«Плитспичпром». Перспективы становятся победами
Наш журнал довольно часто пишет о тех или иных аспектах деятельности предприятий промышленной группы «Союз», и в том числе о входящем в ее состав балабановском АО «Плитспичпром» (более 40 упоминаний на нашем сайте!). Это говорит как о постоянной бизнес-активности компании, на которую оперативно реагирует «ЛПИ», так и о правильном отношении компании к прессе, которая не пренебрегает таким способом заявить о себе на рынке. Благодаря этому мы (а значит, и наши читатели) всегда в курсе новостей «Плитспичпрома».
Мои коллеги побывали на предприятии в 2009 году, результатом этой поездки стал очерк «"Плитспичпром". Формула успеха» в № 5 (63). И когда появился повод для нового визита - а 2015 год стал для предприятия прорывным, - конечно, мы не преминули им воспользоваться.
О том, что произошло на «Плитспичпроме» после нашего первого посещения, о сегодняшнем и завтрашнем дне предприятия в ходе экскурсии по заводу рассказал его генеральный директор Евгений Власов.
Стратегия и тактика «Плитспичпрома»
- Евгений Гаврилович, только за последний год на «Плитспичпроме» осуществлен пуск линии по изготовлению деревянных погонажных изделий в цехе клееных изделий, завершена реконструкция сушильного хозяйства, введены в эксплуатацию вторая очередь производства дверных полотен, новая котельная, новая линия сортировки круглого леса, строится новый цех ДСП. И наконец, реализован масштабный проект создания современного лесопильного комплекса. Получается, что на непростое время кризиса у вас пришелся период активного развития. Понятно, что контракты заключались еще в докризисные времена, и все же - как вам это удается?
- Никакого секрета тут нет. Для экономистов происходящие процессы прозрачны и понятны: одни игроки уходят с рынка, другие занимают их ниши. Одни разоряются - другие зарабатывают. Одни пытаются сокращать издержки - другие вкладывают средства в развитие. Так всегда было и всегда будет. Мы нацелены не на экономию, а на зарабатывание. Считаем, что как раз сейчас начинается определенное перераспределение рынка, а нам реализация инвестпроектов позволит выйти на растущий рынок на новом витке циклично развивающейся экономики. Сейчас, на этапе спада, необходимо так подготовиться к будущему, чтобы на этапе роста получить свою долю рынка, обеспечить объемы выпуска товарной продукции и продаж. Загрузка мощностей обеспечивает рентабельность производства.
- То есть уместно говорить о подготовке к качественному скачку как элементу долгосрочной стратегии?
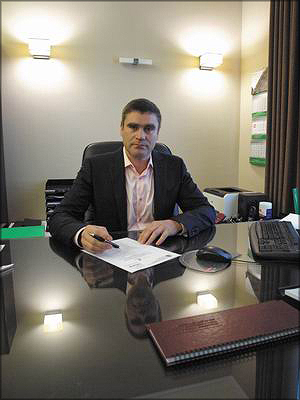
Генеральный директор АО «Плитспичпром» Евгений Власов
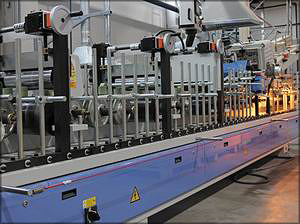
Автоматическая линия по склейке композитных заготовок
- Конечно. Мы идем на серьезные затраты, создавая полный цикл производства. Держа в своих руках такую единую цепочку, можно минимизировать последствия кризисных явлений для предприятия. Когда в том или ином сегменте рынка случается спад, есть возможность перестроить всю цепочку, перестроить звенья замкнутых конечных самодостаточных производств.
- Ваша продукция не так уж «завязана» на рыночные продажи, поскольку по большей части потребляется другими подразделениями ПГ «Союз», верно?
- Именно так. И это тоже помогает нам держать удар. Работая в группе, мы, если можно так выразиться, стоим ближе к сырью, а наши партнеры из компании «СоюзБалтКомплект» занимаются выпуском конечных продуктов с высокой добавленной стоимостью из сырья, которое получают в том числе и от нас: столешницы, мебельные фасады, стеновые панели, фальш-полы и т. п.
Вообще, акцент в работе нашего предприятия и промышленной группы «Союз» в целом делается на том, чтобы в рамках своих структурных единиц выполнять полный цикл производства - от заготовки древесного сырья в лесу до выпуска полностью готовой продукции (как в случае изготавливаемых нами домов). В качестве примера могу привести микрорайон в Балабаново, застроенный нами под ключ: 10 га площади, 500 с лишним квартир в домах.
C воодушевлением восприняли идею импортозамещения. Фактически стремление нашей ГК к созданию полного цикла производства - это и есть самое настоящее импортозамещение: если все «от и до» (этапы производства от заготовки сырья до выпуска конечного продукта) мы способны реализовать здесь, у себя, зарубежная продукция становится просто не нужна! Ведь это и правда никуда не годится: продаем за границу круглый лес, а потом покупаем сделанную из него финскую бумагу, итальянскую мебель... Можно все перерабатывать у себя, важно выдерживать уровень качества, уделять внимание дизайну. «Импортные» концепты, технологии, современные подходы - всему этому можно и нужно учиться, перенимать опыт у ведущих специалистов, но применять его на собственных, российских предприятиях!
Заступив на должность генерального директора в 2013 году, я одновременно стал участником команды, которая разработала концепцию «Стратегии комплексного развития предприятия». Программа комплексного развития включает в себя три больших инвестиционных проекта. Первый - производство межкомнатных дверей на бывших мощностях спичечного цеха; его удалось реализовать быстрее всего (понятно, что реконструкция и техническое перевооружение требуют все же меньше затрат и времени, чем строительство цеха с нуля, - а именно из-за строительных работ у нас в России часто надолго задерживаются сроки пуска проектов). Работы заняли всего полгода с момента старта проекта. Второй - масштабный проект по лесопилению; по сути, за год его удалось воплотить в жизнь. Третий проект - перевооружение производства ДСП; тут мы еще в самом начале пути. Но кое-что из достигнутого я уже готов вам продемонстрировать.
Производство дверей на «Плитспичпроме»
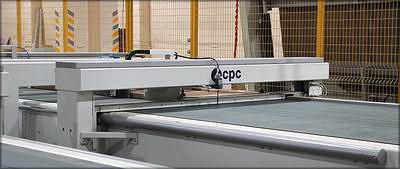
Автоматический пресс линии сборки дверных полотен
Экскурсия по предприятию началась с дверного производства. Межкомнатные царговые двери на «ПСП» выпускаются под брендом Alleanza Doors. Этот продукт был создан в результате сотрудничества российских и итальянских разработчиков на основе наиболее интересных европейских дизайнов и в русле модных тенденций в области интерьера. При этом он полностью адаптирован к российским реалиям.
Приведем пару примеров. Основа дверей серии Gemina - полотно из стекла триплекс и обрамляющих его по бокам стоек из древесной плиты. Серия Ferrata (цветовые и декоративные решения - ясень белый, орех капучино, куба махагон, орех африканский, карамель и др.) - полотно из горизонтальных полос древесной плиты, перемежающихся полосами стекла, плюс вертикальные стойки. Двери изготовлены из плит MDF, облицованных полипропиленовыми покрытиями, имитирующими ценные породы дерева.
