Вохтожский ДОК
ДОК над Монзой: на магистральном пути
Вохтожскому деревообрабатывающему комбинату (Грязовецкий р-н Вологодской обл.) в декабре 2013-го будет 52 года. Переходя в залах музея истории этого предприятия от экспоната к экспонату, от стенда к стенду, я вглядывался в старые фотографии, в лица простых, скромных героев-тружеников, стоявших у истоков комбината, тех, кто в советские годы вывел его в число лучших предприятий Вологодчины. Пережив трудности перестройки и кризиса 2008-го, ООО «Вохтожский ДОК» (тогда - ООО «Монзенский ДОК») сегодня не только крепко стоит на ногах, но и уверенно смотрит в будущее, и гарантия тому - масштабное и поэтапное обновление комбината.
Подъезжая ранним июльским утром к станции Вохтога на проходящем скором, я обратил внимание на впечатляющие производственные площади со складами бревен, просторными корпусами и подъездными путями и сразу понял: это и есть Вохтожский ДОК. Позже мне рассказали, что основные и вспомогательные подразделения, многочисленные элементы инфраструктуры - склады, коммуникации и пр. - все это расположено на 51 га! Комбинат - градообразующее предприятие поселка, в котором насчитывается около 8 тыс. жителей, и почти каждый восьмой житель Вохтоги сегодня работает на предприятии.
В начале 1930-х годов здесь на базе сплавной конторы, располагавшейся на реке Монзе, был организован Монзенский леспромхоз, который стал крупнейшим в европейской части СССР. В 50-е годы прошлого века здесь начали развивать деревянное домостроение, и в 1962 году от леспромхоза было отделено самостоятельное хозрасчетное предприятие - Монзенский домостроительный комбинат, на котором изготавливались деревянные сборные щитовые дома, а также пиломатериалы, технологическая щепа и другие изделия из древесины.
Справа налево: генеральный директор Сергей
Кудрявцев, зам. генерального директора Дмитрий
Воробьев и финансовый директор Даниил Пычин
В начале 1970-х, когда на комбинате было запущено плитное производство на базе финского оборудования Rauma-Repola, он стал в СССР флагманом в выпуске древесно-стружечной плиты; чуть позже на основе импортного оборудования на предприятии стали импрегнировать бумагу, печатать на ней декоры и ламинировать пленкой собственную высококачественную плиту.
Переживший все социальные и экономические потрясения последних двух десятков лет комбинат сегодня претендует на место среди ведущих деревообрабатывающих предприятий Северо-Запада России.
Главное направление деятельности ООО «Вохтожский ДОК» - производство и реализация древесно-стружечных плит и ламинированных ДСП; в последние годы высокими темпами развивается производство клееных деревянных конструкций и домокомплектов из клееного бруса, кроме того, на комбинате изготавливают строганый погонаж и другие изделия из древесины. Устойчивости предприятия способствует выгодное местоположение. Выгодно оно как с точки зрения транспортной инфраструктуры - через поселок проходит одна из оживленных магистралей Северной железной дороги РЖД, совсем рядом (в 76 км) крупный железнодорожный узел Вологда, а большинство поставок древесного сырья осуществляется по местной (частной) Монзенской железной дороге с широкой колеей, - так и с точки зрения изобилия сырья: Вологодская область, как известно, один из самых лесных регионов Северо-Запада России.
Эффективное обновление
ООО «Вохтожский ДОК» - в числе самых востребованных на российском рынке поставщиков ЛДСП для мебельных предприятий. Среди его основных деловых партнеров мебельные производства южных и восточных регионов европейской части РФ, в меньшей степени - Северо-Запада Роcсии. До плановой остановки плитного производства, связанной с модернизацией линии изготовления ДСП (я приехал на комбинат, когда там заканчивались пусконаладочные работы на новой формующей машине), ежемесячный объем выпуска плиты составлял 15 тыс. м3, то есть 500 м3 в сутки.
В качестве технологического сырья используется осиновая, березовая и хвойная древесина, которая в Грязовецком районе в избытке и которую на комбинат поставляют многочисленные местные небольшие лесозаготовительные предприятия.
