«Kastamonu – Алабуга». Все только начинается!
Июльский Татарстан встретил проливным дождем. Все время, пока микроавтобус с логотипом KASTAMONU на борту вез группу журналистов от нижнекамского аэропорта «Бегишево» до аккуратных корпусов предприятий - резидентов особой экономической зоны «Алабуга», небо старательно хмурилось.
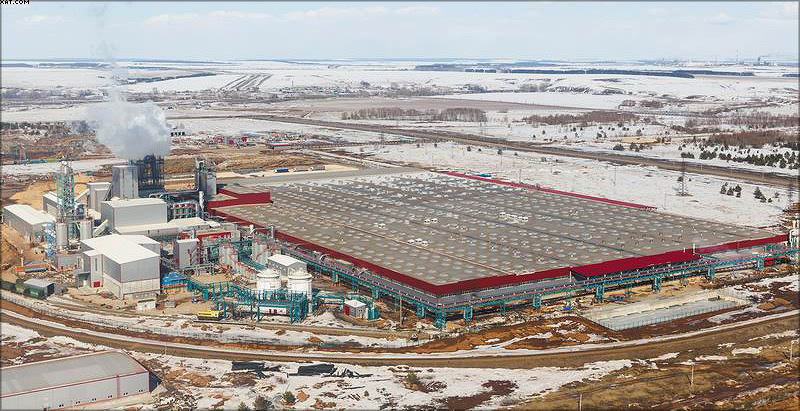
Тем приятнее было встретить радушный прием на заводе, куда нас любезно пригласил генеральный директор завода KASTAMONU Али Кылыч.
Разговор с директором завода KASTAMONU
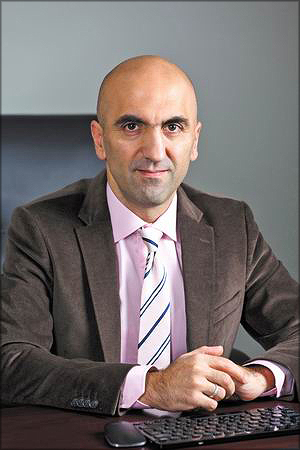
Уважаемый Али-бей сразу принял нашу делегацию, отложив все дела и на хорошем русском языке предложил задавать любые вопросы, пообещав уделить разговору столько времени, сколько понадобится.
- Прежде всего расскажите, пожалуйста, поподробнее о происходящем сейчас расширении производства.
- Сейчас идет строительство второй очереди завода. Ранее мы заявляли, что второй по счету будет линия ДСП, но в связи с изменившейся ситуацией на рынке приняли решение вместо нее ввести в строй еще одну линию по производству плит MDF. Приобретены пресс и другое оборудование, все полностью завезено на территорию, идет монтаж. Рассчитываем до конца февраля 2016 года выполнить пусконаладочные работы и ввести линию в эксплуатацию.
Считаю, что это вполне реальные сроки. Ведь мы за два года создали завод с нуля! А теперь есть действующее предприятие, опытные кадры, так что дело пойдет еще быстрее. Да и объем инвестиций требуется несколько меньший, чем в самом начале - ведь здание уже подготовлено, коммуникации подведены и т. д.
- Говоря о будущем феврале, вы имеете в виду пробный пуск?
- И пробный пуск, и следом за ним выпуск продукции. Обычно у нас так и происходит: прямо с пробного пуска в мае 2014 года мы сразу начали производство партий продукции, готовых к продаже. Так что, думаю, проблем не будет никаких.
- Какие компании выступили поставщиками оборудования?
- Как и для первой очереди, все станки для линии по производству плит MDF были приобретены у немецких производителей. Эта линия почти тождественна по составу оборудования первой.
- Говоря о причинах расширения производства плит MDF вместо пуска линии ДСП, вы отметили экономическую конъюнктуру в стране. А результаты работы первой очереди как-то повлияли на принятие такого решения?
