Эффективное производство пиломатериалов в лесу
Центральный научно-исследовательский институт механической обработки древесины (ЦНИИМОД) в содружестве с Центральным научно-исследовательским дизельным институтом (ЦНИДИ) выполняют поисковый проект, цель которого - создание ресурсосберегающих технологий, обеспечивающих снижение транспортных затрат по комплексу «лесозаготовки - лесопиление», удешевление потребляемой энергии за счет частичного или полного перехода на древесное топливо для отраслевых энергоустановок, уменьшение трудозатрат в производстве пилопродукции, а также улучшение экологии природопользования.
Превращая тонкие бревна в четырехкантный брус или доски на лесосеке, можно практически без потерь в выходе пиломатериалов сократить на 30 % объем перевозок древесины из леса на завод, а это, например, для Архангельской области - почти 400 км. Отходы лесопиления в виде щепы и опилок предполагается использовать в качестве древесного топлива для передвижного газогенератора, работающего в связке с конвертированной на генераторный газ дизель-электрической станцией.
Данная Научно-исследовательская работа входит в Федеральную целевую научно-техническую программу «Исследования и разработки по приоритетным направлениям развития науки и техники на 2002 - 2006 годы» и выполняется по контракту с Министерством промышленности науки и технологий России. В 2002 году ЦНИИМОД проанализировал размерно-качественный состав пиловочного сырья применительно к лесопромышленному комплексу Архангельской области и разработал технологический регламент производства пилопродукции в условиях лесосеки и промежуточных складов. Рассчитан материальный и энергетический баланс древесины.
Согласно материальному балансу при распиловке 1 м3 круглого леса получается 0,3 м3 технологической щепы, 0,1 м3 коры и 0,1 м3 опилок и отсева от щепы.
Что касается отходов лесопиления в виде щепы, коры и опилок, то из них планируется получение генераторного газа как топлива для дизель-электростанции, которая будет вырабатывать электроэнергию, питающую лесопильную установку.
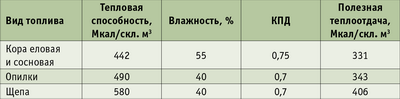
Энергетические характеристики древесного топлива из отходов лесопиления приведены в табл. 1.
Снижение влажности древесного топлива до 20 % позволяет увеличить его теплотворную способность в 1,5 раза и довести ее до следующих величин: по коре и опилкам - до 500 Мкал/скл.м3, по щепе - до 600 Мкал/скл.м3.
Таким образом, энергетический потенциал древесного топлива из отходов лесопиления составляет (0,Зх600)+(0,2х500)=280 Мкал в расчете на 1 м3 распиленного сырья.
На распиловку 1 м3 круглого леса с получением неторцованного бруса или двух толстых досок расходуется около 8 кВт. На сушку древесного топлива, получившегося при этом, требуется приблизительно 13 кВт/ч электроэнергии и 0,1 Гкал тепла. Суммарно это 280 Мкал, что соответствует потенциалу получаемой энергии.
В составе деловой древесины, заготавливаемой в эксплуатируемых лесах Архангельской области, до 40 % составляют сортименты диаметром до 16 см. Они образуются из вершинной части при раскрое хлыстов (до 15 % от их объема) и от рубок ухода. Тонкомерная хвойная древесина от рубок ухода представляет собой медленно растущую и сравнительно прямослойную древесину с плотными волокнами и с небольшим числом сучков. Из нее получаются прочные пиломатериалы высокого качества. Вершинные бревна из крупномерных хлыстов имеют здоровые сучки, которые практически не ослабляют прочность пиломатериалов. По данным Белорусского технологического института, главные прочностные показатели древесины диаметром 6 - 16 см ниже, чем древесины спелой, всего на 8 - 10 %.
Финские исследователи определяют следующие области применения пиломатериалов из тонкомерных бревен:
- строительные детали;
- строительные фермы зданий;
- деревянные клееные конструкции;
- деревоклееные плиты;
- столярно-мебельные изделия;
- строганая пилопродукция;
- деревянные поддоны и тарные комплекты.
При раскрое тонкомерного пиловочника выход пиломатериалов составляет 43 - 44 % от объема распиленного сырья.
На одном мастерском участке лесозаготовительного предприятия в год заготавливается 30 - 50 тыс. м3 круглых лесоматериалов в хлыстах, из них 10 - 15 тыс. м3 тонкомера может быть эффективно переработано в четырехкантный брус и щепу. Такая технология связана с расходом мощности 80 - 100 кВт на комплект лесопильного оборудования производительностью 5 - 8 м3 круглого леса в час с учетом обслуживающего его гидроманипулятора.
