«Лесозавод №1»
Современное лесопиление в российской глубинке
Пятнадцать лет назад в поселке Казлук Республики Коми началось строительство лесопильно-деревообрабатывающего производства с использованием новейших европейских технологических решений – «Лесозавода №1».
Усть-Вымский район по меркам Республики Коми нельзя назвать богатым лесом и славящимся лесопереработкой. Из крупных, известных в России деревообрабатывающих предприятий здесь находится только Жешартский ЛПК, выпускающий фанеру и MDF. Фанерное сырье для этого комбината поступает из более богатых лесом районов Коми, а также из-за пределов республики. Помимо производства древесных плит, в Усть-Вымском районе всегда работали предприятия по распиловке древесины, но многие годы это был уровень малого бизнеса со скромными объемами производства и бюджетным оборудованием.
Ситуация изменилась в 2009 году, когда в район пришел крупный инвестор с проектом строительства большого завода по деревообработке.
Приоритетный проект
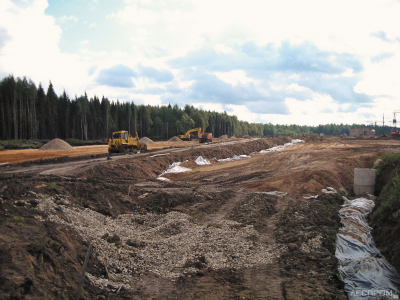
Постановление Правительства РФ №419 от 30 июня 2007 года «О приоритетных инвестиционных проектах в области освоения лесов» дало мощный толчок развитию лесного комплекса России. Волна новых проектов, претендующих на право стать приоритетными, прокатилась по всем богатым лесом регионам страны. В основном это были проекты строительства крупных лесопильно-деревообрабатывающих заводов, и Республика Коми не осталась в стороне.
Одним из таких проектов стал «Лесозавод №1». Его официальное название в качестве приоритетного в области освоения лесов – «Строительство завода по производству конструктивных элементов деревянного домостроения». Приказ Министерства промышленности и торговли Российской Федерации от 28 сентября 2009 года №868 закрепил за инвестпроектом «Лесозавода №1» статус приоритетного с объемом инвестиций 500 млн руб. Этот статус позволил получить без аукциона лесные участки с дисконтом 50% и заключить договоры аренды с годовой расчетной лесосекой почти 180 тыс. м3.
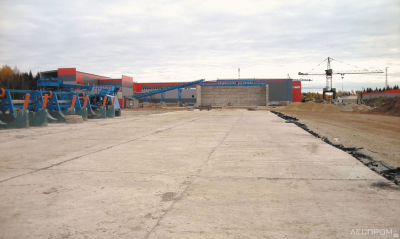
Целью проекта было создание лесопромышленной группы по глубокой переработке древесины, включая следующие структуры: лесозаготовительную, транспортную, лесопильно-деревообрабатывающее производство.
В декабре 2020 года Минпромторг России признал этот проект завершенным, к тому времени фактический объем инвестиций в проект составил уже 1,5 млрд руб. Такое значительное увеличение объема инвестиций относительно запланированных произошло в связи с необходимостью проведения дополнительных работ, неучтенных в концепции приоритетного проекта: строительства высоковольтной линии электропередачи протяженностью 11 км для подключения объектов предприятия к источникам устойчивого электроснабжения; устройства дополнительных свайных оснований под несущими конструкциями зданий цехов и оборудования; модернизации сетей ЖКХ в поселке Казлук; создания современных сетей связи.
То есть приоритетность проекта, с точки зрения государства, заключается только в предоставлении леса на льготных условиях, а бремя создания всей необходимой инфраструктуры полностью ложится на плечи инвестора. С такой ситуацией столкнулись и другие приоритетные инвестиционные проекты в области освоения лесов, реализуемые в Республике Коми.
Финский подход
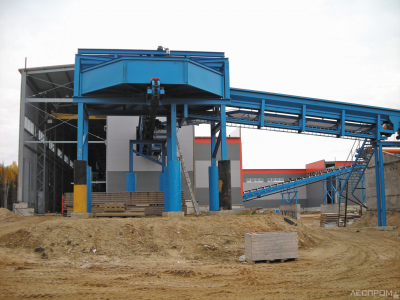
В новых лесопильных проектах конца нулевых в Коми при выборе основного оборудования ориентировались на бывшие в употреблении лесопильные линии европейских производителей. При их строительстве зачастую использовали здания старых деревообрабатывающих заводов и их инфраструктуру. Такой подход позволял серьезно сэкономить.
