Производство клееного щита. Часть 4
Рубрика Деревообработка
Производство клееного щита
Часть 4. Строгание (плоское фрезерование)
Что такое «забирка на шмыгу». Производство клееного щита. Часть 1
Производство клееного щита. Часть 2. Качество - сумма многих слагаемых
Производство клееного щита. Часть 3
Производство клееного щита. Часть 5
Под строганием понимается обработка поверхности древесины со снятием ее слоя определенной толщины (стружки) ножом, перемещающимся параллельно поверхности (например, рубанком), или сострагивание шпона в шпонострогальном станке.
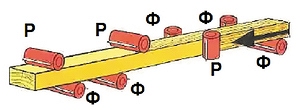
Рис. 1. Вариант расположения суппортов в
четырехстороннем продольно-фрезерном станке:
Ф – фуговальные; Р – рейсмусовые
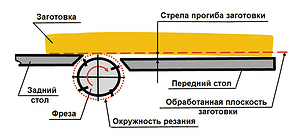
Рис. 2
Фрезерные станки, обрабатывающие плоскую поверхность и также снимающие слой древесины, исторически тоже получили название «строгальные» или «станки строгальной группы», хотя в них и используется фрезерование, коренным образом отличающееся от строгания. К ним относятся станки фуговальные, рейсмусовые и четырехсторонние строгальные, и правильное их наименование продольно-фрезерные.
Станки фуговальные (названы по аналогии с фуганком) предназначены для выравнивания поверхности детали с целью достижения ее прямолинейности и плоскостности - создания базы для дальнейшей обработки. Станки рейсмусовые (по аналогии с мерительным инструментом - рейсмусом) предназначены для получения деталей заданной толщины. Станки четырехсторонние оснащаются набором суппортов, работающих по принципу фугования и рейсмусовой обработки. Аналогичные им станки фуговально-строгальные дополнительно оснащаются удлиненным передним столом и горизонтальным фуговальным суппортом (рис. 1). При обработке изогнутая (покоробленная) деталь располагается на этом столе так, чтобы ее «горб» был направлен вверх (рис. 2), а положение стола по высоте регулируется так, чтобы величина съема материала при фрезеровании несколько превышала величину покоробленности. При продвижении вручную детали по столу к фрезе деталь не разгибается, ее обработанный участок укладывается на стол за фрезой; далее деталь захватывается роликами механизма подачи. Свободный конец заготовки всегда остается в контакте с передним столом. В результате достигается строго прямолинейное перемещение обрабатываемой детали, и на нижней пласти образуется идеально ровная плоская поверхность. Проверка качества обработки после фугования иногда выполняется следующим образом: пласти двух только что обработанных заготовок притираются друг к другу и на образовавшийся стык наливается вода. Если она не проникает между деталями, значит обработка сделана качественно. Вызывает удивление, что на большинстве предприятий, оснащенных фуговально-строгальными станками, их часто используют не по назначению.
Прямолинейность брусковых заготовок, полученных в результате четырехсторонней обработки, определяет качество последующего склеивания щита и бруска: если прямолинейность обеспечена, не будет риска образования непроклеенных фуг и коробления изделий. При отсутствии фуговально-строгального станка базовую поверхность заготовки можно создавать на отдельном фуговальном станке. Если операция фугования не проводится вообще, то покоробленные заготовки распрямляются механизмом подачи четырехстороннего станка и после обработки снова принимают исходную криволинейную форму, которая не может быть исправлена при склеивании из-за недостаточного усилия пресса. Если пресс все же в какой-то мере устраняет покоробленность деталей, то в изделии создаются внутренние напряжения, которые как раз и приводят к короблению всего изделия.
К качеству склеиваемых поверхностей деталей, обработанных на продольно-фрезерных станках, предъявляются довольно высокие требования. На них не должно быть не только таких дефектов, как мшистость, задиры и им подобные, но и явно выраженной кинематической волны. Поэтому ножевые головки после установки на них ножей желательно прифуговывать во избежание формирования рельефа поверхности одним, наиболее выступающим ножом.
