«Первая фабрика фасадов». В центре Евразии
Расположенная в крупнейшем индустриальном, административном, культурном и научно-образовательном центре Уральского региона - г. Екатеринбурге, «Первая фабрика фасадов» из небольшого семейного производства за десять лет существования превратилась в надежного поставщика мебельных фасадов, география поставок которого - Уральский, Сибирский, Дальневосточный федеральные округа и другие регионы России.
О становлении компании рассказывает ее владелец и генеральный директор Антон Осинцев:
«"Первая фабрика фасадов" - это семейный бизнес. Начиналось все с фирмы "Купе-Дизайн", созданной отцом, в ее штате было не больше десяти человек. Освоив производство шкафов-купе, отец захотел развивать бизнес, осваивать новую продукцию. Имея за плечами шестилетний производственный опыт и понимая нужды и запросы производителя мебели, он принял решение работать непосредственно с производителями. В 2005 году было организовано производство фасадов. На тот момент у компании были один небольшой пресс, маленький фрезер и десяток сотрудников. Я тогда еще был наемным работником, занимался снабжением, поскольку в то время качественная пленка, которая сейчас широко применяется при производстве фасадов, была редким продуктом, и приходилось раз в неделю ездить за ней в Челябинск. Постепенно вникал в дела, осваивал производство до мельчайших деталей. В 2009 году отец ушел на пенсию, и мы с женой взяли на себя руководство этим небольшим, но перспективным предприятием. С того момента начался новый этап развития компании - строительство новой фабрики».
Антон Осинцев буквально «болеет» своим производством, вникает во все детали, под его контролем все - начиная с производства и заканчивая сертификацией и выбором поставщиков. Антон, как никто другой, знает весь производственный процесс изготовления фасадов, может встать за любой станок и подключиться к процессу на любом этапе. Подбором станков он занимается сам - ездит по европейским фабрикам, изучает опыт других компаний, что-то берет на заметку и воплощает на собственном производстве. Так, переломным моментом в истории фабрики стал переход от классической схемы производства фасадов к производству по технологии «нестинг» - тогда еще неизвестной и непонятной, да и сейчас еще не очень распространенной в России. Эта технология подразумевает, что плита MDF не форматируется, а целый лист укладывается на рабочий стол обрабатывающего центра и на выходе получается готовый фасад, полностью отфрезерованный, остается только его отшлифовать, нанести клей и пленку. Уход от классической схемы производства к технологии нестинга был очень серьезным шагом для «Первой фабрики фасадов», и именно он, как считает Антон Осинцев, позволил компании войти в число лидеров. Около четырех лет назад на производстве появился первый нестинговый станок марки SCM, после было приобретено еще два сложных обрабатывающих центра того же производителя, в том числе с возможностью пятиосевой обработки. Желание опробовать новые технологии и постоянный поиск эффективного оборудования стали причиной для заказа из Англии высокопроизводительного станка для нанесения клея в автоматическом режиме. Это оборудование обеспечивает высокое качество клеенанесения, что гарантирует и высокое качество отделки фасадов.
Продукция «Первой фабрики фасадов»
Сегодня «Первая фабрика фасадов» (в том числе ее подразделение «Люкс-Профиль») производит не только фасады, но и профили MDF. В ассортименте выпускаемой продукции более 200 вариантов мебельных фасадов - от классических до искусственно состаренных и акриловых высокоглянцевых, а также дверных накладок из плиты MDF, облицованных пленкой ПВХ.
Клиенты «Первой фабрики фасадов»
Основные клиенты «Первой фабрики фасадов» - небольшие производители кухонь, в том числе так называемые «гаражники», которые преобладают на мебельном рынке России. Эти небольшие производства выпускают, как правило, от 1 до 30 кухонь в месяц и нуждаются в надежном и пунктуальном поставщике. Есть в портфеле «Первой фабрики фасадов» и заказы от крупных мебельных комбинатов. Фасады - это индивидуальный продукт, фабрика не делает ничего на склад, никаких производственных партий: у конкретного клиента есть заказ - кухня, и согласно этому заказу производятся индивидуальные фасады. Средний срок выполнения заказа - 10 дней, на сложные заказы требуется чуть больше времени. При наличии широкого ассортимента пленок и декоров стоимость фасадов, которые изготавливает фабрика, не самая низкая, но клиенты ценят качество и сервис, которые гарантирует «Первая фабрика фасадов». Процесс выполнения заказов клиенты могут отслеживать в Интернете, что удобно и исключает лишние звонки, когда заказ готов, клиент это видит и может его забирать.
