«ТранссЛес»: дорогу осилит идущий
Непростые будни сибирской лиственницы
Стало уже привычным слышать, как жалуются руководители деревообрабатывающих предприятий на тяготы бизнеса. Безусловно, есть для этого объективные причины - проблем у российского ЛПК хоть отбавляй. Однако пока одни директора осуждают и сетуют, другие, в буквальном смысле засучив рукава, тратят силы и время на преодоление проблем в своих компаниях. Ведь только так и делается настоящее дело.
На завод ООО «ТранссЛес», расположенный в поселке Березовка Красноярского края, мы заехали по пути с выставки «Эксподрев». Нашими гидами на экскурсии по заводу стали генеральный директор ООО «ТранссЛес» Андрей Николаевич Зарва, его первый заместитель Андрей Михайлович Михайлов и мастер основного производства Наталья Владимировна Парамонова.
Знакомство с предприятием и его людьми показало, что ситуация на заводе далека от блестящей, и, надо признать, его руководителям не отказать в мужестве - открыто рассказывать о трудностях прошлого и настоящего, при этом всерьез задумываясь о перспективах развития. И именно эта откровенность убеждает в том, что самые смелые планы этих людей осуществимы.
ООО «ТранссЛес» занимает площадь 9,8 га в пгт. Березовка. На этой территории располагается как основной производственный цех, так и административные, складские и иные помещения - котельная и т. п.
Проектная мощность предприятия в год: 4800 м3 мебельного щита, 7200 м3 клееного оконного бруса, 16 000 м3 профильных погонажных изделий.
Вся продукция предприятия сертифицирована.
Немного истории. Проект - и прожекты
Незадолго до новогодних праздников 2009 года в Березовском районе состоялось торжественное открытие нового лесоперерабатывающего завода. Местные СМИ тогда писали: «Здесь будут изготавливать мебельный клееный щит в объеме 5280 м3 в год, клееный оконный брус (4000 м3 в год) и профильные погонажные изделия (18 000 м3 в год): паркет, вагонку, различный облицовочный материал, блок-хаусы, евроотделку - все только из массива древесины. Товар востребован на европейском рынке: в Германии, Австрии, Чехии; странах СНГ: Прибалтике, Молдавии, Украине. Ждет его и Азия: Корея, Китай, Япония... Компания намерена направлять половину продукции за рубеж, оставляя 50 % краю.
Новый завод - это и новые рабочие места для жителей Березовского района и Красноярска.
Объем инвестиций в проект составил 850 млн руб. Срок окупаемости предприятия - пять лет. Планируемый объем производства - 30 тыс. м3 продукции в год. Налоговые платежи предприятия в консолидированный бюджет Красноярского края составят ежегодно около 50 млн руб».
Но, как это часто случается, задумать - это одно, а воплотить задуманное - совсем другое. Даже немалые средства, вложенные в создание и запуск предприятия, не помогли ему избежать той ямы, в которую как раз в тот момент покатилась вся российская экономика...
Продукция
Андрей Михайлов, первый заместитель ген. директора ООО «ТранссЛес»
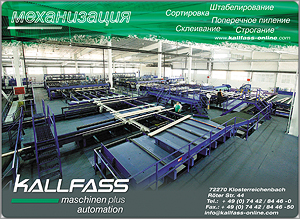
Kallfass. Механизация лесопильных и деревообрабатывающих заводов. Оборудование для штабелирования, сортировки, поперечного пиления, склеивания, строгания
Основной вид деятельности завода - переработка пиломатериалов в мебельный щит и профильные погонажные изделия: элементы лестниц, доска пола, плоские обшивки, террасная доска.
Изначально на «ТранссЛесе» планировалось также производить высококачественный садовый паркет из сибирской лиственницы. Однако, по словам первого заместителя директора завода, паркетную линию временно законсервировали: «На паркет пока нет качественного сырья», - признает Андрей Михайлов.
Сырье
«У нас два основных поставщика, с которыми заключены договоры, поставки от них гарантированны и стабильны. Оба находятся в Сибири. Расстояние довольно большое - 800-900 км, но зато мы всегда уверены в том, что будем полностью обеспечены сырьем, - с удовлетворением отмечает руководитель предприятия. - Получаем пиломатериал двух типов: центральную доску и боковую доску. Боковая идет на погонаж, центральная (толстая) - на изготовление щитов. Закупается все сразу».
«Брака в поставках практически не бывает, - отмечает Андрей Михайлов. - Поставщики стараются подстраиваться под наши весьма высокие требования. Если все же есть брак, его тут же отправляют обратно».