Дверное производство на «Плитспичпроме» состоит из трех очередей: две в настоящее время эксплуатируются, а третья находится в стадии разработки.
Производственные участки:
- участок подготовки заготовок: раскрой листов ДВП/ДСП, склеивание и фрезеровка деталей. Здесь делается погонаж для стоевых, средников, краевых деталей для царговых моделей, а также выполняется укутывание этих деталей;
- участок подготовки филенки; здесь лист ДСП сначала облагораживается, шлифуется, а потом кроится по карте раскроя на части оптимальных размеров (для выполнения последующих производственных операций с минимальными отходами);
- участок нарезки стекла; здесь работает высокопроизводительный раскроечный станок;
- участок прирезки заготовок; здесь полученные со склада полуфабрикатов заготовки прирезаются с учетом задела на следующий день;
- участок сборки; где из заготовок операторы собирают готовые изделия;
- участок проведения испытаний и служба качества: качество изделия в обязательном порядке проверятся на соответствие всем нормативам, отсутствие механических повреждений и технологического брака;
- склад готовой продукции с раздельными зонами комплектации, хранения, долгосрочного хранения.
Поступающее в цех сырье: плита ДВП, ДСП, MDF разной толщины - раскраивается на полуфабрикаты и фрезеруется. Готовые заготовки поступают на специальные прессы для укутывания пленками, и на выходе с линии на специальных столах визуально проверяется качество изделий, на них наклеиваются этикетки со штрих-кодом и индивидуальным номером контролера. Продукцию упаковывают в коробки и отправляют на склад, где она размещается на палетах и затем погрузчиками подается на отгрузку. В работе задействовано оборудование таких производителей, как Altendorf, Barberan и др. Цикл производства от входа сырья до получения готовой двери занимает неделю.
«Производство совсем новое, год как пущено. Надо еще немного времени, чтобы оно в полном смысле развилось, - считает Евгений Власов. - Но перспективы уже сейчас просматриваются очень хорошие. Пока цех работает в одну смену, но объем производства неуклонно растет, что в самом ближайшем будущем приведет к необходимости перехода на двухсменный режим. Мы к этому готовы, сотрудников, можно сказать, с запасом взяли - на основных операциях сейчас по два работника там, где справится и один, второй помогает и обучается. Так что мы без проблем оперативно перейдем на двухсменный режим работы, примерно по 55 человек в смену».
По словам генерального директора, возможность появления брака на производстве фактически сведена к нулю: «По нормам отрасли, на брак отводится до 4% выпуска, но у нас ОТК пресекают нарушения качества на всех этапах производства и выявляют даже скрытые дефекты. Потребителю отправляется только ликвидный товар. По опыту могу сказать, что возникающие у клиентов претензии связаны чаще всего не с производством, а с транспортировкой изделий с завода потребителю.
Пленки для укутывания дверных полотен приходится покупать за рубежом, собственного производства пока нет. Из того, что мы пока не делаем сами, можно еще упомянуть стекло: приобретаем отечественное, оно поступает большеформатными листами и раскраивается на мощном автоматизированном центре в соответствии с задаваемыми в программе размерами. Постоянного поставщика стекла нет, он выбирается по результатам тендеров. Критерии выбора очевидны: цена, логистика, сроки поставки и предоставление отсрочек платежа. Последний момент очень важен: определенное время требуется на отгрузку и доставку готовой продукции, а торговые сети, покупая у нас продукцию, зачастую берут отсрочку на 60-70 дней - нам надо, в свою очередь, "дублировать" ее при покупке комплектующих. Если поставщик готов на такие условия, мы гарантируем, что будем выбирать большие объемы, тем самым заинтересовывая его в сотрудничестве».
Для проверки качества произведенных дверей в цехе установлен испытательный стенд. Из каждой партии произвольно делается выборка, дверь устанавливается на стенд и проверяется на 47 тыс. открываний.
«Даже петли изнашиваются, а с самой дверью все в порядке!» - с улыбкой комментирует генеральный директор предприятия.
Производство погонажа и клееного бруса
В цехе установлено оборудование словенской компании Ledinek. Бóльшая его часть работала здесь и шесть лет назад, когда на завод приезжали мои коллеги, однако в прошлом году добавилось новое оборудование, в частности, для организации участка погонажа.
«Сейчас мощность этого участка невелика, - комментирует Евгений Власов, - но мы планируем увеличить ее раза в три-четыре за счет освоения свободных площадей. Одновременно с поставкой основного оборудования мы приобрели у компании Ledinek и полностью укомплектованную лабораторию, которая позволяет осуществлять проверку прочности изделий: мы периодически проверяем качество и выполняем замеры клеевого шва».
До создания собственного лесопильного комплекса компания закупала лесоматериалы у сторонних поставщиков. В цех лесоматериалы доставляются погрузчиком. После калибровки и строжки досок выполняется вырезка дефектов на линии оптимизации. Далее нарезаются шипы на каждой доске, наносится клей (как и в прошлые годы, используется клей производства AkzoNobel), и заготовки поступают на линию непрерывного сращивания. Ламели нарезаются в размер - как правило, длиной 13 м - а затем поступают в пресс. Готовый брус профилируется в чашку, обрабатывается со всех сторон, упаковывается и поступает на склад, расположенный здесь же. На упаковках готового бруса, вагонки и прочих изделий значится логотип «Доминанта», под которым эта продукция продвигается на рынке.
«Мы очень строго подходим к качеству изделий, соблюдению ГОСТов, - подчеркивает Евгений Власов. - Нескромно себя хвалить, но по отзывам дилеров, наш сорт С соответствует на рынке сорту В, а сорт АВ - сорту А. Это вовсе не значит, что следует просто "переписать" сортность в попытке заработать дополнительную прибыль, это говорит об уважении к клиенту, приверженности компании самым высоким стандартам. Качество всегда должно быть на высоте, продукция должна выпускаться в строгом соответствии с установленными стандартами, а клиент никогда не должен даже задумываться о том, что могло быть иначе. Это один из основных принципов, которыми мы руководствуемся в работе.
Мы готовы предложить клиентам клееный брус сечением 175, 190, 200 и 220 мм. При необходимости выпускаем также и более тонкий брус (для небольших построек и малых архитектурных форм) - сечением 130, 140 мм. Недавно мы осуществили поставку сразу восьми домов из тонкого клееного бруса в одну из среднеазиатских стран - вероятно, их будут использовать в качестве бунгало на побережье. Для теплого климата более толстый брус, пожалуй, избыточен. Успешно продается в Среднюю Азию и тонкая доска пола - видимо, по той же причине».
Производство домокомплектов
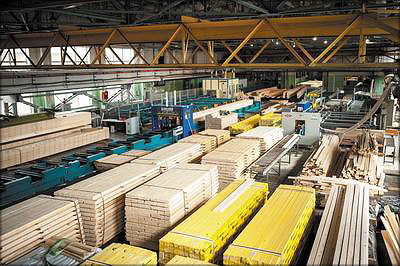
Дома из профилированного клееного бруса и материалы для их строительства «Плитспичпром» производит и реализует под торговой маркой «Доминант», приобретающей все большую известность благодаря участию компании в профильных выставках, а также за счет реализованных проектов - предприятие не только выступает производителем домокомплектов, но и возводит силами своих специалистов как отдельные дома, так и целые коттеджные поселки («Ворсин луг», «Воскресенское», «Микрорайон Гагарина»).