Инвесторы «Лесозавода №1» поступили не так. Рассказывает Тойво Кукк (в 2007 году представитель финской компании Jartek): «На международной выставке деревообрабатывающей промышленности в Ганновере Ligna+ в 2007 году я случайно познакомился в ресторане с человеком, уже два дня искавшим стенд поставщика лесопильного оборудования Jartek. Это был Александр Митрофанов, один из учредителей “Лесозавода №1”. В итоге прямо на выставке был сделан заказ на лесопильный завод под ключ и потом заключена сделка по хорошей для заказчика цене. Проект из Коми оказался как никогда нужным Jartek – ведь это были годы, когда в мировой экономике начался спад, многие западные фирмы, в том числе Jartek, отправили своих сотрудников в неоплачиваемый отпуск».
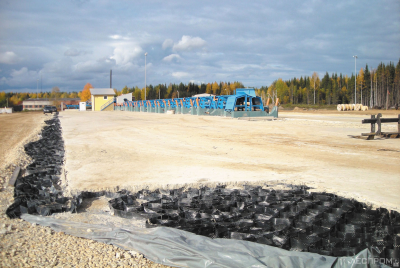
Так в глубинке Республики Коми, на границе с Архангельской областью, в небольшом поселке Казлук с населением 500 человек, стали строить завод с самым современным финским лесопильным оборудованием под контролем финских экспертов. Неудивительно, что в числе первых построенных объектов проекта была гостиница для приезжих специалистов, удобная стильная столовая в ней смотрелась как типичное финское кафе (ravintola по-фински).
К проектированию нового завода привлекли петербургское НПО «Гипродрев». Хотя производство создавалось на площадке бывшего Вашкинского леспромхоза, проект был абсолютно новый. От инфраструктуры старого леспромхоза остались только железнодорожные пути с двумя башенными кранами. Современное мощное оборудование предъявляло высокие требования к фундаментам завода. В 2009 году было устроено свайное поле и привезен большой объем грунта, для того чтобы поднять основание будущего предприятия. Затем построили корпуса лесопильного цеха, сортировочной линии и котельной, причем с применением новых на тот момент технологий. Так, при бетонировании открытых производственных площадок использовалась объемная геосетка.
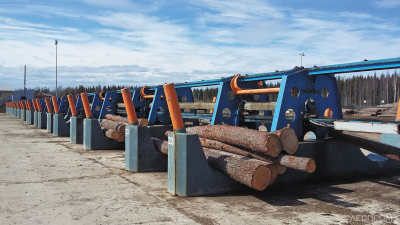
В монтаже линий сортировки пиловочника, подачи на распил, универсального комплекса сортировки пиломатериалов сушильного комплекса и котельной непременно участвовали супервайзеры Jartek. Работа кипела шесть дней в неделю, и проблемы свободного времени у них не было. Ближайший крупный населенный пункт с досуговыми предложениями – поселок городского типа Жешарт – расположен от Казлука в 20 км, и к нему ведет плохая дорога.
Иностранные эксперты рассказывали, что условия труда мало отличались от привычных для Финляндии, а проживание и питание в Казлуке были организованы хорошо. Но им пришлось привыкать к другому ритму работы: если в Финляндии все идет строго по графику, то в России оговоренный срок – понятие растяжимое. Вопросы решаются своеобразно, и с этим надо смириться. Не стоит пытаться что-то изменить, все равно не выйдет. При этом многие российские монтажники имели опыт работы на иностранные фирмы и умели работать в маршевом порядке, но мало кто сталкивался с оборудованием Jartek.
Трудности перевода и многие другие все же преодолели, и в августе 2013 года «Лесозавод №1» выпустил первую партию готовой продукции – высококачественной доски камерной сушки.
Производственный цикл лесопиления
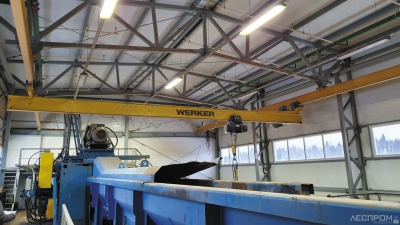
Мощность завода определяет его сердце – фрезерно-брусующий станок HewSaw R250. За год он может переработать до 240 тыс. м3 пиловочника и произвести 120 тыс. м3 пиломатериалов.
