ГК «Русская Лесная Группа»
Одна из крупнейших лесопильных компаний России
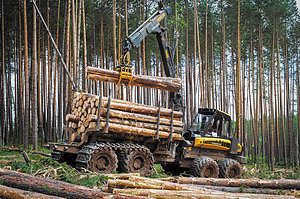
Форвардер Ponsse на участке лесозаготовки
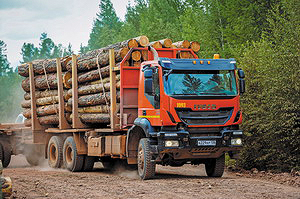
Вывозка древесины сортиментовозами Iveco
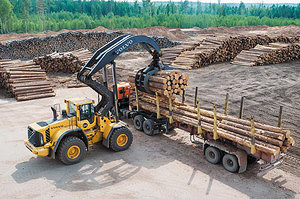
Разгрузка круглых лесоматериалов
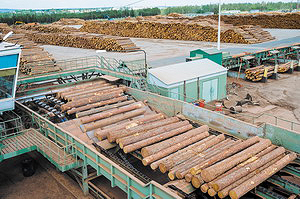
Сортировка круглых лесоматериалов
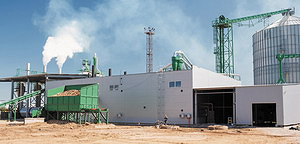
«Сибирские топливные гранулы»
В Иркутской области, в пос. Новая Игирма и г. Усть-Кут действуют три лесопильных предприятия, входящие в состав ГК «Русской Лесной Группы»: ООО «СП СЭЛ-Тайрику», ЗАО «ЛДК Игирма», ООО «ТСЛК», а также два недавно открывшихся завода по производству пеллет - «Сибирские топливные гранулы». Мощность лесопильных заводов компании по входному сырью составляет 2,2 млн м3 пиловочника в год, мощность по производству пиломатериалов - 1 млн м3. В 2015 году ГК «Русская Лесная Группа» произвела 858 тыс. м3 пиломатериалов, что позволило ей стать одной из крупнейших российских лесопильных компаний.
Все начиналось с «СП СЭЛ-Тайрику». В 2004 году с привлечением японского капитала был создан завод по переработке тонкомерной древесины. Станочный парк предприятия формировался по последнему слову техники. Например, сортировочная линия Hekotek на тот момент была одной из крупнейших в России. В том же 2004 году на базе Игирминского леспромхоза был пущен цех лесопиления, а в течение следующего года построен и сдан в эксплуатацию цех строжки. Уже в 2005 году удалось вывести завод на проектную мощность: по объему переработки сырья - 390 тыс. м3 в год, по выпуску пиломатериалов - 155 тыс. м3 в год, и с тех пор предприятие не снижает набранных темпов. В тот же год была образована ГК «Русская Лесная Группа» как объединение лесозаготовительных, лесоперерабатывающих, транспортных и торговых компаний на территории России, в которое и вошло «СП СЭЛ-Тайрику».
ГК «Русская Лесная Группа» продолжала пополняться новыми активами: в ее состав вошли торговая компания «СЭЛ-Трейд» и транспортно-логистическая «СЭЛ-Транс», была образована управляющая компания «РусЛесГрупп»; проведена реструктуризация предприятий. Все заводы успешно прошли сертификацию по системе FSC, были модернизированы производственные мощности, проложены железнодорожные пути с тупиками.
В 2008 году началось строительство лесопильно-деревообрабатывающего комплекса «ЛДК Игирма» для переработки пиловочника диаметром от 26 см. Завод в прямом смысле строился в чистом поле - на месте бывшего игирминского аэропорта. Были проложены все коммуникации, завод был укомплектован передовым оборудованием, и в 2011-м состоялась торжественная церемония открытия производства «ЛДК Игирма». Тогда же «ЛДК Игирма» был включен приказом Минпромэнерго России в перечень приоритетных инвестиционных проектов в области освоения лесов, а также в «Стратегию социально-экономического развития Сибири до 2020 года». В 2014 году «ЛДК Игирма» вышел по переработке сырья на полную мощность - 700 тыс. м3 в год, выпуск пиломатериалов составил 350 тыс. м3 в год.
Начало строительства другого лесопильного предприятия ООО «ТСЛК» в г. Усть-Куте началось в 2008 году, а в эксплуатацию производство введено в 2012 году. «ТСЛК» - одна из крупнейших лесоперерабатывающих компаний Иркутской области. Проект внесен в перечень приоритетных инвестиционных проектов в области освоения лесов. В 2015 году на заводе была введена в эксплуатацию линия радиального распила мощностью 300 тыс. м3 в год по входящему сырью. Пуск линии позволил увеличить мощности завода по производству пиломатериалов до 500 тыс. м3 в год. По итогам августа 2016 года «ТСЛК» вышел на проектные мощности.
