Деревообрабатывающее предприятие «ТАМАК»
Тамбовский дом с австрийским акцентом
В этом году одному из крупнейших деревообрабатывающих предприятий Центрального федерального округа ЗАО «ТАМАК» исполняется 15 лет. Завод развивает свою деятельность по нескольким направлениям: производство цементно-стружечных плит (ЦСП «ТАМАК»), домов по каркасно-панельной технологии и из клееного бруса, а также столярных изделий.
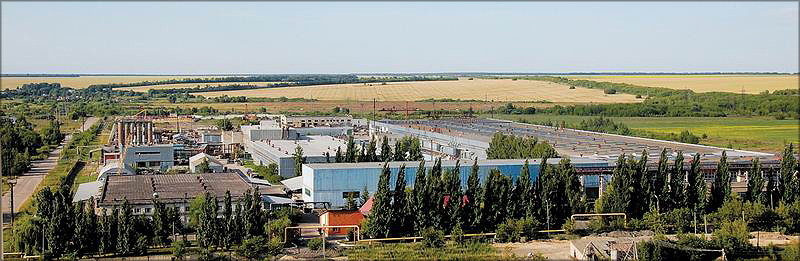
История «ТАМАК»
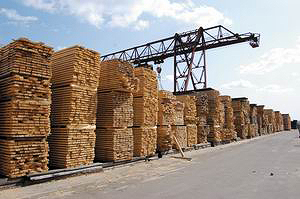
Склад пиломатериалов
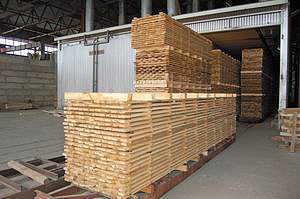
Загрузка пиломатериалов в сушильную камеру
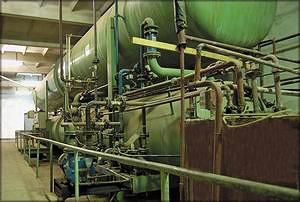
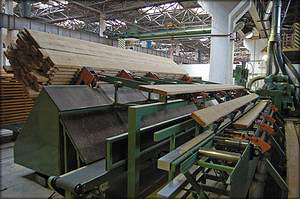
Разобщитель пакетов досок
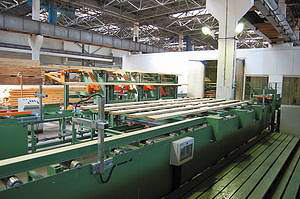
Разобщитель пакетов досок
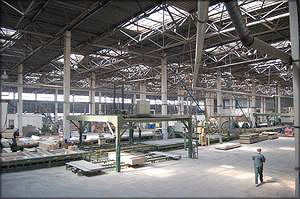
Общий вид цеха
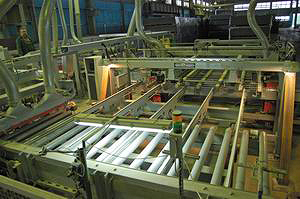
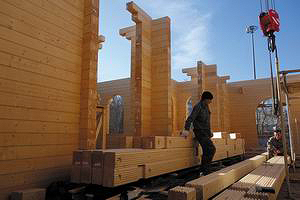
Сборка дома
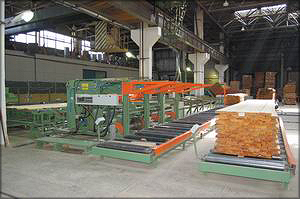
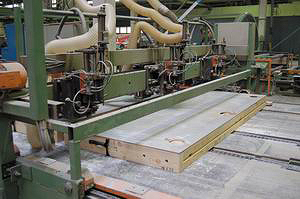
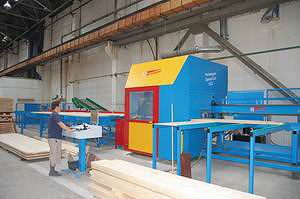
Обрабатывающий центр Hundegger Speed-Cut SC3-2
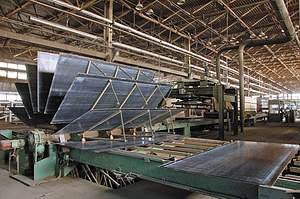
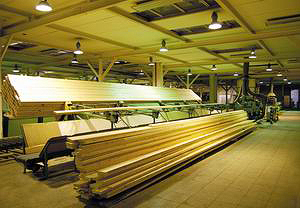
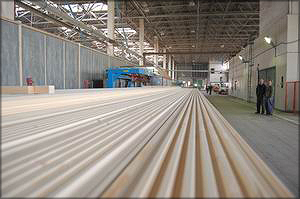
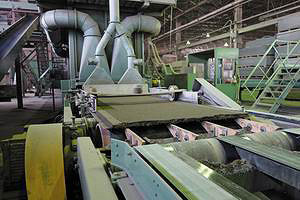
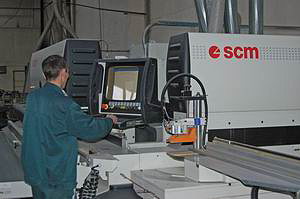
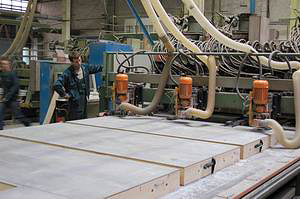
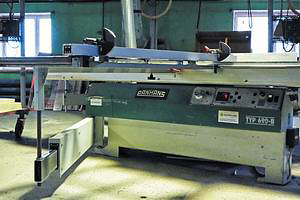
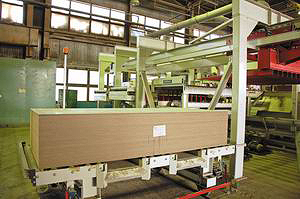
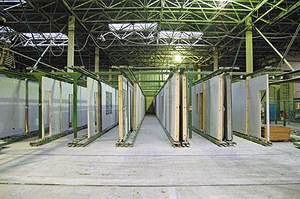
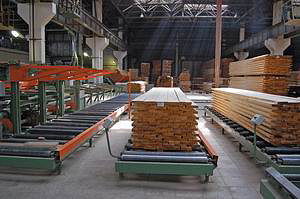
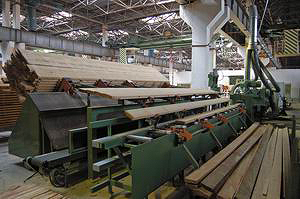
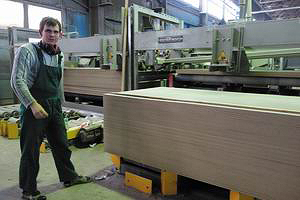
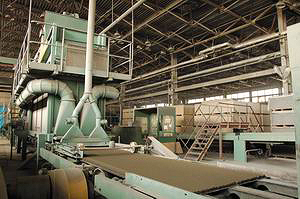
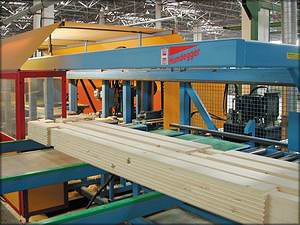
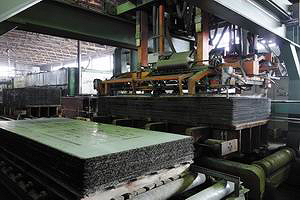
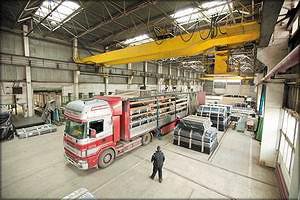
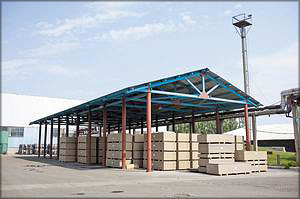
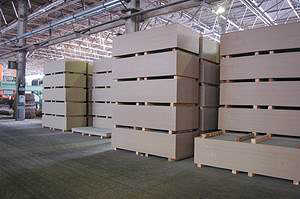
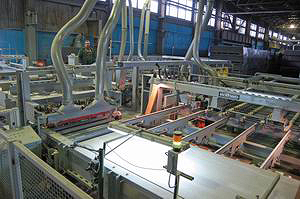
