«UPM Пестово»: в приоритете − качество
Логотип компании UPM хорошо известен ее клиентам. Товарный знак «грифон» (крылатое существо, наполовину лев, наполовину орел) − старейший корпоративный логотип, используемый в Финляндии, − появился еще в конце XIX века. Он был разработан в первую очередь для работы в России, где был официально зарегистрирован в 1902 году и являлся обязательным элементом маркировки на упаковках писчей бумаги и других продуктах.
Вторая бизнес-группа − «Бумага», на нее приходится 70% объема производства всей компании. Сюда входят предприятия, изготавливающие различные виды бумажной продукции.
Третья группа − «Спецматериалы». К ней относятся производства этикеточных материалов, RFID-меток (к примеру, до недавнего времени все многоразовые проездные билеты Московского метрополитена изготавливались из меток UPM). Сюда же входят производства фанеры, древесно-пластиковых композитов и прочих материалов.
В России производственные мощности UPM представлены пока только на Северо-Западе. Это фанерный завод в г. Чудово (Новгородская обл.), ежегодно производящий около 100 тыс. м3 березовой фанеры и 6 тыс. м3 шпона, а также открытый в 2004 году лесопильный завод в г. Пестово, которому посвящен этот материал.
В структуре компании всего семь лесопильных заводов. Пять из них находятся в Финляндии, по одному заводу в Австрии и России. Завод в Пестово построен UPM в партнерстве с российским ОАО «Новгородские лесопромышленники», с которым концерн сотрудничает уже более 20 лет. Первым их совместным проектом было предприятие «Чудово-РВС».
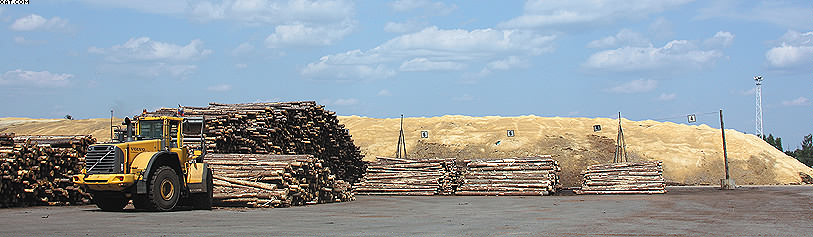
Склад сортированных лесоматериалов и зимний склад (на заднем плане)
Продукция «UPM Пестово»
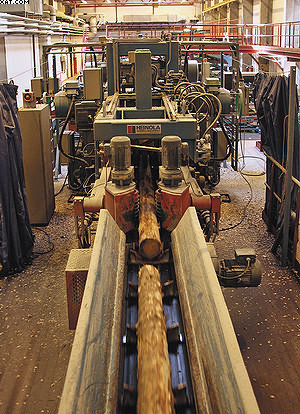
Подача бревен на распиловку
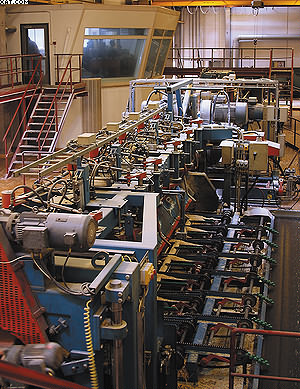
Операторская лесопильного цеха, фрезерный и
круглопильный агрегаты лесопильной линии
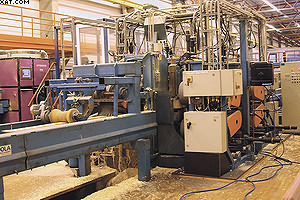
Профилирующий станок лесопильной линии
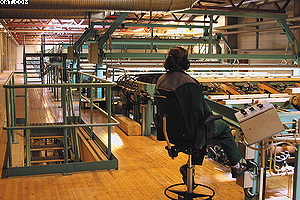
Линия «сырой» сортировки
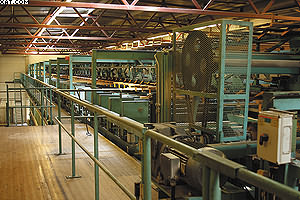
Сортировочный транспортер
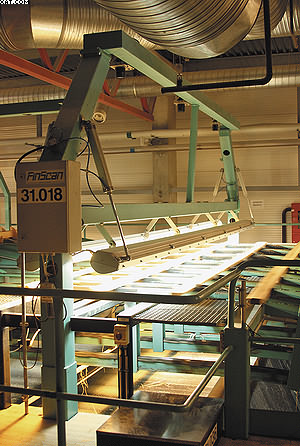
Камеры визуальной сортировки
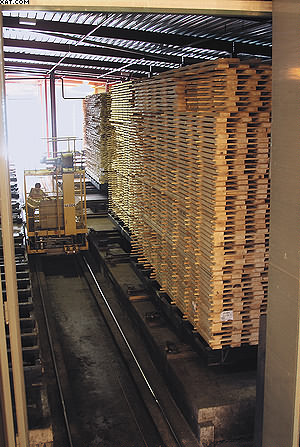
Транспортная тележка и пакеты на «сыром дворе»
сушильного участка
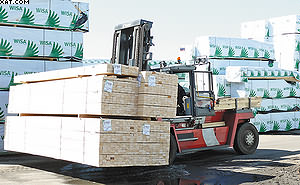
Отгрузка готовой продукции
Продукция завода в Пестово − пиломатериалы, выпускаемые под маркой UPM (в основном UPM wood, UPM strong и UPM pro), используются в строительстве, в том числе в каркасном домостроении, при производстве стропильных конструкций, клееного бруса, а также двутавровой балки для опалубочных систем.
Пиломатериалы UPM wood − традиционные экспортные пиломатериалы северной сортировки по NORDIC TIMBER/ГОСТ 26002-83.