В комплект основного оборудования также входят финский окорочный станок ValonKone, австрийская рубительная машина Bruks, сушильные камеры и линия сортировки пиловочника Jartek, лесопильная линия Kara, литовская котельная Komforts.
Процесс производства товарной продукции следующий. Для сортировки бревен по диаметрам предназначена автоматическая линия. Пачки бревен автопогрузчиком укладываются на приемный транспортер линии, который поштучно подает сортименты на сортировочный транспортер. На транспортере бревна сортируются по диаметрам путем автоматического распределения по расположенным по его фронту накопителям. Из накопителей автопогрузчиком транспортируются на склад сортированного сырья, где укладываются в плотные штабели.
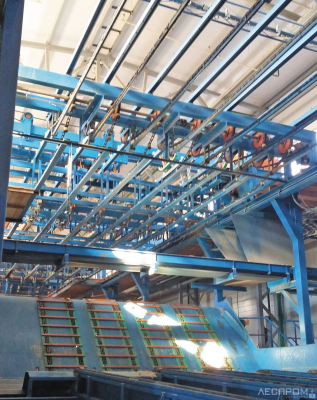
Далее пачки бревен поступают на приемный стол лесопильного цеха. Затем разворотное устройство ориентирует бревна вершиной вперед по ходу технологического процесса. С разворотного устройства они подаются в окорочный станок, а после него – на лесопильную линию, где фрезерно-брусующий станок раскраивает пиловочник на пиломатериалы.
Все полученные пиломатериалы по конвейерам транспортируются на линию сортировки по сечениям, где автоматически распределяются по карманам-накопителям. При поступлении в накопители достаточного для создания полного сушильного пакета количества досок, они выгружаются на пакетоформировочный участок линии, где укладываются через прокладки сушильные пакеты, которые направляются в сушильные камеры. После сушки пиломатериалы поступают на линию сортировки, где по результатам оценки сортиментов торцуются на стандартную длину, маркируются и распределяются по накопителям. После заполнения кармана-накопителя пиломатериалы из него поставляются на участок формирования пакета.
Сформированные на пакетоукладчике транспортные пакеты упаковываются в водонепроницаемую пленку с логотипом компании и обвязываются лентой.
Внутризаводскую логистику обеспечивают фронтальные и вилочные погрузчики. Отгрузка готовой продукции осуществляется в собственных железнодорожных тупиках предприятия.
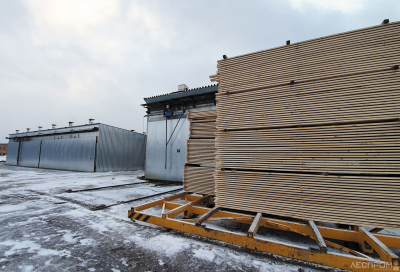
Проектировщик предусмотрел дальнейшее развитие предприятия и возможность строительства второй очереди для более глубокой переработки пиломатериалов.
Сбыт основной продукции
Готовая продукция предприятия – обрезная доска влажностью 18–22% по ГОСТ 8486–86 и различных сортов и размеров по ГОСТ 26002–83. С марта 2014 года завод начал контейнерную отгрузку пиломатериалов на экспорт универсальными 40-футовыми контейнерами с территории предприятия по принципу «от двери до двери». Сейчас отгрузка экспортируемой готовой продукции осуществляется железнодорожными составами из 71 условного вагона. До введения санкций в 2022 году продукция завода поставлялась в страны Европы, Азии и СНГ, а сейчас экспорт переориентирован на Китай и Ирак.
Лесообеспечение
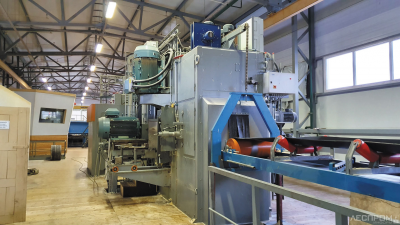
С лесообеспечением у предприятия непросто. Завод арендует для лесозаготовки лесные участки в соседнем Удорском и Княжпогостском районах Республики Коми, однако оказались, что в них вошли кварталы Верхневашкинского массива лесов высокой природоохранной ценности. Возникли серьезные проблемы с некоммерческими экологическими организациями – фондом «Серебряная тайга», Всемирным фондом дикой природы, Greenpeace и с системой добровольной лесной сертификации FSC. Все они заявили, что заготавливать древесину в этом массиве девственных лесов нельзя. Ряд крупных сертифицированных по FSC целлюлозно-бумажных комбинатов отказались закупать у «Лесозавода №1» балансовую древесину и древесную щепу. Вопрос вышел даже на федеральный уровень, переговоры продолжались несколько лет и ничем не увенчались.
