«Вологдабиоэкспорт»: 50 000 тонн пеллет в год
На сегодняшний день ООО «Вологдабиоэкспорт» − это одно из самых современных российских предприятий по производству биотоплива. Завод был запущен в феврале 2006 года на оборудовании датского предприятия Andritz Sprout A/S. К настоящему времени компания «Вологдабиоэкспорт» вышла на полную производственную мощность − 50 000 тонн гранул в год. Эксперты уже назвали её единственным предприятием России, успешно производящим заявленные объемы древесных гранул. В этой статье генеральный директор ООО «Вологдабиоэкспорт» Юрий Матюхин анализирует основные причины неудач предприятий по гранулированию биомассы, дает краткое описание полного технологического цикла, делится своими прогнозами развития биоэнергетики в России.
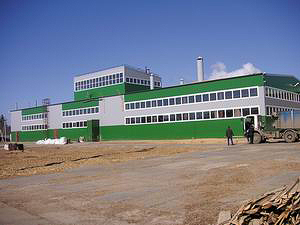
Есть 3 основные причины неудач предприятий по гранулированию биомассы. Первая причина − это ограниченное количество профессионалов, глубоко изучивших технологию производства гранул. Мое замечание относится как к проектным организациям, так и к отдельным инженерно-техническим работникам. Всегда лучше учиться на чужих ошибках, чем их повторять. Жаль, что в сфере производства биотоплива об этом помнят не все. Я регулярно бываю на всевозможных выставках и семинарах и каждый раз наблюдаю тиражирование одних и тех же ошибок. И такое происходит на фоне самых благоприятных условий работы на российском рынке, когда конкуренции нет вообще!
Вторая причина неудач при запуске заводов по гранулированию биомассы − это неприспособленные помещения, в которых руководители пытаются разместить новое оборудование. По сути, они сжимают или даже разрывают оптимальную технологическую цепочку.
Третья причина проблем − это сборное или бывшее в употреблении оборудование, постоянно дающее сбои. Поймите, если установить мотор от современного импортного автомобиля на «Запорожец», никогда «Запорожец» не поедет так же хорошо, как автомобиль, с которого мотор был снят! Можно, конечно, купить и установить на предприятии 1−2 или даже 3 новейших пресс-гранулятора, а все остальное сделать самим или собрать со свалки. Опыт показывает, что и в этом случае выход гранулы есть, правда, ожидаемой производительности достичь не удается.
В России уже получили известность несколько крупных замен оборудования, от использования которого вынуждены были отказаться недавно вступившие в строй производства древесных гранул. Руководителям данных предприятий пришлось заменять не 1−2 шнека, а устанавливать полные комплекты более технологичного оборудования для отдельных производственных участков, и не было другого способа добиться желаемого выпуска продукции.
Международный банк Санкт-Петербурга строил завод, что называется, «в чистом поле». Казалось бы, много ли хлопот, если площадь предприятия − всего 66 на 24 м, высота − 16 м! В перечне затрат пришлось предусмотреть подведение электроэнергии, газа, развитие местной инфраструктуры, складских помещений, очистных сооружений и многое другое. «Вологдабиоэкспорт» первым в России подписал контракт на поставку полного комплекта оборудования завода с датским предприятием Andritz Sprout A/S.
Пока решались вопросы по строительству завода «Вологдабиоэкспорт» и начинался монтаж оборудования, несколько аналогичных производств в России уже построили новые предприятия на оборудовании той же фирмы. Правда, очень скоро выяснилось, что слабо приспособленные производственные помещения и попытка сэкономить, используя оборудование разных фирм-производителей, порождают трудности, о которых уже было сказано выше. Так что вопрос о лидерстве на данный момент решен в пользу ООО «Вологдабиоэкспорт».
Всего в Вологодской области построено около 7 небольших производств, занимающихся изготовлением топливных гранул, скоро к ним присоединятся ещё 10. Если не считать продукции ООО «Вологдабиоэкспорт», все вместе вологодские производители гранул выпускают около 4000 тонн в месяц. Эти объемы сопоставимы с ежемесячным выходом продукции только на одном заводе г. Великий Устюг.