«Пиломатериалы бывают разных сортов, доска приходит и 1-го сорта, и 4-го. Согласно ГОСТу, должно выдерживаться определенное их процентное соотношение, но выдерживается оно не всегда, - добавляет Наталья Парамонова. - Приходится перепроверять - для этого у нас работает сортировщик».
Итак, поставщиками сырья для предприятия являются ЗАО «ЛДК-Игирма» и ООО «Транссибирская Лесная компания» из Иркутской области. Общий объем поставок составляет 30 000 м3 пиломатериалов в год. Сырье - пиломатериалы из лиственницы - поставляется на склад предприятия автомобильным транспортом непосредственно со склада продавца, железнодорожным транспортом - на тупик «В - Сибпромтранс» Красноярской железной дороги, далее автотранспортом «В - Сибпромтранс» на склад сырья ООО «ТранссЛес». Плечо доставки от тупика до склада предприятия составляет около 7 км.
Выгрузка пакетов из автотранспорта осуществляется вилочным погрузчиком Komatsu 150. Пакеты пиломатериалов подаются на приемный стол-разобщитель пакетирующей установки Kallfass для формирования сушильных пакетов либо устанавливаются в штабеля буферной зоны склада, который рассчитан на хранение запаса сырья в объеме 5000 м3. Производительность пакетирующей установки Kallfass составляет около 45 000 м3 в год при односменном режиме работы (8-часовая рабочая смена).
Сушильные пакеты при помощи вилочного погрузчика Komatsu формируются в штабеля перед сушильными камерами для формирования партии либо устанавливаются непосредственно в сушильные камеры.
Во время формирования сушильных пакетов производится выборочная приемка пиломатериалов на предмет соответствия по качеству. Учет сырья ведется на каждом этапе его движения.
Сушка древесины
Некачественная сушка приводит к сокращению сроков службы деревянных изделий и значительным потерям материала. Поэтому сушка пиломатериалов - одна из важнейших технологических операций в деревообработке. Отработанная специалистами «ТранссЛес» технология сушки древесины позволяет получать материал без внутренних напряжений.
«Мы находимся возле сушильных камер, в которые загружается сырой пиломатериал, а выходит с необходимой по технологии влажностью, от 8 до 10%, - рассказывает генеральный директор «ТранссЛеса». - Всего их шесть, камеры фронтальной загрузки периодического действия Eisenmann (Германия). Объем каждой камеры от 180 до 220 м3.
Общий объем разовой загрузки всех камер составляет 1320 м3 условного материала. А условный годовой объем сушки с учетом поступления от поставщиков пиломатериалов транспортной влажности - 31 200 м3. Загрузка осуществляется при помощи вилочного погрузчика Komatsu 150 непосредственно в камеры сушки.
При загрузке камеры в восемь пакетов, находящихся в разных местах сушильного штабеля, устанавливаются датчики контроля влажности древесины, по показаниям которых процесс сушки ведется в автоматическом режиме по заданной оператором программе. В случае возникновения нештатной ситуации управление процессом можно перевести в ручной режим. Пиломатериалы для производства мебельного щита подвергаются сушке до влажности 8±2% (за исключением доски пола). Высушенные пиломатериалы выгружаются из камеры и хранятся до момента переработки под навесом буферной зоны "сухого двора" сушильного отделения. Буферная зона рассчитана на хранение до 1300 м3 сухих пиломатериалов».
«Мы получаем лиственницу влажностью 17-20%, - говорит Андрей Зарва. - За счет того, что она уже частично высушена, период сушки сокращается до 8-10 суток. Мы ее как бы досушиваем. Часть камер работает на сушке естественной влажности, а другая - на транспортной до необходимой влажности. Не всегда так получается, но стараемся, чтобы соотношение в работе сушилок было 50/50.
Сушильных камер нам хватает. Сушилки никогда не работали все вместе, одна всегда "отдыхает". Поэтому пока мы не планируем проводить реконструкцию или модернизацию».
Цех глубокой переработки
Разумеется, главный объект нашего интереса - производственный комплекс. Чтобы показать все этапы технологического процесса, нас приводят в просторный корпус, где шумят внушительные станки и приятно, будто в детстве, пахнет свежеобработанным деревом.