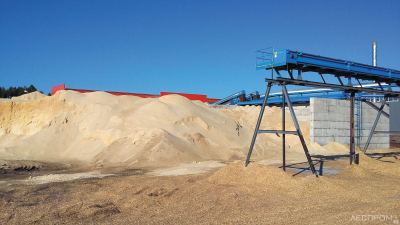
Предприятие между тем закупало пиловочную древесину на рынке, работало на давальческом сырье, заготовка древесины велась силами посредников. В 2018 году «Лесозавод №1» приобрел новый лесозаготовительный комплекс Ponsse, состоящий из харвестера Ergo и форвардера Buffalo, и начал зимние лесозаготовки в ряде арендованных кварталов.
С уходом FSC из России и признанием «зеленых» организаций иноагентами споры по лесным участкам предприятия утихли. Часть пиловочника заготавливается собственными силами, часть закупается у филиала группы «Илим» в городе Коряжме и других поставщиков.
Что с отходами
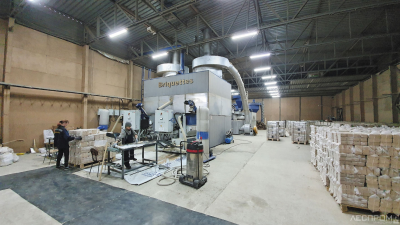
При использовании в лесопилении фрезерно-брусующего станка объем образующихся отходов составляет до 50% объема пиловочника, кроме того, остается кора. Совокупный объем отходов при полной загрузке проектных мощностей в год может достигать 120 тыс. м3. Их движением нужно управлять, осуществлять контроль и сортировку.
На предприятии хорошо продуманная автоматизированная система сбора и сортировки отходов лесопиления. Кора от окорочного станка ValonKone, щепа от фрезерно-брусующего станка HewSaw R250 и опилки от круглопильных пил при помощи системы транспортеров распределяются по назначению. Кора ленточными конвейерами направляется на склад топлива. Щепа от фрезерования бревен поступает на сортировку, после которой технологическая щепа и отсев с опилками отправляются на склады.
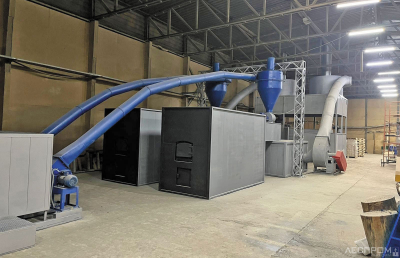
В результате этих производственных операций получают ценный товар – технологическую щепу высокого качества, которая поставляется в столицу Республики Коми Сыктывкар, на ООО «Сыктывкарский фанерный завод», для производства плиты ДСП и в АО «Группа "Илим"» для изготовления бумаги. Часть щепы поставляется на завод по производству ДВП в Княжпогостском районе и другие предприятия по производству древесных плит.
Кора и опилки сжигаются в заводской котельной Komforts мощностью 8 МВт. Тем не менее часть опилок долго накапливалась, не находя применения. Для решения этой проблемы в 2017 году предприятие инвестировало в создание цеха по производству древесных топливных брикетов.
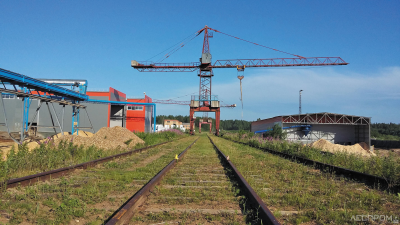
Проект реализовала под ключ компания из Сыктывкара K-Beg с богатым опытом строительства биотопливных линий в Коми и за ее пределами. Она выполнила все строительные работы, изготовила системы подачи сырья, теплогенераторы и сушильные комплексы, а брикетные прессы были литовского производства. В проекте нетривиально решена задача снабжения нового цеха сырьем – отходами лесопиления от основного производства. Поскольку брикетное производство изначально не предусматривалось проектом, его разместили за двухметровой железнодорожной насыпью, разделяющей территорию предприятия. По насыпи проложены железнодорожные пути и установлены башенные краны для погрузки готовой продукции. Инженер компании K-Beg придумал, как поставлять опилки в брикетный цех кратчайшим путем и сэкономить на погрузчике: в насыпи пробили тоннель и проложили трубу, по которой пневмотранспортом доставляется сырье для брикетов.
