Енисейский фанерный комбинат. Тест на прочность
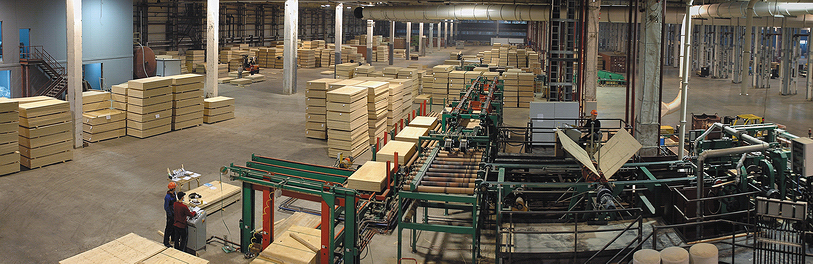
У этого молодого, но довольно перспективного проекта непростая судьба. ООО «Енисейский фанерный комбинат» было учреждено 28 июня 2006 года с целью реализации инвестиционного проекта строительства предприятия по глубокой переработке древесины в г. Сосновоборске Красноярского края. Летом 2008 года началось строительство комбината, а пуск первой линии состоялся в мае 2011-го. Среди причин такого переноса сроков - и влияние кризиса 2008-2009 годов, и сложности с финансированием проекта, связанные с изменением позиции основного инвестора. Однако собственники ЕФК, его руководство и трудовой коллектив борются за предприятие: невзирая на трудности, сегодня комбинат не только выпускает востребованную на рынке продукцию, но и развивается, осваивая новые, перспективные направления в деревообработке и домостроении.
ЕФК получил статус приоритетного инвестпроекта в области освоения лесов еще в 2008 году, но в связи с изменениями в проекте, сроках строительства и объемах финансирования в апреле 2013 года был подтвержден приоритетный статус с обновленными данными проекта. Заявленная стоимость проекта - 7,6 миллиардов рублей.
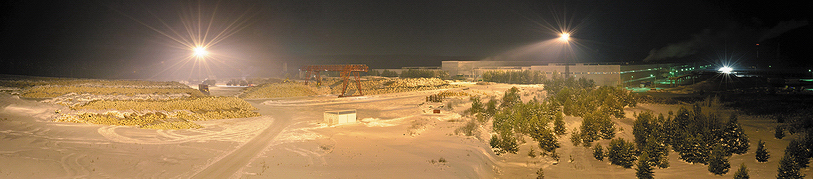
Цифры из инвестиционного проекта ЕФК
Срок окупаемости - по 1-й квартал 2016 г. (9 лет)
Среднесписочная численность работающих - 680 человек
Финансирование: 2350 млн руб. - собственные средства, 5330 млн руб. - заемные средства
(кредит ОАО «Банк ВТБ»)
Енисейский фанерный комбинат (ЕФК) расположен в промышленной зоне г. Сосновоборска, в 30 км от столицы Красноярского края. В январе 2007 года собственники предприятия приобрели у ОАО «Красноярский завод прицепной техники» промышленную площадку - производственные и подсобные корпуса общей площадью около 260 тыс. м2, подъездные железнодорожные пути, электрическую подстанцию и другую инфраструктуру. Общая площадь земельного участка, на котором расположены структуры комбината, - 75 га.
Продукция ЕФК
Хвойная фанера (2440×1220 мм, толщина 9-40 мм), лиственная фанера (2440×1220 мм, толщина 9-27 мм), фанера с наружными слоями из шпона лиственных пород («твин») форматом 2440×1220 мм
и толщиной 9-30 мм, хвойный и лиственный шпон (до 2600×1300 мм).
В планах: ламинированная фанера, облицованная техническими и декоративными пленками на основе фенолоформальдегидных смол (2440×1220 мм, толщина 9-21 мм),
фанера со шпунтом (2440×1220 мм, толщина 9-21 мм).
Планы и реалии
Строительство Енисейского фанерного комбината началось в 2008 году, но, к сожалению, мировой финансовый кризис внес коррективы в планы инвесторов. Только в мае 2011 года состоялся пуск линии по изготовлению шпона, ознаменовавший собой окончание первого этапа инвестиционного проекта, рассчитанного на производство 200 тыс. м3 фанеры в год. По этому случаю на торжественной церемонии на ЕФК присутствовали спикер Государственной думы РФ Борис Грызлов, губернатор Красноярского края Лев Кузнецов и председатель наблюдательного совета ООО «Енисейский фанерный комбинат» (а также председатель совета директоров российско-американской компании ООО «Midway United Ltd», которая и является инициатором строительства ЕФК) Александр Катунин.