В 1986 году, когда государство взяло курс на обеспечение сельского труженика жильем, Росколхозстройобъединение сделало ставку на производство быстровозводимых домов. Так в Тамбовской области было создано объединение «Тамбовагромонтаж», в задачи которого входило производство, строительство и сдача всего поселка под ключ, включая коттеджи, административные здания, ФАПы, здания социально-культурного и бытового назначения, инженерная инфраструктура поселка. Созданием завода - от проектирования до поставки оборудования - занималась немецкая фирма Streif. Для обеспечения нужд панельного домостроения здесь же было организовано производство цементно-стружечных плит.
Продукция «Тамбовагромонтажа» пользовалась огромным спросом. Ежесуточно заводом сдавалось по пять домов. Кроме домов для индивидуального потребителя предприятие проектировало и возводило детские сады, школы, больницы, фельдшерско-акушерские пункты, спортивные сооружения... При этом лишь половина из них строилась на Тамбовщине, остальные отправлялись в Воронежскую, Ростовскую, Липецкую, Оренбургскую области. В 1992 году была выполнена реконструкция предприятия, нацеленная на выпуск панельных домов, пригодных для эксплуатации в условиях Крайнего Севера и Заполярья, и вскоре полносборные дома по немецким технологиям появились в этих регионах.
В 1999 году на базе «Тамбов-агромонтажа» было образовано новое предприятие - ЗАО «ТАМАК», домостроительный и деревообрабатывающий комбинат со 100% австрийским капиталом. Под руководством председателя совета директоров компании Александра Макулана завод начал новую жизнь. Зарубежный инвестор вложил серьезные средства в модернизацию и наладил принципиально новое для завода направление - производство домов из клееного бруса. Сейчас в состав ЗАО «ТАМАК» входит ряд дочерних компаний. В общей сложности здесь работают около 900 человек. Территория завода - без малого 40 га.
Иностранные инвестиции, реорганизация производства и сотрудничество с европейскими партнерами обеспечили «ТАМАКу» лидерство в производстве цементно-стружечных плит в РФ, одно из первых мест на рынке отечественного малоэтажного домостроения и твердые позиции на зарубежном рынке.
