«ПДК Апшеронск» – курс на новое производство
Одно из ведущих предприятий деревообрабатывающей промышленности Краснодарского края - ЗАО «ПДК Апшеронск» реализует крупный инвестиционный проект: строительство завода по производству плит MDF, который будет оснащен высокотехнологичным оборудованием немецкого производства.
Продукция комбината, занимающегося глубокой переработкой древесины, известна далеко за пределами Краснодарского края. Сейчас на базе ЗАО «ПДК Апшеронск» действует производство мебели из массива, на котором (включая лесозаготовительный комплекс) занято 350 человек. В середине 2011 года руководство компании приняло решение о модернизации действующего производства. В основе проекта комплексный подход, предполагающий совершенствование инфраструктуры с целью организации эффективной системы производства и развития производственного комплекса на базе действующего столярного производства, чему способствуют возможности местной сырьевой базы. Расчетная мощность оборудования - 6500 стульев, 1500 столов и 2000 м2 мебельного фасада в месяц. Руководство ЗАО «ПДК Апшеронск» планирует реализовывать продукцию на внутреннем рынке и осваивать рынок СНГ. «У предприятия многолетний опыт в области деревообработки, мы способны выпускать конкурентоспособную продукцию, по качеству соответствующую высоким мировым стандартам. Немаловажную роль в повышении эффективности производства играет его оснащение лучшим современным оборудованием», - говорит генеральный директор Альберт Ашикарян. Условия для достижения поставленных целей у предприятия благоприятные: динамично развивающиеся мебельный рынок региона и туристско-рекреационный комплекс Краснодарского края. Обновленное столярное производство позволит создать еще 117 новых рабочих мест.
Компания ведет лесозаготовку в пяти районах Краснодарского края. Лесоматериалы доставляются на предприятие автотранспортом. Раскрой лесоматериалов выполняется на лесопильных станках турецкой фирмы Ustunkarlı, на которых можно распиливать сортименты любой породы при длине бревен от 2 до 6 м. При выборе этого оборудования сотрудники «Апшеронска» ориентировались на соотношение цены и качества и полагались на положительные отзывы специалистов, эксплуатирующих аналогичное оборудование в России. Обрезка и торцовка досок также выполняются на оборудовании Ustunkarlı. Пиломатериалы, уложенные в плотные пакеты, доставляются на участок сортировки, где укладываются в штабели.
Сушильный комплекс укомплектован оборудованием итальянской фирмы Nardi и состоит из 11 сушильных и одной пропарочной камеры; общая мощность комплекса - 580 м3 в месяц. Перед сушкой древесина бука пропаривается. Сушильный процесс включает в себя пять циклов: нагрев, сушку, выравнивание, влаготеплообработку, остывание. Для каждой партии пиломатериала технологом составляется свой режим, зависящий от многих факторов (начальной влажности, температуры и т. п.), процесс сушки контролируется оператором. Продолжительность сушки пиломатериалов бука толщиной 30-50 мм - 20-30 суток.
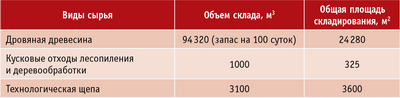
Высушенный пиломатериал поступает в столярный цех. Плинтус, обшивочная доска, погонаж изготавливаются на четырехстороннем станке Unimat Gold (Weinig Gruppe, Германия), точеные изделия - на станке Killender (Германия), дверные филенчатые блоки, евроокна и различные элементы мебели - на оборудовании с ЧПУ Homag BOF 311 Professional (Германия). На предприятии довольны немецким оборудованием - оно качественное, работает безукоризненно, на хорошем уровне налажен сервис. Цех динамично развивается, активно приобретается новое современное оборудование, площади для его установки уже подготовлены. Разрабатывается номенклатура для новой продукции.
Производство плит MDF и ламината на ПДК «Апшеронск»
На территории ПДК активно ведется строительство завода по производству плит MDF и напольных ламинированных покрытий. Генеральный директор ЗАО ПДК «Апшеронск» Альберт Ашикарян подчеркивает, что проект получает огромную поддержку администрации Апшеронского района и Краснодарского края, а в начале 2009 года был включен в Перечень приоритетных инвестиционных проектов РФ в области освоения лесов, что способствовало заключению долгосрочных договоров аренды лесного фонда.