В 2014 году руководство ГК «Русская Лесная Группа» приняло решение о строительстве в партнерстве с компанией «Сибирские топливные гранулы» двух заводов по производству древесных топливных гранул в пос. Новая Игирма и г. Усть-Кут Иркутской области на действующих площадках ГК «Русская Лесная Группа». В 2016 году предприятия были введены в эксплуатацию. Завод «Сибирские топливные гранулы», призванный выполнить задачу полной утилизации отходов лесопильного производства «СЭЛ-Тайрику», «ЛДК Игирма», ООО «ТСЛК», сегодня, по сути, выходит на проектные мощности. Кроме мощностей по деревообработке и производству пеллет на площадках ГК «Русская Лесная Группа» в Новой Игирме есть бетонный, цементный и асфальтный заводы, которые обеспечивают все нужды производств: заливку фундаментов, полов, устройство дорог, благоустройство территории, в том числе зачастую и по просьбе поселковой администрации. У группы есть собственная заправка, вертолет, производственные столовые, гостиница. Предприятия Группы в Новой Игирме самодостаточны и независимы с точки зрения лесосырьевого обеспечения, что, безусловно, способствует бесперебойному выпуску продукции высокого качества.
Стоить отметить, что с целью долгосрочного развития в 2013 году ГК «Русская Лесная Группа» инициировала создание «Национальной ассоциации лесопромышленников - Русский лес». Работа ассоциации основана на взаимодополнении и паритетных отношениях. Такая кооперация позволяет участникам ассоциации эффективно решать общие проблемы, что немаловажно в нынешних экономических условиях. За последние годы предприятия промышленности осознали необходимость партнерства и кооперации. Ассоциация создана, чтобы оказывать влияние на лесопромышленный комплекс России для интенсификации его развития, повышения рентабельности и эффективности работы. Ассоциация открыта для вступления новых участников.
Продукция
Основным видом продукции, производимой на заводах «СП СЭЛ-Тайрику», «ЛДК Игирма» и «ТСЛК», являются сырые, сухие и строганные пиломатериалы и профильные изделия. В номенклатуре выпускаемой продукции высококачественные пиломатериалы для японского домостроения: «таруки» (строганные бруски высокого качества из сосны камерной сушки) и «генбан» (доски высокого качества из сосны естественной и камерной сушки), а также обрезные пиломатериалы транспортной влажности и камерной сушки из сосны и лиственницы, профильные погонажные изделия из древесины сосны, лиственницы и ели (доска пола, евровагонка, террасная доска, имитация бруса, молдинг, блок-хаус, брусок и рейка).
Отдельно стоит отметить, что основная продукция производится из древесины элитных хвойных пород - ангарской сосны и сибирской лиственницы, известных не только в России, но и во всем мире. Отходы лесопиления - щепа, опилки, стружка - используются при производстве топливных древесных гранул (пеллет) на предприятии «Сибирские топливные гранулы».
География поставок
При создании российско-японского предприятия группы предполагалось, что основным рынком сбыта пиломатериалов будет Япония, но за годы работы «СП СЭЛ-Тайрику» в результате наращивания производственных мощностей и становления других заводов ГК «Русская Лесная Группа» география поставок существенно расширилась. Сейчас 85% производимой продукции идет на экспорт: помимо Японии, продукция отправляется на рынки Южной Кореи, Китая, стран Европы и некоторых арабских стран, например Египта. Около 15% поставляется на внутренний рынок и в страны СНГ, в первую очередь профильные погонажные изделия: евровагонка, доска пола, террасная доска, блок-хаус.
Лесозаготовка
У ГК «Русская Лесная Группа» имеются арендованные лесные участки: заключено восемь договоров аренды в Киренском и 11 договоров аренды в Усть-Кутском лесничествах и два договора в Нижне-Илимском лесничестве Иркутской области. Суммарная площадь арендованных лесных участков составляет 2 млн га с общим запасом древесины 416 млн м3 и ежегодным допустимым объемом заготовки 4 млн м3. В планах группы на 2016 год - приблизиться к 100%-ному освоению расчетной лесосеки. На участках лесозаготовки применяется высокотехнологичная техника TigerCat (Канада), John Deere (США) и Ponsse (Финляндия). На заводы группы заготовленная древесина транспортируется на сортиментовозах Man и Iveco.
После проведения заготовки древесины на лесных участках компания осуществляет мероприятия: искусственное, комбинированное и естественное лесовосстановление путем минерализации почвы, сохранения подроста, посева семян с сертификатами 1-го класса и посадкой саженцев с открытой корневой системой. В 2016 году планом мероприятий по лесовосстановлению будет охвачено около 13,3 тыс. га.
