Первая мебельная фабрика. Ответственность и честь
Быть первым, лучшим среди многих - и почетно, и трудно в любом деле, а уж в бизнесе и подавно. Ведь к лидеру всегда повышенное внимание: ему завидуют конкуренты, к его продукции предъявляют особые требования потребители, у него нет права на ошибку... Для предприятия, о котором мы расскажем вам сегодня, бремя лидера привычно. Почти два десятилетия эта компания из Северной столицы входит в число лучших мебельных производств страны, выпускает высококачественную востребованную продукцию и среди первых отечественных предприятий осваивает современное оборудование и новейшие технологии. К тому же быть лидером обязывает название: «Первая мебельная фабрика». Поэтому в нашем рассказе слово «первая» будет встречаться часто.
15 сентября 2013 года предприятию, которое при рождении получило название «Мебельная фабрика № 1», исполнилось 68 лет. В течение этих десятилетий в истории фабрики были разные периоды, немало и значимых событий. С самого начала перед ее коллективом ставились серьезные задачи. В первые послевоенные годы в производственных корпусах, которые располагались в центре города, на Петроградской набережной, изготавливали большой ассортимент мебели разного назначения - от табуреток до раздвижных столов, буфетов, первыми в городе освоили производство деревянных кроватей. В 1956 году фабрика была подчинена Управлению местной промышленности. У переименованного в «Древтехдеталь» предприятия изменился профиль - оно выпускало комплектующие из фанеры, которые поставлялись на другие предприятия, и лишь очень незначительную часть объема продукции составляли предметы мебели: тумбочки для больниц, столики для яслей-садов и т. д.
В 1993 году фабрика была реорганизована в арендное предприятие, а позже в акционерное общество «Первая мебельная фабрика». Новое руководство сразу взяло курс на модернизацию оборудования, освоение новых технологий, повышение общей культуры производства, кардинальное обновление ассортимента изделий - на фабрике наладили выпуск высококачественной мебели для кухонь, прихожих, гардеробных, офисов, гостиниц и медицинских учреждений, а также мебельных фасадов и столешниц.
«"Первая" всегда должна быть первой» - таков негласный девиз предприятия, которое стремится идти на шаг впереди конкурентов, внедряя передовые технологии и современную технику. В 1998 году здесь ввели в строй гибкую автоматизированную линию по производству фасадов различной конфигурации из MDF, облицованных декоративными ПВХ-пленками широкой цветовой гаммы. С того времени фабрика не только не зависит от зарубежных поставщиков, но и может обеспечивать мебельными фасадами других производителей мебели.
В 1999 году «Первая» первой из петербургских производителей мебели приняла участие в международной мебельной выставке в Кельне. Дебют оказался более чем успешным: вся выставочная продукция была раскуплена на месте, а фабрика громко заявила о себе, встав в один ряд с ведущими европейскими фирмами.
Выполняя решение правительства Санкт-Петербурга о переводе промышленных объектов из исторического центра города, в 2004 году фабрика построила суперсовременный производственный комплекс общей площадью более 50 тыс. м2 в северо-западной промышленной зоне Санкт-Петербурга. Разработку нового производства и технологических процессов осуществила международная консалтинговая компания Schuler Business Solutions. Постоянное обновление ассортимента продукции, модернизация машинного парка и внедрение новых технологий обеспечивают качественные характеристики мебели на уровне европейских стандартов.
Фабрика является основой большого холдинга, в состав которого входят крупнейшие мебельные центры «Мебель-Сити», работающие в Санкт-Петербурге и Москве, торговый комплекс «Гарден Сити» в одном из районов Петербурга и ряд других компаний. Продукцию предприятия можно купить в специализированных мебельных салонах Санкт-Петербурга и региональных представительствах в Москве, Архангельске, Хабаровске (всего около 20 фирменных салонов). «Первая мебельная фабрика» - участник и лауреат многих международных и российских специализированных выставок, неоднократный победитель конкурса «Общественное признание» в номинациях «За высокие достижения в профессиональной деятельности», «За вклад в создание высокой репутации отечественного предпринимательства», «Социальная значимость предприятия».
В марте 2013 года генеральный директор ЗАО «Первая мебельная фабрика» Александр Шестаков избран президентом Ассоциации предприятий мебельной и деревообрабатывающей отрасли России.