«Кроме того, для изготовления технологической щепы мы используем отходы лесопильного участка нашего деревообрабатывающего производства, а также обрезки горбыля, рейки и другие древесные отходы, которые нам привозят с ближайших пилорам, - говорит заместитель генерального директора по плитному производству ООО «Вохтожский ДОК» Николай Яковлев. - Всего же в месяц до остановки на модернизацию нам требовалось более 22 тыс. м3 техсырья. Для производства высококачественной ламинированной плиты на нашем предприятии есть все условия. Помимо подготовительного участка и основного цеха, который оснащен добротным оборудованием (достаточно назвать 19-этажный пресс непрерывного действия финской компании Rauma-Repola), у нас действуют цех ламинирования, в котором установлены четыре линии, а также цех импрегнирования, в котором мы варим смолу из концентрата и пропитываем бумагу для облицовки плит. Кроме того, для ламинирования плит используются и пленки, закупаемые у сторонних поставщиков, что позволяет обеспечить широкую гамму текстур. Качество плит мы постоянно проверяем в собственной лаборатории, а также в лаборатории ЗАО "Плитспичпром" (г. Балабаново), оно соответствует самым высоким мировым стандартам, и наши клиенты неизменно довольны поставляемым им продуктом».
Итак, налицо все признаки успешного предприятия: доступное и недорогое сырье, добротное оборудование, налаженная технологическая цепочка, устойчивый спрос на продукцию. Но, как известно, тот, кто почивает на лаврах, всегда оказывается в проигрыше. Производство должно развиваться, идти вперед, добиваться новых высот, чтобы успешно конкурировать с другими и укреплять свои позиции на рынке. Памятуя об этом, собственник Вохтожского ДОКа - Павел Васев и руководство комбината разработали и утвердили обширную программу модернизации производства, предусматривающую замену ряда основного и вспомогательного оборудования современным, более производительным. Курс на обновление был взят два года назад.
«Для оценки объемов модернизации и выработки конкретных рекомендаций - что именно надо поменять, в каком порядке и т. д. - были приглашены специалисты известной немецкой компании, - рассказывает главный инженер ООО «Вохтожский ДОК» Евгений Мельников. - При создании программы нами был изучен опыт плитных предприятий Швеции, Финляндии, Германии, тщательно рассмотрены и оценены варианты технологического оборудования лучших мировых производителей».
«Приняв во внимание прогноз специалистов, которые положительно оценили перспективы развития нашего сегмента рынка, что гарантирует устойчивый спрос на ламинированную ДСП вплоть до 2020 года, мы поставили перед собой цель: в ближайшее время выйти на суточный объем выпуска 850 м3, что позволит изготавливать более 250 тыс. м3 высококачественной ЛДСП в год, - говорит генеральный директор ООО «Вохтожский ДОК» Сергей Кудрявцев. - Конечно, реализация столь масштабной программы обновления предполагает внушительные объемы инвестиций. Так, на выполнение первого этапа модернизации - замену формующей машины - затрачено более 250 млн руб. Мы остановили свой выбор на оборудовании известного мирового производителя - компании Dieffenbacher. Строго в оговоренные сроки новая машина была поставлена на наше предприятие, и опытные немецкие специалисты из Dieffenbacher совместно с нашими сотрудниками приступили к монтажу и наладке новой формашины. В июле был осуществлен пробный пуск линии с новой формашиной, изготовлена первая плита. Вскоре мы планируем выйти на устойчивый выпуск плит и затем будем постепенно наращивать объем. И в том, что это будет именно так, мы полностью уверены».
Уверенность генерального директора комбината в успехе разделил и руководитель группы немецких специалистов, занимавшихся отладкой оборудования перед его пуском, Ханс Кёхерт. Мне удалось немного поговорить с ним, буквально на минуту оторвав его от важного дела. «Наша компания давно производит отличное оборудование, и установка новой формующей машины, безусловно, обеспечит предприятию в Вохтоге работу на новом качественном уровне», - сказал г-н Кёхерт.
Забегая несколько вперед в своем рассказе о комбинате (ведь я был на предприятии в середине июля), скажу: все идет по плану, именно так, как сказал Сергей Викторович, обновленная линия уже выдает готовую продукцию и радует производительностью. А на моем рабочем столе на видном месте лежит квадратный фрагмент ДСП, выпиленный из той самой - первой пробной плиты.