Случайный знакомый, узнав о цели моей поездки в Балабаново, рассказал, что, выбирая для себя брусовой дом, по качеству ориентировался именно на продукцию «Плитспичпрома», но потом вынужден был остановиться на другом производителе - просто «не потянул» по цене.
«Да, отдельные проекты домов из клееного бруса у нас дороже, чем у некоторых конкурентов, - говорит в ответ на мою историю Евгений Власов. - Это обусловлено несколькими важными причинами. Прежде всего это культура производства, которая непосредственно влияет на качество продукта. К сожалению, подавляющее большинство мелких производителей в Подмосковье все еще делают домокомплекты, что называется, "на коленке»: в каких-то гаражах, на неведомых станках и руками совершенно неквалифицированного персонала. Наши изделия изготавливаются на самом современном оборудовании, из самых качественных материалов, что не может не влиять на цену.
Среди несомненных достоинств наших домов есть еще и такое: мы предлагаем клиенту полностью подготовленный комплект - ничего не нужно дорабатывать, подпиливать на стройплощадке. Мы подбираем оборудование, позволяющее изготавливать изделие максимальной готовности. Это действительно такой дом, к которому в полной мере применимо понятие "под ключ". Такую степень готовности декларируют многие, но мало кто ее обеспечивает...»
Есть и особенности упаковки и отгрузки домокомплектов на «Плитспичпроме»: комплекты собираются повенечно. То есть на объекте строителям достаточно последовательно вскрывать упаковки и собирать дом, как конструктор.
«Это очень удобно, но мало кто из производителей так делает, - комментирует директор. - Традиционно складывают комплект, исходя из логистики и компактности упаковок. Думая о своем удобстве, а не покупателя. Понятно, что, складывая детали из бруса по венцам, мы получаем разногабаритные упаковки, которых в транспортное средство помещается меньше, чем в случае отгрузки одинаковых деталей вместе. Но мы считаем свой подход правильным».
На участке сборки домокомплектов работают две линии Schmidler, которые обслуживает один оператор. Все перемещения деталей по цеху осуществляются погрузчиком Combilift. В месяц производится около 20 домов. Загрузка в течение года почти равномерная.
«Тем и хорош клееный брус, - поясняет Евгений Гаврилович, - что дом из него можно собирать в любое время года, даже зимой. Многие заказчики специально так подгадывают: летом закладывают фундамент, а возведение дома оставляют на "несезон", когда строители менее загружены».
Так сложилось, что мы обедали в заводской столовой вместе с одним из деловых партнеров «Плитспичпрома» - бизнесменом из Эстонии, который занимается продажей деревянных домов (в том числе российских) в странах Европы. Евгений Власов надеется, что в числе этих домов будет все больше и больше продукции из Балабаново. Разговорились. Эстонский партнер не впервые размещает свои заказы на «Плитспичпроме» (для него и других заказчиков домокомплекты производятся здесь под торговой маркой клиента) и вполне доволен сотрудничеством. Объездив не один десяток заводов, он выбрал «Плитспичпром» за качество продукции, культуру производства, используемые современные технологии.
«Сейчас мы проходим необходимую для "европейского прорыва" сертификацию, - говорит генеральный директор АО «Плитспичпром». - Процесс начался, пройден аудит, в ближайшее время, я уверен, мы получим FSC-сертификат на цепочку поставок. Параллельно нужно будет получить сертификат EN 14080/14081 по классификации прочности клееной древесины. Каждую партию своей клееной древесины мы тщательно проверяем, и она соответствует всем европейским стандартам. Осталось получить документальное свидетельство - и можно активно заниматься поставками за пределы России».
«Наличие такого сертификата еще пять лет назад рассматривалось всего лишь как дополнительный плюс, а сейчас это уже обязательное требование в Евросоюзе, - поясняет эстонский коллега. - Компании хотят себя всячески обезопасить. Успешно конкурировать без него уже не получится, особенно если клееные изделия поступают из-за пределов Евросоюза, тем более из России. Хорошо, что у руководства предприятия есть понимание необходимости прохождения всех этих процедур!»
«Каждый наш дом индивидуален, - с гордостью говорит г-н Власов. - Подготовлен для конкретного заказчика нашим проектно-конструкторским бюро. Клиент приезжает, при участии наших архитекторов и конструкторов разрабатывает эскиз - с вариантами планировок и оформления, вспомогательных помещений. У нас наработаны тысячи разнообразных эскизов домов».
Новая котельная
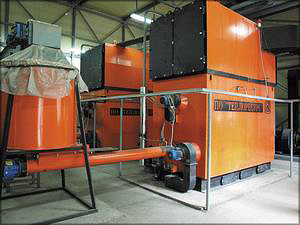
Энергетическая установка – утилизатор древесных отходов
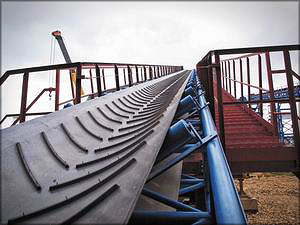
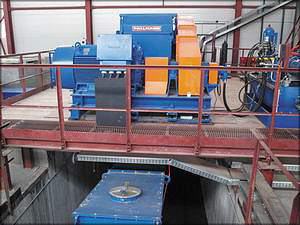
Новый участок подготовки щепы
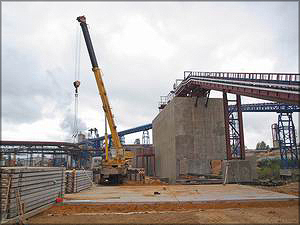
Строительство нового производства плит
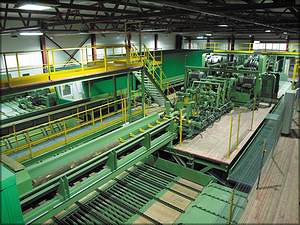
В прошлом году рядом с комплексом сушильных камер была построена новая котельная. В отдельном помещении располагаются насосная станция и два котла (производитель - компания «Теплоресурс»), работающие на древесных отходах: кусковые отходы из цехов и стружка из системы аспирации поступают в большой бункер хранения, далее с помощью подвижных полов в промежуточные бункеры, откуда шнеками подаются в топки котлов. Оборудование полностью автоматическое, обслуживается одним оператором, выполняющим скорее надзорные функции.
Сушильное хозяйство было организовано в 2009 году, однако не так давно пришлось его серьезно реконструировать. Дело в том, что в проекте изначально были допущены технические ошибки: обогрев осуществлялся паром, скапливающийся конденсат гидроударами выводил установки из строя. После четырехлетнего простоя сушилок полностью заменена вся оснастка - и весной 2015 года модернизированные камеры были введены в эксплуатацию одновременно с пуском новой котельной.
Тепло, вырабатываемое котельной, полностью обеспечивает потребности сушильных установок, со временем планируется обогревать им несколько цехов, а потенциал, заложенный в оборудовании, позволяет планировать еще более существенное расширение теплоснабжения производства в будущем.
Производство плит
Один из наиболее амбициозных проектов «Плитспичпрома» - техническое перевооружение производства плит. Первым его этапом стал ввод в строй участка подготовки щепы с установкой новых станков Pallmann, на эту же площадку постепенно будут переводиться и рубительные машины, ранее задействованные в производственном процессе.