Продукция Первой мебельной фабрики
«Первая мебельная фабрика» предлагает потребителям современные высококачественные кухни на заказ в разных стилевых решениях: классика, модерн, хай-тек, кантри, - а также мебель для прихожих. Для производства используются только качественные, экологически чистые материалы и комплектующие отечественного и импортного производства (главным образом из Германии). Внутренние механизмы, которыми оснащается мебель, выдерживают большие нагрузки, отличаются плавностью хода при выдвижении и закрывании, обеспечены пожизненной гарантией.
Клиенты салонов могут выбрать варианты оформления мебели с фасадами из MDF, облицованной ПВХ-пленками или шпоном, из массива ценных пород древесины, а также декоративное оформление элементами из алюминиевого профиля. Здесь же можно обсудить с дизайнерами комплектацию кухни бытовой техникой самых известных мировых брендов.
Второе важное направление деятельности фабрики - реализация комплексных корпоративных проектов, изготовление и поставка офисной мебели для государственных структур и коммерческих организаций. Среди клиентов петербургского предприятия: Полномочное представительство Президента РФ в Северо-Западном федеральном округе, Конституционный суд РФ в Санкт-Петербурге, Государственная дума РФ, Константиновский дворец в Стрельне, Управление охраны по Северо-Западному федеральному округу ФСО России, Управление ФСБ России по Санкт-Петербургу и Ленинградской области, МЧС России, Северо-Западная Академия государственной службы, АО «Ленэнерго», компания «ЛенСпецСМУ», администрации Петроградского, Кировского, Невского районов Санкт-Петербурга, Жилищный комитет Санкт-Петербурга, Управление юстиции по Санкт-Петербургу, ТРК «Петербург», ЗАО «Балтийский банк», Газпромбанк, Петрокоммерцбанк, Внешторгбанк, Сбербанк России и другие организации и фирмы. Кроме того, компания участвовала в реализации значимого государственного заказа - реконструкции и реставрации Государственного Эрмитажа. С мая 2013 года петербуржцы и гости Северной столицы могут любоваться прекрасными интерьерами новой сцены всемирно известного Мариинского театра. Фабрика поставила мебель и интерьерные элементы зрительного зала, оркестровой зоны, гардеробных, всех общественных зон, кабинетов, гримерных комнат, а также музыкальное оборудование и оборудование для ресторанов и зоны кухни. Генеральный директор ЗАО «Первая мебельная фабрика» Александр Шестаков с гордостью отмечает, что, помимо Мариинки, фабрика поставила мебель для Петербургской филармонии, Александринского театра, Дворца дружбы в Республике Башкирия. Один из недавних значимых проектов компании - поставка мебели для государственного комплекса «Дворец конгрессов» в Стрельне, где проходил саммит G20.
Многолетний опыт работы накоплен фабрикой в сфере комплексного оснащения отелей, среди которых Park Inn и «Ибис Санкт-Петербург», городские и загородные гостиницы, мини-отели, крупные санатории и объекты Олимпиады 2014 (санаторий «Сочи», корпус «Приморский»).
«Первая мебельная» осуществляла поставки и для ряда медицинских учреждений: Медицинской академии последипломного образования, ФГУ «Рублево-Звенигородский лечебно-оздоровительный комплекс», санатория «Белые ночи» (г. Сестрорецк), больницы Российской академии наук, Управления ветеринарии Санкт-Петербурга, ФГУЗ ВЦЭРМ им. А. Н. Никифорова МЧС России, НИИ кардиологии, Института им. Д. О. Отта РАМН.
Секрет успешной работы предприятия - в точном соблюдении технологии и постоянном контроле качества.
