Древесные плиты
Экзамен на стойкость
21–22 марта 2023 года в Санкт-Петербургском государственном лесотехническом университете им. С. М. Кирова прошла XXVI Всероссийская научно-практическая конференция «Древесные плиты и фанера: теория и практика». Участники обсуждали как узкоспециальные вопросы о разработке карбамидоформальдегидных связующих, так и прикладные, вроде повышения биостойкости древесных плит.
Начнем с очевидного. В 2022 году трясло весь лесопромышленный комплекс, производителей древесных плит и фанеры в том числе. По данным аналитического агентства WhatWood, производство MDF/HDF/ДВП за год снизилось на 12%, ДСП – на 14%, а фанеры – на 27%. К этому привело как уменьшение экспортных возможностей, так и снижение потребления древесных плит на внутреннем рынке.
Каждый производитель решает сам, что делать в такой сложной ситуации: одни ждут лучших времен, другие ищут новые рынки сбыта, а третьи думают о модернизации производства и новых продуктах. Понятно, что последним нужно либо перенимать удачный опыт коллег, либо искать перспективные технологии. И то, и другое возможно на научно-практической конференции.
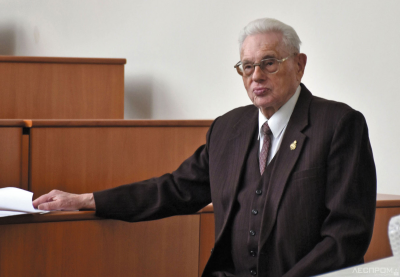
С момента создания конференция была направлена на развитие сотрудничества ученых и инженеров – на тот самый сплав теории и практики, который способствует прогрессу технологий производства древесно-стружечных и древесно-волокнистых плит. Но, как отмечают организаторы, в последние годы ситуация изменилась не в лучшую сторону: предприятия теряют интерес к развитию собственных научных разработок, и российская промышленность базируется на зарубежных технологиях и оборудовании. Однако конференция по-прежнему предоставляет участникам возможность обменяться опытом по тем или иным техническим вопросам.
Обсуждались разные темы практической направленности. Если использование ядерного магнитного резонанса для анализа формальдегидсодержащих смол в перспективе расширит научные горизонты, то в теплоизоляционных древесно-волокнистых материалах, получаемых методом задувания, уже сейчас заинтересованы, например, строители. Периодически обсуждение переходило с технических вопросов на социально-экономические – выживание градообразующих предприятий, обучение специалистов, развитие отрасли.
Наука производству
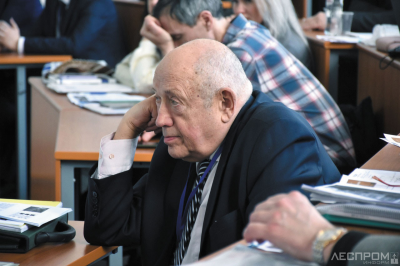
Профессор кафедры технологии древесных и целлюлозных композиционных материалов СПбГЛТУ Адольф Леонович привел пример, как технологии позволяют вовлечь в работу новые сырьевые запасы, например, использовать ту же осину, которая не блещет механическими свойствами. После пропитки карбамидом можно на обычном прессовом оборудовании производить из нее паркет, который в четыре раза прочнее исходной древесины. При этом его плотность повысилась не столь значительно, примерно с 400 до 600 кг/м3. Это не новая разработка, но показательная.
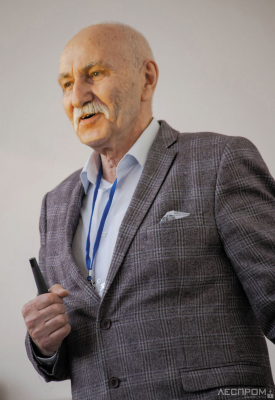
Своими результатами поделился и начальник ЦЗЛ «Витебскдрев» Иван Грошев. В рамках достижения стратегической цели по переработке имеющегося запаса сырья на предприятиях в Белоруссии и обеспечения реализации продукции с высокой добавленной стоимостью лаборатории, которой он руководит, поставили задачу разработать три вида плит: огнестойкие, водостойкие, биостойкие. На данный момент водостойкая плита MDF уже производится и даже экспортируется. Водостойкость плите придают органосиликаты, взаимодействующие с древесиной. Технология не требует нового оборудования, меняются лишь производственные режимы и реагенты. Себестоимость плит выросла лишь на 10%.