«Компания Dieffenbacher также поставила и смонтировала новое автоматическое оборудование на участке приготовления связующего: клеесмесители, дозаторы, систему охлаждения, - говорит Евгений Мельников. - Теперь за всеми процессами на этом важном участке технологической цепочки следит электроника, а это значит, что за качество связующего можно быть спокойным».
Сегодня на комбинате полным ходом идут работы по реализации следующего этапа программы модернизации - создания нового комплекса для сушки стружки.
«Это также очень важный шаг вперед в развитии нашего предприятия, - отмечает генеральный директор. - Действующее сушильное оборудование устарело и морально, и физически. Мы подписали контракт на изготовление и поставку сушильной установки с германской компанией Buttner - дочерним предприятием известного концерна Siempelkamp. Мощности новой сушилки рассчитаны на испарение 30 т воды в час. Для сравнения: на том оборудовании, которое мы эксплуатируем сейчас, можно испарять около 18 т. Немецкие машиностроители уже изготавливают детали и узлы установки, которые будут поставлены нам в конце осени этого года. Зимой мы приступим к ее монтажу, а весной следующего - включим в технологическую цепочку».
Добавлю, что на площадке, отведенной для установки нового сушильного комплекса, уже залит мощный фундамент. А руководство предприятия уже прорабатывает планы дальнейшего обновления мощностей плитного производства.
«Далее мы намерены модернизировать наш пресс Rauma-Repola, - говорит г-н Кудрявцев. - Этот 19-этажный пресс, конечно, надежное и производительное оборудование, которому отдают предпочтение изготовители плит во всем мире. Но и самому надежному оборудованию требуется замена износившихся узлов, да и параметры процесса прессования хочется улучшить. Цикл прессования у действующего пресса - около семи минут, это очень много, и мы думаем о его модернизации, либо примем решение о покупке пресса непрерывного действия, о чем будем говорить с производителями такого оборудования в ближайшее время».
Мероприятия программы модернизации коснутся также и других подразделений плитного производства. Рассказывает главный инженер: «В цехе ламинирования плит установлены четыре линии: две производства компании Siempelkamp эксплуатируются уже давно, а линии производства итальянской фирмы Panioni смонтированы всего несколько месяцев назад, причем одна из них еще не запущена, мы включим ее в технологическую цепочку по мере наращивания объемов изготовления ДСП. Кроме того, в цехе импрегнирования мы планируем перевести линию пропитки бумаги с пара на газ, что позволит существенно расширить технические возможности оборудования и повысить качество продукции».
«Таким образом, реализуя этап за этапом программу модернизации плитного производства, в течение ближайших нескольких лет мы выведем его на новый уровень - как по объемам выпуска ЛДСП, так и по качеству продукции, соответствующему запросам потребителей и отвечающему лучшим мировым стандартам», - подытожил рассказ о мероприятиях по обновлению плитного производства ООО «Вохтожский ДОК» генеральный директор.
От доски до домокомплекта
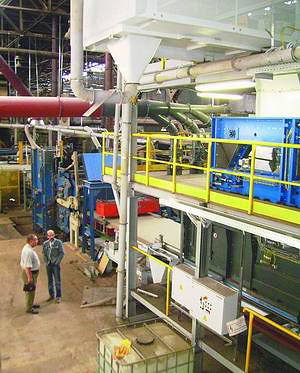
Новая формующая машина фирмы Dieffenbacher обеспечит увеличение объемов выпуска плит высокого
качества
Клееный строганый и нестроганый брус, имитация бруса, домокомплекты из клееного бруса, вагонка, блокхаус, доска пола, фасадная доска, рейка, брусок, транспортные поддоны - вот перечень продукции, которую изготавливают в цехах деревообрабатывающего производства.
«Ассортимент у нас, как видите, большой, поэтому условно можно разделить его на два направления: погонажные изделия и клееные деревянные конструкции и домокомплекты из клееного бруса, - рассказывает о вверенном ему подразделении комбината заместитель генерального директора по деревообрабатывающему производству ООО «Вохтожский ДОК» Дмитрий Воробьев. - Сырье, сосновые и еловые сортименты, нам поставляют небольшие местные компании, заготавливающие лес на севере и востоке Вологодской области. Лесоматериалы на комбинат доставляют в основном по Монзенской железной дороге, которая и в советские времена служила в качестве лесовозной. В месяц нам требуется около 4800 м3 пиловочника, то есть около 58 тыс. м3 древесного сырья в год».