«В этом цеху у нас располагается все основное производство, - комментирует Андрей Михайлов. - Станки на всех участках - марки Weinig. Вот прямо впереди вы можете видеть линию оптимизации, на которой доска оптимизируется и распускается на ламели различной длины, в зависимости от того, сколько и каких в ней было обнаружено пороков. После определения пороки древесины обрезаются на торцовочных станках в автоматическом режиме, затем ламели перемещаются на линию сращивания. Здесь производиться сращивание ламелей на мини-шип, после чего они проходят чистовую строжку и идут на линию прессования, чтобы стать мебельным щитом. А вот и второй участок чистовой строжки, где мы строгаем профильные изделия - доску пола, вагонку. Именно здесь так называемая евровагонка проходит финальную обработку и далее попадает на упаковку...»
Мы идем вдоль станков, стараясь рассмотреть технологические участки подробнее.
Производство готовых профильных изделий и мебельного щита ведется в цехе, можно сказать, параллельными курсами. Для удаления мелких древесных отходов (стружки, опилок, щепы) все станки оборудованы воздуховодами Dantherm, которые составляют единую систему аспирации цеха.
Участок предварительного строгания
Оптимизирующий станок Weinig Opticut S50
Узел подачи заготовок для строгания
На участке предварительного строгания, как уже упоминалось, производится строгание пиломатериалов в заданный размер с распиливанием их на бруски (ламели) для дальнейшего производства мебельного щита. Здесь установлен четырехсторонний строгальный станок Weinig Hydromat 2000 с четырьмя строгальными и одним пильным валом (производительность при работе в односменном режиме - около 13 000 м3 входящего пиломатериала в год).
Пиломатериалы, прошедшие камерную сушку, подаются в цех вилочным погрузчиком с боковым захватом Hubtex и устанавливаются на приемный стол-разобщитель строгального станка. По поперечному цепному транспортеру пиломатериал поступает к устройству поштучной выдачи в строгальный станок, оснащенный четырьмя строгальными валами и одним пильным валом. Входящие пиломатериалы строгаются с четырех сторон и распиливаются на бруски при помощи дисковых пил, установленных на пятом валу.
По продольному ленточному транспортеру калиброванные бруски перемещаются от станка на поперечный цепной оценочный транспортер, где операторы двух торцовочных станков с системой оптимизации Weinig OptiCut 450 Dimter Line оценивают качество каждого бруска с четырех сторон и либо оставляют брусок цельным (укладчики формируют из них пакет), либо наносят на брусок разметку для оптимизации (вырезки дефектов).
Ламели с разметкой по одной проходят через торцовочный станок с системой оптимизации, где при помощи оптического глазка считывается разметка, после чего на торцовочную пилу подается сигнал с заданием, в каких местах необходимо сделать резы.
Weinig OptiCut 450 Dimter Line справляется с древесиной практически любого качества, включая искривленные и покоробленные доски. Система линейных замеров, не связанная с приводом, обеспечивает точность резов ±0,8 мм.
Cтанки укомплектованы запатентованной регулируемой шахтой для отходов с уникальным транспортером VarioSpeed для торцевания без остановок. Cистема полной оптимизации раскроя Weinig Dimter Line обеспечивает максимальный полезный выход при минимальном потреблении древесного сырья: система управления «знает» все данные заготовки и рассчитывает наилучший результат распила еще до того, как будет сделан первый рез.
Полученные ламели переменных длин сортировщики укладывают на поддоны в соответствии с установленным качеством. Цельноламельные бруски погрузчик с боковым захватом Hubtex транспортирует в буферную зону или непосредственно на участок производства мебельного щита. Поддоны с брусками транспортируются на участок сращивания заготовок по длине.
На участке сращивания брусковые заготовки переменных длин сращиваются на зубчатое горизонтальное клеевое соединение - горизонтальный закрытый микрошип. Максимальная длина сращенных брусков - 6 м. Сортировщики укладывают разнодлинные брусковые заготовки в ячейки цепного поперечного транспортера, по которому они поступают в первый шипорезный агрегат линии торцевого сращивания Weinig HS120 GreCon Line. Жесткое позиционирование заготовки и раздельный шипорезный узел позволяют получать стабильное качество торцевого соединения в ламелях. При прохождении бруска через шиповой агрегат с торца каждой заготовки отдельно нарезается шип-паз с «полочками», далее заготовка поступает во второй шипорезный агрегат, где нарезается шип-паз другого торца. Бруски с нарезанными с двух сторон шипами поштучно подаются на клеенаносящую гребенку и плотно сращиваются по шиповому соединению торец в торец. При наборе заданной длины ламели торцовочная пила в автоматическом режиме делает рез, на сращенную ламель с торцов и сверху подается давление. Запрессованная сращенная ламель толкателем выбрасывается на приемный стол, откуда рабочие забирают ее и укладывают в пакет, каждый ряд ламелей в котором разделяется прокладками. После сращивания бруски подвергаются технологической выдержке для высыхания и отверждения клея. При сращивании заготовок используется клей на основе ПВА Kleiberit 303.7 для водостойких соединений согласно нормам DIN/EN 204.
