Красота жидкого дерева
Очередной шаг в сторону комплексной переработки древесины
Древесно-полимерные композиты
На страницах лесных, деревообрабатывающих журналов и газет много говорится о проблемах комплексной переработки древесины и максимальном использовании древесных отходов, которые остаются при производстве основной продукции. Действительно, рациональное использование древесного сырья организовано не на всех предприятиях нашей страны. Но все же российские производители «не стоят на месте» и начинают внедрять новые материалы и технологии с целью получения максимальной прибыли от своей продукции: этому способствуют организации выставок, проведение всевозможных конференций, круглых столов, где российские деревообработчики могут поделиться своим опытом и перенять опыт соотечественников и зарубежных коллег.
Зачем нужна такая продукция на внутреннем российском рынке? Каковы перспективы собственного производства этих композитов?
Ответ на эти вопросы весьма тривиален: спрос рождает предложение. Когда понадобилось строить деревянные здания больших площадей и различных конструкций, массивную древесину стали замещать изделия из клееных древесных материалов. Прошло время, и мебельщики начали использовать плиты MDF, а не ДСП для наружной отделки мебели.
В настоящее время рынок древесно-полимерных материалов (ДПМ) активно развивается во всем мире. Сравнительно несложная организация технологического процесса, минимально занимаемые под оборудование площади, дешевое и практически экологически чистое сырье и материалы серьезно отличают древесно-полимерные профили от «капиталоемких» и «токсичных» ДСП, ДВП и MDF, а способность легкой обработки дереворежущим инструментом не создает препятствий для «полета фантазии» дизайнеров и архитекторов. Кроме того, древесно-полимерный материал можно вторично перерабатывать и, не ухудшая его свойств, получать изделия новых форм.
От общего к частному
Производством композиционных материалов в России занимаются уже давно: это известный всем бетон, органопластики, стеклопластики, углепластики, материалы на основе керамики и многие другие. В деревообработке выделяют древесные композиты.
Яркими представителями этой группы являются фибролит, цементно-стружечные плиты, арболит, массы древесные прессовочные, а также древесно-полимерные композиты.
Древесно-полимерный композит – какой он внутри?
Часто научное название «древесно-полимерный материал» сокращают и употребляют такие термины, как древопласт, «жидкое дерево», древесно-пластиковый композит. Самое главное – чтобы не была утеряна суть названия, а его лингвистические интерпретации могут быть разными.
Если говорить о рецептуре композита, то процентное соотношение древесного наполнителя и связующего определяет области применения и условия эксплуатации материала. Например, для применения материала внутри помещения (мебель, интерьерная отделка) в композицию добавляют меньше связующего, чтобы полученный материал «дышал».
В конструкционных материалах, эксплуатируемых на открытом воздухе, содержится больше связующего. Это позволяет увеличить влагостойкость и способность материала выдерживать серьезные нагрузки. Поэтому для получения продукции с желаемыми характеристиками необходим точный расчет процентного содержания каждой составляющей композиции.
Расширяем рынок древесных композитов
Технологию получения древесно-полимерных материалов, или «жидкого дерева», наша страна заимствовала за рубежом. При этом неверным будет считать, что российский деревообработчик отстал от западного. Ведь фанеру, клееные деревянные конструкции, гнутоклееные материалы, древесные плиты, которые также относят к композиционным материалам, Россия поставляет как на внутренний, так и на мировой рынок.
Экологический кризис, возникший в последнее время, стимулирует отечественного производителя предлагать покупателю безопасную и качественную продукцию. Оговоримся, что сама древесина или древесные частицы различной формы и размеров нетоксичны. Главным источником выделения вредных веществ является формальдегид, содержащийся в связующем, необходимом для «прочного закрепления» древесных частиц между собой и получения материала с отличными от массивной древесины физико-механическими характеристиками. Используемые для производства древесных плит карбамидоформальдегидные и фенолоформальдегидные смолы в процессе эксплуатации выделяют вредные вещества в окружающую среду, а связующие на основе термопластичных полимеров, используемых в древопласте – полиэтилен, полипропилен, поливинилхлорид, – не оказывают пагубного влияния на здоровье человека и защищают сам материал от разбухания, влаго- и водопоглощения, повреждения насекомыми и грибами. Поэтому в настоящий момент расширение рынка экологически чистой продукции актуально не только в России, но и во всем мире.