Производство на Первой мебельной фабрике
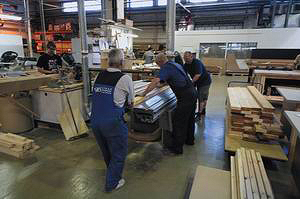
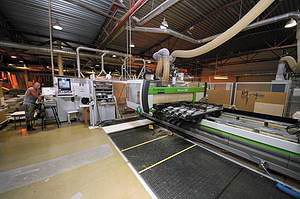
Обрабатывающий центр Biesse Rover C9 используется для фрезеровки, присадки и кромкооблицовки криволинейных деталей
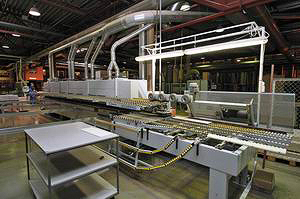
Кромкооблицовочный станок Homag Optimat KAL-310, оборудованный системой возврата детали Boomerang
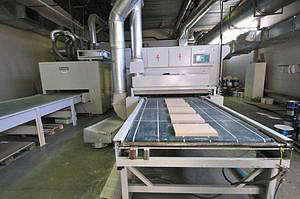
Автоматизированная лакокрасочная установка на
участке окраски фасадов
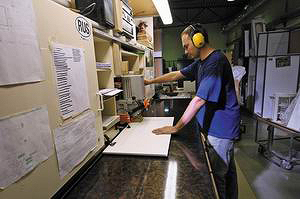
Автоматизированная присадка и запрессовка мебельных петель на прессе Blum
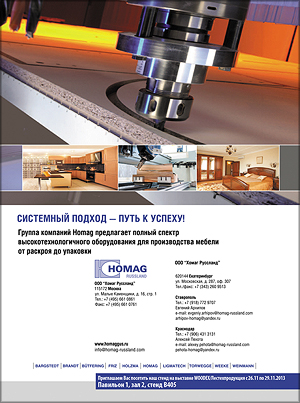
Homag. Деревообрабатывающее оборудование
Именно современные технологии, для реализации которых предприятие оснащено высокопроизводительным оборудованием, лежат в основе производственных процессов на «Первой мебельной». Генеральный директор фабрики Александр Шестаков подчеркивает: «Для того чтобы делать хорошую мебель, у нас есть все необходимое: современное предприятие, оборудованное новейшими автоматизированными линиями, экологически чистые материалы, мастерство дизайнеров, и главное - желание помочь всем, кто приходит к нам».
Компания дорожит своими клиентами и неизменно подтверждает высокое качество продукции. На основании положительных результатов аудита компании орган по сертификации системы менеджмента качества высоко оценил деятельность фабрики, отметив передовые подходы в управлении производственными процессами предприятия, и подтвердил сертификат соответствия ГОСТ Р ИСО 9001-2008 (ИСО 9001:2008) на срок до 02.11.2014 года.
Реализация немецкого проекта обеспечила четкое технологическое планирование производства, а внедрение «сквозного» программного обеспечения на всех этапах создания готового продукта позволило повысить культуру производства и свести к минимуму риск возникновения брака по вине так называемого человеческого фактора. Внедрение программного обеспечения дало возможность оперативно получать задания для производства и избавило от излишней рутинной работы при создании технологических карт раскроя. Программное обеспечение фабрики включает три блока. Используя программу 20-20 Design, разработанную для службы продаж, дизайнеры фирменных салонов принимают заказы от клиентов. Блоки Build rite и Cut rite позволяют создавать списки-задания для производства и тем самым оптимизировать производственный процесс. Данные каждого заказа поступают на автоматизированные обрабатывающие комплексы. Готовые детали отправляются на предсборку, а оттуда на погрузочные линии. Продукция грузится прямо в автомашины, без использования лифтов и дополнительных перегрузок.
Для того чтобы увидеть процесс создания мебели на месте, мы отправились на экскурсию по производственным участкам и цехам предприятия. Нашим гидом стал ведущий технолог ЗАО «Первая мебельная фабрика» Вячеслав Гриценок.
Для изготовления корпусов и столешниц на фабрике используются ламинированные древесно-стружечные плиты (ЛДСП) толщиной 16 и 22 мм (поставщики - российские подразделения австрийской компании Egger в городах Шуя и Гагарин), для задних стенок - ДВПО тех же поставщиков, а для фасадов - плиты MDF толщиной 16-19 мм. Это материал высокого качества, экологически чистый, класс эмиссии Е1. На складе всегда есть запас плитных материалов, чтобы при поступлении заказа была возможность быстро его выполнить.
Начало начал в реализации любого заказа - оформление в салоне или на дому у клиента. Создание проекта дизайнер осуществляет на ПК, используя специализированную программу 20-20 Design канадской компании 20-20 Technologies. Это ПО позволяет не только нарисовать будущий комплект мебели, - в нем запрограммирован набор всевозможных мебельных изделий, каталог, на основе которого и формируется будущий заказ. Выбор в пользу 20-20 Design был сделан руководством фабрики еще 10 лет назад. Представленные на рынке отечественные программные пакеты на тот момент были слабоватыми, а большинство зарубежных - недостаточно гибкими (не было возможности самостоятельно редактировать и обновлять каталог). Конечно, были трудности и с внедрением выбранного ПО, но постепенно, в течение нескольких лет специалисты IT-отдела фабрики и поставщик ПО совместными усилиями внедрили его во всех салонах «Первой мебельной фабрики».