UPM strong − это сортированные по прочности пиломатериалы. Сортировка осуществляется в потоке, в автоматическом режиме в соответствии с европейскими нормами EN338. Прочность доски определяется по скорости прохождения в ней звуковых волн. По результатам замеров доску относят к одному из трех классов прочности − С18, С24 или С30. Причем если в соответствии с требованиями для класса С18 происходит небольшой отсев досок, то для класса С30 требования строже, и поэтому отбраковывается весьма значительная часть материала. Учитывается множество факторов: и сучки, и трещины, и плотность древесины. Как правило, у доски высокого класса прочности сучков немного, но главное − она соответствует определенным прочностным свойствам. После определения класса прочности каждая доска маркируется. Пиломатериалы этой группы производятся строгаными, с четырехсторонним скруглением.
UPM pro − это строганые и профилированные материалы северной сортировки по NORDIC TIMBER/ГОСТ 8242-88. Строганая продукция используется для внутренней и внешней отделки в домостроении.
Кроме пиломатериалов, на заводе в Пестово производятся технологическая щепа и опилки, которые поставляются в Финляндию, на целлюлозные заводы UPM, а часть опилок потребляется местным рынком. Продажа пиломатериалов клиентам осуществляется через глобальную сеть подразделений UPM, занимающихся продажами и логистикой. Основной рынок сбыта пиломатериалов − европейские страны, куда уходит более половины продукции. В первую очередь это Финляндия, причем большая часть материалов поступает в сегмент домостроения. Кроме стран Европы, продукция поставляется также в Японию и Китай. В России сбыт пиломатериалов организуется через сетевой канал (ретейлеры, например 13 магазинов OBI от Омска до Краснодара) или B2B (business to business), то есть с завода в Пестово продукция поступает на обрабатывающий завод или сразу на строительную площадку.
«По объемам мы, конечно, не можем сравниться с нашими коллегами в Финляндии или Японии, − рассказывает Дмитрий Гаврилов, менеджер российского отделения компании по продажам продукции деревообработки. − Сбыт в России − это скромные 5% от общего объема продаж продукции, но и за этой цифрой стоит огромная работа. Ведь с нашей продукцией не во все сегменты рынка можно прийти. На открытый рынок выходить бесполезно, вокруг Пестово функционируют 63 пилорамы, многие работают без НДС, а с такими производителями трудно конкурировать по цене. К тому же не все покупатели готовы платить за высокое качество. Поэтому основными нашими клиентами являются индустриальные компании и сети, которые заинтересованы в бесперебойных поставках продукции с гарантированным качеством». В России пока нет структурированного рынка пиломатериалов, такого как, например, в Финляндии, где хорошо развита промышленная дистрибуция и где компании-производители имеют индустриальные и розничные отделы со своими торговыми площадями, на которых они продают пиломатериалы разных сечений, влажности и качества. Такие компании, как правило, снабжают домостроителей и других потребителей в ближайшей округе.
