Что такое «забирка на шмыгу». Часть 1
Что такое «забирка на шмыгу»
Производство клееного щита. Часть 1
Производство клееного щита. Часть 2. Качество - сумма многих слагаемых
Производство клееного щита. Часть 3
Производство клееного щита. Часть 4. Строгание (плоское фрезерование)
Производство клееного щита. Часть 5
На протяжении веков деревообработчики всего мира пытаются найти оптимальное решение задачи превращения бревна, у которого, как известно, круглое сечение, в прямоугольные доски и бруски. Поиски решения этой задачи чем-то похожи на поиски квадратуры круга, над загадкой которой с давних пор бьются математики.
Выпилить из бревна плиту или щит большой ширины невозможно. Прежде всего потому, что деревьев с необходимым диаметром ствола вырастает мало. Кроме того, щит из цельной доски неминуемо покоробится при сушке или в процессе достижения эксплуатационной влажности.
Древесные плиты
Плиты на основе древесной стружки или древесных волокон, спрессованных со связующим, появились в середине прошлого века: первый завод по производству ДСП был пущен в Германии в 1942 году, а к промышленному выпуску древесно-волокнистых плит сухого способа производства (MDF) впервые приступили в США в 1965 году. До этого деревообрабатывающая промышленность использовала древесно-волокнистые плиты мокрого способа производства. Их появление относится к 1924 году, когда американский инженер Вильям Мэйсон изобрел машину для получения древесного волокна. Первые древесно-волокнистые плиты, изготовленные им в 1929 году на заводе в г. Лорел, в штате Миссисипи, были названы «мазонит». Промышленное производство клееной фанеры началось в конце XIX века с использованием шпона лущеной и строганой фанеры.
До появления всех этих плитных и листовых древесных материалов в деревообработке и мебельном производстве использовались щиты пустотелые, щиты переклейные и щиты дощатые различной конструкции.
Сегодня пустотелые щиты применяются преимущественно при изготовлении полотен межкомнатных дверей и представляют собой рамку с заполнением (склеенные или не склеенные по кромкам бруски, решетки из поставленных на ребро отрезков ДВП или клееной фанеры, сотовое бумажное заполнение и т. п.). Выпускаются также полноформатные безрамочные плиты с сотовым бумажным заполнением, подлежащие раскрою на детали, кромки которых затем усиливаются и облицовываются на станках по специальной технологии.
Промышленное производство переклейных щитов и столярных плит со средним слоем из склеенных или не склеенных брусков, облицованных с двух сторон клееной фанерой, ДВП или шпоном, сегодня почти исчезло.
Однако во всем мире существует множество предприятий, поставляющих на рынок дощатые щиты, состоящие из брусков, склеенных кромками на гладкую фугу. Любопытно, что в начале прошлого века в России такое соединение называлось «забирка на шмыгу». Сегодня материал, в котором используется подобное соединение брусков, носит название «клееный щит».
Проблемы клееного щита
Наружная облицовка и подоблицовочные слои на пластях столярных плит служат для их упрочнения, выравнивают поверхность и предотвращают резкие изменения влажности материала. Кроме того, для среднего слоя столярной плиты могут использоваться рейки из низкосортной хвойной древесины и даже мягких лиственных пород, в том числе полученные из отходов лесопильного и фанерного производства.
В отличие от столярной плиты, клееный щит набирается только из брусков, полученных в результате раскроя пиломатериалов высших сортов. Кроме того, для предотвращения поперечного коробления клееного щита недопустимо применение в нем брусков с тангентальным расположением годичных слоев. А это заставляет производителей щита вести предварительный отбор пиломатериалов или организовывать собственное лесопильное производство, на котором использовались бы специальные способы раскроя круглого леса, обеспечивающие максимальный выход пиломатериалов с радиальным направлением годичных слоев с наклоном к пласти не более 60°.
Щиты с брусками полурадиального напила - с углом наклона годичных слоев до 45° - выпускаются в небольших объемах.
