Мини-ТЭЦ: реально и эффективно
Бывшие отходы идут в дело
Важнейшими вопросами, стоящими перед отечественной энергетикой, являются модернизация и замена морально устаревшего и физически изношенного оборудования, доля которого с каждым годом увеличивается.
Либо коптить небо, либо приносить доход
Энергетические установки, которые обеспечивают развитие нашей цивилизации, являются, к сожалению, одними из основных загрязнителей атмосферы оксидами серы и азота, бензопиреном, твердыми частицами, а их вклад в выбросы диоксида углерода, вызывающего парниковый эффект, можно признать основным.
Одним из направлений снижения выбросов вредных веществ в атмосферу установками топливно-энергетического комплекса следует считать замену невозобновляемых видов топлива - углей и мазутов - на возобновляемые виды биотоплива. Поэтому в развитых индустриальных странах для уменьшения воздействия парниковых газов на климат планеты активно поощряется замена ископаемого топлива биотопливом.
Успешное энергетическое использование отходов, образующихся при переработке древесного сырья, возможно только на основе надежного и отвечающего современным требованиям теплогенерирующего и вспомогательного оборудования, предназначенного для работы на этом виде низкокачественного топлива.
На ЗАО «Лесозавод 25» на протяжении многих лет успешно ведутся работы по комплексному повышению эффективности энергетического использования некондиционных древесных отходов. При этом на протяжении последних пяти лет эти работы проводятся совместно с австрийской фирмой Polytechnik Luft- und Feuerungstechnik GmbH.
Первым итогом плодотворного сотрудничества явилось строительство котельной на Цигломенском участке ЗАО «Лесозавод 25», оборудованной двумя австрийскими водогрейными котлоагрегатами PR-2500 фирмы Polytechnik, работающими на кородревесных отходах, образующихся в технологическом цикле предприятия. Результаты энергетических обследований и анализ работы утилизационно-энергетических котлоагрегатов PR-2500 в период суровой и затяжной зимы 2005-2006 годов позволили сделать вывод, что они имеют очень высокие (комплексные) технико-экономические и экологические показатели, способны длительно обеспечивать не только номинальную мощность, но и в случае необходимости производительность выше номинальной.
В 2008 году на ЗАО «Лесозавод 25» реализован второй значительный этап программы комплексного использования древесного сырья: закончен монтаж и запущена в работу ТЭЦ, позволяющая производить в 5-6 раз более дешевую, чем получаемую от ОАО «АГК», тепловую и электрическую энергию за счет применения древесных отходов. Данное направление энергетического использования некондиционных древесных отходов является наиболее перспективным, так как позволяет реализовать преимущества комбинированной выработки тепловой и электрической энергии и обеспечивает значительное уменьшение зависимости предприятия от внешних источников энергии.
Доход в разрезе
Здание ТЭЦ (размером в плане 36,3×34,6м) имеет два склада топлива (7,2×11,7м каждый) и оборудовано системой автоматической топливоподачи. Топливо с помощью толкателей подается на поперечные транспортеры QF 1340, которыми транспортируется в загрузочную шахту FS 1400. Уровень топлива в загрузочной шахте контролируется фотоэлектрическими датчиками, для защиты от обратного возгорания она оснащена тепловой и электрической защитами. Из шахты топливо поступает на толкатель SS 1400, который обеспечивает его транспортировку через загрузочное устройство на колосниковую решетку топочной камеры.
Для сжигания высоковлажных кородревесных отходов на ТЭЦ ЗАО «Лесозавод 25» установлены австрийские котлоагрегаты РRD-7500 фирмы Polytechnik Luft- und Feuerungstechnik GmbH, оборудованные индивидуальными дымовыми трубами высотой 30м. ТЭЦ оснащена автоматической системой управления всеми процессами. Котлоагрегаты РRD-7500 мощностью
7,5 МВт каждый рассчитаны на выработку перегретого пара давлением 2,4 МПа с температурой 420°С.
Их номинальная паропроизводительность составляет 9,5 т/ч. Перегретый пар поступает в противодавленческую турбину, номинальная электропроизводительность которой - 2,2 МВт.
В топочных камерах котлоагрегатов используется трехступенчатая схема сжигания топлива. Для дополнительного снижения выбросов оксидов азота и повышения надежности работы колосниковых решеток они оборудованы двумя системами рециркуляции продуктов сгорания и дополнительными дымососами. Все тягоподдувные установки котлов имеют частотное регулирование производительности.