Производство в Пестово работает по согласованному с центральным отделением компании плану продаж, который формируется на полугодие и на каждый квартал. В UPM единая сеть продаж: со всеми заказами по всему миру работают одни и те же люди, а продукция может быть поставлена с любого завода, то есть заказчик, например, из Японии может получить материал как из Финляндии, так и из российского Пестово. А это значит, что уровень качества на всех предприятиях компании одинаковый, что само по себе говорит о системном подходе.
Проектирование и строительство на «UPM Пестово»
Технологическим проектированием завода в Пестово занималась финская инжиниринговая компания АО «Планекар», при этом использовались современные технологические решения и опыт работы других лесопильных заводов, в том числе UPM. Достоинство завода в Пестово в том, что на этом новом предприятии (в отличие от аналогичных финских заводов, многим из которых более 100 лет) была возможность использовать современные технологии и разместить оборудование наилучшим образом. В процессе предпроектных проработок инжиниринговой компанией было исследовано несколько площадок и выбор был сделан в пользу Пестово. Ранее здесь был лесокомбинат, выпускавший пиломатериалы и щитовые дома, существовала инфраструктура − железнодорожные пути, подъезды, водоснабжение и другие коммуникации. Здания и инженерные сети, находившиеся на площадке, не соответствовали требованиям нового производства и были демонтированы. «Запомнился масштаб строительства, его объемы и скорость выполнения работ, − рассказывает Виталий Васильев, управляющий по инвестиционной и эксплуатационной деятельности завода. − В сентябре 2002 года компания только зарегистрировалась, с 1 ноября того же года начали демонтаж старых зданий и подготовку площадки на территории 24 га. В июне 2003 года заложили первый фундамент, а в декабре уже запускали лесопильную линию». Проектирование и строительство велись параллельно, одновременно со строительством начался и монтаж оборудования. Такое решение было принято инвестором для сокращения сроков ввода завода в эксплуатацию. В европейских странах такая практика обычна. По бизнес-плану предполагалось, что строительство завода обойдется в 32 млн евро и срок окупаемости составит 5–8 лет, а фактически на запуск производства было истрачено более 50 млн евро.
Комплекс работ по строительству лесопильного завода в Пестово был выполнен генеральным подрядчиком АО «ЮИТ Ракеннус». Инвестор выбирал иностранную строительную компанию, работающую в России и имеющую соответствующие лицензии и опыт работы. Адаптация проектной документации к российским нормам, включая получение разрешений на проектирование, строительство и согласование документации, была выполнена подрядной организацией ЗАО «Лентек» совместно с субподрядной организацией ОАО «Институт Новгородгражданпроект».
Динамика производства и расширение ассортимента продукции показывают, что проектные и строительные решения были приняты верно. Конечно, параллельные проектирование и строительство, быстрый монтаж приводили к некоторым трудностям: пришлось вносить коррективы в проект, но рост производства говорит сам за себя. Сегодня предприятие продолжает развиваться, менеджмент компании принимает меры для оптимизации производственных процессов и повышения эффективности работы предприятия в целом.
Производство на «UPM Пестово»
Годовая производственная мощность завода составляет 260 тыс. м3 обрезных пиломатериалов, а производственная мощность строгального цеха, который начал работу в 2006 году, − 40 тыс. м3 строганых материалов. Завод относительно молодой − официальный запуск состоялся в мае 2004 года, а к началу 2010-го на нем был произведен первый миллион кубометров пиломатериалов.