Ранее применяемые только в космонавтике и авиастроении, сегодня они используются в строительстве, в том числе домостроении, для производства кровельных и напольных покрытий, балок перекрытия, уличных настилов (декингов), ограждающих конструкций; в мебельной промышленности для изготовления окон, дверей, уличной мебели, отделки ванных комнат и бассейнов, товаров народного потребления; в автомобильной промышленности. В нашей стране только начинает формироваться рынок древесно-полимерных композитов. Недавно в Санкт-Петербурге начали выпуск такого материала.
Маркетинговая политика предприятия, или c чего все началось?
Основная цель холдинга ООО «ВЭЭК» – комплексная переработка древесины. Для достижения результата работает большое количество малых и средних деревообрабатывающих компаний. В этой статье будет рассказано о деятельности одной из них – ООО «Древопласт», которое занимается производством древесно-полимерных профилей. Предприятие расположено недалеко от Санкт-Петербурга, в Лодейном Поле. О состоянии и перспективах развития древесно-полимерных материалов в России, об организации технологии изготовления на одном из своих предприятий рассказывают руководитель отдела продаж ООО «ВЭЭК» Александр Олегович Дорохов и генеральный директор ООО «Древопласт» Дмитрий Николаевич Елькин.
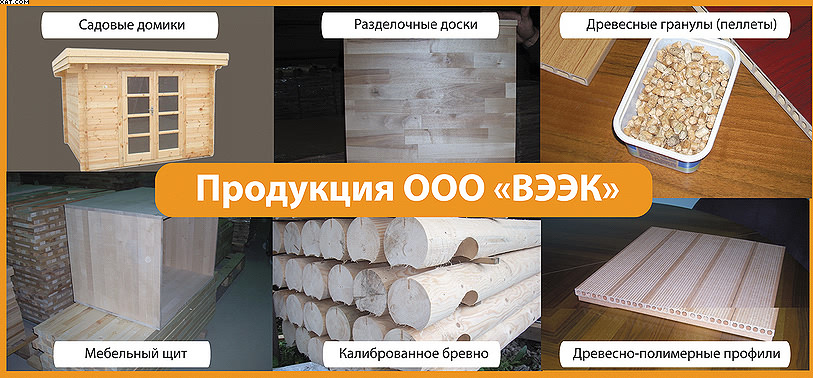
Создаем профиль из ДПК
профилей, получаемых на ООО «Древопласт»
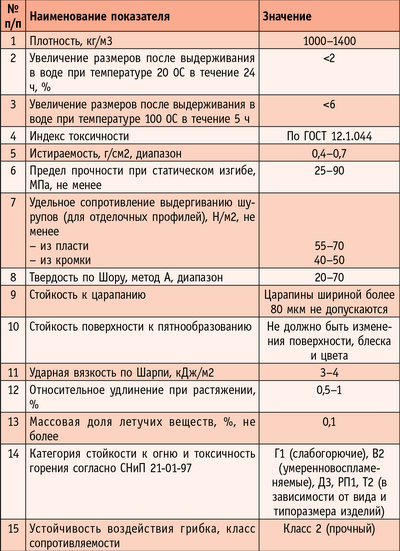
Среди технологий получения древесно-полимерных композитов – литье в формы, экструзия, и прессование. Наиболее распространенной и апробованной за рубежом (апробация – использование научных разработок на практике) остается экструзия.
Традиционно технологический процесс получения изделий из древесно-полимерных композитов (ДПК) состоит из следующих этапов: измельчение древесного сырья, его сушка (при влажности сырья более 15%), дозирование и смешивание древесных частиц, связующего и химических добавок, получение профиля нужной формы и размера, отгрузка готовой продукции на склад.
На ООО «Древопласт» собственное производство древесных гранул из опилок хвойных пород позволяет исключить первые две технологические операции при получении ДПК.
Это экономит время и уменьшает себестоимость получаемых изделий. Следует отметить, что такая организация технологического процесса на первых этапах освоения производства древесно-полимерных профилей является наиболее приемлемой. Кроме того, ранее используемые только в качестве топлива древесные гранулы нашли новую область применения. И теперь они используются не только в виде конечного продукта, но и являются исходным сырьем для древопласта.
Заметим, что производителей экструзионного оборудования для древесно-полимерных профилей на мировом рынке представлено много. Это США, Германия, Австрия, Италия, Китай, Тайвань. Выбор ООО «ВЭЭК» был остановлен на китайском производителе – компании SHANGHAI JWELL MACHINERY CO., LTD.
По мнению Александра Олеговича, китайский производитель оборудования «предлагает не только машины, но очень понятно и компетентно может объяснить принцип организации технологического процесса получения древесно-полимерных профилей».
