«Нархозстрой». Правильные дома
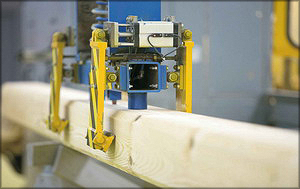
«Что нам стоит дом построить...» - каждый из нас с детства помнит эту легкомысленно-жизнеутверждающую присказку. А дальше: «...Нарисуем - будем жить». Все, казалось бы, просто и по сути верно! Производство любого дома, в том числе и деревянного, начинается с проекта, задуманного и «нарисованного» архитектором, по которому конструктор должен просчитать все необходимые элементы, после чего начинается их производство. Дальше из них - в идеале - должен быть выстроен добротный дом на радость покупателю. Но как же сделать, чтобы созданный вашим воображением воздушный замок воплотился в надежное, теплое и уютное жилище, а не продуваемый всеми ветрами карточный домик?
«Нархозстрой» - домостроительная компания с большим опытом - заинтересовала нас своим подходом к делу: постоянной модернизацией производства, активным внедрением собственных разработок и редкой открытостью для общения. Для любого потенциального покупателя на предприятии готовы устроить подробнейшую экскурсию, в ходе которой можно собственными глазами увидеть, из какого материала, как и на каком оборудовании делаются комплекты будущих домов. Мы решили пойти тем же путем и приехали в гости на производство «Нархозстрой» в Подмосковье.
Стать нашим экскурсоводом по предприятию любезно согласился главный механик - Тимофей Желанников, с которым мы познакомились на выставке WOODEX во время проведения «ЛесПромИнформом» конференции по КДК.
Площадь цехов предприятия составляет около 7000 м2. Начать, пожалуй, следует с места выгрузки, приемки и сортировки пиломатериалов.
Приемка сырья
Машины с досками разгружаются на площадке, где доски вручную перебирают: проверяется качество сырья, обнаруживаются дефекты. Если визуальный осмотр показывает, что в досках большое количество дефектов (гниль, чернота и обзол, много сучков) или сырье просто не соответствует заказанным параметрам, мы возвращаем отбракованную часть - а в крайнем случае - и всю машину обратно поставщику.
Здесь проверяются и брус, и доска, - предприятие работает с разными видами сырья. По породному составу: в основном это сосна и ель, а изредка - кедр (за прошлый год кедр мы заказывали «под клиента» всего дважды, причем пришлось отправлять специалиста в Томск, чтобы проследить, что для нас там отгружают). Вообще, поставщики у нас постоянные, и проблемы с качеством сырья случаются редко, но расслабляться нельзя. Поставщик должен знать, что мы четко отслеживаем качество заказа в каждой поставке. Материалы приходят к нам на производство только из северных регионов страны и из Сибири. Весь лес, что мы завозим на производство, - из экологически чистых районов.
На открытом складе сырье перед сушкой обычно выдерживается несколько недель, если забиваем склад сырьем под длительное хранение на запас - обязательно обрабатываем его антисептиком и укрываем».
Сушильный комплекс
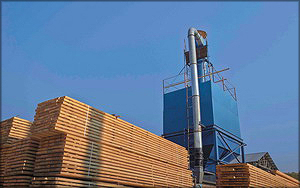
«Огромное значение для нашего производства имеет влажность приходящей на предприятие доски, - продолжает свой рассказ Тимофей Юрьевич. - Участок сушки состоит из четырех сушильных комплексов периодического действия итальянской фирмы Incoplan объемом по 120 м3 каждый. Выбор оборудования обусловлен в том числе и качественным сервисом, предлагаемым российским дилером компании - "Интервесп". Подключение автоматики комплекса к сети Интернет дает возможность специалистам официального представителя Incoplan осуществлять постоянный контроль сушки древесины и техническую поддержку комплекса с помощью удаленного доступа, что очень помогает нашим технологам, обслуживающим эту технику на месте.
Предприятие постоянно расширяется, вводятся в эксплуатацию новые цеха. По мере роста объемов производства будут докупаться и сушильные камеры, скорее всего, того же производителя - за много лет эксплуатации (а камеры Incoplan установлены в 2007-2008 годах) никаких нареканий на них не было, и к тому же электроника комплекса рассчитана на гораздо большее количество камер, чем у нас имеется сейчас, так что можно просто установить дополнительный модуль, и все.
После выхода из сушильных камер доска поставляется в специальный склад, в котором поддерживается такая же температура, как и в цехе производства клееного бруса (20 °C), куда пиломатериал впоследствии поступает. Доска подается в цех один раз в начале смены. "Теплое" складирование сухой доски - одно из обязательных требований в производстве сухого клееного бруса: доска, поступающая в цех для переработки, обязана иметь температуру не ниже температуры цеха».
Антисептическая обработка
«Стоит сделать акцент на таком важном моменте, как биозащита нашей продукции, - отмечает главный механик «Нархозстроя». - Сохранность древесины строительного назначения обеспечиваем за счет использования средств ее биозащиты. Для сравнения эффективности антисептиков наше предприятие организовало лабораторные испытания различных отечественных и зарубежных защитных составов для древесины. Обработанные антисептиками образцы древесины помещались в благоприятную для развития грибков среду. По итогам испытаний был сделан выбор в пользу составов чешского изготовителя, компании Stachema: это составы Lignofix Blue S для пиломатериала и Lignofix Stabil Extra - для готовой продукции, у которых лучшие, на наш взгляд, технологические, экологические, эксплуатационные и экономические характеристики. Это те показатели, которые в первую очередь интересуют конечного потребителя и наших деловых партнеров.
Сырьевые пиломатериалы в весенне-осенний период в связи с большим риском поражения грибками синевы и плесени обрабатываем составом Lignofix Blue S.
Составы наносятся в большой пропиточной ванне методом погружения штабелированного материала. После обработки пиломатериал в течение трех-шести месяцев благополучно хранится до отправки в сушильную камеру. В зимний период временную защиту не применяем.