Еловые и сосновые бревна в соответствии с техническими требованиями сортируются на автоматической линии ЛТ86Б и отправляются в открытый бассейн, в котором находятся некоторое время, для того чтобы пиловочник очистился от песка и грязи. Затем по транспортерам бревна поступают на рамные лесопильные станки Р-75 советского производства.
«Сейчас мы пилим лесоматериалы на одном потоке в две смены и получаем (при выходе 52% полезной древесины из бревна) 120 м3 доски в сутки. Можем пилить и больше, на двух потоках, техническая возможность для этого есть», - говорит Дмитрий Федорович.
Доски поступают на сортплощадку, где вручную сортируются и раскладываются в пакеты по сортам и сечению. Сформированные пакеты отправляются в конвективные сушильные камеры отечественного производства. Их на предприятии 12: четыре камеры «Термак» (объем разовой загрузки 40-45 м3) и восемь камер «Термотех» (объем разовой загрузки 90 м3). Доски сушат до влажности 12±2% по ГОСТ 16588-79. По окончании сушки выполняется контроль качества - с помощью влагомера проверяют влажность древесины. Заготовки, не прошедшие контрольный тест, возвращаются на досушку либо кондиционирование.
«Сушильное оборудование эксплуатируется уже давно и пока более-менее справляется со своими "обязанностями", но качество сушки не всегда удовлетворяет нас, - отмечает Дмитрий Воробьев. - С учетом того, что у нас есть хорошие перспективы на рынке КДК и домов из клееного бруса, конечно, требуется замена сушильных камер современными, более производительными. Тем более что обновление сушильного комплекса - в русле стратегического курса руководства комбината на поэтапную модернизацию оборудования и наращивание мощностей предприятия. За последние два года для развития нашего направления производства было приобретено немало современного оборудования: станок для заточки профильных ножей Randomat, новый строгальный станок для обработки бруса Leadermac 630, станок для строжки ламелей перед склейкой их в брус Leadermac 526, высокопроизводительный делительный станок для изготовления евровагонки (через компанию Global Edge). Хочу отметить, что мы выбрали оборудование именно этой фирмы ввиду его высокой надежности: у нас до сих пор исправно служат станки Leadermac, купленные еще в 1990-годы, это просто "неубиваемые" машины. Ну и, конечно, мы не смогли бы так быстро продвинуться в производстве элементов домокомплектов из клееного бруса без обрабатывающего центра Krusi. Все это оборудование органично вписалось в технологический процесс изготовления погонажа и КДК».
Объем производства погонажа - в среднем 1700 м3 в месяц, из которых около 500 м3 - евровагонка. Для изготовления этой продукции на предприятии есть хороший машинный парк, в составе которого, например, безотказно «трудятся» станки фирмы Weinig, которые были приобретены еще в 1980-1990-е годы. Погонаж отправляется в основном на стройбазы и в строительные компании южных регионов России (среди заказчиков -организации из Ростова-на-Дону, Краснодара, Воронежа и других городов).
«Сейчас мы активно развиваем производство нового для нас продукта - крашеной фасадной доски, - продолжает свой рассказ заместитель генерального директора комбината. - У фасадной доски, которая широко применяется в строительстве в скандинавских странах, множество плюсов: практичность, стойкость к действию внешних факторов, экологичность и т. д. Прежде чем приступить к выпуску этого перспективного материала, мы внимательно изучили все нюансы технологического процесса, побывали в Финляндии - на конференции, посвященной производству фасадной доски, взвесили все за и против, купили высокопроизводительную датскую машину Ceetec A 250 для нанесения краски и понемногу начинаем осваивать российский рынок. Мы считаем, что у этого материала хорошее будущее на отечественном рынке, и спрос на фасадную доску не заставит себя ждать».
