Проблемы механической технологии древесины
Этой теме была посвящена прошедшая 26 марта в Санкт-Петербургской государственной лесотехнической академии им. С. М. Кирова очередная ежегодная международная конференция.
Приходится констатировать: решений, способных кардинально изменить ситуацию, сложившуюся сегодня в лесной и деревообрабатывающей отраслях, пока нет. Но предложения, способствующие ускорению выхода лесного сектора на уровень производства, который существовал до 2007 года, имеются. В ходе работы конференции ее участники предлагали различные пути выхода из кризиса, а также пути развития лесопильного производства, технологий сушки пиломатериалов, производства фанеры и столярно-строительных изделий в условиях российской экономики.
Ориентир − деревянное домостроение
По мнению профессора СПбГЛТА Анатолия Чубинского, нынешнее состояние экспортно-ориентированных производств в России, в том числе производства пиломатериалов, отсутствие производств глубокой переработки древесины, увеличение числа малых и средних предприятий, а также отсутствие внутреннего спроса на производимую продукцию − это то, что мешает отечественному лесному сектору развиваться. Кризис мировой экономики, проявившийся также и в сокращении объемов вводимого жилья, существенно отразился и на объемах производства деревообрабатывающих предприятий отрасли. До начала кризиса за рубеж шло 2/3 объема производимых в стране пиломатериалов; менее 2/3 производимого количества фанеры; 25−30% плит ДВП; 25% мебели или заготовок для деталей мебели из цельной древесины. По материалам Российско-финляндского саммита, который прошел 25 октября 2009 года в Санкт-Петербурге, по отношению к 2008 году объемы производства круглого леса снизились на 15%, пиломатериалов − на 16%, фанеры и древесно-стружечных плит − на 26%, древесно-волокнистых твердых плит − на 33%, мебели − на 26%.
Расширение ассортимента продукции и рост производства древесных материалов для деревянного домостроения − основной путь увеличения внутреннего потребления древесных продуктов в лесной и деревообрабатывающей отраслях и, как следствие, вывода российского лесного сектора экономики из депрессии. Какие же материалы будут иметь спрос? Очевидно, что те, которые и сейчас широко применяются. Для изготовления жилых домов с несущими стенами используют брус как из цельной древесины, так и из клееной сечением 150 х 150, 150 х 180, 150 х 200 мм. Сегодня в строительстве активно используются материалы из древесины лиственницы, ядровая часть которой отличается естественной биостойкостью и физико-механическими свойствами, которые обеспечивают качественные характеристики материалов. По биостойкости клееная древесина при прочих равных условиях превосходит пиломатериалы. При изготовлении ограждающих элементов каркасных и каркасно-панельных домов широкое распространение в мировой практике получили фанера, склеенная клеями повышенной водостойкости, а также плиты ДСП и OSB. Последние теснят на рынке строительных материалов не только классические древесно-стружечные плиты, но и фанеру.
Лесопиление: проблемы и их решения
Основная причина снижения объемов производства пиломатериалов в России − отсутствие развитого внутреннего спроса на них. По мнению Анатолия Чубинского, у отечественного лесопильного производства сегодня весьма тяжелое положение. Согласно статистике, из 16 млн м пиломатериалов, которые в 2009 году отправлялись на экспорт, только 6 млн м были высококачественными. Остальные 10 млн м − низкосортные пиломатериалы, продающиеся по демпинговым ценам, которые чаще ниже средних розничных цен на товар. Кроме того, отечественный производитель не может гарантировать потребителю, что произведенные им пиломатериалы соответствуют качеству пиломатериалов конструкционного назначения.
Малым и средним предприятиям самостоятельно сложно отстаивать свои позиции на мировом рынке и координировать цены на пиломатериалы, что также приводит к демпингу. Попытки создания в стране ассоциаций товаропроизводителей в сфере производства материалов из древесины не увенчались успехом.