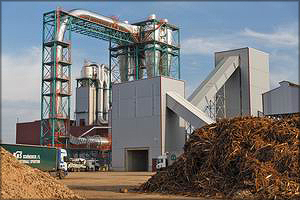
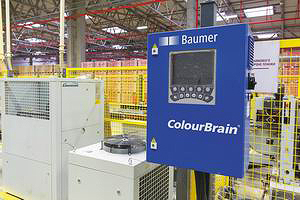
Система оптического контроля ColourBrain
автоматически определяет сортность продукта
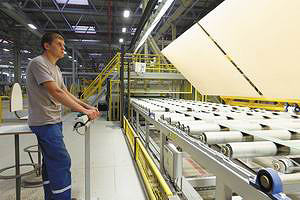
Участок контроля качества
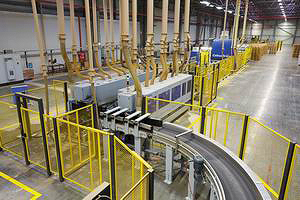
Линия по производству ламинированных напольных
покрытий (HOMAG)
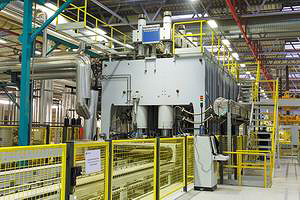
Короткотактный пресс (Wemhoener)
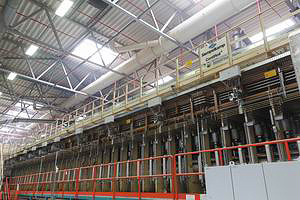
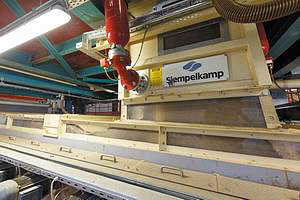
Пресс Siempelkamp для производства MDF
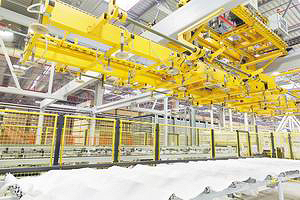
Участок сортировки и контроля качества ламинированной
плиты. Линия ламинирования (Wemhoener)
- Да, конечно. Мы оценили ее рентабельность, перспективы, растущие возможности сбыта. Это также сыграло свою роль. Но все же главный фактор - правильная оценка ситуации рынка ДСП в России: недавно запущенные и планируемые к запуску производства. То есть объемы выпуска этого продукта существенно растут, а рынок при этом очень сильно сузился. По плитам MDF/HDF тоже наблюдается сужение рынка, но в этом сегменте очень большую долю составлял импорт - ламинированные напольные покрытия, производимые на основе плит HDF, активно поставлялись из стран Европы, из Китая... В последний год объемы импорта существенно уменьшились и возникла необходимость в импортозамещении. При этом в России предприятий, производящих плиты MDF/HDF, значительно меньше, чем заводов, выпускающих ДСП. Так что считаю наше решение абсолютно правильным.
- То есть производство плит MDF/HDF KASTAMONU ориентировано прежде всего на потребление внутри страны?
- Да, на внутренний российский рынок, а также на рынки других стран (Азербайджана, Узбекистана, Казахстана, Белоруссии). Недавно отгружена первая партия продукции в Таджикистан. В планах Грузия, Армения, страны Балтии.
- Ни один разговор о древесных плитах не обходится без обсуждения экологических вопросов. Насколько важна для вас экология производства и продукции?
- Очень интересная и важная тема. Для нас вопрос сохранения природы от загрязнений на одном из первых мест, и мы никогда об этом не забываем. В сентябре мы планируем запустить очистные сооружения нового поколения, аналогов которым в России еще нет. И обязательно пригласим вас в гости на их пуск.
- Помимо строительства второй линии по выпуску плит MDF и серьезных вложений в очистные сооружения, каковы дальнейшие планы развития компании в России?
- Не так давно мы обозначили инвестиционные планы в Калужской области. Думаю, наша главная задача на ближайшие два года - создание там еще одного производства, вывод его на проектную мощность. В отдаленной перспективе возможны еще одна-две локации KASTAMONU в России.
- Ваши личные планы на будущее связаны с Россией?
- Однозначно. Неважно, где именно я дальше буду работать, но обязательно в этой стране. У меня ведь жена русская, я сам довольно давно здесь: еще в 1995 году приехал и начал работать в Петербурге.
- В таком случае не могли бы вы поделиться опытом работы иностранца в нашей стране? Каковы особенности ведения бизнеса, отличия от других стран, плюсы-минусы, возможно, какие-то характерные только для России проблемы, с которыми вам довелось столкнуться?
- Россия зарекомендовала себя как страна бюрократии. Причем не надо думать, что это однозначно плохо! Здесь прекрасно налажен документооборот, мне это очень нравится. Все можно найти и отследить по документам, а вот, например, в Турции многие дела строятся на устных договоренностях; бюрократии никакой, зато, случись что, станешь искать документацию и не найдешь ничего. Правда, надо сказать, что в последнее время взаимоотношения в бизнесе там тоже стали более формализованными. Но не до такой степени, как здесь! Подобного объема бумаг я не встречал ни в одной стране мира, хотя учился в Англии, заканчивал аспирантуру в Финляндии, 12 лет проработал в Румынии... На подписание уходит ежедневно час моего рабочего времени. Каждый день папка документов толщиной в хороший фолиант, вы только представьте себе! Если вникать в каждый документ, то ни на что другое времени не останется. Но мы ведь приехали сюда развивать бизнес, заниматься делом, а не тренироваться в росчерках на бумажных листах. Вот, пожалуй, главная для меня проблема работы в России.