Рассказывает генеральный директор «Плитспичпрома» Евгений Власов: «Проект по переоснащению производства ДСП мы изначально разделили на несколько этапов: сначала первый пусковой комплекс нового завода ДСП, в рамках этого этапа создана новая биржа сырья (на месте старой будет стоять главный производственный комплекс с основным конвейером ДСП), участок подготовки сырья и передача полученной щепы в технологию. Готов бункер для щепы, установлена новая рубительная машина, построены транспортеры для подачи щепы в цех, два стола подачи, раскатной стол, на который подается древесина. Раньше у нас были в разных местах два рубительных участка, отдельно для производств ДСП и ДВП, сейчас они объединяются в один, где будет подготавливаться сырье на два потока: сначала на новую площадку переводим поток ДСП, затем и ДВП. Следом на высвобожденных площадях начнется строительство главного производственного корпуса.
Первые наши ДСП были выпущены в 1993 году. Продолжаем выпуск влагостойких и огнестойких плит, начатый в 2006 году.
Структура плитного производства включает цех древесных плит, который состоит из линий ДВП и ДСП, в составе каждой из них целая цепь технологических участков: подготовки стружки, размалывания, клееприготовления, осмоления, формирования ковра, прессования, - и участок подготовки и хранения щепы.
Оборудование: каландровый пресс «Аума 40», пресс ДСП, произведенный на одном из предприятий Днепропетровска. Часть оборудования уже довольно возрастное, но оснащение всех участков постепенно обновляется, приобретается современная техника, например, стружечные станки, система сухого осмоления IMAL, которая позволяет оптимизировать процесс изготовления ДВП сухим способом, и плиты получаются более плотные, чем ранее, качество их поверхности выше.
Недавний ввод в эксплуатацию участка подготовки щепы - это большой, но только первый шаг в создании нового плитного производства. В действующем цехе установлен довольно старый пресс, из-за чего выпускаемые плиты отличаются разнотолщинностью, приходится их шлифовать, причем зачастую необходимо сошлифовывать до 10% толщины! Новые прессы непрерывного действия (Siempelkamp, Dieffenbacher) позволяют выпускать плиту с допуском 0,5 мм (1-3% конечной толщины плиты), то есть уже на этом этапе достигается существенная экономия материалов. А если учесть, что новое оборудование позволит добиться высоких показателей энергоэффективности и производительности, даст возможность выпускать продукцию высокого качества, то необходимость обновления оборудования становится очевидной. Только при совершенствовании технологий и внедрении инноваций можно выжить в условиях современного рынка с его высокой конкуренцией.
Сейчас мы изготавливаем плотную (650-700 кг/м3) плиту, она востребована именно из-за своей высокой плотности. Возможности нового оборудования позволяют выпускать более легкую плиту: уменьшается расход смол и древесины, а значит, снижается себестоимость продукции, - но при этом прочность и другие эксплуатационные качества плиты не ухудшаются, благодаря особенностям технологии изготовления.
Надо отметить, что в текущей экономической ситуации строить завод мощностью 150 тыс. м3 плит в год, что называется, с нуля и в чистом поле - совершенно нерентабельно. Для того чтобы обеспечить мало-мальскую эффективность, нужно выпускать не меньше 250 тыс. м3. А мы можем себе позволить и запускаемся на 150 тысяч, не боясь оказаться в проигрыше, потому что в рамках ПГ «Союз» есть отлаженная структура взаимосвязанных производств под общим управлением. Мы хорошо понимаем сбыт, логистику, всю дальнейшую судьбу этого продукта в рамках ПГ. Самое главное, что к моменту, когда в результате кризиса произойдет перераспределение рынка и начнется неизбежный рост цен на плитную продукцию, у нас будет отлаженное современное производство качественных ДСП, а тот, у кого его нет, будет вынужден покупать их на рынке по возросшей цене. Таким образом, мы получаем независимость по сырью и, помимо всего прочего, подстраховываем себя, предприятия группы компаний от скачков цены и "игр" на рынке, которые ожидаются в будущем».
Лесопильно-деревообрабатывающий комплекс
Наконец перед нами главная цель нашего путешествия по новым производственным площадкам «Плитспичпрома» - мощный комплекс лесопиления, где только что завершились последние испытания оборудования.
На подходе к зданию лесопильного цеха построен новый большой склад для готовой продукции, с которого и будут осуществляться отгрузки погонажа; рядом располагается цех поддонов - реконструированное здание, свежеокрашенное в корпоративные цвета «Плитспичпрома». Эти три структурные единицы и составляют лесопильно-деревообрабатывающий комплекс завода (в дальнейшем в него войдут цех клееных изделий, цех домостроения, сушильное хозяйство для пиломатериалов и котельная).
В ходе реновации старых зданий спичечной фабрики восстанавливать приходилось не только цеховые корпуса и помещения - главные проблемы заключались в обновлении и замене сетей и коммуникаций, проложенных еще в 50-70-е годы ХХ века. По словам Евгения Власова, объем кабелей, труб и прочего - огромный, характеризуется высоким износом.
Генеральным поставщиком оборудования для нового лесопильного комплекса АО «Плитспичпром», согласно контракту, заключенному в июне 2014 года, выступила известная германская компания EWD. Результатом годичной подготовительной работы, поставки и монтажа станков (который начался в феврале 2015 года) стало создание одного из самых крупных и, пожалуй, наиболее современных лесопильных производств в Центральной России.
Лесопильный цех подразделяется на несколько производственных участков: участок приемки и сортировки круглого леса; склады сортированного круглого леса; окорочно-распиловочный (основной производственный) участок; участок сортировки сырых и сухих пиломатериалов (комбисортировка) и пр. Круглый лес к цеху можно доставлять как автотранспортом, так и по собственной железнодорожной ветке.
«Прежде чем начать проект, мы вышли на руководство области, обсуждали и согласовывали его с губернатором. Заручились поддержкой на всех этапах реализации проекта, но главное - получили в аренду лес, - говорит генеральный директор компании. - Только понимая, как в ближайшей и долгосрочной перспективе будет решаться проблема поставок сырья, можно решиться на пуск такого производства с вертикальной интеграцией в другие проекты ПГ «Союз». Мы получили достаточную расчетную лесосеку, для того чтобы будущий комплекс не простаивал. В июне прошлого года подготовили расчеты и планы, заключили договор на поставку станков, для изучения технологии объездили много заводов в России и за рубежом. Искали наиболее высокотехнологичные и эффективные варианты производственных линий. В итоге остановились на фрезерно-брусующей и кромкообрезной технологиях: для обеспечения максимального выхода с каждого бревна необходимо включать в цепочку кромкообрезку, чтобы боковые доски не рубить в щепу, а получать из них пиломатериалы. А собственное производство ДСП/ДВП позволяет нам использовать все отходы, образующиеся в процессе лесопиления».
С этими словами директор открыл дверь и проводил меня в цех. Благодаря помощи специалистов EWD, предоставивших детальную информацию обо всем технологическом процессе, и у читателей «ЛПИ» есть возможность совершить небольшую заочную экскурсию по новому цеху.
Линия сортировки бревен
Поступившее на предприятие древесное сырье попадает на линию сортировки бревен Holtec, на 20 сортировочных карманов для измерения геометрических параметров и сортировки по группам диаметра с целью первичной приемки и оптимизации процесса распиловки. Именно сортировка бревен в дальнейшем определяет технологические режимы процесса распиловки на линии лесопиления.