Поставщиками современного технологического оборудования выступают производители с мировым именем: оборудование для основной технологической линии MDF изготовлено компанией Siempelkamp, а оборудование окорочно-рубительного участка, участка очистки щепы и расщепление на волокна - компанией Pallmann.
Оборудование Pallmann на ПДК «Апшеронск»
Оборудование, поставляемое фирмой Pallmann, установлено в основных цехах и на участках (склад сырья, окорочно-рубительный цех, участок транспортировки, хранения и сортировки щепы, цех очистки щепы и изготовления волокна), используется в технологической цепочке производства плит MDF.
Окорочно-рубительный цех. Круглые лесоматериалы со склада сырья подаются лесоперегружателем Terex Fuchs MHL 454 на продольный цепной транспортер, который доставляет сырье к роторному окорочному станку PRDT-0360. Кусковые отходы лесопиления и деревообработки автопогрузчиком подаются на питающий транспортер. Кора от окорочного станка, рольганга-очистителя, питающего транспортера для отходов лесопиления по ленточным конвейерам поступает на желобчато-ленточный конвейер, над которым установлен сепаратор с электромагнитом для извлечения металлических частиц из коры. Очищенная от металла кора проходит через просеивающий транспортер и поступает в короизмельчитель PMR 12-600. Измельченная кора отправляется на склад топлива.
Окоренная древесина и отходы лесопиления поступают в барабанную рубительную машину PHT 850×1250. Подача древесины на ротор в рубительную машину осуществляется с постоянной скоростью путем зубчатых втягивающих валов, число оборотов ротора, количество ножей на роторе и перфорация подроторного сита определяют конечную фракцию щепы. Разгрузка осуществляется через разгрузочный лоток с контролем уровня заполнения на двойной лотково-шнековый транспортер и далее ленточным транспортёром подается в бункер для промежуточного хранения.
Участок транспортировки, хранения и сортировки щепы. Щепа от рубительной машины с помощью системы транспортеров раздается по четырем отсекам бункера, который предназначен для промежуточного хранения щепы (по породам) и равномерной дозированной выгрузки. Бункер оборудован датчиками контроля заполнения и системой пожаротушения. Привозная технологическая щепа ковшовым погрузчиком подается в шнековый бункер, затем устройством выгрузки и выносными шнеками - на желобчато-ленточный конвейер с ленточными весами, которым передается на ленточный транспортер и далее - на желобчато-ленточный транспортер, на котором установлены металлодетектор и направляющая заслонка, срабатывающая от его сигнала. На ситовом сепараторе из материала отделяется сверхкрупная фракция и мелочь. Крупная фракция поступает в доизмельчитель PSN 300×750, а затем вместе с кондиционной щепой транспортируется желобчато-ленточным конвейером на мойку. Мелкая фракция лотково-шнековым конвейером удаляется в контейнер мелкой фракции.
Цех очистки щепы. Сортированная щепа загружается в промывочную установку PWH 240, в которой проходит первоначальную очистку. Установка предназначена для водной очистки щепы от песка, камней, прочих минеральных, а также металлических примесей, за счет чего увеличивается срок службы рафинера и других узлов и агрегатов и снижается содержание минеральных составляющих в древесно-волокнистых плитах. При погружении щепы в воду ротор ворошителя промывочной установки, вращаясь, создает высокую турбулентность. Тяжелые включения (камни, металл) оседают в гравитационном сепараторе. Загрязнения выводятся через шлюз с двойным (верхним и нижним) клапаном. Затем щепа с водой поступает в предварительный бункер, из которого насосом перекачивается в дренажный шнек и отделяется от загрязненной технической воды. Очищенная щепа подается в бункер рафинера.
Загрязненная техническая вода поступает в гидроциклон, в котором благодаря высоким центробежным силам песок и мелкие оседающие древесные частицы сепарируются, а затем отводятся через специальный износостойкий клапан. Вода из гидроциклона по трубопроводу, расположенному в верхней части гидроциклона, поступает в приемный резервуар, оснащенный насосом. Для улучшения результатов промывки и оттаивания щепы в зимних условиях вода в приемном резервуаре при необходимости подогревается паром.