Владимир Бархет, исполнительный
директор ЕФК
«Чтобы привести в надлежащий вид бывшие корпуса завода прицепных конструкций, от которых остались только остовы, пришлось вложить немало сил и средств, - рассказывает заместитель генерального директора по персоналу ООО «Енисейский фанерный комбинат» Сергей Паклин. - Надо было заново бетонировать полы, укреплять стены и усиливать перекрытия. Основное оборудование было закуплено в США. 30 июня 2011-го мы произвели первую партию фанеры, а готовая продукция начала поступать на склад в сентябре 2011 года. Постепенно наращивая объемы производства, мы вышли на производительность около 8,3 тыс. м3 фанеры в месяц. В настоящее время заканчиваются работы по вводу отдельных единиц оборудования, позволяющих нам выйти на заявленные объемы в кратчайшие сроки. На внутренний рынок уходит около 80% готового продукта, на страны Европы и СНГ приходится 20% общего объема изготавливаемой фанеры. Объемы производства и продажи шпона пока невелики, в основном это разовые заказы предприятий, изготавливающих полы и мебель. Но портфель заказов постепенно формируется, и мы уверены, что наш шпон из древесины лиственницы и кедра найдет своего потребителя».
В рамках второго этапа планируется увеличение мощности завода до 350 тыс. м3 фанеры и до 100 тыс. м3 товарного шпона в год. Третий этап предполагает строительство современного завода по производству ориентированно-стружечной плиты (OSB) мощностью более 400 тыс. м3 в год. Но пока эти планы остаются только планами.
«Для реализации второго этапа нам необходимо закупить и установить еще ряд производственных линий, например линию лущения, сушилку, ребросклеивающее оборудование, оборудование участка ламинирования и другое, а средств на это нет, - говорит г-н Паклин. - Дело в том, что банк ВТБ, один из главных инвесторов проекта, решил приостановить его финансирование, объяснив свою позицию медленными темпами реализации проекта. Руководство нашей компании в течение почти года вело переговоры с банками о реструктуризации кредита. Летом этого года был проведен ряд совещаний в Минпромторге с участием представителей правительства Красноярского края, акционеров и менеджмента ЕФК. В августе был проведен строительный и технический аудит нашего предприятия, результаты которого сейчас рассматриваются рядом ведущих банков для принятия решения».
Но на предприятии не сидят сложив руки в ожидании. Помимо производства фанеры здесь освоили изготовление SIP-панелей и домокомплектов из этого перспективного строительного материала, а также выпуск топливных брикетов.
Производство фанеры
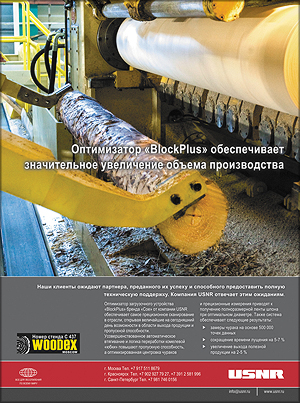
USNR. Оборудование для лесопильных производств
Карман-накопитель сортированного сырья
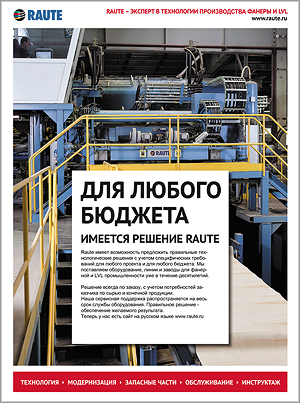
Raute. Оборудование для производства фанеры и LVL
Североамериканская технология производства фанеры, применяемая на Енисейском фанерном комбинате, уникальна для России. Выбор технологического оборудования был обусловлен схожестью свойств сибирской и североамериканской древесины и успешностью этой технологии. В качестве основного сырья для производства шпона, из которого делают фанеру, на ЕФК используется пихта, свойства которой мало изучены изготовителями фанеры и которая в технологическом процессе «капризна», но зато обеспечивает целый ряд достоинств готовой продукции. При стандартных физико-механических свойствах фанера, произведенная из пихты, примерно на 15% легче сосновой, которая традиционно представлена на российском рынке. Кроме того, природные смолы, содержащиеся в древесине хвойных пород, делают фанеру более устойчивой к гниению и заражению грибками. Пихтовая древесина в качестве основного сырья была выбрана еще и потому, что ее запасов в лесах области много.