Ну и есть еще одна, о которой следует упомянуть. Это особенности менталитета. Россияне если и стремятся быть специалистами, то очень «узкого профиля». Это, как если бы работнику поручили прочитать название вашего журнала на обложке, и он крупные буквы «ЛЕСПРОМ» прочитал бы, а мелкие «Информ» во второй строке - нет, да при этом еще непременно обосновал бы свою позицию: «Это в мою работу не входит». С таким отношением мириться нелегко, ведь поручая человеку определенный фронт работы, важное, серьезное дело, рассчитываешь, что он полностью берет на себя ответственность за порученное и исполнит его как должно. А оказывается, что он сделал только «отсюда досюда», а дальше, как он считает, «уже не моя работа»... Этот момент необходимо учитывать, особенно тем турецким специалистам, которые приезжают в Россию впервые и поначалу совершенно не понимают, что делать, как быть в подобных ситуациях. Надо сказать, что в нашем коллективе мы довольно быстро и успешно прожили период достижения взаимопонимания между местными работниками и приезжими.
- Ощущаете ли вы поддержку местных властей?
- Очень большую. Причем не только местных, но и самых разных уровней, вплоть до руководства Российской Федерации. Разумеется, чаще всего приходится взаимодействовать с властями республики. А они заинтересованы в развитии ОЭЗ «Алабуга» и ее резидентов. Глава региона, уважаемый господин Рустам Минниханов, регулярно бывает здесь, видит, как идут дела и строит разговор исключительно верно: «Чем я могу помочь? Чего вы ожидаете от руководства? Что вам нужно прямо сейчас?» Я считаю, именно так должен мыслить и поступать хороший руководитель. Во многом благодаря такому подходу ОЭЗ «Алабуга» так успешно развивается. Похожий склад ума и у калужского губернатора, уважаемого господина Анатолия Артамонова, не случайно ведь мы пришли и в ОЭЗ «Людиново». Инвесторы сразу обращают внимание, насколько серьезно настроена на сотрудничество власть, и отвечают на это своими вложениями в экономику. Поддержка руководства - очень важный фактор для бизнеса, иначе тут просто нечего делать. Власти нам доверяют, мы им доверяем, в результате получается очень хорошее и значимое для обеих сторон сотрудничество.
- Какова сейчас численность работников предприятия и насколько она вырастет с вводом новой линии?
- На момент пуска завода было около 530 человек, сейчас около 650. А вырастет примерно до 800. Время покажет. Я говорю так, потому что мы всегда готовим кадры немножко «с запасом», в расчете на будущие инвестиции и проекты. Выращиваем, что называется. Например, сейчас мы системно обучаем здесь людей с прицелом на работу в Калужской области, причем не только производственный персонал, но и бухгалтеров, логистов.
- Вы чуть опередили мой вопрос. Как раз хотел поинтересоваться профессиональным обучением. Ведь, как я понимаю, сотрудники предприятия - жители близлежащих мест. Едва ли они обладали глубокими знаниями и навыками в деревообработке?
- Верно, 95-97% персонала - местные жители. Рассчитывать на их высокий профессионализм было бы странно. Поэтому мы сделали так: в 2010 году начались проектные работы, а уже в 2013-м (когда и я приехал сюда) набрали костяк коллектива - работников, которым предстояло стать операторами на сложном оборудовании, и отправили их в Турцию, Румынию, Боснию и Герцеговину (в зависимости от участка, на котором предстояло работать), где несколько месяцев обучали на действующих заводах компании. А мой отдел планирования вообще полгода прожил за рубежом, готовясь к созданию этого масштабного проекта. Потом привезли опытных турецких специалистов сюда, чтобы они уже в условиях «своего» предприятия передавали новичкам необходимые знания. Таким образом, процесс обучения занял более двух лет, сейчас он почти завершен, только на двух участках остались турецкие специалисты. Мы добились успеха в деле подготовки кадров.
- И как вы оцениваете текущий уровень профессионализма работников?
- Он достойный. Мы смогли не только научить людей работать на сложных станках в условиях специфического производства, но и привить им то отношение к делу, о котором я говорил раньше. Конечно, всегда есть к чему стремиться, поэтому давайте оценим общую подготовленность в 90 баллов из 100 возможных. В жизни всегда возникают ситуации, которые невозможно предвидеть, поэтому мы продолжаем учиться.
Вообще в России хорошая школа. Инженеры, технологи здесь были подготовлены очень неплохо, просто их нужно правильно сориентировать, дать новые знания, а дальше они осваиваются сами.
- У предприятия есть собственная железнодорожная ветка. Куда она ведет?
- С помощью железной дороги мы решаем три задачи: доставляем метанол и карбамид, завозим лес, осуществляем отправку готовой продукции. Вагоны уходят из ОЭЗ «Алабуга» к станции Тихоново, оттуда - в Круглое Поле и дальше по стране.
