Отделка смолистой древесины
Проблемы и решения
Растительные смолы хвойных пород – это сложные смеси разных индивидуальных веществ, еще недостаточно хорошо изученные. Компоненты смол нелетучие, поэтому не пахнут. И все же, несмотря на разнообразие химического состава смол, общие характерные свойства позволили выделить их в особую группу природных продуктов.
Древесная смола – это «коктейль» из самых разных химических соединений: пиненов, терпеновых кислот, спиртов и многих других. Основное значение этого природного антисептика для растущего дерева – залечивание любых повреждений камбия и ствола.
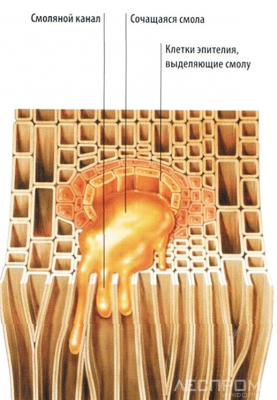
Горизонтальные смоляные ходы проходят через годичные слои и, пересекаясь с вертикальными каналами (рис. 1), соединяются, образуя единую смолоносную систему ствола дерева. В 1 см3 древесины ствола насчитывается 250–600 таких соединений. Это облегчает передвижение живицы из внутренних слоев заболони к различным повреждениям ствола и ранениям при подсочке.
Размеры смоляных ходов зависят от возраста дерева, его диаметра, размеров трахеид и условий произрастания. В наружных слоях ствола средневозрастных деревьев сосны диаметр вертикального смоляного хода достигает 60–80 мкм, приспевающих деревьев – 90-100 мкм, спелых – 110–120 мкм и даже 130 мкм. В среднем диаметр вертикального смоляного хода можно принять равным 100 мкм, или 0,1 мм. При полном заполнении живицей диаметр канала составляет 80% диаметра смоляного хода, или 0,08 мм.
Длина горизонтальных смоляных ходов определяется длиной сердцевинных лучей, однако до сердцевины ствола эти ходы не доходят, так как лучи со смоляными ходами всегда вторичны. Длина деятельной части горизонтального смоляного хода значительно меньше его общей длины и не превышает толщину заболони у хвойных пород.
Длина вертикальных смоляных ходов составляет от 10 до 80 см, а в отдельных случаях достигает одного метра.
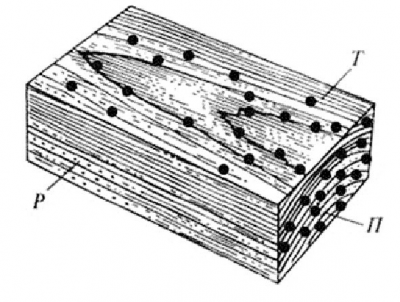
Невооруженным глазом можно обнаружить только вертикальные смоляные ходы, а связанные с ними горизонтальные ходы видны только под микроскопом. Смоляные ходы заметны на поперечном разрезе в зоне поздней древесины годичного слоя в виде белых точек (у сосны и кедра там сосредоточено около 2/3 их общего количества), на радиальном и тангенциальном разрезах – в виде темноватых продольных черточек и линий (рис. 2). Наиболее крупные смоляные ходы у кедра, их средний диаметр 0,14 мм, сосны – 0,1 мм, ели – 0,09 мм, лиственницы – 0,08 мм. Длина ходов 10–80 см. Смоляные ходы занимают от 0,2% (ель, лиственница) до 1% (кедр, сосна) общего объема ствола. Наибольшее количество ходов отмечается на тангенциальном и поперечном разрезах.
Установлено, что в 1 м3 древесины сосны содержится примерно 4 кг живицы, причем в вертикальных смоляных ходах 3,5 кг, а в горизонтальных – 0,5 кг. То есть горизонтальные смоляные ходы не так важны для смоловыделения, как вертикальные, но при подсочке с химическим воздействием их роль существенно возрастает, поэтому пиломатериалы, полученные из подсоченного пиловочного сырья, особенно из вершин и комлевой части, пожалуй, наиболее проблемные с точки зрения дальнейшей переработки и отделки готовых изделий.