Подача сырья ведется мобильными погрузчиками на поперечный цепной транспортер-накопитель, по которому бревна поступают на ступенчатый разобщитель, где разделяются поштучно. Далее они поштучно передаются на бревнотаску и перемещаются в зону с металлоискателем (здесь в сырье выявляются металлические включения). Древесные отходы (кора, щепа), которые образуются при перемещении бревен, удаляются в бункер по системе специальных транспортеров. После металлоискателя бревно передается на сортировочный цепной транспортер, оснащенный десятью двухсторонними выталкивателями бревен, и проходит через трехмерный сканер для измерения полного контура. Сортировка бревен может осуществляться как по отдельным параметрам, так и по группе параметров. Каждому параметру (группе параметров) присваивается свой сортировочный карман.
Линия распиловки бревен
На участке подачи бревен выполняются: поштучная выдача бревен, их правильное позиционирование по направлению подачи, окорка станком Valon Kone и передача на линию распиловки производства EWD. По цепному поперечному транспортеру-накопителю сырье транспортируется в зону разделения, где бревна разделяются поштучно при помощи ступенчатого разобщителя и передаются на бревнотаску, по которой перемещаются в зону с установленным двухмерным сканером, с помощью которого определяется положение вершины и комля бревна по отношению к направлению подачи. При необходимости бревно разворачивается в разворотном устройстве на 180º, комлевой частью вперед, и поступает на окорочный станок, оттуда по продольному транспортеру при помощи выталкивателя - на поперечный транспортер, выполняющий функцию буфера-накопителя. При помощи ступенчатого разобщителя бревна выдаются на участок распиловки, где расположена фрезерно-круглопильная линия EWD.
Двигаясь по продольному цепному транспортеру, бревно проходит через устройство трехмерного сканирования (посредством лазерной триангуляции сканирование осуществляется вдоль его контура, что позволяет определить все неровности ствола) и поступает на центрирующий стол подачи, где автоматически ориентируется точно вдоль оси для обеспечения максимального выхода.
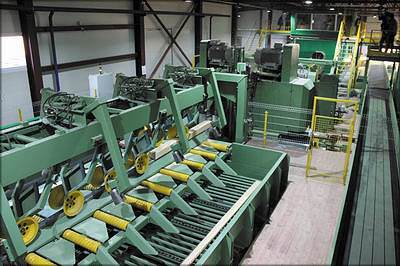
Бревно поступает на фрезерно-брусующий станок, оснащенный двумя фрезерными дисками с прямым расположением ножей. Фрезерный агрегат осуществляет двухполосную редукцию круглых лесоматериалов и двухкантных брусьев с целью получения двух- или четырехкантного бруса; горбыльная часть измельчается с помощью фрез в высококачественную технологическую щепу.
Полученный на фрезерном агрегате двухкантный брус с помощью прижимных роликов подается на двухвальный круглопильный станок, где отпиливаются боковые доски либо выполняется распиловка бруса на обрезные и необрезные пиломатериалы. После выхода из круглопильного станка брус транспортером направляется по системе возврата к началу линии распиловки.
Работа линии построена на технологии распиловки с возвратом: за первый проход выполняется фрезерование горбыля и отпиливание боковых необрезных досок, за второй - фрезерование горбыля и распиловка бруса на обрезные и необрезные пиломатериалы. Бревна большого диаметра распиливаются за три прохода и более, число проходов зависит от карт раскроя.
Полученные после первого прохода боковые необрезные доски уходят на линию кромкообрезки. Они отделяются от двухкантного бруса и удаляются посредством доскоотделителя с винтовыми роликами и доскоотделителя с коническими роликами. Необрезные доски по системе поперечных и продольных транспортеров попадают на поперечный транспортер-накопитель участка кромкообрезной линии Optimes. С транспортера-накопителя необрезные доски подаются на транспортер-разобщитель (состоит из разобщителя и поперечного транспортера).
Пиломатериалы захватываются траверсами, разобщаются на наклонной плоскости транспортера и поступают на другой транспортер-разобщитель, который обеспечивает увеличение расстояния между подаваемыми пиломатериалами. Стоп-захваты для определения центра тяжести обеспечивают постоянный и плотный поток пиломатериалов даже при большой скорости подачи. Зубчатая опорная поверхность и автоматически опускающиеся захваты препятствуют наскакиванию досок друг на друга. Фотодатчики определяют момент подачи очередной доски, как только предыдущая проходит захваты. Оператор может оценить качество доски, задержанной у первых захватов. Бракованный пиломатериал можно сбросить через сортировочный затвор. Далее доски проходят через поперечный транспортер, где выравниваются по упору (при необходимости в случае наличия горбыльной части доски торцуются торцовочной пилой) и передаются на автоматический стол подачи, где, в зависимости от кривизны, выполняется их оптимальное позиционирование для дальнейшей кромкообрезки. Затем необрезная доска проходит через четыреxкамерную систему сканирования, в которой по мере продвижения вперед выполняется ее измерение, считываются все неровности контура доски и тем самым точно определяются ширина, длина и расположение обзола (процесс измерения сопровождается постоянным обдувом сканеров, что обеспечивает их защиту от древесной пыли). По измеряющему транспортеру доска продвигается к круглопильному станку. Тем временем данные измерения обрабатываются компьютерной системой кромкообрезного станка и выполняется автоматическое позиционирование режущего инструмента круглопильного станка.
На обрезном круглопильном станке по результатам сканирования обрезаются кромки вдоль линий раскроя (либо выполняется раскрой боковых досок на узкие доски). Устройство смывания смолы смачивает зону реза, тем самым подавляя образование пыли и улучшая скольжение режущего инструмента по древесине.
После кромкообрезного круглопильного станка пиломатериал поступает на рейкоотделитель, состоящий из винтовых роликов и разделительных ножей: обрезной пиломатериал транспортируется по винтовым роликам, в то время как обзольные рейки отделяются разделительными ножами и удаляются. Ленточными транспортерами доски подаются на систему сортировки.
Комбинированная линия сортировки пиломатериалов
На линии сортировки сырые и сухие обрезные пиломатериалы сортируются по геометрическим параметрам (сечению, длине) и качеству. По мере накопления боковые и центральные доски поперечными транспортерами поочередно выдаются через поперечный подъемный транспортер на цепной транспортер-разобщитель, далее поступают на выравнивающий рольганг, где выравниваются по торцу. Далее доски поступают на участок, на котором при помощи дозатора и плунжерного устройства производительностью до 60 тактов в минуту выполняется их поштучная выдача на участок оценки качества.
После оценки качества материала доски передаются на цепной транспортер со встроенной дисковой пилой, которая торцует доски в размер, заданный оператором (обрезки досок падают на ленточный транспортер и удаляются). Далее доски перемещаются на ременный транспортер, а после измерения геометрии поступают на сортировочный транспортер и перемещаются в сортировочные карманы.
Критерии сортировки досок заносятся в программу управления линией. Каждому критерию (группе критериев) присваивается конкретный карман или группа карманов. Количество досок для формирования пакета пиломатериала (количество досок в заполненном кармане) зависит от сечения досок.
Информация о заполнении карманов поступает в систему управления линией. Карманы выгружаются по команде оператора участка пакетирования пиломатериала. Из сортировочного кармана пиломатериалы выгружаются на поперечный транспортер, по которому передаются на цепной транспортер-разобщитель.