Но самые большие надежды в ООО «Вохтожский ДОК» возлагают на развитие производства клееного деревянного бруса и домокомплектов из него. Экскурсию по деревообрабатывающему производству мы начали со склада готовой продукции. Еще на подходе к нему обращаю внимание на упакованный объемистый пакет, на котором написано: «Домокомплект "Бочаров". Брус профилированный, 185/200, сосна, пакет № 5, 1,82 м3». «Это часть приготовленного к отправке домокомплекта, - поясняет Дмитрий Федорович. - В строительный сезон наша продукция на складе не залеживается: из тех 800-900 м3 клееного бруса, которые мы производим сейчас в месяц, больше половины уходят на строительство индивидуальных домов для наших заказчиков, а остальное забирают стройбазы. Наш склад рассчитан на 1,5 тыс. м3 готовой продукции, но при существующем спросе он вряд ли будет заполнен: сейчас у нас портфель заказов на изготовление домокомплектов сформирован на три месяца и количество обращений к нам только растет».
Вместе с заместителем генерального директора мы прошлись по всей технологической цепочке изготовления домокомплектов. Высушенные доски визуально оцениваются на предмет обнаружения дефектов (сучков, трещин и т. д.), которые выторцовываются на станках с ручной подачей. Затем подобранные по качеству доски сращиваются по длине в соответствии с требуемыми габаритами клееного бруса (максимальная длина ламелей - 13 м). Готовые ламели прострагиваются по пласти на станке Leadermac 526, сортируются на лицевые и внутренние и, по мере накопления, отправляются на склеивание на горизонтальном холодном прессе. «Такой пресс предназначен в основном для изготовления гнутоклееных деталей, кроме того, при его загрузке и выгрузке не обойтись без ручного труда, - говорит Дмитрий Воробьев. - Поэтому в свете тех перспектив, которые открываются перед нами в производстве домокомплектов из клееного бруса, надо в обозримом будущем приобретать современный вертикальный пресс».
Для склеивания ламелей используется высокопрочный водостойкий, экологически чистый двухкомпонентный клей производства концерна AkzoNobel, который на пласти ламелей наносит клееналивная машина производства того же концерна.
«Расход клеевого состава - 320 г на один квадратный метр, - рассказывает Дмитрий Воробьев. - Ежемесячно нам требуется в среднем 6 т готовой смеси, в Вологодской области мы едва ли не самый крупный потребитель клеевых материалов AkzoNobel. Сейчас мы рассматриваем вопрос о переходе с клеевой системы 1249/2579 на систему 1257/7557 с целью оптимизации расходов на клей, потому что объемы КМ, которые мы потребляем, обходятся комбинату недешево».
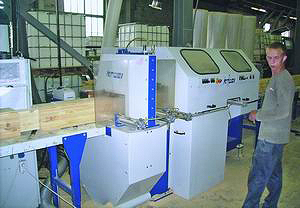
Покупка оборудования Krusi позволило комбинату сделать большой шаг вперед в производстве клееного бруса
После склейки заготовка бруса, состоящая из пяти-шести слоев ламелей, обрабатывается на станке Leadermac 630 - строгается с четырех сторон. А затем на том же станке брусу придают необходимый профиль: под утеплитель или без утеплителя - в зависимости от заказа. Далее профилированный клееный брус нарезается на элементы необходимого размера в соответствии с проектной документацией, на станке Krusi CMI 4×4 зарезаются чашки и сверлятся отверстия под шпилечную систему. И в завершение все элементы будущего деревянного дома упаковывают и отправляют заказчику. Сейчас в активе Вохтожского ДОКа уже около полусотни выполненных заказов, дома из клееного бруса, изготовленные из вологодской древесины на комбинате над Монзою, построены в самых разных уголках России: Подмосковье, Санкт-Петербурге, Ленинградской, Вологодской областях и соседних с ними регионах, даже на Сахалине.
«Как производитель домов из клееного бруса мы еще предприятие молодое, - говорит Дмитрий Воробьев. - Домокомплект для первого нашего дома был изготовлен в марте 2012 года. На одной из московских выставок, в которой мы принимали участие, прямо на стенде был оформлен заказ. Свой выбор клиент объяснил тем, что в нашем предложении его привлекло оптимальное сочетание цены и качества, а в том, что качество нашей продукции высокое, он не сомневался и сказал, что "послужной список комбината из Вологодской области, давно и успешно работающего в деревообрабатывающей области, вызывает доверие"».