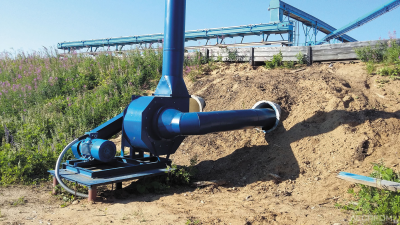
В 2018 году цех по выпуску брикетов заработал. Мощность производства составила 6 тыс. т в год. Брикеты форм-фактора RUF высокого качества упаковываются на поддонах в прозрачную пленку и поставляются в центральную Россию. В цехе предусмотрительно было оставлено место для установки второй брикетной линии, так как новое производство не могло утилизировать весь объем образующихся при лесопилении древесных отходов.
В 2018 году в поисках поставщика пеллет «Лесозавод №1» посетили представители Peltrade, одного из крупнейших европейских пеллетных трейдеров из Великобритании. Они высоко оценили качество древесных отходов. Так как в Казлуке установлено современное лесопильное оборудование, опилки получаются чистыми, без коры. Такое сырье позволяет производить пеллеты премиум-качества, отличающиеся высокой ценой. Подобная продукция востребована в Евросоюзе, особенно в Великобритании. Руководству предприятия поступило предложение построить пеллетный завод по выпуску «белой», так называемой премиальной, пеллеты. При этом всю продукцию гарантированно выкупал бы Peltrade. Возможно, тогда, в 2018 году на предприятии возникли сомнения, что инвестиции были сделаны в брикетное, а не в пеллетное производство, но они развеялись в 2022 году, когда рынок Великобритании, а затем и всего Евросоюза закрыли для пеллет из России.
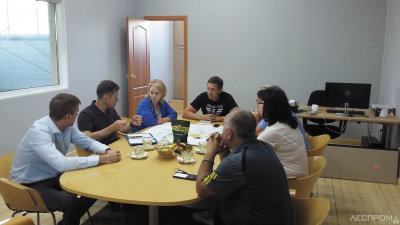
Пеллетный проект под нужды Великобритании в итоге не случился, но зато в 2023 году на предприятии решили расширить брикетное производство. С 2018 года в Республике Коми сформировался рынок потребления брикетов, которые, в отличие от пеллет, на попали под западные санкции и являются востребованным товаром.
Вторую брикетную линию также сооружает K-Beg, с использованием импортозамещенных брикетных прессов. Сейчас на заводе полностью смонтировано оборудование для подачи и сушки древесного сырья, завершается установка двух брикетирующих прессов форм-фактора RUF. Прессы компании «Станки.ру» производятся в соседствующей с Коми Кировской области, срок их службы без капитального ремонта может достигать 15 лет. Совокупная мощность расширенного биотопливного производства составит более 12 тыс. т в год.
Раскрыть потенциал
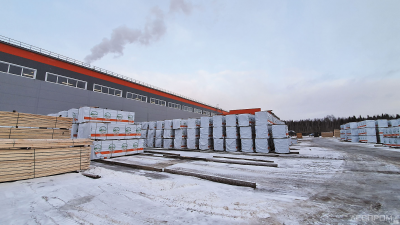
С момента старта проекта с амбициозным названием «Лесозавод №1», в период его реализации команде во главе с генеральным директором предприятия Александром Митрофановым пришлось решить много проблем с энергетиками, экологами, разными органами власти. Была даже реальная угроза лишения проекта статуса приоритетного в области освоения лесов, которое повлекло бы разрыв договоров аренды лесных участков и штрафные санкции Рослесхоза. Но и эти трудности были преодолены.
Проекту всегда помогали руководители администрации Усть-Вымского района и региональный минпром. Сегодня «Лесозавод №1» значимое лесопромышленное производство Республики Коми, он обеспечивает работой более 250 человек, пополняет местные бюджеты налогами. Для маленького Казлука предприятие стало «градообразующим» и выполняет важные социальные функции: строит мосты через реки, модернизирует жилищные коммуникации, чистит от снега дороги, софинансирует благоустройство поселка.
У «Лесозавода №1» есть перспективы развития и раскрытия производственного потенциала, ведь оно оснащено оборудованием, которому могут позавидовать многие лесопильные предприятия Коми.
Текст и фото Андрей Кривошеин