Под знаком золотой птицы
Сыктывкарский ЛПК принимает гостей
Год тому назад Сыктывкарский ЛПК провел ребрендинг всех полиграфических сортов бумаги, тарных и потребительских картонов, товарной целлюлозы, объединив линейки продукции под зонтичным брендом Komi. Главным элементом в логотипе нового бренда стало изображение птицы с распахнутыми крыльями, навеянное образом официального герба Республики Коми. Это подчеркивает взаимосвязь локомотива региональной экономики с местом, где компания осуществляет свою деятельность, и в то же время представляет покупателям со всей страны традиции замечательного северного народа, вполне обоснованно претендующего на неофициальный титул «людей леса».
О том, с чем связан поворот к этническим мотивам и как вообще сегодня поживает целлюлозно-бумажный комбинат, начавший работу более 55 лет тому назад, смогли узнать журналисты, посетившие СЛПК 15–16 августа. В масштабный пресс-тур были приглашены ключевые региональные СМИ (информагентства «Комиинформ» и «БНК», телеканалы «Юрган» и «Коми Гор») и представители профильных организаций со всей страны: портал PrintDaily.ru, портал «Сегмент.ру», журнал «Индустрия печати» и портал «Гофро.орг», журнал «Канцелярское дело», издательство «Курсив», портал UpackUnion (проект «ЦБП в объективе»), а также наш журнал «ЛесПромИнформ», как вы уже наверняка поняли.
Гостеприимные хозяева, не таясь, делились информацией, которая интересовала любознательных посетителей, подробно и последовательно представили всю технологическую цепочку предприятия, а также проходящие за его пределами начальную и финальную стадии цикла глубокой переработки древесины – лесозаготовку и лесовосстановление.
Конечно, за многие годы сотрудничества с комбинатом и несколько визитов на его площадку, корреспонденты «ЛесПромИнформ» уже многое там повидали (и делились с читателями на страницах журнала), однако всякий раз специалисты СЛПК находят, чем удивить – новым и необычным. Так вышло и теперь.
Завтрак с директором
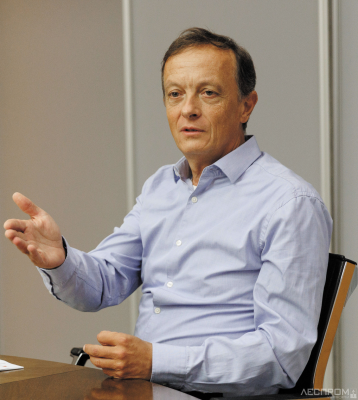
Визит на СЛПК открыла встреча с генеральным директором Клаусом Пеллером. Она прошла в форме делового завтрака – но разговор за большим общим столом вышел совершенно неформальным.
Для начала г-н Пеллер коротко рассказал о положении дел на предприятии. Цитирую: «Ассортимент нашей продукции за последние годы стал шире. Если раньше нашими основными продуктами были белая немелованная бумага, газетная бумага, тарный картон и сухая товарная целлюлоза, то сейчас около трети наших картонов это потребительские картоны, т. е. предназначенные для упаковки напитков и пищевых продуктов. Мы пошли по этому пути с февраля 2022 года, когда в России возник дефицит упаковочных решений (и в первую очередь это коснулось молочной отрасли). Тут мы отреагировали оперативно, запустив производство потребительских картонов. Нужно понимать, что для нас это действительно большой вызов, который касается не только изготовления, но и продаж продукции – тут и новые клиенты, и новые конкуренты, и новые способы продвижения. Всё иначе. Не могу сказать, что было очень тяжело, но постараться пришлось – и вот через два с лишним года эта категория товаров успешно продается на российском рынке. Пока мы эти картоны не экспортируем.
Это крупное, но не единственное изменение. Мы продолжаем выпуск офисных бумаг привычных форматов А3 и А4, “Снегурочка” по-прежнему флагман, но есть и новые марки. Бренды Mondi – Maestro и IQ – уступили место “Чайке”, CartBlanc и Projectа. Первый бренд мы производим для внутреннего рынка, два других продаются как в России, так и за ее пределами.
Газетная бумага – примерно 40–60% мы продолжаем отправлять за рубеж, здесь рамки немного “гуляют” в зависимости от актуальной ситуации на рынке.