Кстати, о качестве изделий: его проверяют как в лаборатории Вохтожского комбината (на скол), так и в лаборатории Сокольского ДОКа, а также в одной из независимых лабораторий в Вологде. Результаты испытаний образцов продукции неизменно подтверждают, что все ее характеристики соответствуют строгим требованиям нормативов, о чем свидетельствуют соответствующие сертификаты. Высокое качество наряду с приемлемой стоимостью продукции, которая обеспечивается в первую очередь транспортной доступностью качественного сырья, - серьезные аргументы в пользу конкурентоспособности домов из клееного бруса, изготавливаемых в Вохтоге.
«Сейчас 90% наших заказчиков - это строительные организации и стройбазы, а не конечный потребитель, - продолжает Дмитрий Федорович. - Пока что о нас узнают в основном заходя на наш сайт или посетив наш стенд на выставке. Конечно, в нашей стране нельзя недооценивать и такой "вид" рекламы, как сарафанное радио, когда клиенты рекомендуют фирму своим родным, знакомым, друзьям, соседям. Вот пример. Когда-то мы поставили домокомплект заказчику из Зеленогорска (Курортный район Санкт-Петербурга). Несмотря на то что у него на руках уже был, по сути, готовый проект дома, подготовленный другой компанией, он предпочел сделать заказ именно у нас. После завершения строительства он прислал нам фотографии своего дома и написал, что обязательно будет рекомендовать нас всем своим знакомым. И вскоре у нас появился один заказчик из Ленобласти - из г. Выборга, приятель того самого заказчика из Зеленогорска.
Безусловно, нам есть над чем работать. Например, надо активнее разворачивать рекламную кампанию, участвовать в выставках, чтобы привлекать конечных потребителей, и мы будем делать шаги в этом направлении, но пока, как я уже сказал, у нас достаточно заказов, для того чтобы загрузить производство. Кроме того, нас пока вполне устраивает схема работы со сторонними строительными организациями, которые приходят к нам с уже оформленными конкретными проектами, и мы, по сути, сразу же приступаем к выполнению заказа. С частным клиентом так не получится. Как показывает практика, от момента знакомства с компанией до момента оформления заказа проходит в среднем полгода - пока человек определится, что именно и как именно он хочет построить у себя на участке... Кроме того, у нас пока нет собственных бригад монтажников, и если клиент обращается к нам с просьбой построить дом под ключ, наши дизайнеры-конструкторы разрабатывают проект, учитывающий все его пожелания, мы изготавливаем в сжатые сроки домокомплект, а для его сборки мы привлекаем деловых партнеров, приобретающих у нас клееный брус для реализации своих заказов, у которых есть такие бригады.
Конечно, со временем, когда о нас узнают множество потенциальных частных заказчиков, мы создадим и собственные коллективы монтажников, которые будут собирать на участках клиентов дома из наших комплектов под ключ - от фундамента до крыши и внутренней отделки. Это наше будущее. А в том, что оно будет успешным, мы уверены. Спрос на нашу продукцию высокий, и мы стремимся к тому, чтобы удовлетворять его. Руководством комбината прнимаются меры для перевооружения машинного парка, и вскоре у нас появятся возможности, для того чтобы удвоить объем выпуска клееного бруса и довести его до 1500 м3 в месяц. С июня мы изготавливаем КДК круглосуточно, силами четырех бригад. Люди постепенно входят в этот рабочий ритм, мы раскручиваем маховик производства, и оно набирает обороты. Наших сотрудников привлекает перспектива работать на современном предприятии, оснащенном передовым оборудованием и выпускающем востребованную продукцию, получать неплохую заработную плату, чувствовать уверенность в завтрашнем дне. Вы обратили внимание, сколько молодых людей работает на нашем производстве?»
Главная ценность – люди
И сейчас самое время рассказать о том, как на Вохтожском комбинате решают проблему кадров - одну из самых острых социальных проблем современных российских предприятий. Ведь, что бы там ни говорили о желании минимизировать влияние так называемого человеческого фактора на результаты производства, без участия людей полноценно пока не может работать ни одно предприятие. Конечно, кадровая проблема актуальна и для комбината, на котором трудятся почти 900 жителей Вохтоги: примерно 600 человек заняты на плитном производстве, еще 300 - на деревообрабатывающем.
«Костяк нашего комбината составляют те, кто пришел сюда 30-35 лет назад, - говорит главный инженер предприятия Евгений Мельников. - Однако нам нужны новые, молодые, квалифицированные кадры, умеющие обслуживать современную технику, которой на предприятии с каждым годом все больше. Нам нужны механики, электрики, слесари и работники других специальностей».