Питающий насос откачивает воду из приемного резервуара обратно в промывочную установку и гравитационный сепаратор. Насосом промывочная вода подается к набивному шнеку и дренажному шнеку. Для дальнейшей очистки вода подается на роторное сито, где от нее отделяются твердые частицы, которые сбрасываются в контейнер для отходов. Пройдя сито, предварительно очищенная вода поступает в бетонный резервуар; работающие в нем мешалки предотвращают оседание тяжелых частиц, техническая вода из этого резервуара подается циркуляционным насосом обратно в систему. В отстойнике тяжелые частицы оседают на дно, очищенная вода с мелкими плавающими частицами снова подается в бетонный резервуар, откуда в объеме 30 м3/ч направляется на очистные сооружения промстоков и повторно используется для мойки щепы. Осевшие частицы подаются насосом на сепаратор, в котором частицы крупнее 0,25 мм отделяются, падают в спиральный шнек и отводятся в контейнер для отходов. Очищенная вода после сепаратора поступает в приемный резервуар и снова используется в системе циркуляции.
Цех изготовления волокна. Щепа размалывается на волокна в пропарочно-размольной установке PR - 62 Eco-Advanced (рафинере). Щепа поступает в бункер для предварительной пропарки объемом 60 м3.
Запас щепы в бункере обеспечивает ее предварительную пропарку и бесперебойную, равномерную подачу в набивной шнек. Набивной шнек сконструирован в виде конуса для образования пробки из щепы, которая предотвращает выход насыщенного пара высокого давления, подаваемого в пропарочный котел рафинера. Из набивного шнека щепа поступает в вертикальный варочный котел объемом 16 м3. Котел предназначен для пропаривания щепы насыщенным паром давлением максимум 12 бар с целью уменьшения ее прочности, особенно в направлении поперек волокон за счет плавления лигнина, который скрепляет отдельные волокна древесины между собой. Пропаривание щепы позволяет снизить расход электроэнергии при размоле и содержание пылевидных фракций в составе получаемого волокна.
В основании котла имеется мешалка, подающая щепу в выносной шнек. Выносной шнек предназначен для регулирования подачи щепы в загрузочный шнек и размольную камеру рафинера. В загрузочный шнек рафинера дозированно подается расплав парафина. Щепа равномерно загружается в пространство между размольными дисками рафинера, где сначала растирается ребрами сегментов (зона предварительного размола), а затем размалывается зубьями размольных сегментов на волокна. Гидродинамический опорный узел особой конструкции и высокоточная система регулировки обеспечивают зазор между сегментами с точностью до 0,01 мм.
Полученная древесно-волокнистая масса выдувается из размольной камеры в массопровод. Направление потока материала изменяется при помощи дефлектора волокнистого материала. В начале операции волокно направляется через пусковой циклон в контейнер-сборник; когда контейнер наполнится, дефлектор автоматически переключается и кондиционное волокно перемещается по продувочному трубопроводу
(в котором обрабатывается клеем) в трубу-сушилку.
Оборудование Siempelkamp на ПДК «Апшеронск»
Оборудование, поставляемое фирмой Siempelkamp, установлено на участках клееприготовления, сушки и сепарации волокна, формовочно-прессовом, охлаждения и штабелеукладки, на автоматизированном участке выдержки плит, участках шлифования и форматной обрезки плит, ламинирования и упаковки плит, а также в лаборатории.
Участок клееприготовления с насосной, расположенный в цехе очистки щепы и изготовления волокна, необходим для приготовления клея на основе карбамидоформальдегидной смолы. В состав клея входят: смола КФМТ-15, карбамид (мочевина), отвердитель (хлористый аммоний) и вода. Из емкостей расходного склада товарная смола через фильтр подается в промежуточную обогреваемую, теплоизолированную, оснащенную датчиками уровня емкость объемом 10 м3, из которой через насосно-дозирующее устройство подается в статический смеситель. В изготовленной из нержавеющей стали емкости объемом 2,5 м3 поочередно приготавливаются рабочие растворы отвердителя и карбамида. Горячая вода через фильтр заливается в емкость с весовым дозированием компонентов. Через две системы опорожнения мягких контейнеров с подъемной рамой, воронкой и шнековым конвейером загружается расчетное количество отвердителя или карбамида. Смесь перемешивается до полного растворения химиката.