Дереворежущий инструмент весьма чувствителен также к ударным повреждениям, особенно при обработке склеенных на зубчатый шип деталей с выступившими каплями отвержденного клея, отличающимися повышенной твердостью. Поэтому не рекомендуется без замены инструмента обрабатывать на одном станке партии цельных и склеенных деталей. Желательно даже при возможности использовать для обработки этих партий отдельные четырехсторонние станки.
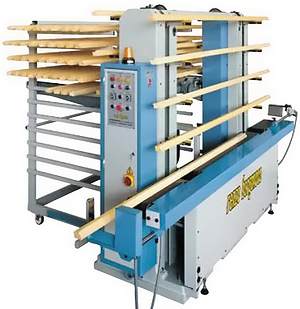
Рис. 3
Большое значение имеет и отсутствие «схватывания» заготовок в четырехстороннем станке - специфического дефекта обработки, выражающегося в появлении на нижней пласти, на некотором расстоянии от торца, параллельного ему полукруглого углубления. Этот дефект чаще всего возникает из-за неправильной настройки прижимов, слишком большого расстояния между задней частью опорного стола и ножевой головкой или неравномерной подачи заготовок, останавливающихся в зоне обработки. При его появлении приходится отрезать торцы заготовок, что приводит к необходимости дополнительной технологической операции, требующей применения отдельного оборудования, и к повышенному расходу отборного материала.
После обработки на строгальных станках должны быть исключены и механические повреждения простроганных деталей. Рабочий, укладывающий детали в стопу, должен относиться к ним бережно, что делается не всегда. Поэтому при больших объемах производства желательно устанавливать за четырехсторонним станком автоматический укладчик, обеспечивающий формирование стопы с прокладками или без них (рис. 3).
В процессе строгальной обработки и при укладке готовых деталей проводится их дополнительная сортировка по расположению годовых слоев. Уложенные в стопу детали передаются на участок склеивания. Склеивание следует выполнять в максимально короткий срок во избежание изменения влажности и коробления деталей.
Нанесение клея
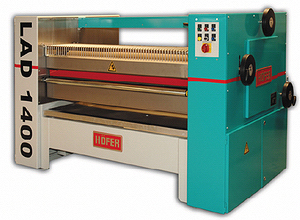
Рис. 4. Станок вальцовый клеенаносящий
двухсторонний
Склеивание клееного щита или клееного бруска из отдельных, обработанных на двухстороннем строгальном или четырехстороннем станке деталей, может выполняться холодным способом или в устройствах, обеспечивающих прогрев клеевого шва, что ускоряет процесс и повышает производительность. Отрезок времени между фрезерованием деталей и их склеиванием должен быть максимально коротким, чтобы избежать изменения влажности заготовок и их коробления.
Собственно склеиванию предшествует нанесение клея на одну из пластей брусков, которые будут составлять клееный щит, или на кромку брусков для клееного бруска. Соответственно различаются и клеенаносящие устройства: универсальные, ручные, одно- и двухсторонние горизонтальные - для нанесения клея на пласть (рис. 4) и односторонние вертикальные - для нанесения клея на кромку.
Использование устройства того или иного типа определяется требуемой производительностью. Ручные устройства применяются при небольших объемах производства, но они не могут обеспечить равномерный расход наносимого клея, что часто сказывается на качестве готовых изделий («голодная» склейка, выступание излишков клея и т. п.). Стационарные устройства с ручной подачей используются при средней производительности участков склеивания, а автоматические и полуавтоматические, оснащенные подающим устройством,
- в составе линий для склеивания.
Подбор брусков
Вне зависимости от применяемого способа склеивания - холодного или горячего - все детали желательно еще до нанесения клея предварительно рассортировать по наклону годовых колец в их древесине, а детали, предназначенные для изготовления клееного щита, - еще и по расположению допустимых сучков в отдельных брусках и расположению этих брусков в склеиваемом щите. Сучки в готовом изделии - склеенном щите - должны быть расположены максимально равномерно и «красиво». В искусстве есть понятие равновесности композиции, которое применимо и к подбору «картинки», которую создает расположение сучков на пласти щита. Иногда достаточно всего лишь поменять местами пару брусков, чтобы эта картинка, как говорят, «встала на место». Бруски одновременно поворачивают вокруг своей оси так, чтобы удалось получить после склеивания изделия высшего сорта: например, сорта А/Б, а не Б/Б, к которому приходится относить изделие из-за невнимательности оператора. Оператор должен также постоянно следить, чтобы в щиты не попадали бруски, сильно отличающиеся по цвету от остальных. Поэтому на его рабочем месте всегда должен быть запас дополнительных брусков разного цвета и текстуры, которые он мог бы использовать при подборе щита, не отвлекаясь на поиск бруска нужного цвета. Вот почему так важно было на всех этапах изготовления проводить постоянную сортировку брусков.