Требования к качеству поверхности готового клееного щита определяются ГОСТом 16371 «Мебель. Общие технические условия». Однако поставщики щитов должны ориентироваться на требования конкретного покупателя, а они могут сильно отличаться от этого ГОСТа.
Но существуют и некие общепринятые требования, которые подлежат обязательному выполнению по умолчанию. Так, влажность брусков в щите не должна превышать 8% и в отдельных брусках не может отличаться больше чем на 1%. Не допускаются продольная и поперечная покоробленность, крыловатость брусков, а в щитах - темные клеевые фуги. Если допускается заделка сучков и других мелких дефектов на поверхности, то для этого используются только специальные круглые пробки, имитирующие сучок, или пробки-«лодочки», но не пробки, высверленные из других брусков. Сучки должны быть равномерно распределены на поверхности щита. Не допускается изготовление щита из брусков, отличающихся по цвету, - это считается браком. Пласти щитов должны быть шлифованными, точно обрезанными по формату, а их ребра смягчены или снабжены небольшой фаской.
Отдельно обсуждается с покупателем возможность применения в щитах брусков, срощенных по длине на зубчатый шип. В любом случае, если с клиентом не оговорено иное, зубцы должны выходить на кромку, не допускаются пустоты у их вершин. Причем в процессе изготовления необходимо следить за тем, чтобы рисунок текстуры у отдельных сращиваемых элементов максимально совпадал.
Проблемы нехватки и качества сырья
Клееный щит на российских предприятиях может изготавливаться из древесины березы, дуба, бука, сосны, ели и пихты, есть спрос и на клееный щит из черной ольхи и лиственницы. Но с заготовкой и доставкой древесины к месту производства щита немало проблем, многие из которых общеизвестны: неудовлетворительное лесоотведение, плохие лесовозные дороги и т. д.
Есть и такая проблема - у древесины березы, а также дуба и бука, заготавливаемых во многих районах страны, красноватый оттенок, а на срезе многочисленные цветные пятна, что недопустимо в готовом изделии - клееном щите. Кроме того, для изготовления щита требуется сырье нулевого сорта, и производители клееного щита вынуждены выдерживать жесткую конкуренцию с производителями клееной фанеры в борьбе за поставки такого сырья.
Все это неминуемо заставит производителей клееного щита «уходить все дальше в лес», чтобы отбирать сырье не только на стадии лесопиления, а еще на лесосеке.
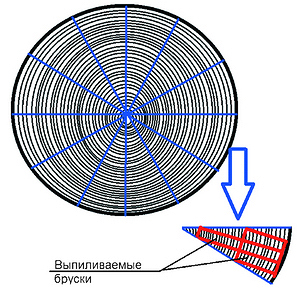
Рис. 1. Схема постава для секторно-радиального («голландского») способа раскроя бревна на заготовки
Количественный (объемный) выход пилопродукции из круглого леса (Q) рассчитывается как отношение объема полученных пиломатериалов (А, м3) к объему сырья, затраченного на их изготовление (B, м3), выраженное в процентах:
На практике количество основной пилопродукции, получаемой в процессе лесопиления, составляет 60-70% объема бревен и во многом зависит от их диаметра. При этом из бревен может быть получено всего 30-35% радиального пиломатериала, пригодного для производства клееного щита, то есть не более 0,24 м3 из одного кубометра кругляка.
При дальнейшей обработке с учетом потерь на торцевание, выторцовывание дефектов, пропилы, плоское фрезерование и другое в готовом щите остается не более 50% этого объема. То есть полезный выход клееного щита из одного кубометра круглого леса не превышает 0,12 м3!