Сырье
Собственными участками для лесозаготовок на сегодняшний день «ТАМАК» не располагает. До недавнего времени в составе компании имелось предприятие с арендованными лесными участками в Архангельской области, но в дальнейшем от него было решено отказаться, все сырье для нужд производства поставляется сторонними компаниями.
География поставок древесины довольно широка: это Республика Коми, Пермский край, Вологодская и Новгородская области. Ежемесячно завод закупает около 4,5 тыс. м3 сосны и 1,5 тыс. м3 ели. Небольшие объемы лиственницы - примерно 50 м3 в месяц - поступают из Красноярского края.
Сырье для производства домокомплектов - обрезной пиломатериал, для ЦСП - неокоренный кругляк, доставляется автомобильным транспортом и по железной дороге. На территорию предприятия заведены две железнодорожные ветки: по ним доставляется сырье и отправляется готовая продукция.
Емкость сырьевого склада завода - около 8 тыс. м3. Поблизости от него расположены пять сушильных камер Eisenmann (Германия) общей вместимостью 1250 м3.
ЦСП
Цементно-стружечные плиты «ТАМАК» - это монолитные плиты толщиной 8-36 мм с гладкой, твердой поверхностью, применяемые в технологии «сухого монтажа». Они изготавливаются путем прессования отформованной смеси, состоящей из стружки древесины хвойных пород (24%), портландцемента (65%) воды (8,5%) и гидратационных добавок (2,5%).
Технологическая цепочка производства ЦСП начинается с окаривания круглого лесоматериала на роторном окорочном станке ОК-63-1 (Россия). Обработанные таким образом бревна перерабатываются на стружечном станке Hombak (Германия) в стружку двух фракций - крупную и мелкую. После первого размельчения отсеивается длинная стружка, а оставшаяся проходит дополнительное размельчение на немецкой молотковой дробилке Bizon (сейчас эта фирма известна как Binos).
Дальше по транспортеру стружка поступает в смесители Erich (Германия). Сюда также подается портландцемент высокой марки, вода, жидкое стекло и раствор сульфата алюминия. Параллельно готовится древесно-цементная смесь двух фракций.
Следующий этап - формирование стружечного ковра формовочными машинами Bizon. Смесь наносится на ровные, предварительно обработанные металлические листы. Для изготовления наружных слоев используется мелкодисперсионная смесь, что обеспечивает плитам гладкую поверхность, а для внутренних слоев (одного-двух), которые определяют прочность плит, - смесь с более крупной фракцией. Получившаяся плита прессуется и отправляется в камеру твердения, в которой обеспечивается определенная температура и циркуляция воздуха для равномерной просушки. Затем клеть с плитами изымается из камеры твердения, плиты снимают с поддона и укладывают в пакеты. Поддоны вновь отправляют на линию к формовочным машинам, а плиты остаются в цехе до завершения процесса гидротации и получения окончательной прочности.
Затем плиты проходят через сушильный канал, где доводятся до влажности, соответствующей требованиям ГОСТа, а затем попадают на форматно-обрезной станок Anthon (Германия), на котором обрезаются под стандартные размеры. Готовую ЦСП остается только упаковать, наклеить на упаковку ярлык с номером партии и артикулом и можно отправлять на склад либо заказчику. Тем плитам, которые пойдут на изготовление элементов домов для панельного домостроения (около 10% всего объема ЦСП), необходимая форма придается на раскроечном станке Anthon.
«В месяц мы перерабатываем 3,5 тыс. т цемента и 3,5 тыс. м3 древесины, - рассказывает генеральный директор ООО «ТАМАКцсп» Андрей Савин. - Качество поставляемой древесины, а это в основном сосна из лесхозов Тамбовской области и ближайших регионов - вполне годится для производства ЦСП».
«Вряд ли какой-нибудь другой плитный материал может превзойти ЦСП по своим физико-механическим качествам, - говорит руководитель департамента развития ЗАО «ТАМАК» Александр Колмаков. - Цементно-стружечная плита экологически безопасна, ведь при ее производстве не применяются фенол, асбест, формальдегидные смолы и другие вредные компоненты. В то же время это весьма прочный материал. Внутренняя обшивка стен из ЦСП "ТАМАК" толщиной 12 мм при креплении к ней навесных конструкций на двух стандартных шурупах с дюбелем-бабочкой выдерживает вес до 418 кг! ЦСП - огнестойкий материал (он при нагревании не выделяет токсичные продукты), водо- и морозостоек, не подвержен воздействию термитов, грибков, насекомых и грызунов, его индекс изоляции воздушного шума - 30 дБ, он пригоден для использования абсолютно во всех климатических районах».
Цементно-стружечную плиту используют преимущественно как строительный материал. Ее применяют для наружной и внутренней обшивки стен, на ЦСП прекрасно ложатся отделочные материалы - краска, штукатурка, монтируется сайдинг и укладывается керамическая плитка, широко используется эта плита для ремонтных, реставрационных и восстановительных работ, утепления зданий, сооружения влагостойких перегородок, кровель, полов, опалубки и т. д. В ремонтно-строительных работах, о которых рассказывается в программе «Первого канала» «Фазенда», используется ЦСП именно производства ЗАО «ТАМАК».