Стеновая обшивка «Штиль»
Производительность линии сращивания на горизонтальный шип-паз GreCon HS120 при работе в односменном режиме - 2260 м3 брусков в год. При необходимости возможен переход на двухсменный 11-часовой режим работы, в этом случае производительность повышается до 4300 м3 в год.
Линия шипового сращивания, компактная установка Weinig Ultra TT GreCon Line обеспечивает все преимущества передовой технологии GreCon: высокую производительность и гибкость в использовании. Модель имеет передвижной разворотный стол. В типовом исполнении линия предназначена для обработки заготовок шириной до 205 мм, длиной 150-1000 мм, однако при необходимости возможна подача в станок двух- и даже трехметровых заготовок. Если же увеличить усилие прессования до 160 кН (16 т), на этой линии можно с высокой безопасностью и точностью фрезеровать заготовки довольно большого сечения.
Строгание заготовки перед склейкой в щит ведется на станке Weinig Unimat Super 4 - это узкоспециализированный станок, который выполняет только одну операцию: 4-стороннее строгание. При этом за счет конструкции строгально-фрезерной головки пласти заготовки строгаются, а бока фрезеруются, что обеспечивает максимальную адгезию при склейке.
Участок чистового строгания оснащен четырехсторонним строгальным станком Weinig Hydromat 2000 с девятью строгальными валами (производительность около 6500 м3 входящего пиломатериала в год при работе в односменном режиме). Станок предназначен для строгания сращенных брусков в заданный размер для дальнейшего производства мебельного щита, а также для производства профильных погонажных изделий.
При строгании сращенных брусков в заданный размер пакет брусков подается вилочным погрузчиком с боковым захватом на стол-разобщитель строгального станка, откуда бруски послойно скатываются на оценочно-торцовочный стол, оснащенный поперечными цепями и двусторонним проходным торцовочным устройством, в котором в качестве инструмента используются дисковые пилы. Бруски проходят через дисковые пилы, где производится прирезка брусков в установленный размер. Далее при помощи устройства поштучной выдачи бруски поступают в строгальный станок. Строганный с четырех сторон брусок по продольному ленточному транспортеру от станка передается на поперечный цепной транспортер с оценочным столом. Здесь бруски собираются в ковер на «лыжах» пакетоформирующей машины, с помощью которой они укладываются в плотный пакет и далее транспортируются при помощи погрузчика с боковым захватом на участок производства мебельного щита.
При производстве профильных погонажных изделий пакет сухих пиломатериалов погрузчиком подается на стол-разобщитель строгального станка, откуда доски послойно скатываются на поперечный цепной оценочный стол, на котором перед прохождением через торцовочное устройство оператор визуально оценивает каждую доску и ориентирует лучшую пласть вверх или вниз, в зависимости от профиля погонажного изделия. Далее ориентированные доски поступают в строгальный станок. Профилированное изделие при помощи ленточного транспортера передается на поперечный цепной оценочный стол, на котором контролеры качества визуально оценивают продукцию и присваивают ей соответствующий сорт. При помощи пакетоформирующего устройства профилированные изделия укладываются в плотный пакет и при помощи погрузчика с боковым захватом транспортируются на участок упаковки палет в термоусадочную пленку.
На участке производства мебельного щита (горячее прессование) цельные и сращенные ламели склеиваются в мебельный щит. Он оснащен прессом проходного типа Weinig ProfiPress 4500 Dimter Line (особенностью этого пресса является нагрев клеевого шва токами высокой частоты - ТВЧ), двусторонним торцовочным станком проходного типа ЕiМА TipDK120 и форматно-раскроечным станком Altendorf WA 80.
Пакет брусков, предназначенных для склеивания мебельного щита, при помощи погрузчика с боковым захватом устанавливается перед наборным столом пресса. Сортировщики набирают ламели одного сорта и укладывают на поперечный цепной стол, с которого при помощи устройства поштучной выдачи ламели поступают на ленточный транспортер, проходят через клеенаносящую гребенку и подаются толкателями на поперечный транспортер формирования ковра щита перед загрузкой в пресс. Время нагрева и прессования составляет всего около 3 мин. Производительность пресса ТВЧ при работе в двухсменном 11-часовом режиме составляет около 5400 м3 щитов в год.