- Есть ли особенности у татарстанского завода KASTAMONU в сравнении с другими предприятиями компании?
- Главная особенность этого завода в том, что он стал для нас первым в России. И всегда будет оставаться таким - форпостом KASTAMONU в этой стране.
Татарстан - не самый лесистый регион России, площадь покрытия лесом всего 17%. Так почему же мы пришли именно сюда? Не только производить и продавать плиту, но и для того чтобы своей деятельностью изменить качество лесов. Это цель компании, и моя тоже. Ее достижению способствует государство: здесь открыт большой питомник, высаживаются дубравы. Мы используем в производстве перестойные и переспелые деревья, что позволяет на их месте высаживать новые качественные лесные насаждения, которые обеспечат через 30-40 лет совершенно иную картину по лесам. Мы не напрасно называем себя чистильщиками лесов - ведь мы берем древесину больше нигде не востребованных пород безотносительно ее качества.
- Какой объем сырья потребуется предприятию после пуска второй очереди?
- В общей сложности 1,2-1,3 млн м3. В основном сырье закупается в Татарстане, но также в Кировской области, Пермском крае, Удмуртии. При необходимости будем доставлять лес из Республики Башкирии и Республики Марий Эл.
- Получается довольно большое плечо доставки. Насколько рентабельно в этом случае будет производить здесь плиты MDF?
- Мы делали расчеты, на основании которых можно с уверенностью сказать, что это рентабельно.
- А на сколько лет заводу хватит того сырья, которое есть поблизости?
- Вопрос хороший. Но не совсем верный. Как я уже упоминал, наша деятельность способствует ликвидации переспелых лесов в пользу новых качественных насаждений. Поэтому лесов будет не меньше, а больше. Расчетная лесосека в Татарстане составляет 2,2 млн м3 в год, так что никаких проблем с сырьевым обеспечением я не вижу. Более того, можно и нужно открывать новые производства, чтобы полностью осваивать имеющиеся ресурсы.
- Я имел в виду несколько другое. Есть планы по лесосеке, а есть реальная ситуация с лесами, которая зачастую не совпадает с официальными данными. Есть ли сейчас в Татарстане те самые 17% лесистости? Не получится ли, что существуют они только на бумаге и в отчетах чиновников?
- Как раз в настоящее время идет таксация, составляется новый план на основе космических снимков. Эта работа еще не закончена, и мы ждем точные данные, но по опыту Турции могу сказать, что по результатам таксации, как правило, леса оказывается даже больше, чем ожидалось. Думаю, похожая ситуация и в Сибири, где большой естественный прирост. В Татарстане едва ли - местность равнинная, активно развивается сельское хозяйство, но заявленные 17% лесистости, скорее всего, подтвердятся.
- Существуют ли, на ваш взгляд, какие-то недостатки в организации ОЭЗ «Алабуга»? Комфортно ли вам здесь?
- Никаких серьезных недостатков у этой локации нет. Любой из местных резидентов вам это скажет. Я вообще не представляю себе наш завод за пределами «Алабуги». Сильную поддержку и помощь получаем от управляющей компании ОЭЗ. Чтобы оперативно решить любой инфраструктурный вопрос, мне достаточно снять трубку и позвонить в их офис. Я благодарен этим людям, которые берут на себя все заботы, не связанные непосредственно с промышленным производством, и серьезно облегчают нам жизнь.
- С рабочими кадрами они помогают тоже?
- Да, в рамках этой организации существует ресурсный центр, к услугам которого можно обратиться для решения проблем с персоналом. Там помогают решать и вопросы финансового обеспечения профессионального обучения работников.
- Велика ли на предприятии текучка кадров?
- Крайне мала, могу даже сказать, что ее нет. Мы - социально ориентированная компания, заботимся о своих сотрудниках, и им нравится работать в KASTAMONU.
- Если можно, расскажите немного о себе. Как получилось, что вы оказались в России и возглавили предприятие в Татарстане?
- У меня лесотехническое образование (магистр, окончил факультет лесного хозяйства и инженерии Стамбульского университета), я вообще потомственный «лесник». Отец заведовал лесхозом в Анкаре. Впервые я приехал в Россию в 1995 году - в Санкт-Петербурге было лесопильное предприятие, делали доску и отправляли на экспорт в Европу, Северную Африку... То предприятие, а также логистический центр, которые находились на Северо-Западе России, входили в структуру строительно-промышленной группы, основная часть которой располагалась в Сибири.
Потом я решил делать карьеру в лесной промышленности. Сначала поехал учиться в Англию, изучал язык (и менеджмент). Потом окончил аспирантуру в Финляндии. Получил предложение занять руководящую должность на предприятии KASTAMONU в Румынии (2003 год), проработал там несколько лет. С 2010 года в России, с основания нашего российского бизнеса вместе с Онуром Гювеном (вице-президентом группы компаний KASTAMONU. - Примеч. ред.). Получил в Турции MBA по менеджменту.