Что касается товарной целлюлозы, никаких изменений нет: как и раньше, она продается в соотношении 50/50 на экспорт и внутри страны. А вот объем производства последовательно увеличивается – это прямое следствие усилий по повышению эффективности работы предприятия.
Мы полностью поменяли нашу брендовую политику, создав зонтичный бренд Komi. Теперь название каждого продукта СЛПК (кроме офисных бумаг) начинается с этого слова: тарные картоны KomiWhite и KomiFlex, книжная бумага KomiStory, потребительские картоны KomiPak, KomiBase и KomiFresh, офсетная бумага KomiOffset, газетная бумага KomiPress и KomiReader, типографская бумага KomiText, товарная целлюлоза KomiSoft и KomiPrime и т. д. В логотипе зонтичного бренда используются корпоративные цвета и символическое изображение птицы.
В нашем портфолио есть новинки, например, пухлая книжная бумага кремового цвета. Новые продукты – это подспорье в ситуации, когда экспортные операции ограничены.
Причем причины ограничений – это ведь не только санкции. Очень большая проблема – транспортно-логистическая. Стоимость перевозок высока, доступность не всегда гарантирована.
Хочу подчеркнуть: создание новых продуктов – не самоцель, ЦБП – достаточно консервативная отрасль. Наша задача – обеспечить рынок необходимыми товарами, и прежде всего полностью загрузить работой наше производство».
А потом были вопросы. И директор комбината старался подробно отвечать на все, освещая самые разные темы.
– Уточните, пожалуйста, в какие зарубежные страны сейчас экспортируется продукция СЛПК?
– Мы экспортируем продукцию примерно в 20 стран, но основных направлений четыре: Китай, Турция, Индия, ОАЭ. Причем первые две страны – несомненные лидеры, с большим отрывом.
– Как обстоят дела с запчастями, химикатами и другими расходными материалами, необходимыми для работы предприятия?
– В 2022 году для решения этой проблемы мы запустили проект с говорящим названием GoEast.ru – то есть с запада мы переориентировались на восток. В основном, речь идет, конечно, про Китай. Почему так? Все просто: основные мировые производители давным-давно организовали там филиалы или вообще перенесли туда свои производства. Соответственно, оттуда можно получить те же самые запчасти, оборудование и другие нужные нам товары. Безусловно, все критерии качества и надежности тщательно отслеживаются. Мы проводим серьезные технические проверки. Сотрудничество с новыми поставщиками требует времени и определенных усилий, постепенно мы налаживаем новые связи. Но на сегодняшний день всё необходимое нам доступно.
– То есть процесс технического оснащения и переоснащения не прерывается, даже в непростой нынешней обстановке?
– Если говорить про оборудование и инвестиции, то впереди у нас второй этап модернизации ТЭЦ. Мы начали c модернизации энергетической инфраструктуры, эта часть проекта реализована уже на 45%. Вторая часть предполагает строительство газового котла и паровой турбины. На данный момент выбраны поставщики оборудования – китайская и индийская компании. Второй этап модернизации ТЭЦ рассчитан на 3,5 года и не подразумевает увеличения мощности – это требование времени: оборудование работает уже более полувека и его нужно обновить. А поскольку мы обеспечиваем не только бесперебойную работу комбината, но и стабильное снабжение электроэнергией населения региона (СЛПК покрывает 17% потребности Коми в электричестве), понятно, что эта работа необходима.
Общая стоимость второго этапа проекта – около 14 млрд рублей.
Кстати
- 14 января 1963 года строительство целлюлозо-бумажного комбината в Эжвинском районе Сыктывкара объявили Всесоюзной комсомольской стройкой. По путевкам в Коми прибыло около 5 тысяч молодых стройотрядовцев со всех концов СССР.
- На комбинате работает три бумагоделательных машины (11, 14, 15) и одна для производства картона (БМ-21). Пятая машина – сушильная, для производства сухой товарной целлюлозы.
- Офисную бумагу «Снегурочка», очень скоро ставшую настоящим бестселлером, компания начала выпускать в 2000 году.
- С начала работы комбината на СЛПК сварено более 25 млн т целлюлозы.
Источник: БНК
– Немного о лесной сертификации. В свое время комбинат был активным участником системы FSC. После ухода из России этой международной организации СЛПК не присоединился к преемникам FSC, а выступил одним из инициаторов новой национальной системы лесной сертификации (НСЛС). Чем продиктовано такое решение?