Оказывается, китайцы умеют делать пусть не такое качественное оборудование, как немцы или итальянцы, зато способность быстро и верно подбирать режимы под объемы выпуска и требуемые характеристики продукции позволила им заинтересовать такой гигант, как ООО «ВЭЭК», в покупке своего оборудования.
Процесс производства древесно-полимерных профилей состоит из двух участков: участка получения полуфабриката и линии получения готовой продукции. Вначале древесные гранулы влажностью 4–5% поступают на участок смешивания. Здесь получают полуфабрикат, в состав которого входят пеллеты (древесные гранулы), химические добавки (термостабилизатор, различные наполнители, краситель и смазка), связующее (полиэтилен низкого давления, а также предварительно измельченная в дробилках пленка).
Сам процесс происходит следующим образом: вначале в бак горячего смешивания, температура в котором достигает порядка 100°С, подается смесь. При такой температуре связующее расплавляется и равномерно распределяется по всей массе древесного наполнителя. Затем для охлаждения полученная масса подается в бак теплового смешивания. Смесь, нагретая до 40°С, пропускается через экструзионную головку, на выходе из которой получают гранулы нужного размера и форм. Гранулы охлаждаются до комнатной температуры в специальной емкости и фасуются.
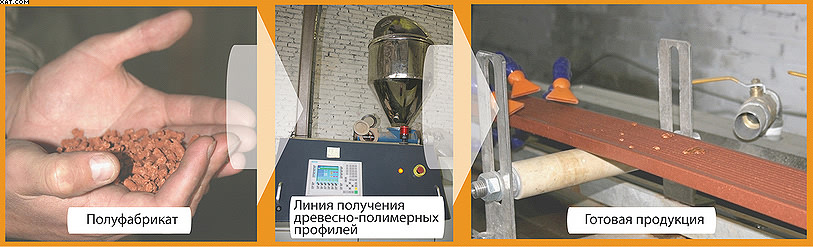
Рис. 1. Получение древесно-полимерных профилей
После этого «полуфабрикат» поступает либо на линию получения декинга, либо на линию получения шпунтованной доски. Вначале гранулы подаются в бак для смешивания, затем проходят через пять цилиндрических головок, температура которых 230, 220, 210, 155 и 155°С соответственно. Давление при экструзии для получения декинга составляет 10–11 МПа, шпунтованной доски – 3–3,5 МПа. На выходе из экструзионной головки профиль охлаждается сверху и снизу холодной водой. Затем для удаления лишнего количества воды с поверхности он обдувается с трех сторон холодным воздухом (рис. 1).
Все рисунки к статье Красота жидкого дерева см. в PDF-версии журнала
Лента профиля обрезается на определенную длину торцовочной пилой и сбрасывается в карманы-накопители. После этого полученная продукция должна полежать на складе 24 часа. За это время изделие приобретает необходимую в процессе эксплуатации прочность. Производительность линии по производству шпунтованной доски составляет 90 кг/ч; декинга – 120–180 кг/ч.
По словам генерального директора ООО «Древопласт» Дмитрия Николаевича Елькина, «разработка режимов технологического процесса работы линии занимает много времени и сил. При ее настройке на выпуск профиля требуемой формы необходимо учитывать большое количество факторов. Много проблем возникает с таким профилем, как шпунтованная доска. В результате чего производительность у этой линии невысокая».
Комментарий специалиста
Александр Олегович Дорохов, руководитель отдела продаж ООО «ВЭЭК»
- Почему и когда вы заинтересовались технологией изготовления «жидкого дерева»?
- Наша компания развивает производство экологически чистой продукции в России. Довольно долго мы занимаемся выпуском древесного топлива (пеллет) из опилок хвойных пород. Около года назад совместно с руководством нашей компании приняли решение расширить область применения биотоплива. Анализ спроса и предложения на отечественном рынке показал, что в нашей стране отсутствует рынок древесно-полимерных композитов. В Америке он существует уже десять лет, а в Европе вырастает примерно на двадцать процентов за год. Очень бурно рынок ДПК развивается в Китае. Следовательно, в России освоение собственного производства древесно-полимерных материалов является актуальным.
- Каковы перспективы использования «жидкого дерева» в России?
- У древопласта множество свойств: технологичность, долговечность, влагостойкость. Это экологически чистый продукт. К тому же, его цена намного ниже пластмасс. По физико-механическим показателям плита MDF значительно уступает древопласту.