Готовые изделия защищаем антисептиком долговременного действия Lignofix Stabil Extra. Антисептик поставляется в виде жидкого концентрата, для получения рабочего раствора разводим его водой на месте обработки пиломатериалов. Нанесение защитного раствора на поверхность готовых изделий выполняем механизированным способом в проходной камере.
Благодаря применению качественных антисептиков и технической поддержке российских представителей чешского изготовителя наши клиенты могут быть спокойны за "здоровье" своих домов, которые надежно защищены от поражения грибками и насекомыми».
Производство клееного бруса
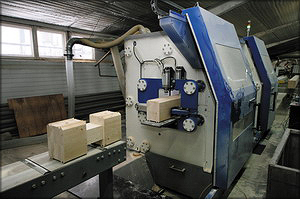
Станок для производства деталей срубов
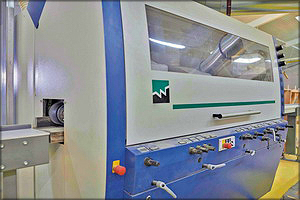
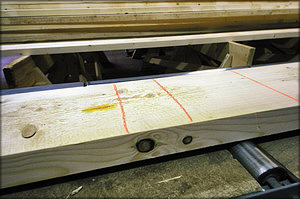
Отмеченные куски доски с дефектами
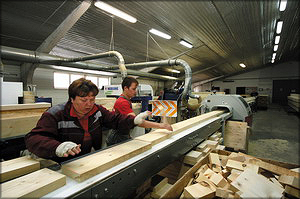
Операторы линии оптимизации
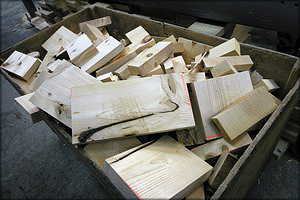
Вырезанные дефектные куски досок поступают в
котельную предприятия
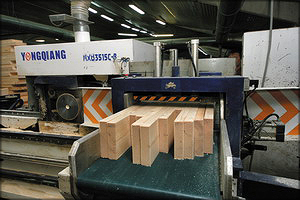
Шипорезный станок
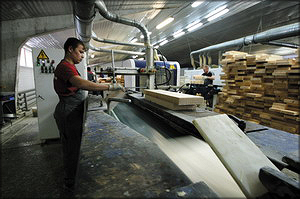
Заготовки поступают на склейку в ламели
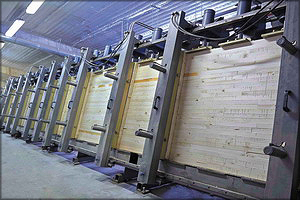
Пресс для склейки бруса
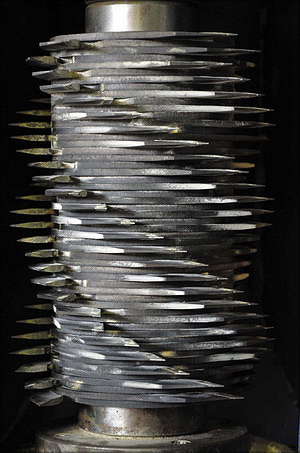
Оптимальная температура на производстве поддерживается в пределах 22-24°C с помощью теплого воздуха, который возвращается от бункера аспирационной системы производства Nestro. Также на предприятии установлены три системы удаления лакокрасочного тумана - распылительные стенды NFW 3020 с сухой фильтрацией производства той же компании. Этот тип оборудования успешно применяется при расходе распыляемых материалов в количестве около 50 кг в смену.
Влажность в помещении поддерживается на уровне 50-60%. Под крышей цеха расположена система автоматического увлажнения, контролирующая влажность в цехе.
При входе в цех сразу обращает на себя внимание станок производства «Нархозстрой» - настоящий гигант, на котором можно обрабатывать брус сечением от 180х185 до 300х370 мм.
«Наш директор Александр Иванович Туркин - опытный конструктор, он сам разработал этот станок, применив ряд собственных технических решений, - отмечает г-н Желанников. - Станок предназначен для производства готовых деталей срубов: на нем зарезаются чашки, выполняются сверловка и торцовка. Система подачи к станку, чашкорезы также разработаны и сделаны нами, и даже программное обеспечение мы также создали своими силами.
Почему все пришлось делать самим? Ни у одной станкостроительной компании нет большого опыта работы одновременно и в деревообработке, и в деревянном домостроении. А у нас такой опыт есть, он, без преувеличения, огромен - и кто лучше нас может знать, какой именно станок нужен тут? На тот момент, когда нам понадобилось такое оборудование, подобного предложения на рынке не было, да если бы мы покупали и такой станок, цена, мягко говоря, кусалась бы. Поэтому пришлось сделать самим, исключив ошибки, присущие даже ведущим производителям оборудования. Это нормально - адаптировать под свои нужды типовую технику или создавать по ее принципу свою, оптимально подходящую конкретно для твоих условий работы. В целом станок аналогичен, скажем, обрабатывающим центрам Stromab, которые работают у нас на производстве, просто у нашего оборудования все больше - фрезы и т. п.
На тот момент на станках Stromab невозможно было производить брус сечением более 200х240, так как в станках Stromab Blox максимальная ширина фрезеровки составляла 200 мм за один проход. На нашем станке за одну операцию можно фрезеровать брус сечением 285х370 мм.
Станок работает уже почти год, и в процессе эксплуатации мы его продолжаем совершенствовать, дорабатывать: усиливаем прижимы, модернизируем фрезы - есть еще возможности сделать лучше. Такой большой брус, который на нем производится, понятное дело, дороже обычного, он делается исключительно под конкретные проекты архитекторов.