– Выбор очевиден. Прежде всего, новую систему сертификации поддерживает государство. И это очень важный момент. В целом, изменение системы сертификации ничего не изменило в наших процессах, мы работаем в лесу так же ответственно, как раньше. Сертификат НСЛС подтверждает нашу приверженность устойчивому лесопользованию, а также прозрачность и легальность поступления древесного сырья на комбинат. Сейчас к НСЛС уже присоединились наши коллеги и основные конкуренты.
– Что касается государства: ощущаете ли вы поддержку с этой стороны?
– Мы реализовали с господдержкой три крупных проекта: проект модернизации комбината STEP в 2010 г., пуск новой сушильной машины для производства товарной целлюлозы в 2014 г. и комплекс инвестпроектов «Горизонт» в 2021 г. Сейчас находится на рассмотрении наша заявка на получение транспортной субсидии. Пока подтверждения мы не получили, но надеемся, что государство нас поддержит.
– Поделитесь, пожалуйста, рецептом успеха СЛПК и главными факторами его реализации.
– Основной фактор успеха любого дела это, конечно, люди. Раньше мы были частью глобальной компании и, если возникала какая-то проблема, достаточно было просто спросить коллег. Синергия предприятий внутри группы помогала наращивать эффективность каждого из них. Такой обмен опытом позволил накопить большой объем знаний и экспертизы. Сегодня мы поддерживаем достигнутый уровень, хотя, конечно, добиваться всего теперь приходится только собственными силами. Но все становится возможным благодаря высокому профессионализму нашей команды.
Успешность ЦБК зависит также от сырья и энергии. С лесфондом у нас в регионе всё в порядке, на сегодня мы даже не используем его в полном объеме. На комбинате мы тщательно выстроили всю цепочку сырьевого обеспечения, понимая важность этого вопроса.
То же и с энергией. Мы генерируем 40% «зеленой» энергии из отходов производства (черный щелок, кородревесные отходы), а остальные обеспечивает надежный поставщик газа. Это позволяет уверенно вести нашу деятельность.
– Сколько людей сейчас работает на СЛПК?
– Трудовой коллектив – почти 4,5 тыс. человек. Из них примерно 1400 работает в лесу, остальные трудятся на производственной площадке. Производственный персонал – более 3300 человек.
– Существует ли проблема с нехваткой персонала?
– Разумеется. Как и везде, во всех отраслях экономики России. Есть вакансии на лесных делянках, которые расположены на расстоянии до 450 км от комбината, есть на производстве. Молодые люди сегодня не хотят работать по сменам на промышленном предприятии.
Из-за кадрового дефицита, возможно, придется в будущем подумать об усилении акцента на автоматизацию производства. Это вариант решения проблемы, но пока таких планов нет. Мы не стремимся сокращать численность.
Подводя итог встречи с журналистами, Клаус Пеллер высказался оптимистично:
– Я считаю, что у нас очень крепкий фундамент, который вместе с тщательно продуманной стратегией позволит нам пережить еще несколько лет любой турбулентности. Мы работаем на уровне почти полной загрузки мощностей, это важно как для людей, имеющих возможность получать зарплату, так и для компании, которая может инвестировать в дальнейшее развитие. Мы получаем прибыль, мы можем вкладывать в будущее и уверенно смотрим вперед. Основные вызовы – кадровый дефицит, улучшение логистики и транспортной инфраструктуры. Рано или поздно эти вопросы мы тоже решим.
Экскурсия по комбинату
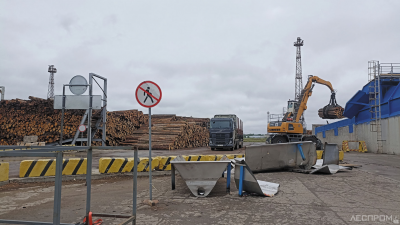
Посетив специальный салон (да-да, именно так!) средств индивидуальной защиты, получив каски, сигнальные жилеты, защитные очки и беруши, пройдя обязательный инструктаж по технике безопасности, сплоченная группа журналистов погрузилась в автобус и отравилась в путешествие по технологическим участкам предприятия.