«Береза, из которой в России традиционно делают фанеру, у нас также растет, но ее не рубят по той причине, что нам требуется только фанерный кряж, а даже из самой образцовой березовой делянки можно "выжать" максимум 40% фанкряжа из всего объема заготовки, - вступает в разговор исполнительный директор комбината Владимир Бархет. - На остальную заготовленную березовую древесину надо будет искать покупателей, и поэтому сейчас вести рубки березы невыгодно. Когда мы приступим к созданию производства OSB-плит, эту проблему можно будет решить с выгодой для всех сторон».
«Заготовку древесины на закрепленных за ЕФК участках леса ведут наши деловые партнеры», - уточняет Сергей Паклин.
«Из-за того что рынок фанерного кряжа в Красноярском крае развит плохо, мы вынуждены приобретать у поставщиков не только стандартный фанерный кряж, но и сырье в виде шестиметрового пиловочника, - добавляет Владимир Бархет. - Строительство линии по производству OSB позволит существенно оптимизировать процесс лесозаготовки и снизить себестоимость сырья (лучшая по качеству древесина будет поставляться длиной 5,4 м и использоваться в производстве фанеры, а остальная древесина - длиной 6 м - пойдет на производство OSB).
В связи с использованием некоторой доли сырья длиной 6 м у нас образуется довольно большой объем отходов (обрезки бревен длиной 60 см), примерно половину из них мы используем для изготовления топливных брикетов, часть - в качестве топлива для котельной, но все же их остается еще немало. Сложившуюся ситуацию с образованием отходов нам однозначно поможет решить строительство завода OSB, а для более глубокой переработки сырья мы прорабатываем вопрос об организации производства топливных гранул. Тем более что в рамках прошедшей в Красноярске выставки ExpoDrev производство топливных гранул неоднократно называлось приоритетным направлением для Красноярского края».
Коротко опишем технологию производства фанеры на Енисейском фанерном комбинате.
Участок разделки лесоматериалов
Все начинается с участка разделки лесоматериалов для лущения.
Сырье при помощи челюстных погрузчиков Liebherr подается на раскатной стол (два последовательно расположенных поперечных цепных транспортера), габариты которого позволяют принимать сырье длиной до 20 м. С раскатного стола бревна поштучно поступают на участок окорки. Двухроторный окорочный станок Valon Kone VK5000 HD-Combi-2R c пневматическим прижимом ножей позволяет окаривать сырье диаметром от 100 до 680 мм со скоростью подачи до 120 м/мин. Окоренное сырье проходит через сканер, который считывает геометрические характеристики сортимента (параметры кривизны, величину сбега и т. д.) и оптимизирует раскрой сырья на чураки длиной 2,6 м с целью достижения максимального полезного выхода. Раскрой сортиментов может выполняться как в ручном, так и в автоматическом режиме. На линии раскряжевки используются три пилы, что позволяет значительно повысить ее производительность по сравнению с традиционными схемами, когда используется одна пила. После участка раскроя выполняется сортировка чураков по диаметру, что повышает эффективность гидротермической обработки и качества лущения.
Участок гидротермической обработки сырья
Пригодное для обработки сырье поступает на участок гидротермической обработки (ГТО), где загружается в наземные тоннели. Объем сырья, единовременно загружаемого в каждую из 16 пропарочных камер ГТО, составляет около 150 м3. Гидротермическая обработка заключается в орошении штабеля чураков горячей водой (температурой до 60єС), которая разбрызгивается через форсунки, расположенные в потолке тоннеля ГТО. После закрытия дверей тоннеля начинается цикл пропарки, который состоит из двух стадий: прогрева и выдержки при заданной температуре. Предварительный прогрев с плавным повышением температуры позволяет снизить вероятность появления торцовых трещин из-за резкого перепада температуры сортимента и теплоносителя - воды. «Продолжительность гидротермической обработки зависит от породы древесины, начальной температуры и диаметра чураков и может продолжаться до 18 часов. В зимнее время года технологией предусмотрено оттаивание мороженного сырья перед гидротермической обработкой при цеховой температуре в специальных накопительных карманах».
В процессе орошения чураков вода циркулирует по замкнутому контуру, что исключает сброс загрязненной технологической воды. Она стекает по штабелю на пол и по системе каналов поступает в резервуар, где очищается от коры и других взвешенных частиц. Очищенная вода циркуляционными насосами по системе трубопроводов подается обратно в камеры ГТО, а перед распылением проходит через теплообменник, где нагревается до заданной температуры.