Рациональное использование имеющихся лесных ресурсов невозможно без высотехнологичного оборудования. И оборудование, выпускаемое компанией Kara, о котором рассказал генеральный директор фирмы «КАРА МТД» Константин Фролов, именно такое. Продукция Kara позволяет создавать небольшие лесопильные линии малой и средней производительности. Эта техника выгодна предприятиям, которые занимаются не только производством пиломатериалов, но и их переработкой, в частности для мебельных компаний (при производстве мебельного щита). Например, станок Kara PPS 500 предназначен для обработки вершинной части бревен, которые в России используются как балансовая древесина. При помощи оборудования Kara их можно перерабатывать и получать качественную пилопродукцию. На станке можно производить распиловку бревен хвойных и лиственных пород максимальным диаметром 22 см и максимальной длиной 4 м (возможен вариант распиловки бревен длиной 6 м). При этом минимальный диаметр бревна 7 см, а минимальная длина − 1,25 м. Станок предназначен для распиливания как окоренных бревен со сложной кривизной, крупными здоровыми сучками, так и неокоренных, мерзлых. На первом этапе производится распиловка бревна на брус двумя пилами. На втором этапе брус распиливается на доски 2−5 пилами. Станок работает в температурном диапазоне от -20 до +35 °C, то есть специального отопления помещения, в котором он будет установлен, не требуется.
Лесопильная отрасль должна перестраиваться с производства пиломатериалов на выпуск специализированной продукции. Помимо тонкомерной древесины, глубокой переработке подлежат пиломатериалы низкого качества. Получением из них заготовок для клееного бруса занимаются в г. Архангельске. По словам профессора Архангельского государственного технического университета Любови Суровцевой, освоение такой технологии поможет стабилизировать работу лесопильной отрасли в целом и даст лесопильным предприятиям дополнительный источник прибыли. Экономические расчеты показали, что срок окупаемости производства заготовок для клееного бруса − 3,5 года. Эта цифра справедлива при стабильном уровне продаж. При этом внутренняя прибыль составит около 19% в год.
Проблемы сушки древесины
и породы древесины
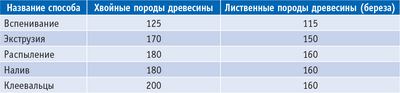
Правильная организация труда на участках сушки играет огромную роль при производстве пиломатериалов требуемого качества. Старший преподаватель СПбГЛТА Алексей Артеменков отметил, что на предприятиях часто сталкиваются с проблемами коробления пиломатериалов, образованием трещин, появлением синевы, перепадами влажности по толщине, неравномерностью влажности отдельных досок как в штабеле, так и в партиях, обрушением сушильных штабелей в камерах в процессе сушки.
Что же делать в таких случаях? Технологу или мастеру сушильного участка в первую очередь следует правильно формировать штабели из сушильных пакетов, обеспечивать загрузку сушильных пакетов в соответствии с нормативами, соблюдать условия сушки и выгрузки пиломатериалов из камеры. И если все вышеназванные операции выполнены, приступать к корректировке режимов сушки.
Зачастую на предприятиях простейшие правила укладки сушильных пакетов, прописанные в ГОСТах, нормативах или учебниках, не выполняются либо игнорируются. В то время как одно из основных требований успешной сушки − правильное формирование штабеля. Он должен быть прямоугольной формы. Если прокладки выступают за его габариты больше чем на 5 мм, то это сказывается на аэродинамике в камерах. При загрузке такого пакета возникает опасность смещения досок в соседних штабелях, что может привести к обрушению целого штабеля как при загрузке в камеру, так и в процессе сушки.
Кроме того, изначально качество пиломатериалов формируется не в сушильном, а в лесопильном цехе. Поэтому необходимо обратить внимание на разнотолщинность пиломатериалов, тщательно контролировать точность их размеров. Не следует применять сдвоенную укладку пиломатериалов.
