ЗДИ: дверь в третье десятилетие
Можно сказать, что это предприятие - ровесник перестройки. В марте 2011 года один из крупнейших производителей деревянных и металлических дверей в Москве и России - ЗАО «Завод деревоизделий» (ЗДИ) - отметил двадцатилетие.
Начав свою деятельность в 1991 году на базе производственных мощностей деревообрабатывающего цеха, входившего в состав известного российского производителя грузовых автомобилей «АМО ЗИЛ», предприятие пережило разные времена - были и достижения, были и вынужденные спады производства, но сегодня ЗДИ смотрит в будущее с надеждой на лучшее.
В поисках своего пути
Компания рождалась в трудное время. Плановой экономики и народного хозяйства некогда могущественного СССР больше не существовало. Бывший автогигант ЗИЛ, по сути, развалился, объемы производства резко пошли вниз, перед коллективами производственных подразделений, входивших в состав объединения, встала нелегкая задача - найти путь выживания. Это означало определиться с тем, какой востребованный потребителями товар производить, и понять, как найти свою нишу на зарождавшемся внутреннем рынке и закрепиться в ней. Стояла такая задача и перед молодым деревообрабатывающим предприятием, которое было создано на основе бывшего склада пиломатериалов ЗИЛа. Его возглавил опытный производственник и менеджер Юрий Черкасов (ныне генеральный директор ЗДИ), несколько лет проработавший в должности главного инженера автомобилестроительного объединения.
«Производственная площадка, где расположены мощности нашего завода, до начала 90-х годов прошлого века была занята складом пиломатериалов, которые использовались для изготовления кузовов грузовых автомобилей марки "ЗИЛ", и цехом, в котором эти пиломатериалы обрабатывались перед отправкой на сборку, - вспоминает Юрий Михайлович. - Надо сказать, что здесь перерабатывались значительные объемы древесного сырья - 120 тыс. м в год, железнодорожные составы шли в Москву один за другим. Операции выполнялись несложные: доски строгали, сверлили в них отверстия для болтов и отправляли в цех, где из них собирали борта, бока, кузова. Из дощечек сколачивали вручную тару для запчастей автомобилей. Ну а когда ЗИЛ стал терять позиции и объемы выпуска автомобилей сильно уменьшились, резко сократились и объемы поставок пиломатериалов».
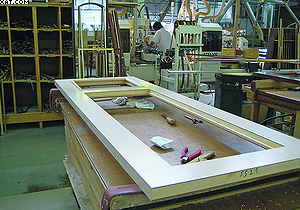
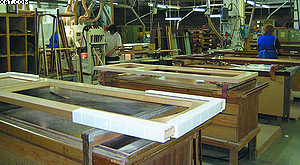
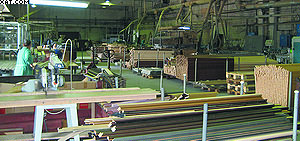
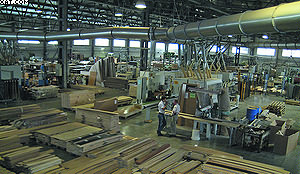
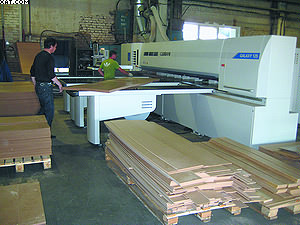
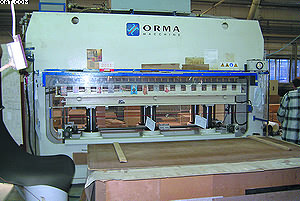
Мембранный жидкостный пресс для оклейки
профилированных деталей (модель PM2, Ormamacchine)
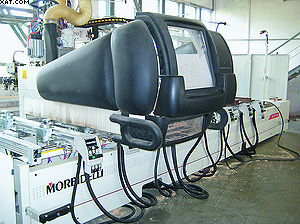
Обрабатывающий центр с ЧПУ Author 344, Morbidelli
(SCM Group)
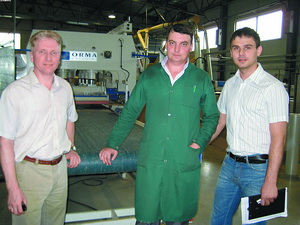
Вадим Крючков (Ormamacchine), Дмитрий Власов (ЗДИ),
Борис Чернышёв (SCM Group)
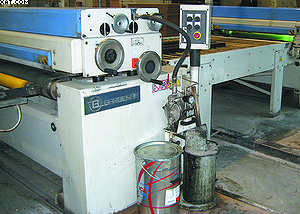
Лакировальный станок BRB-1400
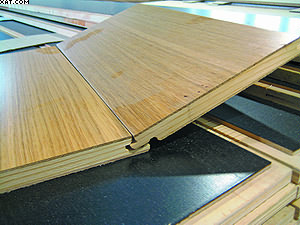
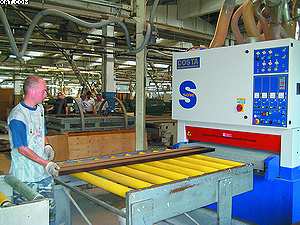
Высокопроизводительная шлифовальная линия S XCTT
1350 (Costa Levigatrici)
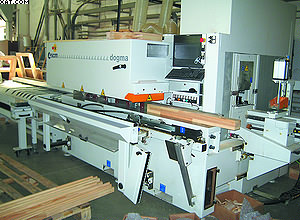
Угловой обрабатывающий центр Dogma (SCM Group)
По сути, надо было либо закрываться, либо начинать все с нуля. Это сказано без преувеличения: в наследство молодому предприятию достались два американских четырехсторонних станка 1946(!) года выпуска, один триммер и еще кое-какое простейшее оборудование. В актив можно было занести только свободные производственные площади и потенциал трудового коллектива.
«Стали думать, чем занять людей, как загрузить площади. Решили взяться за производство деревянных кроватей, - продолжает генеральный директор ЗДИ. - Делали даже двухъярусные кровати. Купили токарные станки - у наших работников получалось делать неплохую "точенку" (то есть фигурные детали изделий - ножки кроватей, декоративные украшения). Изготавливали бра с деревянными элементами и параллельно начали осваивать производство деревянных дверей из массива. Спустя какое-то время, столкнувшись с проблемой реализации кроватей и бра через розничную сеть, поняли, что это не наш путь. Зато в производстве дверей стали вырисовываться неплохие перспективы. Несмотря на то что в начале 1990-х хорошей рекламы у нас в стране еще не было и работало в основном сарафанное радио, к нам стали приходить заказчики, среди которых были даже бывшие работники ЗИЛа».
