Смолы на основе меламина для производства фанеры
Исповедь смоляного чучела
Рынок клееной фанеры может быть охарактеризован как насыщенный. Производство фанеры растет умеренными темпами, близкими к темпам роста мировой экономики.
В России выпуск фанеры стабильно увеличивается на протяжении последних 10 лет после значительного производственного спада в 1991 - 1994 годах, вызванного политическими и экономическими изменениями ситуации в России. С 1994 по 2003 год объем производства фанеры в России вырос в 2,49 раза, среднегодовой темп прироста составил 8,7 % (табл. 1 ).
Рост производства в России в большей мере определяется увеличением экспорта, чем внутреннего потребления. По нашим расчетам, 62% прироста фанеры в России с 1995 по 2003 год осуществлены за счет экспорта и лишь 38% - за счет внутреннего потребления.
Доля России в мировом объеме производства начала увеличиваться только с 1998 года. И если в 1997 году в РФ было произведено только 1,7% мирового объема, то в 2005-м эта доля составила уже 3,5%, то есть увеличилась более чем в 2 раза.
В настоящее время выделяют всего две марки фанеры общего назначения в соответствии с уровнем водостойкости: ФК и ФСФ.
Фактически классификация фанеры по маркам соответствует принятой в мировой практике классификации по возможности или невозможности использования ее для наружных элементов конструкций и оформления. Фанера ФК может использоваться без ограничений в производстве мебели и как конструкционный материал в условиях отапливаемых помещений. На нее приходится 69% российского производства фанеры общего назначения. Фанера марки ФК в России всегда выпускается форматом 1525 х 1525 мм.
Таблица 2. Объем производства фанеры в РФ по форматам и
маркам (2005 год)
Таблица 3. Характеристика газовых выбросов производства
феноло-формальдегидных смол
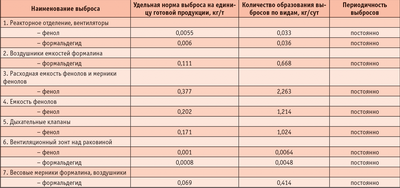
Очевидно, что 31% российского производства фанеры общего назначения составляет фанера марки ФСФ. В основном это большеформатная фанера, которая производится практически только на основе клеев повышенной водостойкости (табл. 2). Фанеру марки ФСФ используют как конструкционный материал в условиях более агрессивной внешней среды, в производстве опалубки, автофургонов и контейнеров.маркам (2005 год)

Таблица 3. Характеристика газовых выбросов производства
феноло-формальдегидных смол
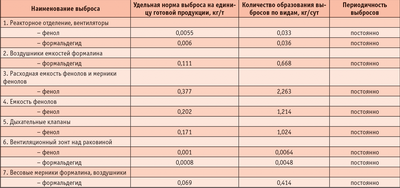
Для изготовления фанеры марки ФСФ применяются фенолоформальдегидные смолы. Однако феноло-формальдегидные смолы токсичны и являются экологически опасными вследствие токсичных газовых выбросов.
Суммарное количество токсичных газовых выбросов из хранилищ сырья, емкостей аппаратов, мерников и другого технологического оборудования составляет 700-1000 м/ч. Содержание вредных веществ в газовых выбросах, в частности по фенолу, во много раз превышает нормы ПДК (табл. 3). Это привело к прекращению выпуска фанеры на ряде деревообрабатывающих предприятий.
Больших объемов фанеры на основе меламино-формальдегидных смол и клеев в России пока нет. В 2005 году компания UPG (Жешартский фанерный комбинат) начала осваивать производство фанеры на основе меламиновых смол. Однако объем производства фанеры на таких смолах остается очень незначительным.
В данный момент разработки и освоение меламиновых смол и клеев для производства клееных материалов из древесины имеют большое практическое значение для лесопромышленного комплекса России. В США и на европейском рынке заметно снижение спроса на поставляемую отечественную водостойкую фанеру на основе феноло-формальдегидных смол и клеев. Одновременно с этим наблюдается высокий спрос на водостойкую низкотоксичную фанеру на основе меламино-формальдегидных клеев, которая в отличие от фанеры марки ФСФ не только экологически безопасна, но и отличается большой атмосферостойкостью. Экологически чистая и атмосферостойкая фанера на меламиновых клеях занимает основную часть экспорта в США и страны Евросоюза.