После освобождения плит пресса от предыдущего щита подготовленный ковер заготовок в автоматическом режиме подается на прессование. После выхода из пресса щит укладывается на рольганг двустороннего торцовочного станка проходного типа ЕiМА, где производится обрезка кромок щита по заданным размерам, после чего с обеих сторон щита зашпатлевываются дефектные места. Щиты укладываются в пакеты (с прокладками через каждый ряд) и выдерживаются до полного отверждения клея и шпатлевочного состава. Для склеивания щитов применяется клей на водной основе (ПВА) Klebit 303.2.7 со степенью водостойкости D3.
Пакеты щитов, прошедших технологическую выдержку, погрузчиком подаются на односторонний двухвальный шлифовальный станок, где пласти щитов шлифуются по одной за каждый проход. После шлифования щиты поступают на участок упаковки в термоусадочную пленку, либо на промежуточный буферный склад, с которого партия щитов подается на участок раскроя щитов на элементы.
Участок производства мебельного щита (холодное прессование) предназначен для склеивания цельных и сращенных ламелей в мебельный щит и оснащен клеенаносящим устройством, роторным прессом Polzer VS-H4E и торцовочным станком Weinig OptiCut 50 Dimter Line.
Здесь пакет брусков при помощи погрузчика с боковым захватом устанавливается перед клеенаносящим устройством. Сортировщики набирают ламели одного сорта, оператор пресса подает ламели на клеенаносящие вальцы, помощник оператора и укладчик формируют ковер щита на раме пресса, устанавливают и фиксируют прижимы, поворачивают заполненную раму пресса для освобождения и заполнения следующей рамы. Вышедший из прессования щит укладывается в пакет с прокладками через каждый ряд, шпатлюется и выдерживается до полного отверждения клея и шпатлевочного состава. Производительность роторного пресса при работе в односменном 8-часовом режиме - около 2250 м3 щитов в год.
Пакеты щитов, прошедших технологическую выдержку, погрузчиком подаются к торцовочному станку, где производится прирезка щитов в заданный размер. Если щит имеет ширину более 300 мм, пакеты подаются при помощи погрузчика к двустороннему торцовочному станку проходного типа ЕiМА, где производится прирезка щитов в заданный размер. Прирезанные щиты устанавливаются на двухвальный шлифовальный станок для обработки пластей щитов (по одной за проход).
По завершении шлифования щиты поступают на участок упаковки в термоусадочную пленку или на промежуточный буферный склад, откуда партия щитов подается на участок раскроя щитов на элементы.
Участок шлифования мебельных щитов (Weinig)

Трансслес. Производство мебельного щита
и погонажных изделий из лиственницы
На участке шлифования мебельных щитов поверхности щитов шлифуются для придания им необходимой степени шероховатости. Здесь установлен односторонний двухвальный шлифовальный станок Optimat SCO 243 производительностью 7700 м3 щитов в год (при работе в двухсменном 11-часовом режиме).
Боковой вилочный погрузчик доставляет пакет со щитами к шлифовальному станку, оператор и укладчик вручную подают щиты по одному в станок. На выходе из станка шлифованные щиты принимают укладчики и переворачивают их обработанной стороной вниз. После того как все щиты прошлифованы с одной стороны и уложены в пакет, их снова устанавливают перед станком, повторяя те же операции со второй стороной щита. На торец каждого шлифованного щита ставится знак сортовой принадлежности, после чего они поступают на участок упаковки в термоусадочную пленку.
Рассказывает Андрей Михайлов:
«На шлифовальном станке работают четыре человека: двое подают щит на станок, двое принимают. Загрузка односторонняя: щиты из пакета по одному шлифуются с одной стороны, переворачиваются, после чего пакет повторно подается на шлифование обратной стороной. Хотим заменить станок, но пока еще не решили, на какую модель и какой фирмы».
Комментирует мастер основного производства Наталья Парамонова:
«При шлифовании щита на подаче стоит станочник, а на приемке - укладчик. Сортировщиками работают в основном девушки: принимают подвезенные пакеты и сортируют щиты по нескольким сортам, отбирают щиты по качеству и тангентал с радиалом разделяют, сортируют по качеству. Щиты идут не одного сорта, так же как и погонажная продукция. В каждом сорте допускаются определенные пороки. Сырье идет потоком, мы не специально заказываем разные сорта. Сортировщик как раз и сортирует его либо маркирует (на погонаже). Если сортировщиков не ставить, производительность труда резко падает. Потому что нужно набрать определенное количество брусков, чтобы собрать щит. Ручного труда тут очень много, хотя и вообще в деревообработке везде требуется ручной труд. Вот для раскроя пиломатериалов по длине заготовки просто выбрасывает на стол, их надо по поддонам разбирать (потому что работает линия сращивания), - и все это вручную. Плюс шлифовка щитов, зарезка щитов...»