«Первая фабрика фасадов» сейчас активно развивает свою дилерскую сеть. Уже есть дилеры в Москве, Перми, Уфе, а в Новосибирске - полноценное представительство. Фабрика активно работает с транспортными компаниями, но есть и два собственных грузовых автомобиля; со склада при производстве на этих автомобилях готовая продукция доставляется до склада грузоперевозчика, и тем самым исключается оплата услуг экспедирования, что выгодно для клиента.
Кадры «Первой фабрики фасадов»
Сейчас на фабрике работает около 70 человек. Костяк коллектива составляют те 10-15 человек, которые начинали производство, они трудятся на предприятии до сих пор. «Мне кажется, что эти люди любят работу даже больше, чем я, они не мыслят своей жизни без нашей фабрики», - отмечает Антон Осинцев. В самом начале пути 70% работ выполняли именно люди и лишь 30% - имевшееся на тот момент оборудование. Сейчас процесс производства фасадов автоматизирован, на долю ручного труда приходится 30% операций, но без квалифицированных кадров не обойтись. Старожилы занимаются обучением молодых сотрудников: вновь пришедшего прикрепляют к опытному сотруднику, и в процессе работы происходит обучение. Но в планы руководства предприятия входит направлять работников на повышение квалификации - без этого сегодня никак.
Говорит г-н Осинцев: «У нас семейный бизнес. Во главе фирмы, которую основал отец, сейчас мы с женой, задействован и двоюродный брат. В коллективе тоже несколько трудовых династий - родители и дети. Сотрудники сами проявляют инициативу - видят, на каком участке не хватает человека, предлагают посмотреть кого-то, кто у них уже есть на примете. Текучки кадров на фабрике нет, если кто-то не хочет трудиться, он и не задерживается у нас. И тут уж не играет роли - кто сват, а кто брат. Некоторые говорят, что это не очень хорошо, когда семейный бизнес и в коллективе работают семьями, но исходя из моей практики, я знаю, что это не так. Люди в нашем коллективе переживают за наше дело как за свое личное и максимально вовлечены в процесс развития компании. А мы, руководители, обеспечиваем работникам комфортные условия и достойную заработную плату, гораздо выше среднерыночной. И люди это ценят, держатся за свои места».
Производство на «Первой фабрике фасадов»
Для производства продукции предприятию ежемесячно требуется почти восемь фур плит MDF - 160 т или 10 тыс. м2. Сейчас основным поставщиком плит MDF толщиной 16 и 19 мм является компания Kastamonu, которая год назад начала производство этого материала в ОЭЗ «Алабуга» (Республика Татарстан). До того времени плиту приходилось закупать на Украине, что было довольно дорого, но на тот момент ни один отечественный завод не мог обеспечить стабильное качество продукции. В связи с политическими и экономическими событиями покупать украинскую плиту MDF стало крайне невыгодно, поэтому, по словам Антона Осинцева, открытия завода в Алабуге на фабрике ждали с нетерпением. «Первая фабрика фасадов» стала одним из первых клиентов Kastamonu - еще до официального открытия завода в Татарстане руководство фабрики оценило качество пробных партий плит и в результате предприятие из Екатеринбурга стало постоянным клиентом нового крупного плитного комбината.
Процесс производства мебельных фасадов осуществляется в пять-шесть этапов, а применение технологии «нестинг», как уже было сказано выше, сокращает несколько этапов классической схемы. С одной стороны, эта технология производства довольно проста, но приходится учитывать очень много факторов, которые влияют на качество производимого продукта: температуру окружающей среды, влажность воздуха и сырья, состав клея, характеристики пленки и т. д.