По завершении создания заказа на компьютере дизайнера создается файл, на основе которого формируется техническое задание на изготовление комплекта мебели. «В заказе комплекта мебели присутствуют, как правило, стандартные секции (их в нашем каталоге ни много ни мало около двух с половиной тысяч вариантов), но могут быть и нестандартные, - говорит Вячеслав Гриценок. - Стандартизация позволяет максимально автоматизировать производство, сократив время выполнения одинаковых производственных операций, поэтому у нас предусмотрено два технологических процесса и, соответственно, два маршрута движения заготовок - для стандартных и нестандартных секций». Стандартные детали изготавливаются в большом количестве и впрок, после чего отправляются на хранение на буферный склад, где находятся до момента, когда поступит заказ на стандартные секции.
При заказе секций по индивидуальному проекту техническое задание на производство формирует конструктор, который находится на фабрике. Такие детали делаются под заказ, то есть их нет нужды хранить на буферном складе.
Управление производством осуществляется в другом ПО того же канадского разработчика - 20х20 Inside. В этом программном пакете определяется, какое именно оборудование, какие технологические операции и какие комплектующие будут задействованы в процессе создания комплекта мебели.
Раскрой плит на детали
Первым этапом производства корпусов и фасадов для мебели можно считать раскрой плит на заготовки. В соответствии с заказом на складе берется плита ЛДСП или MDF определенной толщины и необходимой расцветки, которая поступает на раскроечные станки. Групповой раскрой плит на детали для стандартных секций осуществляется на станке Holzma Optimat HPL 11 (на нем одновременно можно раскраивать пять листов материала). На рабочий стол второго станка - Holzma Optimat HPP 250 - плиты загружаются оператором с помощью вакуумного погрузчика.
Затем плиты раскраивают на детали в соответствии с заданием, которое содержится в памяти станков с ЧПУ, после чего полученные детали укладывают в пачки и отправляют на облицовку кромки.
Если же заказчику требуется особая секция, которой еще нет в каталоге 20-20 Design, изготовление нестандартных деталей пойдет по другому маршруту. Раскрой нестандартных деталей выполняется поштучно на станке марки Holzma Optimat HPP 250.
Здесь оператор принимает более активное участие в процессе раскроя: укладывает плиту на приемный стол станка, запускает процесс раскроя в соответствии с исполнительным файлом, который поступил в ЧПУ станка от конструктора, контролирует правильность выполнения операции и размеры полученной детали. Для того чтобы готовые детали для конкретного заказа не потерялись и не перепутались с другими, они маркируются. Когда готовая деталь выходит из станка, на печатающем устройстве, подключенном к оборудованию, распечатывается этикетка со штрих-кодом и информацией о детали, которую оператор наклеивает на эту деталь, а затем укладывает деталь на тележку.
Облицовка кромок
По таким же схемам, как и раскрой - исходя из статуса заказа (стандартный или индивидуальный) - выполняется следующая технологическая операция - кромкооблицовка деталей. Облицовка унифицированных деталей ведется на четырех станках. Довольно интересным нам показалось технологическое решение на базе станка Combima (производитель - фирма IMA). «Облицовка кромки здесь осуществляется сразу целыми пачками, - рассказывает Вячеслав Гриценок. - Станок настраивается на необходимую программу, пачка деталей подается в загрузочный отсек, где они автоматически укладываются на рабочий стол и за один проход каждая деталь облицовывается с четырех сторон. Это машина проходного типа. Деталь движется по столу, два агрегата облицовывают ее кромкой с противоположных сторон, затем деталь попадает на поворотный конус, который разворачивает ее на 90 градусов, после чего такая же машина проходного типа облицовывает кромкой эту деталь еще с двух сторон. На выходе получается пачка деталей одного размера, одного цвета, облицованных кромкой со всех сторон. Затем готовые детали аккуратно укладываются на палеты и отправляются на следующую операцию».
Кромкооблицовка - одна из тех операций, от которых во многом зависит качество и надежность всего изделия, и поэтому руководство фабрики внимательно следит за тем, чтобы оборудование, задействованное на этой операции, постоянно обновлялось. На каждом из станков обрабатывают какие-то определенные детали. Выбор станка, на который отправляется стандартная деталь, запрограммирован в маршрутах движения деталей по производству.
Для кромкооблицовки деталей, предназначенных для нестандартных секций, используется односторонний станок BRANDT Optimat KDF-350C. Оператор вручную укладывает деталь на рабочий стол именно так, как требуется по техническому заданию. Для облицовки детали со всех сторон оператор должен четырежды запустить ее по кругу.
