Оцениваем качество насадочных фрез
В серии публикаций, которую мы начали в этом году, авторитетные специалисты немецких компаний AKE, JSO, LEITZ, LEUCO и PREWI, входящих в Союз немецких машиностроителей (VDMA), дают свои рекомендации по определению качества деревообрабатывающего инструмента, делятся опытом в его выборе. Эта публикация рассказывает, по каким техническим характеристикам следует определять качество насадочных фрезерных инструментов.
Все начинается с корпуса
Отделить зерно от половы можно, просто внимательно рассмотрев корпус инструмента. Поскольку резцы крепятся пайкой, необходимость в зажимном механизме отпадает, что дает широкие возможности при проектировании каркаса вокруг резца. Итак, корпус можно определенным образом смоделировать вокруг резцов, что улучшает характеристики инструмента. Круглая форма корпуса существенно уменьшает уровень шума на холостом ходу при ручной подаче инструментов (MAN), однако предопределяет ограничения толщины режущей пластины и, как следствие, зоны заточки (такие случаи мы рассмотрим ниже).
Размер, форма и поверхность межзубных впадин определяют, как будет происходить накопление стружки, какими будут потребляемая мощность, качество фрезерования и шумообразование. Широкие межзубные впадины создают много шума, плоские и узкие приводят к многоразовой обработке резанием и большим усилиям подачи. На шершавую поверхность межзубной впадины стружка может налипать вплоть до полного закупоривания впадины. При узких, но глубоких межзубных впадинах уровень шума снижается. Кроме того, стружка легче подается из зоны обработки, что улучшает ее удаление и повышает качество обработанной поверхности.
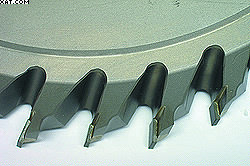
Рис. 3. Оптимизированная межзубная
впадина
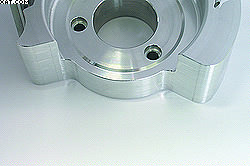
Рис. 2. Инструмент некруглой формы,
например ножевая головка
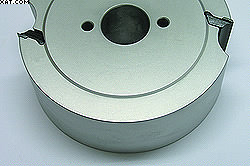
Рис. 1. Инструмент круглой формы,
например ножевая головка
Равномерность стружкообразования на отдельных резцах, а значит, и качество фрезеровки в значительной мере зависят от радиальной и осевой точности резцов. Существенную роль при этом играет точность размеров отверстия и втулки. Лучше всего, если их функциональные поверхности отшлифованы, а не только выточены. От допуска отверстия, кроме того, зависит максимальный эксцентриситет, с которым инструмент установлен на вале, а следовательно, качество балансировки в эксплуатационном стане. Поэтому отверстия нужно делать с минимальным допуском H7.
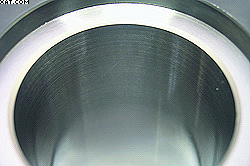
Рис. 6. Шлифованное отверстие
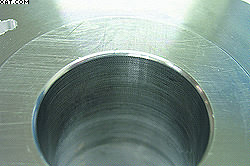
Рис. 5. Отверстие после точения
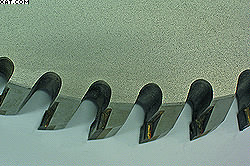
Рис. 4. Меньшая межзубная впадина
На фрезерованной поверхности качество балансировки инструмента отображается в виде своеобразной «волнистости», которую оставляет после себя резец. Чем больше разбалансировка, тем больше и «волнистость». Минимальная точность балансировки фрезы, предусмотренная Европейским стандартом для инструментов деревообрабатывающих станков, − G16. Качественные инструменты, однако, из соображений, о которых шла речь выше, балансируют с еще более высоким уровнем точности − G6,3. А фрезы, которые применяют при обработке на высоких скоростях, когда частота оборотов превышает n = 10 000 мин, для защиты подшипника шпинделя балансируют еще более точно.