Участок упаковывания профильной погонажной продукции в палеты и мебельного щита (каждого индивидуально) в термоусадочную пленку оснащен упаковочными машинами Fischer SFV-800/N и Kallfass 1200.
Профильные погонажные изделия доставляются боковым вилочным погрузчиком к упаковочной машине Fischer, оператор с помощником укладывают их в стопу изделий одного сорта и направляют палету по роликовому транспортеру в пленочный рукав, далее палета перемещается в термокамеру. На выходе из термокамеры укладчики снимают палету и укладывают на поддон в соответствии с сортом продукции. Одновременно упаковываются изделия только одной длины.
Изделия, которым для повышения качества требуется дополнительная обработка, укладывают в отдельный пакет и транспортируют к станку Opticut S50, где производится вырезка дефектных мест. После этого продукцию также упаковывают в термоусадочную пленку. Поддоны с палетами передают на склад готовой продукции.
Подобным образом производится упаковка щита: готовые мебельные щиты при помощи бокового вилочного погрузчика устанавливаются перед упаковочной машиной Kallfass 1200; оператор и укладчик вручную разматывают из рулона термоусадочную пленку, укладывают на нее щит, обрезают пленку по длине щита, подворачивают ее и направляют щит в термокамеру, на выходе из которой укладчики укладывают упакованный щит на поддон. Заполненный упакованными щитами одного сорта и размеров поддон передается на склад готовой продукции.
Склад готовой продукции
Поступающие на склад из цеха основного производства пакеты с готовой продукцией оборачивают в полиэтиленовую пленку и упаковывают полиэстеровой лентой. На транспортный пакет крепится ярлык с информацией о продукте.
На складе готовой продукции производится ответственное хранение (склад рассчитан на одновременное максимальное хранение 2000 м3 готовой продукции), отсюда же продукция в транспортных пакетах отгружается покупателю - в автотранспорт вилочным погрузчиком Komatsu согласно спецификации, выданной на склад отделом сбыта.
Котельное хозяйство, тепло- и водоснабжение предприятия
Проектом предусмотрен замкнутый цикл производства: отходы деревообработки доставляют механизированными транспортерами в дробилку и после измельчения в щепу они поступают в котельную, где в автоматическом режиме подаются дозатором на сжигание.
Котельное хозяйство предприятия состоит из трех котлов Lambion мощностью 2,2 МВт каждый, с собственной водоподготовкой. Котельная отапливает производственные и административные здания, снабжает теплом сушильный комплекс.
Водоснабжение предприятия осуществляется из собственной скважины (5 м3 в час) через водонапорную башню, оборудованную системой водоподготовки. Давление в системе - 1,8 атм.
Обслуживание и ремонт. Проблемы и решения
«Если говорить о технологическом процессе, нужно признать, что некоторые виды оборудования изначально не были правильно согласованы друг с другом по мощности, - говорит Андрей Зарва. - Это создает определенные проблемы. В одних случаях мы изменяли конфигурацию линий, а какое-то деревообрабатывающее оборудование даже было выведено из эксплуатации. Так, делительную линию мы просто убрали и, скорее всего, больше не поставим. Также оказалось, что при минусовых температурах оборудование Kallfass дает сбои либо не работает вовсе. Нормально функционирует до минус 15, а дальше начинаются сложности. Приходится дополнительно обогревать помещение».
Специалисты Kallfass при заключении договора обращали особое внимание прежнего руководства «ТранссЛеса» на то, что на всех линиях, работающих в условиях пониженных температур, рекомендуется устанавливать гидравлические элементы. Именно гидравлика, в отличие от более дешевой пневматики, при низких температурах может обеспечить бесперебойную работу оборудования. Однако, несмотря на предупреждения поставщика, клиент тогда сделал выбор в пользу экономии средств.
«Надо правильно понимать, что приближается такое время, когда оборудование начинает ломаться просто по причине износа, - добавляет Андрей Михайлов. - Вот, например, с сушильными камерами до последних дней все было в порядке, а недавно отметили небольшую неприятность: потолок из нержавеющей стали проржавел. Причем это в одной камере, а в других только начинает. Наверное, от влаги и высокой температуры.