«А вот эти два станка используются для облицовывания деталей как стандартных, так и нестандартных секций. Один из них - IMA Novimat/I/G80 куплен в прошлом году, второй - Homag Optimat KAL-310 оборудован системой возврата детали Ligmatech Boomerang ZHR 05. Особенность конструкции этих станков в том, что заготовка проходит обработку и возвращается к оператору. Кроме того, на этих станках можно облицовывать детали не только АБС или меламиновой кромкой, но и шпоновой - в том случае, если обрабатываются детали, облицованные шпоном, - рассказывает ведущий технолог фабрики. - Но это все оборудование, предназначенное для облицовывания кромкой прямолинейных деталей. Для кромкооблицовки криволинейных деталей на фабрике имеется обрабатывающий центр Biesse Rover C9.
На него поступают прямоугольные детали с необлицованными кромками. С наклеенной на деталь этикетки считывается ее номер. В памяти электронного устройства ОЦ хранится файл с программой обработки и эскизом будущего изделия, соответствующий номеру этой детали. После фиксации заготовки на рабочем столе обрабатывающий центр сначала фрезерует деталь по заданному радиусу, а после этого осуществляет криволинейную облицовку кромки и снимает свесы кромочного материала. Кроме того, на этом обрабатывающем центре можно получать отверстия сложной формы, например, в столешницах под мойки требуемых размеров. Это высокотехнологичное оборудование, поэтому все работающие на нем специалисты прошли обучение. Таких центров у нас несколько. Эти станки оснащены системой защиты, не допускающей получения работниками травмы: фронтальная часть оборудована ковриком, при наступании на который во время обработки детали станок автоматически останавливается, а с остальных сторон рабочая зона огорожена защитными сетками».
Присадка
За операциями раскроя и кромкооблицовки прямолинейных деталей следует присадка, то есть сверление отверстий для крепежа и фурнитуры. И здесь также есть два технологических потока - для обработки стандартных деталей для типовых секций и нестандартных деталей для секций индивидуальных заказов.
Стандартные детали обрабатываются на станке проходного типа Biesse Techno 7, который предназначен для обработки большого количества деталей одинакового размера. В соответствии программой, заложенной в память ЧПУ станка, присадка осуществляется с подовой пласти и двух торцов деталей. После процедуры присадки детали отправляются на буферный склад.
«Присадка деталей по индивидуальным заказам выполняется на станках Biesse Skipper, у нас их два, - говорит Вячеслав Викторович. - Тут такой же порядок, как и при индивидуальном раскрое: конструктор изготавливает конструкторскую документацию и создает исполнительный файл для управляющего устройства станка. Оператор находит в памяти компьютера станка этот исполнительный файл и запускает процесс присадки. Он контролирует точность выполнения заложенной программы и при необходимости может внести в нее изменения».
Изготовление и отделка мебельных фасадов
Для производства фасадов «Первая мебельная фабрика» покупает у немецких производителей плиты MDF толщиной 16-19 мм для глубокого фрезерования. Также в качестве материала для мебельных фасадов используется и массив древесины, например дуба. После раскроя детали в размер она поступает на обрабатывающие центры Biesse Rover C6 и Rover B4, Weeke Optimat BHC 550 и IMA 310.
На этом оборудовании осуществляется фрезеровка фасада, то есть выполняется объемный рисунок по пласти и кромке согласно заказу и требованиям и пожеланиям заказчика. Затем заготовку будущего фасада в зависимости от выбранного заказчиком оформления отправляют на участок облицовывания ПВХ-пленкой либо на покраску.
Облицовывание фасадов пленкой выполняется методом 3D-прессования. Сначала фрезерованная заготовка фасада помещается в клеевую камеру, где очищается от пыли и выкладывается на специальные подкладки. Затем на нее вручную, с помощью распылителя, наносится термореактивный клей фирмы Kleiberit. «В связи с тем, что у нас заказы разноплановые и фасады разного размера, с разными рисунками, лучше человека это никто не сделает, - поясняет Вячеслав Гриценок. - Если бы заказы были одинаковые, можно было бы поставить робота, который выполнял бы однообразную работу».
После того, как клей высыхает, деталь поступает на вакуумный пресс Wemhoner мод. Basic 1000 Variopress с двумя загрузочными столами с рабочей высотой 55 мм и мультифункциональной рамой. Пока заготовка, уложенная на один стол, прессуется, на второй укладывают следующую партию заготовок. В соответствии с заказом выбирается нужная ПВХ-пленка, от рулона отрезается кусок необходимого размера, который укладывается на загрузочный стол, после чего загрузочный стол подается в пресс.
