С чем едят четырехсторонники
Уважаемые читатели!
В третьем номере нашего журнала («Глас семи нянек», «ЛесПромИнформ» № 3, 2007. — С. 42 ) мы заявили, что намерены организовать на наших страницах обсуждение техники и технологий для деревообрабатывающей промышленности. Идею таких «форумов» мы уже в течение мая интенсивно обсуждаем с дружественными нашему журналу компаниями, среди которых есть и те, кто продает оборудование, и те, кто его использует. Решено было начать с материала по четырехсторонним станкам. Почему? Просто потому, что с чего-то все равно надо начинать, а эта тема сегодня одна из самых обсуждаемых.
В качестве первого шага в этом направлении мы проводим опрос наших рекламодателей и читателей на предмет того, что важно учитывать при выборе четырехстороннего станка, прежде чем его купить, а также каковы актуальные вопросы эксплуатации этих станков. Предлагаем всем заинтересованным лицам поделиться своим мнением по этому поводу. Сделать это можно, либо отправив письмо главному редактору по электронной почте или факсу, либо позвонив непосредственно к нам в редакцию. Все контактные данные вы найдете на первых страницах этого номера.
К настоящему времени мало кто из производителей и дилеров четырехсторонников успел отреагировать на наши запросы и предоставить в редакцию обстоятельные ответы — все готовились, а потом уехали на выставку Ligna+ в Ганновер. Именно поэтому мы особенно благодарны компании «Глобал Эдж» за тот материал, который она подготовила специально для нас к этому номеру. Это в некотором смысле «ликбез» по четырехсторонникам, полезный, прежде всего, для новичков, но материал может представлять интерес и для профессионалов.
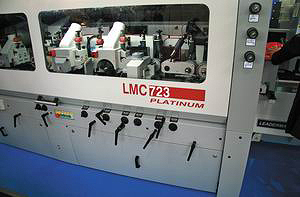
Четырехсторонние станки, дававшие возможность за один проход обрабатывать длинномерные детали из древесины, были впервые разработаны в первой четверти ХХ века. У нас они получили неверное наименование «строгальные», с которым приходится бороться и до сих пор. Дело в том, что строгание — процесс обработки поверхности резцом, перемещающимся параллельно обрабатываемой им поверхности. Так, в чистом виде процесс строгания наблюдается в производстве строганого шпона или при циклевании. В четырехсторонних станках обработка поверхности осуществляется вращающимися фрезами или ножевыми головками — происходит процесс фрезерования. При этом каждое лезвие режущего инструмента описывает циклоиду, а обработанная поверхность формируется в виде параллельных друг другу вогнутых участков, образовавшихся при взаимном движении фрезы и детали.
Поэтому в начале 70-х годов прошлого века при разработке стандарта на эти станки они были названы в нем четырехсторонними продольно-фрезерными, хотя, как дань традиции в скобках ещё оставалось наименование «строгальные», которое предполагалось исключить при первом же пересмотре ГОСТ.
Наименование «калевочные», также относящееся к этим станкам, происходит от русского наименования рубанка «калевка», в свою очередь, происшедшего от немецкого Kehle — «углубление, выемка». В русской терминологии под калевкой понимается также профильная выемка, идущая по пласти детали вдоль всей её кромки. Раньше калевочными назывались четырехсторонние продольно-фрезерные станки, оснащенные дополнительным пятым шпинделем, как раз и осуществлявшим фрезерование профиля. Но сегодня все современные станки могут выполнять фрезерование профиля сечения погонажных деталей, что сделало применение термина «калевочный» нецелесообразным.
Количество типов четырехсторонних станков очень велико. Они различаются по своим технологическим возможностям, количеству фрезерных агрегатов, по их конструкции и взаимному расположению.
Одно из главных отличий — возможность осуществлять фугование нижней пласти заготовки и её кромки (обычно правой) с целью устранения коробления заготовок, возникающего в процессе сушки из-за появления внутренних напряжений.