Следует понимать, что от подготовки оператора, его ответственности и отношения к работе в основном зависит экономика всего производства клееного щита и клееного бруса, а также имидж предприятия. При том же расходе материала и тех же трудозатратах только за счет правильного подбора брусков можно добиться повышения сорта, качества готовой продукции и, соответственно, ее цены, а стабильность подбора рисунка текстуры щитов и материала клееного бруска делает продукцию более привлекательной для потенциальных покупателей, упрощая и удешевляя ее сбыт.
Поэтому кандидатура оператора для набора склеиваемых изделий, качество его обучения и воспитание в нем чувства ответственности имеют для предприятия немалое значение.
Склеивание
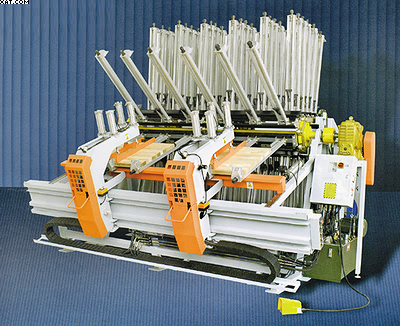
Рис. 5. Вайма веерная
Склеивание деталей холодным способом в щит или брус выполняется в ваймах разного типа: в составленных из независимых секций, в вертикальных, горизонтальных - настольного типа или многоярусных, или в веерных (рис. 5). Сжатие деталей и их выдержка под давлением до отверждения клеевого шва ведется винтовыми или гидравлическими устройствами, пневматические для этой цели не применяются из-за неминуемого просачивания воздуха из системы и больших потерь энергии.
При создании усилия сжатия, особенно в ваймах с винтовым зажимом, необходимо обеспечивать равномерный шаг зажимных устройств и добиваться одинаковой величины усилия сжатия по всей длине склеивания. В противном случае в зоне клеевых фуг, сжатых с недостаточным усилием, возможно образование непроклея. Склеиваемый щит или брусок должны быть особенно надежно сжаты в зоне их торцов, где из-за ускоренного испарения влаги трещины и непроклей образуются в первую очередь. Здесь не должно быть и деталей с дефектами строгальной обработки у торцов («схватывание»), так как даже при наличии хотя бы одного дефектного бруска в готовом склеенном щите или бруске придется отторцовывать всю деталь или выбраковывать ее целиком, что приведет к огромной потере материала. Склеиваемый щит должен быть надежно прижат и по пласти во избежание его поперечного коробления или смещения в щите брусков друг относительно друга, особенно изогнутых или покоробленных. Взаимное смещение брусков у торцов при холодном склеивании щита проявляется почти в каждой детали, что заставляет увеличивать припуски по длине брусков и приводит к перерасходу материала.
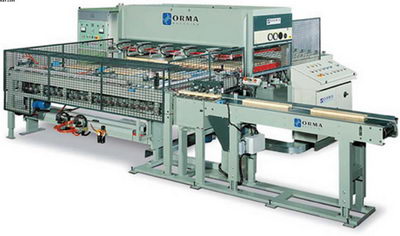
Рис. 6. Пресс однопролетный для склеивания клееного щита
Склеивание горячим способом, с прогревом клеевых швов ведется в прессах разной конструкции: веерных, позиционных с откидной верхней плитой, позиционных однопролетных с загрузкой по узкой или широкой стороне или на полуавтоматических линиях, построенных на основе проходных однопролетных прессов с ленточной загрузкой (рис. 6). Нагрев плит пресса может выполняться перегретой водой, паром, термомаслом или токами высокой частоты (ТВЧ). Однако в последние десятилетия нагрев плит прессов с помощью ТВЧ почти не используется, потому что такой вид нагрева требует очень точного выдерживания технологии: если влажность склеиваемых брусков отличается от необходимой или имеются отклонения в расходе клея, возможно появление так называемых прожогов - обугливания материала в зоне клеевых швов, деструкции клея и т. д. Кроме того, у генератора ТВЧ высокая стоимость, сопоставимая со стоимостью самого пресса, а создаваемое им излучение опасно для живых организмов и по воздействию сходно с радиацией. Такие генераторы также создают помехи радиосвязи и работе радиолокаторов, а поэтому подлежат специальной регистрации. В целях безопасности все оборудование с использованием ТВЧ должно закрываться специальным сетчатым экраном, который должен быть обязательно заземлен. Эффективность действия этой защиты должны периодически проверять надзорные органы с помощью специальных приборов, что требует постоянной оплаты.