Смола хвойных деревьев пока остается почти непреодолимым «врагом» производителей деревянной продукции – мебели, дверей и окон, клееных конструкций, музыкальных инструментов и т. д. Хвойная древесина пользуется немалым спросом, поскольку она относительно недорогая, упругая, прочная и отличается красивой структурой. Но из-за высокого содержания смолы быстро изнашиваются режущие инструменты, затрудняется обработка древесины и формирование декоративного и защитного слоев на основе различных лакокрасочных материалов (ЛКМ).
Кроме смоляных ходов, смола может содержаться в сучках, смоляных кармашках, засмолках, трещинах, что также отражается на качестве отделанной готовой продукции.
Молекулы смол связаны не химическими связями, а межмолекулярными силами сцепления, которые легко нарушаются при нагревании или растворении. При этом на поверхности растворов или расплавов появляются свободные, не связанные друг с другом молекулы смоляных компонентов с большим запасом свободной энергии. За счет этой энергии они могут захватывать и удерживать молекулы других веществ, которые приближаются к поверхности раствора или расплава. Вот почему растворы или расплавы смол липкие и у такой поверхности низкая адгезия, например, к лакокрасочным материалам и клеям.
Отделка
Отделка деревянных деталей и изделий заключается в создании на их поверхности покрытий, защищающих от механического, химического и теплового воздействия, влажности, ультрафиолетового излучения и т. д. Кроме того, отделка придает изделию высокие эстетические и декоративные свойства. Выбор вида и способа отделки зависит от специфических свойств древесины. Различают прозрачную, непрозрачную, имитационную и комбинированную отделку деревянных изделий и деталей.
Прозрачными лаками покрывают изделия из массивной древесины красивой текстуры и облицованные шпоном или декоративными (чаще текстурными) бумагами.
Непрозрачные лакокрасочные покрытия меняют цвет и делают невидимой текстуру отделываемой поверхности за счет использования материалов разных цветов с высокой укрывистостью. Такими материалами являются краски, эмали, порошки, грунтовки и шпатлевки на основе карбамидоформальдегидных, полиэфирных и других смол. Для отделки поверхности изделий, выполненных из малоценных пород древесины, плитных или листовых материалов, применяют непрозрачную пленку, ЛКМ, пластик или бумагу.
Имитационная отделка улучшает декоративные свойства поверхности обычных древесных и композиционных материалов за счет наклейки пленок, чаще всего имитирующих текстуру ценных пород древесины или фактуру тканей, камня, или на основе пропитанных бумаг с глубокой степенью отверждения смолы. Имитационная отделка позволяет экономить шпон и плитные материалы при раскрое, упрощает подбор текстурного рисунка смежных лицевых элементов мебели, в первую очередь дверей. Комбинированные покрытия – это сочетание пленочных или бумажных покрытий с последующим нанесением на них различных лакокрасочных материалов.
При отделке изделий из древесины мягких пород для укрепления поверхности необходимо наносить твердый слой грунта или шпатлевки, служащий подложкой для основного покрытия. В противном случае поверхность легко истирается, крошится, покрывается царапинами. Древесину твердых пород перед отделкой не укрепляют.
Грунтование применяется для снижения расхода дорогостоящих лаков, красок, эмалей за счет уменьшения впитывающей способности подложки и обеспечения прочного сцепления последующих покрытий с древесиной. Некоторые грунтовки предназначены для создания цветового фона под печать текстуры древесины, повышения электропроводности изделий при отделке в электрическом поле высокого напряжения. Различают карбамидные, нитрокарбамидные, полиэфирные грунтовки, на базе ПВА-дисперсии, полиакриламида, а также УФ-отверждаемые. В состав грунтовок входят пленкообразователи, растворители, поверхностно-активные вещества и ряд целевых добавок.