Двери из массива изготавливали на заказ, и их отменное качество обеспечивало предприятию неплохую рекламу и приток клиентов. Тогда для расширения станочного парка и увеличения производительности завода был куплен отечественный широколенточный калибровальный станок.
«Ох, и намучились мы с ним, - досадливо морщится Юрий Михайлович. - Он был несовершенной конструкции, процесс его наладки был сложен, а качество выполняемых операций оставляло желать лучшего...» Но все же это был пусть и небольшой, но шаг вперед. Вот таким образом и определилась специализация предприятия, так была найдена своя ниша на рынке. Но, говоря об этом, невозможно не сказать и о том, что, помимо деревянных дверей, на предприятии параллельно освоили изготовление и металлических.
«Дело в том, что в свое время в этом цехе производили отечественные микроволновые печи ("Вега", "ЗИЛ"), причем объем выпуска был внушительный - около 120 тыс. микроволновок в год, - говорит г-н Черкасов. - Они были громоздкими, очень тяжелыми и неудобными в пользовании. Судите сами: комплектовались они не преобразователями, а громоздкими, очень тяжелыми трансформаторами. Да и стоили недешево. Одним словом, когда на российском рынке массово появились микроволновые печи зарубежного производства, конкуренции мы не выдержали. Стали искать, чем же заменить печи, и попробовали запустить производство входных металлических дверей с деревянными элементами».
Металлические двери тогда тоже были новым продуктом на российском рынке, проектировать модели и разрабатывать технологию их изготовления пришлось с нуля. Несомненным плюсом было наличие производственных мощностей по металлообработке, а также грамотных специалистов в этой области, что позволило заводу быстро наладить успешное производство: было время, когда в день на заводе изготавливали около 100 дверей.
На новом этапе
К концу 1990-х годов компания, в которой трудилось 240 человек, уже довольно прочно стояла на ногах, и ее руководство предпринимало шаги для укрепления своих позиций на рынке и завоевания новых клиентов. Завод активно готовил собственные технические кадры, предоставляя инженерам и конструкторам возможность получить ценный опыт работы в области дерево- и металлообработки. Помимо этого, были сделаны масштабные закупки оборудования на европейском рынке: у известных производителей приобретены прессы, линии окраски (которые впоследствии были заменены прогрессивными вальцовыми линиями окраски акриловыми материалами), кромкофанеровальное оборудование, четырехсторонние обрабатывающие станки, автоматические обрабатывающие центры, линия полиэфирной порошковой покраски, металлообрабатывающие и гибочные центры.
Памятуя о том, что древесина - «хлеб» деревообрабатывающих производств и от ее качества и своевременных поставок во многом зависит благополучие предприятия, руководство ЗДИ сделало в 1998 году очередной шаг к укреплению своих позиций. «Завод деревоизделий» приобрел лесозаготовительное предприятие в Костромской области (пос. Октябрьский, Мантуровский район) и инвестировал в развитие его инфраструктуры: были вложены немалые средства в строительство новых производственных площадей, увеличение лесозаготовительных мощностей, а также производство погонажных изделий. Обеспечив себя надежной сырьевой базой, предприятие приступило к расширению ассортимента продукции. В 2005 году было построено здание цеха по изготовлению паркета и закуплено соответствующее оборудование. И сегодня производство паркета - это одно из ведущих направлений деятельности компании. Обладая солидным опытом в области деревообработки и располагая необходимыми материалами и неплохим станочным парком, ЗАО «Завод деревоизделий» запустило производство мебели с отделкой в своем фирменном стиле. В 2007 году, в связи с возросшим спросом на деревянные двери и другую продукцию со стеклом и безопасным стеклом «Триплекс», компания создала собственную линию по обработке стекла и изготовлению художественного стекла. А в марте 2011 года при уже имеющейся линии по производству стеклопакетов ЗДИ запустил производство деревянных окон из массива, для чего предприятием было приобретено современное оборудование.
Завод сегодня: цифры и факты
Сегодня в структуру ЗАО «Завод деревоизделий» входит несколько подразделений: дочернее предприятие ЗАО «ЗИЛ-Лес» (Костромская обл.) и головная площадка в Москве. На головной площадке расположены цех металлических изделий (ЦМК), где изготавливают металлические двери; цех комплектации, в котором делают заготовки для деревянных дверей; цех столярных изделий, где выполняется сборка дверей; паркетный цех, в котором изготавливают соответствующее названию цеха покрытие для пола; цех деревообработки, который обеспечивает основное производство заготовками для деревянных дверей; мебельное производство; производство стекла и стеклопакетов; оконное производство; обработка поставляемого шпона; производство топливных гранул (пеллет). Таким образом, можно смело сказать, что ЗДИ - многопрофильное предприятие (о каждом из перечисленных подразделений мы коротко расскажем ниже), обладающее полностью поточным производством с системой мониторинга качества.
У ЗДИ есть собственные склады готовой продукции, мощная котельная, обеспечивающая теплом все предприятие, хорошо развитая внутрицеховая и внешняя дорожная структура: автомобильные дороги, железнодорожные подъездные пути. Общие производственные площади - 9 га. Сейчас в штате «Завода деревоизделий» около 600 сотрудников. Компания владеет двумя собственными магазинами в Москве с бригадами профессиональных замерщиков и установщиков.
Естественно, у предприятия, выпускающего столь многообразную продукцию, множество деловых партнеров - поставщиков сырья, комплектующих, оборудования, оснастки и инструментов. О поставщиках оборудования мы расскажем ниже, в ходе представления каждого направления производства ЗДИ.
Общие объемы производства (в денежном выражении) генеральный директор ЗДИ Юрий Черкасов охарактеризовал так: «Самым успешным у нас был 2008 год, когда объем превысил 1 млрд руб., а затем в связи с кризисом объемы стали падать: в 2009 году - 850 млн руб., в 2010-м - около 730 млн руб. Сейчас мы держимся на уровне прошлого года. Но оптимизма не теряем, надеемся, что с запуском производства окон дела у нас пойдут лучше». Показатели объемов производства конкретных видов продукции из номенклатуры ЗДИ будут приведены в ходе рассказа о производствах завода.