Отделение изготовления шпона
Загрузочное устройство лущильного станка
Общий вид линии лущения
Электрощитовая линии лущения
Роторные ножницы линии лущения
Участок стопоукладки линии лущения
По окончании цикла прогрева открываются двери туннеля ГТО и включается принудительная вентиляция для удаления пара. Затем челюстными погрузчиками Liebherr пропаренные чураки выгружаются из камер и укладываются в карман-накопитель, откуда при помощи загрузочного устройства подаются поштучно на центровочное загрузочное устройство (ЦЗУ). После позиционирования чурака прецизионное рычажное устройство снимает его со шпинделей ЦЗУ и передает в лущильный станок фирмы Cое (входит в состав концерна USNR, США). Этот станок укомплектован тройными телескопическими шпинделями. При достижении чураком определенного диаметра в процессе лущения наружные шпиндели отводятся и долущивание чурака осуществляется на внутренних шпинделях. В станке предусмотрен обжим шпона как линейкой, так и рифленым роликом с сервоприводом. Использование для обжима шпона приводного ролика позволяет значительно повысить скорость лущения по сравнению с традиционными схемами, в которых используется прижимная линейка с нажимной кромкой. Использование ролика наиболее целесообразно при изготовлении толстого шпона.
Получаемая в процессе лущения лента сырого шпона на высокой скорости поступает на один из этажей трехэтажного ленточного конвейера-накопителя. Использование такого конвейера позволяет синхронизировать работу лущильного станка и роторных ножниц, обеспечивая максимальную производительность лущильной линии. После конвейера-накопителя шпон проходит через сканер и компьютер выполняет расчет оптимальной схемы рубки каждой ленты шпона. Параметры дефектов, требующих вырубки, в память ПК вводит технолог.
Кстати, о компьютерах. Отдавая должное производительности и надежности оборудования компании USNR, Владимир Бархет заметил, что некоторые трудности возникают с адаптацией программного обеспечения, созданного по стандартам, существующим в США, к тем частотам, на которых обычно работают в России. Эти сложности связаны с тем, что ЕФК приобрел оборудование, изначально изготовленное именно для работы на американском заводе, а уже впоследствии, оно было перепродано в Россию. «Найти специалистов для работы с этим оборудованием (Allen Bredley) непросто. Хорошо, что сейчас у нас есть такие сотрудники, выросшие в стенах нашего предприятия, так как готовых специалистов со знанием этого оборудования в России почти нет», - сказал он.
Одновременно со сканером на линии лущения работает влагомер шпона, использование которого позволяет осуществлять предварительную подсортировку шпона по влажности. Затем лента сырого шпона раскраивается роторными ножницами фирмы Raute на отдельные листы.
Рассортированный по влажности форматный шпон укладывается в две стопы (условно подразделяется на ядровый и заболонный) и при помощи вилочного погрузчика транспортируется на склад сырого шпона.
Для обеспечения экономии сырья на линии лущения выполняется отбор кускового (неформатного) шпона, который после сушки попадает на участок ребросклеивания или непосредственно на линию сборки пакетов и используется для формирования внутренних слоев фанерного листа. Отобранный на линии лущения кусковой шпон, так же как и форматный, поступает на склад сырого шпона.
Отделение сушки и облагораживания шпона
Отсортированный ядровый и заболонный шпон сушатся при разных режимах, что позволяет сократить общее время сушки и обеспечивает одинаковую конечную влажность шпона на выходе из сушилки. На Енисейском фанерном комбинате используются паровые линии сушки шпона марки COE от компании USNR с сопловым дутьем. Применение соплового дутья позволяет резко повысить интенсивность сушки за счет обеспечения высокой скорости (10-12 м/с) воздушного потока, выходящего из коробов через сопла. Для нагрева воздуха в сушилках установлены теплообменники. В качестве теплоносителя используется пар. Агентом сушки является воздух, который нагревается до 200°С.
Загрузка листов сырого шпона в сушилку выполняется при помощи вакуумного загрузчика. При помощи распределительного устройства шпон равномерно распределяется по этажам и поступает в сушильную камеру.
Управление сушилками ведется системой Sequoia Sentry производства компании Ventek Inc. (США). Эта система позволяет при измерении влажности вносить в режим сушки поправки на толщину и температуру шпона. Температура шпона измеряется инфракрасными датчиками, влажность шпона - щеточными кондуктометрическими датчиками. Влажный шпон при прохождении влагомера маркируется краской, распыляемой на поверхность листа. Недосушенные листы отправляются на досушку.
Режимы сушки корректируются на основе статистики измерения влажности в одной или нескольких рабочих сменах. Управление скоростью сушки осуществляется путем изменения давления технологического пара, подаваемого в калориферы, и скорости прохождения шпона через сушилку.