«Кровли с нашей ЦСП построены в аэропортах Шереметьево и Внуково, а также в очень многих гипермаркетах, - говорит начальник отдела маркетинга ЗАО «ТАМАК» Вадим Фидаров. - Цементно-стружечные плиты очень хорошо зарекомендовали себя в ходе эксплуатации в зданиях и помещениях с агрессивными средами. В частности, в животноводческих комплексах. Отлично подходят они и для предприятий химпрома. У этого материала уникальная износостойкость. Приведу такой пример. В 2004 году к нашей заводской столовой проложили дорожку из цементно-стружечных плит - вместо обычных бетонных. Прошло десять лет, по этой дорожке в зной, дождь и снег ежедневно проходят сотни человек. Плиты почти не изменились! Какой другой плитный материал, кроме разве что бетона, может выдержать такую нагрузку?»
Тамбовская ЦСП поставляется во все регионы России (продажами занимаются около 40 дилеров) и в некоторые страны ближнего зарубежья. ЦСП «ТАМАК» также получен сертификат качества, дающий право применения плит в странах Евросоюза. По данным отдела по продажам, в 2001 году «ТАМАК» продавал 500 м3 ЦСП в месяц, в 2003-2004 - 2,5 тыс. м3, сейчас - 4,2 тыс. м3. Производство загружено по максимуму, работа ведется круглосуточно, в четыре смены.
Сегодня о существенном увеличении объемов производства ЦСП речь пока не идет - для этого необходимы значительные инвестиции в строительство новых линий. Руководство ЗАО «ТАМАК» решило пойти по другому пути и сделать ставку на производство новых видов продукции из того же материала.
«Один из вариантов - покрытие плит HPL-пластиком. Это трудногорючий материал, сертифицированный для применения в детских и лечебных учреждениях, что согласуется с политикой компании в части производства экологически безопасной продукции, - демонстрирует образцы ЦСП с разнообразными покрытиями Андрей Савин. - Материал можно шлифовать и фрезеровать, можно выпускать плиты с различной текстурой, например, "под древесину" - так что на вид его трудно отличить от настоящей доски. ЦСП может использоваться как отделочная плита - фасадная, напольная либо интерьерная. Можно комбинировать разные текстуры - это будет очень интересно дизайнерам и архитекторам! Все это пока в стадии разработки - мы изучаем наши возможности, подбираем материалы и оборудование, проводим испытания, присматриваемся к потребностям рынка».
«Все эти мероприятия направлены на расширение областей применения продукции, повышение ее конкурентоспособности и, как следствие, большей эффективности продаж, - заключает Александр Колмаков. - Сейчас наша ЦСП - это все-таки монопродукт, который служит исходным элементом для различных конструкторских решений, будь то стеновая панель, пол, кровля. А нам хочется создать еще и конечный продукт. Вот покрытая пластиком плита - это уже готовое решение для конструкции стены. Интересным вариантом может стать применение ЦСП в навесных вентфасадных системах для наружной отделки ветхих фасадов. Это ведь существенная проблема для многих российских городов. Снести все старые "хрущевки" пока не представляется возможным, а облагородить их внешний вид можно - для этого можно использовать вентилируемые фасадные системы с ЦСП любого цвета. Красиво и вместе с тем в доме станет теплее».
В ближайших планах «ТАМАКцсп» - создание безотходного производства. Так, обрезанные кромки плит и пыль, образующаяся в процессе обработки плит, в перспективе могут быть использованы при изготовлении ЦСП, а для утилизации коры планируется приобрести котельную, работающую на древесных отходах.
Каркасно-панельное домостроение
Сухой пиломатериал поступает на калибровочно-сортировочную линию Minda (Германия), которая состоит из блоков расштабелирующего устройства, тактового влагомера Gann, строгального станка Rex Bigmaster-310-K и штабелирующего устройства с тремя подсобными местами. Здесь пиломатериал рассортировывается на три потока - для производства элементов для брусового домостроения, для каркасно-панельного домостроения и для столярных изделий.
Древесина, отобранная для изготовления панелей, проходит обработку на полуавтоматической строгальной линии Weinig (Германия), а затем поступает на обрабатывающий центр Hundegger Speed-Cut SC3-2 (Германия), который в соответствии с компьютерной программой выполняет все необходимые операции: вырезает элементы необходимой конфигурации и размеров, фрезерует, торцует, сверлит и т. д. - то есть полностью производит детали для панелей.
Панели собирают при помощи системы пневмоприжимов и устройств для пневматической забивки скоб. На каркас из сухого строганого бруса толщиной 144 мм укладывается пароизоляционная пленка, утеплитель - полужесткая базальтовая минераловатная плита марки П-75 (ее поставляет компания ISOROC, расположенная неподалеку от «ТАМАКа» и входящая в этот же холдинг), с обеих сторон крепится обшивка из ЦСП толщиной 12 мм, монтируются уплотнители. Из готовых панелей собирается комплект будущего дома и упаковывается в транспортные пакеты. Доставка к месту монтажа осуществляется еврофурами либо спецприцепами. В перевозимые спецтранспортом панели могут устанавливаться окна и двери, наружные поверхности стен могут быть окрашены или оштукатурены.
Несомненное достоинство панельных домов «ТАМАК» - в сухом способе строительства и высокой скорости сборки, отмечают на предприятии. Двухэтажный дом площадью 120 м2 монтируется в течение трех - пяти дней. Такие сжатые сроки обусловлены тем, что 80% строительных работ осуществляется в заводских условиях. На стройплощадке выполняется сборка уже готовых стен, перекрытий, фронтонов, стропильной системы в единую конструкцию.