Большое значение имеет правильная эксплуатация лесосушильного оборудования, в том числе его тщательная подготовка к проведению каждой сушки. Надо следить за работой двигателей и системой автоматики, проверять направление вращения вентиляторов, вовремя смазывать подшипники, чистить калориферы. Кроме того, следует помнить о соблюдении правил хранения сырых пиломатериалов до сушки.
Старший преподаватель ЛТА Вадим Харитонов в своем докладе подчеркнул, что в современных условиях работы лесосушильных цехов результат каждого процесса сушки пилопродукции зависит от скрупулезного соблюдения многих условий, которые считают «мелочами» как руководители предприятий, так и операторы сушильных установок. Но если на предприятиях ликвидировать большую часть таких «мелочей», результат незамедлительно скажется на качестве сушки пилопродукции.
Новый взгляд на фанерное производство
В настоящее время для изготовления фанеры повышенной водостойкости используются фенолоформальдегидные смолы. Их производство является экологически опасным. Содержание вредных веществ в газовых выбросах, в частности фенола, во много раз превышает ПДК (предельно допустимые концентрации). По этим причинам на ряде деревообрабатывающих предприятий прекращен выпуск фенолоформальдегидных смол. Еще одним токсичным продуктом, выделяющимся из фанеры, изготовленной с применением клеев на основе фенолоформальдегидных смол, является формальдегид.
Сейчас странами Евросоюза разрабатывается стандарт, ограничивающий содержание формальдегида до 4 мг на 100 г абсолютно сухой массы фанеры. Последнее обстоятельство ограничивает экспорт российской фанеры на Запад.
В производстве фанеры основным направлением энергосбережения является интенсификация склеивания. Сотрудниками ООО «ЦНИИФ» и ЛТА был разработан состав быстроотверждающегося клея на основе фенолоформальдегидной смолы, модифицированной карбамидомеламиноформальдегидной смолой. При сокращении периода склеивания в среднем на 30% показатели прочности и токсичности соответствуют как отечественным, так и зарубежным стандартам.
Также был разработан рецепт клея на основе карбамидомеламиноформальдегидной смолы, в состав которого вошел активный наполнитель − аэросил технический. Показатели прочности и токсичности склеиваемой им фанеры соответствуют всем современным стандартам. При этом время склеивания в сравнении с существующим режимом уменьшается на 37%. Причем содержание формальдегида по перфораторному методу (ГОСТ 27678) составило 1,8 мг на 100 г абсолютно сухой массы фанеры при норме до 8 мг на 100 г. Поэтому совершенствование процессов склеивания и получение нетоксичных и прочных материалов при использовании энергосберегающих технологий весьма актуально, как подчеркнула в своем выступлении аспирант ЛТА Екатерина Соколова. Это позволяет отечественным производителям уверенно конкурировать на рынке с производителей из других стран.
При производстве фанеры важен не только состав используемого клея, но его расход, а значит, и способ его нанесения. Как считает глава представительства компании Raute Corporation в России Александр Кирпичников, выбор оптимального способа нанесения клея − один из факторов успеха современного производства. По его словам, лидеры фанерного производства в России уже вышли на объемы выпуска продукции докризисного периода, сократив при этом на 15−20% численность персонала по сравнению с 2007 годом. Следовательно, эффективность труда персонала становится сейчас очень актуальной: теперь на предприятиях стараются уменьшить количество операций, требующих ручного труда, и механизировать или автоматизировать производство. Автоматические и полуавтоматические способы клеенанесения Raute, учитывающие породу древесины, толщину шпона и вид клея, позволяют проектировать линии для различных уровней производства. Экономия клея и затрат на обслуживающий персонал − такая задача возложена на современные линии. Помимо традиционного использования клеевальцев, клей можно наносить «бесконтактными» односторонними методами, такими как экструзия, вспенивание, распыление и налив.