Давайте перейдем к линии по изготовлению клееного бруса. Производство ведется с использованием преимущественно пиломатериалов 1-го и 2-го сортов. Производственная цепочка начинается с контроля влажности доски на этапе первой строжки. После сушки в комплексе Incoplan этого можно было бы и не делать, но таковы требования технического контроля производства сухого клееного бруса (стадий технического контроля две: на первой стадии его выполняют наши специалисты, а на второй - специалисты компании AkzoNobel, которые полностью контролируют все рабочие процессы - дважды в месяц они посещают предприятие и проверяют все этапы производства бруса).
Доска с влажностью 10-12% поступает в цех и подается на четырехсторонний станок Beaver для первой строжки. Станок четырехшпиндельный, его четыре фрезы обрабатывают детали размером 240х60 мм на скорости около 24 м/мин.
В отличие от многих других компаний, мы осуществляем обязательное вскрытие дефектов после первой строжки, ведь именно здесь становятся заметны те недостатки материала, которые перед обработкой были не видны.
Делается это так. После строжки доска поступает на стол маркировщика, который проверяет состояние доски - и если он обнаруживает выпадающие сучки, непростроги, иные дефекты - то люминесцентным мелом помечает их и передает на линию оптимизации. Оптимизирующий станок CFS-100 в автоматическом режиме вырезает дефекты и производит заготовку для ламелей длиной от 20 см до 1 м. Это ограничение вызвано особенностями технологии - если увеличить длину заготовок, например, до 2 или 3 м, производительность повысится, но при этом резко упадет качество бруса. Уже в построенном жилом доме в большом количестве появятся горизонтальные трещины. В нашей технологии производства это исключено. Если длина заготовки не превышает 1 м, напряжение в ламели снимается.
После линии оптимизации установлены два шипореза, они зарезают шипы высотой до 210 мм с одной и с другой стороны ламели. Было время, когда мы рассматривали возможность приобретения линии непрерывного сращивания, но потом отказались от этой идеи - скорость работы такого оборудования невысока.
Заготовки сращиваются в 6-метровую ламель и укладываются на линию тангентально либо радиально, чтобы сохранить направленность волокон и избежать последующих напряжений в древесине. После нарезания мини-шипа и нанесения клея D-4000 ламели поступают в пресс, а оттуда - в буфер, где вылеживается 5-7 минут.
Ламели проходят финишную строжку на 7-шпиндельном погонажном станке Beaver и перед клеенанесением поступают в накопитель, где выполняется сортировка ламелей по тангентальному и радиальному сечению древесины.
Для склеивания бруса используется клей нового поколения на меламиновой основе от AkzoNobel, он не содержит формальдегида, экологически чист и обеспечивает высокую прочность клееной конструкции. Клей конструкционный, по сравнению с EPI-системами и полиуретановыми системами он сложнее в производстве, зато изделия, при изготовлении которых использовался новый клей AkzoNobel, намного превосходят при тестировании на разрыв, на излом, на влагоустойчивость и т. д. изделия, при изготовлении которых использовались другие клеевые системы.
Ламели подаются в клеенаносящую машину AkzoNobel нового поколения, она полностью автоматизирована и не нуждается в регулировке подачи клея человеком. Точнее сказать, сама возможность такого вмешательства здесь абсолютно исключена. Машина оснащена датчиками уровня влажности (материала и воздуха помещения), температуры, скорости и давления клея. От датчиков информация передается с помощью специального программного обеспечения на управляющий компьютер, который и принимает решение, сколько подать клея и отвердителя на 1 м2 поверхности заготовки.
Количество слоев ламелей в брусе и, соответственно, его толщина - по желанию заказчика. Максимально чистые от сучков лицевые ламели (две на брусе, маркируются литерой Л) выбираются в результате ручной сортировки. Количество материала, которое закладывается в пресс единовременно, зависит от заявленной толщины бруса, от того, сколько в нем ламелей; оптимальное количество брусьев - 5-7 (в пресс помещается до 30 досок)».
Клеи в производстве бруса
«Каждый покупатель, заказывая клееный брус, спрашивает: какой клей будет использоваться для его производства? Чем выше качество склейки, тем прочнее конструкция.
А кроме того, не будем забывать, что главное достоинство деревянного дома (и, соответственно, основное требование к нему) - экологичность. И клей здесь играет главную роль, - подчеркивает Тимофей Желанников. - Мы традиционно ориентируемся на лучшее, и поэтому наш выбор - "Акзо Нобель". Двухкомпонентные клеи AkzoNobel не содержат формальдегида и толуола, свободны от тяжелых металлов. Для склеивания по пласти применяется водостойкий клей 1249/2579. Безопасность клеевых основ AkzoNobel настолько высока, что они получили европейский сертификат, допускающий использование при производстве продукции, контактирующей с пищей».
Контроль качества склеивания
235
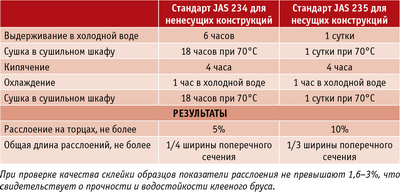
Испытания, позволяющие определить, соответствует ли изделие стандартам качества, проводятся в собственной лаборатории предприятия. Дополнительно брус подвергается экспресс-проверке непосредственно на производстве - готовые образцы бруса раскалывают по шву.
Эксперты испытывают образцы клееного бруса на расслоение. Исследуемый кусок обрабатывается водой, а затем подвергается высокотемпературной сушке. Техника анализа базируется на японских стандартах проверки качества несущих (JAS 235) и ненесущих (JAS 234) клеевых конструкций.
Испытания выполняются холодным способом (замачивание в холодной воде) и горячим (кипячение) (см. таблицу).
Качество склеивания на «Нархозстрое» контролируется несколькими способами - визуальным контролем (ОТК), электронными средствами контроля. Для дополнительного контроля на линии устанавливаются специальные сканеры. Смысл в том, что все завязано в единую цепь: компьютер контролирует производство деталей и плюс к тому на выходе еще одна компьютерная система со сканером проверяет качество, а дополнительно ведется визуальный контроль.
