Развитие лесной промышленности невозможно без новых технологий
С 31 марта по 1 апреля в американском городе Сиэтл, штат Вашингтон, прошел 43-й Международный симпозиум по древесным композитам.
Работой симпозиума руководил президент и главный исполнительный директор компании «Диффенбахер» (Dieffenbacher GmbH), разрабатывающей и изготавливающей прессовальные системы и комплексное технологическое оборудование для производства древесных панелей, Вольф-Герд Диффенбахер (Wolf-Gerd Dieffenbacher).
В своем обращении к участникам симпозиума он призвал мировое бизнес-сообщество в период текущего экономического кризиса принимать активные меры для того, чтобы избежать разочарования во время спада деловой активности и, эффективно используя новые технологические разработки, готовиться к возможному подъему.
Глобальный взгляд на отрасль
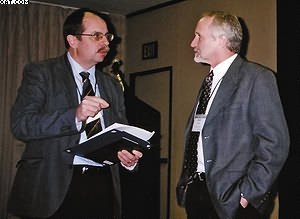
Одна из целей симпозиума − выявить, в каком состоянии дела у поставщиков сырья и насколько они пострадали из-за финансового кризиса, ведь лесопильные предприятия и комбинаты, выпускающие фанеру, всегда выступали отправной точкой для производства древесных композитов. Картина невеселая: многие предприятия этого сектора значительно сократили объемы выпускаемой продукции, вследствие чего и древесных отходов на выпуске становится все меньше и меньше. Чтобы предотвратить неизбежное закрытие или приостановку производства, таким предприятиям приходится закупать более дорогое сырье. Это означает, что они вынужденно вступают в конкурентную борьбу за один и тот же древесный ресурс с работающими на биомассе электростанциями, которые активно поддерживаются государством. Результатом такого обострения конкуренции за сырье становится увеличение его себестоимости. Подобное положение дел может привести к тому, что сырье станет для промышленности чрезмерно дорогим и, как следствие, менее доступным. Кроме того, увеличиваются расходы на защиту окружающей среды, которые заводы обязаны закладывать в общую смету производства.
Но благодаря тому, что цены на нефть упали, у предприятий ЛПК появилась возможность снизить затраты на смолы, сырьем для которых является «черное золото».
Г-н Диффенбахер подчеркнул необходимость создания новых технологий, связанных с сокращением применения смол в плитном производстве. Это вопрос первостепенной важности, так как стоимость смол − одна из самых больших статей расходов в производстве широкой линейки продукции, связанной с древесными композитами. Более того, когда начнется восстановление экономики, заводы, которые потребляют древесное сырье, смогут за счет использования современных технологий ещё больше повысить эффективность своей работы и получить существенные дивиденды от дальновидно сделанных ранее вложений.
В своем выступлении главный исполнительный директор компании «Диффенбахер» также отметил, что сегодня большой потенциал потребления древесных плит в России, Китае, Индии и на юго-востоке Азии, а вот в Европе и в Северной Америке спрос на плиты стал снижаться ещё в 2003 году и продолжался вплоть до 2006 года без перспектив на рост.
Многие из выступавших на симпозиуме в Сиэтле вторили г-ну Диффенбахеру, особенно заявлению главного исполнительного директора компании «Диффенбахер» о необходимости использования современных методов технического контроля в процессе производства важнейшей продукции − MDF, LVL, ДСП и клееной фанеры, обладающей высокими физико‑механическими свойствами.
Плитный рынок Индии
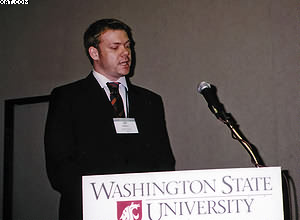
Все вышесказанное стало своего рода кульминацией симпозиума, но были и другие темы, нашедшие живой отклик у участников. Например, большой интерес вызвало выступление исполнительного директора компании Greenply Industries Limited (Индия) Шобхана Миттала (Shobhan Mittal), посвященное особенностям производства плит и их применения в Индии. Аудитория симпозиума внимательно выслушала рассказ о ситуации на рынке седьмой по величине страны в мире, население которой насчитывает около 1,6 млрд человек. ВВП Индии превышает $1 трлн, а доход на душу населения постоянно растет. Если говорить о природных ресурсах, то у Индии высокий рейтинговый показатель: она занимает 10‑е место в мире по площади лесов − на них приходится 20,6% территории страны, что составляет 68 млн га. Плитная индустрия Индии обеспечивает производство всего спектра продукции: от клееной фанеры до MDF и ДСтП. В стране работает большое количество предприятий. Г-н Миттал в качестве примера назвал компании Bhutan Boards (производство ДСтП от 100 м3) и Bajaj Hundustan (производство MDF от 570 м3 в день). В настоящее время планируется запуск двух новых заводов по производству ДСтП: Balaji Action и Star Panel с ожидаемой производительностью соответственно 285 и 600 м3 в день. Более того, полным ходом идет строительство завода Greenply по производству MDF. Планируется, что комбинат будет выпускать до 600 м3 продукции в день (180 тыс. м3 в год). Всего в стране около 20 комбинатов по производству ДСтП и MDF, объемы производимой ими продукции вряд ли могут сравниться с европейскими показателями. Плитный рынок приносит Индии около $2 млрд в год.