Я постоянно учусь, развиваю свои навыки. Владею четырьмя языками: турецким, английским, румынским и русским. Немножко финским. Это необходимо, ведь впереди еще много работы!
Экскурсия по заводу KASTAMONU
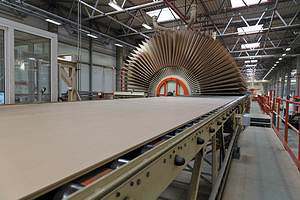
Трехсекционный веерный охладитель плит
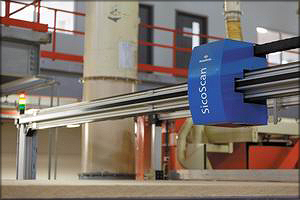
Толщинометр и ультразвуковой дефектоскоп (SicoScan)
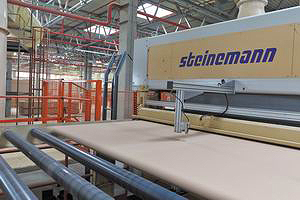
Линия шлифования MDF/HDF (Steinemann)
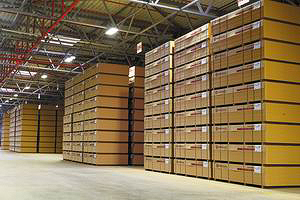
Готовая продукция транспортируется на склад
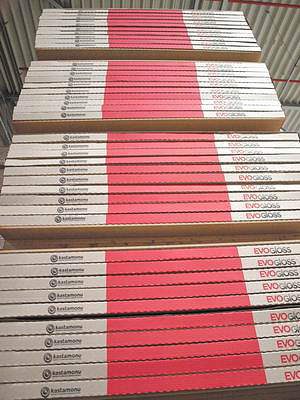
Глянцевые панели EVOGLOSS, используемые для
изготовления мебельных фасадов
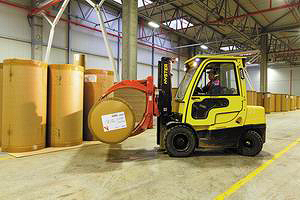
Для декора плит используется бумага производства
Schattecor и Interprint
Поскольку на предприятии вовсю идет монтаж второй линии по производству плит MDF, то на некоторые участки мы не могли попасть просто по соображениям безопасности. Однако наш сопровождающий, начальник цеха плит MDF Мустафа Гек, и его коллеги в цехах сделали все, чтобы гости получили исчерпывающие ответы на все их вопросы о технике и технологиях, применяемых здесь.
Большая часть древесного сырья закупается предприятием у министерства лесного хозяйства Республики Татарстан, остальное - у частных лесных хозяйств. В производстве плит используются береза, липа, сосна, а также осина и ель. Сырье на завод доставляется как автомобильным транспортом, так и по железной дороге, специально построенной вместе с первой очередью предприятия. Древесина перед поступлением на производство проходит контроль качества в лаборатории завода, а затем отправляется на базу сырья и складируется по породам.
На входе в основной цех неделовая древесина проходит через окорочный станок и измельчается в щепу на рубительной машине дискового типа производства австрийской фирмы Andritz. Щепа в зависимости от древесной породы направляется в четыре бункера промежуточного хранения (объем каждого 1700 м3), откуда сырье по системе воздуховодов (производства компании Scheuch) поступает на рефайнинг, подается на вибрационное сито, где сортируется по фракциям. Далее щепа по конвейеру отправляется в промывочную установку, где из древесной массы удаляются примеси. Очищенная щепа отделяется от технологической воды и подается в бункер пропарочно-размольной установки. На предприятии установлена многоступенчатая система очистки производственных сточных вод производства турецкой фирмы EnTa; в ней выполняется механическая, биологическая и химическая очистка воды, а также дополнительная очистка на мембранных системах и обезвоживание образовавшихся осадков.
После предварительной пропарки щепа через набивной шнек равномерно подается в варочный котел Andritz, а затем в размольную установку того же производителя. На выходе полученное волокно поступает на мощную установку для осмоления Ecoresinator (производительность - 65 т волокна в час), где используется новейшая технология инъекционной пропитки, позволяющая экономить до 15% твердого клеящего вещества по сравнению с традиционным способом нанесения клея методом продувки. Оптимальное давление разбрызгивания гарантирует отсутствие капель клея на волокне и низкий износ сопел. Смеситель работает на невысокой скорости, вследствие чего сохраняется структура стружки и снижается потребление энергии, необходимой для охлаждения. На производстве используется карбамидоформальдегидная смола, основную часть которой KASTAMONU производит на собственном клеевом заводе, кроме того, смолы закупаются у российских компаний.