О том, как можно дополнительно использовать в производственном процессе отходы лесозаготовок, рассказал доцент кафедры органической химии и технологии органических веществ филиала СибГУ в г. Лесосибирске Алексей Кукушкин. Если вводить фунгистатический препарат в древесно-волокнистый полуфабрикат на стадии подготовки волокна, можно получить равномерно окрашенную в объеме ДВП с повышенной биостойкостью.
Кафедра технологии древесных и целлюлозных композиционных материалов СПбГЛТУ предложила для индустриального производства использовать древесное волокно, которое образуется при производстве ДВП сухим способом. Метод задувания материалов плотностью 40–80 кг/м3 в полости конструкций позволяет повысить их теплоизоляционные характеристики. Этой технологией уже не одно десятилетие пользуются американцы, но в качестве сырья они используют макулатуру, которую сложно собирать и перерабатывать. Кроме того, материалы плохо работают на вертикальных поверхностях – со временем оседают, то есть образуются пустоты. С оседанием можно бороться разными методами: конструкционным (делить полости на меньшие объемы), технологическим (модифицировать волокно добавками) и рецептурным (включить в состав жесткий наполнитель и сделать волокно гидрофобным). В результате удается добиться стабильной, не имеющей дефектов новой формы теплоизоляционного древесно-волокнистого материала.
Лучше вы к нам
Живая дискуссия – важная составляющая конференций, форумов и других встреч отраслевых профессионалов, причем обсуждение нередко идет нелинейно. В этот раз неожиданно болезненную тему затронул генеральный директор компании «Профи» Михаил Тарасенко, призвавший предприятия периодически устраивать экскурсии для своих технологов.
«Когда человек работает на одном и том же заводе, у него замыливается глаз, – констатировал спикер. – Он перестает видеть мелкие нарушения технологии. Поэтому, уважаемые представители заводов, посылайте своих технологов друг к другу. И ваши люди, и технологи ваших конкурентов будут обновлять собственное видение, это может принести пользу предприятию.
Сейчас узкопрофильных специалистов у нас ни один институт не выпускает, это исключительно практики, которые годами наработали некие знания. Поэтому квалификация ваших специалистов зависит от опыта, и она становится ниже, если они не видят других производств. На деревообрабатывающих заводах обмен специалистами – это обычная практика. Поверьте, ничего принципиального у вас не украдут, потому что ничего принципиально нового нет. Зато визиты на соседние предприятия заставляют сотрудников думать».
Представители отрасли чуть ли не единодушно возразили: если в советское время обмен опытом так и происходил, то сейчас этого нет и не будет. Даже иностранные компании вроде IKEA, отправлявшие своих работников с российских предприятий на заводы во Франции или Германии, учили своеобразно: говорили, что надо делать, но не объясняли почему.
Представители предприятий не готовы пускать на производство технолога от конкурентов. Пусть он не сможет повторить всю технологическую цепочку, но, просто скопировав что-то на своем уровне компетенции, уже станет более дееспособным.
Масла в огонь подлил главный специалист технической поддержки «ПК ТС» Николай Романов. «Если я приеду на предприятие, которое производит смолу, и пройду по складу, мне станет ясно, что делают. А если поднимусь на пульт управления, где делают смолу, то пойму, как делают. Нет, чужих специалистов пускать к себе нельзя!» – заключил он.
Алексей Кукушкин предложил компромиссный вариант. «У нас в регионе, за Уралом, не так много предприятий, занимающихся производством лекарственных препаратов. И у них сформировался определенный портфель работников, которыми они обмениваются. Раз в год начальники кадровых служб этих предприятий сидят вместе, пьют чай и думают, какого технолога на какого поменять, потому что одному хочется переехать, хочется развития, а другому – заниматься более творческой деятельностью, пускай и далеко. У нас это проще. Я призываю коллег из других отраслей перенять такой опыт, главное, чтобы это не противоречило коммерческим тайнам предприятий», – сказал представитель СибГУ.