Мультифункциональная рама создает в закрытом прессе систему из трех камер и обеспечивает управление силиконовой мембраной посредством программ прессования, разработанных под различные типы пленок. Горячий воздух подается над силиконовой мембраной на протяжении контролируемого периода времени, обеспечивая определенный уровень провисания мембраны, а в объеме между мембраной и пленкой создается вакуум, обеспечивающий контакт пленки и мембраны в течение заданного промежутка времени. По завершении этого отрезка времени в объеме под пленкой, где располагается заготовка, создается вакуум и одновременно над мембраной подается горячий воздух, который обеспечивает давление, необходимое для прессования. Мембрана прогревает пленки лучше и равномернее, чем горячий воздух, к тому же, плотно прилегая к размягченной пленке, она противодействует проникновению воздуха между пленкой и поверхностью заготовки, исключая срыв всего процесса в случае, если герметичность пленки нарушена.
В связи с тем, что MDF для фасадов уже изначально облицована с одной стороны, клей наносится только на лицевую сторону плиты, ту, которая фрезеровалась. Под действием высокой температуры пленка становится пластичной, мягкой, обтягивает углы и весь рельеф. Охлаждение заготовки выполняется в прессовой камере под давлением - в пространство между пленкой и мембраной нагнетается воздух комнатной температуры, обеспечивая охлаждение и окончательное отверждение пленки, гарантируя таким образом отсутствие деламинации на кромках и углах после раскрытия пресса и снятия давления. При остывании клей схватывает пленку намертво.
Период прессования занимает около двух с половиной минут и зависит от параметров плиты, пленки, клея и иных факторов. Облицованные заготовки необходимо освободить от излишков ПВХ-пленки, которые вручную аккуратно снимают работницы этого участка. В одном и том же заказе обычно большое количество разнотипных фасадов, разного размера, поэтому излишки удаляются вручную.
«Пленки немецкие и итальянские, китайскими материалами мы не пользуемся, - говорит ведущий технолог. - Китайские пленки слишком тонкие, при глубоком рельефе на фасаде высока вероятность их разрыва. К тому же китайским поставщикам из-за больших расстояний, на которые требуется отправлять пленки заказчикам, неинтересно работать с малыми объемами, а европейские компании готовы продавать материалы минимальными количествами - от рулона».
Облицованные ПВХ-пленкой мебельные фасады проходят контроль качества, в ходе которого проверяется, не попал ли случайно мусор под пленку, нет ли еще каких-нибудь других дефектов. Затем фасады еще раз проверяются на соответствие комплектности и упаковываются.
Вообще технология облицовки фасадов пленками ПВХ имеет один недостаток: такие фасады боятся воздействия высоких температур. Максимальная температура, которую выдерживает такой фасад без деформаций, зависит от используемого клея. Клеи Kleiberit позволяют фасадам выдерживать до 120 °C, пар от чайника им не опасен.
Помимо отделки фасадов декоративными пленками, на фабрике налажена отделка заготовок фасадов и боковин мебели эмалями и лаками. Поставки лакокрасочных материалов на предприятие осуществляют несколько компаний, в том числе AkzoNobel; а краски Sayerlack итальянского производства поставляет фирма «Лак-Премьер».
«У нас есть две камеры ручной отделки и автоматическая линия нанесения ЛКМ, с помощью которых мы окрашиваем фасады, а также боковины, отделанные шпоном, - рассказывает Вячеслав Гриценок. - По желанию заказчика мы можем подбирать различные варианты цветового оформления фасадов, их декорирования. Камеры для ручной окраски мы используем для отделки деталей для мебели по индивидуальным заказам. По желанию заказчика можно подбирать эмали, различные варианты цвета, оформления фасадов, их декорирования, например с эффектом серебряной патины. С массивом тоже возможны самые разные комбинации отделки, включая покрытие прозрачным лаком».
С помощью окрасочных пистолетов фасады окрашиваются сначала с обратной стороны, затем с лицевой. Для того чтобы отпыл - облако взвешенных частиц ЛКМ, образующееся при распылении, - не разлетался по всему помещению, в камерах есть вытяжка, мокрый пол и водный фильтр. Вытяжка создает тягу, воздух с крупинками краски подтягивается к воде, и краска оседает в ней, эта смесь потом очищается, а вода возвращается в систему, то есть «Первая мебельная фабрика» не сливает загрязненную воду в канализацию.