Заточный участок
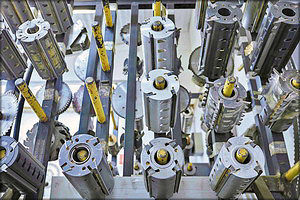
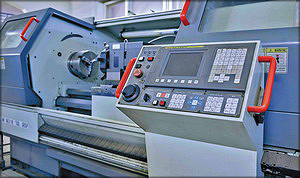
Механический цех
«Как человека встречают по одежке, так о хорошем производстве сразу многое может сказать наличие отдельного заточного участка, - говорит главный механик компании. - У нас здесь самые точные и современные станки. Инструмент от ведущих производителей - таких, как Leitz, Stark. Мы можем в кратчайшие сроки изготовить ножи любого профиля - как для стенового, так и для отделочного материала».
Механический цех
Любое оборудование может сломаться. А когда станки по большей части иностранного производства, к этой проблеме добавляется еще одна - поставка запасных частей. Приходилось слышать, что деревообрабатывающим производствам случается простаивать до двух месяцев из-за задержки деталей на таможне.
В «Нархозстрое» такой проблемы нет: потратив немало денежных средств и усилий, руководство предприятия организовало механический цех, в состав которого входят служба по настройке станков, ремонтная служба, служба механиков по нестандартному оборудованию, токарей и фрезеровщиков, сварщиков. В цехе установлены все необходимые металлообрабатывающие станки: фрезерный центр с ЧПУ, токарные станки с ЧПУ, гильотина, листогиб, станок гидроабразивной резки и много вспомогательной техники.
«Для нас не составляет труда изготовить любую деталь для импортного оборудования, - говорит г-н Желанников. - Механический цех также изготавливает фрезы для станков и все околостаночное оборудование».
«Мы не делаем станки для продажи, мы их делаем только для нашей компании. И главная цель, которая при этом преследуется - ничто не должно помешать заводу выполнить любой заказ в срок!» - с гордостью заметил главный инженер производства Олег Величко.
Производство домокомплектов
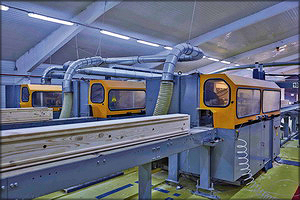
Цех изготовления готовых комплектов домов
Оборудование в цехе изготовления готовых комплектов выстроено примерно по такой схеме: профилирование, сверловка, нарезание чашек, упаковка, отгрузка. Но процесс изготовления комплектов домов начинается с профилирования бруса на четырехстороннем восьмишпиндельном станке Winner Filler FE8-32.4 - качество лицевой части бруса таково, что после ее строжки шлифовка не нужна, можно наносить лакокрасящие материалы. Также в цехе установлен станок для производства евровагонки Weinig Unimat 500 Pro.
Сверловка под нагели осуществляется на оборудовании Strоmab. «Нагели (шканты) многогранной формы с диаметром 25 мм разработаны и произведены нашей компанией, - говорит главный механик предприятия. - Особая форма нагеля позволяет выдерживать несущие нагрузки, но при этом не мешает усадке венцов.
Вслед за профилирующим станком установлена линия антисептирования, также изготовленная мастерами "Нархозстроя". Раньше на ее месте стояла линия, приобретенная у компании, которую мы не станем здесь называть: оборудование не отвечало нашим требованиям и пришлось изготовить собственный станок, который не только обрабатывает брус спецсредствами, но и на выходе бруса из станка втирает в него антисептики с помощью специальных щеток. Такой метод обработки гарантирует глубокое проникновение состава в древесину.
Три чашкозарезных станка Stromab управляются одной программой. Программное обеспечение и система подачи, позиционирование бруса - от начала и до конца наши: такая подгонка "под себя" позволяет изготавливать детали срубов с минимальной погрешностью по длине - не более 0,5 мм. На станках установлены высокотехнологичные фрезы, с помощью которых можно выполнять точную и качественную фрезеровку, что важно для производства так называемого теплого угла.
При разработке сечения фрезеровок и выбора утеплителя угловые соединения прошли целый ряд серьезных испытаний в заводских условиях на продуваемость напором горячего воздуха, результаты фиксировались тепловизором.
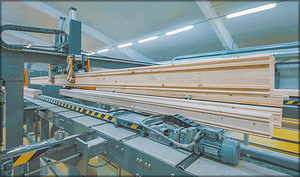
Цех изготовления готовых комплектов домов
Профили у нас свои, специалисты на производстве разработали. Они отлично соединяются по системе "шип-паз", что способствует снижению теплопотерь и обеспечивает непродуваемость дома. Для этого в паз еще закладывается утеплитель по выбору заказчика.
При нарезании чашек фрезы настраиваются определенным образом, чтобы все чашки нарезались одинаково - иначе домокомплект не соберется. При настройке сначала собирают крестовину - и она стоит, пока собирают комплект. Хранится до установки дома, потом утилизируется.
Система контроля производства полностью исключает ошибки - как программные, так и по причине пресловутого человеческого фактора. Прямо на выходе из станка готовые детали маркируют термоэтикетками, наклеенными и зафиксированными степлером. На такой этикетке указывают номер детали, номер линии. На компьютерах, задействованных в производственном процессе, установлена программа контроля линии, в ней указаны все элементы дома, и если по какой-то причине одну из деталей в цехе не сделают, на мониторе сразу появится сообщение об ошибке и ответственные лица без промедления решат эту проблему».
После выхода с линии деталь сруба попадает в зону упаковки или в зону ремонта, где осуществляется заделка дефектов, пороков, например смоляных кармашков до линии антисептирования, и здесь же обрабатываются торцы. Делается это при помощи лака JRM производства компании «Текнос», который зарекомендовал себя как лучшее средство для защиты торцов: он глубоко проникает в древесину, защищая торец от попадания влаги, легко шлифуется, и поверх слоя без проблем ложится финишное лакокрасочное покрытие. И самое главное - лак не растрескивается.