После разобщения доски выравниваются по торцу на выравнивающем рольганге и поступают на участок непрерывной поштучной подачи, которая выполняется при помощи дозатора. Разобщенные доски перемещаются далее по цепному транспортеру, в который встроен рольганг для выравнивания торцов досок разной длины по разным сторонам пакета. Затем доски перемещаются передаточным транспортером на участок с автоматической круглопильной установкой, где при необходимости могут раскраиваться в одинаковый размер по длине. Далее выполняется автоматическое пакетирование пиломатериала на штабелеформирующей машине.
Ширина пакетов пиломатериала - от 1200 до 1500 мм, длина - от 2000 до 6000 мм. Максимальная высота пакетов - 1500 мм. При формировании пакетов пиломатериала для сушки укладка межрядовых прокладок выполняется при помощи устройства автоматической укладки, оснащенного двенадцатью магазинами для реек.
Сформированные пакеты по цепному поперечному транспортеру передаются на рольганг, по которому перемещаются за пределы цеха, и далее при помощи вилочного погрузчика транспортируются на промежуточный склад.
Для сортировки сухого пиломатериала пакеты загружаются на цепной поперечный транспортер. Далее при помощи устройства для расформирования пакетов выполняется разобщение рядов пиломатериала и отделение межрядовых прокладок. Разобщенные ряды пиломатериала поступают на цепной транспортер-накопитель и далее на участок поштучного разобщения досок. Разобщенный сухой пиломатериал сортируется в соответствии с заданными критериями. Сформированные пакеты сухого пиломатериала могут быть обвязаны при помощи устройства обвязки пакетов.
Участок удаления отходов
Удаление отходов на всех операциях линии лесопиления осуществляется при помощи системы транспортеров, оборудования для измельчения кусковых отходов и разделения измельченной фракции.
Отходы и кора из-под поперечного транспортера-накопителя на участке подачи сырья удаляются цепными скребковыми транспортерами, подаются в измельчитель и далее в измельченном состоянии по транспортеру перемещаются в приемный бункер либо контейнер.
Кусковые отходы пиломатериала, образующиеся на линии сортировки, а также кусковые отходы с участка кромкообрезки подаются по ленточным транспортерам на вибротранспортер, по которому отправляются в рубительную машину Bruks барабанного типа, измельчаются и ссыпаются на продольный скребковый транспортер. Для предотвращения попадания металлических частиц в рубительную установку после вибротранспортера установлен металлоискатель.
Отходы с линии пиления по системе транспортеров поступают на осциллирующее сито, где происходит разделение щепы, опилок и крупной фракции, размеры которой превосходят размеры щепы. Щепа и опилки транспортируются в отдельные бункеры, крупная фракция по ленточному транспортеру возвращается на вибротранспортер и повторно измельчается в рубительной машине. Система удаления отходов работает в автоматическом режиме и не требует вмешательства оператора.
***
«Вопросам безопасности уделено самое пристальное внимание, везде установлена защитная автоматика, - поясняет на выходе из цеха Евгений Власов. - На производственных участках установлены ограждения, на входных дверях - электронные замки, при любом несанкционированном их открытии автоматика срабатывает, и все оборудование останавливается.
На нижнем уровне цеха, отведенном под сбор отходов со всех участков и измельчения их в щепу, люди работать не будут - станки полностью автоматизированы, транспортером подаются отходы, рубятся в щепу и укладываются в карманы для щепы.
Для утилизации коры мы заказали котлы Polytechnik. Долго проводили тендер, изучали модели разных производителей и выяснили, что работать на коре с соблюдением необходимых для нас параметров могут именно котлы Polytechnik. Сжигая кору, будем получать тепло для сушильных камер: нынешнее сушильное хозяйство может обеспечить потребности построенного комплекса на 30-50%, значит, для обеспечения полной загрузки линии мы будем его наращивать. Уже заключен договор на поставку и новых сушильных камер Katres. Они будут установлены прямо около цеха, транспортером кору будем подавать на подвижные полы в котельную. Таким образом, мы будем максимально экономично и эффективно, с минимальными трудозатратами качественно сушить произведенные пиломатериалы. Безусловно, все эти меры скажутся на себестоимости продукции и экономике предприятия в целом. Собираемся к следующему сезону оборудование смонтировать и запустить».
Кофе-брейк с производственным уклоном
С новенького, с иголочки, корпуса, где располагаются сбытовые службы, мы начали обход заводской территории и снова вернулись сюда, чтобы за чашкой кофе в спокойной обстановке продолжить беседу.
- Наш новый офис продаж открылся совсем недавно, в начале 2015 года. Причем отделов продаж здесь несколько. Разделение сделано сознательно - как по направлениям нашей деятельности (отдельно продаются двери, древесные плиты, дома из клееного бруса, погонаж и пиломатериалы), так и по подходам к реализации продукции: одни менеджеры работают с сетями DIY, другие - с частными клиентами, физлицами, третьи - с сегментом B2B, четвертые закреплены за крупнейшими дилерами и торговыми партнерами.
Отдельно расположены здания заводоуправления и технической библиотеки, где аккумулированы все знания, накопленные специалистами за много лет работы предприятия. Нередко приходится проводить там время, и помногу. То опыт прошлых лет изучаю, то разбираюсь в технических моментах. Нужно постоянно быть, что называется, в теме.
- После такой впечатляющей демонстрации технического переоснащения предприятия не могу не спросить вот о чем. Уже по названиям станков видно, какие средства вы в них вложили, ведь вы используете в работе технику производителей, которых заслуженно считают лидерами в своих сегментах ЛПК. Какими критериями вы руководствовались при выборе поставщиков оборудования для новых производственных линий?
- Оборудование дорогостоящее, конечно. Однако экономить на оборудовании себе дороже. Можно купить китайское, и потом с ним мучиться, но лучше работать с проверенным и ответственным поставщиком и покупать такую технику, в надежности и эффективности которой можешь быть уверен на все 100 процентов: если правильно установил, она будет работать без сбоев.
Прежде чем что-либо приобрести, заключить контракт на поставку, мы проводим очень большую подготовительную работу, которая иногда занимает больше времени, чем собственно поставка и монтаж. При выборе учитываем много разных факторов. Например, очень внимательно изучаем так называемый референс-лист: он отражает опыт поставщика оборудования, глубину знания технологий (взять хотя бы «Weinig-концепт» - его суть в том, что компания поставляет не просто станок, а технологию производства целиком). Очень важно обеспечение первоначального инжиниринга (проработка техдокументации, инженерных и технических решений). Конечно, играют свою роль и цена, условия поставки, оплаты, отсрочки и т. д. Ну и, конечно, мы стараемся сотрудничать с передовыми компаниями-производителями.
- Всегда ли приобретенные станки оправдывают возложенные на них ожидания?