Был обоснован выбор типа лесопильного агрегата для работы на лесосеке.
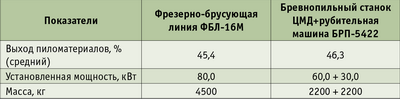
Сравнение выхода пиломатериалов при обработке круглых бревен диаметром в вершине 8 - 18 см и длиной 4 м на фрезерно-пильном и круглопильном оборудовании дает следующий результат (табл. 2).
Небольшая разница в выходе пилопродукции - в пользу круглопильного станка, но операции отбора реек и подачи их в дополнительно необходимую рубительную машину склоняет чашу весов в пользу фрезерного агрегата.
Он должен быть оснащен впереди- и позадистаночным оборудованием, работать в неотапливаемых помещениях и быть приспособлен для перевозки на автотранспортных средствах, предназначенных для лесных грузов, таких как полуприцепы-сортиментовозы мод. 930702 производства ООО «Тавдинский мехзавод». Грузоподъемность такого полуприцепа - 31 тонна, длина груза - до 12,5 м.
Конструкторская документация на опытный образец фрезерно-пильного агрегата была разработана ОАО «Научдревпром-ЦНИИМОД» (проект 1498.00.00.00) в 2002 году.
Агрегат ФПА-180 предназначен для переработки тонкомерных бревен в пиломатериалы стандартных размеров, а также в топливную щепу непосредственно на лесосеке или на промежуточных складах лесозаготовительных предприятий.
Подающий конвейер предназначен для приема бревна, ориентации его кривизной вниз и подачи во фрезерно-брусующий модуль.
Он состоит из проталкивающей цепи с упором, скользящей по направляющим и проходящей через фрезерно-брусующий модуль до пильного модуля. На входе конвейера имеется подъемная секция, а далее перед фрезерно-брусующим модулем установлен прижимной валец.
Фрезерно-брусующий модуль состоит из двух соосно расположенных валов, на консольных концах которых закреплены двухножевые торцово-конические фрезы.
Пильный модуль предназначен для деления бруса на две доски и состоит из пильного узла, закрепленного на качающейся рамке; на ней также закреплен электродвигатель.
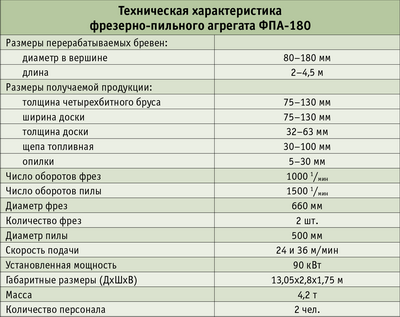
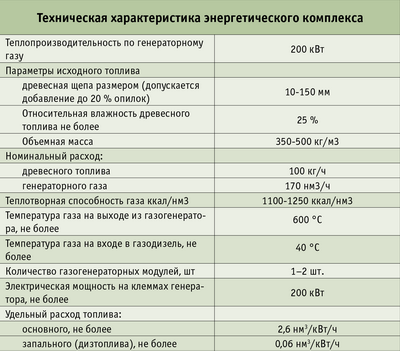
Известные мобильные лесопильные установки, созданные в разное время в России, Канаде, Финляндии и Германии, приводятся в действие от трактора или от передвижной дизель-электростанции.
Оба эти варианта требуют подвозки дизельного топлива к месту базирования лесопильной установки. При цене дизельного топлива 10 руб./кг и удельном расходе через дизель-электростанцию, работающую в номинальном режиме, 0,26 кг/кВт/ч. Минимальная стоимость электроэнергии, вырабатываемой в лесосеке по такому способу, будет равна 2,6 руб./кВт/ч.
В то же время при производстве пиломатериалов на лесосеке или на промежуточном лесном складе имеется возможность без специальной подготовки получать топливную щепу-дробленку, энергетический потенциал которой покрывает энергозатраты на распиловку.
Превращение данного вида древесных отходов в технологическую щепу экономически неэффективно по причине необходимости дополнительных операций по окорке бревен и сортировке щепы, а также дорогостоящей перевозки к местам ее переработки.
Для выработки электрической и тепловой энергии существуют энергоустановки, в которых в качестве топлива могут быть использованы органическое сырье (древесная щепа, торф, сланцы и т. п.) или органосодержащие отходы (отходы лесозаготовительных и лесоперерабатывающих предприятий, лигнин, сельхозотходы, коммунальные и бытовые отходы и т. п.).
