Сушка древесины как искусство
Производитель сушилок ООО «Ремдрев» не новичок в своем деле: многие годы компания выпускала установки в Санкт-Петербурге, а последние пять лет обосновалась и производит их в Вологде, как рассказал ее основатель Руслан Богданов. Сушильные камеры здесь выпускались и для других производителей, но сейчас компания делает ставку на свой бренд Remdrev.
Помимо сушильных камер, завод может поставлять заказчикам в комплекте котельные на древесных отходах. Получается сушильно-котельный комплекс под ключ, что особенно удобно, если на производстве заказчика нет избыточных теплогенерирующих мощностей.
Вкалывают роботы
Общая площадь предприятия составляет 4 тыс. м2 – это 3 тыс. м2 цехов и 1 тыс. м2 открытых площадей. При этом на заводе работает всего 20 человек, включая офисный персонал. Это стало возможным благодаря высокой автоматизации и роботизации производства.
Поначалу на производстве было много ручного труда. Рабочий для обработки заготовки сначала направлялся к одному станку, выполнял операцию торцовки, затем ему нужно было направиться к сверлильному станку, сварочному аппарату и так далее, то есть не было прямоточного процесса, а значит, и должной производительности труда. В месяц удавалось сделать всего пять сушильных камер. Для сравнения: в настоящее время годовой объем выпуска основной продукции – до 300 сушильных камер
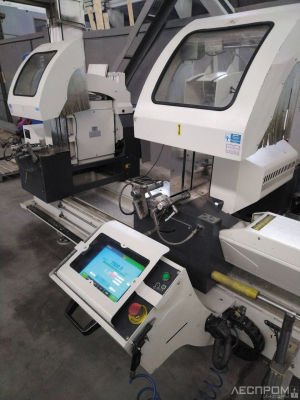
Современное оборудование позволило заметно увеличить объемы и скорость выпуска готовой продукции. С тем, что двое сварщиков раньше выполняли за три дня, один робот справляется часа за четыре. Еще один яркий пример: даже высококлассный специалист сваривает в день всего две большие детали, а робот вполне может шесть – восемь. При этом повысилось и качество продукции, так как из производственной цепочки почти полностью удален пресловутый человеческий фактор.
В итоге «Ремдрев» может изготовить сушилку за один рабочий день. Именно столько времени проходит с момента поступления технологической карты по заказу в производство до отгрузки изделия заказчику. Другое дело, что большинству клиентов такая скорость не требуется. Тем не менее даже в нынешней сложной ситуации в день происходит в среднем три отгрузки. А за месяц завод теперь выпускает 30 камер, и ограничением служит не мощность производства, а спрос. В лучшие времена производилось до 80 сушилок.
Подробнее о технологии
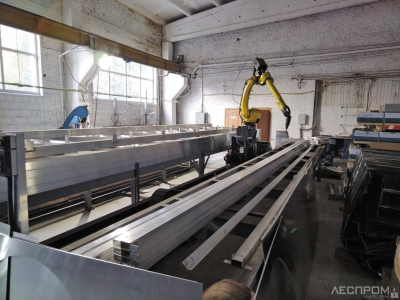
Технологический цикл изготовления сушильной камеры начинается, как это ни удивительно, не в Вологде, а на двух заводах – партнерах по производству алюминиевого профиля, которые поставляют цельнотянутые заготовки обезличенной длины, некоторые из них создают по матрицам, предоставленным компанией «Ремдрев».
Сушильные камеры производятся полностью алюминиевые, – используется сплав АД31, характеризующийся высокой коррозионной стойкостью. Необходимо запастись этим сырьем в достаточном количестве – не менее 150 т на месяц, поэтому фуры с листовым алюминием, столбами и профилем регулярно прибывают на завод. На складе всегда поддерживается запас заготовок минимум на 100 сушильных камер. Специальная программа, разработанная специалистами завода, позволяет контролировать снабжение и предупредит, если на складе останется материалов меньше чем на 50 камер.