Как театр начинается с вешалки, так цикл лесопереработки стартует с доставки на предприятие древесного сырья. В сутки на СЛПК поступает от 10000 до 20000 м3 сырья автомобильным и ж/д транспортом. Всего комбинат перерабатывает 4,2 млн м3 древесины ежегодно, объем собственной лесозаготовки – 3,5 млн м3.
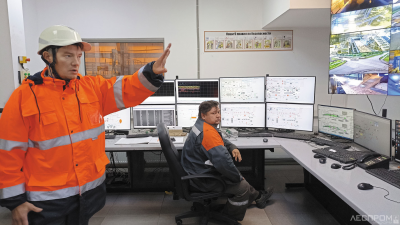
Лесовозы заезжают в ворота и попадают на пункт приема древесины, где фотоскан с помощью лазера производит объемное измерение содержимого кузова каждого грузовика. И пока машина еще движется на биржу сырья (где ее возьмут в оборот шустрые перегружатели Liebherr и Sennebogen), объективная информация о пополнении сырьевого запаса уже попала в общую систему учета.
По словам начальника древесно-подготовительного цеха Максима Булгина, площадки хранения древесины вмещают около 800 тыс. м3 сырья, такой запас позволяет нивелировать сезонность и возможные перебои с доставкой древесины, обеспечить непрерывное производство. Круглые лесоматериалы приходят как с собственной заготовки, так и покупаются со стороны, привозная щепа – от различных лесопильных компаний Коми. Взаимодействие с ними, как и непосредственно лесозаготовка, строительство дороги лесовосстановление находятся в ведении управления лесообеспечения.
Древесно-подготовительный цех
Здесь из поступившей из леса древесины получают технологическую щепу.
«ДПЦ включает участок приемки древесины (как круглых лесоматериалов, так и насыпных), зоны хранения и двух участков переработки. На одном перерабатывается 100% ель, на другом – хвойная и лиственная древесина. Переработка ведется раздельно, чтобы направлять в процесс измельченную древесину по породам. Все процессы управляются автоматикой с центрального пульта, от входа сырья и окорки до подачи готовой щепы на варочный участок, – рассказал Максим Булгин. – Если идти «по технологии», в начале располагается камера разморозки с водой, нагретой до 70 градусов – здесь древесина и ее кора размягчается, отмывается от минеральных примесей (для их исключения из процесса по пути установлено три камнеловушки) и далее поступает на окорку. Рядом с основной технологической линией располагаются три короотжимных пресса, туда попадают кородревесные отходы, чтобы далее по транспортеру отправиться для сжигания в корьевой котел ТЭЦ или на склад хранения».
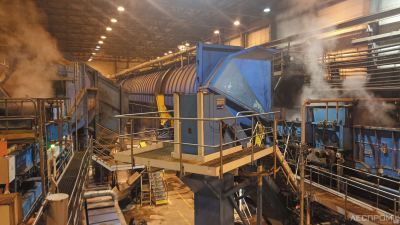
ДПЦ начал функционировать в 1969 году, в 1982 году был модернизирован, а в 2010 году в рамках проекта STEP здесь коренным образом изменили технологию переработки древесины и транспортировки щепы, создали склады щепы открытого хранения.
Успешно внедряются средства автоматизации. Так, система WoodSmart от Teknosavo Oy (Финляндия) работает в цехе с 2016 года, она позволяет анализировать и оптимизировать процесс окорки – управляет скоростью загрузки, вращением барабана, степенью открытия шабера и т. д. Система ChipSmart была внедрена двумя годами позднее. Она производит оценку качества готовой продукции цеха и оптимизирует отбор щепы по всем необходимым показателям.
Производство бумаги
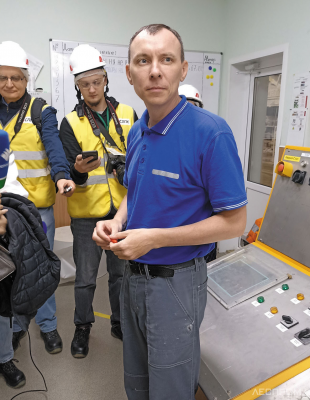
Бумагоделательную машину №14, выпускающую офисную бумагу, представил гостям начальник цеха БМ-14 Михаил Зверев.
