Мебельный холдинг «Ангстрем»: точность, профессионализм и ответственность
Перефразируя крылатое выражение, можно сказать: «Точность - вежливость профессионалов», - и в бизнесе она не менее важна, чем, например, высокое качество продукции. Именно так понимают значение точности в отношениях с деловыми партнерами, заказчиками и потребителями в группе компаний «Ангстрем» - крупном российском производителе корпусной мебели для дома.
Компания «Ангстрем» основана в Воронеже в 1991 году. За четверть века она прошла путь от небольшого производства детских тренажеров-«прыгунков» до одного из крупнейших производителей мебели в России. По оценкам немецкой инжиниринговой компании Shuller Business Solution, сейчас это одно из самых эффективных мебельных производств России, а региональная розничная сеть «Ангстрем» входит в пятерку российских лидеров по продаже мебельной продукции.
«Ангстрем» сегодня - это современное предприятие, у которого больше чем на 40 тыс. м2 выстроены технологические цепочки производственных подразделений, оснащенных высокопроизводительным оборудованием (в скором времени эти площади расширятся за счет ввода новой площадки в индустриальном парке «Масловский», где сейчас располагается логистический центр компании и будут развернуты цеха).
В штате ГК «Ангстрем» более 2000 сотрудников, у компании более 200 торговых точек больше чем в 100 городах России и больше 200 оптовых партнеров во всех регионах России, Казахстане и странах Балтии.
Мебельный холдинг «Ангстрем» производит продукцию под двумя брендами в разных ценовых сегментах, чтобы точно соответствовать потребностям разных категорий покупателей. ТМ «Ангстрем» - первый бренд компании, созданный почти одновременно с ее появлением. А в 2012 году из продуктовой линейки «Ангстрема» специально для оптовых покупателей были отобраны модели недорогой качественной мебели, которая выпускалась под маркой Hitline (сейчас эта линейка разрабатывается и производится самостоятельно и исключительно под этим брендом). Под обеими торговыми марками выпускается мебель как в современных, так и в классическом стилях. Основные товарные группы: гостиные, спальни, прихожие, библиотеки и детские; под ТМ «Ангстрем» продается мебель высокого ценового сегмента, под ТМ Hitline - среднего и невысокого.
Производство корпусной мебели «Ангстрем» разнесено по двум площадкам. Цеха деревообработки и изготовления фасадов работают на той территории, откуда начала свою историю мебельная фабрика. Мебельные каркасы изготавливают на построенной в 2007 году площадке. Именно с нее мы и начнем обзор производства «Ангстрем».
Фабрика по изготовлению мебельных каркасов
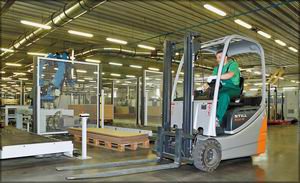
Электропогрузчик Still (Германия)
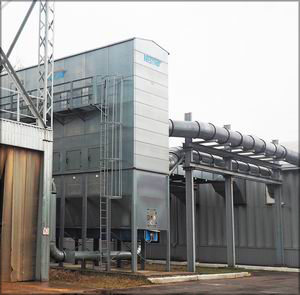
Система аспирации Nestro (Германия)
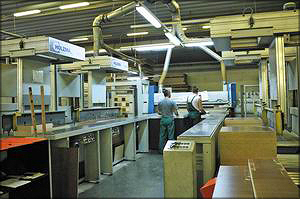
Автоматический форматно-раскроечный центр Holzma
HCL 11/38/22 Profiline (Германия)
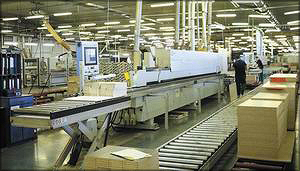
Кромкооблицовочный станок Homag Optimat KAL 310
(Германия)
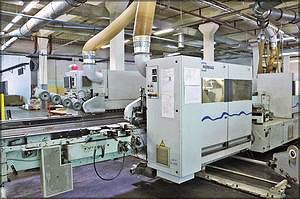
Автоматизированная кромкооблицовочная линия Homag
KAL526+KAL526 Profiline с системой Bargstedt
(Германия)
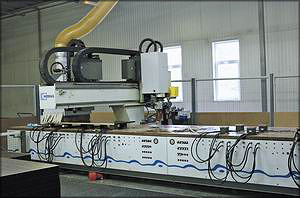
Деревообрабатывающий центр Homag BAZ 32/50/G
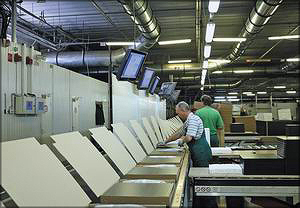
Автоматическая упаковочная линия Ligmatech VKV 700
Optimat (Германия)
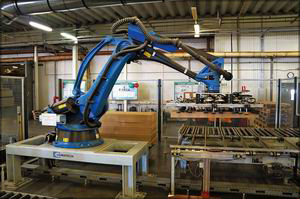
Робот-манипулятор Kuka (Германия)

Присадочный центр с ЧПУ Weeke ВНТ-500
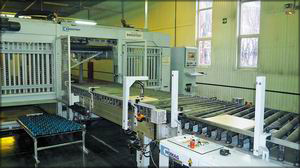
Автоматизированная кромкооблицовочная линия Homag
KAL526+KAL526 profiline (Германия) с системой
Bargstedt (Германия)
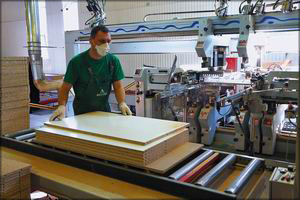
Cверлильный станок проходного типа Weeke BST 500
с подъёмными столами
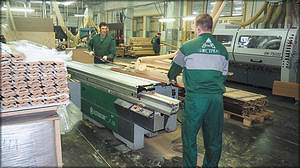
Форматно-раскроечный станок Altendorf F45 (Германия).