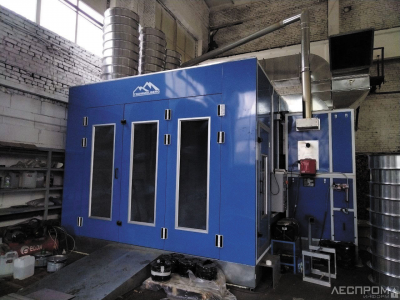
«Конечно, с одной стороны, большие запасы на складе – это выведенные из оборота деньги, но с другой – учитывая регулярный рост цен на металл и инфляцию, это надежное вложение средств, – говорит Руслан Богданов. – А главное – запасы позволяют обеспечить непрерывность производства».
Все необходимые для сушилок заготовки обрабатываются в двух цехах. Один – цех первичной заготовки и обработки металла. Здесь установлен станок китайского производства Ironmac для лазерной резки листового металла и труб. Рабочая головка станка способна как резать, так и сверлить. Для раскроя многокамерных профилей толстого сечения, в том числе под разными углами, используются турецкие торцовочные станки с ЧПУґ – Meteor-II 420 и Gemini V SA.
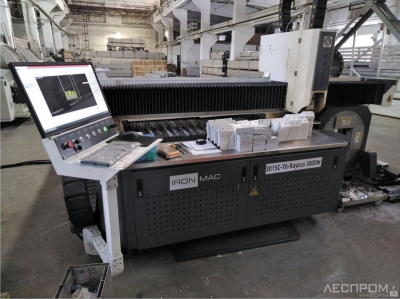
Затем заготовленные по длине профили сверлят, фрезеруют на специальном станке с ЧПУ, на них гравируют номера деталей. Для сварки ферм используется японский робот Fanuc (с финским сварочным аппаратом), этот бренд один из ведущих в промышленной автоматизации и робототехнике. Сварка ферм происходит на двух столах, длина готовых изделий до девяти метров.
Современная сушильная камера – это по сути конструктор, который собирается на площадке покупателя по сборочному чертежу, а задача «Ремдрева» – с высокой точностью изготовить детали этого набора и пронумеровать. На заводе четыре сборочные бригады, которые выезжают к клиентам при необходимости, но большинство заказчиков собирают камеры самостоятельно, а заводским специалистам остается только подключить электрическую составляющую и обучить персонал пользоваться оборудованием.
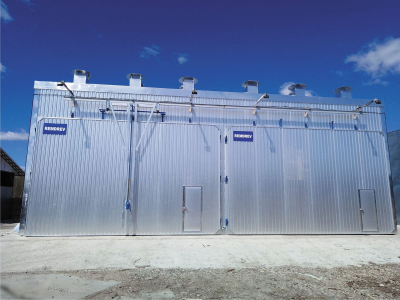
Во втором металлообрабатывающем цехе, из которого тоже отгружается готовая продукция, изготавливаются листовые детали для корпусов сушильных камер, обечайки, выполняется покраска. Установленный здесь станок китайского производства MetalTec для лазерной резки листового алюминия и два гидравлических листогибочных пресса SMD PBC с ЧПУ производят стеновые панели будущей сушильной камеры. В помощь им гидравлические гильотинные ножницы KSM, тоже китайского производства. Итальянская автоматическая сушильная камера используется при покраске некоторых деталей оборудования.
Сварку небольших деталей выполняет промышленный робот GSK китайского производства. Обечайки (части вентилятора) изготавливаются на отбортовочном станке, изготовленном в Китае по спецзаказу «Ремдрева». Прежде такие обечайки выпускали только в Европе. Теперь завод продает полный комплект – обечайка + мотор + вентилятор. Алюминиевые двигатели для вентиляторов поставляет российский электротехнический завод «Уралэлектро», счет им идет уже на тысячи, и они доказали свою надежность.
Параллельно в электроцехе собираются шкафы с автоматикой для управления камерой. На этом технологический цикл завершается. Изготовленные на заводе детали комплектуются двигателями, швейцарскими приводами, вентиляторами, клапанами, форсунками, утеплителем и отгружаются заказчику.
Ну и конечно, в комплект входят электронный «мозг» камеры – контроллер Logica H&S производства Италии. Эта система управления процессами сушки древесины хорошо зарекомендовала себя в России и стала достойной альтернативой другим европейским брендам, в том числе премиальным. К счастью, поставки автоматики из Италии и других комплектующих из стран Евросоюза возможны благодаря параллельному импорту.