Приготовленный раствор центробежным насосом перекачивается через фильтр в расходные емкости объемом по 5 м3 (изготовлены из нержавеющей стали, оснащены мешалками, датчиками уровня). Твердый парафин в плитках загружают в емкость (плавильник) объемом 5 м3, с обогреваемым паром змеевиком, терморегулятором, мешалкой и датчиком уровня. После расплавления парафин перекачивается обогреваемым теплоизолированным насосом через фильтр по трубопроводу с обогревом в обогреваемый расходный бак объемом 3 м3. С подачей расплава в патрубок перед размольной камерой рафинера с помощью специального устройства выполняется непрерывное дозирование пяти компонентов смеси. Каждый компонент дозируется насосами отдельно - в соответствии с заданным рецептом. Компоненты добавок клея и вода смешиваются в первом статическом смесителе, затем подаются во второй статический смеситель для смешивания с товарной смолой. Предусмотрена дозированная подача раствора отвердителя по трем вариантам: раздельно - через индивидуальное распылительное сопло; в патрубок перед размольной камерой; через статический смеситель, где смешиваются вода, растворы карбамида и отвердителя, после чего эта смесь подается во второй статический смеситель, в котором смешивается с товарной смолой.
Клей и раствор отвердителя наносятся на волокна дутьевой клеенаносящей установкой Blow-Line методом распыления через форсунки. Из статического смесителя рабочий раствор смолы подается в распределительную трубку с 11 форсунками, откуда через электромагнитные клапаны распыляется на древесно-волокнистую массу в трубопроводе. Расход клея определяется качеством древесного сырья и влияет на качество изготавливаемой плиты. Если используется здоровая свежесрубленная древесина, особенно хвойная, расход клея невысок. А в случае гнилой, залежавшейся трухлявой древесины расход смолы увеличивается. Расход отвердителя зависит от качества и реакционной способности смолы.
Участок сушки и сепарации волокна. Осмоленное и гидрофобизированное волокно по массопроводу вдувается в трубу-сушилку и там высушивается до влажности 10%. Сушка осуществляется дымовыми газами, которые от энергетической установки дымососом нагнетаются в сушилку. Длина трубы сушилки - 120 м, диаметр трубопровода - 2650 мм. В четырех циклонах волокно отделяется от агента сушки, движется по спирали трубопровода и разгружается шлюзовыми питателями на два спаренных шнековых транспортера. В трубопроводе сушилки и после шлюзовых затворов установлены датчики искры. В случае обнаружения искрения в шнековых конвейерах и трубопроводах подачи волокна в сепараторы предусмотрено тушение (заливка) возгорания. После шнековых конвейеров установлены переключающие заслонки. В потоке волокна до сепаратора двумя инфракрасными установками измеряется влажность волокна. Для отделения комочков волокна и клея от искр, а также для поддержания волокна в горячем состоянии между сушилкой и формовочно-прессовым участком предусмотрены два сепаратора.
Высушенное волокно поступает в систему воздушной сепарации. В сепараторы оно загружается сверху. На входе в сепаратор волокно разрыхляется зубчатыми валками и поступает внутрь корпуса. Отбор кондиционной древесноволокнистой массы проводится через верхний патрубок сепаратора, а по бокам сепаратора продувается нагретый воздух, потоки которого обеспечивают изменение траектории полета частиц. Воздух нагревается до 80°С при прохождении через паровой калорифер. Тяжелые частицы опускаются в низ сепаратора и конвейером через шлюзовой затвор отправляются в бункер отходов. Кондиционное волокно от сепараторов двумя вентиляторами направляется к участку формирования ковра, волокно в двух циклонах отделяется от воздуха и через шлюзовые затворы поступает в спаренный шнековый конвейер, загружающий древесно-волокнистую массу в бункер-дозатор формирующей машины. В трубопроводах перед сепараторами и в крышках шнековых конвейеров предусмотрены противовзрывные мембраны. Выхлопной воздух из циклонов направляется на поддув в сепараторы. В трубопроводах подачи волокна в спаренный шнековый сборный конвейер размещены две инфракрасные установки измерения влажности. В технологической схеме предусмотрена установка систем обнаружения искры перед входом в циклоны и после вентилятора, подающего горячий воздух к сепараторам.