Цех деревобработки
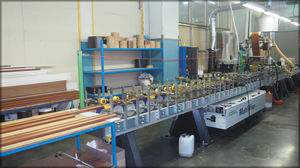
Профилеоблицовочная установка Duspohl MultiWrap
400S (Германия). Цех деревообработки
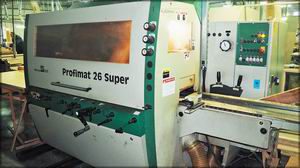
Четырехсторонний станок Weinig Profimat 26 Super
(Германия). Цех деревообработки
Арочный тип производственных помещений площадки по изготовлению корпусов мебели позволил выстроить технологическую цепочку в линейку (в отличие от самой первой площадки фабрики, где оборудование расположено на разных этажах). Помещение хорошо отапливается, причем за счет грамотного проектирования и в теплый, и в холодный период в производственных помещениях и в помещении склада поддерживаются необходимые температурные режимы. Централизованная система аспирации производства немецкой компании Nestro очищает воздух в помещениях и удаляет из них древесную пыль. Отходы деревообработки - опилки и обрезки древесных материалов используются в качестве топлива для сжигания в топках твердотопливных котлов Uniconfort (Италия) и Kohlbach (Австрия), которые вырабатывают тепловую энергию для отопления помещений предприятия (логистический центр и фабрика-1).
Общая площадь складских помещений для хранения материалов, комплектующих и готовой продукции - 5,5 тыс. м2. В качестве основного материала для производства корпусов используются ЛДСП толщиной 16 и 22 мм, основной поставщик которых - компания Egger. Он давний и надежный партнер фабрики, по поводу качества продукции которого никогда не возникает сомнений. Кроме компании Egger на «Ангстрем» поставляют свою продукцию такие производители плит, как «Увадрев-Холдинг» и Кronostar. Для изготовления задних стенок мебели, доньев ящиков и других элементов производитель «Изоплит» поставляет ДВП и плиты HDF.
Кромочный материал закупается у компании Egger (производство в Турции), Bramek (импортер из Китая), занимающейся поставкой кантов и кромки ПВХ на российский рынок, компании «Едличка» (Россия).
Все необходимые материалы доставляют на фабрику автотранспортом, со склада их перемещают в цех на электропогрузчиках фирмы Still (Германия).
Производственные подразделения по выпуску корпусов гостиных, спален, библиотек, детских располагаются на площади 8300 м2. Основным поставщиком оборудования для фабрики выступила Homag Group (Германия). По словам руководства компании, станки и линии именно этого машиностроительного концерна в наибольшей степени отвечали требованиям, которые были поставлены перед поставщиками. Специалисты Homag помогли спланировать производство, представители Homag Russland регулярно посещают фабрику для диагностики оборудования, его модернизации и ремонта в случае необходимости. В процессе развития фабрики и освоения новых видов продукции появляется необходимость в дополнительных опциях, и специалисты Homag разрабатывают их и устанавливают на имеющееся оборудование, обучают станочников фабрики работе на модернизированной технике.
На всех площадках «Ангстрема» задействовано оборудование еще одного известного европейского машиностроительного концерна - Altendorf. Менеджмент фабрики объясняет выбор в пользу форматно-раскроечных центров этой немецкой компании их надежностью и работоспособностью.
Почти все используемое на фабрике оборудование приобретено и установлено в период с 2005 по 2012 год. Для обработки древесных материалов используется режущий инструмент немецкой компании Leuco (пилы, фрезы, сверла) твердосплавный и с алмазным покрытием, у которого, по словам сотрудников «Ангстрема», оптимальное соотношение цены и качества. Твердосплавный инструмент на фабрике затачивают на станке Vollmer СХ100 (Германия), алмазный инструмент в сервисном центре Leuco в Москве.
