Стали, сплавы и покрытия для дереворежущего инструмента
Дереворежущий инструмент эксплуатируется в условиях длительного контакта и трения с обрабатываемыми материалами – древесными и древесно-полимерными композитами. При этом должны оставаться неизменными конфигурация и свойства режущей кромки. Для изготовления режущего инструмента используются материалы, характеризующиеся высокой твердостью – от 60–62 HRC и износостойкостью – способностью долго сохранять режущие свойства при трении.
Вместе с тем дереворежущий инструмент должен отличаться высокими прочностью и вязкостью, чтобы сохранять форму режущей кромки и сопротивляться разрушению от действия изгибающего (зубья пил, насадных фрез и т. п.) и крутящего (концевые фрезы и сверла) моментов и динамических нагрузок.
В процессе резания нагревается как режущая кромка, так и корпус инструмента. Поэтому основным требованием, предъявляемым к инструментальным материалам, является высокая теплостойкость (красноломкость) – способность сохранять твердость и режущие свойства при длительном нагреве во время работы.
По теплостойкости применяемые материалы подразделяются на следующие виды:
- углеродистые и низколегированные стали с теплостойкостью до 200°С (нетеплостойкие);
- среднелегированные стали с теплостойкостью до 400–500°С (полутеплостойкие);
- высоколегированные быстрорежущие стали с теплостойкостью до 600–640°С (теплостойкие);
- спекаемые и литые твердые сплавы с теплостойкостью до 800–1300°С;
- особо твердые материалы (алмазы и материалы с покрытием) с теплостойкостью до 1200°С (в статье не рассматриваются).
В настоящее время из-за санкций в связи с СВО поставки в Россию импортных, особенно европейских, материалов резко сократились, поэтому рассмотрим современные отечественные инструментальные материалы на предмет более широкого вовлечения в производство дереворежущего инструмента.
Инструментальные углеродистые стали
Инструментальные углеродистые стали широко применяются при изготовлении пил (рамных, ленточных и круглых), различного фрезерного инструмента (насадных и концевых фрез, сверл, зенкеров и т. п.), резцов, скребков и крючков для токарной обработки древесных материалов, а также различного ручного режущего инструмента (стамесок, ножовок, долот, ножей для рубанков и т. п.).
Углеродистые стали (У) содержат ≥0,7% углерода (в маркировке цифрой обозначается средняя массовая доля углерода в десятых долях процента).
Качественная углеродистая сталь (в маркировке нет буквы A) содержит примеси серы – 0,03% и фосфора – 0,035%, в марках более высокого качества серы уже 0,02%, а фосфора 0,03%. Наиболее чистая высококачественная сталь маркируется буквой A. Высокое содержание марганца в составе стали обозначается буквой Г в маркировке. Химический состав углеродистых сталей регулирует ГОСТ 1435-99.
Углеродистые стали характеризуются высокой твердостью и высокой прочностью после закалки. В табл. 1 приведены основные марки углеродистых сталей и их назначение.
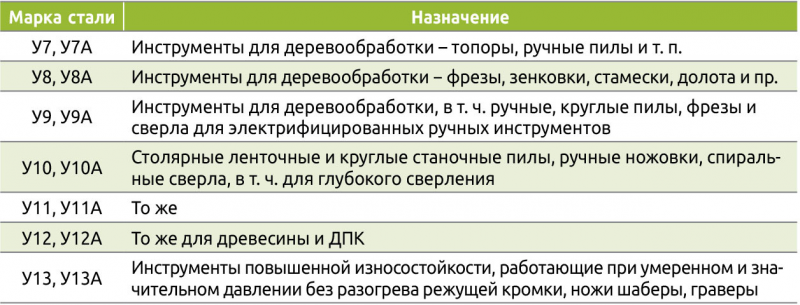
Химический состав некоторых углеродистых сталей приведен в табл. 2. Преимущества углеродистых сталей:
- низкая стоимость изготовленного из этих сталей режущего инструмента;
- высокая поверхностная твердость и вязкая сердцевина материала, обеспечивающие улучшенные механические свойства режущего инструмента;
- возможность закалки при умеренной температуре (не выше 770–820°C), при этом аустенит остается в минимальном количестве, что повышает устойчивость инструмента к пластической деформации;
- при охлаждении в воде после закалки поверхность режущего инструмента остается чистой.
