемый метод акустического резонанса. Данная система незаменима при контроле качества особо толстых плит: мебельных до 100 мм и LVL − до 200 мм. Компания EWS поставила её на выходе непрерывного пресса LVL на новом заводе «Талион Терра» в Торжке. К преимуществам Ultra-Scan относится нечувствительность к пыли, пару и высокой температуре.
Для лабораторного анализа профиля плотности готовой продукции компания EWS разработала специальный рентгеновский анализатор Dense-Lab X. Он будет очень полезен для тонкой настройки производственного оборудования и контроля качества насыпки ковра при производстве MDF.
На конференции «Древесные плиты: теория и практика» также было сделано много научных докладов, посвященных получению и модификации связующих для древесных плит, снижению их расхода и т. п.
Михаил ЯШИН