У компании развита обширная сеть дилеров в Москве и других городах России, а также в странах ближнего и дальнего зарубежья. В начале деятельности ЗДИ основным рынком сбыта продукции был рынок российской столицы. В расширении географии заказчиков предприятию очень сильно помогло участие в выставках, на которых продукция ЗДИ была замечена и высоко оценена специалистами и покупателями. Сегодня у «Завода деревоизделий» около 250 дилеров на всей территории России - от Северо-Запада до Дальнего Востока и Сахалина. Вслед за отечественным потребителем интерес к продукции компании стали проявлять и ближнее и дальнее зарубежье: Украина, Казахстан, другие бывшие республики Советского Союза; деревянные и железные двери ЗДИ востребованы даже в США. И это несмотря на то, что на американском рынке широко представлена продукция китайских компаний. «В США сейчас живет немало наших бывших соотечественников, которые занимаются в том числе и поставкой на рынок Соединенных Штатов деревянных и металлических дверей, - рассказывает Юрий Черкасов. - До того, как вышли на нас, они работали с китайскими поставщиками. Но когда познакомились с нашей продукцией, впечатлились, хорошенько взвесили все за и против и поняли, что с нами работать гораздо выгоднее и надежнее. Конечно, нам пришлось немало поработать над перестройкой производства, ведь в России и США строительные нормативы сильно различаются. Кроме того, заокеанские клиенты капризны - каждый раз заказывают разные модели и конфигурации дверей. Но мы справляемся - в том числе с помощью современного оборудования, оснащенного программным обеспечением».
Рассказ о подразделениях многопрофильного предприятия «Завод деревоизделий» начнем с ЗАО «ЗИЛ-Лес» - одного из ключевых звеньев всего производства на ЗДИ, ведь от своевременных поставок качественных пиломатериалов во многом зависит успех всей компании.
«ЗИЛ-лес»: лесозаготовка и деревообработка
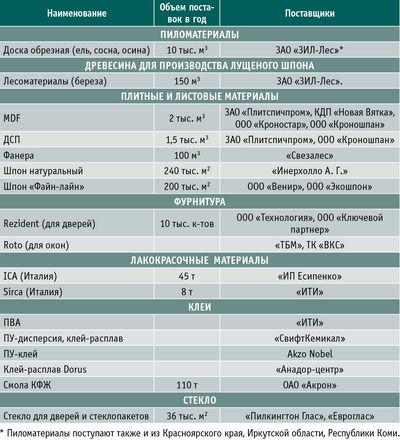
В 1998 году на базе обанкротившегося лесопильного цеха Октябрьского лесничества в Мантуровском районе Костромской области было образовано ЗАО «ЗИЛ-Лес». Поселок Октябрьский расположен на Северной железной дороге, в 600 км от Москвы. На момент создания нового предприятия на нем работали не более десяти человек, машинная база была в плачевном состоянии. Новый владелец предприятия - ЗАО «Завод деревоизделий» начал здесь работу, по сути, с нуля. В результате многомиллионных вложений в дочернее предприятие было обновлено оборудование для лесопиления, построены: цех деревообработки, модуль для окутывания деревянных изделий шпоном и проведения финишной отделки (лакирования, шлифовки, окраски), цех погонажных изделий, электростанция, котельная, смонтированы новые сушильные камеры, возведены дополнительные склады. Общая площадь производственных подразделений - 2,8 га.
Имеется железнодорожный тупик. Отгрузка готовой продукции ведется как железнодорожным, так и автомобильным транспортом. Сейчас на предприятии трудятся 100 человек.
Один из основных видов деятельности - лесозаготовка. Размер арендуемого участка леса в Октябрьском лесничестве - 23 348 га. Заготовка древесины хвойных (ели) и лиственных (березы, осины) пород ведется хлыстовым способом вручную - с использованием пил «Хускварна». Заготовленный лес доставляется на предприятие тракторами ТДТ55. Годовой объем лесозаготовки - 32 тыс. м. Годовой объем производства пиломатериалов - 10 тыс. м. Лесопиление выполняется на пилораме РД-63 (пила «Магистраль») и на фрезерно-пильном станке Кировского завода. Получаемая продукция - осиновые и березовые балансы и пиловочник, а также фансырье, сырой и сухой (8-18%) обрезные пиломатериалы (доски) толщиной от 22 до 200 мм и шириной от 82 до 200 мм, брус (50-100, 100-100, 150-150, 200-200, 100-200, 100-150). Сушка пиломатериалов ведется на оборудовании Katres (поставщик - «Аграф»), за одну закладку в камерах сушится до 300 м сырья.
На предприятии в пос. Октябрьский налажено производство погонажных изделий для дверей: коробок из массива древесины, шпонированных (цвет «венге») размером 78-2070, 78-2070, 60-2070 и 60-2070 мм; наличников гладких фанерованных с покрытием размером 7-2150, 70-2520, 70-1000, 70-1500, 70-2150 (поперечка-1000), 70-2150 (поперечка-1500) мм. Изготавливают здесь и погонаж других видов: плинтус одинарный/двойной с покрытием ПВХ, вагонку, доску для пола. Лакокрасочные материалы на погонаж наносят на линии окраски Giardina (поставщик - фирма «Эста», г. Тверь).
Предприятие также предлагает потребителям отходы деревообработки: сырые и сухие опилки, срезку от пиловочника (горбыль), березовые и осиновые дрова.
ЗАО «ЗИЛ-Лес» для пос. Октябрьский является градообразующим, поэтому руководство ЗДИ планирует здесь увеличение объемов лесозаготовки, развитие деревообработки и увеличение выпуска пиломатериалов и другой продукции. В решении этих задач менеджмент «Завода деревоизделий» получает поддержку руководства региона; оказывает помощь предприятию в пос. Октябрьский и инвестиционный совет при губернаторе Костромской области.
Дверное производство
По понятным причинам мы не станем говорить в этой публикации о производстве металлических дверей, хотя и в этой сфере ЗДИ добился заслуживающих уважение результатов. Наше издание посвящено древесине, поэтому обратимся к дверям из этого материала. На мировом рынке деревянных дверей есть две страны - законодательницы моды: Италия и Испания. Двери итальянских фирм отличаются авангардным дизайном, подчеркнутым вниманием к деталям и традиционно высоким качеством. У испанских производителей дизайн дверей более сдержанный, даже консервативный, а качество столь же высоко, впрочем, как и цены. Двери многих отечественных производителей (среди которых продукция ЗАО «Завод деревоизделий» занимает достойное место) сегодня не уступают зарубежной продукции ни в дизайне, ни в качестве. Зато, используя те же материалы, что и иностранные компании, современное импортное оборудование и передовые технологии, российские производители предлагают покупателю товар, который намного дешевле. Неудивительно, что многие потребители, как в России, так и за ее пределами, предпочитают двери российского производства (вспомните приведенный выше рассказ генерального директора ЗДИ Юрия Черкасова о завоевании американского рынка).