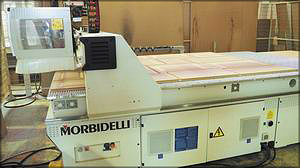
Обрабатывающий центр Morbidelli (SCM Group)
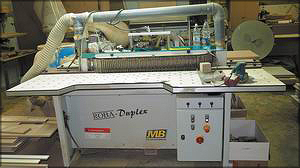
Шлифовальный станок Roba-Duplex (MB Maschinenbau)
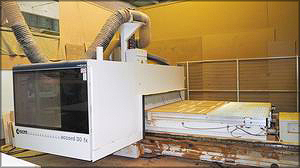
Обрабатывающий центр с ЧПУ SCM accord 30 fx (Италия)
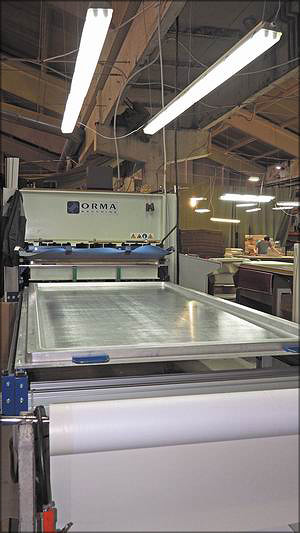
Мембранно-вакуумный пресс ORMA (Италия)
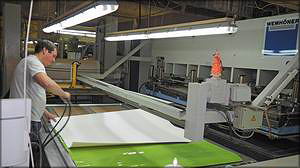
Мембранно-вакуумный пресс Wemhoener (Германия)
На площадке установлены три итальянских обрабатывающих центра, работающих по технологии «нестинг»: самый первый станок SCM без какой-либо автоматизации и два обрабатывающих центра (ОЦ) с ЧПУ. ОЦ компании Morbidelli (входит в SCM Group) оснащен автоматической загрузкой и выгрузкой: станок сам берет лист плиты MDF и укладывает его на рабочий стол и сам же его после обработки выталкивает, но готовая деталь снимается с рабочего стола вручную. А третий обрабатывающий центр с ЧПУ SCM accord 30 fx - наиболее сложный «нестинговый» станок на фабрике. На этом ОЦ есть функция обработки деталей по пяти осям, что дает возможность, например, производить радиусные фасады, наносить на них любой рисунок, придавать любую форму. Каждая деталь промаркирована, в бирке указаны все необходимые данные конкретного заказа, например, номера заказа и позиции детали в заказе и т. д. Оператор формирует лист заказа, станок считывает с маркировки все данные, обрабатывает плиту в соответствии с ними и автоматически выталкивает отфрезерованные фасады. За один проход станок может обработать несколько деталей разных заказов. После фрезерования фасады еще раз маркируются и раскладываются согласно заказам по цветам.
Применение технологии «нестинг» на этих обрабатывающих центрах позволяет свести к минимуму отходы после раскроя листа MDF. По сути, все обрезки при таком способе раскроя - это опилки, ни на одном форматно-раскроечном станке такого результата не добиться. Хотя и без обычного «форматника» зачастую не обойтись, поэтому на «Первой фабрике фасадов» установлен еще и форматно-раскроечный станок Griggio (Италия).
После обработки на нестинговых станках отфрезерованные фасады отправляются на шлифование на автоматическом станке Butfering производства компании Homag Group (Германия). Два таких станка компания «Сапем-Инвест» поставила на «Первую фабрику фасадов» почти пять лет назад. Пока на производстве используется только один станок, но впоследствии они должны встать в линию на новой площадке. На Butfering сначала шлифуются плоскость и фрезеровка, а затем - торцы. На этом этапе осуществляется контроль качества шлифовки. Кроме того, в цехе установлен шлифовальный станок Roba-Duplex (производитель - MB Maschinenbau, Германия), также поставленный на предприятие компанией «Сапем-Инвест».