«СЭЛ-Тайрику»
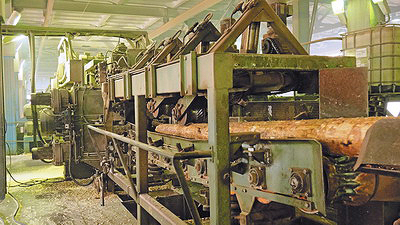
Лесопильный цех «СП СЭЛ-Тайрику»
Общий объем входящего сырья составляет 28 тыс. м3 в месяц. Пиловочник выгружается на площадку нижнего склада, откуда попадает на сортировочную линию Hekotek (Эстония), которая позволяет сортировать сырье как по диаметру, так и по качеству: древесина движется по линии и рассортировывается в карманы по сортам, породам и качеству (в соответствии с заданиями на распил, сортировка сырья по диаметру выполняется с градацией 1 см). Скорость подачи сырья на линию - 825 бревен в час. За процессом пристально следят операторы, обладающие многолетним опытом сортировки.
Для загрузки лесоматериала на приемный стол и складирования рассортированного сырья с линии Hekotek используются три погрузчика Volvo L-150E с захватами. Рассортированный пиловочник складывается в штабеля высотой 2,5-4 м по диаметру, породам и качеству на прилегающей к сортировочной линии площадке вместимостью до 45 тыс. м3. С этой площадки круглые лесоматериалы отправляют в лесопильный цех на комплексный стол подачи, а с него - на раскатный стол и горку поштучной выдачи, оттуда бревнотаской подают на разворотное устройство, которое автоматически ориентирует бревна в нужном направлении.
Окорка бревен осуществляется на окорочном станке Valon Kone 450 (Финляндия). Окоренная древесина проходит через измеритель (кубатурник), где автоматически обсчитывается диаметр бревна. Полученные данные (диаметр, длина, объем) регистрируют и хранят в базе данных компьютера.
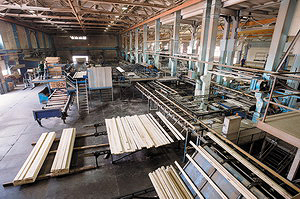
Лесопильный цех «СП СЭЛ-Тайрику»
Щепу из станка вместе с опилками подают на просеивающее сито. Кондиционную щепу отделяют и транспортером отправляют на площадку складирования и отгрузки вместимостью до 10 тыс. м3, откуда она загружается ленточным транспортером или ковшевым погрузчиком на базе Volvo L-150E в железнодорожные вагоны. Отходы производства (опилки, стружка, кора, отсев), топливная щепа поступают в котельные КУК ЖКХ пос. Новая Игирма и «СП СЭЛ-Тайрику» (здесь установлено оборудование финского производителя Wärtsilä - три котла мощностью 6 МВт), где используются в качестве топлива.
После окорки происходит распиловка бревен на фрезерно-брусующем станке HewSaw R 200 SE (производитель - компания Veisto, Финляндия). Центральные доски, полученные при распиловке, поступают на торцовку, где выполняются предварительная подторцовка и сортировка пиломатериалов. Далее доски поступают на пакетоформирующую машину для укладки в сушильный пакет: боковые доски на выходе из станка отделяются делительным устройством и подаются на подторцовку, после чего рассортировываются и по транспортеру поступают в карманы-накопители, откуда их вручную укладывают в сушильные пакеты.
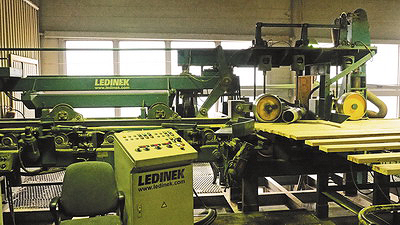
Многопильный строгальный станок Ledinek на «СП СЭЛ-Тайрику»
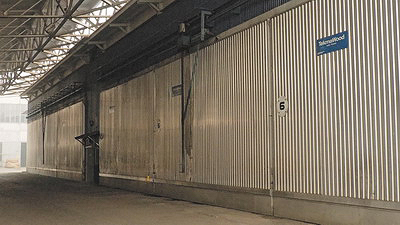
Сушильный комплекс «СП СЭЛ-Тайрику»
Готовые изделия от станка транспортером подают на сортировочно-упаковочную машину, сортируют, пиломатериал упаковывают в блок-брикеты, формируют транспортный пакет. Отходы, полученные при распиловке, подаются транспортером в рубительную машину Morbark 48 (США) для измельчения. Готовая продукция электропогрузчиком Shinko 8FB (Япония) отвозится на участок упаковки пиломатериала.
В цехе имеется участок подготовки инструмента для заточки дисковых пил, крючков для брусующих головок станка HewSaw R 200 SE. Заточка крючков выполняется на двух станках HewSaw RM-12C и RM-8D. Подготовка пил - от фазы напайки твердых пластин до протачивания по боковой и передней кромкам зубьев - осуществляется вручную на станках Shimada и Vollmer CHHF.
На прилегающей к лесопильному цеху территории работает вилочный погрузчик Komatsu 70FD, который обеспечивает доставку сушильных пакетов от цеха на площадку формирования партий объемом до 2 тыс. м3 для сушки.