ЗДИ относится к числу предприятий, которые пользуются у заказчиков заслуженно высоким авторитетом и доверием. Сейчас на заводе изготавливают деревянные межкомнатные двери более 120 моделей, общий объем выпуска составляет 60 тыс. шт. в год. Каждая модель из этого многообразного ассортимента родилась после вдумчивого изучения рынка, модных тенденций и потребительского спроса. Весьма богатую пищу для новых идей и интересных разработок дает специалистам и дизайнерам технического и конструкторского отделов ЗДИ посещение специализированных выставок, проходящих в России и за рубежом.
«Посмотрев новинки лучших компаний и уловив тенденции моды, мы берем на вооружение интересные идеи и развиваем их, придерживаясь своего фирменного стиля, - говорит Юрий Черкасов. - Конструкторы делают эскизы и чертежи, сотрудники технического отдела разрабатывают или модернизируют технологии, затем мы изготавливаем опытную модель, макетный образец, после чего запускаем серию и выставляем уже серийный образец в отделе заказов. Если потребители принимают нашу модель и мы видим, что она востребована, начинаем постепенно увеличивать объем ее выпуска, и некоторые модели переходят в складской остаток. В нашей номенклатуре более 120 моделей, и она все время обновляется и расширяется».
Потребителям предлагаются следующие коллекции: серия «Флэт» (10 моделей, стоимостью от 2,88 до 7,52 тыс. руб.); серия «Композит» (с остеклением безопасным стеклом «Триплекс», 35 моделей стоимостью от 6,45 до 11,3 тыс. руб.); серия «Витро» (цельностеклянные двери, 15 моделей стоимостью от 9,91 до 13,12 тыс. руб.); серия «Диамант» (со стеклянными вставками, 18 моделей стоимостью от 4,07 до 6,7 тыс. руб.); серия «Сапфир» (с большой площадью остекления стеклом «Триплекс», 5 моделей стоимостью от 4,47 до 6,27 тыс. руб.); серия «Ретро» (с каркасной конструкцией, филенкой и остеклением, 21 модель стоимостью от 4,95 до 14,06 тыс. руб.); серия «Эконом» (каркасная конструкция с ячеистым наполнителем, 2 модели стоимостью от 1,84 до 2,54 тыс. руб.); серия «Кристалл» (сборная конструкция с несущим стеклом «Триплекс», 18 моделей стоимостью от 7,73 до 14,42 тыс. руб.); серия «Люмина» (сертифицированные противопожарные двери стоимостью 16,5 тыс. руб.). На двери шести серий - «Диамант», «Сапфир», «Флэт», «Ретро», «Эконом» и «Композит» - может быть установлена фурнитура для раздвижных дверей. Кроме того, на ЗДИ на заказ изготавливают нестандартные витражные конструкции разных габаритов, расцветок, дизайна.
В качестве основного материала для производства межкомнатных дверей на ЗДИ используются пиломатериалы хвойных пород, ЧМЗ (черновые мебельные заготовки) твердых лиственных пород, листовой материал - ДВП, ДСП, MDF. Двери, относящиеся к сегменту «глухих» (серия «Флэт»), изготавливаются из плоских полотен, отделанных шпоном древесины разных сортов. Высококачественный плитный материал нужных кондиций поступает на предприятие от проверенных, надежных поставщиков. Для изготовления каркаса каркасных дверей (например, серии «Сапфир», «Ретро», «Эконом») используется хвойный брус высокого качества.
Доставленные на ЗДИ из Костромской области сырые пиломатериалы (обрезные доски) сушат до требуемых кондиций (6-8% влажности) в двух сушильных установках Katres (Чехия) с камерами по 50 м, которые были поставлены на предприятие фирмой «Аграф». Высушенные доски поступают на линию оптимизации и сращивания по длине, на которой из пиломатериала с помощью станка Omga (поставщик - фирма «Интервесп») вырезаются сучки, смоляные карманы и другие пороки, присущие натуральной древесине. Затем торцы досок фрезеруются на станке Goma (Польша; куплен на выставке) для создания шипового соединения, необходимого для сращивания. После чего в прессе Omga (куплен на выставке) под давлением происходит сращивание, то есть склеивание пиломатериала, в результате получается клееный брус длиной 6 м. Далее на четырехсторонних станках Gau Jiwg, Unimat 23E, Superset XL строгается планка для сборки каркаса дверей каркасного типа, которая используется для производства стоявых и поперечин сборных дверей, и наполнитель на склейку щита. Листовой материал раскраивается на форматно-раскроечном станке Galaxy 125 производства компании Gabbiani, который поставила на ЗДИ компания SCM Group.
К собранному каркасу с двух сторон приклеиваются листы MDF толщиной 4 мм. Это повышает прочность и долговечность, а также уменьшает степень микродеформации при резком изменении влаги в помещениях (в отопительный период в помещениях низкая влажность, в остальной период она существенно выше). В соответствии с запатентованной ячеистой конструкцией, которая обеспечивает оптимальные прочность и вес двери, между листами укладывается наполнитель - ребро 4 мм плиты MDF, чередующееся с хвойным бруском. Такая конструкция способствует высокому звукопоглощению (от 34 до 37 дБ) и обеспечивает конструкционную жесткость при среднем весе дверного полотна около 26 кг. Пласть фанеруется шпоном на смолу КФЖ, кромка - на клей-расплав в прессах ORMA.
В зависимости от модели двери для облагораживания поверхностей используются разные материалы. Если фасад имеет внутреннюю фрезеровку, он оклеивается термопластичными пленками, если же дверь филенчатая - шпоном. Для того чтобы облагородить дверь и сделать ее однотонной и одноцветной, все филенки и стоявые покрываются шпоном.
Для окутывания деталей используется пленка: фрезерованная деталь накрывается пленкой, пресс смыкается, мембрана продавливает рисунок и нагревает клей. Клей полимеризуется, высушивается, и материал полностью окутывает деталь.