Общая территория предприятия с учетом участков перспективного развития − 33 га: на 16 га разместились производственные здания, остальная часть занята складами лесоматериалов и подъездными путями. На площадке четыре железнодорожных тупика, два из которых предназначены для доставки сырья, а два − для отгрузки готовой продукции. Здесь все очень компактно, процессы логично выстроены один за другим. Все производство сосредоточено в одном здании. Фактически под одной крышей размещены и распиловка, и сортировка, и сушилки. Все оборудование на предприятии финское, и это понятно: в Финляндии есть хорошие производители машин для обработки древесины, и у UPM с ними давние партнерские связи. Основные поставщики оборудования в Пестово − Heinolan Sahakoneet Oy, Nordautomation Oy, Järme Wood Oy (ныне Jartek), Valutec Oy, OT-Laite Oy.
Завод в Пестово изначально проектировался для работы только с еловой древесиной, но по экономическим соображениям и с учетом того, что ель не всегда можно купить в достаточном количестве, сейчас здесь перерабатывают и сосновую древесину (около 30–40% от общего объема древесного сырья). Интересно, что в Финляндии не принято объединять сосну и ель в одну группу хвойных пород, как это делается в России. Это продукты для разного рынка и для разного использования.
Сейчас большая часть (60%) сырья подается на площадку автомобильным транспортом, 40% − железнодорожным, впрочем, это соотношение год от года меняется. Предприятие принимает пиловочник диаметром от 13 до 38 см и длиной от 4 до 6 м, который сразу после разгрузки подается на линию сортировки лесоматериалов. Двусторонняя сортировочная линия с 44 «карманами» работает с неокоренным лесом. Сортировка сырья осуществляется по диаметру, длине и качеству. Принимают лес, сортируют и ведут учет всего три человека. Отсортированные лесоматериалы укладываются в штабеля на складе, объем которого при необходимости может достигать 40 тыс. м3, что позволяет снабжать предприятие сырьем в течение 1,5–2 месяцев. Для обеспечения сохранности лесоматериалов на складе установлена система дождевания с переносными опорами.
Все разгрузочные и транспортные операции на площадке осуществляются четырьмя погрузчиками Volvo L150E и L180E. На территории завода работает подрядчик, финская компания, которая обеспечивает все транспортные перемещения леса, то есть Пестовский завод владеет только одним маленьким вилочным погрузчиком, занятым на вспомогательных ремонтных работах. Такой необычный для России подход − заниматься только основным производством, а вспомогательные операции покупать как услугу − принят на всех предприятиях компании. Здесь считают, что нужно концентрироваться на пилении хорошей доски, а не заниматься ремонтом погрузчиков. Судя по всему, экономические основания для этого тоже есть.
На заводе в Пестово применяется еще один интересный способ хранения древесного сырья, который у нас в России, кажется, начинают забывать, − это замораживание. Поступившее в холодное время года сырье в неокоренном виде укладывается на снеговую подушку, пересыпается снегом, а сверху укрывается слоем теплоизоляции (коры и опилок или щепы). Лес сохраняется в таком «холодильнике» в замороженном виде до осени, когда начинается его дефицит. В Пестово замораживают лес уже не первый год, для этих целей куплена даже «снеговая пушка». Такой способ хранения древесины хорошо себя зарекомендовал, замороженной древесине не страшны ни грибок, ни короед. Объем складирования меняется от года к году, но обычно составляет около 100 тыс. м3, которых хватит на два месяца работы. В Скандинавских странах сезонные проблемы с обеспечением сырьем выражены не так сильно, как в России, но и там тоже используется такая практика. В Финляндии, например, замораживают в основном балансы. Конечно, хранение древесного сырья в замороженном виде гарантирует большую защиту, чем дождевание, однако есть у этого способа и недостатки. Он требует большого расхода вспомогательных материалов и отличается высокой трудоемкостью. Кроме того, после разборки склада опилки нужно утилизировать. Еще один недостаток − это в прямом смысле замороженные деньги, ведь замороженный лес оплачен, но не используется. Эти деньги можно вернуть, только когда лес будет распилен. Тем не менее предприятие в Пестово содержит этот склад, потому что работает в первую очередь с иностранными потребителями, которые ценят стабильность и должны быть уверены, что доска будет поставлена в любой сезон.