«Машина построена компанией Valmet и установлена в 1982 году. Сначала она производила типографскую бумагу, 180 тыс. т в год, – рассказал он. – В процессе деятельности прошло несколько модернизаций. В 1998 г. машина была переориентирована на производство офсетной бумаги. В 2000 и 2008 гг. провели еще два обновления: первое позволило перейти на выпуск офисной бумаги (той самой знаменитой “Снегурочки”), а второе – увеличить мощность до 360 тыс. т в год. То есть – удвоить ее, по сравнению с начальной».
Сырье подается на БМ жидким потоком. Затем производится сортирование, добавление химикатов и создание композиции, удаление воздуха – и далее через напорный ящик сырая бумажная масса набирается на сеточном столе и частично обезвоживается.
После стола эта масса идет на прессование, при этом удаляется еще какое-то количество воды и производится сушка полученного бумажного полотна горячим паром с помощью специального цилиндра.
Далее на специальном клеильном прессе осуществляется проклейка поверхности с каждой из сторон тонким слоем крахмала. Снова просушивание – и полученный огромный рулон бумаги (массой 27–28 т, шириной 8,72 м) при помощи крана снимается с наката и подается на продольно-резательный станок, где нарезаются материнские рулоны по 2–4 т. Они упаковываются в пленку и по транспортеру поступают в цех форматной резки бумаги (где рулоны поставят в раскат по шесть штук и нарежут в листы и пачки – но об этом чуть дальше).
Все рабочие процессы на БМ по большей части автоматизированы, и сотрудники цеха выступают скорее контролерами, отслеживая технологические параметры и корректность работы оборудования. Но если происходят какие-то отклонения, они готовы оперативно вмешаться и устранить неполадку – ведь одним из основных условий эффективности в производстве целлюлозы и бумаги является его стабильность.
Цех форматной резки бумаги
Здесь бумажные рулоны нарезают на нужный формат, упаковывают в пачки и коробки. Происходит всё настолько быстро, что глаз еще как-то успевает следить за движением листов, стоп и пачек, а вот камера уже не справляется – и на фото наблюдаешь только след предмета, ода как сам он давно уже «поехал» дальше. Отчасти спасает спортивный режим.
«На автоматической линии бумажное полотно после размотки разрезается специальными ножами продольно и (затем) поперечно. Из полученных листов форматов А3 и А4 формируются стопы по 500, которые ленточным транспортером подаются в упаковочную машину», – рассказал начальник ЦФРБ Леонид Литке.
В ЦФРБ работают три малоформатные линии. Плюс отдельная линия формата фолио. И участок упаковочных материалов, где производится упаковка для пачек бумаги и гофрокартон для коробок, в которые на «выходе» пакуются брендированные пачки. Здесь выпускают бумагу «Чайка», «Снегурочка» и других известных брендов.
Выпарная станция и содорегенерационный котел
Это технологический этап, который на СЛПК обычно не включают в экскурсии. А вместе с тем он наиважнейший, ведь именно здесь ликвидируют дурнопахнущие газы, являющиеся, увы, неотъемлемым «довеском» любого целлюлозного производства. Здесь возвращаются в оборот и ценные химикаты.
Замначальника цеха регенерации щелоков и производства извести Дмитрий Шеин сообщил: «Наш цех – самый крупный на комбинате, он включает три выпарные станции, содорегенерационный котел (СРК), турбину Siemens и известерегенерационные печи, а также цех по варке таллового масла».
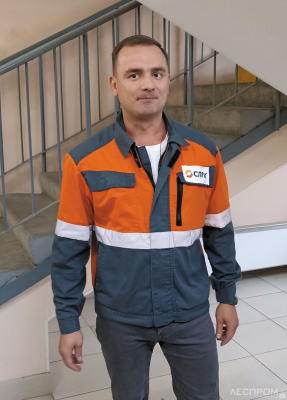
Эксперт показал представителям СМИ новую выпарную станцию, которая начала работу в 2021 году. Работает на хвойном щелоке, который впоследствии смешивается с лиственным и подается на СРК.
«Основная задача станции – упаривание водного раствора, остающегося после варки щепы, с получением из него черного щелока. Полученный щелок поступает на сжигание в СРК, там вся органика сгорает и остается минеральная составляющая – ее возвращают на каустизацию и обратно на варку щепы. Наша задача – это регенерация ценных химикатов для повторного использования. И дополнительно мы получаем «зеленую» энергию – 87 мВт! Кроме того, очищаем от метанола и скипидара конденсаты, которые также подаем обратно в производственный процесс», – рассказал Дмитрий Шеин.