«На "Завод деревоизделий" наша компания поставила целый ряд разнообразного оборудования, среди которого масляный мембранный пресс PM2 с давлением до 18 кг/см2 для изготовления двухсторонних филенок, проходной автоматический пресс горячего прессования NPC/A для сборки дверных полотен и оклейки плоских панелей, - говорит представитель компании Ormamacchine Вадим Крючков. - Для увеличения производительности у этой модели пресса загрузка и выгрузка осуществляются в автоматическом режиме с противоположных сторон. Оператор укладывает деталь на загрузочный стол и с помощью педали запускает рабочий цикл. Как только пресс откроется, автоматически включается функция перемещения загрузочного транспортера и транспортера, находящегося внутри пресса, и деталь подается в пресс. Перемещая заготовку в пресс, транспортер одновременно выгружает из него запрессованную ранее деталь. Тем самым исключается простой станка для загрузки-выгрузки и увеличивается производительность оборудования. В свое время наша компания провела модернизацию старых прессов советского производства, имеющихся у ЗДИ, установив на них новые стальные столы и системы нагрева, то есть мы дали прессам вторую жизнь. Таким образом, старые и новый прессы, дополняя друг друга в машинном парке компании, позволяют оптимизировать цикл изготовления дверей».
Отделка дверных полотен и филенок осуществляется на линии вальцового нанесения акриловых материалов УФ-отверждения линиях Barberan (поставщик - компания «Негоциант -Инжиниринг»). Шпон для своих моделей на ЗДИ окрашивают в цвета древесины венге, белого дуба, ореха, красного дерева, анегри, ясеня, серебристого дуба. Вся продукция покрывается семью слоями лакокрасочных материалов с разными характеристиками и проходит межслойную шлифовку на станках Costa, что позволяет достигнуть высокой прочности покрытия и зеркальной гладкости поверхности.
Для окутывания деталей используется ПП-пленка цвета венге и бежевого дуба. Кромка дверного полотна изготавливается из натурального шпона, который используется при отделке двери по пласти, что позволяет избежать разнотональности. Приклеивание кромки к полотнам осуществляется на двухстороннем станке Evolution SSB от фирмы Stefani (SCM Group), которая является одним из главных в мире производителей подобных специальных кромкооблицовочных машин для дверных предприятий.
Обрабатывающий центр с ЧПУ модели Author 344 от фирмы Morbidelli от SCM Group - в машинном парке предприятия оборудование довольно новое, его запустили на ЗДИ полтора года назад. Основное его предназначение - фрезерование филенок из твердых пород древесины для дверей, обработка криволинейных деталей, которые не могут быть обработаны на двухстороннем шипорезном станке.
«Это очень интересный станок, на нем выполняется обработка элементов для так называемой спецпродукции, например, дверей, которые изготавливаются по индивидуальному заказу, - говорит Борис Чернышев. - В таких дверях всегда много криволинейных деталей. Главная отличительная особенность этого станка - система двойной мощности вакуумного насоса, которая позволяет, включив сначала низкий уровень мощности, аккуратно разложить и базировать по упорам несколько элементов дверей на рабочем столе и только после этого, активировав высокий уровень мощности, провести их полную фиксацию одновременно. В связи с тем, что зачастую по технологии, применяемой на ЗДИ, на этом станке обрабатываются детали, уже покрытые лаком, то без использования этой уникальной системы было бы просто невозможно обрабатывать сразу несколько элементов на рабочем столе, что, безусловно, повлияло бы на производительность.
Изначально, когда оговаривалась комплектация станка, предусматривалась возможность его эксплуатации на будущем производстве окон. (Об оконном производстве мы расскажем ниже. - Прим. ред.) Поэтому станок был оснащен дополнительными мощными грибковыми захватами и лазером для базирования арочных элементов. И сейчас, когда оконное производство запущено, этот станок изготавливает все арочные элементы окон, а все прямолинейные детали обрабатываются на станке Dogma».
Готовая продукция упаковывается при помощи упаковочной машины H. Böhl GmbH (куплена на выставке) и отправляется на склад. Но прежде каждая дверь, все ее элементы, проходит строгий контроль качества. «Последние тенденции рынка таковы: появляется все больше индивидуальных заказчиков, требования которых постоянно меняются, а конкуренты не дремлют и готовы в любой момент перехватить клиентов. Поэтому для нас вопросы качества продукции всегда на первом плане, - говорит главный инженер ЗАО "Завод деревоизделий" Дмитрий Власов. - Мы своими клиентами дорожим и гордимся тем, что у нас немало зарубежных заказчиков, для которых мы специально разрабатываем модели дверей и изготавливаем ряд строительных элементов. Таких покупателей интересуют в первую очередь высокое качество изделий и соблюдение сроков заказа. Как говорят сами заказчики, пока на российском рынке дверных предприятий, которые бы соответствовали высоким международным стандартам, не так много. Очень приятно, что нас относят к лучшим, но это и очень большая ответственность. Поэтому организации работы отдела технического контроля мы уделяем большое внимание».
Служба контроля на предприятии занимает отдельное здание и оснащена различными современными приборами и оборудованием диагностики и контроля.
На их приобретение на ЗДИ денег не жалеют. Взять хотя бы прибор для проверки замкового соединения паркетной линии - профилограф. Он способен отображать увеличенный в разы профиль деталей на экране, что облегчает процесс сравнения с шаблоном и дает возможность максимально точно настраивать инструмент. Эта установка стоит около 7 тыс. евро. Такие же полезные приборы, созданные специально для проверки качества материалов и готовых изделий, имеются в службе контроля и для других видов продукции. И затраты на их приобретение оправданны.
Производство мебели
ЗАО «Завод деревоизделий» производит на заказ офисную и домашнюю мебель: офисные столы, кресла, напольные вешалки, офисные стеллажи, шкафы, тумбы, стойки ресепшен, комоды. Объем производства - 720 комплектов в год. У предприятия немало заказчиков, ведь мебель, изготовленная по индивидуальному заказу, позволяет решить широкий спектр самых разнообразных задач. Дизайнеры и конструкторы ЗДИ разрабатывают модели с учетом индивидуальных потребностей и пожеланий клиента и специфики помещений. Офисная мебель помогает грамотно организовать рабочее пространство, повысить производительность сотрудников и способствует формированию имиджа компании. Мебель для дома предоставляет большие возможности для создания индивидуального стиля интерьера, комфорта и атмосферы домашнего уюта.