- Недостатки углеродистых сталей:
- предел твердости сохраняется до 170–200°C;
- низкая прочность в сравнении с прочностью быстрорежущих сталей (HSS) вследствие более крупного зерна, причем зернистость повышается даже при незначительном нагреве сталей во время закалки. Кроме того, при изготовлении инструмента могут появиться неравномерность твердости, внутренние напряжения и трещины;
- повышенная склонность к отпуску наружных слоев при нагреве в процессе работы, шлифовки или заточки, поэтому такие стали рекомендуется использовать для изготовления небольших инструментов (концевых фрез и сверел диаметром не более 30 мм), особенно если предполагается большое давление на рабочие кромки.
Углеродистые стали чаще применяют для изготовления ручного режущего инструмента, в том числе электрифицированного, наиболее подходящего для обработки мягколиственной древесины.
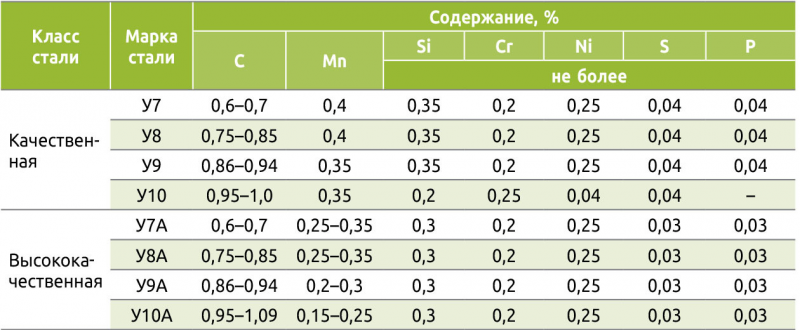
Легированные быстрорежущие стали
По химическому составу быстрорежущие стали подразделяются на три основные группы:
- с высоким содержанием вольфрама (W);
- молибденовые (M);
- высоколегированные.
Быстрорежущие стали широко применяются для изготовления различного режущего инструмента, работающего в условиях высоких силовых нагрузок и сильного (выше 600–640°С) нагрева режущих кромок. К этой группе сталей относятся высоколегированные вольфрамом (W) вместе с другими карбидообразующими элементами (молибденом, хромом и ванадием) стали, приобретающие высокие твердость, прочность, тепло- и износоустойчивость в результате двойного упрочнения – мартенситного при закалке и дисперсионного при относительно высоком (500–620°С) отпуске.
Для импортных легированных быстрорежущих сталей используются следующие обозначения:
SP – легированная инструментальная сталь, применяемая для обработки мягких лиственных и хвойных пород;
HL – высоколегированная инструментальная сталь для обработки мягких пород дерева;
HS (HSP) – высокопроизводительная быстрорежущая сталь с содержанием не более 6–8% вольфрама, используемая для обработки мягких и средне-твердых лиственных пород, а также иногда для работы с твердыми породами дерева;
HSS – высокопроизводительная быстрорежущая сталь, содержащая 18% вольфрама, с покрытием для обработки дерева, включая древесину твердых лиственных и хвойных пород.
Для маркировки отечественных быстрорежущих сталей применяется буква Р (от rapid – «быстрый») и цифра, отражающая среднее содержание вольфрама в составе, а затем буквы, указывающие наличие других легирующих элементов как в стандартной маркировке легированных сталей: Б – ниобий (Nb), Н – никель (Ni), Ф – ванадий (V), В – вольфрам (W), М – молибден (Mo), Х – хром (Cr), Г – марганец (Mn), К – кобальт (Co), Т – титан (Ti), А – азот (N) – только в середине обозначения стали. Цифры после букв указывают примерное содержание легирующих элементов в целых процентах. Отсутствие цифры означает, что содержание легирующего элемента до 1,5%.