На сегодняшний день крупных европейских покупателей интересует как минимум одна ежемесячная судовая партия древесных гранул, для которой надо собрать не менее 3000 тонн пеллетной продукции. 3000 тонн в месяц − это минимальный взнос для того, чтобы войти в этот клуб делового сотрудничества. Небольшим производствам приходится либо объединяться, либо продавать свою продукцию через спекулянтов.
Преимущества техники от Andritz Sprout A/S
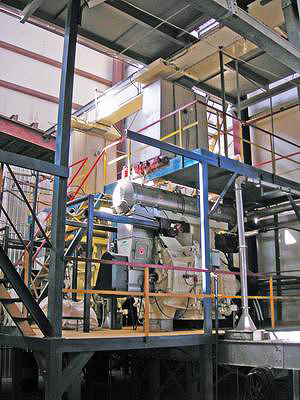
Статуса надежного партнера большинству российских предприятий не позволяют добиться бесконечные пробы и ошибки. Самые частые огрехи встречаются при выборе оборудования для строящихся заводов. В случае если Международный банк Санкт-Петербурга соберется построить ещё 1 завод, безусловно, он будет закупать оборудование у того же поставщика − на предприятии Andritz Sprout A/S. Данное оборудование не самое дешевое на рынке, но есть причины, по которым стоит заключать договор именно с этой фирмой, а не с какой-либо иной. Хочу подчеркнуть, что заявленная производительность оборудования Andritz Sprout A/S полностью соответствует фактической, и это первая причина, побуждающая к работе именно с этим поставщиком.
Более того, 2 пресса, установленные в Великом Устюге, имеют даже большую производительность, чем 3,5 тонны гранул в час. В этом мы смогли лично убедиться. Из сырья, которым располагает ООО «Вологдабиоэкспорт», с каждого пресса-гранулятора получается до 4,5 тонн гранул в час, что на 13% больше, чем указано в техническом паспорте оборудования Andritz Sprout A/S. Значит, 3,5 тонны − это всего лишь гарантированный минимум при плохом сырье и среднем техническом обслуживании.
Вторая важная причина для выбора оборудования Andritz Sprout A/S заключается в том, что оно высокотехнологично, удобно в эксплуатации, позволяет быстро и эффективно производить замену изнашиваемых комплектующих деталей: матриц, роликов и многого другого. Кстати, стоимость запчастей Andritz Sprout A/S на 1 тонну готовой продукции действительно соответствует тем цифрам, которые называют в своем предложении изготовители.
В случае с заводом в Великом Устюге стоимость запчастей на 1 тонну готовой продукции оказалась даже несколько ниже, чем планировалась. На это обстоятельство повлиял ряд показателей, в том числе качество сырья, опыт персонала, регулярность обслуживания оборудования и другие факторы.
Третьей причиной для выбора данного партнера заключается в том, что датчане полностью выполнили перед ООО «Вологдабиоэкспорт» как свои гарантийные обязательства, так и обязательства, связанные с выводом завода на заявленную мощность. Все, что по объективным причинам не подошло для работы на заводе в Великом Устюге, было сразу же заменено самим поставщиком.
Некоторые проблемы возникли лишь потому, что в России нет ни одного предприятия, полностью ориентированного на выпуск гранул из сухого сырья, а именно по этой технологии работают большинство европейских заводов. Датским специалистам пришлось адаптировать некоторые технологические узлы под российскую специфику, поскольку практически весь поступающий в переработку материал (как круглый лес, так и древесные отходы) имеет влажность от 40 до 70 %.
Все узлы, которые не давали достаточной производительности при использовании обычного для нашей страны влажного сырья, датские специалисты заменили за свой счет. Наш опыт позволяет сделать вывод о том, что, если новый построенный завод не даст ожидаемого результата сразу после его наладки, датские специалисты доведут дело до конца. Ещё раз прошу всех своих нынешних и будущих коллег остерегаться использования сборного оборудования, на совместную работу которого никто не даст гарантии. Представьте, что будет, если у вас 8−10 поставщиков оборудования, если треть транспортеров вы собрали сами, а другую часть реанимировали со свалок. Кто из поставщиков оборудования ответит за работу завода в целом? По крайней мере я не слышал ни об одном удачном опыте такого рода в России.
