Honeywell: в центре внимания – пользователь

Развитие технологий промышленной автоматизации продолжается: появилось уже четвертое поколение систем. На современном этапе разработчики стремятся сделать системы цифровой автоматизации более удобными для диспетчеров, ищут пути к достижению максимальной гибкости и большей совместимости решений.
Центр передовых технологий компании Honeywell находится в городе Куопио. Он специализируется на разработке инновационных решений для предприятий, выпускающих целлюлозно-бумажную продукцию и листовые материалы.
Датчики будущего
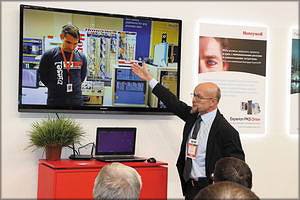
Владимир Семенов, ведущий консультант по процессам ЦБП Honeywell ProcessSolutions, ведет презентацию продукции компании на выставке PAP-FOR
Одно из направлений деятельности Центра передовых технологий – создание перспективных датчиков, которые можно использовать в системах автоматизации.
Например, датчики, основанные на использовании рентгеновских лучей, можно устанавливать в бумагоделательные машины. Они позволяют эффективно собирать подробную информацию об определенных характеристиках бумаги, следить, например, за ее цветом, контролировать такие ее свойства, как гибкость и прочность. Пользовательский интерфейс устройства обеспечивает визуализацию результатов наблюдений, что дает возможность оперативно вносить необходимые изменения в производственный процесс.
Четыре поколения систем
В последнее время технологии автоматизации стали более совершенными благодаря внедрению виртуализации и технологии настраиваемого ввода-вывода. Марко Ямсен, руководитель направления целлюлозно-бумажной промышленности и производства листовых материалов Honeywell, считает, что сейчас создано уже четвертое поколение средств цифровой автоматизации.
«Виртуализация позволила значительно сократить сети, поскольку несколько виртуальных компьютеров можно запускать на одном устройстве, – поясняет г-н Ямсен. – А чем меньше промежуточного оборудования используется, тем меньше опасность поломки».
Раньше порты ввода-вывода приходилось настраивать для каждой платы отдельно. Теперь технология настраиваемого ввода-вывода позволяет использовать аналоговые и дискретные входы и выходы на одной плате.
«Вам не нужно даже открывать шкаф с оборудованием ввода-вывода, – говорит Марко Ямсен. – Технология виртуальных серверов позволяет быстро обновлять отдельные компьютеры, используемые в системе автоматизации. Еще больше возможностей открывается при разработке и диверсификации сетей и каналов. Расходы на техническое обслуживание можно сократить без угрозы снижения функциональных возможностей решений. Можно также уменьшить затраты на резервное копирование».
Облачные технологии
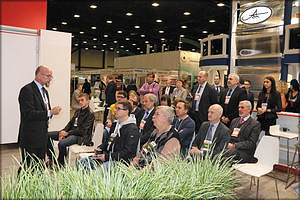
Во время онлайн-трансляции из Центра передовых технологий Honeywell в Куопио демонстрировались новинки в области видеомониторинга и интеграции систем
Большим достижением в сфере системных технологий г-н Ямсен считает возможность разрабатывать решения для автоматизации путем развития программного обеспечения и снижения зависимости от аппаратных ограничений. «При разработке систем автоматизации теперь все активнее используют облачные среды, – объясняет он. – Место для разработки систем выбирается с учетом того, где удобнее и экономичнее собрать специалистов. Основное внимание уделяется тестированию и качеству, проекты готовятся и сдаются по той же схеме, по которой выпускается программное обеспечение».
Путь, который прошли системы автоматизации со времени появления, можно поделить на четыре этапа. На смену первому поколению – централизованным закрытым системам 1980-х годов пришли серверы UNIX, жесткие диски, графические пользовательские интерфейсы и первые в истории системы сбора данных. «На тот момент системы были еще очень дороги и сложны. И зарабатывали на них профессионалы с очень узкой специализацией, – поясняет Марко Ямсен. – В 1995 году сервер UNIX для сбора данных с одной линии бумагоделательных машин стоил как трехкомнатный дом». Третий этап начался с эпохой Windows: автоматизированные рабочие места диспетчеров и разработчиков стали создаваться на основе этой операционной системы. «Все привыкли к пользовательскому интерфейсу, разработанному для потребительского сегмента. Заказчики из промышленного сектора тоже захотели им пользоваться, – говорит г-н Ямсен. – Распространение Windows, программного обеспечения и сопутствующих решений упростило производство новых продуктов, дающих дополнительные преимущества». Основной проблемой для пользователей систем третьего поколения стала необходимость постоянного обновления программного и аппаратного обеспечения, которая повышала стоимость этих систем. Ситуация также осложнялась тем, что появились угрозы информационной безопасности. Различные системы защиты практически сводили на нет гибкость, которой удалось добиться с помощью новых технологий. Решить эти проблемы и преодолеть ограничения должны системы автоматизации нынешнего, четвертого поколения. Они, по словам Марко Ямсена, позволяют интегрировать системы промышленной автоматизации и автоматизации зданий, средства контроля доступа, камеры и противопожарные системы в решения, сочетающие современные технологии с технологиями предыдущих поколений.
Без человека не обойтись
Сейчас одна из первостепенных задач, стоящих перед разработчиками, – сделать системы промышленной автоматизации более удобными для пользователей. Усилия направлены прежде всего на совершенствование функций пользовательского интерфейса, с тем чтобы облегчить диспетчерам монотонную работу.
Прямое взаимодействие машин становится все более распространенным, однако без человека в производственном процессе пока не обойтись. «Автоматизированные системы не могут самостоятельно производить электроэнергию или бумагу, они скорее контролируют производственный процесс. Бумагоделательным машинам и технологическому оборудованию по-прежнему требуется техническое обслуживание. Далеко не все операции можно выполнить удаленно через облако», – описывает г-н Ямсен текущую ситуацию.
Точнее контроль – меньше расходы
Разработанная в Финляндии система Honeywell Experion PMD R800 для управления технологическими процессами, оценки качества продукции и хранения технологических данных за короткий период была поставлена более чем на 50 предприятий в разных странах.
Эту систему внедрил, например, целлюлозно-бумажный комбинат Sappi в Граткорне (Австрия), преследуя цель ускорить процесс контроля качества бумаги и повысить его точность, чтобы улучшить механические свойства полотна, добиться стабильного качества продукции и тем самым сократить эксплуатационные расходы. Новая система позволила руководству комбината достичь цели: теперь производственные задачи планируются точнее, что способствует сокращению издержек, повышению качества продукции и росту эффективности производства.