В маркировке быстрорежущих сталей не отражается содержание углерода и хрома (их массовая доля ≥1% и ≥ 4% соответственно), а также молибдена (до 1% включительно) и ванадия в сталях Р18, Р9, Р9К5, Р6М5, азота – в сталях марок 11Р3АМ3Ф2 и Р2АМ9К5.
По основным свойствам быстрорежущие стали подразделяются на пять групп:
- умеренной теплостойкости (типа Р9, Р6М5);
- повышенной износостойкости (типа Р12Ф3, Р6М5Ф3);
- повышенной теплостойкости (типа Р6М5К5, Р9К5);
- высокой износо- и теплостойкости (типа Р18К5Ф2);
- высокой твердости и теплостойкости с улучшенной шлифуемостью (типа Р9М4К8, В11М7К23).
Вместе с тем у этих сталей много общих характеристик. Поэтому для упрощения рассмотрения особенностей структуры, свойств и режимов термообработки их можно разделить на три группы по производительности обработки:
- стали нормальной производительности (стали умеренной теплостойкости);
- стали повышенной производительности (стали повышенной тепло- и износостойкости);
- стали высокой производительности (стали высокой тепло- и износостойкости с улучшенной шлифуемостью).
Наиболее известные отечественные легированные стали, предназначенные для изготовления дереворежущего и измерительного инструмента, – 7ХФ, 9ХФ, 9ХС, 9ХВГ, 9Х5ВФ, Р6М5, Р9, Р12, Р18, Р6МЗ, Р9К5, Р9К10, Р18К5Ф2 и др.
Химический состав легированных и быстрорежущих инструментальных сталей, применяющихся для дереворежущих инструментов, представлен в табл. 3.
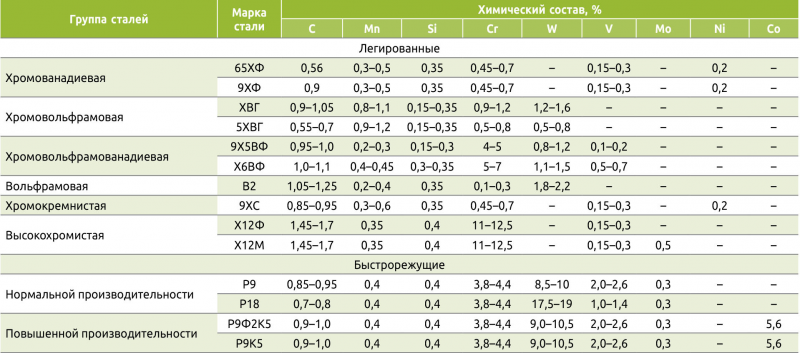
Закалка, напыления и покрытия режущего инструмента из легированных сталей
Инструменты из быстрорежущих сталей приобретают высокую твердость и теплостойкость при удовлетворительных прочности и вязкости в результате закалки и многократного отпуска.
При нагреве под закалку необходимо обеспечить максимальное растворение в аустените труднорастворимых карбидов вольфрама, молибдена и ванадия. Такая структура увеличивает прокаливаемость и позволяет получить после закалки высоколегированный мартенсит высокой теплостойкости. Поэтому температура закалки очень высокая – 1200–1300°С.
Инструменты простой формы закаливают в масле, а сложной – в растворах солей (KNO3) при 250–400°С.
После закалки структура быстрорежущей стали состоит из высоколегированного мартенсита, содержащего 0,3–0,4% С, не растворенных при нагреве избыточных карбидов и примерно 20–30% остаточного аустенита. Последний снижает твердость, режущие свойства инструмента, ухудшает шлифуемость, и его присутствие нежелательно.