Следует особенно отметить, что страны Евросоюза подготавливают законодательство по химической безопасности продукции, начало действия которого запланировано на 1 января 2008 года. Согласно данному законодательству, все виды поставляемой продукции должны проходить тест на анализ выделяемых вредных летучих химических веществ. По мнению специалистов ЕС, это позволит прекратить поступление продукции с вредными химическими веществами, в том числе и фанеры, в страны Евросоюза. Новое европейское химическое законодательство (РИЧ) «Распоряжение о порядке регистрации, оценки и одобрения химических веществ» устанавливает правила, достаточно жесткие и непростые для исполнения.
Российские предприятия, в том числе и деревообрабатывающие, не смогут поставлять в страны ЕС продукцию без регистрации всех химических веществ, которые входят в ее состав. В том числе это коснется поставляемой на экспорт фанеры. Фанера, не прошедшая тест на химическую безопасность, будет возвращена обратно уже на границе. Если же продукции все-таки удастся проникнуть на территорию ЕС без регистрации ее химических компонентов, поставщиками займется химическая полиция.
Одним из направлений снижения токсичности является переход на использование в производстве фанеры низкотоксичной меламиновой смолы.
Меламино-формальдегидные смолы (МФС) являются одним из известных синтетических продуктов, которые широко применяются в качестве основы для производства клеев, связующих, ламинатов, ДСП, лаков и эмалей. В данный период наблюдается рост производства древесностружечных плит и отделочных бумажно-смоляных пленок повышенного качества с использованием стабильных при хранении меламиновых смол.
Реакция меламина с формальдегидом подчиняется закономерностям общего кислотно-основного катализа, причем величина рН не только определяет скорость реакции, но и структуру образующейся смолы.
Поскольку меламин имеет три аминогруппы, возможно образование девяти различных метиломеламинов. Метилольные производные образуются из меламина и формальдегида и образуют метиленовые и метиленэфирные мостики. Кроме этого, протекает реакция разложения метиленэфирных мостиков с образованием метиленовых мостиков. Таким образом, в условиях реакции синтеза меламиновых смол диметиленэфирные мостики и метиленовые мостики образуются одновременно. На рис. 1 представлена схема поликонденсации.
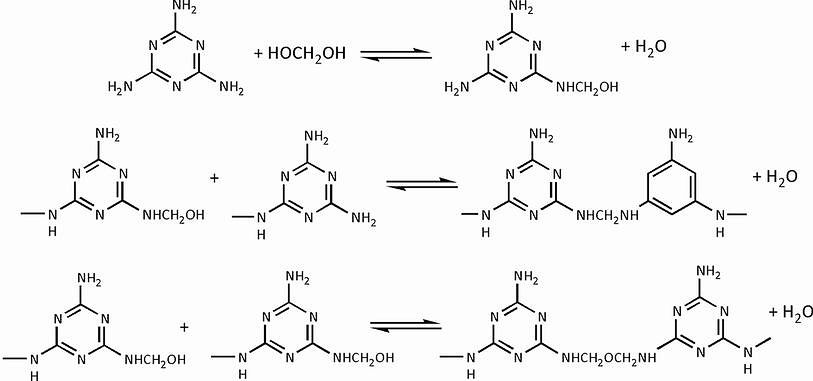
Рис.1. Поликонденсация
Механизм стабильности при хранении растворов меламиновых смол является комплексным и включает различные процессы, которые, возможно, происходят одновременно в растворе смолы с определенной степенью конденсации. Стабильные при хранении меламиновые смолы можно получить только при строго определенных условиях. Полученные смолы в процессе хранения при температуре 20-250°С из прозрачных жидкостей превращаются в мутные гели, а затем переходят в твердоподобное состояние. При нагревании таких гелей и масс меламиновые смолы становятся вновь прозрачными жидкостями.