К примеру, древесно-полимерные профили имеют меньший показатель разбухания по толщине и влагопоглощению. Материал может впитывать влагу (до 2%), при этом не изменяя своих свойств. Возможно лишь незначительное изменение цвета, но это допускается для изделий, эксплуатируемых на открытом воздухе. Если же плита MDF начнет разбухать и поглощать воду или влагу, получить материал с исходными свойствами даже после сушки не удастся - все равно произойдет расслоение плиты. Называя факторы, стимулирующие увеличение выпуска древесно-полимерных профилей в России, выделю следующие: значительные объемы запасов лесных ресурсов, верная политика государства в сторону снижения таможенных пошлин на экспортируемую готовую продукцию из древесины, развитие рынка полимеров и вторсырья.
Среди наиболее перспективных областей применения древопласта в России отмечу строительство, автомобилестроение и мебельную промышленность, которым необходимы недорогие материалы разных форм и размеров.
- Каков срок эксплуатации ваших изделий?
- На данный момент мы не можем определенно сказать, какой гарантийный срок у нашей продукции, так как процесс производства запущен с мая этого года. Аналогичная продукция в Америке эксплуатируется около 20 лет. Такой срок установлен на изделия, которые подвергаются внешним атмосферным воздействиям. Внутри помещения, думаю, не меньше. В рекламных проспектах можно встретить срок эксплуатации и до 50 лет. Все еще зависит и от вида продукции. По крайней мере, сроки эксплуатации изделий из ДПК очень большие.
- Есть ли сдерживающие факторы развития рынка древесно-полимерных материалов в России?
- Определенно они существуют. Во-первых, это низкая осведомленность отечественного потребителя. На сегодняшний день в России отсутствуют квалифицированные специалисты как в лесной, так и в экономической отраслях, которые занимаются продвижением ДПК на внутренний рынок. Во-вторых, у нашей страны нет опыта работы с этим материалом. Добавлю, что именно опыт и большое количество научных исследований в области ДПК определили такое сильное развитие спроса и предложения на «жидкое дерево» за рубежом.
- Вы поставляете свою продукцию только строительным организациям или продукцией интересуются еще и мебельщики?
- На сегодняшний день осуществляем поставки древесно-полимерных профилей только строительным организациям, но в дальнейшем будем расширять свой ассортимент, увеличивать области применения и наращивать объемы выпуска нашей продукции.
- Планируете ли осуществлять поставки за рубеж?
- У нас налажены поставки биотоплива со Швецией, Данией, Голландией, Финляндией. Если будем там конкурентоспособны и интересны, то можем также поставлять в эти страны продукцию из древопласта.
- Как заинтересовать зарубежных потребителей? Какие у вашей продукции должны быть преимущества?
- Самое главное преимущество отечественного «жидкого дерева» - это его цена. Низкая стоимость электроэнергии, дешевое сырье и материалы способствуют получению невысокой себестоимости продукции. Импорт такой технологичной продукции на сегодняшний день очень выгоден. Таким образом, мы в состоянии заинтересовать своей продукцией иностранных клиентов.
- Можно ли изготавливать из древопласта двери? Есть ли у них какие-то преимущества по сравнению с филенчатыми дверьми?
- Я бы не стал сравнивать этот продукт с массивной древесиной. Филенчатые двери из массивной древесины как были, так останутся. Нельзя говорить, что древопласт сможет заменить все изделия из цельной древесины или все изделия из пластмассы. Древопласт - это комплекс из древесных частиц, различных химических добавок и термопластичного связующего. Именно поэтому получаемый материал имеет такие хорошие, по сравнению с массивной древесиной или с древесными плитами, физико-механические показатели. Продукцию из древопласта можно сравнить с дверьми экономкласса - дверьми с сотовым заполнением, производство которых широко распространено в Китае. Можно делать двери и из древопласта, но это уже другая ниша, как потребительская, так и ценовая.
- Древесно-полимерные композиты получают методом экструзии. Аналогичная технология используется при производстве экструзионных ДСП (ДСПэ). В России такие плиты не нашли широкого распространения, а вот в Германии этим занимаются. ДСПэ используют в дверной промышленности. Можно ли сравнить два эти материала?
- При производстве ДСПэ и древопласта применяют разные виды связующего: для ДСПэ - это термореактивные синтетические смолы, содержащие большой процент формальдегида, у древопласта - это термопластичные полимеры. Добавлю, что древопласт - продукт глубокой переработки древесины. К тому же одно из самых замечательных свойств древесно-полимерных композитов - возможность управлять в процессе производства конечными свойствами получаемого продукта. В зависимости от компонентов, входящих в состав, точнее от их соотношения, можно получить материал со свойствами, близкими к пластмассе либо к древесине. Область применения ДПК очень широка.