«Мы остаемся приверженцами классического немецкого каркасно-панельного домостроения, - подчеркивает начальник производства домостроения Дмитрий Алексеев. - По большому счету, в основе производства - те же узлы, которые были спроектированы и впервые изготовлены в 1980-х годах фирмой Streif. В то же время мы несколько изменили технологический процесс. Например, стали выпускать крупноразмерные панели - длиной до 12 м, максимальный размер панелей, разработанных специалистами фирмы Streif, был 6 м. Значительно увеличили толщину плит перекрытия - со 169 до 238 мм, сделали так называемый вентилируемый фасад. Таким образом, мы улучшили шумо- и теплоизоляцию домов».
Толщина стен домов варьируется в зависимости от климата местности, в которую они поставляются. Для Южного федерального округа - это 94 мм, для ЦФО - 168 мм, для ХМАО - 220 мм. География поставок панельных домов «ТАМАК» весьма широка, это почти все регионы России и страны СНГ, дальнее зарубежье - Швейцария, Германия, Турция и даже Иран (для этого заказа панели пришлось пропитывать противотермитными препаратами). Дома «ТАМАК» предназначены для использования в различных климатических условиях с температурными режимами от -50°С до 50°С и условиями сейсмичности 6-9 баллов, а также для строительства на мелкозаглубленных фундаментах и слабых грунтах.
Рассказывая о качествах своих панельных домов, сотрудники «ТАМАКа» отмечают их высокую энергоэффективность. «Один из наших сотрудников построил себе типовой панельный дом на четыре комнаты площадью 112 м2, - рассказывает начальник отдела сбыта ЗАО «ТАМАК» Станислав Соболев. - После того, как он прожил в новом доме зиму (а она тогда выдалась настоящая, с морозами под -25), я поинтересовался его впечатлениями. "Дом отлично держит тепло, - отвечает он. - А за газ, который пошел на отопление и нагрев воды, я заплатил всего 3400 руб. за семь месяцев! Представляете, какая экономия?"».
В общей сложности к настоящему моменту заводом возведено больше 1 млн м2 панельного жилья.
«Проехав по Тамбовской области, вы увидите в деревнях целые улицы из наших домов, построенных еще в 1987-1989 годах. Кто-то облицевал их кирпичом, а чьи-то дома еще даже не перекрашивались и очень неплохо выглядят. Некоторые предприимчивые люди даже покупают эти дома, разбирают, перевозят в райцентр, монтируют их там заново и продают с неплохой прибылью, - говорит технический директор ЗАО «ТАМАК» Сергей Алентьев. - Панельные дома хороши еще и тем, что их, в отличие от каменных или кирпичных, можно изготавливать и монтировать круглогодично. А в случаях техногенных или природных катастроф (пожары, наводнения, землетрясения) панельные дома просто незаменимы, ведь именно используя эту технологию можно быстро построить жилье для людей, пострадавших от таких катастроф. Подобный опыт у нас имеется. В 2010 году, когда в стране бушевали лесные пожары, мы за один месяц поставили в Волгоградскую область 70 комплектов домов. Застраивали поселки после землетрясений в Турции и Армении, принимали участие в ликвидации последствий наводнения в Краснодарском крае. В одном из селений Южной Осетии после известных событий 2008 года построена улица из домов «ТАМАК», которая называется Тамбовской».
«Помните крушение "Невского экспресса" в ноябре 2009 года? Многие СМИ тогда рассказывали про бабушку Елену Голубеву, возле дома которой произошла катастрофа. Она первой помогала пострадавшим в той катастрофе, - говорит Станислав Соболев. - Хорошо помню, как мы с женой вечером видели ее в программе "Пусть говорят": бабушка рассказывала о произошедшем, волновалась, ей в прямом эфире стало плохо... А буквально на следующий день в "ТАМАК" позвонили: "Здравствуйте, необходимо как можно скорее сделать двухкомнатный дом. Это для Елены Голубевой". Такой дом мы можем сделать всего за две смены. 12-го числа мне позвонили, 16 и 17-го две фуры ушли от нас в Бологое, а уже 27-го по телевизору показали репортаж о том, как бабушка отмечает новоселье в нашем доме».
Из панелей «ТАМАК» возводятся не только коттеджи, но и административные здания, школы, детсады, больницы. Бывают необычные и сложные заказы. На заводе с гордостью вспоминают об ответственном проекте строительства катков на Красной и Дворцовой площадях, которым предприятие занималось в 2007 году. В Москву тогда было отправлено 24 грузовика с панельными конструкциями, в Петербург - 37. Правда, каток на Дворцовой площади отработал только один сезон (руководство Эрмитажа настояло на прекращении этого проекта), а каток на Красной площади с успехом эксплуатировался (его разбирали и монтировали заново) до 2014 года.
Руководство «ТАМАКа» уверено: для роста объема производства панельных домов есть все предпосылки. «Я проработал здесь 30 лет. И, вы знаете, только сегодня мы начали возвращаться к первоначальным объемам, - отмечает Сергей Алентьев. - В 1986 году завод выпускал пять домов в сутки. И уверен, стране это нужно: для реализации программ расселения из ветхого жилфонда, строительства домов для детей-сирот, ветеранов, для решения проблем жителей, оказавшихся в зоне бедствий... Словом, сфера применения наших домов весьма широка».