В состав сушильного комплекса «СП СЭЛ-Тайрику» входят 18 сушильных камер периодического действия финского производства Tekmawood объемом 120 м3 каждая и четыре сушильных камеры австрийского производства Mühlböck-Vanicek, вместимостью 190 м3 каждая. Сушка пиломатериалов в камерах проходит в автоматическом режиме и контролируется компьютером. Продолжительность сушки пиломатериалов из сосны до влажности 18-20% составляет 120-130 ч, а из лиственницы до влажности 10-12% - 240-250 ч.
Общий объем пиломатериала, высушенного за месяц, составляет 14 тыс. м3 при соблюдении пропорции породного состава заготовки сосна/лиственница 85:15. Сушильный комплекс обслуживают два погрузчика Kalmar DСЕ-120 (Швеция). Для хранения сухой заготовки есть две крытые площадки, позволяющие разместить до 1 тыс. м3 пиломатериала. Высушенная древесина поступает на участок переработки пиломатериалов.
Цех переработки сухих пиломатериалов предназначен для получения готовых строганных изделий в виде брусков, досок и профильных изделий. На площадке возле цеха можно хранить запасы сухих пиломатериалов объемом до 2 тыс. м3, а производственные мощности позволяют выпускать 11,5 тыс. м3 готовой продукции в месяц. В составе станочного парка цеха несколько видов оборудования, включая строгально-многопильный станок фирмы Ledinek Superplan 5V-S200 (Словения) с сортировочно-упаковочной линией Kallfass (Германия).
Погрузчик Komatsu 70 FD подвозит сушильные пакеты к цеху и сгружает их на подающий транспортер, далее они поступают на пакеторазборщик, откуда по транспортеру доски подаются к механизму поштучной выдачи, проходя через автоматический измеритель влажности. Датчики определяют влажность каждой доски. Заготовки, влажность которых превышает установленную, отбраковываются. Заготовки требуемой влажности попадают на станок Ledinek, который обеспечивает гладкую строжку их горизонтальной и вертикальной поверхностей, а также деление пильным блоком. Стружки и опилки удаляются от станка пневмотранспортером через станцию сбора отходов в бункер-накопитель.
Готовые изделия от станка Ledinek ленточным транспортером подают на сортировочно-упаковочную линию Kallfass (подобных линий в цехе три), где продукцию (в основном идущую на экспорт) сортируют, формируют в блок-брикеты, которые обвязывают полипропиленовой лентой, торцуют и формируют из них транспортные пакеты, после чего электропогрузчиком фирмы Shinko 8 FB отвозят эти пакеты на участок упаковки пиломатериалов.
На строгально-пильном станке Weinig Hydromat Н 25-R (Германия) изготавливают евровагонку и разные опалубочные материалы. Сушильные пакеты подают вилочным погрузчиком на пакеторазборщик, далее заготовки поступают к устройству подачи на станок, на котором выполняется гладкая строжка горизонтальной и вертикальной поверхностей заготовок и профильных поверхностей. Стружки и опилки удаляют пневмотранспортером в бункер-накопитель, откуда щеповозом с тягачом доставляют к котельной КУК ЖКХ пос. Новая Игирма и собственным котельным завода, где их используют в качестве топлива.
Готовые изделия от станка транспортером подают на сортировочно-упаковочную машину, где выполняется сортировка, упаковка пиломатериала в блок-брикеты и формирование транспортных пакетов. Готовую продукцию электропогрузчик Shinko 8FB доставляет на участок упаковки пиломатериалов.
В цехе переработки сухих пиломатериалов также имеется участок подготовки инструмента. Здесь установлены станки Weinig Rondamat 912 и STIHL НК 3-720, на которых выполняют заточку прямых ножей для строгальных станков Ledinek Superplan 5V-S200 и Weinig Hydromat Н 25-R. Подготовка и заточка профильных ножей для строгального станка Weinig Hydromat Н 25-R ведется на заточном станке Weinig Rondamat 960, а для точной установки профильных ножей на строгальные головки предназначен прибор измерения инструмента Weinig OptiControl. Кроме того, цех укомплектован заточным станком Vollmer CHC 020 (Германия).
К вспомогательным службам, обеспечивающим оптимальную и безаварийную работу основного производства, относятся службы главного энергетика и главного механика, в состав последней входит группа внедрения, занимающаяся разработкой, изготовлением и монтажом нестандартного оборудования.
Следующий участок в производственной цепочке «СП СЭЛ-Тайрику» - участок упаковки готовой продукции. Готовые транспортные пакеты в зависимости от сорта вручную упаковывают в целлофан и бумагу или только в бумагу, обвязывают полиэстеровой лентой и электропогрузчиком подают на транспортер выноса готовой продукции, откуда их забирает вилочный погрузчик Komatsu 50FD и отвозит на склад готовой продукции, на котором можно разместить единовременно более 10 тыс. м3 пиломатериалов.