Формовочно-прессовый участок. Кондиционное волокно после сепарации направляется в спаренный шнековый транспортер, состоящий из транспортного лотка, в котором навстречу друг другу вращаются два шнека, установленные на одной оси. Шнековый транспортер оснащен сигнализатором уровня заполнения и форсунками для пожаротушения. Из шнекового транспортера волокно поступает в загрузочный короб, в котором равномерно распределяется по ширине бункера-дозатора формирующей машины. Волокно выгружается в переднюю часть бункера-дозатора (его объем 110 м3), на ленту донного конвейера, и с помощью цепного конвейера со скребками выравнивается высота слоя волокна, излишки которого отгребаются в направлении задней стенки бункера. Скорость донного конвейера регулируется в зависимости от толщины и плотности выпускаемых плит. На выгрузке из бункера-дозатора наклонно установлены 14 дисковых разгрузочных валиков, которые разрыхляют и выгружают волокно из бункера в настилочную головку машины для настилания ковра из волокна.
Бункер-дозатор оснащен системой измерения и регулирования уровня заполнения и форсунками пожаротушения. В настилочной головке установлены зубчатые валики, предназначенные для интенсивного разрыхления и точного распределения волокна. Наклон и высота настилочной головки регулируются при помощи электроприводных подъемных шпинделей. Волокно настилается на движущийся формирующий конвейер, ширина настилания - 2700 мм.
Для выравнивания сформированного волокнистого ковра и обеспечения равномерной насыпной плотности предназначен эгализатор, состоящий из зубчатых валиков, регулируемых по высоте с помощью электроприводных подъемных шпинделей с контролем позиции. Настилочная машина формирует непрерывный волокнистый ковер на подвижной ленте формирующего конвейера. Устройство взрывозащиты позволяет в случае взрыва быстро разгрузить давление за счет мембран, разрушающихся на заднем фронте бункера формирующей машины. Формирующий ленточный конвейер длиной 64,6 м предназначен для приемки настилаемого древесноволокнистого ковра и транспортировки его к горячему прессу. Конечная часть конвейера - подвижная, она обеспечивает возможность сброса (при необходимости) отрезка ковра в бункер приема волокна бракованного ковра (воронка для настельного брака).
Следом за формирующим ленточным конвейером установлен промежуточный ленточный конвейер длиной около 5 м, предназначенный для передачи ковра на стальную ленту горячего пресса ContiRoll. Сформированный ковер взвешивается на ленточных весах, его влажность определяется при помощи установки инфракрасного излучения, а насыпная плотность массы одного квадратного метра измеряется по ширине ковра прибором для измерения веса единицы площади. Система непрерывного измерения насыпной плотности ковра по ширине позволяет получать визуализацию поперечного и продольного профиля настилаемого ковра. Информация, поступившая от влагомера, используется при корректировке режима прессования.
Далее ковер поступает в непрерывный форпресс, предназначенный для уплотнения и упрочнения ковра. Гидравлическое давление и управление функциями подпрессовщика обеспечиваются гидростанцией. После подпрессовки ширина ковра увеличивается. Для обрезки кромок ковра до требуемого размера используется продольно-обрезная пила. Отрезанные излишки ковра возвращаются пневмосистемой в машину для настилания волокна. Металлодетектор (поисковая катушка), который установлен после пилы для обрезки продольных кромок, при обнаружении металлических включений в ковре дает сигнал для сброса ковра в приемный бункер волокна бракованного ковра. Это выполняется с целью предохранения стальной ленты горячего пресса от повреждений. В формовочно-прессовой линии имеется роторная распылительная установка для увлажнения ковра. В комплекте оборудования предусмотрен переносной пресс для склеивания лент формирующей линии.