Дальше наступает этап нанесения пленки. На складе в наличии постоянно имеется около 150 образцов пленок азиатских и 60 пленок европейских производителей, что позволяет выпускать широкий ассортимент продукции. Сначала на фасад вручную наносится клей специальными пистолетами, затем фасад сушится и направляется с пленкой на мембранно-вакуумные прессы. На фабрике используется в основном клей DORUS от Henkel (Германия). На фабрике установлены три пресса производства компаний Bürkle и Wemhöner (Германия), ORMA (Италия). Фасады вручную раскладываются на рабочем столе пресса, после чего раскатывается пленка и фасады загружаются в пресс, где осуществляется склеивание. После того как фасады с нанесенной пленкой выходят из прессов, вручную обрезаются излишки пленки и при необходимости фасады направляются на станок Roba Profi Clean (производитель - MB Maschinenbau, Германия), на котором удаляются остатки клея с обратной стороны запрессованных деталей. Подобная очистка выполняется далеко не на всех производствах, а если и осуществляется, то чаще всего вручную, а на «Первой фабрике фасадов» этот процесс автоматизирован.
Затем проверяется качество готовых фасадов, после чего в соответствии с заказами формируются партии для отправки клиентам. В зависимости от желания заказчика фасады могут быть искусственно состарены - на них вручную наносится патина, что делает каждый фасад уникальным. Готовые фасады направляются на упаковку, в процессе которой еще раз проверяется качество изделия. Упакованные фасады на складе не задерживаются - почти сразу же они отгружаются клиентам.
Контроль качества на «Первой фабрике фасадов»
Как такового, отдела качества на производстве нет. Оценка качества фасадов выполняется на каждом этапе производства, в обязанностях каждого сотрудника проверять изделие на наличие брака. Если ты пропустил брак, который был допущен на предыдущем этапе, то считается, что это брак твой. Поэтому каждый сотрудник заинтересован в том, чтобы не допустить ошибок и недоработок, и если обнаруживает брак, то возвращает заготовку на переделку. Окончательный контрольный осмотр осуществляют упаковщики.
Планы «Первой фабрики фасадов» на будущее
В начале 2016 года на «Первой фабрике фасадов» запланирован окончательный переезд на новую площадку, которая располагается рядом с Екатеринбургской кольцевой автодорогой (некоторые участки, например производство акриловых фасадов, туда уже перебрались). Нынешнее здание фабрики уже не отвечает требованиям времени и производства. Изначально, когда фабрика открывалась, оборудование на площадке размещалось по кругу, а не выстраивалось в линейку, как это должно быть в идеале, потом оборудование менялось, новые, более мощные станки приходилось размещать в пределах имеющихся площадей. Новая площадка построена с учетом всех критериев, важных при производстве фасадов: в отдельном здании будут располагаться обрабатывающие центры и «форматники», и вся пыль и возможные отходы, образующиеся при раскрое плит, будут утилизироваться отсюда. В отдельном помещении, где поддерживаются необходимые влажность, температура и чистота, будут выполняться основные технологические операции - финишная обработка, приклеивание пленки. Предусмотрен склад полуфабрикатов и готовой продукции. На новой площадке установлена аспирационная система, мощности которой позволят раз в час выполнять однократный обмен воздуха в каждом помещении. Разработкой этой системы занималась отечественная компания «Тепловей» из Челябинска. Вообще же здания и коммуникации новой фабрики спроектировал сам генеральный директор Антон Осинцев: научившись пользоваться программой AutoCad, он же подобрал новые станки в соответствии с требованиями расширяющегося производства, расставил их вместе с уже имеющимися так, как посчитал нужным, рассчитал размеры помещения, комплектацию цехов. Сейчас проект на финальной стадии реализации. Идет монтаж газопровода, завершается внутренняя отделка помещений, оборудуются санузлы и душевые. Площадь нового помещения - 4,5 тыс. м2.
«Сейчас такое время, когда без перемен не обойтись, - говорит генеральный директор «Первой фабрики фасадов» Антон Осинцев. - Нужно смотреть - что надо клиенту, меняться, отвечать требованиям времени, соответствовать реалиям рынка. Чем мы и занимаемся. Чтобы остаться на плаву, нужно развиваться, вкладываться. Мы стараемся не только ориентироваться на нужды клиентов, на спрос и новые тенденции, нам важно, чтобы и наши сотрудники держались за свои места и работали с удовольствием. Только так - комплексно, постоянно совершенствуясь и развиваясь, можно добиться успеха».
Ольга РЯБИНИНА