Топка оборудована наклонно-переталкивающей колосниковой решеткой HVR-7500, состоящей из 27 рядов колосников, при этом 13 из них подвижные. Каждый ряд состоит из 45 колосников, выполненных из жароупорного хромлегированного стального литья (содержание хрома > 30%). В обмуровке боковых стен над колосниковой решеткой расположены четыре фотоэлектрических барьера для контроля высоты слоя топлива на ней.
Под колосниковой решеткой с помощью перегородок созданы три зоны с индивидуальным подводом в них, с одной стороны, первичного воздуха, а с другой - рециркулирующих продуктов сгорания после воздухоподогревателя. При этом в две первые зоны подается горячий воздух после воздухоподогревателя (LUVO), а в третью - воздух, прошедший по охлаждающим каналам, выполненным в обмуровке котлоагрегата. Котло-агрегат РRD-7500 оборудован двумя линиями рециркуляции, в одну из них с помощью дымососа рециркуляции направляются отработанные газы
после воздухоподогревателя, а в другую с помощью второго дымососа рециркуляции - продукты сгорания из камеры очищенного газа золоуловителя. Под колосниковую решетку газы рециркуляции подаются позонно.
Воздух на вторичный поддув забирается из верхней части помещения ТЭЦ и с помощью двух вентиляторов вводится в объем топочной камеры рассредоточенно через сопла (36 шт.) цилиндрической формы. Вторичный воздух обеспечивает дожигание горючих компонентов топлива и позволяет минимизировать образование оксидов азота. Над соплами вторичного воздуха расположены сопла для ввода газов рециркуляции, отбираемых после золоуловителя. Последняя ступень регулирования состава и температуры продуктов сгорания выполнена из двух вертикальных рядов сопел, расположенных над первым промежуточным сводом.
Мелкодисперсная зола, просыпающаяся через зазоры колосников, с помощью толкающей штанги перемещается к поперечному транспортеру, а крупнодисперсная зола и шлак поступают на него непосредственно с колосниковой решетки.
Стены топочной камеры выполнены из огнеупорной шамотной обмуровки, для увеличения времени пребывания дымовых газов в ней установлены два промежуточных свода. При этом у второго имеется специальный турбулизирующий выступ, интенсифицирующий сепарацию крупных фракций золы и частиц недогоревшего топлива на горизонтальный участок первого свода, расположенный у задней стены котлоагрегата. Топочное устройство выложено высокотемпературным жароупорным шамотным кирпичом с запальными арками и каналами для пламени. Этот способ высокотемпературных запальных сводов гарантирует минимальный выброс вредных веществ и представляет собой результат многолетних исследований фирмы.
В обмуровке топки предусмотрены температурные швы, обеспечивающие компенсацию температурных расширений шамота в процессе растопки котла. Для продления жизненного цикла шамотной обмуровки необходимо соблюдать температурные графики растопки котлоагрегата и его охлаждения, а также обеспечивать периодическую чистку. Чем стабильнее режим работы котлоагрегата и меньше его остановов, тем продолжительнее жизненный цикл обмуровки.
Температурный уровень обмуровки топочной камеры контролируется с помощью термопар в четырех точках по ходу циркуляции продуктов сгорания. Пятая термопара размещена перед входом дымовых газов в поворотную камеру котла и обеспечивает контроль температуры продуктов сгорания на выходе из топочной камеры.
Котлоагрегаты оборудованы двухходовыми дымогарными газо-водяными теплообменниками, расположенными горизонтально, вдоль продольной оси, непосредственно над топочными камерами. Продукты сгорания, совершив три хода в каналах топочной камеры, поступают в водоохлаждаемую поворотную камеру, в которой разворачиваются на 90° и проходят по дымогарным трубам первого хода (41 шт.), выполненным из стали 15Мо3. В поворотной камере у задней стены котлоагрегата они разворачиваются на 90° и, двигаясь вниз, омывают трубы пароперегревателя.
В конструкции конвективного пароперегревателя реализована схема многократноперекрестного тока при общем противотоке, компоновка коридорная. Поверхность нагрева пароперегревателя составляет 133 м,
для регулирования температуры перегретого пара он оборудован охладителем впрыскивающего типа SPID. Линия подачи воды в пароохладитель оснащена сетчатым фильтром с максимальным размером ячеек сетки 0,1мм. Проектная температура пара во входном коллекторе - 240°С, а в выходном - 420°С. При этом дымовые газы охлаждаются с 670 до 513°С (при номинальной нагрузке).
После пароперегревателя продукты сгорания по двум газоходам возвращаются в верхнюю часть котла и после поворота совершают второй ход по 280 дымогарным трубам, двигаясь к фронтальной стенке котлоагрегата.