Дурнопахнущие газы также собираются и утилизируются в СРК, при этом опять получается польза: из них извлекается необходимая для варки сера. Известковые отходы и золу, образующиеся при сжигании биотоплива, продают производителям удобрений и стройматериалов. Талловое масло охотно приобретают предприятия нефтехимической, дорожной и энергетической отраслей, ценный продукт СЛПК использует также и в собственном производстве как добавку при варке целлюлозы.
СРК размещается во внушительном, высотой 70 м здании – и большую часть его внутреннего объема занимает 48-метровый котел. Особенностью его конструкции является то, что огромное устройство подвесное: то есть основание котлоагрегата не жестко зафиксировано на фундаменте, а приподнято над полом. Так сделано потому, что при нагревании корпус работающего котла расширяется вниз на целых 100 мм. Горение в нижней части топки происходит с температурой 1150 градусов.
Штат сотрудников цеха – около 130 человек. Это работники разных профессий, но самая «футуристическая» работа досталась операторам группового щита: датчики и камеры передают информацию на стену из видеомониторов – сюда поступают показатели всех систем управления СРК и выпарными станциями. И выглядит это всё, будто командная рубка звездолета.
Интерлюдия
Делу время – потехе час. И о культурно-развлекательной программе для гостей принимающая сторона тоже подумала: начиная с посещения санатория–профилактория СЛПК (кстати, приехать сюда отдохнуть и подлечиться может любой желающий за довольно-таки небольшие деньги) и посещения экспозиции Национального музея республики Коми (экскурсоводы которого просто поражают глубиной знаний и заражают увлеченностью) – вплоть до торжественного ужина в этно-стиле и шуточного конкурса, посвященного истории и культуре народа коми. Но это уже совсем другая история…
Чем дальше в лес…
На второй день пресс-тура журналисты отправились в лес. По сути дела, с лесной делянки следовало начать производственную цепочку, хотя и в таком построении поездки был свой резон: последовательно пройдя весь технологический процесс комбината от входа сырья до отгрузки готовой продукции, журналистам осталось «замкнуть цикл» – узнать, откуда сырье берется, и что делают для того, чтобы этот ресурс был по-настоящему возобновляемым. Но обо всем по порядку.
Лесопитомник
На текущий момент мощность цеха лесовосстановления СЛПК по выращиванию сеянцев с ЗКС – 8,6 млн ежегодно, в две ротации (май, июль). Шесть теплиц и столько же полей для доращивания сеянцев, линии для приготовления субстрата и посева семян, упаковочная и энергетическая установки – все это мы увидели своими глазами.
Об истории и достижениях предприятия рассказал начальник цеха лесовосстановления Родомир Куликов: «В теперь уже далеком 2006 году, после того, как наша компания стала заключать договоры аренды лесных участков для собственной заготовки древесины и возникла необходимость обеспечивать себя качественным посадочным материалом для лесовосстановления, было принято решение о строительстве собственного лесопитомника для выращивания сеянцев с закрытой корневой системой– и два года спустя он был открыт на площади 5,2 га близ села Визинга. Мощность тогда составляла 1 млн сеянцев в год. Закупили две теплицы 16,5 х 70 и необходимое оборудование (итальянская посевная линия, установка для приготовления субстрата), построили ангар, разбили два поля доращивания. Пусконаладочные работы еще не завершились, а мы уже сделали первый посев. Учиться приходилось на ходу, ездили перенимать опыт в другие регионы (Архангельская область, республика Карелия) и страны (Финляндия) – но в итоге 429 тыс. сеянцев с ЗКС мы получили!
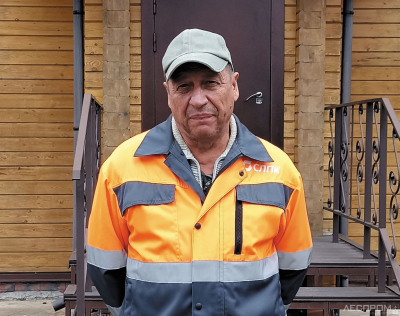
В 2009 г., посеяв семена ели, мы вырастили уже 845 тыс. сеянцев и начали использовать собственный посадочный материал на территории аренды комбината. Параллельно решалась задача по снижению себестоимости продукции – и мы перешли на две ротации посадок, а также заменили финский питательный субстрат на отечественный торф. На третий год работы мы уже сами делали субстрат и в 2011 году получили 1,5 млн сеянцев. Конечно, не обходилось без ошибок, но все же задачу по обеспечению лесовосстановления для своей лесосеки мы решили. Появились и первые покупатели сеянцев.