Производственные возможности предприятия позволяют изготавливать мебель любой сложности и в любом стиле - подразделения ЗДИ оснащены современным высокопроизводительным оборудованием. Мебель изготавливается с использованием современных, экологически безопасных материалов. Технология ее производства похожа на технологию изготовления дверей: раскрой материалов на детали, оклеивание фасадов и кромок, фрезерование отверстий и пазов для фурнитуры, упаковка.
Кроме того, предприятие производит и осуществляет продажу деревянных стеновых панелей, мебельных щитов ДСП, фанерованных с двух сторон шпоном натурального дерева: сосны, дуба, ясеня и других пород. Мебельный щит - экологически чистый материал, который используется для разных видов отделочных работ, а также для изготовления мебели и лестниц. Мебельный щит представляет собой панели ДСП толщиной 16 мм, фанерованные с двух сторон натуральным шпоном ценных пород древесины. Для придания изделиям завершенности и привлекательного внешнего вида их кромки обрабатывают полосками шпона. У этого материала нет недостатков, присущих натуральной древесине. Он не деформируется, не растрескивается и после соответствующей обработки приобретает определенную степень пожаростойкости.
Предприятие предлагает также экологически чистый мебельный щит с сотовым заполнением (стандартные габаритные размеры - 2440-1200-25 мм, но по желанию заказчика щит может быть изготовлен любых размеров) производится без использования MDF и ДСП. Структура этого вида мебельного щита: каркас, сотовое заполнение, слой фанеры, на который приклеивается шпон. Лакирование выполняется акриловыми материалами. Кромка фанеруется шпоном. По такой же технологии изготавливается экологически чистый мебельный щит из массива древесины, с той лишь разницей, что вместо сотового заполнителя используется высушенный массив хвойных пород древесины.
Паркетное производство
Один из наиболее востребованных видов продукции, выпускаемых на ЗАО «Завод деревоизделий», - паркетная доска. Этот вид напольных покрытий - прекрасная альтернатива штучному паркету: при более приемлемой, чем у штучного «собрата», цене и сопоставимом качестве паркетная доска выглядит элегантно и в то же время солидно, благодаря чему интерьер приобретает эффектный вид. Кроме того, паркетная доска ценится за высокую ударопрочность: с таким покрытием можно не бояться царапин, сколов и вмятин на полу. Обладая повышенной стойкостью к перепадам влажности и температуры, этот строительно-отделочный материал сохраняет форму в любом климате. Среди неоспоримых достоинств паркетной доски долговечность, простота и невысокая стоимость монтажа, а также огромное разнообразие расцветок. По внешнему виду паркетная доска подразделяется на одно-, двух- и трехполосную - в зависимости от количества плашек в верхнем слое. По структуре паркетная доска состоит из двух или трех слоев. Нижний слой обычно делают из древесины сосны или ели, а верхний - из более дорогих пород: дуба, ясеня, венге, бука. Слои склеиваются под давлением и покрываются несколькими слоями лака. Массивная паркетная доска создается полностью из массива древесины, слои которой склеиваются.
«Мы изготавливаем трехслойную паркетную доску и массивную доску из разных пород дерева и предлагаем потребителям огромный выбор этой продукции, различающейся по типу конструкции, дизайну и цвету, - говорит главный инженер Дмитрий Власов. - Трехслойная паркетная доска производится из материалов отличного качества на самом современном импортном оборудовании, с применением передовых технологий. Выпускаемое нами напольное покрытие обладает множеством замечательных качеств, например, оно, по сути, не подвержено короблению, у него прекрасная износоустойчивость в процессе эксплуатации. А благодаря особой конструкции доски - с соединением типа "замок" - монтаж пола несложен, выполняется довольно быстро. К тому же эта технология обеспечивает отличное качество и высокую прочность соединения - по полу можно ходить сразу после монтажа. Также настеленное покрытие можно многократно разбирать и вновь настилать, потому что соединять элементы такого пола между собой можно без использования клея».
Неудивительно, что продукция ЗДИ пользуется устойчивым спросом у заказчиков. Годовой объем производства трехслойной паркетной доски - 35 тыс. м2. На расспросы о секретах производства работники ЗДИ улыбаются: «Секреты? Есть такие. Надо использовать возможности оборудования и правильно обслуживать машины, соблюдать технологические режимы и думать о заказчике».
На практике это происходит так. Сначала на ТВЧ-прессе ORMA (поставщик - компания Ormamacchine) изготавливают клееный паркетный щит толщиной 14 мм. В разрезе он представляет собой «пирог»: нижний слой (толщина 1,7 мм) - это шпон хвойных пород, покупной лущеный шпон; средний слой (толщина 9 мм), который располагается перпендикулярно к верхнему и нижнему слоям, - это пиломатериал хвойных пород, крайние замочные ламели изготавливаются из твердых пород древесины или фанеры; верхний слой (толщина 3,3 мм) - это либо шпон твердых лиственных пород (дуба, ясеня, бука), либо тонкий пиломатериал (дуб, бук, ясень, береза). Распил заготовок для среднего слоя, а также для верхнего, если он пиленый, выполняют на станке Zaffaroni (приобретен на выставке). Склейку трехслойного щита в прессе ORMA делают на смолу «Каскорит» (поставщик - фирма Akzo Nobel).
Затем на вальцовой линии окраски Barberan на готовый щит наносят шесть слоев лака или масла (поставщик ЛКМ - фирма ICA). В финишном лаковом покрытии содержится оксид алюминия, повышающий износостойкость защитного лакокрасочного покрытия доски. Шлифовка слоев выполняется на станке Costa Levigatrici (куплен через московское представительство итальянской компании Costa Levigatrici S.p.A.). Замковую часть паркетной доски фрезеруют на станке Celaschi (поставщик SCM Group). После раскроя щита на штучную паркетную доску на станке Zaffaroni готовая продукция упаковывается и отправляется на склад.
Производство погонажа
Мы уже упоминали выше о том, какую огромную роль в процессе производства продукции ЗДИ играют погонажные изделия. От их качества зависят качество, рабочие характеристики, внешний вид готовых изделий и в конечном счете востребованность продукции предприятия на рынке, ее конкурентоспособность. Поэтому руководство ЗАО «Завод деревоизделий» уделяет этому важному участку повышенное внимание.