Окорка лесоматериалов на предприятии происходит непосредственно перед подачей на лесопиление, окорочный станок Valon Kone 820 установлен в одной линии с фрезерно-брусующим агрегатом. Такой вариант размещения оборудования, конечно, снижает межоперационный запас, однако практика показывает, что простоев из-за окорочного станка почти не бывает. Зато древесина на распиловку подается чистой (без песка и грязи), чего сложно добиться, если станок для окорки включен в линию сортировки леса. К тому же неокоренный лес после сортировки легче транспортировать и складировать.
Лесопильная линия, поставленная на завод в Пестово фирмой Heinola, работает в таком же режиме, как и все остальное производство, − двухсменный график шесть дней в неделю по 10 часов. Перерывы между сменами − один час, два получасовых перерыва на обед. Обслуживающий персонал работает в три смены, а замена инструмента осуществляется в перерывах между сменами. «Средний диаметр пиловочника − 23 см, − рассказывает начальник производства Дмитрий Гупаленко. − Объем бревна при этом − около 0,23 м3. Из такого бревна (22–24 см) выход пиломатериалов обычно самый лучший. И задача службы закупки лесоматериалов привозить именно такой лес. Размеры вырабатываемых пиломатериалов по толщине − от 22 (19 мм для сосны) до 75 мм, по ширине − от 100 до 225 мм, но по заказу возможны и другие, нестандартные размеры».
Для уменьшения нагрузки на фрезы при входе на линию распиловки бревна подаются вершиной вперед. Перед подачей на линию распиловки бревно автоматически базируется кривизной вверх. Первый станок линии − фрезерно-брусующий. В паре с ним круглопильный восьмипильный станок, который отделяет одну-две доски с каждой стороны бруса. Отделенные доски поступают на линию обрезки, где необрезные части специальной фрезой перерабатываются в щепу. После первой группы станков находится еще одна линия обрезки, которая запускается при увеличении скорости работы основной линии. Кстати скорость пиления устанавливается автоматически: в зависимости от диаметра бревна − от 40 до 110 м/мин. После отделения боковых досок полубрус переворачивается на пласть и направляется на второй брусующий станок, где отделяются боковые доски и формируется четырехкантный брус. Далее брус базируется в автоматическом режиме и направляется в профилирующий станок, где формируется профиль боковых досок (максимально по две доски с каждой стороны). Сердцевинная часть раскраивается на доски на последнем делительном агрегате. Максимальное количество сердцевинных досок, которое можно выпилить, − семь, но в обычном поставе их от двух до шести штук. Под линией распиловки установлены раздельные транспортеры для выноса опилок и щепы. Собранные щепа и опилки поступают на вибросита и далее на склад. Объемный выход материалов зависит от размера и количества выпиливаемых досок, от характеристик пиловочника и, как правило, не превышает 50%; при этом в щепу перерабатывается чуть более 30% каждого куба древесины, а остальная часть уходит в опилки.
К лесопильному цеху примыкает здание участка сортировки, где установлена линия «сырой» сортировки Jarme. Боковые и центральные доски поступают на сортировку по разным транспортерам − это связано с тем, что доски разной толщины и их лучше сразу разделить, чтобы они не мешали друг другу при сортировке. Сортировка досок осуществляется в автоматическом режиме. Размер и качество досок определяются двумя группами камер FinScan − по три камеры для нижней и верхней пласти. Специальный транспортер переворачивает доски, чтобы камеры могли видеть вторую пласть. Качество определяется по нескольким параметрам (сучки, обзол, гниль), а скорость сортировки может достигать 120 шт. в минуту. Эти же камеры подают команду триммеру, который отторцовывает обзольную часть доски. Далее сортировочный транспортер верхнего расположения быстро перемещает доски в сортировочные «карманы», разгрузка которых осуществляется на нижний транспортер и далее в штабелеформирующую машину. Операторы на линии «сырой» сортировки присутствуют лишь для контроля работы аппаратуры и могут своевременно исправить ошибки в случае их возникновения.