При непрозрачной отделке для заполнения и сглаживания неровностей поверхности древесины применяются шпатлевки – смесь пигментов, минеральных наполнителей и связующих веществ. На мебельных и деревообрабатывающих предприятиях, выпускающих продукцию полной заводской готовности (паркет, окна, двери и т. д.) широко используются нитроцеллюлозные быстросохнущие и акриловые водостойкие шпатлевки, в том числе УФ-отверждаемые.
Смола на поверхности древесины либо в непосредственной близости к ней снижает адгезию ЛКМ и подложки, затрудняет крашение и может снизить качество лакокрасочного покрытия (ЛКП). Разработчики ЛКМ предлагают специальные композиции для отделки смолистых пород, изолирующие смолу внутри подложки и препятствующие ее выходу на поверхность ЛКП за счет создания барьерного слоя. В связи с уходом с российского рынка ведущих европейских производителей ЛКМ проблема отделки смолистой древесины обострилась.
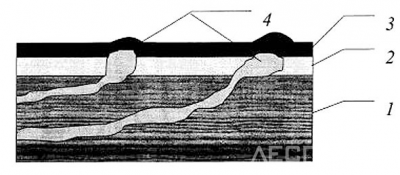
При общепринятой схеме покрытия (рис. 3) сначала с поверхности древесины удаляется смола, далее наносится грунтовочный состав, а на него защитно-декоративное покрытие (ЗДП).
Сегодня применяется несколько способов удаления смолы с лицевых отделываемых поверхностей изделий из хвойной древесины:
- обессмоливание химическими составами;
- специальный раскрой пиломатериалов;
- вырезка всех пороков строения древесины из пиломатериалов и сращивание заготовок по длине;
- правильная сушка пиломатериалов с полимеризацией смолы;
- специальная гидротермическая обработка пиломатериалов;
- использование комбинированных покрытий
- обработка готовых изделий барьерными (изолирующими) грунтами.
Обессмоливание
Возможны два способа обессмоливания.
Один – растворение смолы на поверхности ацетоном, спиртом, бензолом, четыреххлористым углеродом и другими веществами. Все применяемые растворители огнеопасны и токсичны.
Второй – смывание смолы с поверхности омыляющими составами: растворами углекислого натрия (Na2CO3, 5–6%), углекислого калия (K2CO3, 5–6%), едкого натрия (NaOH, 4–5%). Но под действием щелочи древесина темнеет.
Обессмоливание дает кратковременный эффект устранения смолы с поверхности.
Специальный раскрой пиломатериалов
Смола появляется на лицевой поверхности деревянного изделия из сучка, засмолка или смоляного кармана, не удаленных на этапе производства заготовки.
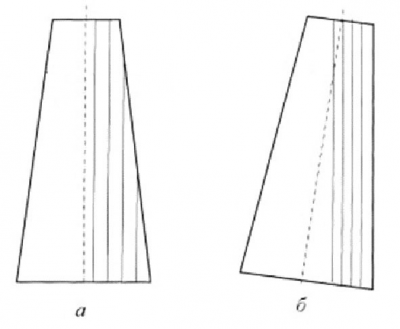
При стандартном раскрое досок параллельно оси пиловочного бревна смола выступает на пластях и кромках пиломатериалов, поскольку перерезается много годичных слоев, в том числе поздние зоны годичных колец, в которых в основном и находятся смоляные ходы.
В связи с этим считается, что распиловку бревен следует выполнять параллельно образующей бревна, а обрезку досок – параллельно образующим кромок доски (рис. 4), и не использовать для производства мебели и некоторых столярно-строительных изделий (например, элементов дверной коробки) комлевую и фаутную (перестойную) часть ствола сосны, лиственницы и кедра.
Понятно, что при массовом производстве продукции и закупке готовых пиломатериалов реализовать это не представляется возможным.