Брусовое домостроение
В качестве сырья для производства клееного бруса используется высококачественная хвойная древесина из северных и сибирских регионов России.
Пиломатериал, высушенный в пределах 10%±2%, калибруется, затем выполняется разметка и автоматическая вырезка дефектных мест, а также нарезание шипа с нанесением клея. Следующий шаг - сращивание заготовок, предварительно разделенных по фактуре и внешнему виду на внутренние и внешние ламели. В основе линии сращивания оборудование GreCon с тактовым прессом ТР 12-25Li (Германия). На прессе Minda (Германия) заготовки склеиваются в «бесконечный брус», ламели торцуются на заданную длину, от 8 до 12 м. Ламели проходят строжку на четырехстороннем строгальном станке Rex-310 (Германия), в результате чего им придаются точные геометрические размеры и необходимая для дальнейшей склейки шероховатость. Из ламелей с нанесенным на них влагостойким клеем на меламиновой основе собирается набор для бруса, который в течение двух часов выдерживают под давлением в гидравлическом прессе. Готовый брус прострагивается до первого класса чистоты и профилируется на станках Rex-410 и Rex-1100. Производственная мощность участка составляет 1200 м3 в месяц при 11-часовом рабочем дне.
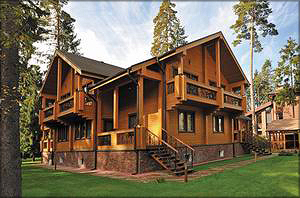
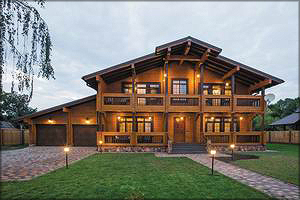
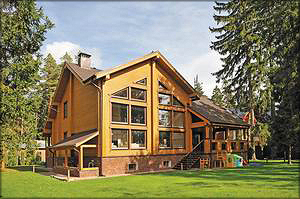
Последний этап - зарезка бруса в зависимости от задания, заложенного в компьютер (дома проектируются в программе Cardwork) - выполняется на универсальном многоцелевом автоматическом обрабатывающем центре Hundegger K2. Готовый комплект брусового дома упаковывается и отправляется заказчику. На стройплощадку поставляются полностью готовые к сборке элементы конструкций. В комплект дома общей площадью 200 м2 входит около 3 тыс. деталей стен. Квалифицированная бригада монтирует такой дом за три-четыре недели.
Пазы и гребни смежных брусьев Ш-образного профиля обеспечивают плотное соединение «с натягом», благодаря чему брус жестко фиксируется в стене, не образуя зазоров. Специальный профиль «ТАМАК» не требует укладки утеплителя между брусьями. Стены дома после возведения становятся монолитными и герметичными, что исключает их продуваемость, промерзание и проникновение влаги внутрь. Утепляются только замковые соединения по углам дома.
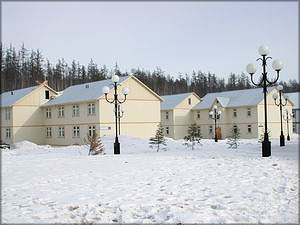
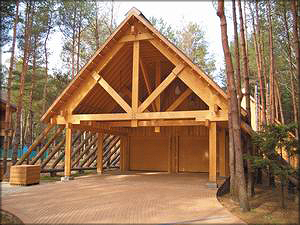
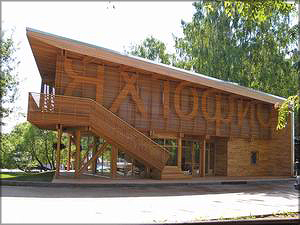
«Специалисты нашего завода на основе европейских стандартов разработали оптимальную конструкцию бруса. У еловых ламелей клееного бруса "ТАМАК" толщина 40 мм, а у лиственничных - 33 мм. Это позволяет сохранить естественные свойства древесины, добиться стабильной и точной геометрии бруса, а также минимальной и прогнозируемой осадки конструкции дома, - рассказывает Александр Колмаков. - Для создания готовых конструкций дома требуется высокая точность пропорций и геометрических размеров клееного бруса по всей длине. Поскольку автоматические линии зарезают сложные замки с абсолютной точностью, то и брус должен иметь идеальные характеристики, иначе в узлах могут возникнуть разного рода несовпадения. Согласно внутренним техническим условиям, для 12-метрового клееного бруса "ТАМАК" отклонение по длине не должно превышать 2 мм (0,025%), по толщине - 1 мм (0,49%)».
«Вообще-то основоположники брусового домостроения - финны. Но финские станки для производства и обработки клееного бруса более громоздкие и дорогие, чем немецкие аналоги. Поэтому, принимая решение о закупке оборудования, мы остановились на станках фирмы Hundegger и очень довольны их работой, - говорит Сергей Алентьев. - В планах по модернизации производства мы по-прежнему будем ориентироваться на немецкое оборудование. Увы, сегодня в России нет предприятия, которое могло бы делать хорошие, долговечные, ремонтопригодные станки. Большие надежды мы возлагаем на пятикоординатный центр, который собираемся приобрести в этом году. Он позволит нам значительно продвинуться в изготовлении сложных деревянных конструкций. Мы и сейчас прямо на заводе можем укомплектовывать наши дома лестницами и окнами, а в недалеком будущем, может быть, даже дополним их и кухонной мебелью из массива. В Финляндии, например, все жилье строят сразу с мебелью для кухни».