Сформированные штабели траверсными тележками доставляются на «сырой двор» сушильного участка. Двухзонные туннели WSValutec интегрированы в здание, то есть вся технологическая цепочка производства пиломатериалов выстроена таким образом, что после подачи бревен в цех все перемещение досок механизировано и погрузчики не используются до перевозки уже готовых пакетов. Сушка основного объема продукции осуществляется до транспортной влажности (18%), однако возможна и специальная сушка до 12–16%. Всего установлено семь сушильных туннелей, три из которых используются для быстрой (до 48 ч) сушки боковой (тонкой) доски. Остальные четыре туннеля используются для сушки центральных досок, которые, в отличие от боковых, толще, в них, как правило, больше влаги, они плотнее и поэтому требуют более длительного режима сушки.
Максимальная разовая загрузка камер − 2800 м3, а производительность сушильного комплекса − до 950 м3 в сутки. Основная продукция предприятия − это конструкционные строительные пиломатериалы влажностью 18–20%. Процент выхода тонких досок высокий, а производительность лесопильной линии очень высокая, поэтому, чтобы не сдерживать производство, применяются сушильные камеры туннельного типа.
Тепловая энергия для сушильных туннелей, отопления и ГВС вырабатывается в котельной MW Power (Финляндия) мощностью 10 МВт, обслуживание которой осуществляется концерном MW Power. Котельная работает на измельченной коре, которая поступает по транспортеру, проходя через металлоискатель, дробилку и промежуточный склад от окорочного станка. Кроме биокотельной, на предприятии установлена вспомогательная котельная, мощностью 2 МВт, работающая на дизельном топливе. Эта котельная используется крайне редко (раз в два года) − в том случае, если основная котельная останавливается на ремонт или на обслуживание. Кстати, предприятие ежегодно останавливает производство на 3–4 недели для проведения плановых ремонтных и профилактических работ. Обслуживанием оборудования в это время занимаются финские компании-подрядчики и персонал предприятия.
Сушильные пакеты пиломатериалов из сушильных туннелей транспортируются на линию «сухой» сортировки, которая, как и линия «сырой» сортировки, поставлена на пестовское предприятие фирмой Jarme. Эта линия также укомплектована вертикальными «карманами». Сорт доски здесь определяется оператором (сортировщиком). Именно на этой линии установлена система Dynagrade (Швеция–Финляндия), позволяющая проводить сортировку пиломатериалов по классам прочности С16-С30. Принцип действия установки основан на измерении резонансной частоты и длины доски. После сортировки пиломатериалы маркируются, укладываются в плотные пакеты и поступают на участок упаковки. Персонал, который работает на сортировке, проходит ежегодную переподготовку и сдает экзамен в международной аудиторской компании Inspecta Sertifiointi Oy.
Сегодня на заводе работает чуть больше 200 человек, и только четверо из них финны − они работают на тех позициях, где требуется знание финского языка. Остальные работники завода − жители Пестово и ближайших поселков. Исторически сложилось так, что в Пестово всегда работали лесопильные предприятия, и население с раннего возраста ориентируется на работу в лесных компаниях. Многие местные жители получают высшее образование в крупных городах и возвращаются обратно, тем более что для этого есть мотивация, ведь средняя заработная плата на заводе − 22,8 тыс. руб. в месяц. В компании UPM уделяют особое внимание вопросам обучения, безопасности и ответственности. Так, перед запуском завода инженерный персонал и операторы станков были направлены в Финляндию для обучения на заводах компании UPM, и такое обучение проводится регулярно, по мере надобности. Причем обучается не только производственный, но и офисный персонал. Средний возраст работников − 34 года, и треть из них с высшим образованием.