Станки четырехсторонние фуговально-фрезерные оснащаются длинным загрузочным столом с продольной линейкой, на который покоробленная обрабатываемая заготовка укладывается выпуклой стороной вверх и наружу. При её продвижении в станок по фуговальному столу вручную, первый фрезерный агрегат формирует на ней базирующую поверхность, которой она начинает опираться на основной стол станка. При такой обработке деталь не распрямляется и на её нижней стороне образуется плоскость, служащая базой для всей последующей обработки. Аналогично происходит и обработка кромки. Покоробленность деталей по пласти и кромке оценивается станочником индивидуально для каждой из них, а величина снимаемого припуска регулируется изменением положения стола и направляющей линейки относительно горизонтального и вертикального фрезерующих шпинделей. Наличие получаемых после первоначального фрезерования двух обработанных баз и обеспечивает получение прямолинейных деталей.
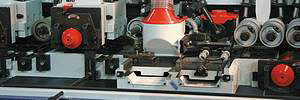
Если четырехсторонний станок не имеет фуговального стола, это значит, что сушка проводится всегда идеально и после нее не происходит коробления, требования к величине покоробленности деталей отсутствуют или заготовки предварительно обрабатываются на отдельном фуговальном станке.
Четырехсторонние станки различаются также по размеру обработки (наибольшей ширине и толщине деталей). Можно условно разделить четырехсторонние станки по ширине обработки на четыре группы: до 100, 170, 220−250 и более 300 мм. Существуют и четырехсторонние станки, построенные на основе двухсторонних рейсмусовых с шириной обработки 900 и даже 1200 мм, дополнительно оснащенных на выходе двумя вертикальными фрезерными суппортами. Параметр ширины обработки является главным и определяет мощность всех агрегатов станка и, соответственно, его цену.
Другой конструктивный параметр — вид механизма подачи. Они разделяются на концентрированные, состоящие из двух пар вальцев, расположенных на входе станка и осуществляющих проталкивание заготовок торец в торец, и распределенные, состоящие из приводных роликов, осуществляющих прижим обрабатываемых заготовок к рабочему столу станка и их одновременное продвижение по нему. Преимущество механизмов второго типа в том, что последние заготовки не остаются в станке, а выводятся из него, отсутствует смещение заготовок при наличии у них неправильно обрезанных торцов, разворот роликов на некоторый угол по отношению к направлению подачи дает возможность одновременно осуществлять дополнительный прижим заготовок к направляющей линейке. Недостаток — меньшее усилие подачи из-за наличия трения по столу заготовки, прижимаемой к нему роликами механизма подачи, что заставляет использовать смазку, наносимую на стол, и удалять её фрезерованием нижней пласти заготовки фрезой, установленной на выходе из станка.
На цену станков оказывает влияние и максимальная скорость подачи, которая у небольших станков, предназначенных для предприятий с малыми объемами выпуска продукции, составляет не более 20 м/мин, а у самых мощных — до 300, 450 и даже до 600 м/мин!
Большое значение имеет конструкция фрезерных суппортов. Так, при большой ширине обработки (свыше 300 мм) шпиндели с фрезами во избежание вибраций оснащаются съемными опорами. При меньшей рабочей ширине станка шпиндели делают в виде консоли. Станки, у которых шпиндели не имеют ременных передач (клино- или плоскоременных), имеют более простую конструкцию и не требуют замены ремней в процессе эксплуатации.
Также важно, какими устройствами для торможения оснащены шпиндели. Такие устройства делятся на механические и электрические, когда электродвигатель останавливаемого шпинделя переводится в генераторный режим, чем и создается сопротивление вращению, приводящее к быстрому затормаживанию. Наличие таких устройств обязательно, поскольку в соответствии с действующими нормами безопасности вращающийся инструмент должен остановиться не более чем за 6 с после нажатия кнопки «Стоп».
При выборе оснащения станка особую роль играет профиль сечения обработанной детали. Так, если на выходе из станка она имеет прямоугольное сечение, то наименьший съем припуска будет производиться правой фрезой, обрабатывающей кромку, несколько больший съем припуска — левой фрезой, ещё больший — первой нижней, а самый большой — верхней горизонтальной. Соответственно должна выбираться и мощность электродвигателей всех шпинделей. Но если деталь должна иметь сложный профиль, в особенности с глубокими продольными выемками, то требуемая мощность шпинделей подлежит специальному расчету. Ведь, если мощность даже одного шпинделя окажется недостаточной, это приведет к существенному снижению производительности всего станка.