Для окраски большого количества однотипных деталей используется автоматизированная лакокрасочная установка.
Оператор укладывает заготовки на загрузочный стол линии, после чего они обдуваются воздухом из форсунок агрегата для обеспыливания, пыль удаляется по системе аспирации. Затем детали поступают в окрасочную камеру HGS DUO/Z Venjakob, где установлен робот, на котором находятся четыре пистолета. Когда заготовка подается в камеру, робот автоматически включается и, двигаясь по запрограммированной траектории, наносит лакокрасочное покрытие на деталь. Затем окрашенные детали отправляются в сушильную камеру Elmab Superfici, где проходят через несколько температурных зон. Температурные режимы задаются в соответствии с программой сушки выбранных деталей. После сушки окрашенные стандартные детали шлифуются на станке Venjakob VBS 1300/40. Штучные детали для индивидуальных заказов, например фигурные рамки, шлифуются вручную.
Изготовление столешниц
Столешницы для выпускаемых кухонь фабрика изготавливает сама. Столешницы могут быть двух видов: из ДСП, облицованной пластиками, или более дорогие - из искусственного камня. Первые наиболее популярны сегодня на массовом рынке, так как при дешевизне имеют довольно прочное покрытие и приятный внешний вид.
Производство облицованных пластиком столешниц начинается с раскроя неламинированной ДСП на стандартный размер (3000 × 600 мм), кромка с лицевой стороны фрезеруется в обрабатывающем центре.
Материал, которым столешница в дальнейшем будет облицована, а это может быть как пластик, так и натуральный шпон, тоже раскраивается на листы стандартного размера с запасом на свесы, но есть нюанс. Для облицовки одного полотна используются два листа такого материала, например пластика. Лист пластика, которым будет отделана лицевая поверхность полотна, должен раскраиваться с запасом на завал для облицовки методом постформинга передней, скругленной кромки плиты. Оборотная сторона заготовки тоже облицовывается пластиком, но более дешевым.
Затем плита и листы пластика поступают на участок прессования столешниц. Здесь установлен специальный пресс, на загрузочный стол которого выкладываются два листа пластика для облицовки плиты с двух сторон. На обе поверхности ДСП с помощью клеемаза OSAMA S4R-1300 ровным слоем наносится клей Kleiberit, после чего заготовка с нанесенным клеем укладывается на один лист облицовочного пластика, а потом сверху на нее укладывается второй лист пластика. Этот «сэндвич» подается под горячий пресс и выдерживается под давлением в определенном температурном режиме. Процесс облицовки шпоном аналогичен этой технологии.
«В этом прессе можно склеивать по пласти и ДСП. Дело в том, что мы выпускаем столешницы толщиной 38 мм, в то время как стандартная толщина выпускаемых сегодня ДСП составляет 16, 18, 22, 25 и 38 мм. Бывают дизайнерские заказы, в которых толщина столешницы может достигать 70 мм, - рассказывает Вячеслав Гриценок. - Плит такой толщины нет у поставщиков, поэтому мы своими силами получаем заготовку нужной толщины».
Для производства столешниц, облицованных пластиками или шпоном, используется влагостойкая ДСП - внешне от обычной она отличается зеленоватым оттенком. Пластик, которым облицовывается лицевая сторона столешницы, отличается высокой прочностью, благодаря чему ее поверхность устойчива к образованию царапин и сколов. В то же время этот пластик - постформируемый, то есть при нагревании может изгибаться. Это его свойство используется при облицовке передней кромки столешницы методом постформинга на станке Brandt PF 20-31.
Заготовка подается в станок, зажимается, и на лицевой торец столешницы пистолетом наносится клей, затем нагревательный элемент станка разогревает завал пластика, после чего обкатывает его вокруг торца заготовки. Стык приклеенного завала и пластика на оборотной стороне столешницы герметизируется. Полученный шов выполняет также функцию каплесборника, то есть капли воды, скатываясь со столешницы, задерживаются на нем.
Свесы пластика на заднем и боковых торцах столешницы срезаются, после чего кромки облицовываются тем же материалом, что и лицевая поверхность.
Сборка мебельных секций
Детали для сборки стандартных секций, после того как пройдут по всем участкам своего технологического маршрута, отправляются на хранение на буферный склад. Если в заказе присутствуют стандартные секции, в производственной системе формируется исполнительный файл, задание, в котором указано, какие детали должны отправиться с буферного склада на сборку. Такой подход существенно сокращает время исполнения заказа, так как необходимые детали уже готовы.