Чтоб не пропасть поодиночке
Докладчики, не сговариваясь, регулярно, возвращались к теме взаимодействия отраслей. Например, руководитель ассоциации «Лестех» Александр Тамби призвал комплекс¬но развивать разные предприятия на одной территории, поскольку отходы одного могут быть сырьем для другого. «Нужно комплексно развивать и лесопиление, и плитную, и фанерную промышленность, потому что те бревна, которые мы заготавливаем на лесосеке, являются сырьем для предприятий сектора В2В, – пояснил спикер. – В идеале ставить в середине территории крупное целлюлозно-бумажное предприятие, которое будет перерабатывать балансовую древесину».
Михаил Тарасенко заметил, что многие вопросы, с которыми он сталкивался, уже успешно решены в смежных отраслях промышленности. К примеру, много пересечений он отмечает у деревообработки, текстильной промышленности и производстве гидроизоляции. Как представитель химической отрасли он также предостерег, что уже зафиксированный дефицит некоторых компонентов, которые не производились в России, может выйти на новый уровень.
«Бывает, что на заводах надо подкорректировать технологию – немножко, в рамках разумного. Это поможет пользоваться тем сырьем, которое есть. – заметил директор ООО “Профи”. – Но сами заводы выступают принципиально против, они не хотят решать проблемы и требуют весь комплект реагентов полностью.
Плитные производства по большей части гиганты, они привыкли немного задирать нос. Но наша химическая промышленность ровно в тех же условиях, а запросы к ней идут из разных отраслей. Обращаюсь к представителям заводов: если вы сейчас отвернетесь, химическая промышленность развернется к текстильной отрасли и все свои объемы направит туда. А когда вам понадобятся материалы, производственных мощностей на вас уже не хватит. Будьте коммуникабельнее».
Другой пример того, как разные отрасли могут найти общий интерес, дала сама конференция. Если в докладе Адольфа Леоновича речь шла о производстве волокна для утеплителя, то Алексей Кукушкин рассказывал о переработке отходов лесозаготовки в волокно, причем с фунгицидами. То есть выстраивается цепочка бенефициаров: одним нужно сбыть отходы лесозаготовки, другим – получить волокна с фунгицидами для теплоизоляции, четверым – производить из этих волокон плиты. И дело еще не дошло до конечных потребителей, тех самых строителей, которые получат не только новые материалы, но и возможность решить нерешаемые прежде задачи.
В заключение
Конференция «Древесные плиты и фанера: теория и практика» прошла уже в 26 раз; участники отмечали сильные стороны организации и высказывали пожелания на будущее.
«В Союзе было распределение, и все специалисты знали друг друга, и нечего было скрывать, – сказал Иван Грошев. – С появлением рынка ситуация изменилась, появились новые производства, стали секретничать. Я вспоминаю девяностые годы, первые конференции, был информационный голод, люди впитывали информацию как губки. Спасибо ВНИИДРЕВ и СПбГЛТУ, что они сделали эту конференцию. Нонужно что-то менять, например, делать тематические конференции. На рынок приходят новые материалы, по информации некоторых аналитиков ДСП исчезнет лет через 7–10, а мы не готовы к этому».
Николай Романов предложил организаторам обратить больше внимания на перспективное, на его взгляд, направление: «Очень любопытная тенденция, – идея в том, чтобы заменить формальдегид, исключить его и сделать связующие для плитных материалов на основе растительного сырья: лигносульфатов, лигнина».
Доцент кафедры технологии древесных и целлюлозных композиционных материалов СПбГЛТУ Даниил Иванов от лица организаторов пояснил: «Надо понимать, в чем особенность нашей конференции – это событие не уровня генеральных директоров или менеджмента, которые думают о глобальных вещах, это конференция уровня инженера. Одна из немногочисленных площадок, где специалисты могут собраться и поделиться мнением о каких-то технических или технологических моментах. Учитывая, что конференция существует больше 20 лет и на нее люди каждый год приезжают и приезжают, значит, мы своей цели добиваемся».
Конференция «Древесные плиты и фанера: теория и практика» проходит каждый год, но регулярно меняет площадку. В четном 2024 году ее участников соберет второй организатор – ВНИИДРЕВ в городе Балабаново Калужской области.
Текст Роман Иванов