Осмоленное волокно по массопроводу подается в одноступенчатую трубу-сушилку Buettner с мгновенным парообразованием. Агентом сушки является воздух, смешанный с топочными газами. В трубе-сушилке влажность древесного волокна снижается с 80-100 до 6-14%. Сухое волокно поступает в систему воздушной сепарации фирмы Scheuch (Австрия), где отделяется от воздуха и по шнековому транспортеру поступает в бункер-дозатор формующей машины. Отсюда волокно равномерно подается на линию формирования древесноволокнистого ковра. После подпрессовки (за счет нее удаляются излишки воздуха и влаги) ковер необходимой ширины и толщины поступает в гидравлический пресс горячего прессования ContiRoll производства компании Siempelkamp (Германия) мощностью 1,8 тыс. м3 в сутки (максимальная производительность пресса, заявленная изготовителем, составляет 1,93 тыс. м3 в сутки). Пресс, который эксплуатируется на заводе KASTAMONU, самый крупный из подобных прессов, установленных на плитных производствах в Европе: его длина 55,3 м, а ширина 2,8 м.
Перед прессованием ковер проходит контроль влажности, насыпной плотности и наличия металлических вкраплений. Бракованная продукция сбрасывается с линии. Температура в прессе варьирует от 170 до 240°С. Скорость прессования составляет 1,5 м/с.
Линия по производству плит MDF (пущена в мае 2014 года, оборудование обслуживает 14 человек в смену) производит плиты толщиной от 4 до 40 мм и плотностью до 900 кг/м3. При толщине плиты 16 мм ежедневная мощность линии достигает 1845 м3. Компания Siempelkamp установила энергетическую систему мощностью 85 МВт, а также паровую турбину 52 МВт. На выходе из пресса ковер поступает на участок раскроя Siempelkamp.
Технология предполагает два этапа раскроя плит, первый выполняется на выходе из пресса. Здесь две пилы разрезают бесконечное древесноволокнистое полотно на полуфабрикаты крупного размера для охлаждения в веерном охладителе. Это огромный ротор с направляющими, на которые помещается до 45 плит одновременно, полуфабрикаты достигают длины 7320-8625 мм и ширины 2460-2850 мм. После охлаждения плиты пропускаются через толщиномер и ультразвуковой дефектоскоп SicoScan, разработанные Siempelkamp в сотрудничестве с Electronic Wood Systems (Германия).
По завершении этапа охлаждения плиты выдерживаются на промежуточном складе в течение 24-48 ч, а затем поступают на участок шлифования, где установлена линия Satos 28 K-KK-NNN фирмы Steinemann (Швейцария). Скорость станка, на котором установлено 12 шлифголовок, достигает 200 м/мин., а максимально допустимое отклонение по толщине не превышает 0,2 мм. Используются шлифовальные ленты как производства Steinemann, так и местных производителей, которых KASTAMONU старается поддерживать (правда, российские компании сами не делают ленту, а покупают за рубежом, здесь склеивают и подготавливают в соответствии с нуждами конкретного производства).
Далее продукция проходит второй этап раскроя. Ширина готовой плиты - 2440-2800 мм, а при раскрое посередине - 1220-1400 мм, длина варьирует в пределах 1700-4300 мм. Толщина плит - 6-30 мм, при этом около половины продукции составляют плиты толщиной 16 мм. Далее плиты поступают на две линии ламинирования Wemhoener (Германия), которая за один такт ламинирует три плиты. Ее производительность достигает 180 тактов в час, то есть 540 плит в час. Совокупная годовая производительность двух линий ламинирования составляет 3 млн м2.
У обоих короткотактных прессов в «Алабуге» формат прессования - 8,850 x 2,200 мм, они рассчитаны на давление от 400 до 650 Н/см3. Общая длина установок - 161 м. Они оснащены полностью автоматизированной системой подачи материала и приема необработанных и готовых плит, а также подачи бумаги. Кроме того, одна из установок оснащена системой тиснения в регистр. В состав установок входят устройства для укладки плит перед прессом, обработки краев изделий после их прохождения через пресс, охлаждения плит, штабелирования и упаковки. По завершении ламинирования плиты проходят контроль качества. Система оптического контроля ColourBrain автоматически определяет сортность продукта.
Часть плитной продукции HDF поступает в цех производства напольных покрытий на линию Homag (Германия) максимальной мощностью 20 млн м2 в год. Для декора плит используется бумага производства компаний Sсhattdecor и Interprint. Выпускается ламинат 31-33-го класса износостойкости. Толщина стандартная: 8 и 6 мм. Цветовая линейка - более 70 декоров (планируется увеличение до 100 декоров и фактур). Стандартная программа ламинированных полов Floorpan насчитывает 52 декора, дополнительно 22 декора производятся для крупнейших российских гипермаркетов. Производственную цепочку в цехе ламината завершает участок контроля качества продукции, где проверяется выбранная тестовая часть из каждой готовой партии: оператор вручную проверяет качество продукта, геометрию профиля, чтобы не было расхождений с установленными стандартами.