Признаки балансировки
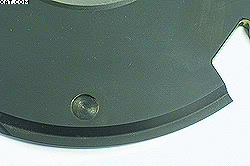
Рис. 7. Высверленный материал во время
балансировки
О качестве инструмента свидетельствуют балансировочные отверстия или шлифованные поверхности, ведь даже в случае применения компьютеризированных проектировочных методов, дающих возможность разрабатывать уже заранее сбалансированный инструмент, нужно компенсировать влияние допусков на готовое изделие. Балансировка − сложная и затратная процедура. Чтобы предотвратить вибрацию во время работы, тонкие инструменты балансируют в одной плоскости (с одной стороны), а широкие инструменты − в двух плоскостях (с двух сторон). Так вот, инструмент, на котором незаметны следы балансировки, может с эстетической точки зрения оставлять лучшее впечатление, но при этом выше вероятность того, что он не сбалансирован. Наконец, это приводит к повреждению подшипников шпинделя, сопровождаемому громким гудением.
Внимание на шов паяния!
Сделать вывод о качестве оборудованных вставками фрез можно, осмотрев форму паяного стыка между режущей пластиной и корпусом. Качественная пайка − это равномерный, без пор, дырок и следов вытекания лишнего припоя шов. Чтобы лучше компенсировать напряжения, возникающие в спайках большой площади, последние выполняют с промежуточным пластом меди − по принципу сэндвича. Поры и дырки снижают прочность, вытекание лишнего припоя приводит к смолообразованию, а клиновидная паяльная щель предопределяет погрешности угла режущей пластины и шага между резцами и приводит в конце концов к радиальному битью инструмента.
Резцы определяют производительность
Выше речь шла о том, что нужно учитывать, чтобы продуктивно и эффективно применять фрезу в процессе обработки. Сама по себе производительность в значительной степени зависит от резцов инструмента. Если предположить, что при его разработке придерживались правильной угловой геометрии, то ключевыми критериями становятся материал резца, толщина вставок и качество шлифовки, а значит, острота резальной кромки.
Насколько чисто отделяются волокна древесины, мнутся ли и вырываются они при этом, зависит прежде всего от остроты режущей кромки. Ее острота − это производная заточки задней и передней поверхностей лезвия резца. В режущей зоне обеих поверхностей образовывается режущая кромка. При максимально гладкой заточке поверхностей − так называемой зеркальной − улучшаются скольжение стружки, уменьшается ее накопление и трение, однако это не свидетельствует о том, что режущая кромка является острой. Ее острота зависит от того, как происходит процесс заточки, например от того, как осуществляется подача, каково усилие шлифования, как выставлен шлифовальный круг. В резцах, изготовленных из твердых сплавов, фаска, образованная вследствие излома резальной кромки, должна быть очень маленькой − примерно 1−2 мкм. У фрез, изготовленных из быстрорежущей стали, для предотвращения износа резца нужно свести к минимуму образование заусениц, чтобы их можно было легко устранять. Простейший способ выяснить, острый ли резец, − проверить, разрежет ли он лист бумаги, если им провести по резцу. Изначально очень острый резец обеспечивает не только высокое качество обработки, но и более длительный срок эксплуатации фрезы.
Поскольку во время паяния неизбежны высокие температуры и большие напряжения, материалы, из которых изготовляют резцы фрез, должны иметь достаточную вязкость, что ограничивает твердость, а значит, износоустойчивость. При условии, что период стойкости резальной кромки не связан с ее поломкой, увеличить его в 3−5 раз, объединив взаимоисключающие свойства − твердость и вязкость, можно, нанеся твердый сплав, так как само покрытие от поломок не защищает.
Фрезы с покрытием лучше поддаются перезаточке
Несмотря на нанесенное покрытие, фрезы можно перезатачивать, поскольку покрытие наносят лишь на одну поверхность − обычно заднюю. На поверхность, которую перезатачивают, покрытие не наносят.