Руководство компании, посетив питомник, озадачило вопросом: что нужно для увеличения продуктивности до 4 миллионов? Ответ, конечно, простой: средства! Деньги были выделены и уже к апрелю следующего года мы получили две новые теплицы, сделали дополнительно два поля доращивания и уже к лету вышли на показатель 2,6 млн. Две ротации в 2013 году дали результат 4,2 млн – и тут новые события пошли чередой: после совещания с представителями Рослесхоза предприятие подняло цифры ежегодного лесовосстановления с 643 до 1500 га и кроме того республиканские власти сделали запрос на 11 млн сеянцев.
Мы решили довести производительность лесопитомника с 4 млн до 8 млн сеянцев. Для этого были закуплены две большие (25х100) теплицы, построен холодильник для хранения зимних сеянцев в коробках и ангар для хранения торфа, куплены упаковочная установка и современная линия для заполнения и засева кассет, а также другое оборудование и техника, пробурена скважина глубиной 112 м. И к 2016 г. комплекс выдал 8,2 млн сеянцев сосны и ели. С тех пор мы ежегодно выращиваем больше 8 млн – в прошлом году был достигнут рекордный результат 8,7 млн, а всего на настоящий момент в питомнике выращено около 90 миллионов новых деревьев.
В 2015 году наш комплекс завоевал третье место в конкурсе лучших лесопитомников России, а в 2016 уже стал первым!
Сейчас здесь работает пять сотрудников: инженер, механик, водитель погрузчика, контролер качества и подсобный рабочий. Поскольку официально наше подразделение называется «цех лесовосстановления», на нас возложен еще ряд задач в этой области – в частности, передача посадочного материала подрядчикам и контроль за выполнение работ. В сезон с апреля по ноябрь мы по договорам привлекаем работников на посев, прополку и разреживание, упаковку посадочного материала и другие работы.
На достигнутом не останавливаемся. Мало того, что теперь ежегодные объемы лесовосстановления СЛПК выросли до 2,5 тыс. га, мы обеспечиваем постоянных клиентов из нашей республики, Пермского края, Вологодской и Архангельской областей».
Все 100% посадок (а это около 3,5 млн штук) на территории лесной аренды СЛПК осуществляет сеянцами с ЗКС из собственного питомника. Приживаемость саженцев составляет 90–95%.
Лесозаготовка
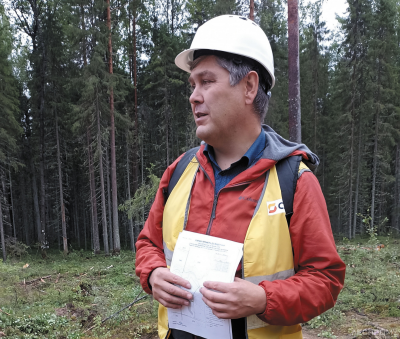
«Чтобы СЛПК работал в полную силу, в день на комбинат приходит около 300 лесовозов, - начал рассказ по пути на делянку начальник отдела планирования лесообеспечения предприятия Василий Чупров.
Общий объем заготовки в республике колеблется от 7 до 9 млн м3 в год, то есть большую часть нетоварной древесины в Коми потребляет СЛПК». Пик рубок и поставок на комбинат приходится на зимний период, с ноября по апрель. Лесозаготовки идут на арендованных участках в семи муниципальных районах республики: Сысольском, Удорском, Усть-Куломском, Корткеросском, Прилузском, Койгородском и Сыктывдинском. Чтобы сделать эти участки доступными для техники, СЛПК ежегодно строит более 120 км лесных дорог.
Производство СЛПК уникальное, других таких в России нет.И вот почему. Комбинат потребляет примерно в равных пропорциях древесину четырех основных пород: ель, сосну, березу и осину. Другие заводы используют чаще всего хвойную древесину, редко в каких-то комбинациях. И случается, что по этой причине заготовка для них превращается в такое однобокое лесопользование: выбираются хвойные деревья, а все остальное оставляют стоять в лесу или бросают на делянках.