Прессование плит производится в непрерывном гидравлическом прессе горячего прессования ContiRoll проходного типа. Для создания гидравлического давления и управления гидравлическими функциями пресса предусмотрена гидроустановка для пресса ContiRoll. Прессование плит выполняется между двумя бесконечными стальными лентами, движущимися на калиброванных роликах (стержнях) по нагревательным плитам пресса. Тепло от нагревательных плит пресса к стальным лентам передается движущимися стержнями, закрепленными в звеньях тяговых цепей верхнего и нижнего конвейеров. Стальные ленты ходят по движущимся стержням качения, что снижает силу трения при их движении и уменьшает износ лент. Номинальная длина нагревательных плит пресса - 55,3 м, ширина прессования - 2,55 м. Скорость прессования регулируется от 90 до 1100 мм/с в зависимости от толщины, типа выпускаемых плит, разных нюансов технологии. Плиты пресса нагреваются термомаслом с максимальной температурой в контурах термомасла около 250°С. На протяжении пресса предусмотрено пять регулируемых ступеней давления (вторичные контуры нагрева для пресса СontiRoll). Парогазовая смесь от пресса через местные отсосы-приемники отбирается системой отсоса выпара. Неочищенный газ охлаждается в вытяжных кожухах и трубопроводе неочищенного газа путем впрыскивания через форсунки оборотной воды до достижения точки насыщения, за счет чего предотвращаются отложения на стенках трубопровода от неочищенной парогазовой смеси. Через капельный охладитель отработанный газ отсасывается центробежным вентилятором.
Пресс оснащен установкой водораспылительного пожаротушения, которая «отвечает» за следующие зоны: вход в пресс, зону прессования, выход из пресса, верхний тепловой туннель, нижний тепловой туннель, шахту распределителя термомасла. В этих зонах установлены сигнализаторы и форсунки для тушения возгорания. Работа оборудования участка управляется из операторской. Готовая спрессованная плита непрерывной лентой выходит из пресса и подается на станцию обрезки и торцовки. Непрерывное полотно плиты с обрезанными продольными кромками по рольгангу подается к двухпильной диагональной пиле, расположенной над пильным столом. Диагональная пила предназначена для поперечной распиловки непрерывного полотна на заданные форматы. Предусмотрена сбрасывающая заслонка для коротких первых отрезанных кусков плит и образцов, предназначенных для проверки их характеристик в лаборатории. Обрезки плит сбрасываются на расположенную под столом транспортную ручную тележку.
Измельченные фрезами опилки и обрезанные кромки подаются системой пневмотранспорта на фильтр-циклон, в котором воздух отделяется от пильных отходов; через шлюзовый питатель опилки поступают в систему пневмотранспорта, а затем в бункер пильных отходов. Отработанный воздух направляется в систему воздухоуравнивания. Раскроенные по формату плиты по ускорительному рольгангу, расположенному за пильным столом, проходят через толщиномер, который осуществляет контроль толщины в семи точках по ширине плиты, и через ультразвуковой дефектоскоп, определяющий наличие в изготовленном материале дефектов (вздутий, расслоений и др.).
Участок охлаждения и штабелеукладки. После раскроя плита транспортируется на весы ременным транспортером, под которым установлены весы. По результатам взвешивания выдается информация по отклонению веса плиты от установленной нормы (недовесу или перевесу). За ременным конвейером расположен участок отбраковки с оборудованием для образования пакетов. Участок предназначен для транспортировки плит в продольном направлении, формирования пакетов плит и вывода из потока бракованных плит путем приподнимания одной стороны ременного конвейера. Кондиционная плита продольным рольгангом загружается на полку первого веерного кантователя, при повороте ротора веера на 180° плита перемещается по рольгангу во второй веерный кантователь, после поворота ротора второго веерного кантователя на 180° рольгангом плита перегружается на полку третьего веерного кантователя, а после поворота ротора третьего веерного кантователя на 180° рольгангом выполняется выгрузка плиты. Веерный охладитель используется для охлаждения плиты и снятия остаточных напряжений в ней. Общее количество полок на полуокружности - 80. После веерных охладителей рольгангом плита перемещается на пакетообразующий стол, на котором можно сформировать пакеты максимальной высотой 260 мм. На этом столе предусмотрено выравнивание пачек по ширине и длине. Захватной ходовой тележкой, расположенной над пакетообразующим столом, сформированный пакет забирается для формирования большого штабеля из отдельных пакетов. Максимальная высота формируемого штабеля - 4 м.