Собственник и руководство ООО «Вохтожский ДОК» хорошо понимают необходимость смены поколений рабочих и инженерных кадров. И поэтому на комбинате действует программа привлечения и подготовки молодых кадров. Сейчас в вузах за счет предприятия обучаются инженерным специальностям 11 человек. В этом году в здании заводоуправления открываются учебные классы филиала Грязовецкого техникума, в котором по рабочим специальностям готовят две группы вчерашних школьников.
«У нас они учатся, можно сказать, без отрыва от производства, - рассказывает генеральный директор комбината Сергей Кудрявцев. - Теоретические знания закрепляют прямо в цехах предприятия, корпуса которых расположены рядом с местом учебы. Проходя практику на производственных участках, где трудятся их родственники и знакомые, видя положительные перемены, которые происходят в жизни комбината, - модернизацию оборудования, освоение новой, интересной продукции, зная, что на предприятии стабильно выплачивается достойная заработная плата и что есть возможность продолжить учебу в вузе и делать карьеру, учащиеся техникума укрепляются в желании влиться в наш коллектив. Тем более что, кроме заботы о подготовке молодых кадров, мы уделяем большое внимание поддержке тех, кто у нас работает в штате. Ежегодно руководство комбината заключает с трудовым коллективом предприятия коллективный договор, в котором фиксируются обязательства руководства по обеспечению работникам необходимых условий для продуктивного труда и полноценного отдыха».
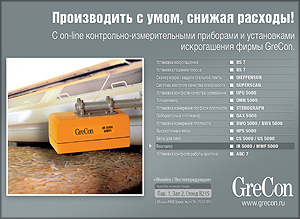
GreCon. Системы искрогашения и измерительные
системы
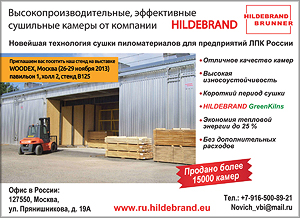
Hildebrand. Сушильные камеры для древесины
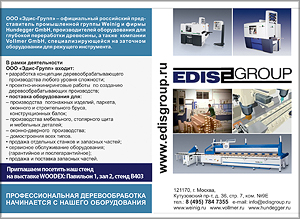
Эдис-Групп. Деревообрабатывающее оборудование
Активное участие в подготовке и подписании коллективного договора принимает профсоюзный комитет Вохтожского ДОКа. Председатель профкома Любовь Васильева рассказывает: «Сегодня на профсоюзном учете состоят 450 работников комбината - это половина штатного состава предприятия. Задача нашего комитета - защита прав трудящихся и оказание им разного рода материальной помощи, сплочение коллектива. Это поддержка ветеранов войны и труда, работавших на нашем предприятии и находящихся сейчас на пенсии, помощь инвалидам и остро нуждающимся в деньгах. Комбинат оплачивает 70% стоимости путевок в летние оздоровительные лагеря для детей наших работников, выделяет деньги на юбилеи, свадьбы, а также на организацию похорон. У нас функционирует физкультурно-оздоровительный центр, а комиссия профкома по культуре производства заботится о ремонте помещений комнат отдыха в цехах и на участках, об оборудовании их бытовыми приборами. Профсоюзный комитет организует культурно-массовые мероприятия, например зимнюю и летнюю спартакиады, в которых охотно принимает участие наша молодежь. На все эти нужды руководство комбината выделяет немалые средства - в прошлом году более 120 тыс. руб.».
Многое делается комбинатом и для обеспечения жизнедеятельности и развития пос. Вохтога, для которого предприятие является градообразующим. При самом активном участии ДОКа создавался мемориальный комплекс, посвященный воинам, погибшим во время Великой Отечественной войны, заасфальтирована центральная площадь поселка, сейчас ведутся работы по обновлению фасада Дома культуры. Собственник комбината Павел Васев поддерживает эти инициативы и выделяет на их реализацию необходимые средства.
На территории комбината находится муниципальная котельная, которая обеспечивает теплом жилые дома и социально значимые объекты поселка: школы, детские сады, общественные учреждения. Комбинат предоставляет котельной древесные отходы, которые используются в качестве топлива.