- Что касается дверного производства, трудно было сделать ошибку: мы хорошо знали, как и что в этой сфере делается, ведь наша линия является аналогом производства другого предприятии промышленной группы, - «Лесплитинвест», но усовершенствована и осовременена немецкими и итальянскими технологами. По лесопильному оборудованию выбор был, можно сказать, идеологическим: в Европе наиболее распространены скандинавская и немецкая технологии. Первая ориентирована на работу с качественным ровным сортовым лесом и характеризуется высокой скоростью обработки, вторая дает возможность получать максимальный выход при обработке даже не самой качественной древесины - менее плотной, меньшего диаметра, большей кривизны. Это как раз наш случай, подходящий для средней полосы России, поэтому мы ставим у себя немецкие станки. Они отлично обеспечивают текущие потребности предприятия, дают запас мощности для роста: так, лесопильная линия перерабатывает 120 тыс. м3 в год круглого леса, но может и 150 при двухсменной работе (то есть 300 в круглосуточном режиме).
Что касается рабочих режимов загрузки техники, то мы стараемся работать таким образом, чтобы не хранить у себя большие объемы готовой продукции, и действуем по принципу just in time, то есть точно в срок, ориентируясь на текущие и перспективные заказы клиентов. Именно так организовано дверное производство: на складе есть сток, страховой запас, который обеспечивает наполнение рынка наиболее востребованными моделями и видами продукции.
Бизнес в кризис
- В статье, написанной моими коллегами по итогам предыдущего визита к вам, приводились слова тогдашнего руководства предприятия: «...потребность в спичках всегда была, есть и будет». Так понимаю, подразумевалось, что на «Плитспичпроме» производство спичек есть и будет всегда. Но очень скоро технологические линии были свернуты, и знаменитых балабановских спичек не стало... Почему так произошло, и кто же теперь обеспечивает страну спичками?
- Сейчас на производственных площадях бывшего спичечного цеха установлено оборудование для производства межкомнатных дверей. Основная причина смены направления деятельности - нехватка подходящего сырья и его невысокое качество: местная осина дуплистая, и при лущении древесина трескается, слишком много отходов. Себестоимость продукции постепенно выросла до такого уровня, что выпускать ее стало попросту невыгодно, и было принято стратегическое решение о прекращении производства спичек.
Никакой трагедии не произошло. Продолжает выпуск спичек целый ряд российских фирм, в том числе ГК «Объединенная спичечная компания». Мы часть своего оборудования продали им, другую - за рубеж...
- Раз уж мы заговорили о сырье, расскажите, заготовку древесины вы тоже ведете сами?
- Лесные участки арендуем в Калужской области. Расчетная лесосека - более 400 тыс. м3. Наш департамент лесного хозяйства (в разных вариантах - и по договорам подряда, и собственными силами) осуществляет заготовку древесины и поставку ее на предприятие.
- Какие заготовительные машинные комплексы используете?
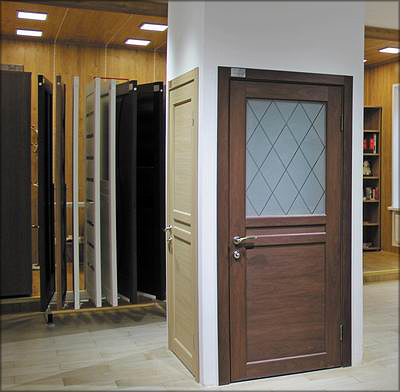
Межкомнатные двери Alleanza doors (готовая продукция)
- Для заготовки в нашей местности, в наших лесах и с учетом объемов локализованной заготовки крупные машинные комплексы (харвестеры, форвардеры) неэффективны. Поэтому наши машинные комплексы Logset мы передали подрядчикам. Широкого распространения эта техника здесь не получила.
- Евгений Гаврилович, признайтесь: приходится ли делать какие-то «поправки на кризис» при реализации намеченной стратегии, в процессе развития проектов? Ведь вы начинали еще в то время, когда ничто не предвещало беды...
- Кризис, конечно, оказывает влияние на нашу деятельность, но не на стратегию развития, а скорее на тактику в достижении поставленных целей. Перераспределяем средства, корректируем планы, но таким образом, чтобы в новых экономических реалиях все же выполнить всё намеченное.
У нас хороший запас прочности благодаря тому, что предприятия группы «Союз» работают в одной цепочке. Но я вижу, насколько непростая ситуация в экономике. Многие предприятия останавливаются, кто-то даже разоряется. Мы с коллегами посещали несколько в Архангельской, Тульской областях - стоят цеха с новеньким, с иголочки, оборудованием. Только успели начать работу, грянул кризис, и все - продаются...
И вот если раньше мы даже не обсуждали возможность приобретения оборудования б/у, то сейчас предложения такого рода невольно обращают на себя внимание и заставляют задуматься о разумной альтернативе закупкам дорогостоящих новых станков из Европы. Если оборудование рассчитано на длительные сроки эксплуатации, а ресурс его не выработан, почему бы нет?
- Какова нынешняя численность персонала предприятия?
- Когда мы начинали перепрофилирование спичечного производства, на «Плитспичпроме» работало около 1200 человек. Сейчас по штатному расписанию - 900 работников. Реализация новых проектов позволит вновь увеличить штат до 1200, но товарной продукции эти люди будут выпускать раза в полтора больше, чем прежде, за счет автоматизации производства, оснащения более эффективным оборудованием. Повышается производительность труда - соответственно, повышается рентабельность производства.
Примерно половина сотрудников проживают в Балабаново. Остальных специальный автобус развозки доставляет из ближайшей округи - Боровска, Обнинска, Ермолино. Многие работники бывшего спичечного цеха трудятся на предприятии в других подразделениях. Несмотря на смену направления, остались на «Плитспичпроме» технологи - а ведь найти хорошего технолога в области деревообработки ох как непросто! Если те, кто раньше работал здесь и ушел, сейчас решил вернуться, - с радостью берем опытных специалистов обратно. И они, знающие всю структуру предприятия, дополняют коллектив новых сотрудников, которых обучаем работе на новом высокотехнологичном оборудовании. В этом нам помогают представители компаний-поставщиков, они приезжают и проводят необходимое обучение.
- В советские времена «Плитспичпром» носил гордое звание градообразующего предприятия. Можно ли сейчас называть его так, и каковы ваши взаимоотношения с городом Балабаново?
- Каких-то плюсов для предприятия подобный статус не дает. Но это часть нашей истории и отчасти сегодняшнего дня. Звучит, действительно, красиво... Но на деле это своего рода обременение: волей-неволей такие предприятия берут на себя все проблемы города, который когда-то образовали. Так, сегодня мы занимаемся очисткой сточных вод для всего Балабаново (как промпредприятий, так и жилых кварталов), 40% отопления городских зданий тоже обеспечиваем мы. Согласно принятой стратегии компании, мы будем постепенно уходить от таких непрофильных активов и заниматься строго своим профилем деятельности: если взялись за деревопереработку, то именно ее и будем развивать. А «коммуналкой» должны заниматься специальные службы. Мы общались на эту тему с руководством города и даже региона, достигли взаимопонимания - ведь все согласны с тем, что каждый должен заниматься своим делом, только тогда оно будет эффективным. В конце концов, поставить в городе современные модульные котельные экономичнее и выгоднее, чем загружать котельную предприятия. Город при поддержке правительства области уже делает первые шаги в этом направлении.
- Пару слов о реализации продукции: вы делаете ставку на продажи внутри страны, или у компании, как это зачастую бывает, серьезные планы по экспорту?
- При нынешних курсах валют экспорт, конечно, более чем актуален. Мы только начинаем работать за рубежом, идут точечные поставки - в Болгарию, Индию. Просчитываем, анализируем рынки. Например, в страны Западной Европы выгодно продавать пиломатериалы, а вот плиты - совершенно неинтересно.