В цехе производят домокомплекты из сухого клееного бруса сечением от 120x185 до 370x285 мм. К каждому домокомплекту прилагается так называемый упаковочный лист, в который вписывают каждую деталь комплекта.
Элементы упаковывают в пачку в специальную перфорированную пленку. Пленка защищает от загрязнений при транспортировке, а перфорация позволяет избежать возникновения парникового эффекта от конденсата внутри пачки. Пачка стягивается упаковочной лентой.
По венцам сруб упаковывают в следующей последовательности:
1. 0-3 венец (к ним относят балки, лаги, полубрус и стойки);
2. 4-10 венец;
3. 10-20 венец;
4. венцы с 20-го и далее.
Какой процент от общего объема бруса приходится на потери от вырезки дефектов, профилирования, строжки?
«В сравнении с объемом пришедшего сырья на выходе бруса теряется около 40% древесины. Но мы сознательно идем на такие потери ради того, чтобы конечный продукт был самого лучшего качества, - подчеркивает г-н Желанников. - Идеальной древесины не бывает. И каждый дефект необходимо тщательно убирать, иначе он потом проявится, что приведет к продуванию бруса, а это одна из самых больших проблем в деревянном домостроении. Или при профилировании вылезет и - нет профиля!
Из домокомплекта заказчик может сам построить нужный ему дом в любом выбранном для этого месте. Также мы осуществляем установку домов и сами - есть бригада рабочих, строительный отдел. Они делают фундаменты, ставят дома, если нужно - наводят кровлю (мы ее заказываем у наших партнеров), выполняют отделку и т. д.».
Теплоизоляция

Специалисты компании в процессе строительства применяют следующую технологию уплотнения (утепления): между брусьями (венцами) помещают специальный межвенцовый уплотнитель, который прокладывается равномерно по всему брусу до шейки чаши так, чтобы он не торчал. Дополнительно оборачивают и чашу. В «Нархозстрое» используют специально разработанный в этих целях ПСУЛ (предварительно сжатую уплотнительную ленту) финского производства. Толщина утепления пола и кровли составляет не менее 200 мм. Стоит отметить, что наряду с утеплением конструкций дома на этапе закладки выполняют утепление фундамента. Для шумоизоляции и утепления перекрытий используютнадежный и эффективный материал - базальтовую вату.
Оконный центр
Есть на предприятии и такое подразделение, как столярный цех. Здесь изготавливают под заказ окна, окосячку, двери, лестницы, производят иные столярные работы.
Окна производят традиционным способом: нарезают профиль, зарезают шипы, детали шлифуют, оснащают резиновыми прокладками (как в металлопластиковых стеклопакетах), далее на вайме собирают готовое изделие.
Котельная завода и производство брикетов
Мощность заводской котельной - 1500 кВт, этого хватает и для обеспечения работы сушильного комплекса, и для отопления цеховых помещений. Котел брянского производства, в качестве топлива используются отходы собственного производства - стружка, опилки, обрезки - до 2 м длиной. Также применяют топливные брикеты из сухих опилок, которые производят здесь же, на «Нархозстрое», методом непрерывного прессования - без добавления клея, воды и пр., что позволяет полностью решить вопросы утилизации отходов предприятия и его теплообеспечения. В зимний период брикеты главным образом используют для собственных нужд, а летом успешно продают сторонним потребителям, в том числе экспортируют за границу.
В гостях у директора
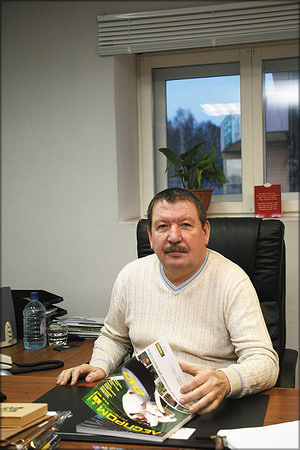
После посещения производственных корпусов нас пригласили в кабинет директора, где уже ждал Александр Туркин.
- Александр Иванович, традиционно мы начинаем разговор с небольшого экскурса в историю: почему так названо предприятие, почему вы занимаетесь деревянными домами...
- Наша компания из тех немногих, что стояли у истоков деревянного домостроения в постсоветской России. Сейчас на рынке таких ветеранов немного наберется. К производству домов из клееного бруса шли долго и постепенно, набили себе шишек, научились технологиям. Опыт ведь не купишь - его годами нарабатывать нужно. Поэтому то, что компания давно на рынке, очень важно. Мы работаем с 1994 года - как видите, в этом году у нас юбилей, 20 лет. За это время мы построили более 3500 домов.
Начинали работать на отечественном оборудовании. Достаточно вспомнить четырехсторонник Боровичского завода: отработал лет 5-7, нормально себя показал и вполне ремонтопригоден. Потом пришли к мысли о необходимости закупать импортное оборудование, научились на нем работать. Как и на любом другом, на деревообрабатывающем предприятии должны быть не только хорошие станки, но и высокопрофессиональный коллектив, который мог бы их обслуживать. В этом смысле, думаю, наша компания опережает большинство конкурентов - у нас своя сильная инженерная группа, конструкторский отдел, специалисты в цехе металлообработки, профессиональные механики...
У инженеров, досконально знающих все производство, оборудование, технологический цикл, разработаны жесткие регламенты на обслуживание станков - ежедневное, еженедельное, ежемесячное. Раз в год выполняется профилактика: в январе мы останавливаем завод и проводим ремонтные работы, переоснащение, модернизацию производства. Большинство запчастей (многие из которых уже не выпускаются производителями оборудования), а также контроллеры, электронные компоненты, программное обеспечение мы можем делать и делаем сами. Благодаря профессионализму сотрудников, мы способны изготавливать для собственных нужд и целые станки, а также оптимизировать покупные. Никаких длительных простоев по причине поломок станков у нас не бывает. Это очень важно при работе с конечными потребителями, когда по договору берешь на себя полную материальную ответственность.