Основой технологического процесса является термическая переработка углеродосодержащего сырья в горючий газ посредством химических реакций окисления, восстановления и термолиза, протекающих в газогенераторах. Получаемый газ имеет теплотворную способность 1000 - 1100 ккал/нм3 и может быть использован в качестве топлива в двигателях внутреннего сгорания.
При переводе дизеля на генераторный газ он оборудуется системой принудительного (искрового) зажигания. При выработке 1 кВт/ч электроэнергии неизбежно выделяется до 1,66 кВт/ч (0,0014 Гкал) тепловой энергии, которую нужно либо сбрасывать в атмосферу, либо использовать для технологических или коммунальных нужд.
Выход сухого газа из 1 кг плотного древесного топлива влажностью 25 % - 1,7 нм. Удельный расход генераторного газа через мотор-генератор - 2,6 нм3/кВт/ч.
Первые отечественные газогенераторные установки появились в 1933 году на автомашинах ГАЗ-АА и ЗИС-13, а также на тракторах Челябинского и Харьковского заводов. В качестве топлива использовались сосновые и березовые чурки размером 5х5х7 см.
Мощность газогенераторов ограничивалась мощностью дизельных двигателей, которая в ту пору не превышала 80 л. с. Газогенераторные двигатели использовались и на речных судах.
Новая волна интереса к газогенераторным установкам относится к 90-м годам XX века, что было связано с поворотом российской экономики на рыночные рельсы и, как следствие этого, резким увеличением цен на традиционные энергоносители и тарифов на их перевозку.
Энергетическую часть настоящего проекта, связанную с созданием газогенератора, работающего на дробленой древесине, и с конвертацией дизелей на газогенераторное топливо, в тесном содружестве с ЦНИИМОД выполняет ФГУП «ЦНИДИ» (г. Санкт-Петербург).
Энергокомплекс состоит из газогенератора, мотор-генератора, конвертированного для работы на газе из древесины, блока охлаждения и очистки генераторного газа, сушилки древесных отходов.
Газогенератор представляет собой аппарат для термопиролизной обработки древесины с получением топливного газа, основными горючими составляющими которого являются водород (Н) и окись углерода (СО). Для получения качественного топливного газа, необходимого для использования в поршневых двигателях, в газогенераторе реализуется обращенная схема газификации твердого топлива, при которой смолистые летучие соединения проходят через активную зону раскаленного углерода, разлагаются и газифицируются, что уменьшает содержание смолистых веществ в топливном газе.
Корпус генератора имеет разъем, который делит его на две части. Верхняя часть является бункером, на время транспортировки газогенератора он может быть демонтирован. Нижняя часть газогенератора футерована огнеупорным кирпичом. В ней располагается активная зона, колосниковая решетка и зольник. Активная зона имеет два ряда воздухоподводящих фурм. В зоне верхнего ряда фурм происходит предварительный пиролиз древесного топлива: возгонка летучих и карбонизация (обугливание). Подвижность карбонизированного топлива резко возрастает и дает ему возможность равномерно поступать в основную реакционную зону - зону второго ряда фурм с интенсивностью газификации твердого топлива порядка 500 кг/м2 в час и далее в зону восстановления продуктов горения, расположенную между вторым рядом фурм и колосниковой решеткой. Колосниковая решетка качающегося типа предназначена для удержания слоя раскаленного углерода в реакционной зоне, предотвращения спекаемости золы и удаления золы и угольной мелочи. Ниже колосниковой решетки располагается зольник. Генераторный газ отбирается с двух сторон зоны восстановления над колосниковой решеткой и через коллектор, являющийся одновременно подогревателем дутьевого воздуха, поступает в циклонные очистители, поверхность которых используется в качестве теплообменника для охлаждения генераторного газа и нагрева воздуха, подаваемого в сушилку древесного топлива.