В общем, пока необходим только мелкий ремонт, и нам проще содержать своего ремонтника, чем приглашать кого-то от поставщиков. Для экономии и ускорения сервисных работ я планирую собрать собственную группу слесарей и мастеров, которые знают все нюансы конкретного производства и будут работать наиболее эффективно».
Персонал
«Я пришла на завод в конце 2008 года, прямо к его запуску, - рассказывает Наталья Парамонова. - К тому моменту здесь уже было установлено то оборудование, которое вы видите сейчас, - все совершенно новое, "в масле". Раньше здесь было законсервированное предприятие. Многое было построено "с нуля": склады, гараж, цех основного производства, сушильные камеры, котельная. В начале января 2009 года приехали немцы - специалист от производителей оборудования (Weinig) и несколько наладчиков. Месяц они настраивали станки и обучали рабочих. Главное, чему учили: правильно работать на тех конкретных станках, что установлены в цеху. Некоторые из тогдашних "учеников"-рабочих до сих пор работают тут. Говорю "некоторых" потому что были в жизни завода тяжелые времена, когда не платили зарплату, ушло много людей. Да вы сами помните 2009-2010 годы. За это время и руководство предприятия менялось раза два или три...»
«На протяжении пяти лет зарплата не поднималась. Вовремя выплачивать ее стали только с приходом новой команды, - продолжает Наталья Владимировна. - Такого, можно сказать, не было никогда. Аванса, как такового, практически не существовало, а задержка денег редко когда была меньше месяца. А сейчас все четко и вовремя!»
«Да уж, не могу не похвастаться, - улыбается Андрей Зарва. - Я впервые за всю историю завода "ТранссЛес" поднял зарплату рабочим...»
По проекту, общее количество работников на заводе при полной загрузке - 132 человека. Сейчас работает 111, из них 5 - административно-управленческий состав, в основном и вспомогательном производстве, ИТР и специалистов - 106 человек.
Часть людей работают с 8 до 17 в режиме пятидневки, но есть и те, кто работает посменно с 8 до 8, в 2 смены, - это вынужденная мера для участка прессования щита, который иначе не справляется с объемом. Это «узкое место» производства, заложенное еще при проектировании.
«Проблема с людьми была, есть и, наверное, будет, - говорит Андрей Михайлович. - Кто-то приходит, кто-то уходит. Стараемся привлекать молодежь, обзваниваем лесные техникумы. Конечно, сегодня этот вопрос уже стоит не так остро, как прежде».
«С приходом новой команды руководства количество рабочих увеличилось, - подключается к беседе мастер основного производства Наталья Парамонова. - В первый год набрали 60 человек, но потом люди стали увольняться, и уже никого на их место не принимали. Списочная численность работников сократилась до 32-33 человек. А сейчас единовременно в течение дня 37-38 человек работает в цеху.
Коллектив на предприятии по большей части молодой - средний возраст работников 32 года. Персонал в основном из Сосновоборска, Березовки и близлежащих деревень, но есть люди и из Красноярска (их примерно 20%), для них организованы развозки на микроавтобусе с утра и вечером.
Подобрать в наше время квалифицированные кадры очень сложно: деревообрабатывающих предприятий мало, а с оборудованием такого уровня, как наше, - просто очень мало. Неподготовленного человека к подобным станкам не поставишь. Поэтому опыт работы активно приветствуется. Если же нет, что делать - сначала берем укладчиком и там приглядываемся: я к ним, они - ко мне. Если у человека есть желание и позволяют способности, мы беремся за его обучение и после подготовки по технике безопасности переводим на место станочника, сортировщика или оператора. Хочется надеяться, что проблемы с персоналом остались позади: к примеру, на сегодняшний день у нас только одно место станочника свободно. Желающие есть, потому что зарплата у рабочих сейчас хорошая, но мы не спешим переводить работников с других должностей. Есть небольшая проблема с укладчиками, там зарплата пониже, но и работа не требует особой квалификации».
Специфика, нюансы, достоинства
«Главная особенность нашего завода заключается в самой древесине, которую мы используем для производства изделий, - говорит директор «ТрассЛеса». - Лиственница очень долго не подвергается гниению, сама по себе прочная и очень красивая по текстуре.
Для лиственницы необходимы особые режимы обработки. Например, при сушке. Она сохнет с естественной до необходимой влажности около месяца. Процесс довольно долгий. Вода плохо выгоняется из нее из-за высокого содержания смолы. Потому же она и обрабатывается тяжелее, чем, например, сосна. Требуются более мощные станки и больший расход инструмента.