Экструдеры могут гибко работать с любыми клеями, породами древесины, толщинами и типоразмерами шпона. Такие системы позволяют менять дозировку клея между слоями, использовать специальные схемы наборки и применять наиболее быстроотверждающийся клей для «серединок». Экструдер позволяет по сравнению с другими способами снизить потребление клея на 5−10% за счет более аккуратного клеенанесения.
«Близким родственником» метода экструзии является вспенивание, которое позволяет еще больше снизить расход клея и затраты на персонал.
Распыление или налив в основном применяются при производстве фанеры из шпона хвойных пород и LVL.
Для традиционного способа с применением клеевальцев Raute предлагает свои новые разработки − систему «паук» автоматической подачи шпона, которая может использоваться на действующих линиях с увеличением производительности в 3 раза по сравнению с существующей. При этом достаточно двух операторов на линии вместо четырех.
Показатели расхода клея для каждого способа приведены в таблице.
Развитие отечественного станкостроения
Сегодня на рынке возникла потребность в производстве пиломатериалов специального назначения, которые должны соответствовать требованиям, указанным не в ГОСТе, а в спецификации заказчика. Компания ООО «Рифт-механика» (Санкт-Петербург) занимается разработкой лесопильного бревнопильного оборудования, в том числе для получения радиальных пиломатериалов − станков серии «Рифт». Принцип действия этих станков довольно прост: две угловые пилы при неподвижно закрепленном гидравлическими зажимами бревне перемещаются вперед-назад, оператор осуществляет позиционирование пильного узла вверх-вниз, вправо-влево. Это позволяет получить пиломатериал любого сечения с произвольным расположением досок в бревне. По мнению директора компании «Рифт-механика» Михаила Беспалова, многие виды оборудования, которое выпускают сегодня, достаточно работоспособны, но из-за отсутствия механизации работа на них малоэффективна.
Пример. При распиловке бревен из лиственницы диаметром 36 см и больше для их транспортировки к станку требуется вспомогательное оборудование (тельфер, кран-балка, погрузчик). Поэтому был разработан станок с гидравлическими зажимами и выравнивателями бревна по высоте, кантователями бревна и транспортером для удаления отходов при пилении. Применение электронной системы позволяет теперь оператору с высокой точностью определять размеры продукции. Специально для этого предназначен датчик перемещения (энкодер). Принцип его работы следующий: количество импульсов пропорционально перемещению; электроника подсчитывает требуемое количество импульсов в соответствии с заданным размером и управляет приводом. Оператор только задает размер продукции. Остальное выполняет и проверяет электроника. Станок «Рифт-03» оборудован загрузчиком бревен с пола, но по желанию заказчика можно комплектовать его загрузчиком бревен с эстакады. У него усовершенствованная электроника, а пилы приводятся в движение мотор-шпинделями, что повышает жесткость установки пил и режимы нагрузки, которые можно на них передавать. Для перемещения пильного узла используются линейные шариковые направляющие и шарико-винтовые пары.
Такие станки чаще всего приобретают представители малого бизнеса, которые в отличие от крупных предприятий не испытывают проблем с сырьем и сбытом продукции. Малое предприятие, выпуская более дорогую продукцию специального назначения, но в меньших объемах, имеет ту же прибыль, которую получает крупное предприятие при изготовлении большего объема пиломатериалов общего назначения.
Использование 3D-технологий при проектировании оборудования позволяет видеть расположение каждого узла станка, а также получить объемно-планировочное решение предприятия. Это помогает избежать досадных накладок при размещении оборудования.
Случается, что на действующих предприятиях при покупке единиц оборудования забывают об обеспечении их взаимосвязи. Это приводит к простоям или неполной загрузке техники. Решение проблемы − приобретение вспомогательного оборудования (например, цепных, ленточных, скребковых транспортеров).