Безопасность производства и охрана окружающей среды «UPM Пестово»
На предприятии проведена аттестация рабочих мест, сделаны замеры электромагнитных излучений, вибрации, освещения и определена степень вредности работы на каждом участке. В целом по предприятию превышения нормативных показателей по вредности не установлено, а работникам, которые трудятся в тех местах, где нельзя создать комфортные условия (например, снизить шум), выплачивается компенсация за вредность. «Весь персонал, работающий на предприятии, обеспечен средствами индивидуальной защиты − спецодеждой, спецобувью, шумозащитными наушниками, световозвращающими жилетами, перчатками. Носить их мы обязываем работников и жестко контролируем исполнение, потому что от этого зависит здоровье и жизнь людей, − говорит Татьяна Иванова, инженер по охране труда и окружающей среды завода в Пестово. − Компания UPM понимает важность обеспечения нормальных условий труда и охраны труда, и наше предприятие никогда не испытывает трудностей с получением дополнительного финансирования на эти цели. И это касается не только средств индивидуальной защиты, но и комнат отдыха, душевых. У нас великолепные бытовые условия, есть своя столовая, которую обслуживает предприятие-подрядчик. Есть медицинский пункт, где тоже работает подрядчик − фельдшер центральной районной больницы».
Большое внимание обеспечению безопасности труда на предприятии уделяется также и в связи с сертификацией производства. В мае завод получил обновленные сертификаты ISO 14001:2004 по экологическому менеджменту и ISO 9001:2008 по менеджменту качества. Предприятие имеет также сертификат на цепочку поставок древесины по системе FSC. В России эти сертификаты пока не очень востребованы, но для зарубежных покупателей, особенно европейцев, они имеют большое значение. Сертификат помогает покупателю оценить продукцию, понять, по каким стандартам работает предприятие, как планируется его работа и как осуществляется управление компанией. Сертификация, как правило, оказывается полезной и для предприятий, сам процесс подготовки к процедуре сертифицирования помогает упорядочить производственные процессы и создает хорошую базу для развития, так как в стандартах четко обозначена модель, по которой компания должна развиваться.
Остальные заводы UPM уже давно прошли необходимую сертификацию, и завод в Пестово тоже стремился к этому. Подготовкой к ней здесь занимались с момента запуска, шаг за шагом. Это был долгий и успешный процесс. Для сертификации по экологическому менеджменту, например, как это и принято, работали по трем направлениям: охрана воздуха, охрана водных объектов и почвы. Самое сложное было − добиться качественной очистки дождевых стоков. «Мы долго искали решение, − рассказывает Татьяна Иванова. − В начале работы завода дождевые стоки с площадки нашего предприятия очищались на механических очистных сооружениях и мы не могли достигнуть требуемого санитарными нормами качества очистки. А в России довольно жесткие экологические нормы, жестче, чем в Финляндии. В стоках было высокое содержание фенолов, образующихся при хранении древесины. Требовалась установка биологических очистных сооружений, но беда была в том, что и они не стали бы работать при том соотношении элементов, которое было установлено в пробах дождевых сточных вод. Тогда после некоторых исследований мы заключили договор с городской службой “Водоканала”, которая теперь принимает дождевые стоки на очистку. Интересно, что через некоторое время после этого очистка воды на городских очистных сооружениях даже улучшилась».
Процесс сертификации по стандартам ISO и FSC предусматривает регулярную аудиторскую проверку, в ходе которой каждый раз предприятие должно подтверждать, что оно работает по правилам, указанным в этих стандартах. Это обстоятельство требует постоянного внимания собственника к производству, позволяет поддерживать его высокий уровень и помогает компании развиваться. Соответствие стандартам требует системного подхода к управлению заводом, что, в свою очередь, обеспечивает стабильность работы, в том числе и в отношении качества. Интересно, что в службе контроля качества на таком крупном предприятии работает всего три человека (руководитель службы и два контролера), притом что проверка осуществляется пооперационно, от бревна до упаковки. Служба качества здесь выполняет скорее статистические функции, позволяет среагировать на какие-то систематические ошибки, отработать новые технологии или разобраться в причинах отклонений. Но за качество отвечают все, каждый оператор и каждый мастер на своем рабочем месте. Принцип «Качество − это дело каждого» зафиксирован и в стандарте ISO. Такой подход к организации работы на пестовском предприятии позволяет руководству компании UPM быть уверенным в том, что качество пиломатериалов, изготавливаемых на этом заводе, находится на том же уровне, что и на других предприятиях UPM. Это означает, что для продажи клиентам можно использовать материал с любого завода корпорации без опасения рекламаций.
Виталий ТИКАЧЕВ