Возьмем для примера оборудование Stomab - довольно хорошо известное итальянское оборудование, востребованное на нашем рынке по причине своей невысокой цены. У нас много их станков, но мы их модернизировали, оптимизировали, сделали полностью автоматическими. Все станки, что мы разрабатываем сами, тоже автоматизированные, человеческий фактор в их обслуживании сведен к минимуму.
- Уточните, пожалуйста, насчет модернизации станков Stromab: вы добавляете те опции, которые компания в принципе предложить не может, или такое «фирменное» перевооружение обошлось бы слишком дорого?
- На тот момент, когда мы модернизировали это оборудование, у компании подобного предложения не было. Мы с ними обсуждали эти вопросы. Оно появилось много позже, итальянцы выпустили подобное оборудование, но долго-долго у них не получалось его изготовить.
- Если можно, назовите основные вехи развития предприятия.
- Мы 20 лет на рынке, хотя клееным брусом стали заниматься не сразу, последние лет 10. А до этого работали с брусом естественной влажности (сейчас спрос на него упал почти до нуля), который тоже использовался для строительства домов по так называемой финской технологии. Хотя и тут немного оптимизировали, улучшили.
Наш лозунг - это «Правильный дом», то есть мы стремимся не заработать деньги на клиенте - а предложить ему по-настоящему качественный добротный дом. Наша цель в том, чтобы заказчики были полностью довольны - и это не пустые слова, а четко выстроенная стратегия.
Наша компания не из тех, которые появились в одночасье за счет стороннего инвестирования, внезапного и спонтанного желания обладающих средствами людей. Мы последовательно прошли все этапы развития - как все профессионалы развиваются снизу и вверх. Зачастую слышу на европейских выставках от иностранцев: у вас в России бизнес неправильно организован - появляются какие-то шальные деньги, бездумно вбухиваются в оборудование, строится производство - а потом все благополучно загибается...
- А ваш механический цех сразу появился?
- Нет, конечно, в процессе работы постепенно становилась все очевидней потребность в нем. Чем больше росли объемы производства, тем острее вставали для нас вопросы качества, тем выше ответственность за выполнение договорных обязательств. Мы закупили самое современное и сложное оборудование с ЧПУ, электроникой, которое позволяет выпускать практически любые вещи.
- Почему все же вы выбрали именно это, а не иное направление, почему дома и почему - премиум-класса? Судя по тому, что у вас все так хорошо получается, решения приняты верные.
- Рынок сам диктует правила и меняет условия. 10 лет назад клееным брусом у нас почти никто не занимался, а ведь это передовые технологии, современный материал - и, вместе с тем, хорошо изученный, опробованный, в Западной Европе давно применяется. Более того, он там весьма хорошо «раскручен», то есть активно продвигается на рынок. По мере того, как он приобретал известность в России, с каждым годом занимал все большее место в деревянном домостроении, росла потребность в этом продукте.
А ведь Россия испокон веков - страна деревянного зодчества, у нас многие сотни лет традиций создания домов именно из древесины. Где как не здесь, с нашими лесными богатствами, развивать эту тему!
- По вашему мнению, что именно побуждает заказчиков обращаться в «Нархозстрой»?
- Наш продукт весьма качественный - поскольку российский заказчик вообще очень требователен. А наши заказчики еще сверх того - это люди из тех, которые ездят по предприятиям, придирчиво сравнивают, стремятся все своими глазами увидеть. И когда заказчик получает возможность сравнить, то его выбор склоняется в нашу сторону.
Требования к клееному брусу за границей и у нас - разные. У них допустимы и сучки, и трещинки, там к такому гораздо спокойнее относятся, чем у нас. Древесина дышит, а значит, может трескаться - и это нормально, таково свойство материала. У нас гораздо более жесткие требования. Российский клиент попросту этого не понимает, считая, что сучки в продукте из древесины означают - производитель плохой, ошибки делает. Качество бруса на нашем рынке по сравнению с тем, что предлагают западные компании, находится на значительно более высоком уровне.
Мы открыты, совершенно ничего не скрываем - организуем экскурсии, мастер-классы, демонстрируем типовой дом из нашего бруса. Для всего персонала предприятия проводятся специальные занятия по технологии не только нашего производства, но и возведения домов - так что каждый работник может стать гидом для наших гостей.
Потенциальные заказчики охотно приезжают к нам, несмотря на то что находимся мы относительно далеко от Москвы, знакомятся с производством. Проходят по заводу, смотрят, какое работает оборудование, каковы культура производства и качество готовой продукции - и понимают, что хотят вот именно здесь получить готовый комплект изделий из клееного бруса для своих домов.
Производство клееного бруса достигает 1000 м3 в месяц.
- Какова ценовая политика предприятия?
- Работаем в средней ценовой категории. Но мы не делаем маленьких домов, наша продукция - это, скорее, такой средний дом для среднего класса. Для человека, который не хочет по несколько раз перестраивать свое жилище, а изначально ориентирован на ту продукцию, которая позволяет достичь ожидаемого результата: построить в надежной компании качественный дом. Мы готовы строить дома и по 100 м2, и по 600-800. Первый вариант - бюджетная версия, мы не так давно вывели ее на рынок, между собой называя «домом для кризисных времен».
Да, кризис, конечно, ощущается, было бы смешно это отрицать. Продажи падают у всех. До приснопамятного 2008 года заводы работали беспрерывно, по 24 часа в сутки, и мы в том числе. Ориентиры были немного другими. А сейчас и конкуренция растет, и люди стали гораздо осмотрительней при серьезных приобретениях. И в этом смысле кризис, безусловно, идет на пользу производителям - мы (может, и вынужденно) стали активнее работать, думать об улучшениях, привлекательности своей продукции для заказчика, повышении конкурентоспособности. И все так делают, не только мы. А кто не думает, уходит с рынка...