«Сейчас у нас имеются три линии сушки, из которых эксплуатируются две, третью скоро также запустим, - говорит Сергей Паклин. - При положительном решении о дальнейшем финансировании проекта введем в эксплуатацию и четвертую линию, что позволит достичь максимальной плановой производительности».
Высушенный и рассортированный шпон при помощи вилочных погрузчиков отвозится на склад промежуточного хранения, где выдерживается в течение суток. Со склада промежуточного хранения шпон распределяется по следующим этапам производственного процесса:
● на шпонопочиночные станки поступает шпон, потенциально предназначенный для использования в качестве рубашки 1го и 2го сорта (то есть верхних слоев фанерного листа). Починка шпона заключается в удалении дефектных мест с последующей заменой их вставками из качественного шпона (на ЕФК имеется пять станков марки COE от компании USNR для починки шпона);
● на линии ребросклеивания шпона фирмы Raute направляется кусковой неприрубленный шпон, отобранный на линии лущения и частично образовавшийся в процессе сушки. На линиях ребросклеивания получают поперечный шпон, который идет на внутренние слои фанеры. Ребросклеивание обеспечивает повышение качества и сортности фанеры, позволяет уменьшить трудозатраты при сборке пакетов фанеры;
● прирубленный кусковой шпон, отобранный на линии лущения, поступает непосредственно на участок сборки, на линию сборки пакетов (ЛСП) № 2;
● форматный шпон сорта «рубашка 3го сорта» и сорта «серединка» поступает непосредственно на участок сборки;
● реброскленный шпон поступает на линию сборки пакетов № 1.
Отделение сборки и прессования
Со склада промежуточного хранения и комплектации стопы сухого шпона погрузчиками подаются на линии сборки пакетов № 1 и 2 и на клеенаносящие вальцы, которые входят в состав оборудования отделения сборки и прессования.
Для склеивания листов шпона используется клей на основе фенолоформальдегидной смолы, произведенной ОАО «Уралхимпласт».
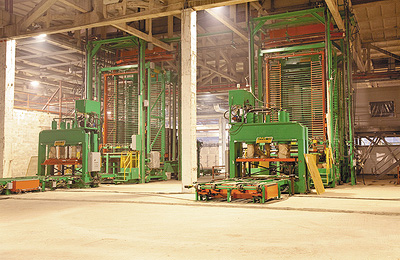
Горячие прессы Spar-Tek Industries Inc. (США)
Горячий пресс
На линии сборки пакетов № 1 (производитель - компания Raute) листы шпона проходят через вертикальную клеевую завесу и собираются в пакеты на столе сборки. Метод нанесения клея - налив, заключающийся в нанесении клея на одну поверхность листа шпона, пропускаемого с определенной скоростью через вертикальную клеевую завесу. Технология нанесения клея методом налива в России широко не распространена, хотя несколько заводов используют подобное оборудование в настоящее время.
На линии сборки пакетов № 2 (производитель - фирма Spar-Tek Industries Inc., США) листы шпона собираются в непрерывную ленту следующим образом: на главный конвейер друг за другом укладывают форматные листы шпона с направлением волокон, совпадающим с осью конвейера, в результате чего образуется непрерывная лента шпона. Клей на поверхность шпона наносится методом мелкодисперсного распыления в клеевых кабинах под высоким давлением при помощи форсунок. Избыток клея, образующийся в процессе распыления, по системе рециркуляции возвращается в систему клеенанесения высокого давления, что обеспечивает минимальный расход клея. Расход клея определяется скоростью движения ленты шпона в распылительной кабине и расстоянием между поверхностью шпона и форсунками. Для уменьшения вязкости и с целью повышения качества распыления клей перед подачей в форсунки нагревается. После прохождения первого слоя шпона через первую клеевую кабину на него укладывается второй (внутренний) слой из прирубленного кускового шпона с перпендикулярным направлением волокон. Затем непрерывная лента проходит через вторую клеевую кабину, где клей наносится на верхнюю поверхность второго слоя. После прохождения второй клеевой кабины на непрерывную ленту укладывается следующий слой шпона с направлением волокон, параллельным наружному. В составе линии сборки пакетов № 2 восемь клеевых кабин, что позволяет производить фанеру от трехслойной до девятислойной.
Полученная таким образом многослойная непрерывная лента поступает на участок раскроя, оснащенный диагональной пилой, где раскраивается на пакеты определенной длины. Полученные пакеты складываются в стопу и по системе транспортеров поступают на участок прессования.