Котел оборудован предохранительными клапанами, воздушником, регулятором уровня воды. Для поддержания требуемого уровня солесодержания имеет непрерывную и периодическую продувки. Продувочная вода поступает в расширитель продувки. Тепловая изоляция котла выполнена из минеральной ваты (d = 200мм), которая снаружи покрыта металлической обшивкой.
После котла дымовые газы с температурой 315°С (при номинальной нагрузке) поступают в газораспределительную камеру экономайзера PRH-7500, из которой по 351 трубе движутся вниз, охлаждаясь до 175°С. Поверхность нагрева экономайзера составляет 398 м. Подвод воды осуществляется в нижнюю часть корпуса, а ее отвод - из верхней части, максимальная температура подогрева воды составляет 220°С.
После экономайзера дымовые газы поступают в батарейный циклон, где очищаются от твердых частиц, которые по системе автоматического золоудаления поступают в сборные контейнеры, из которых регулярно выводятся. Очищенный газ поступает в рекуперативный трубчатый воздухоподогреватель LUVO 7500, в котором, совершая два хода, обеспечивает подогрев первичного воздуха. Воздухоподогреватель выполнен из 398 труб, имеющих шахматную компоновку.
При движении газов в трубчатом воздухоподогревателе происходит дополнительная сепарация зольных частиц. Уловленные зольные частицы из-под экономайзера, золоуловителя и воздухоподогревателя с помощью шнеков направляются в поперечный транспортер.
Для очистки от золовых частиц поверхностей дымогарных труб котла, труб пароперегревателя, водяного экономайзера и воздухоподогревателя котлоагрегат оборудован системой пневмообдувки. Эта система состоит из баллона со сжатым воздухом, из которого воздух поступает к группе клапанов, управляемых электронным модулем. Клапаны по очереди автоматически открываются, обеспечивая очистку определенной группы труб поверхности нагрева.
Для комплексной оценки эффективности работы установленного оборудования в апреле-августе 2008 года было проведено энергетическое обследование ТЭЦ. При проведении обследования в работе находились оба котлоагрегата, при этом их паропроизводительность изменялась в диапазоне от 40 до 93% от номинальной, а температура перегретого пара tпп = 388-405°С. Выработка электроэнергии турбоагрегатом ТЭЦ составляла 1,1-1,5 МВт. Диапазон возможного изменения нагрузки котлоагрегатов был ограничен технологическими потребностями ЗАО «Лесозавод 25».
Овчинка выделки стоит
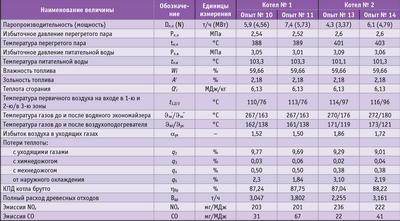
По словам главного энергетика ЗАО «Лесозавод 25» А. Шурыгина, во время балансовых испытаний при пусконаладочных работах вырабатываемая мощность котлоагрегатов составляла 9-9,5 МВт с каждой установки, при этом с турбогенератора снималась электрическая мощность до 2,5 МВт. Стоит также отметить, что не было задержек с регистрацией оборудования в Управлении по технологическому и экологическому надзору по Архангельской области Ростехнадзора. Фирмой Polytechnik Luft- und Feuerungstechnik GmbH своевременно было получено разрешение Федеральной службы по экологическому, технологическому и атомному надзору на применение на паровой котел высокого давления (тип PRD-7.500), перегреватель, экономайзер и относящееся к ним оборудование.
В ходе энергетического обследования проведено шестнадцать балансовых опытов при различных режимах работы котлоагрегатов, при этом в топки котлов подавались несортированные древесные отходы, в составе которых преобладала кора. Доля коры в биотопливе составляла от 74 до 94%, гранулометрический состав топлива был крайне неоднородный, с большим содержанием крупных фракций.
Влажность древесных отходов (W - содержание воды) на рабочую массу изменялась в диапазоне Wtr = 51,7-59,7%, зольность Аr составляла 0,81-2,18%, а низшая теплотворная способность Qri - 6,13-7,84 МДж/кг.
Результаты балансовых опытов показали, что конструкция котлоагрегатов и система автоматического регулирования режимов их работы обеспечивают высокую полноту выгорания монооксида углерода, концентрация которого составляла КСО = 38-186 мг/нм3 (при КO2 = 6%). Потери теплоты с химическим недожогом топлива изменялись в диапазоне q3 = 0,03-0,11% для котла №1 и q3 = 0,02-0,04% для котлоагрегата №2 (табл.).