На ЗДИ для обеспечения дверного производства изготавливают следующие виды погонажа:
- дверную коробку в трех вариантах - шириной 60, 78, 110 мм;
- добор, который используется в тех случаях, когда толщина стены в помещении, где устанавливается межкомнатная дверь, больше ширины коробки (ширина изготавливаемых стандартных доборов - 33, 43, 61, 79, 97, 115, 132 мм; кроме того, добор может регулироваться (выдвигаться) из коробки на +5 мм);
- наличник, который нужен для обрамления двери с внутренней и внешней сторон и закрывает щель между дверной коробкой (или добором) и стеной (ширина - 55, 70 и 100 мм);
- держатель наличника используется для крепления наличника к дверной коробке без использования гвоздей или шпилек, что позволяет избежать риска внешних повреждений.
На линии изготовления погонажа выпускается 80 тыс. пог. метров изделий в месяц. «Исторически так сложилось, что оборудование для этой линии мы приобретали в разное время и у разных производителей и поставщиков, - говорит Юрий Черкасов. - Есть и такое, которое мы купили на специализированных выставках, есть бывшее в употреблении. Но люди у нас квалифицированные, мастеровитые, к оборудованию относятся бережно, понимают его возможности, и оно служит исправно».
В принципе технологическая цепочка изготовления дверного погонажа мало чем отличается от общеизвестной технологии. После сушки пиломатериалы сращиваются на линии оптимизации и сращивания (станки Goma и Omga). Профиль строгается на четырехсторонних станках Gau Jiwg, Unimat 23E и Superset XL (SCM Group). Далее погонажные изделия окутываются шпоном ценных пород на станках Barberan и Duspol (оба приобретены на выставках). Погонажные изделия окрашиваются лакокрасочными материалами фирмы ICA, сушатся в ультрафиолете (станок Superfici, поставщик - компания SCM Group) и шлифуются на оборудовании Makor, Giardina.
«Мне нравится, как на ЗДИ используют возможности оборудования, - говорит директор московского представительства SCM Group Борис Чернышев. - Например, для увеличения производительности линии производства погонажа некоторые детали здесь делают в кратном формате, после чего делят их пополам на отдельном делительном станке. Это грамотная технология, которая дает ощутимый эффект. Весь цикл обработки, в который входят операции нанесения грунта, шлифовки в линии, нанесения финишного слоя и окончательной сушки, деталь проходит за один подход».
Оконное производство
Это самое молодое и одно из перспективных направлений деятельности ЗАО «Завод деревоизделий» - пример того, как развивается это предприятие. Производство деревянных окон было запущено только в марте текущего года. Сейчас на новом производстве изготавливают около 50 окон в месяц, планируется вскоре достичь отметки 100 окон - количество заказов постоянно растет. Окна от компании «Завод деревоизделий» изготавливаются в соответствии с европейскими стандартами из 78- и 92-миллиметрового профиля, склеенного из пиломатериалов хвойных (сосны) и твердолиственных (дуба, ясеня, лиственницы) пород, оснащаются одно- и двухкамерными стеклопакетами собственного производства и качественной немецкой фурнитурой компании Roto NT. Предприятие изготавливает окна по заказу, в соответствии с индивидуальными требованиями и размерами оконных проемов помещений клиента.
Процесс изготовления следующий. Пиломатериалы сушатся, оптимизируются, сращиваются по длине. Далее доски строгают и склеивают (клей GXL4, поставщик - фирма «ИТИ») под давлением в прессе (ORMA) по толщине из трех ламелей. Полученный конструкционный материал прекрасно подходит для изготовления деревянных окон: по сравнению с цельным брусом он характеризуется более высокими прочностью и жесткостью, низкой теплопроводностью и меньшим весом, не растрескивается и почти не подвержен усадке.
Ну а почти все остальные операции на ЗДИ решили доверить уникальной технике от SCM Group. Новый угловой обрабатывающий центр Dogma от признанных итальянских мастеров машиностроения, который был поставлен московским представительством компании SCM на «Завод деревоизделий» меньше года назад, - это оборудование нового поколения для выпуска оконных блоков на предприятиях малой и средней производительности (20-30 окон в смену). Именно такая машина и требовалась ЗДИ, руководство которого сделало ставку на индивидуального заказчика и выпуск небольших партий изделий нестандартных размеров и конфигураций. «У SCM также есть и комплексные линии, на которых можно выпускать по 100-200 оконных блоков в смену, - отмечает Борис Чернышев. - Но именно машины такого класса, как Dogma, будут все более востребованы, так как в мире укрепляется тенденция к снижению партийности как в производстве окон, так и дверей и расширению ассортимента».
Этот станок состоит из двух частей - он оснащен шипорезной кареткой для зарезки шипов и узлом для профилирования. После того как на сверлильной группе Optima 1 зарезают шипы и делают все отверстия и выемки под фурнитуру в элементах окна, заготовка поступает на продольную часть станка, где выполняется профилирование. Затем заготовка возвращается к оператору (кстати, конструкция станка хорошо продумана в части эргономики - ОЦ обслуживается одним оператором, рабочее место которого находится посередине станка, и оператор совершает минимум перемещений, так как заготовка, как уже отмечено, возвращается к нему после обработки). После этого заготовки склеиваются на вайме, и склеенное окно заново поступает на данный центр для обгонки по периметру.
Рассказывая о достоинствах Dogma, Борис Чернышев подчеркивает: «Станок уникальный в своем классе и оснащен многими функциями, которые прежде могли осуществлять только очень дорогие оконные линии. Например, у шипорезной каретки станка есть возможность интерполированного поворота от ЧПУ, что позволяет делать любые косоугольные окна. Не могу не отметить еще один очень интересный момент: этот центр оснащен системой быстрой смены инструментов на базе шпинделей HSK, какие используются на всех обрабатывающих центрах. То есть здесь не используются классические фиксированные шпиндели, как на большинстве подобных угловых центров, где смена инструмента и набор нового пакета занимает несколько десятков минут, не говоря уже о риске ошибки оператора при выполнении этих операций. Все перечисленное - ответ SCM современным требованиям рынка, так как сейчас на разных предприятиях изготавливается множество типов окон и, как правило, на большинстве оконных производств в наши дни не выпускаются серии объемом несколько сотен одинаковых окон. В последние годы производители окон во всем мире предъявляют требования к гибкости перенастройки машин. За счет такой быстрой системы крепления инструмента, которая используется в нашем ОЦ Dogma, станок может быть перенастроен за считаные минуты с одного типа профиля на другой. В случае с ЗДИ мы поставили на это предприятие комплексный инструмент, который может быть комбинированным - толщина створки делается и 78, и 92 мм».