Автоматика человека не заменит
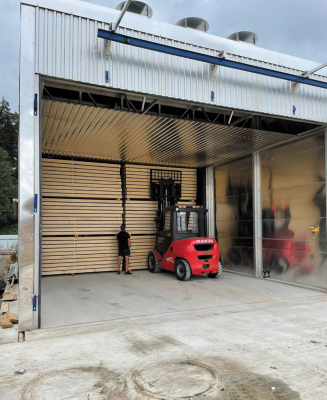
Сушильная камера готова – сверкает алюминием на солнце. Но, даже оснащенная итальянским контроллером, она не высушит доску быстро и качественно без участия человека.
«Подготовка сушильщиков – боль для предприятий, какой бы ни была автоматизация сушильных камер, человек должен быть профессионалом, – делится Артем Лукичев, генеральный директор ООО “Ремдрев”. – В этом деле очень много мелочей, сушильщик должен "чувствовать древесину", понимать физические процессы, происходящие в камерах.
Зачастую даже на довольно успешных деревообрабатывающих предприятиях клиентов мы видим недостатки в организации сушильного хозяйства. Не умеют выкладывать штабеля пиломатериалов, загружаемые в камеры, поэтому ухудшается циркуляция воздуха, не умеют устанавливать датчики влажности. Все это приводит к снижению качества сушки».
«Стандартная минимальная процедура обучения при подключении новой сушильной камеры занимает 2–3 часа. Но у "Ремдрева" есть возможность организовать "контрольную сушку", при которой эксперт предприятия остается на пять дней на предприятии заказчика и проходит с оператором весь технологический цикл сушки партии древесины, – рассказывает Руслан Богданов. – За это время происходит полное погружение в искусство сушки доски, люди за это благодарны».
Если на деревообрабатывающем предприятии установлена не одна сушильная камера, а несколько, суммарным объемом 500 м3 и более, каждая ошибка оператора сушильного комплекса обойдется очень дорого. Например, если оператор ушел с работы в 17 часов и до 8 утра следующего рабочего дня не пользуется возможностью современной камеры контролировать процесс удаленно, оперативно не управляет им, то цикл сушки удлиняется, растет себестоимость производства, а количество брака может увеличиться до 3% партии. Качественно обученный работник сушильного комплекса может заработать для своего предприятия десятки миллионов рублей в год.
Планы развития
«Планируем расширяться, у нас появится дополнительно 1 тыс. м2 производственных площадей, – рассказывает Руслан Богданов. – В новом цехе будет установлен пятиосевой обрабатывающий центр с ЧПУ. Конечно, есть сложности с этой закупкой… Станок из Европы приобрести еще можно, а вот программы к нему уже нет. Поэтому, скорее всего, металлообрабатывающий центр придется закупать в Южной Корее. Инвестиции в это оборудование составят 30 млн руб. Также для расширения возможностей производства будет закуплен координатно-фрезерный станок».
В ближайшем будущем компания будет уделять больше внимания обучению операторов сушильного оборудования. Уже готов собственный учебный центр, в нем на обучающих стендах установлены не только используемые в камерах «Ремдрева» контроллеры Logica H&S, но и контроллеры других марок, в том числе от некоторых крупных зарубежных изготовителей сушильных камер. На них можно будет полностью освоить теоретические процессы сушки пиломатериалов, разобрать многочисленные режимы управления.
Теперь деревообработчики со всей России смогут приехать в Вологду и овладеть тонкостями камерной сушки древесины, но предусмотрен и вариант пройти такой тренинг дистанционно. Это направление планируется отнюдь не коммерческим, стоимость обучения будет минимальной возможной. Задача другая: поделиться накопленным богатым опытом и обеспечить доступ к знаниям пользователям сушильных камер из разных категорий бизнеса (в том числе и обладателям небольших бюджетов), и привлечь новых клиентов. Еще одна новация – создание на площадке «Ремдрева» демонстрационного объекта. Это две сушильные камеры с котельным оборудованием на древесном топливе. Здесь операторы смогут на практике применить свои теоретические знания, увидеть и понять, как выставленные технологические параметры влияют на конечный продукт – сухую доску.
Текст и фото Андрей Кривошеин