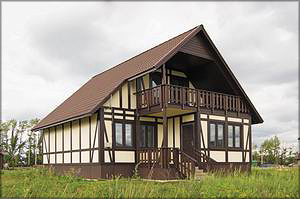
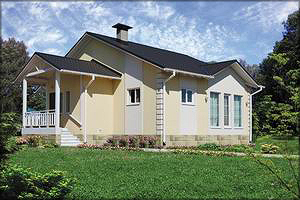
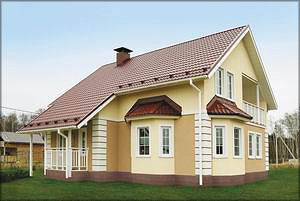
По данным директора по продажам ЗАО «ТАМАК» Ильи Сергеева, 70% домов из клееного бруса поставляются в Москву и Подмосковье. В последние два года наметилась тенденция покупки таких домов и в Тамбовской области. «Если с 2001 до 2012 года мы продавали на Тамбовщине в лучшем случае один дом из клееного бруса в год, то сегодня - около десяти, - отмечает Илья Сергеев. - Будем наращивать объемы производства - рынок позволяет. Кстати, на фоне устойчивого спроса на брусовые дома в последнее время у потребителя вырос интерес к каркасно-панельному домостроению. Это радует. Значит, люди - даже не самые обеспеченные - все больше отдают предпочтение индивидуальным домам из натурального материала, а не квартирам многоэтажек».
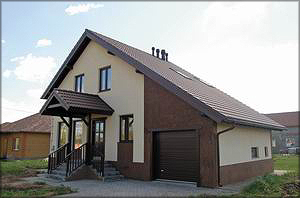
В каталоге «ТАМАКа» около сорока проектов брусовых домов. Но в действительности заказов на типовые варианты почти не бывает. «Дома из клееного бруса крайне редко похожи друг на друга на 100%. Если уж заказчик готов тратиться на жилье из древесины, он обычно не жалеет денег и на разработку индивидуального проекта. Если надо, выезжаем на местность, изучаем площадку, где будет стоять дом, рельеф, ближайшие строения. Одни хотят, чтобы их дом не диссонировал с окружением, другим важно наоборот: выделиться - так выделиться, - рассказывает начальник проектно-конструкторского отдела ЗАО «ТАМАК» Александр Кофанов. - Мы всегда открыты для контактов с заказчиком и ни в коем случае не стремимся навязать ему конкретный комплект - в отличие от многих других заводов, которые не вносят изменения в раз и навсегда утвержденную комплектацию домов. В конце концов, сделать перепланировку на основе уже разработанных вариантов не так и дорого стоит. Это касается и панельных домов - несмотря на наличие каталога, количество возможных вариантов планировок и разнообразных отделок велико. Мы производим действительно индивидуальное жилье и гордимся этим. Есть у нас такая задумка - сделать дом для молодой семьи, который со временем можно будет достраивать. То есть вначале ставится только первый этаж, но с высокой крышей. Семья живет там, а как только финансы позволяют, достраивает мансардную часть дома. Без съема кровли и дорогостоящих перестроек возводится мансардный этаж, ставится лестница, проводится отопление и освещение - все быстро и удобно».
Столярные изделия
В столярном цехе производят оконные конструкции, лестницы, мебель и прочие деревянные изделия.
Сухой калиброванный пиломатериал распускается на многопильном станке Paul K34 G/800 (Германия). Затем поступает на линию торцовки и сращивания коротья фирмы Sharp & Kögel SC-30-520 (Германия). «Мы уделяем большое внимание устранению дефектов древесины, - подчеркивает Дмитрий Алексеев. - Даже небольшие трещинки и сколы шпаклюем, ставим пробки и специальные торцевые накладки. В некоторых случаях используем "элементы-сучки" - декоративные пробки».
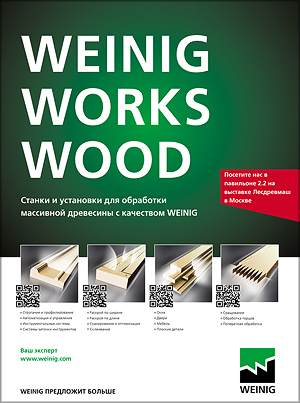
Weinig. Деревообрабатывающее оборудование
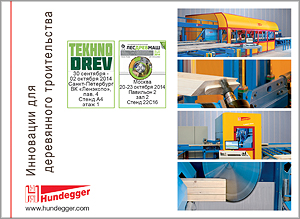
Hundegger. Оборудования для производства деревянных
конструкций, деревянных домов
Ламели склеивают в брус, который после определенной выдержки поступает на линию изготовления оконных блоков. Обработка бруса (профилирование, зарезка под фурнитуру и т. д.) выполняется на четырехстороннем шестишпиндельном станке Winner BL 6-23. В этом же процессе задействован строгальный агрегат Rex-310. Элементы собирают в оконные блоки вручную на сборочном столе. Затем они поступают в лакокрасочное отделение, которое в этом году было реконструировано. В его основе - оборудование Cefla (Италия). На финальном сборочном участке рабочие комплектуют стеклопакет фурнитуруой, стеклами, уплотнителями - и упаковывают для отправки заказчику либо для комплектации домов.