Производство плит в Индии началось в 1950 году, когда был построен первый завод по выпуску ДСтП. В конце 1950‑х началось строительство комбината древесно-волокнистых плит, а в 1989 году появилось ещё одно предприятие по выпуску MDF. Индийская фанера, ставшая знаменитой во всем мире благодаря легендарным коробочкам для чая, в 1961 году выпускалась в объемах от 62 520 т в день, в настоящее время показатель упал до 1 461 т в день. Такой упадок производства связан с принятым в 1996 году постановлением Верховного суда Индии о приостановлении лесной деятельности. Сегодня рабочие плитного производства получают в среднем $100 в месяц.
Сотрудники Greenply наряду с другими соотечественниками стараются вывести Индию на уровень развития производства XXI века, так как высокотехнологичные плиты сегодня стремительно завоевывают рынок, находя применение в строительстве сборных домов и в производстве мебели «сделай сам». Экономика также не стоит на месте, и общий спрос на плиты соответственно растет, вследствие чего в стране образовался вакуум, связанный с поставками продукции. По имеющимся данным, после того как к изготавливающим сегодня плиты MDF восьми заводам добавятся ещё несколько планируемых к запуску, суммарный объем выпускаемой ими продукции составит около 600 тыс. м3 в год.
Вард УИЛЬЯМС, специальный корреспондент
Мнение
И все-таки доля оптимизма есть
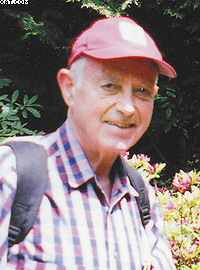
В ходе симпозиума его ведущий Вольф Герд Диффенбахер задал всем участникам вопрос: «В период кризиса обоснован ли оптимизм в сфере производства древесных плит?». Проанализировав выступления участников симпозиума, наш корреспондент Вард Уильямс (Ward Williams, Global Forest Products, Tigard, Oregon, USA) попытался найти ответ на этот вопрос.
С сожалением приходится констатировать: сегодня ответ на вопрос г-на Диффенбахера раздается эхом, как в Сиэтле, так и в моем родном Орегоне: нет! Строительство новых домов заморожено. Большинство разнообразных конструкторских проектов отложено до лучших времен. Большое количество старых и новых домов пустуют по причине задолженности их владельцев. Безусловно, правительство ищет как помочь домовладельцам, но пройдет ещё немало времени, прежде чем его действия дадут желаемый результат.
Строительство новых домов − вот основа развития производства плит и лесоматериалов, но по причине спада в жилищном строительстве предприятия этой отрасли также несут убытки. Лесопильные заводы, комбинаты, выпускающие плиты (MDF, ДСП, древесно-волокнистые, OSB, LVL) и клееную фанеру), а также заводы по производству комплектующих приостановили сегодня деятельность, а некоторые из них, по всей видимости, закрылись навсегда. В плачевном состоянии находится мебельная промышленность. Финансовый кризис серьезно ударил и по лесозаготовительной отрасли.
Предприятия сталкиваются с проблемами невыплат, вследствие чего вынуждены сокращать персонал и уменьшать издержки производства.
Я не первый год принимаю участие в работе этого симпозиума и каждый раз наблюдаю, как несколько сотен специалистов стремятся обменяться опытом в области развития передовых технологий и создания новых образцов продукции. Но то, что я увидел здесь в этом году, не идет ни в какое сравнение: все три дня ораторы вспоминали прекрасное прошлое, работу производственных комбинатов и отрасли в целом в течение последних 20 лет. И все потому, что предприятия и исследовательские институты испытывают огромные финансовые трудности. В этом году в Сиэтл приехали 150 делегатов, в том числе из Австралии, Бельгии, Индии, Италии, Канады, Малайзии, Новой Зеландии, Пакистана, России, Словакии, Чили и Швеции.
Тем не менее, симпозиум, проводимый в Сиэтле при поддержке Вашингтонского университета (Pullman, USA) и проектно-исследовательского центра древесных композитов WSU, продолжает оставаться мероприятием, объединяющим первоклассных специалистов, готовых поделиться с коллегами передовыми технологиями отрасли. Лесопромышленные компании и поставщики коллективно пытаются найти новые решения, многие из которых могут быть воплощены в жизнь уже в ближайшем будущем. Безусловно, не стоит рассчитывать на быструю финансовую отдачу от всех тех передовых нововведений, которые были представлены здесь первоклассными специалистами из университетов, правительства и научно-исследовательских организаций, но то, что это случится рано или поздно − это факт. Поэтому, г-н Диффенбахер, подводя итоги симпозиума, хочется сказать: доля оптимизма все-таки есть!
На симпозиуме был представлен ряд инновационных решений
Специалист по производственным процессам американской компании Flakeboard Горан Оскарсон рассказал, как можно уменьшить расходы, применяя в производстве MDF операцию сухого осмоления.
goran.oscarsson@flakeboard.com
Новый полусухой непрерывный технологический процесс производства тонких древесноволокнистых термоизоляционных плит введен в действие на заводе Gutex в немецком городе Вальдшут.
d.koltze@siempelkamp-usa.com
Представитель компании-производителя плит с сотовым наполнением Stiles Machinery г-н К. Макфадден рассказал о результатах проведенных испытаний этих плит, включая сборку, кромкооблицовку и крепление.
kmcfadden@stilesmachinery.com
Контроль качества плит ДСП, MDF и фанеры с помощью ультразвуковой установки UPU 3000 производства фирмы GreCon, Германия, позволяет своевременно обнаружить отклонения от оптимального технологического процесса.
Новый способ непрерывного измерения толщины в производстве панелей от компании Electronic Wood Systems повышает экономическую эффективность предприятия.
mk@electronic-wood-systems.ru
Итальянская компания PAL предлагает улучшенную технологию получения, сортировки и просеивания древесной стружки для производства ДСП.
alessandro.marcolin@pal.it