Завершается производственный цикл на участке погрузки. Упакованные пиломатериалы загружают в полувагоны посредством крана ККС-10, а в контейнеры - устройством для погрузки. Каждый вагон и контейнер обязательно взвешиваются. В месяц отгружается до 140 контейнеров и 100 полувагонов.
«ЛДК Игирма»
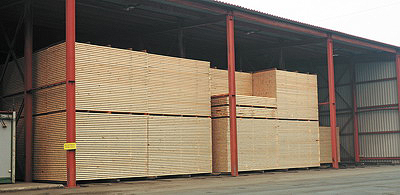
Сушильный комплекс «ЛДК Игирма»
Мощности завода расположены на площади 45,8 га. Производственный процесс «ЛДК Игирма» по большому счету идентичен процессу на «СЭЛ-Тайрику», есть небольшие различия в составе станочного парка, мощности которого превышают мощности «СЭЛ-Тайрику». Сырье складируется на сырьевой бирже - трех площадках вместимостью 200 тыс. м3 (на площадку можно одновременно выгружать сырье из железнодорожных вагонов и автотранспорта). Древесина, поступившая на площадку, так же, как на заводе «СЭЛ-Тайрику», сортируется на линии Hekotek с трехмерным измерителем, металлодетектором и 60-ю карманами, скорость подачи - 835 бревен в час.
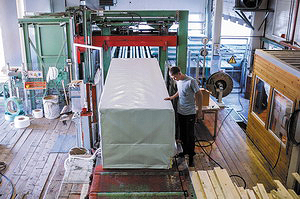
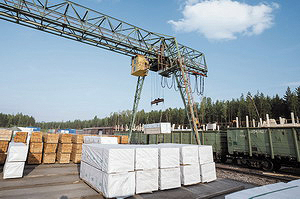
Участок погрузки пиломатериалов «ЛДК Игирма»
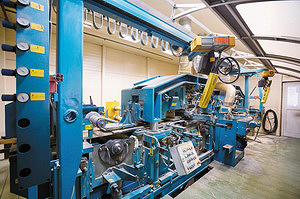
Строгальный станок Ledinek на «ЛДК Игирма»
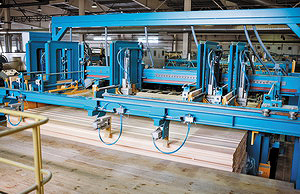
Пакетоформирующая машина Kallfass на «ЛДК Игирма»
Сырье сортируется по породам древесины, диаметру, длине, конусности, кривизне. Каждое бревно проходит перед оператором, который визуально оценивает его, а компьютер считывает размеры, определяет породу и т. д. Бревна движутся по сортировочной линии и падают в определенные карманы в соответствии с заданными параметрами. Основные функции склада круглых лесоматериалов: прием, учет, сортировка и своевременная подача на подающий транспортер лесопильного цеха.
В цехе лесопиления по линии Hekotek отсортированные бревна поступают на подающий стол, а оттуда - на окорочный станок финского производства Valon Kone. В операторской установлены 18 мониторов, которые отражают всю информацию по проходящим через станок бревнам. В соответствии с заданными параметрами выполняется распиловка бревен на немецкой линии Linck. Сортировка центральных и боковых досок ведется на линии Springer (Австрия), после чего пиломатериалы попадают на пакетоформирующую машину того же австрийского производителя. Производительность цеха лесопиления и сортировки сырых пиломатериалов - 63 тыс. м3 в месяц по входящему сырью. Отходы лесопиления идут на отопление предприятия. Сосновые и лиственничные опилки складируют отдельно и используют для производства пеллет на предприятии «Сибирские топливные гранулы».
После цеха лесопиления отсортированные пиломатериалы направляют в сушильный комплекс, состоящий из девяти сушильных камер шведской фирмы WSAB (семь камер периодического действия и две тоннельного типа) и десяти сушильных камер финской фирмы Jartek (восемь сушильных камер маятникового типа и две - тупикового). Общая производительность комплекса в настоящее время составляет 32 тыс. м3.
Высушенная древесина поступает в цех сортировки сухого пиломатериала, где из полуфабрикатов производят готовую продукцию, которая сортируется в соответствии с техническими условиями. Для выполнения этой задачи в цехе установлена линия сортировки досок Springer (Австрия). На выходе линии формируют и готовят к отгрузке пакеты конечной продукции. Производительность цеха составляет 18 тыс. м3 в месяц.
В цехе строжки из высушенных полуфабрикатов производят высококачественные строганные пиломатериалы: бруски, рейки, погонажные изделия. Здесь установлены четырехсторонний строгальный станок фирмы Ledinek (Словения) и линия сортировки-пакетирования Kallfass (Германия). На выходе линии формируют пакеты готовой продукции. Производительность цеха составляет 11 962 м3 в месяц.