Температура генераторного газа на выходе из газогенератора может достигать 600°С. Для нормального протекания процесса наполнения поршневого двигателя температура генераторного газа снижается до 40°С. Так как использование в газогенераторе древесного топлива с относительной влажностью более 25 % приводит к резкому снижению калорийности генераторного газа, то физическое тепло от охлаждения генераторного газа в виде горячего воздуха направляется на сушку древесного топлива. Древесным топливом наполняется специальная кассета, имеющая форму параллелепипеда с размерами, соответствующими размерам бункера газогенератора. Кассета со щепой при помощи гидроманипулятора опускается в сушильную камеру, где продувается нагретым до 200 - 300°С горячим воздухом. После сушки кассета с топливом опускается в бункер газогенератора через открытую верхнюю крышку, и содержимое кассеты заполняет бункер газогенератора. Пустая кассета направляется на загрузку. После охлаждения генераторный газ направляется в фильтр тонкой очистки, в котором используется кассета, аналогичная загрузочной. В качестве фильтрующего элемента применяется топливная щепа, которая располагается на трех горизонтальных перегородках фильтрующей кассеты с толщиной каждого слоя 100 - 200 мм. После загрязнения фильтрующая кассета также помещается в сушилку для удаления лишней влаги, затем содержимое кассеты сжигается в газогенераторе. В случае использования сухого древесного топлива, горячий воздух в процессе охлаждения генераторного газа сбрасывается в атмосферу или используется на технологические нужды и отопление. Из фильтра тонкой очистки генераторный газ, пройдя каплеуловитель, направляется в смесительное устройство мотор-генератора.
В ЦНИДИ разработан способ перевода дизеля на генераторный газ, предусматривающий работу двигателя на двух топливах одновременно: генераторном газе и жидком дизельном топливе. Двигатель, реализующий такой процесс, называется газодизелем. При номинальной нагрузке он потребляет 80 % газа и 20 % жидкого топлива.
Обоснованы принципы построения пневматической системы автоматического регулирования частоты вращения газодизельгенератора, обеспечивающей высокую приемистость газодизеля, несмотря на инерционность газового тракта. К преимуществам такой системы следует отнести упрощение переоборудования, высокие показатели переходного процесса при резком изменении нагрузки и простоту в обслуживании и освоении.
Препарируется только крышка регулятора частоты вращения дизеля. На ней монтируется передача, кинематически связывающая рычаг муфты штатного регулятора со штоком пневмодатчика, установленного также на крышке регулятора. Все остальные элементы системы навесные (рис. 4).
Испытания конвертированного газодизельгенератора мощностью 200 кВт, оснащенного новой системой регулирования, подтвердили заявленные характеристики агрегата после перевода на газ, полученный из древесины, с сохранением номинальной мощности.
Класс точности регулирования частоты вращения газодизеля - третий по ГОСТ 10511 - 83, как у базового двигателя.
В I квартале 2003 года проведена технологическая подготовка изготовления опытного образца газогенератора и изготовлены его основные узлы.
Во II квартале из изготовленных по технической документации ФГУП «ЦНИДИ» и ООО «Машзапсервис» (проекты УВТ 10.00.00.00, УВТ 12.00.00.00) основных узлов на испытательной базе ЦНИДИ собран газогенератор и система подготовки газа к сжиганию и проведена его опытная проверка.
Газогенератор был установлен на открытой площадке и системой трубопроводов связан со стационарным воздушным охладителем газа и скруббером. В качестве топлива использовались древесная щепа размером до 100 мм в смеси с корой и опилками, являющаяся отходом фанерного производства и хранящаяся на открытом складе.
Полученный из древесных отходов газ подавался в камеру сгорания топлива дизель-генератора переменного тока.
Тепловые параметры газа и мощностные характеристики, развиваемые газогенератором, регистрировались имеющимися на стенде приборами.
Результаты испытаний подтвердили работоспособность созданной модели газогенератора. Расход газа соответствовал тепловой мощности газогенератора 200 - 240 кВт. Продолжительность работы на одной полной загрузке 3 - 3,5 часа.
Развиваемая дизель-генератором электрическая мощность равнялась 75 кВт при сжигании невысушенной щепы и достигала 90 кВт на щепе, подсушенной до 16 - 20% относительной влажности (от одного модуля газогенератора).
В 2004 году, в соответствии с настоящим контрактом, планируется изготовление опытных образцов лесопильного и энергетического оборудования и испытание их на заводах-изготовителях, для чего необходимо обеспечить финансирование этих работ в размере
2500 тыс. рублей.
Экономический эффект от реализации результатов НИОКР:
- снижение энергозатрат на 20%;
- уменьшение трудозатрат в 1,25 раза;
- сокращение затрат на транспортировку пиловочника на 30 %;
- снижение расходов, связанных с вывозом и хранением отходов лесопиления на заводе, в 2 раза;
- снижение стоимости электроэнергии в 4 - 5 раз (применительно к Архангельской области).
Новая технология и оборудование предназначены для использования всеми лесозаготовительными предприятиями сезонного и круглогодичного действия. Область применения может быть расширена за счет переработки сухостоя и древесины, оставшейся на корню после лесных пожаров.
Утилизация отходов лесопиления в лесу посредством газогенераторных установок снижает экологические нагрузки на окружающую среду.