Процесс изготовления корпуса начинается с раскроя плитных материалов, для чего используют два раскроечных центра Homag, позволяющих переработать за смену 3,5-4 тыс. м2 ДСП 16 мм. На форматно-раскроечном центре Holzma HPL 11 раскраивают плитные материалы - ДСП, ДВП и HDF. Его производительность позволяет обрабатывать до 1,5 тыс. м2 плит в смену. На полностью автоматическом форматно-раскроечном центре Holzma HCL 11/38/22 Profiline выполняется раскрой ЛДСП (его производительность - до 3,5 тыс. м в смену).
Вот как работает «автомат»: размеры деталей задаются или загружаются из конструкторской программы списком на рабочем месте технолога и после обработки программой оптимизации CutRite передаются на станок, где оператор начинает процесс раскроя, который выполняется в полностью автоматическом режиме. Оператор контролирует работу оборудования и по выходу первых раскроенных деталей проверяет их параметры на соответствие заданным параметрам. На станке Holzma HCL 11/38/22 Profiline можно одновременно выполнять раскрой от одного до шести листов плиты толщиной 16 мм или от одного до четырех листов толщиной 22 мм. Распиленные детали отправляют в так называемый буфер, где они ожидают отправки для дальнейшей обработки, причем буфер никогда не переполняется - производственная линия была спроектирована таким образом, чтобы производительность двух пильных центров соответствовала производительности кромкооблицовочного участка, поэтому заготовки оперативно отправляются на следующий участок. Некондиционные обрезки плит и другие древесные отходы измельчаются на дробилке Weima D 74360 Ilsfeld / Heilbronn (Германия) и поступают в бункер-накопитель аспирационной установки.
Заготовки из промежуточного буфера поступают на участок кромкооблицовки. Станочный парк этого производственного подразделения состоит из односторонних станков и четырехсторонней автоматизированной линии. Детали поступают на него в соответствии с техническим заданием. На двух кромкооблицовочных станках Homag Optimat KAL 310, оборудованных подъемными столами, обрабатываются кромки деталей и одновременно выполняется пазование. Детали, которые необходимо облицевать кромкой с четырех сторон, отправляются на автоматизированную кромкооблицовочную линию Homag KAL526+KAL526 profiline. На этой линии загрузка, разгрузка и штабелирование деталей осуществляются при помощи системы Bargstedt (Homag Group), что позволяет значительно сократить время на выполнении этих операций и обеспечивает полную автоматизацию процесса.
После кромления детали попадают в буфер облицованных деталей, откуда поступают на операции присадки (сверление отверстий). Общая производительность участка - 9,5-10 тыс. деталей за смену.
Для обработки деталей здесь установлены четыре станка в комплексе с линией автоматизации Bargstedt. На проходном сверлильном станке Weeke BST 750 с автоматической загрузкой и выгрузкой деталей обрабатывают крупные серии заготовок (от 100 шт.). За один проход здесь можно сделать сотни отверстий. Станок оснащен встроенными щетками Wandres для очистки деталей по двум плоскостям от пыли, образующейся при сверлении и на предыдущих операциях. У станка проходного типа Weeke BST 500, который также предназначен для обработки больших партий деталей, возможности несколько скромнее, на нем можно за один проход выполнить в деталях меньше отверстий, чем на Weeke BST 750, поэтому на нем сверлят детали небольших размеров. Эти станки довольно сложно переналаживать, поэтому они эффективны при обработке больших партий деталей.
Для работы со средними сериями (от 50 до 100 деталей) используется присадочный центр проходного типа Weeke BHT 500 Optimat. Он быстро перенастраивается: при активации определенной программы станок сам выбирает в магазине инструмента нужное сверло и запускает процесс сверления. На этом оборудовании также установлены для очистки деталей выходящих из линий от опилок щетки Wandres. Участок также оснащен сверлильным центром с ЧПУ Weeke BHX 500, который используется для обработки небольших партий деталей (до 50 шт.). Он не нуждается в перенастройке, поскольку работает в автоматическом режиме по программам, которые индивидуальны для каждой детали. Карта присадки выбирается из перечня, содержащегося в памяти ЧПУ. С целью дополнительного контроля параметров детали специальное устройство сверлильного центра BHX 500 предварительно измеряет длину детали и сопоставляет полученные данные с параметрами образа заготовки из программы, загруженной в память ЧПУ.
На универсальных деревообрабатывающих центрах Homag BAZ 32/50/G Optimat и Homag BAZ 222/40/K можно выполнять множество операций: раскрой, пазование, сверление, фрезерование и облицовку кромок криволинейных деталей. С этого станка детали мебели могут отправляться прямо на участок упаковки.