С этим связана еще одна особенность предприятия - высочайший уровень установленного оборудования, которое позволяет достигать и соответствующего качества готовой продукции, относящейся к премиум-классу. Впрочем, есть у нас и продукция эконом-класса. Вся она типовая, массовая - что погонаж, что мебельный щит. Это позволяет с помощью отработанной технологии и благодаря хорошему качеству входящего сырья получать гарантированно качественную продукцию. Ну и отсюда же наше дополнительное преимущество - оперативность выполнения заказа».
Планы на будущее
«Рассудите сами: заводу уже 4 года, и все это время им толком не занимались, работал от случая к случаю, - Андрей Михайлов предпочитает быть реалистом. - Подолгу люди не получали заработанные деньги... Так что первым своим долгом мы считали, извините за случайный каламбур, отдать долги по зарплате. Отдали. Теперь можно ставить себе очередные цели. Так, в следующем году собираемся сделать частичный ремонт котельной».
«Прежде всего мы планируем наращивать объемы выпуска существующей продукции до проектных мощностей, - говорит директор. - Так что новые виды продукции запускать пока не думаем».
«Но кое-какие изменения все же будут, - подхватывает его зам. - В частности, для производства щита хотим переходить на сосну. Точнее, не полностью на нее переходить, а частично добавлять; это обосновано прежде всего некоторым снижением спроса на щиты из лиственницы из-за кризиса в Европе. Погонаж оставляем на 100% лиственничным. Еще рассматриваем вариант шпонирования - тех же сосновых щитов, к примеру. Впрочем, шпонировать мы можем что угодно - это будет выполняться под конкретный заказ клиента».
Мало сделать - нужно продать
«Мы работаем не только с местным рынком - слишком уж тяжело он "переваривает" нашу продукцию, - поясняет маркетинговую стратегию директор завода. - Ради совершенствования сбыта четыре месяца назад создана компания, которая занимается продажами нашей продукции, базируется она в Москве. Продажи идут централизованно через эту компанию. Продаем на Украину, возрождаем старые и организуем новые каналы экспорта. Планируем поставки в Корею, возможно, в Китай. Для этого используются все доступные средства: есть страничка в интернете, плюс какие-то личные связи, контакты и т. д.
В разное время года запросы рынка меняются. Так, допустим, террасная доска весной лучше покупается, но из-за этого объемы производства других изделий мы не уменьшаем. Вся продукция выпускается круглогодично. Лето для нас - сезон максимальной загрузки».
Прощаясь с гостеприимными хозяевами, мы пожелали им и всему «ТранссЛесу», чтобы никакие кризисы и проблемы более не становились преградой на их пути и не сбивали предприятие с правильного курса.
Беседовали Светлана Яровая и Елена Шумейко
Подготовил Максим Пирус
Фотографии: Светлана Яровая
Справка о продукции завода
Мебельный щит - экологически чистое изделие, полученное путем склеивания ламелей, выпиленных из массива натуральной древесины. Используется для изготовления мебели и лестниц. Также применяется при проведении различных видов отделочных работ. Является одним из самых востребованных материалов в строительстве и мебельном производстве. Бывает несращенным (цельным) или сращенным по длине и ширине (клееный щит). Чтобы уменьшить внутреннее напряжение древесины, ламели укладываются друг c другом так, чтобы направление годичных слоев в них не совпадало. Поэтому мебельные щиты практически не деформируются.
Погонажная продукция на ООО «ТранссЛес» изготавливается из лиственницы, отвечает всем российским и европейским стандартам, обладает низкой теплопроводностью и хорошей шумоизоляцией. К ней относятся:
● стеновая обшивка - вагонка самых разных профилей (стеновая обшивка плоская «Штиль», стеновая обшивка плоская «Евровагонка», стеновая обшивка плоская «Имитация бруса»);
● доска пола - очень популярный материал для создания напольного покрытия из древесины, монтируемого по системе «шип-паз» (несмотря на огромный выбор древесных пород, самым лучшим материалом для этой доски является именно лиственница - пол получается особо прочным, влагоустойчивым, износостойким и долговечным; такая доска может служить десятилетиями, не теряя эксплуатационных и эстетических качеств, ведь лиственница известна своей устойчивостью к гниению и короблению);
● террасная доска с нескользящей поверхностью «антислип» - удобное покрытие для террас, беседок, веранд, садовых дорожек, обустройства саун и бассейнов. У террасной доски две лицевые поверхности, пригодные для использования.