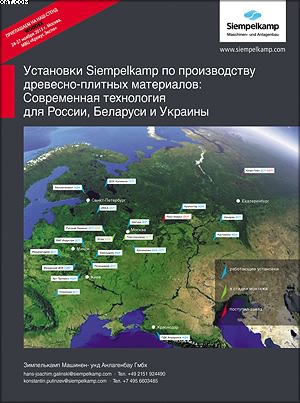
Siempelkamp. Оборудование для производства
древесных плит
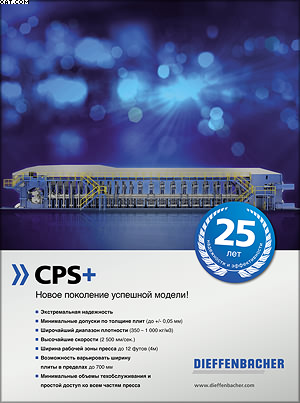
Dieffenbacher. Оборудование для производства
древесных плит
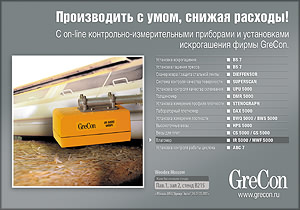
GreCon. Системы искрогашения и измерительные
системы
На заводе изготавливают плиты MDF толщиной от 6 до 30 мм. На наиболее популярные 16-миллимметровые шлифованные и ламинированные плиты средней плотности, которые используют производители фасадов и мебели, приходится около половины выпуска. На предприятии налажено производство глянцевых панелей EVOGLOSS, используемых для изготовления мебельных фасадов.
Готовые, разрезанные по размеру и отшлифованные плиты подаются на участок, где их сортируют по качеству и формируют в пакет, который затем идет на упаковку. Станок фирмы Orgapac (Швейцария) обтягивает фиксирующей лентой, итальянский станок Seat пакует в стрейч-пленку. Промышленный робот-манипулятор Kuka формирует палеты с упакованной продукцией. Поскольку на экспорт готовые изделия отгружаются водным транспортом (надо отметить, что продукция завода поставляется в том числе и на родину KASTAMONU - в Турцию), использование стрейч-пленки обязательно - это позволяет защитить поверхность плиты от механических повреждений, избежать попадания влаги и т. д.
На том же участке установлено вспомогательное оборудование от итальянского концерна SCM - линия с пильным центром, на которой из плиты MDF производят бруски с заданными геометрическими размерами для перекладки пакетов. Производительность этого оборудования - 8 шт./мин. (до 120 тыс. брусков в месяц).
Готовая продукция поступает в складской комплекс площадью 55 тыс. м2 (124 тыс. м2 с учетом открытых площадок). В одной зоне складируются плиты MDF и HDF, в другой - ламинированные полы. Отгрузка продукции происходит как автомобильным транспортом (вблизи предприятия проходит федеральная трасса М7), так и по железной дороге. Продукция может транспортироваться еврофурами, контейнерами, крытыми грузовыми вагонами, морскими сухогрузными контейнерами. Электроэнергия для нужд предприятия вырабатывается собственной газотурбинной электростанцией (ГТЭС) мощностью 30 МВт. Блочно-модульная ДКУ (дожимная компрессорная установка низкого давления) от компании «Энергаз» установлена в звукопоглощающем укрытии, оснащена системами жизнеобеспечения (обогрев, вентиляция, освещение) и безопасности (пожарообнаружение, пожаротушение, газодетекция). Ранее «Энергаз» поставил для нужд завода блок подготовки топливного газа, оснащенный системами фильтрации и коммерческого учета, а также узел редуцирования газа.
Что касается второй очереди предприятия, ввод которой в эксплуатацию намечен на будущий год, то новая линия по производству плит MDF строится параллельно действующей и будет почти идентична ей. За исключением «сердца» системы, то есть пресса: там устанавливается оборудование от другого германского промышленного гиганта - компании Dieffenbacher. Необходимо отметить, что смена поставщика пресса произошла не из-за предпочтений по качеству или цене, а продиктована политикой компании: еще в 2007 году, до появления завода в «Алабуге», руководство KASTAMONU вело переговоры о совместном проекте с Dieffenbacher, но впоследствии возникла идея строительства линии ДСП и проект решили отложить. Когда от этой идеи отказались в пользу второй очереди производства плит MDF, к этому проекту вернулись.
Оборудование по окорке, производству и подготовке щепы и волокна, рефайнеры - все производства компании Andritz. Послепрессовое оборудование и станки для шлифовки поставят компании Contra и Steinemann. Для сушки Dieffenbacher поставит сушильную систему собственного производства.