Некоторые из импортных грануляторов различных производителей, поступившие в Россию в готовом виде, действительно могут работать неплохо. И все-таки главная проблема заводов по производству биотоплива заключается в другом: для того чтобы вывести завод на заявленную производительность, придется наладить весь цикл подготовки и сушки сырья, организовать бесперебойную загрузку грануляторов максимальным количеством сырья, а также отрегулировать и автоматизировать весь производственный цикл − от рубительной машины или измельчителя до подачи сырья непосредственно в гранулятор. Но даже при достижении полной загрузки самих грануляторов надо ещё и обеспечить качество пеллетной продукции: её влажность, размер, плотность, зольность. Вот почему так важно правильно выбрать поставщика оборудования.
Наши специалисты убедились в том, что имеет смысл заключать договоры не о поставках отдельных частей «разношерстного» оборудования разных производителей, а на полную поставку завода «под ключ».
Надежная технология рождает капитал
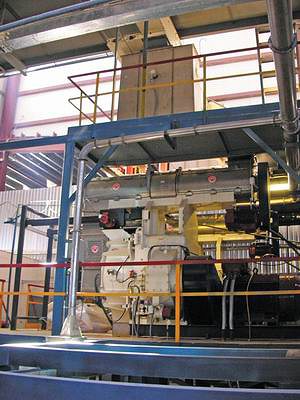
Для выпуска древесной гранулы на ООО «Вологдабиоэкспорт» используются щепа, стружки или опилки. Сначала на участок подготовки сырья выгружается биомасса, только что привезенная от поставщиков. Затем при помощи рубительной машины Bruks Klockner происходит измельчение материала, потом фронтальный погрузчик загружает щепу в бункер, после чего цепной транспортер передает содержимое в производственный процесс.
Поскольку доставленная на предприятие щепа в среднем имеет фракции размером около 5 см и её невозможно равномерно высушить, необходимо перед этим использовать измельчитель древесных гранул. Под действием этой машины щепа измельчается до 0,5−1 см, после чего подается в сушильное оборудование производства швейцарско-итальянской фирмы CRSI. После прохождения через 2 сушильных барабана полученный материал накапливается и измельчается во второй раз до фракции, необходимой для осуществления качественного процесса пресс-гранулирования. Размер фракции должен быть около 3−4 мм.
В дальнейшем пневмотранспортер подает полностью подготовленное сырье в загрузочный бункер пресс-грануляторов. Непосредственно перед подачей в камеру гранулирования биомасса дополнительно обрабатывается паром. Наконец, выходит долгожданная гранула. Она сразу же попадает в охладитель, затем в вибросито, где удаляются мелкие некондиционные частицы, образовавшиеся в процессе гранулирования. И только после данной процедуры уже готовые пеллеты накапливаются в бункере готовой продукции и грузятся в биг-бэги.
Технологическая специфика работы завода имеет особенность в том, что сама линия состоит из большого количества транспортеров (в том числе и пневматических), шнеков, гидравлических подвижных полов, других структурных единиц. Каждый из этих узлов по технологии дает загрузку следующему звену, функционально определяя общую производительность завода в целом. Если хотя бы один из транспортеров или шнеков отказывает в работе или не обеспечивает необходимую производительность, тогда и весь завод начинает давать сбои.
Один из ярких примеров данной проблемы − это работа сушильного оборудования. Если в этот отсек не будет регулярно подаваться достаточное количество сырья по причине остановки или внезапного уменьшения производительности подающего шнека, температура на входе в сушильный барабан мгновенно достигнет 900 градусов, сработает автоматика, завод экстренно остановится.
Система защиты реагирует адекватно, в противном случае неминуемо должен возникнуть пожар. Впрочем, для его успешного предотвращения обязательно включатся системы пожаротушения и другие блокирующие устройства. В любом случае, эти или другие отклонения от распорядка производства нежелательны, так как при малейшем сбое технологического цикла происходит сложная цепная реакция всего оборудования. После завершения этой реакции требуется значительное время для того, чтобы вновь запустить завод в обычном режиме. Фактически от надежности работы одного шнека стоимостью 1000−2000 долларов может зависеть аварийность завода стоимостью 9 млн долларов.
О том, как предприятие работает в действительности, сколько сил и энергии требуется от каждого сотрудника, можно судить по тому, что ежечасно завод производит более 7 тонн гранул.