Так, мы сегодня единственная компания в России, которая организовала покраску домов на производстве. Заводская покраска подразумевает совершено новый уровень производства: обычно этого не делают, потому что сразу становятся заметными все дефекты - и если мы решились на такое, это сразу говорит понимающему клиенту об очень высоком качестве бруса, высоком качестве домов из него. Все знают, что мы используем только лучшие утеплители, клеи, краски. Кстати о красках - мы перешли на одни из самых дорогих, но и самые лучшие, только на водной основе.
Не могу не отметить и культуру производства. Осваивая новые технологии для того, чтобы не просто удержаться на рынке, а стать наиболее привлекательным выбором для заказчика, мы ставим культуру производства на одно из первых мест. Как здесь принято говорить, все должно быть как в операционной: у врача халат - белый! Если там будет грязь, больного можно угробить. Так и у нас: для того чтобы выпускать высококачественную продукцию, на производстве должны быть чистота и порядок, соблюдаться инструкции по технике безопасности. Не говоря уже о тщательном поддержании технологических параметров в цеху - температуры, влажности и т. д. Мы всему этому уделяем большое внимание.
Строим дом от «Нархозстрой»
- Наша компания производственно-строительная, - продолжает рассказ о предприятии его директор. - То есть мы не только делаем комплекты домов и возводим их. Большую часть наших домов строят наши собственные бригады, также мы реализуем домокомплекты через дилеров (примерно 25-30%), которые занимаются последующим их строительством. У многих строительных компаний своего производства нет, и они работают с такими производителями, как мы, а сами только собирают дома.
Большой плюс собственного производства - возможность снижения стоимости готовых домов. Фирмы, приобретающие материалы «на стороне», делают на них свою наценку, в итоге заказчик вынужден переплачивать 10, а то и 15% от стоимости дома.
Мы предлагаем дома под ключ, с дизайн-проектом, подбором мебели. На недавней выставке «Деревянное домостроение» в ВЦ «Крокус» наш дом размером 8х8 который мы собрали прямо там за три дня (и разобрали за два!), произвел настоящий фурор. Устроители выставки подходили и говорили: надо же, все посетители - на вашем стенде! В самом деле, людям интересно было зайти в дом хорошего европейского уровня, своими руками пощупать его, «примерить под себя». Заинтересовались не только россияне, но и иностранцы. Сейчас ведем переговоры - недалеко от Копенгагена хотят возводить поселок, датчанам понравился наш дом, обсуждаем возможности его застройки.
- Неужели им нечего было выбрать в Финляндии или Швеции?
- Видимо, нет, если предпочли нас. Понравились им качество бруса, сборка, дизайн, интерьер, мебель. Наши партнеры, белорусская компания «Белфан», делает отличную, экологически чистую мебель из массива.
- Насколько индивидуальным может быть дом от «Нархозстроя»?
- В компании работают шесть штатных архитекторов, есть собственное конструкторское бюро. Каждый проект может быть видоизменен с учетом конкретных предпочтений клиента. Технологический расчет выполняется опытными конструкторами с помощью современного ПО, данные конструкционного расчета дома напрямую поступают на управляющий компьютер автоматизированной производственной линии. Далее на трех деревообрабатывающих линиях выпускаются полностью готовые к сборке элементы домов (мощность производства - до 100 м3 в день). Многоступенчатый контроль качества исключает выход бракованных деталей.
Под определенный проект рассчитывается смета, по которой заказчик может отследить, на что конкретно идут его деньги. И в смету, и в проект на этапе согласования клиент вправе вносить изменения по своему усмотрению.
Наши заказчики посвящены в каждый этап возведения дома, начиная от геодезических работ и заканчивая отделкой. Немаловажно, что к строительству привлекаются только штатные бригады компании. В строительстве, как и на производстве, компания внедряет собственные инновации, модифицируя современные и классические технологии возведения домов, готовя оптимальные решения для клиентов. При монтаже сруб собирается в «теплый угол». Наши дома не продуваются по углам, а «коробка» получает дополнительное укрепление. Сборка ведется на многогранные деревянные нагели («ромашки»), их производим сами из сухой древесины хвойных пород. Дополнительно силовая часть строения собирается на оцинкованные шпильки, поскольку обычная сталь подвергается коррозии. При сборке шпилька не контактирует с деревом.
Возведение сруба дома 200 м2 занимает всего 6-7 дней. При строительстве дома «под ключ» срок гарантии составляет 10 лет, при строительстве дома под крышу - два года. В сервисное обслуживание входит обеспечение правильной усадки дома.
Стоимость домокомплекта составляет от 22 тыс. руб. за 1 м3 (это наша цена с подрядом) до 23,5 тыс. руб. (цена за 1 м3 без подряда).
Индивидуальный проект обойдется в 700 руб. за 1 м2, но при заключении договора-подряда на строительство вычитается 50% стоимости АР и КД для дома «теплый контур», а при заключении договора «под ключ» заказчику надо заплатить всю стоимость, в итоге проект рабочей документации достанется вам абсолютно бесплатно. Цена проекта может быть включена в стоимость дома, как часть предоплаты. Качество нашей продукции подтверждено международными сертификатами. Система менеджмента компании сертифицирована по ISO 9001. ТУ, разработанные компанией, гораздо жестче общепринятых ГОСТов. Мы строим по всему миру - в Чехии, Исландии, Германии...
В «копилке» собственных разработок компании - патент на обработку угловых соединений, патент на универсальный торцовочный станок, еще ряд изобретений и технических новаций.
В том числе запатентован наш профиль бруса, есть свидетельство на изобретение так называемого элит-бруса. Такого никто не производит на европейском рынке, кроме нас.