Помимо линий сборки пакетов № 1 и 2 в отделении сборки и прессования установлены клеенаносящие вальцы. Это наиболее известный и максимально распространенный способ сборки пакетов.
Стопы набранных пакетов подаются на линию горячего прессования Spar-Tek Industries Inc. и после подпрессовки поступают на горячее прессование. Подпрессовка пакетов шпона осуществляется в стопе в одноэтажном прессе и обеспечивает необходимую транспортную прочность пакета шпона за счет слипания соседних листов шпона. Уплотнение пакетов также позволяет уменьшить высоту рабочих промежутков горячего пресса, увеличить скорость загрузки в этажерку и уменьшить количество брака в результате смещения листов шпона в пакете.
После холодной подпрессовки стопы пакетов поштучно загружаются в загрузочную этажерку 40-этажного горячего пресса для склеивания фанеры.
У пресса горячего прессования фанеры рамная конструкция со стальными нагревательными плитами. Внутри них выполнены каналы диаметром 20 мм, по которым циркулирует пар при температуре 184°С и давлении 1,1 МПа, подаваемый от коллектора по гибким шлангам. Размер плит пресса -
2700Ч1370 мм.
Температура прессования - 125-150°С, его продолжительность зависит от толщины фанеры.
Отделение форматной обрезки
Необрезанная фанера после горячего прессования поступает на линию форматной обрезки (производитель - компания Con Vey), где листы раскраиваются на заданный формат. В процессе форматной обрезки листы проходят через ультразвуковой сканер-детектор (производитель - компания GreCon), который предназначен для обнаружения дефектов склеивания. В случае их обнаружения сканер маркирует дефектные листы путем нанесения краски на торец листа. После обрезки фанера поступает на кантователь, где оператор визуально оценивает качество лицевой и оборотной стороны фанеры и распределяет ее по карманам в зависимости от дальнейшего назначения.
После обрезки фанера, в которой обнаружены внешние дефекты, перевозится погрузчиком на линию починки фанеры (производитель - компания Con-Vey Keystone Inc., США), на которой при помощи высококачественной двухкомпонентной замазки выполняется заделка дефектов фанеры.
Фанера, предназначенная для шлифования, как непосредственно с линии форматной обрезки, так и после линии починки, подается на линию шлифования. Шлифование фанеры осуществляется на 6-головочном шлифовальном станке фирмы Kimwood Corporation (США), встроенном в линию сортировки Con-Vey. После шлифования готовая фанера сортируется по качеству поверхности и складывается в пачки для последующей упаковки.
Складирование готовой продукции
Упакованные полиэстеровой лентой пачки фанеры отправляются на склад готовой продукции, который расположен в главном корпусе. Отгрузка фанеры выполняется автопогрузчиком в автотранспорт или железнодорожные вагоны.
Отделение клееприготовления
Большое значение для успешного функционирования технологической цепочки производства фанеры имеют правильный состав клеевых материалов и грамотный режим их использования.
Для приготовления клея на ЕФК используют фенолоформальдегидную смолу, произведенную ОАО «Уралхимпласт». Порошковые компоненты клея поступают в мешках Big Bags вместимостью 1 м3. Погрузчиком мешки доставляются к подъемнику, который переносит мешки в разгрузочную воронку. Из загрузочной воронки порошки шнековым конвейером поступают в одну из четырех воронок для компонентов клея, из которых шнековыми конвейерами они подаются в смеситель порошковых компонентов емкостью 3,8 м3, оснащенный тензометрическими весами. Из смесителя разгрузочным шнеком сухие компоненты подаются в вертикальный скоростной смеситель с импеллерной мешалкой. Готовый клей подается роторными насосами в резервуары для хранения, оснащенные мешалками и ультразвуковыми датчиками уровня. Из резервуаров хранения клей поступает в расходные резервуары линий сборки пакетов.
Использование отходов и производство топливных брикетов
Отходы, образующиеся в процессе окорки, раскряжевки и лущения древесного сырья, по системе транспортеров поступают на открытый склад и в дальнейшем используются в качестве топлива для собственной котельной комбината. «Конечно, отходы пихтовой древесины - не самое лучшее топливо, достаточно сказать, что теплотворная способность древесины пихты в 2,5 раза ниже березовой, - говорит Владимир Бархет. - Но наша котельная, которая оборудована котлами производства ООО "ПКЦ «Бийскэнергопроект»", полностью справляется со своими "обязанностями": обеспечивает предприятие паром для технологических нужд (гидротермическая обработка, сушка, прессование), горячей водой и отоплением». Мощность оборудования котельной - 23 Гкал/ч.