Вся продукция завода KASTAMONU в ОЭЗ «Алабуга» сертифицирована по стандартам ISO 9001, ISO 14001, OHSAS 18001. Также компания является обладателем сертификата FSC, подтверждающего, что выпускаемая продукция соответствует международным экологическим стандартам. KASTAMONU работает только с сертифицированными поставщиками сырья.
Подготовил Максим ПИРУС
Благодарим компанию KASTAMONU и агентство медиакоммуникаций Feedback за помощь в организации поездки
Справка
Компания KASTAMONU образована в Турции в 1969 году в составе холдинга HAYAT, который существует с 1937 года. Компания специализируется на производстве древесных плит MDF, ДСП, ламинированных напольных покрытий, дверных накладок, глянцевых панелей и столешниц. KASTAMONU входит в пятерку крупнейших компаний деревоперерабатывающей отрасли в Европе. Ее годовой оборот в 2014 году составил $1,2 млрд.
Первый завод по производству ДСП был пущен в 1971 году в г. Кастамону. В 1998 году открыт первый зарубежный завод по производству дверных панелей Dorpan - в Румынии, на базе выкупленного и переоборудованного предприятия S. C. Petrolemn S.A. В 1999 году на заводе в г. Гебзе было запущено производство ламинированных напольных покрытий Floоrpan.
Начиная с 1999 года ежегодно или раз в два года в той или иной стране открывалось очередное производство KASTAMONU. Введены в эксплуатацию десять новых и модернизированы три первых завода компании. Румыния, Болгария, Босния и Герцеговина, Россия стали для KASTAMONU важными стратегическими точками в завоевании европейского потребителя.
В ближайшие четыре года запланирован очередной пакет инвестиций объемом $500 млн. Следующий завод KASTAMONU планируется к открытию в 2018 году в Калужской области.
Справка
Завод KASTAMONU по производству плит MDF/HDF в ОЭЗ «Алабуга», г. Елабуга, Республика Татарстан, Россия.
Продукция: необработанные и покрытые меламином плиты MDF, ламинированные напольные покрытия.
Крытых площадей - 120 000 м2. Открытых площадей - 600 000 м2.
Инвестпроект стартовал в 2012 году. Первая очередь - линия по производству плит MDF мощностью 565 тыс. м3 в год пущена в мае 2014 года. Летом того же года пущена линия по производству ламинированных напольных покрытий годовой мощностью 20 млн м2. В планах компании на 2016 год увеличение мощностей по производству плит MDF еще на 450 тыс. м3. Срок окупаемости проекта - 7-10 лет.
Решение инвестировать средства именно в Татарстане принималось с учетом тесных культурно-исторических связей этой республики с Турцией, а также логистических преимуществ, связанных с географическим положением региона. С открытия первого завода в г. Елабуге начинался масштабный выход KASTAMONU на рынки России и ближнего зарубежья. ОЭЗ «Алабуга» должна стать базой для развития отраслевых отношений между Россией и странами СНГ.
Предполагается, что около 75% продукции завода будет реализовываться в России. Оставшиеся 25% будут направлены на экспорт в страны Азии и Европы.
На заводе KASTAMONU создано более 600 новых рабочих мест непосредственно на производстве и более 2500 - в смежных и вспомогательных отраслях (транспорт, лесозаготовка и т. д.).
Справка
ОЭЗ «Алабуга» создана в соответствии с постановлением № 782 Правительства Российской Федерации от 21 декабря 2005 года на территории Елабужского района (Республика Татарстан). Приоритетными направлениями бизнеса в этой зоне являются автомобилестроение и производство автокомпонентов, приборостроение, выпуск композитных материалов, строительство, нефтехимия и производство товаров народного потребления.
Государство предоставляет инвесторам налоговые и таможенные льготы, льготные арендные ставки и готовую инфраструктуру, за счет чего у бизнеса появляется возможность для более интенсивного развития. Объем государственных инвестиций - 23 млрд руб. Объем инвестиций компаний-резидентов - 86,9 млрд руб.
Общая площадь ОЭЗ - 4 тыс. га. Более 5 км железнодорожных путей, интегрированных в сеть «РЖД», соединяют ОЭЗ с грузовой железнодорожной станцией Тихоново. Ближайший пассажирский железнодорожный вокзал находится в 25 км, в г. Набережные Челны.
В полукилометре от ОЭЗ проходит федеральная трасса М-7.
До международного аэропорта Бегишево 60 км.
На 15 мая 2015 года в ОЭЗ «Алабуга» насчитывалось 47 компаний-резидентов с общим объемом заявленных инвестиций примерно 150 млрд руб. В их числе две компании международного холдинга HAYAT: KASTAMONU (производство древесно-плитной продукции) и HAYAT KIMYA (производство санитарно-гигиенической продукции).
ЛесПромИнформ №7 (105), 2014 г. Kastamonu – новый деревообрабатывающий комбинат в Татарстане