Готовую упакованную продукцию отправляют на открытый склад пиломатериалов, который предназначен для хранения сухих упакованных пиломатериалов, его емкость больше 15 тыс. м3. Оттуда пакеты поступают на участок погрузки, который делится на три зоны: погрузки-разгрузки круглых лесоматериалов, погрузки щепы, погрузки готовой продукции в железнодорожные вагоны (с помощью двух кранов ККС-10) и в контейнеры (здесь используется устройство загрузки контейнеров). Пропускная способность участка - до 73 вагонов в сутки.
Отапливает предприятие котельная фирмы Wärtsilä (Финляндия), которая работает на древесных отходах. Она оснащена двумя водогрейными котлами мощностью 10 МВт каждый. Кроме того, на предприятии имеются и вспомогательные подразделения, обеспечивающие бесперебойную и эффективную работу производства. Сюда можно отнести отдел главного механика, осуществляющий техническое обслуживание станков и механизмов предприятия, его сотрудники могут выполнять токарные и сварочные работы на объектах. Отдел главного энергетика осуществляет техническое обслуживание электрических сетей, подстанций и устройств программного обеспечения станков и механизмов. Имеется и автотранспортный цех, обеспечивающий внутреннюю логистику производства, в составе которого 23 единицы техники таких известных марок, как Volvo, Kalmar, Richtacker, Hyundai.
«ТСЛК»
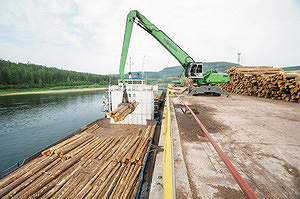
Разгрузка сырья машиной Sennebogen на «ТСЛК»
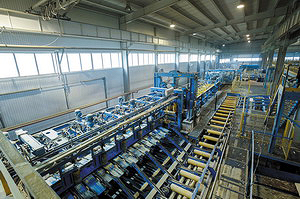
Линия лесопиления EWD на «ТСЛК»
Производственная программа ООО «ТСЛК» рассчитана на годовую переработку круглого леса в объеме 1 млн м3. Круглый лес на предприятие поступает в период навигации баржами по реке Лене к причалу, расположенному на территории завода, зимой - автомобилями. Выгрузка пиловочника из барж осуществляется с помощью колесных погрузчиков Sennebogen 850М, выгрузка из автомобилей и подача ни линию сортировки - лесопогрузчиком Volvo L180E.
На предприятии установлена автоматическая линия сортировки круглого леса фирмы Holtec из 56 сортировочных карманов-накопителей с возможностью развития линии до 70 карманов. Карманы по мере заполнения освобождаются погрузчиком Sennebogen 735М в буферные штабели, расположенные рядом с линией сортировки. При накоплении в штабеле бревен объемом более 50 м3 они загружаются в телеги и перевозятся на буферный склад отсортированного леса, где хранятся до момента пиления. Завод оснащен двумя фрезерно-брусующими группами и двумя фрезерно-профилирующими группами станков.
Отсортированный по группам диаметра пиловочник подвозят со склада к столам подачи и загружают погрузчиком Sennebogen 735М на поперечный цепной транспортер-накопитель линии подачи пиловочника в цех. Каждое бревно проходит через сканирующее устройство. Данные сканирования передаются для обработки на центральный компьютер лесопильной линии. Результаты измерения дают возможность получать данные о геометрических параметрах бревна, в том числе о кривизне, что позволяет в любой момент получать статистику смены, а также определять коэффициент выхода готовой продукции. Кроме того, сканирование дает возможность определить форму бревна, оптимально сориентировать его для процесса обработки и таким образом повысить выход конечной продукции.
Каждое бревно при подаче в цех продольным цепным транспортером проходит через сканирующее устройство. Сканирование дает возможность определить форму бревна и затем оптимально сориентировать его для процесса обработки, что в свою очередь позволяет повысить выход конечной продукции. После позиционирования бревна происходит его двухплоскостное фрезерование на станке FZ5 с целью получения двухкантного бруса. Полученный двухкантный брус при помощи разворотного устройства TKV-Н поворачивают на 90° и подают на фрезерно-брусующий станок FZ5. Во время прохождения бруса через фрезерно-профилирующую группу осуществляется профилирование боковых пиломатериалов при помощи фрез и подрезных пил фрезерно-профилирующего станка FR15S.
После формирования поверхностей боковых пиломатериалов путем фрезерования брус подают на станок DWK T2, на котором выполняют распил боковых пиломатериалов. Конструкция оборудования позволяет отделить боковые пиломатериалы без механических повреждений. Поперечный цепной транспортер передает пиломатериалы на ленточный конвейер, который транспортирует доски на линию сортировки пиломатериалов. Далее двухкантный брус поворачивают на 90°. Как и на станках первой группы фрезерно-профилирующего оборудования, на фрезерно-профилирующих станках FR15S второй группы выполняют фрезерование контура боковых досок.