У нас ситуация другая. Забираем всю древесину с вырубки. Поскольку деловую древесину не используем, ее продаем, остальное идет на комбинат. Это и наиболее рентабельный путь, и нацеленность на будущее с лесохозяйственной точки зрения. – Следом можно начинать лесовосстановительные мероприятия с нулевого уровня. И мы используем эту возможность для создания хвойных насаждений с должным за ними уходом».
По словам Василия Чупрова, история лесозаготовки СЛПК насчитывает уже 20 лет: «В 2004 г. было принято решение о получении собственной лесной аренды. К 2008 г. это уже был серьезный лесной фонд – и для регулирования всех работ по заготовке древесины был организован отдел лесообеспечения, в который пришел работать и я.
Арендованные леса расположены в южных и центральных районах Коми – вверх по Вычегде и в Удорском районе. На севере своей заготовки нет, оттуда поступает только покупное сырье.
На делянках работает несколько десятков сортиментных комплексов Ponsse. При этом две пары ведут выборочные рубки ухода в молодняках, они выделены в отдельную вахту и мобильно перемещаются между участками. Остальные вахты более или менее стационарны – поселки перебазируются максимум 2–3 раза в год».
Самые близкие лесные участки комбината располагаются в 120 километрах от Сыктывкара в Сысольском районе. Сюда и привезли группу журналистов – если официально, на Сысольский участок Южного отделения службы лесозаготовок. Заготовка ведется исключительно машинным (сортиментным) способом. О ручных бензопилах тут забыли с 2012 года. Возраст деревьев для рубки в хвойных насаждениях составляет 81 год.
Харвестеры работают строго по заранее подготовленному нормативному документу – технологической карте. За смену один оператор вырубает около 200 м3 сортиментов и складывает в штабеля, сортируя попутно по породам, калибрам (минимальный диаметр ствола, пригодного для технологии – 6 см, максимальный – 60) и качеству. Срезанные харвестерным агрегатом ветки и прочая древесная «мелочь» идет под колеса, так снижается воздействие тяжелой техники на весьма чувствительную к повреждениям лесную почву и образуется задел нового плодородного слоя.
По магистральному волоку следом за харвестером проходит форвардер и, собрав заготовленные бревна, переносит их в место, откуда удобнее загрузить лесовоз.
Для обеспечения стабильности поставок на комбинат в периоды сезонных ограничений организованы промежуточные склады заготовленных сортиментов, различной емкости – от 70 тыс. м3 до 500 тыс. м3. Работающие вахтовым методом операторы лесных машин, механики и сотрудники сервисных служб живут в полностью оборудованных домах-вагончиках расположенного километрах в 20 от делянки вахтового поселка. Помимо собственно жилищ, в нем есть столовая с кухней, электрогенератор, парковка для личной и спецтехники, бытовка с сушилкой для спецодежды и даже сауна. А также доступен интернет – что выглядит немного чудом в лесной глуши, где даже телефонная связь есть далеко не везде.
Лесовосстановление на площадях ведущихся рубок – комплексное: наряду с естественным самосевом (для чего на делянках оставляют самые продуктивные деревья) используется искусственное лесовосстановление: площадка полностью расчищается техникой, создаются специальные борозды и микроповышения, в которые высаживают сеянцы с ЗКС.
Спустя десятилетия при должном лесохозяйственном уходе на участках будет расти новый лес. Причем «правильный», без бурелома и деревьев-сорняков. Что в целом обещает хорошее будущее – и обычным жителям, которые придут в лес за грибами и ягодами, и огромному комбинату, обеспечивающему работой тысячи из них, и зеленому лесному «морю» Коми, которое из окна уносящего меня домой самолета по-прежнему выглядит бескрайним.
Справка
Общая площадь земель лесного фонда Коми составляет 36,3 млн гектаров, это 87% территории республики. Расчетная лесосека по всем видам рубок – около 33 млн м3, при этом предприятиями ЛПК реально заготавливается только 9 млн м3. Из этого объема на долю СЛПК приходится 3,4 млн м3 собственной лесозаготовки в год, что уверенно делает комбинат ведущим лесозаготовителем региона.
Источник: БНК
Текст и фото Максим Пирус, «ЛесПромИнформ»