...Уезжал я из Вохтоги под проливным теплым дождем, крупные капли которого весело барабанили по оконному стеклу электрички, увозившей меня в Вологду. Проезжая мимо корпусов Вохтожского ДОКа, я невольно вспомнил народную примету: если дело начинается под дождиком, будет оно удачным. Именно так складываются дела у коллектива ООО «Вохтожский ДОК», который находится сейчас на магистральном пути развития.
Технические характеристики ЛДСП производства ООО «Вохтожский ДОК»
Стандарт - ГОСТ Р 52078-2003
Класс эмиссии - Е1 (на заказ - Е2)
Размеры - 2750х1830 мм
Толщина - 16 мм
Плотность - 680-740 кг/м3
Материалы для ламинирования - текстурная бумага Schattdekor, Interprint, Lamigraf, Impress, «Пензадекор», «Маяк», «Техноцелл», пропиточные смолы на основе меламина
Цветовая гамма облицовки - фоновая (белый, серый), цветная (зеленый, кремовый, голубой, бордо, желтый), текстура древесины (11 видов «под орех», 4 - «под вишню», 4 - «под бук», 10 - «под дуб», 2 - «под ольху» и др.), металлики - всего более 50 видов
Виды тиснения - универсальные древесные поры, шагрень
Условия отгрузки - в пачках 2750×1830×600 мм по 36 листов (181,17 м2)
Технические характеристики четырехстороннего станка Leadermac серии Compact
Ширина обрабатываемой заготовки - 15-230 мм (опции: 150, 250, 300 мм)
Высота обрабатываемой заготовки - 10-150 мм (опции: 180, 200, 250 мм)
Количество шпинделей, min-max - 4-8
Мощность двигателей шпинделей - 5,5 кВт (опции: 7,5; 11; 15 кВт)
Мощность двигателя подачи - 3,5 кВт (опции: 5,5; 7,5; 11 кВт)
Скорость вращения шпинделя - 6000 об./мин. (опции: 7200, 9000 об./мин.)
Диаметр шпинделя - 40 мм (опция - 50 мм)
Диаметр резания первого нижнего шпинделя, min-max - 125-160 мм
Диаметр резания левого вертикального, min-max - 112-200 мм
Диаметр резания правого вертикального шпинделя, min-max - 112-200 мм
Диаметр резания верхнего горизонтального шпинделя, min-max - 100-200 мм
Диаметр резания нижнего горизонтального шпинделя, min-max - 100-200 мм
Скорость подачи (бесступенчато регулируется инвертором - 6-36 м/мин. (опция - 55)
Диаметр подающего ролика - 140 мм
Ширина подающего ролика - 15 мм (50)
Максимальное давление пневматической системы - 6 бар
Диапазон регулирования для подающего стола и упорной планки - 10 мм
Диапазон регулирования для вертикальных шпинделей (осевой) - 30 мм
Диапазон регулирования для горизонтальных шпинделей (осевой) - 20 мм
Длина подающего стола - 2 м (опции: 0,8, 2,5, 3)
- механические цифровые индикаторы для прижимных башмаков и других прижимных устройств;
- полный звукоизоляционный кожух;
- подъем и опускание траверса осуществляется посредством электрического мотора-редуктора;
- боковой прижимной ролик установлен напротив первого правого шпинделя;
- подача выполняется системой редукторов и карданных передач.
Характеристики станка Krusi CMI 4x4
Количество основных шпинделей - 2 шт.
Максимальная ширина обрабатываемой заготовки - 245 мм
Максимальная высота обрабатываемой заготовки - 250 мм
Мощность двигателей (4 основных шпинделя) - 4 кВт
Скорость вращения шпинделей - 2900 об./мин.
Диаметр шпинделя - 40 мм
Длина принимающего рольганга - 6 м
Требуемое давление воздуха - 6 кг/см2
Вес - 1700 кг
Габариты - 1700×1100×600 мм
Александр РЕЧИЦКИЙ
Фото автора
P. S. Когда автор дописывал эти строки, из Вохтоги пришли две отличные новости. Обновленная линия изготовления ДСП работает с производительностью, которая превзошла ожидания, - в сутки теперь можно изготавливать 633 м3 плиты, причем более 95% продукции - первого сорта. И еще - в семье Дмитрия Воробьева пополнение - родилась дочка! Поздравляем от всей души!