«В деревянных евроокнах "ТАМАК" используется фурнитура Maco (Австрия). У нее есть специальное приспособление - микролифт, который защищает створку окна от провисания (вес створки может достигать 35 кг) и обеспечивает длительный срок безотказной службы окна, - сообщают специалисты завода. - Для защиты от шума, холода, пыли и дыма окна комплектуются двумя контурами уплотнителей. Мы используем уплотнители Deventer и Q-Lon (Германия), изготовленные из термопластичного эластомера. Краска, которой окрашиваются рамы окон, - на водной основе Sikkens (концерн AkzoNobel), имеет высокую эластичность, хорошее сцепление с деревянной поверхностью, УФ-фильтры, а главное, позволяет древесине "дышать". У краски хорошие защитные функции, еще один плюс - она оставляет видимой структуру древесины».
В столярном цехе также производится погонаж: доска пола, имитация бруса, имитация бревна, всевозможные заготовки для ограждений и т. д.
Новые изделия разрабатывают и тестируют в экспериментальном цехе. «Скамейки, столы, лестницы, качели, декоративные мельницы - все это изготавливают в экспериментальном цехе, - рассказывает директор по производству Лариса Федянина. - Высокопрофессиональные специалисты по индивидуальным заказам и для выставок делают уникальные изделия. На одной из строительных выставок наш стенд был оформлен в виде корабля из клееного бруса - с мачтой, штурвалом, парусами. Конечно, он привлекал внимание специалистов, потенциальных покупателей и просто зрителей».
«У нас хорошая машинная база: форматно-раскроечный станок Panhans TYP 690-B (Германия), рейсмусы Panhans и SCM AB/202679 (Италия), шлифовальная машина Panhans, ленточный шлифовальный станок ШЛПС-КСПО (Россия), фрезерные станки Griggio T220 (Италия) и Hammer F3 (Австрия), - начальник экспериментального участка Галина Прокудина демонстрирует установленное в цехе оборудование. - Кроме того, есть несколько старых станков, которые в свое время были куплены для этого цеха. Это настолько хорошее профессиональное оборудование, что оно служит уже двадцать лет и работает порой лучше современного. И конечно, на нашем участке много ручного труда - здесь около полутора десятков столов для работы ручным инструментом».
Отдельного рассказа заслуживает «Садовая программа». В свое время это направление было создано для производства садового паркета, который поставлялся преимущественно в Германию и Австрию. Сейчас в рамках этой программы выпускаются дачная мебель, беседки, арки, ограждения, перголы и другие элементы садово-паркового дизайна. Ассортимент выпускаемой продукции насчитывает более ста наименований. Материал - исключительно сибирская лиственница. «В древесине сибирской лиственницы есть камедь, обеспечивающая естественную стойкость к гниению, - объясняют специалисты предприятия. - Из-за повышенной твердости и высокого содержания смол и камеди лиственница сложна в обработке, зато изделия из нее прочны и долговечны. Сушка пиломатериала до оптимального уровня влажности 10 ±2% и сращивание деталей на минишип исключают рассыхание и коробление готовых изделий, а использование водостойких двухкомпонентных клеевых систем гарантирует продолжительный срок эксплуатации на открытом воздухе».
Что касается отходов деревообработки, то можно сказать, что для такого крупного производства, как ОАО «ТАМАК», их объем невелик: 2200 м3 стружки и опилок и 1000 м3 сырой коры ежемесячно. «Этого недостаточно, чтобы наладить производство пеллет или брикетов, поэтому сухие стружку и опилки мы продаем птицефабрикам. За ними даже присылают транспорт из Курской области. Думаем над покупкой оборудования для сушки и измельчения коры, чтобы ее также использовать для птицефабрик, - говорит Иван Данилов. - К 2016 году объемы производства продукции должны вырасти в полтора раза, а значит, значительно увеличится количество отходов. Поэтому мы рассматриваем и другие варианты их использования. Есть перспективные планы на этот счет, изучаются оборудование и технологии, которые можно задействовать. Основная задача - снижение объемов закупаемого для производства сырья и затрат на энергопотребление, что позволит снизить себестоимость выпускаемой продукции».
Евгения Чабак
Статистика
Годовые объемы производства ОАО «ТАМАК»:
- 50 000 м2- каркасно-панельные дома;
- 14 000 м3- дома из клееного бруса,деревянные клееные конструкции;
- 1 000 шт. - фахверковые дома;
- 54 000 м3- цементно-стружечные плиты;
- 6 000 м2- деревянные евроокна;
- 11 500 шт. - элементы садово-паркового дизайна;
- 1 300 м3 - единовременная сушка древесины;
- 35 000 м2 - объем переработки древесины
С 1986 года до настоящего времени построено более 1 млн м2 жилья, в том числе комплектов домов для индивидуального проживания, а также 4 тыс. м2 многоквартирных домов, административных зданий и сооружений из сэндвич-панелей.
ЛесПромИнформ №6 (104), 2014 г. Покупают! Потому что это – «ТАМАК»