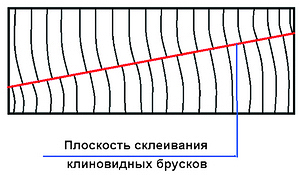
Рис. 2. Схема склеивания обработанных брусков клиновидного сечения, полученных сразу после раскроя бревна
Впрочем, существуют способы повышения выхода радиальных пиломатериалов. Наибольший выход брусков с радиальным расположением годичных колец обеспечивает секторно-радиальный способ раскроя бревен, со времен Петра I иногда называемый голландским (рис. 1). Но общий полезный выход материала при таком способе все равно весьма низок из-за необходимости превращать заготовки трапециевидного сечения в прямоугольные. Однако некоторые производители нашли возможность увеличить выход прямоугольных брусков за счет склеивания полученных клиновидных заготовок с последующим раскроем по толщине и ширине на бруски нужного сечения (рис. 2). Оригинальность такого решения состоит в том, что заготовки брусков будущего клееного щита выполняются из двух симметрично склеенных продольных секторных досок радиального распила. При этом обеспечивается оптимальный наклон структурных колец древесины относительно плоскости доски, близкий к 90°, а направления радиусов этих структурных колец противоположны друг другу. Благодаря этому возникающие естественные внутренние напряжения в одном слое компенсируются за счет противоположно направленных внутренних напряжений сопрягаемого.
Потребители и цены
Существует ли рынок для поставки клееного щита? Это первый вопрос, который должны задать себе те предприниматели, которые собираются организовать производство этого материала.
Да, спрос на клееный щит сегодня есть. Причем в основном в Европе, где покупатели все больше заботятся об экологической чистоте приобретаемой продукции и не очень-то доверяют уверениям производителей древесно-стружечных плит о полной безопасности этих изделий. Исторически сложилось, что основными поставщиками клееного щита из хвойной древесины на европейский рынок являются скандинавские страны, причем первенство принадлежит Дании, которая получает пиломатериалы для производства этого материала из Финляндии и Швеции.
Пик спроса на этот клееный щит наблюдался в Европе в начале 1990-х, когда была мода на мебель в скандинавском стиле - изготовленную из необлицованной древесины с множеством сучков. В те годы, когда курс рубля к иностранной валюте был исключительно выгодным для экспортных поставок, на многих отечественных лесопильных и деревообрабатывающих предприятиях активно создавались цеха по производству клееного щита. Однако вскоре из-за гиперинфляции и роста внутренних цен экспорт пилопродукции и клееного щита перестал быть выгодным, множество лесопильных и деревообрабатывающих предприятий остановились, остановился и процесс создания новых производств. В результате европейский рынок клееного щита был для нас потерян.
Кроме того, сегодня цена радиальных пиломатериалов на российском рынке едва ли не превышает цену готового клееного щита в Европе и у российской продукции просто нет шансов на европейском рынке. Тем более что в последние годы европейские потребители все в больших объемах импортируют клееный щит из Китая.
Цены в Европе на весь пиломатериал и изделия деревообработки сейчас очень низкие. Причем, как и раньше, их диктуют скандинавские предприятия, более чуткие к рынку и более гибкие, чем российские. Но и им сегодня приходится сокращать объемы выпуска и даже закрывать целые заводы.
Российский рынок клееного щита также ограничен. В первую очередь из-за того, что основные его потребители, мебельные предприятия, в большинстве своем ориентированы на производство изделий из древесно-стружечных плит и не обладают технологиями и техникой для изготовления мебели из массива, в частности, оборудованием для отделки.
Кроме того, российские цены по многим позициям уже достигли уровня европейских или даже превышают их. Однажды поднявшись, они почти никогда, в силу рыночных механизмов, не снижаются. В результате оказывается, что, к примеру, черновую мебельную заготовку и клееный щит из дуба отечественным предприятиям выгоднее покупать в Канаде, а не в России.
Руководителям предприятий, имеющим намерение организовать производство клееного щита, следует прежде всего оценить потенциал возможного рынка сбыта, перспективы изменения цен на эту продукцию и определить стабильные источники получения качественного сырья по выгодным ценам. Расчеты специалистов показывают, например, что экономически выгодным будет производство клееного щита в объеме более 10 тыс. м3 в год, для чего может понадобиться переработка не менее 80 тыс. м3 круглого леса.
В следующем номере журнала мы расскажем о разных технологиях изготовления клееного щита.
Андрей ПЕТРОВ, компания «МедиаТехнологии»,
по заказу журнала «ЛесПромИнформ»