При многократном отпуске из остаточного аустенита выделяются дисперсные карбиды, легирование аустенита уменьшается и он претерпевает мартенситное превращение. Обычно применяют трехкратный отпуск при 550–570°С в течение 45–60 мин. Число отпусков может быть сокращено при обработке холодом после закалки, в результате чего уменьшается содержание остаточного аустенита. Обработке холодом подвергают инструменты сравнительно простой формы. После закалки твердость достигает HRC 62–63, а после отпуска она повышается до HRC 63–65.
Для дальнейшего повышения твердости, износостойкости и коррозионной стойкости поверхностного слоя режущих инструментов применяют такие технологические операции, как цианирование, азотирование, сульфидирование, обработку паром и другие способы поверхностного упрочнения. Их проводят после окончательной термообработки, шлифования и заточки инструментов.
Для улучшения характеристик готовые изделия из инструментальных сталей покрывают разными составами. Зачастую специальные покрытия позволяют повысить стойкость режущего инструмента на 15–20%.
Сегодня для режущего инструмента из HSS по древесине и ДПК чаще всего применяются следующие покрытия и напыления:
- TiN – напыление нитрида титана (желто-золотистое), однослойное покрытие, повышает поверхностную твердость инструмента до ~2300 HV (микротвердость от 20–25 ГПа) и термостойкость до 600°C, а также упругость инструмента и сцепление с материалом, облегчает отвод стружки, снижает общее трение и вибрацию;
- TiAlN – напыление нитрида титана, легированного алюминием (серо-фиолетовое, почти черное), наноструктурированное покрытие, повышает поверхностную твердость инструмента до ~3300 HV (микротвердость от 30–33 ГПа), термостойкость до 900°C, снижает поверхностное трение и вибрацию и в итоге за счет более низкого коэффициента трения, чем в случае покрытия TiN, значительно повышает стойкость и производительность инструмента;
- Black (BlackOxide) – оксидирование, обработка в среде перегретого пара (черная оксидная пленка), часто используется на концевых фрезах, иногда на сверлах, хорошо работает по ДПК и не подходит для цветных металлов, повышает стойкость инструмента к ржавчине (коррозии), продлевает срок его службы, а также предотвращает перегрев при высоких скоростях обработки;
- TiC – напыление карбида титана, повышает твердость инструмента до 2800–3000 HV, термостойкость – до 720°C, но обуславливает низкую стойкость к разрушению – 45–55 H;
- TiCN – напыление карбонитрида титана (серо-голубого цвета), многослойное покрытие, повышает поверхностную твердость до 3000 HV и термостойкость до 400°C, по твердости TiCN превосходит TiC-напыление, а по пластичности не уступает TiN;
- TiALN+WC/C – покрытие на основе алюмонитрида титана (темно-серое), многослойное, повышает твердость до ~3300 HV, а термостойкость – до 800°C;
- CrN – напыление нитрида хрома (серебристо-серое), однослойное покрытие, повышает твердость инструмента до 1750 HV и стойкость к нагреву до 700°C, обеспечивает оптимальное соотношение твердости и пластичности, повышает стойкость инструмента к коррозии, появлению трещин даже при циклических нагрузках;
- AlCrN – покрытие нитридом хром-алюминия (серо-синее), однослойное, повышает твердость до 3200 HV, а стойкость к перегреву – до 1100°C.
Применение инструментальных сталей
Выбор стали для изготовления инструмента, основанный на условиях его работы и виде обрабатываемого материала, дает возможность максимально использовать свойства выбранной марки и, как следствие, рационально расходовать легирующие материалы, а также определять необходимость тех или иных покрытий, наплавки (напайки) и других способов поверхностного упрочнения.
Рекомендуемые области применения наиболее распространенных марок быстрорежущих сталей в зависимости от типа обрабатываемых материалов и вида обработки представлены в табл. 4. Такой подход к выбору инструментальных сталей любого назначения способствует повышению производительности и экономичности любого производства.