Спрофилированный брус подают на многопильный станок FR12, на котором осуществляется распил бруса на центральные и боковые пиломатериалы. При помощи отделителя боковых досок пиломатериал передают на поперечный цепной транспортер и далее по ленточному конвейеру на линию сортировки пиломатериалов, центральный пиломатериал по ленточным транспортерам поступает на линию сортировки.
Обрезной пиломатериал передают по ленточному транспортеру на автоматическую линию сортировки пиломатериалов, а рейку направляют в транспортер удаления отходов и затем в дробилку.
Сортировка пиломатериалов ведется на трех линиях, работающих по одному принципу. На третьей линии можно обрабатывать пиломатериал шириной менее 90 мм. Пиломатериал подают на линию сортировки с лесопильных линий при помощи семи ленточных транспортеров, причем конструкция транспортеров позволяет по желанию подавать пиломатериалы с любого ленточного транспортера на любую линию сортировки.
Лесопильный цех оснащен оборудованием сбора и транспортировки отходов, которое включает в себя скребковые транспортеры, вибролотки, барабанную дробилку, сито и др. Все отходы производства собирают и транспортируют к специальным бункерам. В процессе транспортировки происходит их сортировка по фракциям. Кора, технологическая щепа и опилки подаются в бункеры отдельно.
На линии пакетоформирования при формировании плотных пакетов пиломатериалов они выравниваются по вершинному торцу. Измерение длины выполняют ступенчато, с интервалом 300 мм. Между третьим и четвертым слоями вручную укладывают две транспортные прокладки. Плотный пакет размером примерно 1,2 х 1,2 м обвязывают на обвязочном прессе для транспортировки.
Для перевозки сформированных пакетов в сушильные камеры и после сушки в цех сортировки сухих пиломатериалов используют вилочные погрузчики Kalmar DCE160 грузоподъемностью 16 т. Сушильный комплекс состоит из 30 камер фирмы Jartek, средняя вместимость одной камеры - 300 м3 пиломатериалов. Сушильный комплекс и производственные цеха теплом обеспечивает автоматизированная котельная (два котла мощностью 10 МВт каждый) фирмы Polytechnik (Австрия), работающая на отходах производства - коре, щепе и опилках.
Погрузчик доставляет высушенные пакеты пиломатериалов в начало линии сортировки на подающий транспортер. Пакет перемещается в автоматическом режиме на разборочное устройство, которое наклоняется, поднимает его в положение для разборки и разбирает послойно на подающий транспортер. Когда от пакета остается часть высотой примерно 1,0 м, несущие консоли вспомогательного разборочного устройства входят под пакет и продолжают разбирать его. В это же время основное разборочное устройство поднимает следующий пакет для разборки. Сформированный пакет перемещают на роликовый транспортер, где его обвязывают и обжимают на прессах по программе обвязки.
Обвязанные пакеты движутся по транспортеру на упаковочный участок. Упаковочная машина укладывает упаковочный материал на пакет и отрезает его по заданному размеру, после чего оператор укладывает и закрепляет упаковочный материал на пакете. Затем пакет перемещается на обвязочный автомат, на котором выполняется обвязка поверх упаковки. Упакованные пакеты пиломатериалов вывозят погрузчиком на склад готовой продукции, откуда вилочными погрузчиками Kalmar DCE70-10 грузоподъемностью 10 т, подвозят к ж.-д. тупикам, где грузят в вагоны с помощью погрузчиков Sennebogen 735М, укомплектованных автоматическим захватом для пакетов пиломатериалов. Погрузка пиломатериалов в контейнеры осуществляется погрузчиком-ричстакером DRF 450-65S5 грузоподъемностью 45 т.
«Сибирские топливные гранулы»
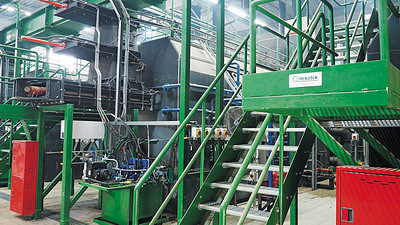
Завод по производству пеллет
С целью эффективной утилизации древесных отходов, образующихся на описанных выше лесопильных предприятиях, в 2016 году был пущен завод по производству пеллет «Сибирские топливные гранулы».
Он оборудован прессами голландского производителя CPM. Генеральным поставщиком оборудования (включая поставку системы аспирации) стала эстонская компания Hekotek. Древесные отходы сначала попадают на автоматические линии сушки на базе барабанных сушилок Hekotek, проходя через которые сырье сушится, а потом по транспортерам поступает в прессы фирмы CPM. Всего на предприятии установлено пять линий по производству пеллет. Производительность каждой линии 5 т/ч. Готовая продукция поступает на загрузку в биг-бэги, контейнеры и крытые вагоны. Общая производительность завода «Сибирские топливные гранулы» составляет 16,5 тыс. т в месяц, или 200 тыс. т в год.