Это брус больших размеров, мощный, у него плавный, объемный, закругленный, декоративный силуэт. Важен и эстетический момент - людям нравится, как выглядит этот профиль, его активно применяли в проектах объектов, возведенных на Рублевском шоссе, на черноморском побережье.
Усовершенствовали мы и стандартный финский профиль, сечением 270 мм. В нашем варианте он непродуваемый и к тому же очень плотно садится, нет зазоров между венцами. Мы долго работали для достижения такого результата и создали оптимальный вариант. На вид профиль очень похож на стандартный финский, но отличия весьма ощутимы на практике - а ведь все дело в нюансах...
На производстве клееный брус и другие деревянные конструкции (например, элементы стропильной системы) проходят тщательную обработку огнезащитными экологически чистыми пропитками на водной основе, на все составы имеются сертификаты. Огнезащита древесины на стадии производства клееного бруса избавляет от необходимости использования антипиренов во время строительства. Препараты, применяемые нашей компанией, сохраняют активность в течение 10 лет - и лишь по истечении этого срока следует нанести противопожарную защиту повторно.
Еще один важный момент. В цехе 20 °С тепла и 60% влажности; у бруса равновесная влажность на уровне 12%. А когда домокомплект вывозят на место установки, обстановка другая. Равновесная влажность меняется, а это может оказать влияние на геометрию конструкции.
Так вот, настоящие профессионалы обязаны делать такой брус, чтобы его размеры, конфигурация не менялись. А мы порой строим очень сложные дома...
Вместо послесловия
Во время посещения завода нас ни на минуту не оставляло какое-то особенное, приподнятое настроение. Приятно наблюдать за тем, как знающие люди занимаются тем делом, которое им нравится и которое - что немаловажно - отлично у них получается! Специалисты предприятия открыты к общению и готовы делиться мельчайшими деталями производства. Потенциальный клиент в этом общении обретает уверенность в качестве приобретаемого дома, заинтересованный коллега - поучительный опыт для применения в своей будущей деятельности.
«Нархозстрой» постоянно развивается. За последнее время пополнился станочный парк Stromab, усовершенствована линия оптимизации, организованы цех покраски и участок обслуживания бруса, открыт шоу-рум. В планах на ближайшее будущее - обустройство цеха для вспомогательных операций (как говорит Тимофей Желанников, «брус напилить, плинтус, вагонку - чтобы основное производство на такие заказы не отвлекать»). Для цеха уже подготовлена площадка...
Беседовала Светлана ЯРОВАЯ
Подготовил Максим Пирус
Фото: Андрей Забелин и компаниии «Нархозстрой»
Благодарим Александра Туркина и Тимофея Желанникова («Нархозстрой») за гостеприимство и помощь в подготовке публикации.
«Нархозстрой»
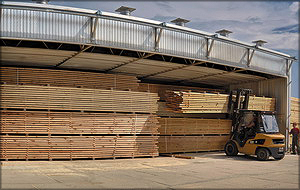
Производственно-строительная компания «Нархозстрой» начала свою работу в 1994 году в дер. Симбухово Наро-Фоминского района Московской области. Основное направление деятельности - проектирование, производство и строительство деревянных домов из клееного бруса и массива, а также строительство домов по каркасной и фахверковой технологии, кирпичных и комбинированных домов.
За 20 лет на предприятии организовано производство, оснащенное современным оборудованием (Stromab, Winner, Weinig, SCM, Incoplan Weinman, OMGA), позволяющим производить все материалы и конструкции из древесины, необходимые для строительства дома: стеновые комплекты, перекрытия, фермы, окна, двери, лестницы, материалы для внутренней отделки дома.
Достоинства домов из клееного бруса:
● клееный брус устойчив к деформации и не подвержен растрескиванию;
● влажность готового клееного бруса - 12%;
● в процессе производства брус и конструкции из него обрабатываются антипиреном и антисептиком;
● клееный брус «дышит», т. е. регулирование влажности происходит естественным путем;
● конструкции из клееного бруса легкие, не требуют усиленного фундамента;
● клеевая система соответствует всем требованиям экологического сертификата, которым сопровождается в обязательном порядке;
● сруб из сухого клееного бруса после строительства дает усадку максимум в 1,5%;
● дом из бруса толщиной 200 мм не нуждается в дополнительном утеплении стен: у клееного бруса низкая теплопроводность;
● стойка из клееного бруса остается прочной в пламени пожара 25 минут, тогда как аналогичная металлическая конструкция становится пластичной и теряет прочность в течение гораздо меньшего периода времени.
Укладка досок на прокладки для сушки в сушильных камерах выполняется следующим образом: доски укладываются по 5 шт. в ряд на 10 калиброванных сухих прокладок (20×50 мм). В одной пачке 55 досок. Пачки между собой перекладываются сухими калиброванными брусками (7 шт. сечением 90×90 мм).
Подготовка ламелей
При подготовке ламелей для бруса вырезают все бракованные части, склеивается только здоровая, без изъянов, древесина. При сборе ламелей в брус есть возможность идеально подобрать даже оттенок и фактуру древесины. Благодаря особенностям технологии склеивания волокна ламелей располагаются под углом друг к другу, что добавляет всей конструкции прочности, превосходящей показатели кирпича и бетона. А прочность стропильной системы, изготовленной из клееного бруса, на 50% выше, чем у такой же конструкции, изготовленной из массива древесины.
Рассказывает Тимофей Желанников: «Большую роль для нюансов производства бруса играют эстетические запросы и вкусы клиентов. Иногда они заказывают на лицевую сторону бруса только ель, она светлее и в ней меньше сучков, она посуше и менее смоляная, чем сосна. Другим, наоборот, больше нравится именно сосна, и мы делаем лицевую поверхность из нее. Некоторым вообще кедр подавай... А вообще в производстве смешиваем хвойные породы».