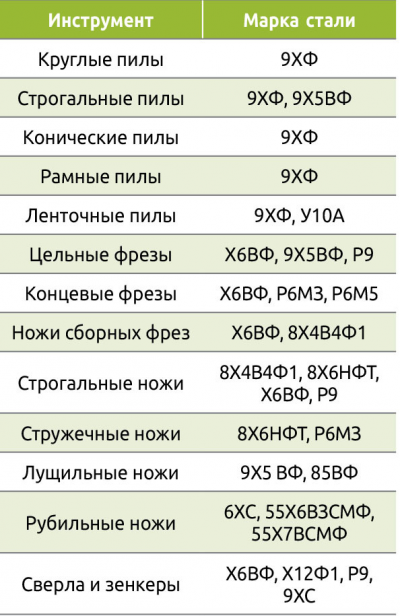
Порошковые быстрорежущие стали
Использование в производстве инструментов порошковых сталей вместо быстрорежущих традиционного производства позволяет получить мелкозернистую структуру с равномерным распределением дисперсных карбидов при отсутствии макро- и микроликвации и шлаковых включений, а также повысить технологическую пластичность, что особенно важно для сложнолегированных высокоуглеродистых сталей.
В силу указанных особенностей порошковые быстрорежущие стали характеризуются высокими теплостойкостью, износостойкостью и технологичностью.
Согласно технологии получения порошковой стали исходная шихта, состоящая из порошка или тонко измельченной стружки быстрорежущей стали (с добавлением 1% парафина), подвергается холодной формовке и последующему твердофазному спеканию заготовок. Спекание производится при 1180°С в вакууме в течение 3–5 ч. Для уменьшения пористости заготовки подвергаются дополнительной горячей штамповке или прессованию. После этого заготовки отжигаются в защитной среде. Твердость после отжига достигает 269–285 НВ в зависимости от марки стали.
Термическая обработка порошковых быстрорежущих сталей отличается от обработки сталей, произведенных по традиционной технологии. После механической обработки изготовленный из них инструмент, особенно сложной формы и крупногабаритный, целесообразно подвергать отжигу для снятия напряжений (680–720°С). Последующая закалка и трехкратный отпуск проводятся так же, как для инструмента из обычных быстрорежущих сталей.
Литые твердые сплавы
Литые твердые сплавы – стеллиты, сормайты – занимают промежуточное положение между быстрорежущей сталью и металлокерамическими твердыми сплавами.
Стеллиты применяются в виде наплавок на режущую часть дереворежущего инструмента посредством автогенной сварочной аппаратуры или электродугового метода. Износоустойчивость дереворежущего инструмента с наплавкой из стеллитов в 2–3 раза выше износоустойчивости инструмента из быстрорежущей стали. Основные характеристики литых твердых сплавов приведены в табл. 5.
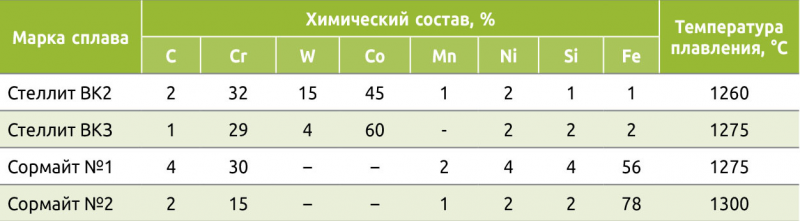
Металлокерамические твердые сплавы
Твердые сплавы – это сплавы на основе высокотвердых и тугоплавких карбидов вольфрама, титана, тантала, соединенных металлической связкой, как правило, кобальтом.
Применяемые для дереворежущего инструмента твердые сплавы относятся к металлокерамическим. Твердые сплавы получают методом порошковой металлургии. Порошки карбидов (WC) смешиваются с порошком кобальта (Co), эта смесь спрессовывается в изделия необходимой формы, которые спекаются при 1400–1550°С в защитной атмосфере (водород) или в вакууме. При спекании кобальт плавится и растворяет часть карбидов, что позволяет получить плотный материал (пористость не превышает 2 %), на 80–97% состоящий из карбидных частиц, соединенных связкой. Увеличение содержания связки вызывает снижение твердости и повышение вязкости.