- А много ли сейчас контрактов с бывшими республиками Советского Союза? Например, азиатскими. Собственная древесина там в дефиците, в последние годы это уверенно растущий рынок сбыта российской продукции...
- Наибольшее число экспортных поставок идет именно в страны СНГ, в том числе в Узбекистан, Таджикистан. Правду сказать, сейчас объемы несколько меньше, чем раньше, ввиду непростой экономической ситуации в этих странах. Белоруссия, Украина также покупают нашу продукцию.
Перспективы следующих побед
Как уже упоминалось, вниманием властей предприятие обласкано: губернатор области Анатолий Артамонов присутствовал на всех пусках новых цехов и линий. Значимость предприятия для региона несомненна. Какую же поддержку получает бизнес от государства?
Как рассказал руководитель «Плитспичпрома», «проекты компании вошли в реестр приоритетных инвестпроектов Калужской области, в минпромторговский список предприятий, оказывающих существенное влияние на отрасль промышленности РФ, в перечень градообразующих и стратегических предприятий Калужского региона и включены в перечень комплексных инвестпроектов по приоритетным направлениям гражданской промышленности Минпромторга. Каждое такое «включение» - не просто строка в списке, это реальные преференции и какие-то новые возможности: Калужская область обнуляет налог на имущество на вновь вводимые здания, снижает долю налога на прибыль в областной бюджет, Минпромторг дает возможность на федеральном уровне получать государственные субсидии.
Зачастую господдержка перерастает в своеобразный PR власти. Вроде бы тебе хотят помочь, а потом такое стремление превращается в навязывание своих условий с требованиями последующих помпезных отчетов об этой самой помощи, чтобы тот или иной чиновник мог в выгодном свете представить свою работу «вышестоящим инстанциям». В этом плане калужский губернатор - замечательное исключение из правил: Анатолий Дмитриевич последовательно привлекает в регион крупный бизнес и эффективно поддерживает его. А ведь именно крупный бизнес способен обеспечивать экономическое развитие региона, именно на его основе, рядом с ним начинают жить и работать сопутствующие бизнесы - малый и средний. На момент прихода Артамонова область была дотационной, а сейчас уже стала своеобразным донором российской экономики, это безусловная заслуга губернатора. Появились целые кластеры новых заводов: Samsung, Volvo и пр. В нашей отрасли считаю самым важным, что он уберег леса, не раздал налево-направо всем, кто просил, суля невнятные перспективы, - арендные участки здесь выдаются только под серьезные, обоснованные инвестиционные проекты».
- Насколько мне известно, у вас были планы организации производства в особой экономической зоне «Людиново».
- Сейчас эта концепция находится в разработке. Есть несколько вариантов по производству различных видов продукции на площадке в Людиново. Чтобы не получилось как со спичками, мы хотим досконально просчитать и подготовить проект: что именно можно там выпускать из леса, растущего на арендных участках в Калужской области, сколько древесины посильно переработать, какие технологии задействовать. Ведем переговоры с инжиниринговой компанией, которая могла бы помочь с детальной проработкой всех вопросов. Скорее всего, это будет плитное производство.
- Если не секрет, скажите, нет ли планов по ребрендингу компании? «Плитспичпром» - звучит странновато, если «спич»ки здесь больше выпускать не будут.
- Мысли на эту тему были, но не планы. Для того чтобы провести неизбежно сопровождающую подобный шаг широкомасштабную рекламную кампанию, представить новый бренд рынку, требуются огромные вложения. А насколько они оправданны? Эффект, возможно, и будет, но процесс этот долгий, непростой и, поверьте, очень-очень дорогой. Кроме всего прочего, наше название за много лет стало узнаваемым безотносительно его смысловых частей. Вопрос решается и с помощью введения отдельных брендов для разных видов нашей продукции.
- Если можно, дайте оценку перспективам предприятия в связи с реализацией выбранной вами стратегии и, может быть, российского ЛПК в целом.
- Что ж, тогда давайте пойдем от общего к частному. Я считаю, что лесопереработка сегодня недооценена. В части возможностей зарабатывать, возможностей приложения усилий. Их не в полной мере реализуют и бизнес, и власть. Лес - возобновляемый ресурс, крупные предприятия обеспечивают баланс воспроизводства лесов. Прошли те времена, когда недальновидно считалось, что лес нельзя трогать и, если его будут рубить, скоро от него ничего не останется. Нет, ЛПК может не только обеспечивать народное хозяйство ценнейшими продуктами, но и успешно осуществлять воспроизводство, обновление лесов.
А предприятие, как уже упоминалось, вскоре ждет качественный скачок на «расчищенном» кризисом рынке. Сейчас происходит некий отсев: те, кто не может или не хочет перестраиваться с учетом новых экономических условий, постепенно уходят с рынка, а те, кто вложился в современное высокотехнологичное оборудование, эффективное и производительное, заберут себе доли ушедших игроков.
Вообще, делать прогнозы - дело неблагодарное, в нашей стране особенно. Хочется надеяться, что вскоре политика перестанет давить на экономику, игры в санкции закончатся и бизнес получит условия для нормального, полноценного развития. Предполагаю, что некое движение вверх начнется уже в 2016 году, но оно не будет таким резким, каким был спад, - начнется восстановление экономики и постепенный стабильный рост. Вообще, кризис - это когда все случается внезапно, люди не могут подготовиться, а если (при разумном ведении дел) есть возможность адекватно оценить ситуацию, подстраховаться, создать какие-то запасы, перераспределить силы и средства, то никакого кризиса и нет. Не возьмусь утверждать за всю страну, но у нас на предприятии кризиса нет, мы работаем, развиваемся, двигаемся в правильном направлении. Запас прочности у нас достаточный, заказы расписаны на полгода вперед, мощности загружены. Все это дает нам возможность смотреть в завтрашний день совершенно спокойно.
- В заключение позволю себе вопрос «не для протокола». Как вы оцениваете собственные перспективы в русле развития возглавляемого предприятия?
- Вы уже, вероятно, поняли, что непростые экономические ситуации я расцениваю как вызов, в том числе и для себя лично. Это проба сил, проверка на прочность, а также и самое интересное время, которое можно будет потом вспоминать. Родился я на Северном Урале, где заготовка и переработка древесины являются одним из основных видов экономической деятельности. Высшее техническое и экономическое образование получил в Уральском государственном университете, затем окончил Российский экономический университет им. Плеханова, получил дополнительное образование в области менеджмента и маркетинга. Параллельно с учебой много и, как утверждали мои работодатели, эффективно работал в качестве руководителя на всех уровнях управления предприятиями. У меня есть серьезный опыт руководства предприятиями, в том числе их вывода из кризисных ситуаций.
Сейчас «Плитспичпром» - это в полном смысле моя жизнь. Проблемы и успехи предприятия я воспринимаю как собственные. По-другому, видимо, просто не умею.
* * *
На этом мы по обоюдному согласию с Евгением Гавриловичем решили поставить точку. Или все же многоточие? Ведь мы посетили не все цеха и технологические участки предприятия - просто невозможно с должным вниманием осмотреть их за один день. А ведь совсем скоро будет реализован проект по плитному производству - чем не повод приехать на «Плитспичпром» снова?
Подготовил Максим ПИРУС