Пыль, образующаяся при шлифовании фанеры, и измельченные отходы сухого шпона пневмотранспортом подаются в фильтровальную станцию № 1. Оттуда по системе транспортеров они поступают на гидравлический брикетирующий пресс RUF-400, изготавливающий топливные брикеты методом холодного прессования.
«Мы приступили к производству брикетов в начале этого года, - говорит Сергей Паклин. - Этот вид топлива обретает все большую популярность в мире. У него множество достоинств: он хорошо горит, почти без остатка, дает много тепла, удобен в использовании и, что очень важно, экологичен. Например, наши брикеты изготавливаются без всяких клеевых составов, опилки хвойных пород за счет внутренней структуры древесины и лигнина, содержащегося в ней, прекрасно соединяются при прессовании».
Плотность брикетов RUF в полтора раза выше плотности обычных дров, а их теплотворная способность почти как у каменного угля. Брикеты удобны при транспортировке и складировании и занимают совсем мало места. Так, объем 1 т колотых березовых дров - 3 м3, а 1 т брикетов - 1 м3. В отличие от угля, брикеты не пачкают руки и не загрязняют помещение. Горят ровным пламенем, сохраняя стабильно высокую температуру горения в течение 1-1,5 ч, а в режиме тления - до пяти часов. Подходят в качестве топлива к любым твердотопливным котлам, печам, каминам, топкам всех видов. После сгорания масса золы - не более 1%. Кроме того, зола от брикетов RUF может служить экологически чистым удобрением и не наносит вреда здоровью людей или окружающей среде. В любом топливе есть сера, а водяной пар, соединяясь с окисью серы, образует серную кислоту, которая, проникая в щели стенок дымохода, приводит к их разрушению. При горении древесных брикетов серы выделяется в 100 раз меньше, чем при горении угля, а СО2 в - 10 раз меньше, чем при горении природного газа.
Ну и, конечно, организация производства брикетов способствует решению проблемы отходов на предприятии, которых на фанерном комбинате образуется много. Осталось найти своего потребителя...
«К сожалению, в России топливные брикеты пока еще не так востребованы, как, скажем, в Западной Европе, и внутренний рынок сбыта еще в стадии формирования, - продолжает Владимир Бархет. - Пока что мы выпускаем тот объем, который определяется местным спросом: в основном это владельцы частных домов и небольших организаций. При этом спрос стабильно растет, и уже сейчас мы рассматриваем вопрос об увеличении производственных мощностей».
Производство SIP-панелей
Михаил Петухов, генеральный директор ДСК «Енисей»
На участке производства SIP-панелей
Участок складирования необрезанной фанеры
Еще одним перспективным направлением развития ООО «Енисейский фанерный комбинат» является производство стеновых панелей по технологии SIP (СИП-панелей).
«В 2011 году мы сделали два пробных домокомплекта из сэндвич-панелей, дома эти построили, люди, которые живут в них, довольны своим жильем, - рассказывает исполнительный директор комбината. - Этот успех вдохновил нас на организацию производства структурных изоляционных панелей (СИП-панелей) и домокомплектов из этого материала. Мы закупили необходимое оборудование - отечественную линию, внимательно изучили нюансы технологии, вступили в Ассоциацию домостроительных технологий СИП и летом этого года приступили к работе».
«Мы - единственное в России предприятие, на котором для изготовления СИП-панелей используются листы фанеры, а не OSB-плиты, - вступает в разговор генеральный директор ДСК «Енисей» (входящего в группу компаний «ЕФК») Михаил Петухов. - Имеющиеся сегодня у комбината мощности позволяют в месяц поставлять домокомплекты общей жилой площадью 9 тыс. м2. Конструкция панелей позволяет гибко проектировать и строить многоквартирные дома высотой до трех этажей, любых размеров и сложности - по требованию заказчика. Технология изготовления сэндвич-панели очень проста: между двумя листами фанеры толщиной от 12 до 24 мм под давлением, с помощью однокомпонентного полиуретанового клея Kleiberit крепится в качестве утеплителя прослойка из пенополистирола. В результате получается монолитная, весьма прочная конструкция, которую можно использовать в качестве материала для создания элементов здания - стен, перекрытий, крыши, мансарды». В Северной Америке дома из SIP сертифицированы высотой до семи этажей.