Разрабатывая центр Dogma, конструкторы SCM продумали, как сделать удобным и безопасным процесс замены инструментов, а это на таком оборудовании в прямом смысле слова нелегкая операция - вес комплекта шипорезных инструментов может доходить до 50 кг. Для того чтобы упростить и облегчить эту задачу, на SCM разработали небольшой манипулятор, с помощью которого оператор может, открыв защитный кожух, захватить весь комплект инструментов вместе со шпинделем HSK и вытащить его, установить на тележку, взять новый комплект и т. д.
Еще один из несомненных плюсов станка - наличие узла для сверления отверстий под всю фурнитуру. Если на других машинах после склеивания окна сверловку под ручки и петли необходимо выполнять на специальном оборудовании или вручную, то Dogma позволяет сверлить отверстия под фурнитуру прямо на станке, во время шипорезания. Таким образом, окно после обработки на этом станке остается только собрать и покрасить.
Обработка шпона
На ЗДИ налажена обработка такого важного отделочного материала, как шпон. Он может использоваться и для облицовывания пластей и кромок, и в качестве фанеровки, например, дверных полотен. Этот материал более пористый, чем натуральная древесина, и при фанеровании требует большего расхода клея, но зато в процессе отделки снижается расход лака. Получив шпон от нескольких поставщиков, на предприятии его разрезают на листы определенного размера на гильотине Kuper, сращивают на одноименном станке и дублируют флисом на линии Barberan. Шлифуют шпон на станке компании Costa. Годовой объем производства - 600 тыс. м2 в год.
Производство пеллет
На «Заводе деревоизделий» давно и успешно решена проблема использования отходов деревообработки - как крупных твердых (обрезки пиломатериала, фрагменты плитных материалов), так и опилок и древесной (шлифовальной) пыли. На линии по производству древесных гранул «ОГМ-1,5» (производитель - предприятие из г. Радвилишкис, Литва) они перерабатываются в пеллеты. Пневмотранспортом из накопителя отходы подаются в молотковую дробилку (фирма «Доза-Гран»), затем в пресс-гранулятор и через колонну охлаждения - на упаковку в биг-бэги. Годовой объем производства - 600 т. Продукция поставляется за рубеж через фирмы-посредники.
Добавим, что цех ЗДИ, в котором находится это производство, стал съемочной площадкой для сюжета о производстве пеллет телевизионной программы «Галилео» на канале СТС.
Важное звено
Именно так, с полным на то основанием, мы можем назвать те подразделения ЗАО «Завод деревообработки», которые обычно называют вспомогательными. Но без них немыслима успешная работа всего огромного и сложного производственного организма ЗДИ. Итак, хотя бы перечислим их.
Котельная. В 2009 году котельная ЗДИ была модернизирована, в ней были установлены газовые котлы немецкой компании Viessmann - два котла по 2,9 МВт; этой мощности вполне достаточно, для того чтобы обеспечить завод.
Аспирационная система. На ЗДИ установлено оборудование фирмы «Нестро» (приобретено через московское представительство - фирму «Консар»).
Участок подготовки инструмента. Без использования инструмента таких компаний, как Leitz, АКЕ, Italtools, Freud, была бы невозможна успешная работа любого, даже самого современного, оборудования. Затачивается и ремонтируется инструмент на оборудовании компаний Randomat, Griggio, Lakfam, Wintersteiger (приобретено на выставках и у компании «КАМИ-Cтанкоагрегат»).
Ремонтная группа. В нее входят квалифицированные токари, фрезеровщики, слесари, которые круглогодично следят за состоянием эксплуатируемой техники и обеспечивают ее оптимальные рабочие кондиции.
Внутрицеховой транспорт. Для перевозок материалов, сырья, заготовок и готовой продукции и погрузо-разгрузочных работ на ЗДИ используются погрузчики Jungheimrich, Komatsu, Hyundai, тракторы «Амкодор».
Движение вперед
На предложение поговорить о перспективах развития предприятия его генеральный директор реагирует так: «Честно говоря, главный пункт плана сегодня - выдержать испытания последних лет, пройти через них, не потеряв позиций, не растеряв людей. У нас крупное многопрофильное предприятие, и именно поэтому нам непросто в нынешней экономической ситуации.
Вот ведь как делают все на периферии? Дробят производства, превращают их в малые и средние предприятия, получают максимальные льготы по упрощенной системе налогообложения. А у нас отпуска, больничные листы - мы все оплачиваем, НДС 18 %, почти 50 % уходит на ЕСН - вот поэтому для нас сейчас главная задача - устоять. Персонал важно для меня сохранить. Беда ведь еще в том, что квалифицированных кадров даже в Москве сегодня не сыщешь. Вот, допустим, высококвалифицированным токарю, фрезеровщику у нас по 70 лет. А без этих специалистов обслуживать оборудование чрезвычайно сложно. Не буду же я просить привезти мне из Италии ту деталь, которая у меня сломалась! Эх, нет таких специалистов, которых раньше на ЗИЛе было пруд пруди! Нужно поднимать престиж рабочих специальностей, улучшать профессиональное образование - оно у нас сейчас, так же как и вся промышленность, в плачевном состоянии... Современного конкурентоспособного оборудования в стране почти не производится. Раньше можно было купить хоть какой-то более-менее сносный шлифовальный или фрезерный станок отечественного производства. Я даже помню, что в Москве, на Почтовой улице, был завод деревообрабатывающего оборудования, мы там покупали шипорезы, еще что-то. В Нальчике было предприятие, которое производило кромкофанеровальные станки. Сейчас ничего этого нет... Даже на московских специализированных выставках очень мало наших предприятий представлено. Почему?.. Поймите, все, что я сейчас сказал, имеет прямое отношение к моему ЗДИ, к людям, которые у нас трудятся, к будущему нашего предприятия».
Спрашиваем Юрия Михайловича: «Но ведь у вас есть движение вперед, предприятие развивается - вы открыли новое производство, купили новое оборудование...»
«Конечно, нельзя стоять на месте, никто за нас не будет думать и решать, - говорит Юрий Черкасов. - Да, оконное производство - это шаг вперед, который совпал с нашим шагом в третье десятилетие ЗДИ.
Мы возлагаем на него большие надежды. Ну а лично я возлагаю надежды на своего сына - 26-летнего Михаила, который вместе со мной встает утром полшестого и приезжает сюда к семи, вникает в дела предприятия, болеет, как и я, за его судьбу, думает о его будущем и, надеюсь, станет хорошей сменой мне и встанет у руля "Завода деревоизделий"».
Елена ШУМЕЙКО,
Александр РЕЧИЦКИЙ