Вырезка пороков и сращивание заготовок
Вырезка всех пороков строения древесины из пиломатериалов и сращивание заготовок по длине, ширине, толщине – довольно эффективные способы удаления смолы, позволяющие получить качественное ЗДП при отделке. При вырезке всех дефектов строения ствола можно вовлечь в переработку практически любую низкосортную древесину. Однако из-за высокого отпада древесины в результате вырезки дефектов из пиломатериалов эффективность такого способа не всегда является адекватной.
Общий недостаток способов – высокая себестоимость готовой продукции.
Правильная сушка пиломатериалов с полимеризацией смолы
Для получения качественных отделочных покрытий влажность древесины не должна превышать 8 ± 2%. Древесину такой влажности используют при производстве столярно-строительной продукции и мебели.
При сушке древесины сосны выделяют три основных режима:
- без выгонки смолы – до 55°С;
- с выгонкой смолы – 55–70°С;
- с отверждением или кристаллизацией смолы – 75–85°С.
В последнем случае для отверждения смолы сушка при такой температуре должна продолжаться не менее 24 ч, а лучше 48–72 ч. Речь идет, разумеется, о конечном этапе сушки, так как при высокой влажности такая начальная температура не обеспечит полимеризацию смолы. Наиболее интересен более жесткий режим сушки, до 110–115°С, гарантирующий получение древесины с полимеризованной смолой, правда, если эта древесина не будет использована как конструкционная.
Недостаток сушки – необходимость высокотемпературных сушильных камер.
Специальная гидротермическая обработка пиломатериалов
Возможны несколько вариантов.
- Температурная обработка в конце сушки при 200–300°C для «выпаривания» смолы и испарения ее жидкой части – живицы (в основном скипидара) с поверхности. При этом твердый остаток – канифоль теряет текучесть.
- Впрыск специальной водяной аэрозоли с веществом, выступающим в роли порозаполнителя, в сушильную камеру и осаждение этого раствора на поверхности обрабатываемых досок. Затем диффузия вещества в вакуумной сушильной камере внутрь древесины (на глубину 3–5 мм с учетом последующей механической обработки) и подсушка поверхности пиломатериалов.
- Погружение пиломатериалов в емкость с водным раствором этого порозаполнителя и выдержка (для пропитки на глубину 3–5 мм).
Недостаток способа – высокая себестоимость готовой продукции.
Использование комбинированных покрытий
Использование пленочных или бумажных покрытий, например, для погонажных заготовок, с применением укуточного оборудования и клеев-расплавов и последующее нанесение лакокрасочных материалов гарантируют стопроцентное качество. Такой способ эффективен для разных древесных материалов, в том числе клееных.
Недостаток – необходимость разного технологического оборудования.
Обработка готовых изделий барьерными грунтами

Вместо обычного грунтовочного состава наносится грунт, изолирующий смолу внутри древесины и не позволяющий ей выходить наружу (рис. 5). За счет этого значительно повышается качество ЗДП.
Получаемые покрытия отличаются высокими декоративными свойствами. Согласно разным исследованиям, барьерные грунты создают прочную и светоустойчивую пленку, защищающую заготовку от воздействия внешних факторов и повышающую адгезию. Финишное покрытие, нанесенное на барьерный грунт, создает более прочную, ровную, гладкую пленку и улучшает внешний вид заготовки в сравнении с окрашиванием неподготовленной поверхности. Грунт заполняет микронеровности заготовки и обеспечивает запечатывание смолы внутри нее, повышает адгезию краски, которая ложится равномерно, без дефектов. Это упрощает технологический процесс, способствует экономии ЛКМ, уменьшает долю бракованных изделий.
Напрашивается вывод
Наиболее эффективные решения при отделке смолистой древесины – качественная сушка пиломатериалов с кристаллизацией смолы внутри и (или) применение подходящих барьерных грунтов.
Текст Владимир Падерин