Очень важно, что весь завод управляется посредством 1 компьютера. Старший оператор смены все свое рабочее время проводит за этим пультом. На экране он видит все характеристики действий пресс-грануляторов, показатели работы двигателей, температуру пара и многое другое, следит за процессом подачи сырья, выставляет те или иные технические параметры, обеспечивающие бесперебойную работу грануляторов и всего оборудования в целом.
Управление оборудованием полностью автоматизировано. Если на экране появляется надпись красного цвета, это означает, что какой-то узел временно вышел из работы. Возможно, забился один из переходов, что привело к остановке транспортера. В таких случаях компьютер выдает письменный отчет о том, какой именно транспортер или электродвигатель вышел из строя. Если возникла более серьезная проблема, раздается дополнительный звуковой сигнал и в зависимости от серьезности неисправности автоматика отключает отдельный узел или завод в целом.
В каждой смене заняты по 6 человек, а всего на производстве круглосуточно находятся 24 работника. Также необходимо наличие электрика, специалиста по КИП, энергетика, специалиста по газовому хозяйству, специалистов по подготовке пара − всего 80 человек. В основном это молодежь с высшим образованием, после армии, все до одного, включая генерального директора, прошли специальную переподготовку у датских специалистов.
Пеллетные капризы
Единственное, что останавливает инвестора в желании построить ещё 1 завод, − это не очень высокая цена реализации гранул и постоянно растущие цены на логистику, сырье, газ, электроэнергию. За год работы предприятия стоимость всех видов затрат значительно выросла, при этом в мае 2007 года на европейском рынке пеллет сложилась ситуация, когда цены на гранулы упали до тех, что были в мае 2006 года. Таким образом, прошедший отопительный сезон показал, что пеллетный рынок крайне зависим от капризов погоды.
Как известно, среди производителей древесных гранул появились предприятия, которые начали использовать свои же изделия для отопления производственных помещений. В ближайшее время мы не собираемся следовать их примеру. Все-таки в России есть ещё альтернативная более дешевая энергия, и пока гранулы выгоднее продавать. Продукция ООО «Вологдабиоэкспорт» полностью уходит на экспорт в Швецию, Германию, Швейцарию. И пока это происходит только через порт Санкт-Петербурга.
В России потребление гранул только начинает развиваться. К примеру, у предприятия «Вологдабиоэкспорт» есть заказы от российских потребителей, закупивших котлы на биотопливе, действующие ныне в непосредственной близости от Великого Устюга. К сожалению, эти заказы невелики − на 150 тонн в год. Вся партия заказа вырабатывается за сутки работы завода.
Выходит, что нам ещё рано ориентироваться на сотрудничество данного типа, хотя становится все более очевидно, что рынок уже начал формироваться в сторону роста спроса на гранулы. Есть уверенность, что в ближайшей перспективе будет реализация пеллетной продукции и в Российской Федерации.
Гранулы, производимые на заводе в Великом Устюге, имеют очень высокое качество, что оценили покупатели в Европе. К примеру, зольность нашей гранулы − всего 0,7 %. Это намного ниже, чем допускается импортерами, которые указывают в договорах 1,5% зольности как максимально допустимый предел по данному показателю.
Практически гранулы из Великого Устюга можно использовать не только для отопления иностранных электростанций, но и для обогрева частных домов хоть в нашей стране, хоть за рубежом. Гранулы ООО «Вологдабиоэкспорт» не выглядят белыми, как того требует европейская традиция рынка бытовых гранул, но это не говорит о том, что они некачественные. Выбраковке по принципу цвета наша продукция не подлежит, потому что при сушке традиционно влажного российского сырья выделяются смолы, сгущающие пеллетный древесный колор. Кроме того, проходя через сушильное оборудование и нагреваясь до 400 градусов, древесина меняет свой структурный состав, так что гранула темнеет ещё и по этой причине.
Однако, если однажды покупатели крупных партий потребуют изменения некоторых характеристик гранулы из Великого Устюга, включая её цвет, на оборудовании Andritz Sprout A/S, в принципе, эту задачу можно решить без проблем.
Юрий МАТЮХИН, генеральный директор ООО «Вологдабиоэкспорт»,
начальник департамента холдинга Международного банка Санкт-Петербурга