Прессы с откидной верхней плитой используются на предприятиях средней мощности. Предварительно подобранные склеиваемые детали укладываются вручную на нижнюю плиту пресса. Затем верхняя плита опускается и включаются горизонтальные прижимные гидроцилиндры, расположенные между плитами, которые прижимают склеиваемый щит или сразу несколько уложенных комплектов деталей клееного бруса к упорной линейке, расположенной на нижней плите, в передней части пресса. После выдержки под давлением и отверждения клея верхняя плита откидывается автоматически. Часто эти прессы изготавливаются двухпозиционными: во время выдержки деталей под давлением на одной из позиций, на второй ведутся загрузка и выгрузка. Такие прессы могут оснащаться механизмами автоматической загрузки в виде ленты, проходящей вдоль нижней плиты, на которой остаются детали во время прессования, или механизмом загрузки с боковым толкателем в виде линейки, перемещаемой цепным механизмом. Такие прессы снабжены устройствами для регулирования давления сжатия и усилия прижима верхней плиты. Наибольшие размеры плит однопозиционного пресса обычно не превышают 3,0 х 1,2 м.
Однопролетные прессы для склеивания щита и бруса отличаются от обычных проходных прессов с ленточной загрузкой, используемых для облицовывания деталей, наличием упорной линейки и гидроцилиндров для бокового сжатия склеиваемых изделий.
В линии, построенной на основе такого пресса, подача предварительно отсортированных брусков осуществляется из горизонтального или вертикального магазина. На кромку или пласть брусков с одной стороны в автоматическом устройстве проходного типа наносится клей. После этого детали поступают на формирующий стол, на котором оператор набирает рисунок щита или контролирует набор пакетов прессуемого бруса, добавляя вручную бруски без нанесенного клея и обеспечивая разделение прессуемых пакетов. При склеивании бруса составляющие его отдельные бруски устанавливаются на ребро, что позволяет склеивать и брус ступенчатого сечения. В этом случае последовательность подачи брусков разной ширины на формирование пакета контролируется еще до нанесения клея. Сформированные пакеты ленточным загрузочным устройством задвигаются в пресс, одновременно из него выводятся уже спрессованные детали. Затем верхняя плита пресса опускается и включаются боковые прижимы, обеспечивающие необходимое сжатие прессуемых пакетов. После выдержки плиты размыкаются, и склеенные заготовки выносятся ленточным конвейером на приемный стол, после чего укладываются в стопу.
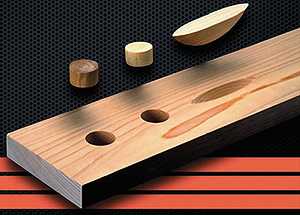
Рис. 7. Пробки для заделки дефектов
Такие установки используются на предприятиях довольно большой мощности. Но если предприятие производит массовую продукцию, например в объеме более 20 тыс. м3 клееных изделий в год, то наиболее эффективно использование прессов проходного типа. В состав таких прессов входят две параллельные горизонтальные обогреваемые плиты, верхняя состоит из отдельных секций. Детали с нанесенным клеем подаются транспортером в зону загрузки, где периодически действующий толкатель двигает их в поперечном направлении, создавая из деталей «ковер» и постепенно проталкивая его в пространстве между плитами. Необходимое давление прессования создается за счет трения между плитами и проталкиваемыми деталями. Период выдержки задается частотой работы толкателя и длиной канала, образованного плитами. При склеивании щита бруски подаются горизонтально, а при склеивании клееного бруса - вертикально, на кромке. Детали без клея, отделяющие друг от друга несклеиваемые между собой пакеты, подаются отдельно. Но на этой установке можно производить и непрерывное полотно клееного щита, для чего на выходе из пресса устанавливается суппорт, отпиливающий отрезки полотна нужной ширины. Такие линии позволяют производить щит длиной до 4,5 м или выполнять склеивание в несколько потоков. Их недостатком является невозможность подбора рисунка склеиваемого щита и производства клееного бруска ступенчатого сечения.