Максимальный вес перемещаемого пакета - 2,85 т. На участке имеется рама с присосками для загрузки обкладочных (защитных) плит.
Автоматизированный участок выдержки плит. Прием штабелей плит с установки охлаждения и штабелирования, их транспортирование на выдержку, складирование, выдача и перекладка штабелей плит, доставка штабелей на шлифовальную линию выполняются складскими транспортными средствами типа SFG (5201, 5202), состоящими из двух базисных тележек со спутниковыми парами. Базисная (траверсная) тележка предназначена для приема и поперечной транспортировки двух спутников.
Штабели складируются рядами на подштабельные места. Каждое подштабельное место состоит из трех стоек с плоской широкой опорной поверхностью. Для нормального функционирования системы передвижения необходимо расстояние между штабелями 300 мм, а между рядами 500 мм. Две механические, независимые, одинаковые по конструкции спутниковые тележки со штабелями перемещаются по рельсам в продольном направлении между стойками. Спутники заезжают на базисную (траверсную) тележку с поперечным направлением движения и на ней перемещаются к любому заданному ряду. Требуемые штабели плит при помощи спутниковых тележек перемещаются на базисную тележку и транспортируются на продольный цепной конвейер, расположенный на входе шлифовальной линии.
Участок шлифования и форматной обрезки плит. Штабели плит перемещаются на подштабельный цепной транспортер и подштабельный рольганг, предназначенные для транспортировки штабелей плит в продольном направлении, и передаются на гидравлическую подъемную платформу загрузочной станции. Она обеспечивает пошаговый подъем штабеля плит для загрузки шлифовальной линии. Над подъемной платформой установлена загрузочная станция, которая сдвигает плиты со штабеля в продольном направлении для загрузки шлифовальной линии.
Плита входит в роликовое приводное подающее устройство и поступает на рольганг, транспортирующий плиты в продольном направлении. На рольганге с помощью присосной тележки защитные плиты снимаются и транспортируются к месту для формирования штабеля защитных плит. Рольганг подает плиту для шлифования в комбинацию шлифовальных станков, состоящую из калибровального станка с четырьмя головками, предназначенного для грубого шлифования плиты с двух сторон до точной толщины, и станка для тонкого шлифования с четырьмя головками, предназначенного для получения требуемой чистоты верхней и нижней поверхностей плиты. Передача плит от калибровального станка к станку тонкого шлифования выполняется по рольгангу.
После станка тонкого шлифования предусмотрена контрольная станция для визуального контроля при помощи зеркал качества верхней и нижней сторон плит без остановки потока плит. После контроля качества поверхности шлифованная плита по рольгангу транспортируется к продольно-обрезной пиле для обрезки продольных кромок. После обрезки плиты транспортируются по рольгангу к пакетообразующему столу для дальнейшего раскроя, и во время транспортировки их поверхности очищаются от пыли струей сжатого воздуха, который подается через специальное сопло, установленное над рольгангом.
Затем плиты поступают на пакетообразующий стол с центрирующим устройством и механизмом подъема, на котором формируются пачки плит максимальной высотой 60 мм. Сталкивающим устройством в виде поперечной балки-толкателя, расположенной над пакетообразующим столом, пакет (или плита) подается к поперечно-обрезной и делительной пиле для обрезки плит по ширине и раскроя на заданные форматы. По рольгангу отдельные плиты или пакеты раскроенных плит перемещаются в поперечном направлении на угловую станцию, предназначенную для приемки плит/пакетов в поперечном направлении и передачи их в продольном направлении на рольганг.