Явление нестабильности растворов меламиновых смол при хранении и его взаимосвязь с условиями синтеза смол и их строением исследовано в работах специалистов фирмы DSV Melamine (Нидерланды), одной из ведущих фирм в мире среди производителей меламина. В результате исследования установлено, что нестабильность меламиновых смол вызвана процессом физического гелирования за счет водородных связей; образование агрегатов меламиновых смол происходит сразу же после охлаждения смолы от температуры синтеза до комнатной и продолжается в течение определенного временного периода. Процесс отверждения меламиновых смол - продолжение химических реакций их синтеза.
Таблица 4. Основные свойства меламино-формальдегидной смолы
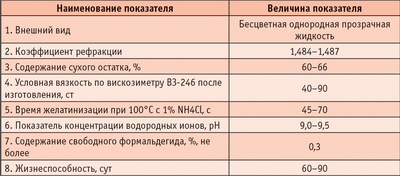
Таблица 5. Свойства смол
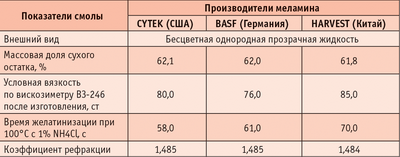
Изученные закономерности позволили разработать технологию производства стабильных низкотоксичных меламино-формальдегидных смол и клеев на их основе. Основные показатели данных смол приведены в таблице 4.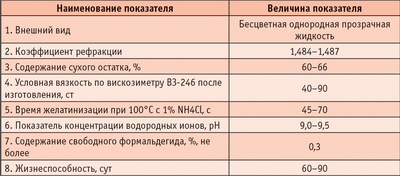
Таблица 5. Свойства смол
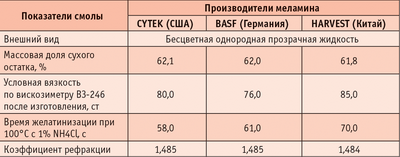
Меламино-формальдегидные смолы могут выпускаться на обычном установленном в цехе смол оборудовании, а меламиновые клеи приготовляются в обычных смесителях, имеющихся на фанерных заводах. Таким образом, синтез меламиновых смол и приготовление клеев на их основе не требуют дополнительного оборудования и дополнительных капитальных затрат.
От основного поставщика меламина в Санкт-Петербурге - Единой торговой системы - была получена опытная партия меламина производства США, Германии и Китая. Из полученных партий меламина были изготовлены опытные партии меламиновых смол. Основные показатели данных смол приведены в таблице 5.
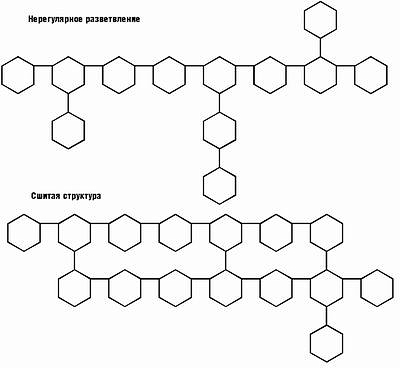
Рис.2. Структура отверждения меламинового полимера
Отвержденные пленочные покрытия на основе меламиновых смол придают поверхности твердость, прозрачность, устойчивы к образованию пятен, пожелтений и имеют общую износостойкость. Кроме того, основная структура меламиновой смолы, то есть основные преимущества метилирования - это быстрое отверждение, улучшение стойкости к действию окружающей среды.
С целью оценки прочности фанеры, изготовленной с применением клеев на основе меламино-формальдегидных смол, и предварительного установления условий и режима склеивания шпона был поставлен ряд экспериментов. Они проводились с использованием смол, изготовленных на меламине китайского и американского производства. Ряд показателей этих смол, параметры условий и режимы склеивания приведены в таблице 6.