В оборудованных вставками фрезах с резцами из твердого сплава или быстрорежущей стали, как правило, перезатачивают переднюю поверхность. Иногда, чтобы избежать изменения ширины паза, в цельных пазовых фрезах заостряют заднюю поверхность. Количество возможных перезаточек зависит от толщины вставок. С каждой заточкой увеличивается передний угол и уменьшается задний. Поэтому профиль становится все более плоским − можно даже говорить о его искажении. Из-за такого искажения профиля толщину вставок, а значит, зону перезаточки фрез с ровным или вогнутым шлифованием задней поверхности ограничивают до 6−8 мм. Определенные изменения вследствие затачивания допускаются для формы профилей без особых требований к точности подгона. При высоких требованиях к точности воспроизведения профиля всю зону затачивания, однако, иногда полностью использовать невозможно. В таком случае фрезу с самого начала оборудуют пластинами резца меньшей толщины.
В инструментах круглой формы, предназначенных для ручной подачи (MAN-исполнение), из-за ограничений, накладываемых на выступ резца относительно корпуса, максимальную ширину вставок, согласно конструкции составляющую 3 мм, ограничивают приблизительно до 4 мм, иначе при профилировании задней поверхности шлифованию будет подвергаться и корпус. Лучшим решением для увеличения периода стойкости, выраженного длиной резания, является увеличение толщины вставок, воплощенное в MAN-фрезе с отводными упорами. Каждый раз их заостряют на допустимый радиальный выступ резца относительно отводного упора − 1,1 мм.
Закрытые профили, в которых задний угол имеется и сбоку, на боковой поверхности при заточке, кроме укорачивания, о котором шла речь выше, искажаются и в ширину. Чтобы компенсировать это, высококачественные фрезы изготавливают как сборные инструменты. Изменение профиля сбоку компенсируют за счет кольцевой прокладки соответствующего размера. Это дает возможность многократно перезатачивать фрезу, в то время как такую же фрезу, выполненную как сплошной инструмент, можно перезатачивать не более одного-двух раз.
Достичь абсолютной точности воспроизведения профиля можно в том случае, если форма резца предусматривает выпуклую заточку задней поверхности. Типичными примерами такого выполнения инструмента являются так называемые массивные фрезы. Этот тип фрез нуждается в иной технике заточки. Затачивая переднюю поверхность, шлифовальный круг не устанавливают параллельно, поскольку фреза крутится вокруг своей оси. Благодаря этому передний угол остается стабильным, равно как и задний угол в связи с особой выпуклой заточкой задней поверхности. В таких условиях не изменяется и профиль.
Диаметр фрез всех описанных выше конструкций при каждой перезаточке существенно уменьшается, из-за чего необходимо дополнительно переналаживать станок, что может потребовать много времени. Во избежание этого применяют так называемые константные инструменты, в которых резцы в подвижном состоянии закреплены в корпусе таким образом, что после затачивания они всегда восстанавливают прежний диаметр, потому их профиль и диаметр являются постоянными. Применять такие инструменты рекомендуется, например, при изготовлении контрпрофилей или круглопалковых профилей.
Выводы
Как было показано на примере конструкций, описанных в этой статье, делая вывод о фрезе, нужно учитывать не только ее поверхностные качественные признаки, но и оценивать концепцию фрезы, принимая во внимание все аспекты ее использования. Инструмент, который кажется привлекательным благодаря низкой цене, может быть очень затратным из-за того, что не обеспечивает ожидаемое качество обработки и неточен при эксплуатации. Внимательный выбор перед приобретением со временем окупается.
Андреас Киссельбах
Статьи из цикла «Качество режущего инструмента»:
Режущий инструмент: секреты правильного выбора
Оцениваем качество концевого инструмента
Оцениваем инструмент: критерии оценки качества фуговальных фрез
Оцениваем инструмент: строгальные инструменты с интегрированным гидрозажимом
Оцениваем инструмент: Рентабельные сверла по низкой цене… А нет ли здесь противоречия?