Детали по индивидуальным эскизам, производство которых стартовало с момента поступления заказа, по мере их изготовления маркируются и накапливаются в специальной двухъярусной тележке: в верхней части - детали верхних секций, в нижней - нижних. К этому моменту комплектуется еще одна тележка с деталями для стандартных секций с буферного склада. Затем тележки отправляются на участок сборки секций.
Прежде чем приступить к сборке секций, работники участка вручную устанавливают в подготовленные отверстия и пазы крепежные элементы: направляющие, ножки опоры, подпетельники и т. д. «Вся фурнитура, которую мы используем для оснащения нашей мебели, производства фирмы Blum. У нас все присадочное оборудование, все присадки сделаны под эту фурнитуру, вся система производства "заточена" под направляющие и механизмы этой фирмы», - поясняет ведущий технолог фабрики.
Вопросу оптимизации процесса сборки руководство фабрики уделило особое внимание. По возможности используется быстросъемная промышленная фурнитура с системой «клик», что значительно сокращает время ее установки. Для автоматизации установки шкантов на клей используется специальное оборудование Gannomat Selekta 252 - пистолет, к которому подведены податчики шкантов и клея под давлением. Поднося пистолет к изделию, оператор нажимает кнопку, и клей впрыскивается в отверстие на детали и туда вставляется шкант.
Присадка и установка мебельных петель на фасады автоматизированы и выполняются с помощью специального оборудования - пресса фирмы Blum, который запрессовывает петли Blum системы «клик» в предназначенные для них отверстия. На установку петли уходит не больше минуты, поскольку оператор не тратит время и силы на работу с шуруповертом - он только запускает пресс и контролирует качество установки фурнитуры.
После предсборки изделия отправляются для сборки на станок Ligmatech Optimat MPP 100.
Оператор собирает секцию и подает под пресс, датчики которого определяют размер секции. В случае, когда сборка выполняется на шкант и клей, секция выдерживается под давлением до момента, когда клей схватится. Сжатие секции осуществляется по обоим направлениям - вертикальному и горизонтальному.
Дальше в секцию вставляется необходимая фурнитура, вкладывают ящики, полки, устанавливаются (по необходимости) определенные механизмы. Собранные секции укладывают на специальные тележки и направляют на участок комплектации заказа.
Комплектация заказа
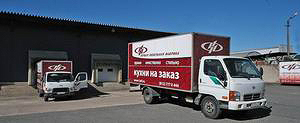
В конце конвейера к мастеру на тележке доставляется готовая секция, в которой установлена вся фурнитура и на которую наклеена этикетка. Мастер снимает с тележки и выставляет секции кухни в зависимости от набора, после чего на них навешиваются присаженные фасады и мастер еще раз все проверяет. Далее присаживаются ручки согласно документации, кухня комплектуется необходимым погонажем (цоколями, карнизами, соединительными планками, заглушками и т. п.), выставляется на тележку, еще раз проверяется мастером, который ставит на нее штамп ОТК, после чего комплект мебели для кухни поступает на склад готовой продукции. На следующий день кухня отправляется заказчику.
«По Петербургу доставка, грузчики, установка - все наше, - говорит Вячеслав Гриценок. - На установку одной кухни уходит один-два дня, в зависимости от сложности. Мы поставляем петербургским заказчикам неупакованные кухни, в упаковке нет необходимости, так как доставляем мебель заказчикам своими силами, а ту мебель, которая отправляется в регионы, упаковываем и снабжаем необходимой документацией, а ее транспортировку и сборку осуществляют сторонние фирмы».
Не сдавать позиции
Быть лидером всегда трудно. Особенно сейчас, когда эксперты и специалисты все чаще говорят о стагнации мебельной отрасли в России. И для таких оценок есть объективные причины: замедление темпов роста экономики, падение спроса на продукцию, появление на рынке большого числа иностранных мебельных компаний в связи с вхождением России в ВТО. Но коллектив «Первой мебельной фабрики» привык, как сегодня говорят, отвечать вызовам времени. Соответствовать требованиям меняющегося рынка, запросам потребителей, модернизировать машинный парк, обновлять ассортимент продукции, осваивать современные технологии, держать марку - вот рецепт решения возникающих проблем от «Первой мебельной». Ведь быть первым - это не только большая честь, но и большая ответственность.
Олег ПРУДНИКОВ, Александр РЕЧИЦКИЙ
Фото: Андрей ЗАБЕЛИН