Температура воды на входе в экономайзеры котлоагрегатов была стабильной: tпв = 101-104°С, что позволяло обеспечить ее дегазацию и достаточно глубокое охлаждение дымовых газов. Так, температура продуктов сгорания после водяных экономайзеров составляла 161-181°С.
Установка золоуловителей инерционного типа в газовых трактах котло-агрегатов до рекуперативных воздухоподогревателей не только обеспечила высокую степень очистки продуктов сгорания (yз. у = 88,6-90,2%), но и повысила эффективность и надежность работы воздухоподогревателей. Температура воздуха на выходе из воздухоподогревателей изменялась в диапазоне 110-128°С, при этом продукты сгорания охлаждались до 119-138°С.
Суммарное сопротивление котло-агрегата с газоводяным теплообменником, пароперегревателем, водяным экономайзером, золоуловителем и воздухоподогревателем изменялось в диапазоне: 168-200 кг/м - для котла №1 и 136-150 кг/м - для котлоагрегата №2. При этом сопротивление отдельных элементов составляло:
44-59 кг/м - котла с газоводяным теплообменником и пароперегревателем; 24-41 кг/м - водяного экономайзера; 32-42 кг/м - золоуловителя; 36-58 кг/м - воздухоподогревателя.
Исследования гранулометрического состава очаговых остатков, отобранных из сборных бункеров котлов, показали, что они имеют высокую степень полидисперсности гранулометрического состава (n = 0,778-0,854) и относятся к тонкодисперсным материалам (b = 0,0129-0,0215).
Анализ условий тепловой работы котлоагрегатов показал, что потери теплоты с уходящими газами изменялись в диапазоне q2 = 9,01-10,38%. Однако имеется резерв для дальнейшего уменьшения данных потерь за счет дополнительной настройки системы автоматики и снижения коэффициента избытка воздуха в топочных камерах.
Конструкция наклонно-переталки-вающей решетки HVP-7500 и системы охлаждения ее рамы обеспечили отсутствие шлаковых наростов и надежную работу установки шлакоудаления при высокой полноте выгорания горючих веществ в очаговых остатках (Сгшл = 2,8-3,8%, Сгун = 4,6-5,7%). Потери теплоты с механической неполнотой сгорания составили q4 = 0,38-0,50%, а с физической теплотой шлака - q6 ≤ 0,16%.
Высокое качество обмуровочных и теплоизоляционных материалов позволило обеспечить для исследованного диапазона нагрузок невысокие значения потерь теплоты от наружного охлаждения (q5 = 1,84-3,71%).
КПД брутто котлоагрегатов PRD-7500 изменялся в диапазоне от 86,71 до 88,22% при нагрузках 40-93% от номинальной. Удельный расход условного топлива на выработку 1 ГДж составил 38,64-39,31кг у. т/ГДж, а эмиссии вредных веществ: ЭСО = 21-102 мг/МДж; ЭNOх = 201-243 мг/МДж и Этв. частиц = 52,4-55,9 мг/МДж.
Реализация проекта по энергетическому использованию древесных отходов для комбинированной выработки тепловой и электрической энергии на основной площадке ЗАО «Лесозавод 25» позволила уменьшить выбросы вредных веществ: сернистого газа - на 524,7 т/год, оксида углерода - на 58,8 т/год, оксидов азота - на 14,8 т/год и углекислого газа - на 29867 т/год, а также обеспечила потребности завода в электрической энергии на 65-70% (при полной загрузке цехов).
Энергетическое обследование показало, что котлоагрегаты PRD-7500 имеют резерв для дальнейшего снижения эмиссии оксидов азота, а также повышения КПД, что достигается путем дополнительной настройки системы автоматического регулирования с учетом изменения теплотехнических характеристик сжигаемого топлива. Установка воздушного конденсатора повысит маневренность оборудования ТЭЦ и выработку электроэнергии.
Таким образом, результаты энергетических обследований и анализ работы котлоагрегатов PRD-7500 фирмы Polytechnik Luft- und Feuerungstechnik GmbH в течение 7 месяцев 2008 года позволили сделать вывод, что они имеют наиболее высокие технико-экономические и экологические показатели из всех теплогенерирующих установок Архангельской области, работающих на биотопливе, и способны обеспечивать не только номинальную мощность, но и в случае необходимости производительность выше номинальной. Реализованный проект полностью соответствует положениям Киотского протокола к Конвенции ООН об изменении климата на планете.
В.К. ЛЮБОВ,
заведующий кафедрой ПТЭ
Архангельского государственного
технического университета,
д. т. н., профессор, член научного совета СЗО РАН по горению и взрыву