Таблица 6. Свойства использованных смол, параметры условий и
режима склеивания
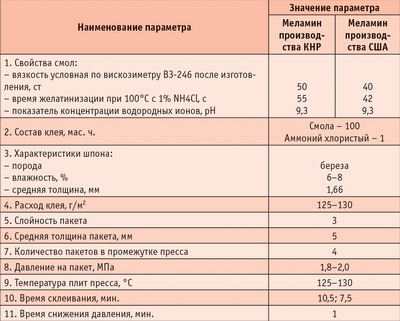
Таблица 7. Сравнительные результаты испытания фанеры
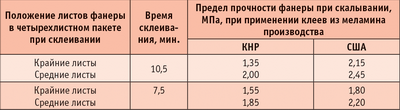
Таблица 8. Нормативная прочность фанеры

Сравнительная оценка прочности экспериментальных образцов фанеры, склеенной с применением меламиновых смол из меламина вышеуказанных производителей за различное время, проводилась в соответствии ГОСТ 9624 после кипячения в течение 6 ч. Результаты испытаний фанеры приведены в таблицах 7 и 8.режима склеивания
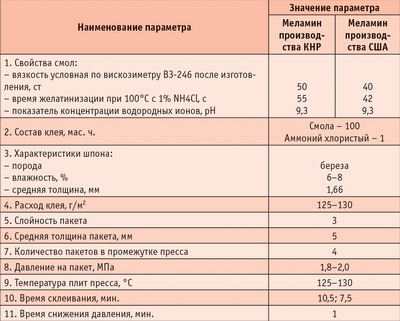
Таблица 7. Сравнительные результаты испытания фанеры
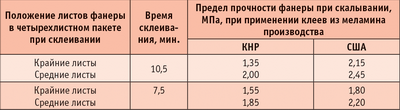
Таблица 8. Нормативная прочность фанеры

Из таблицы 7 видно, что прочность крайних листов в пакете для всех условий склеивания на 12-30% ниже, чем средних. Это, вероятно, связано с термоупругими напряжениями, возникающими при нагреве отвержденного за принятое время склеивания клеевого слоя. С учетом этого обстоятельства и достигаемой высокой прочности склеивания средних листов в пакете можно считать, что даже время склеивания 7,5 мин. выше требуемого. Следует отметить, что время склеивания такой же фанеры на феноло-формальдегидных клеях (12,4 мин.) значительно больше, чем минимально принятое - 7,5 мин. Полученный результат позволяет увеличить производительность процесса склеивания фанеры повышенной водостойкости.
Нормативная прочность фанеры с учетом доверительного интервала, равного 1,68 среднего квадратичного отклонения, приведена в таблице 8.
Данные, приведенные в таблице 8, свидетельствуют о более низкой прочности склеивания при применении смолы на основе меламина производства КНР по сравнению с произведенным в США.
Таким образом, прочность фанеры, использующей клей на основе меламина производства КНР и США, отвечает требованиям ГОСТ 3916.1 не менее 1,2 МПа.
На основании результатов проведенной работы можно сделать следующие выводы:
1. Освоение производства меламиновых смол обусловит:
- исключение из технологического процесса изготовления водостойких смол высокотоксичного компонента - фенола - и, как следствие, ликвидацию на деревообрабатывающих предприятиях участков по его приемке и хранению в подогретом (до температуры 42-50°С) состоянии;
- улучшение экологических показателей окружающей среды из-за отсутствия высокотоксичных газовых выбросов в атмосферу, а также сточных вод;
- уменьшение вредного влияния на организм человека ядовитых веществ - меламин на порядок менее токсичен, чем фенол.
2. Разработка и освоение технологий производства меламино-формальдегидных смол и изготовления фанеры позволит предприятиям лесопромышленного комплекса:
- получить экологически безопасную древесную клееную продукцию повышенной водо- и атмосферостойкости для использования в строительстве, в частности в домостроении, на транспорте и в производстве мебели;
- уменьшить не менее чем на 20% время склеивания в сравнении со временем склеивания на феноло-формальдегидных клеях, а также тепловые затраты на производство фанеры;
- уверенно конкурировать на рынке высоководостойкой фанеры с другими странами.
Владимир КОНДРАТЬЕВ, Алексей ЧУБОВ, Никита БЕЛЯЕВ
Благодарим за предоставленную информацию Центральный научно-исследовательский
институт фанеры
Благодарим за предоставленную информацию Центральный научно-исследовательский
институт фанеры