Ширина СИП-панелей - 1,22 м, длина - 2,5 м, толщина - от 10 до 30 см, в зависимости от назначения и климатических условий строительства. Вес 1 м2 панели - 13-18 кг.
«У этого материала большие перспективы в малоэтажном деревянном домостроении и немало преимуществ перед другими строительными материалами, - продолжает свой рассказ г-н Петухов. - По теплосберегающим характеристикам 15-сантиметровая стена из структурной теплоизоляционной панели соответствует 200-сантиметровой стене из кирпича. Затраты на отопление дома, возведенного из СИП-панелей, в пять-шесть раз меньше, чем на отопление дома из традиционных материалов. Строительная конструкция из СИП-панелей выдерживает горизонтальную нагрузку до одной тонны на квадратный метр и вертикальную нагрузку более 10 т. Так что на стену из таких панелей можно абсолютно спокойно вешать не только картины в тяжелых рамах, но и кухонные шкафчики, книжные полки и т. п. В своей лаборатории мы провели испытания образцов панелей на прочность, которые показали, что фанера Енисейского фанерного комбината по некоторым физико-механическим характеристикам превосходит плиты OSB, например, на усилие выдергивания шурупа - в два раза: шуруп, ввинченный в СИП-панель, выдерживает нагрузку до 120 кг».
СИП-панели, которые изготавливают на ДСК «Енисей», с успехом прошли всесторонние испытания на пожаробезопасность. Российской ассоциацией домостроительных технологий СИП, членом которой является комбинат, предприятию выдан сертификат соответствия пожарной безопасности № С-RU.ПБ37.В.00200 с присвоением класса КМ2: группа Г1 - слабогорючие; группа В1 - трудновоспламеняемые; группа Д2 - с умеренной дымообразующей способностью; группа Т1 по токсичности продуктов горения - малоопасные.
«В производстве панелей мы используем высококачественный, экологически чистый пенополистирол, при изготовлении которого наш поставщик - предприятие из г. Ангарска - использует антипирены, - говорит Михаил. - Этот полистирол не поддерживает горение».
Одно из главных достоинств домокомплекта из СИП-панелей - быстрота монтажа конструкций и возведения зданий: в течение двух-трех недель и в любое время года. На дом небольшой площади требуется 60-80 панелей, в которых, в соответствии с проектом, на предприятии делают все необходимые технологические проемы. Кроме того, такое строительство весьма выгодно в финансовом отношении.
«Клиенты могут заказать у нас необходимое им количество плит и самостоятельно построить из них дом по своему проекту и исходя из своих соображений, - продолжает гендиректор ДСК "Енисей". - Клиент, желающий самостоятельно построить дом, может получить от нас полный комплект, что называется, "в одной коробке": все элементы дома, комплектующие, крепеж, вплоть до всего необходимого инструмента. Характеристики домов из СИП-панелей и почвы в наших краях позволяют строить дома на винтовых сваях. А это можно делать и без привлечения тяжелой строительной техники, установить сваи и, пригласив друзей и знакомых, собрать свой дом самостоятельно, как конструктор. А можно заказать у нас домокомплект со сдачей дома под ключ. Наши дома пользуются успехом, хотя много еще надо сделать для коммерциализации технологии. Сейчас участвуем в нескольких тендерах на строительство коттеджных поселков в Омске. Несколько домокомплектов изготовлены и ждут отправки на Дальний Восток - в районы, пострадавшие от наводнения».
«Ну и, конечно, мы рассчитываем на то, что региональные и федеральные власти подключат нас к реализации государственной программы развития малоэтажного домостроения, - говорит Владимир Бархет. - Тем более что у нас есть и хороший потенциал: сырье, производственные мощности, кадры и желание расти, развиваться».
Укрепить позиции и идти дальше
Эта основная мысль звучала во всех интервью, которые дали нам сотрудники ООО «Енисейский фанерный комбинат». Все наши собеседники и гиды по огромному предприятию выражали уверенность в том, что вопрос с финансированием будет решен положительно и комбинат продолжит поступательное движение вперед, наращивая темпы производства фанеры и товарного шпона, продолжая развивать производство СИП-панелей и укрепляя позиции на рынке деревянного домостроения. Готовы здесь приступить и к комплектованию линий и освоению технологии производства OSB-плит: уже разработан бизнес-план, сейчас рассматриваются предложения компаний - потенциальных поставщиков основного оборудования, в числе которых и такой известный машиностроитель, как IMAL.
Подготовили Светлана ЯРОВАЯ,
Елена ШУМЕЙКО, Александр РЕЧИЦКИЙ
Фотографии: ЕФК и Светлана Яровая