Твердые сплавы производят в виде пластин, которыми оснащаются режущие инструменты (резцы, сверла, фрезы и др.), а также прутков (для концевых фрез и сверел) и элементов измерительных инструментов.
Такие инструменты характеризуются высокой твердостью HRA 80–92 (HRCЭ 73–76), износостойкостью и высокой теплостойкостью (до 800–1000°С). По эксплуатационным свойствам они превосходят инструменты, выполненные из инструментальных сталей. Их недостатки – высокая хрупкость и сложность изготовления фасонных изделий.
Свойства твердых сплавов и, следовательно, область их применения зависят от состава и зернистости карбидной фазы (WC, TiC, TaC), а также от соотношения карбидной и связывающей фаз.
В соответствии с ГОСТ 3882-74 в РФ выпускаются три группы твердых сплавов: вольфрамовая (однокарбидная), титановольфрамовая (двухкарбидная) и титанотанталовольфрамовая (трехкарбидная).
Сплавы вольфрамовой группы (WC–Со) характеризуются самой высокой прочностью, но низкой твердостью в сравнении со сплавами других групп. Теплостойкость этих сплавов достигает 800°С. Их применяют в режущем инструменте для обработки чугунов, сталей, цветных сплавов и неметаллических материалов. Повышенная износостойкость и сопротивляемость ударам определяют применение таких сплавов в горном инструменте и для изготовления штампов, пуассонов, матриц, фильер и т. п.
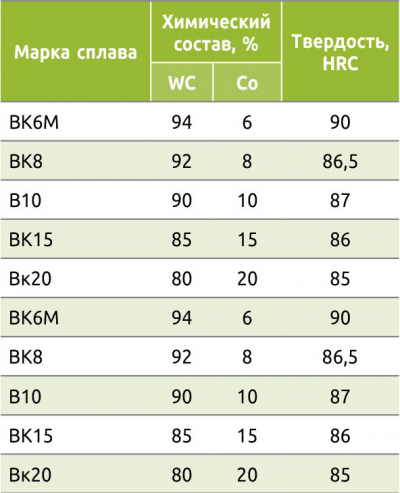
Сплавы титановольфрамовой группы (WC–TiC–Co) отличаются высокими теплостойкостью (до 900–1000°С) и твердостью. Их применяют в основном для высокоскоростной обработки сталей и чугунов.
Сплавы титанотанталовольфрамовой группы (WC–TiC–TaC–Co) отличаются от сплавов предыдущей группы более высокой прочностью, лучшей сопротивляемостью вибрациям и выкрашиванию. Они применяются в наиболее тяжелых условиях резания – при черновой обработке стальных поковок, отливок, а также труднообрабатываемых сталей и сплавов.
Общим недостатком всех рассмотренных твердых сплавов (помимо высокой хрупкости) является дефицит исходного вольфрамового сырья – основного компонента, определяющего их высокие физико-механические характеристики. В связи с этим перспективно использование безвольфрамовых твердых сплавов. Хорошо себя зарекомендовали сплавы, в которых основой служит карбид титана, а связкой – никель и молибден. Они маркируются буквами КТС и ТН. Твердые сплавы КТС-1 и КТС-2 содержат 15–17% Ni и 7–9 % Mo соответственно, остальное – карбид титана. В твердых сплавах ТН-20, ТН-25, ТН-30 в качестве связующего металла в основном выступает никель, 16–30%, молибдена 5–9%, остальное – карбид титана. Твердость подобных твердых сплавов 87–94 HRA, они характеризуются высокой износо- и коррозионной стойкостью. Их используют для изготовления металлорежущего инструмента и быстроизнашивающихся деталей технологического оборудования.
Текст Владимир Падерин