Генеральный директор Александр Васильев ООО «Боровичский завод деревообрабатывающих станков» (г. Боровичи) рассказал о деревообрабатывающем и околостаночном оборудовании, инструментах и запасные частях отечественного производства. В настоящее время завод выпускает серию станков: С 25-4АМ, С25-5А.08, С25-5А.09, С25-5А.PRO и С25-6АБ. Станки предназначены для изготовления высококачественных погонажных изделий и в зависимости от модели оснащены четырьмя, пятью или шестью шпинделями, расположенными по классической схеме. На этих станках выполняется обработка заготовок с четырех сторон за один проход.
Основа выпускаемого оборудования − мощная литая чугунная станина. Она обеспечивает максимальную виброустойчивость и стабильность всех узлов станка. Верхние подающие ролики с рифлением обрабатывают заготовки любой влажности. Секционные прижимы полностью устраняют вырывы из заготовки на входе и выходе из зоны резания и оснащены направляющим элементом, обеспечивающим точное базирование и простоту настройки.
На пятишпиндельных станках устанавливается калевочный суппорт, который работает как в верхнем, так и в нижнем положении. На нем можно установить пилы для продольного деления материала. Профилирование на станках выполняется фрезами, установленными на всех шпинделях, кроме нижнего. Станки оснащены звукоизолирующими ограждениями, предохранительными устройствами и блокировками, обеспечивающими безопасную работу.
Для высококачественной продольной распиловки бревен из любых пород предназначена мини-пилорама МПЦ-1. Она может быть использована для изготовления шпона, лафета, необрезной и обрезной доски, тонкомера, бруса разного сечения. Получить обрезной пиломатериал из необрезной доски и горбыля можно на двухпильном кромкообрезном станке СДК-1.
В ходе конференции были рассмотрены вопросы применения средств защиты древесины (Петр Порфирьев, компания ООО «Сенеж-препараты»), эффективности выработки тепловой и электрической энергии при сжигании древесных гранул и прессованных брикетов, выпускаемых из отходов лесопиления (доцент Борис Локштанов, СПбГЛТА). Разные виды лесозаготовительного оборудования, в частности харвестеров Ergo 8W для работы в тяжелых условиях, представил специалист компании Ponsse Евгений Кашин. О возможности государственного стимулирования деятельности деревообрабатывающих предприятий в области глубокой переработки древесины на примере Красноярского края рассказала Евгения Сырова; о проектировании аспирационных установок посредством моделирования и расчета в САПР доложил доцент Сергей Трофимов (Белорусский государственный технологический университет, г. Минск).
Екатерина МАТЮШЕНКОВА
Справка
Развитие лесотехнического образования в нашей стране было тесно связано с подъемом народного хозяйства. В 1920-е годы. в 1925 году постановлением правительства в Ленинград был переведен Московский лесной институт, в составе которого был лесотехнологический факультет. Последний вместе с лесотехнологическим отделением лесного института в Ленинграде образовал лесотехнологический факультет. Этот период и считается началом образования современного факультета механической технологии древесины (МТД) (В. И. Санев. Факультет механической технологии древесины//Известия Санкт-Петербургской лесотехнической академии: Сб. тр./СПб., 1993. С. 100–110). В этом году факультет МТД СПбГЛТА им. С. М. Кирова отметит 85-летие со дня своего основания. Возникновение и развитие факультета МТД и кафедр тесно связано с деятельностью ученых и специалистов, которые организовывали учебный процесс, разрабатывали учебные планы, определяли оптимальный набор дисциплин, создавали лаборатории, обосновывали перспективные направления научной работы, создавали научные школы, обеспечивали подготовку научно-педагогических кадров для академии и лесотехнических вузов страны, готовили инженерные кадры для деревообрабатывающей промышленности. Широкую известность факультету, как в нашей стране, так и за рубежом, создали работавшие здесь многие годы профессоры Д. Ф. шапиро, М. А. Дешевой, Е. Г. Кротов, Г. П. Быстров, В. Н. Михайлов, А. Н. Песоцкий, М. С. Мовнин, А. Э. Грубе, С. Н. Святков, В. Я. Филькевич и многие другие.