Профиль детали заставляет производить выбор не только мощности, но и последовательности обработки — взаимного расположения горизонтальных и вертикальных шпинделей и их количества. При этом может оказаться, что некоторые вертикальные шпиндели (расположенные слева) должны иметь возможность наклона. Некоторые глубокие профили не могут быть обработаны только одной фрезой — для их формирования используются два шпинделя, располагаемых последовательно: один для съема основного припуска, а второй — для чистового фрезерования.
Самые сложные профили обрабатываются с использованием дополнительного суппорта, шпиндель которого имеет возможность обрабатывать детали под любыми углами к горизонтали и вертикали: сверху, сбоку, слева и справа. В некоторых случаях появляется необходимость оснащения станка двумя такими суппортами.
Общее число шпинделей в одном станке, предназначенном для обработки особо сложных профилей, может быть более десяти!
На последовательность обработки сложного профиля в станке накладывает ограничения и необходимость обеспечить надежный контакт роликов механизма подачи с его верхней поверхностью: если она окажется слишком узкой, то может наблюдаться проскальзывание и её повреждение роликами.
Конструкция шумопоглощающих кожухов всех известных четырехсторонних станков не может обеспечить уровня шума на рабочем месте станочника, не превышающего 60 Дб, как это предусмотрено нормами. Фактический уровень звука от работающего станка, как правило, превышает 100 Дб. Поэтому наиболее мощные станки помещаются в отдельную шумопоглощающую кабину, располагаемую внутри цеха и имеющую проемы для пропускания заготовок и обработанных деталей, и плотно закрывающиеся двери для входа внутрь.
Как правило, большинство фирм, производящих четырехсторонние станки, специализируется на оборудовании с определенными, довольно ограниченными размерами обработки. Это в первую очередь связано с унификацией отдельных узлов и агрегатов.
Так, очень мало фирм, выпускающих легкие станки, с рабочей шириной до 100 мм, которые производили бы, например, оборудование для фрезерования бруса сечением 220×350 мм. Почти нет и фирм, производящих тяжелые станки с рабочей шириной 900 мм и более, которые выпускали бы станки с шириной даже 300 мм.
Поэтому любой потребитель при выборе станка должен ясно понимать, какие требования будут к нему предъявляться: будет ли необходимо фугование, как велики будут припуски на обработку по ширине и толщине, какие профили будут фрезероваться и какая требуется производительность (скорость подачи). Именно это определяет конструкцию, оснащение станка и его цену. Ведь четырехсторонний станок нельзя будет просто дооснастить или модернизировать: повышение мощности шпинделей может оказаться невозможным, например, из-за слишком малой мощности механизма подачи.
При приобретении нескольких станков желательно, чтобы все они были поставлены одним производителем: унификация станков в рамках гаммы одного изготовителя упрощает снабжение быстроизнашивающимися деталями, запасными частями, обучение персонала настройке и наладке.
Специалисты компании «Глобал Эдж»
Одной из фирм, выпускающих надежные четырехсторонние станки в виде нескольких гамм, различающихся размерами обработки, предназначенные для использования в производстве столярно-строительных изделий, деталей мебели, в деревянном домостроении и других отраслях, является американская фирма Leadermac, 30 лет назад организовавшая свое производство на Тайване. Сегодня это известный на весь мир поставщик, оборудование которого успешно эксплуатируется в США, странах Юго-Восточной Азии, в Западной и Восточной Европе, а также в России, предприятиями которой только за последние 10 лет было приобретено несколько сотен четырехсторонних станков этой фирмы.
Её номенклатура включает несколько гамм четырехсторонних станков с рабочей шириной от 100 до 300 мм, со скоростью подачи от 20 до 300 и даже до 450 м/мин, а состав оборудования этих гамм позволяет в зависимости от конкретных условий производства потребителя точно подобрать мощность шпинделей, их количество и расположение. Поставки этих станков со своего склада в Москве осуществляет компания «Глобал Эдж», которая производит также их монтаж, наладку, обучение персонала потребителя, поставку быстроизнашиваемых и запасных частей к оборудованию, дереворежущего инструмента, в том числе профильного, гарантийное обслуживание и ремонт по окончании срока гарантии.