В состав угловой станции входят рольганг поперечный и продольный плоскоременный конвейер. После угловой станции плита транспортируется в продольном направлении рольгангом, и во время транспортировки ее поверхности очищаются от пыли, нагнетаемой вентилятором высокого давления, струей воздуха, которая подается через сопло, установленное над рольгангом; частицы грязи отсасываются аспирацией. Далее плита поступает на станцию формирования штабелей. Станция состоит из подающего роликового устройства с верхним прижимным и нижним приводным роликом, пневматических центрирующих устройств для выравнивания плит по длине и ширине пачки, подъемных устройств, приподнимаемых ременных конвейеров.
Формирование пачек плит происходит на трех подштабельных рольгангах, расположенных в подъемной этажерке. Сформированные пачки плит тремя подштабельными цепными конвейерами транспортируются в поперечном направлении к передвижной тележке, на которой они перемещаются к подштабельному рольгангу для съема. Рядом со станцией формирования штабелей расположено устройство загрузки защитных плит. Пачка защитных плит ставится на это устройство вилочным погрузчиком. Для формирования пачки, предназначенной для ламинирования, устройство выдвигает нижнюю защитную плиту.
Передвижная тележка доставляет защитные плиты к местам формирования штабелей (пачек) плит. Передача отдельных защитных плит к подштабельным местам формирования штабелей (пачек) плит выполняется тремя подштабельными рольгангами. Основная часть плит транспортируется автопогрузчиком грузоподъемностью 5 т на участок выдержки перед ламинированием. Остальные плиты транспортируются к рольгангам на упаковку, затем на склад готовой продукции.
Участок ламинирования и упаковки плит. Управление линиями облицовывания автоматизировано. Автоматика управляет следующими операциями: перемещением плит и пакетов плит на линиях, укладкой декоративной пленки, подачей защитных панелей, укладкой на них ламинированных плит и перемещением пакетов ламинированных плит с помощью штабелирующего устройства на роликовые тележки.
Физическая, химическая и санитарно-экологическая лаборатории, расположенные в главном корпусе завода MDF, контролируют качество сырья и готовой продукции, соблюдение санитарно-гигиенических норм, проверку и наладку систем автоматики.
Энергетический центр на ПДК «Апшеронск»
Для организации замкнутого цикла производства предприятием приобретен энергетический центр, который будет вырабатывать тепло для производства плит MDF (кроме прессов ламинирования), а также для отопления, вентиляции и горячего водоснабжения. Мощность энергоцентра - 74 МВт (63,64 Гкал/ч).
В качестве теплоносителей будут использоваться дымовой газ (380°С), термомасло (280°С), насыщенный пар под давлением 16 бар. Топливо - измельченные отходы производства плит MDF (кора, отходы сортировки, мойки щепы, насыпной брак, отходы, образующиеся при сепарации волокна, отходы обрезки), отходы, которые образуются при шлифовке и раскрое плит (опилки и обрезки), а также природный газ.
Рынок ждет продукцию «Апшеронска»
Кризис 2008 года заставил приостановить строительство завода по изготовлению плит MDF и ламинированных напольных покрытий до лучших времен. К реализации проекта вновь приступили в 2010 году, и сейчас работы идут полным ходом. Общий объем инвестиций в проект составляет более 9 млрд руб. Проектная мощность будущего предприятия предусматривает производство 300 тыс. м3 плит MDF в год, причем оборудование позволяет производить плиту толщиной от 3 до 40 мм любого формата.
25% произведенной продукции будут использоваться для собственного производства ламинированных напольных покрытий. Руководство компании отмечает, что завод будет ориентироваться на запросы покупателей и изготавливать ламинат именно того класса, который будет востребован рынком. По информации руководителя отдела развития «ПДК Апшеронск» Ирины Дегтеревой, интерес к продукции, которую будет выпускать предприятие, проявляют не только ближайшие потенциальные потребители, но и крупные мебельные фабрики Центральной России. Сейчас активно изучается рынок напольных покрытий в России и его перспективы, результаты этой работы найдут отражение в формировании концепции производства конечного продукта и сбытовой структуры.
Александр КЕДРОВ