О кадрах
Сегодня на «СП СЭЛ-Тайрику» работает 360 человек, на «ЛДК Игирма» - 473, на «Сибирских топливных гранулах» - 44, на «ТСЛК» - 567, на лесозаготовках занято около 1300 человек, в штате «СЭЛ-Транс» 14, «СЭЛ-Трейд» - 29, в управляющей компании «РусЛесГрупп» - 87 человек. И 95% работников всех заводов ГК в Иркутской области - это местные жители.
«Наши предприятия - это хорошая кузница кадров. Через систему наставничества происходит процесс обучения и передачи опыта. По сути, нет текучки кадров, - говорит управляющий директор «ЛДК Игирма» и «СЭЛ-Тайрику» Виктор Мукорез. - Мы социально ориентированное предприятие, предлагаем достойные условия и оплату труда, расширенный социальный пакет, адресно помогаем, например, молодым семьям. На рождение ребенка выделяем средства, на Новый год дарим подарки детям сотрудников. Несмотря на тяжелую кризисную ситуацию в экономике в последние годы, мы индексируем зарплату: в прошлом году было принято решение о повышении заработной платы на 10-20% в зависимости от разных факторов.
В 2015 году мы за свой счет построили тренажерный зал. К слову, наши спортсмены активно участвуют в летних и зимних поселковых спортивных играх, да и сами мы периодически проводим соревнования и спортивные мероприятия. Например, традиционно на 9 мая организуем легкоатлетический кросс. А еще периодически устраиваем спартакиады, в которых участвуют коллективы наших заводов, иногда к нам присоединяются и другие предприятия. Конечно же, проводятся и корпоративные праздники: например, в этом году в преддверии Дня лесника в поселковом Доме культуры была организована дискотека для сотрудников. А еще у ГК "Русская Лесная Группа" есть корпоративная газета, в которой рассказывается и о производственных успехах наших сотрудников, и о ярких личностях, и о хобби наших сотрудников, и так далее. Мы готовы помогать нашим работникам, люди это ценят и отвечают хорошим трудом. Нужно, чтобы люди чувствовали личную ответственность и заинтересованность, понимали, что это их родное предприятие. У нас отличный коллектив!»
Об участии в жизни поселка
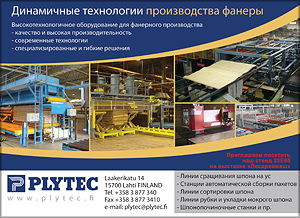
Plytec. Оборудование для производства фанеры
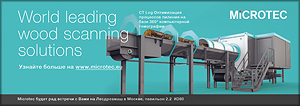
Microtec. Измерительное оборудования для
лесопильных заводов
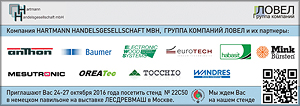
Ловел (Hartmann). Деревообрабатывающее
оборудование и запчасти
Конечно же, предприятия ГК «Русская Лесная Группа» активно участвуют в жизни поселка. С руководством области было подписано соглашение о социально-экономическом партнерстве. Предприятия группы по мере выхода на проектные мощности оказывают в том числе и материальную помощь поселку - в этом году более 6 млн руб. было выделено на ремонт детских садов, школ, оказание адресной помощи пенсионерам. Почти заново был построен спортивный комплекс для всех жителей. Предприятие гарантирует местному населению помощь в виде пиломатериалов, дров. Кроме того, уже много лет предприятия группы содержат все дороги в поселке, проводят своими силами и за свой счет их чистку, грейдирование и т. п.
О планах по развитию
«Сейчас заводы группы находятся на довольно высоком уровне развития, - говорит г-н Мукорез. - Наша основная задача на сегодня - это снижение себестоимости производимой продукции. Понятно, когда стоимость продукции на рынках падает (особенно в нынешнее непростое время), чтобы остаться на плаву, нужно максимально снизить долю себестоимости в цене товара. И второй момент - это переработка отходов. Мы только выходим на рынок пеллет, только изучаем этот процесс, но, в принципе, неплохо решаем задачу. Мы одна из немногих компаний в России, которая, пройдя международную аттестацию, получила сертификаты, подтверждающие высокое качество пеллет. Получены сертификаты FSC, EN Plus и SBP.
В наших ближайших планах обеспечение утилизации отходов на 100% и выход на полную мощность производства. Ну и, конечно же, повышение производительности предприятий за счет внутренних резервов - потенциал у заводов для этого есть. Сейчас в отрасли наблюдается тенденция сокращения числа предприятий малого бизнеса. Небольшие производители вынуждены уходить с рынка или входить в состав крупных корпораций, которые могут конкурировать за счет сокращения издержек производства. Рынок очень сложный. Сырьевые базы уходят все дальше и дальше от производств - доступность сырья падает, само сырье дорожает, из-за этого себестоимость продукции растет. Так что легкой жизни не будет, но мы понимаем это и будем решать возникающие вопросы. Думаю, что справимся. У ГК "Русская Лесная Группа" есть все возможности, для того чтобы оставаться на вершине».
Подготовила Ольга РЯБИНИНА