После склеивания в обогреваемых прессах детали должны длительное время выдерживаться в стопах до полного остывания и выравнивания их влажности, изменяющейся за счет влаги, содержащейся в нанесенном на них клее.
Заделка дефектов
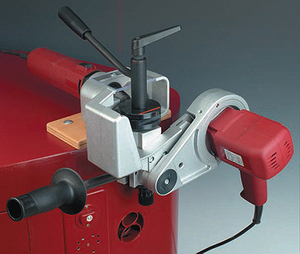
Рис. 8. Устройство для производства пробок-лодочек
Lamello Patchmaker (Швейцария)
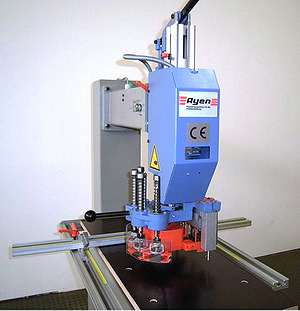
Рис. 9. Станок для выборки гнезд под пробки
На склеивание поступают бруски, несколько раз подвергавшиеся сортировке и контролю. Однако не исключается, что на них могут оставаться незначительные дефекты в виде отдельных дефектных сучков, смоляных «кармашков» и т. п. Заделку таких дефектов целесообразно проводить еще до механической обработки клееного щита или бруска, так как повторная обработка уже полностью обработанных изделий после заделки дефектов может привести к изменению заданных размеров изделия. Заделка после окончательной обработки (калибрования и форматной обрезки) проводится только в случае вскрытия новых дефектов.
Для заделки дефектов используются специальные цилиндрические деревянные пробки, изготовленные на специальных станках из сердцевинной части толстых сучьев и имитирующие здоровые сросшиеся сучки, а также одинарные и двойные овальные пробки-«лодочки» (рис. 7). Использование пробок, вырезанных цилиндрической пилой из бруска (что практиковалось ранее), в высококачественных изделиях недопустимо.
Пробки для заделки поставляются специализированными предприятиями. Но если необходимо использовать для заделки пробки-«лодочки», идеально соответствующие материалу используемой древесины, они могут быть изготовлены на предприятии самостоятельно, с использованием довольно простого устройства, формирующего их из заранее простроганных и напиленных из отходов используемой древесины брусков определенного размера, производимого компанией Lamello (рис. 8).
Сверление или фрезерование отверстий под пробки выполняются с помощью ручного механизированного инструмента либо специализированного оборудования.
Универсальный станок для выборки гнезд под пробки всех видов (рис. 9) оснащается суппортом, в составе рабочей головки которого имеется профильная фреза для формирования пазов под пробку-«лодочку» и три (или более) чашечных сверла для выборки отверстий под цилиндрические пробки разного диаметра. Оператор укладывает заготовку на стол станка и, поворачивая рабочую головку, подводит нужный инструмент к дефектному участку и опускает инструмент, который делает выборку необходимого отверстия. Пробки устанавливаются вручную, на клею.
Во избежание повреждений пласти других деталей в стопе выступающая часть пробки фрезеруется заподлицо с поверхностью с помощью специального ручного инструмента.
Заделка дефектов ведет к снижению сорта и, соответственно, цены изделий. Поэтому оператор не должен «переусердствовать», от его квалифицированных действий, как и от действий оператора на подборе деталей при склеивании, во многом зависит размер прибыли, которую рассчитывает получить предприятие.
Андрей ПЕТРОВ,
компания «МедиаТехнологии», по заказу журнала «ЛесПромИнформ»