Параллельно с основным потоком изготовления серийной продукции работа идет на участке изготовления серий деталей с мелкими размерами и единичных изделий. Здесь на станке Altendorf F45CE (Германия) осуществляется раскрой небольших деталей. В целях достижения максимально полезного выхода из полос плит, оставшихся после основного раскроя, на этом станке получают цокольные планки, ящичные элементы и элементы декора. Таким образом минимизируются отходы плитного материла.
На автоматическом кромкооблицовочном станке Homag Optimat KL 79 выполняется облицовка прямых кромок, а на станке Stemas (Италия) облицовываются небольшие детали и профили с торца любой конфигурации.
Деревообрабатывающий центр с ЧПУ Weeke Optimat BHC 550, установленный на этом участке, выполняет функции сверления и пазования. Здесь же эксплуатируются два сверлильно-присадочных станка Vitap Forma 85 (Италия).
Детали, прошедшие все стадии технологической цепочки, перед последним этапом - упаковкой проходят контрольную сборку. Основная задача контрольной сборки - подтвердить, что все операции выполнены правильно, с необходимыми требованиями и высоким качеством. Поскольку продукция выпускается серийная, то из стопы выборочно собирают одно изделие. Здесь же проверяются наличие и комплектность фурнитуры (короб с фурнитурой формируется на другой производственной площадке), а также правильность изготовления картонного короба для деталей. Контрольный сборщик укладывает изделие в упаковку и проверяет, правильно ли все закрывается. И только затем в специальном журнале делается запись, подтверждающая, что партия изделий готова к упаковке. Цикл изготовления каркаса серийного изделия занимает четыре смены.
Кроме деревообрабатывающего оборудования в цехе имеется специальный автоматический станок Packsize ЕМ6 (Швеция) для изготовления из гофрокартона упаковки разного формата. Сформированные пакеты по конвейеру попадают на автоматическую упаковочную машину Ligmatech VKV 700 Optimat (Homag Group), после чего робот-манипулятор Kuka (Германия) складывает их на поддон с готовой продукцией и с помощью специального щупа измеряет толщину пакета, а датчики контролируют размеры пакета и определяют его вес. Если робот выявит какое-то несоответствие, он остановится и просигнализирует оператору об ошибке. За смену упаковывается 1800-2200 пакетов. Поддоны с готовой продукцией перемещаются в зону промежуточного хранения (на склад), откуда автотранспортом вывозятся в логистический центр «Ангстрем», расположенный за городом, а оттуда выполненные заказы отправляются клиентам.
Отбракованные детали направляют в изолятор брака, чтобы они не попали в готовую продукцию. Специальная комиссия (инженер ОК, инженер-технолог, начальник цеха) на основании маршрутных листов и бланков брака выясняет, почему произошел брак; если выявлена вина поставщика материалов, то деталь направляется ему для ознакомления и принятия меры, если по вине производства, то заготовки отправляют на доработку на участок изготовления единичных деталей, когда подобная доработка возможна.
Производство фасадов и другие подразделения
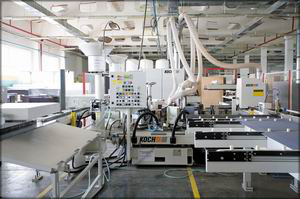
Универсальный двусторонний станок Koch SBD 45
(Германия). Цех изготовления фасадов
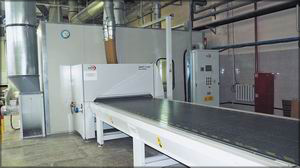
Линия отделки Easy 2000D Cefla (Италия).
Покрасочный цех
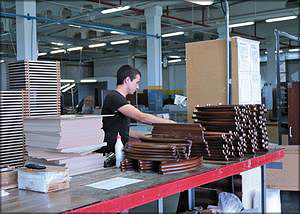
Участок сборки фасадов
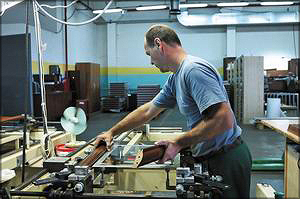
Вайма для сборки фасадов V/Grum-Snhwensen
(Германия)
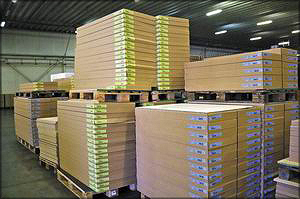
Упакованная продукция
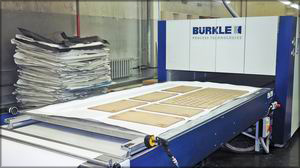
Пресс Burkle (Германия). Цех производства фасадов
с покрытием из пленки ПВХ
Складские помещения фабрики по производству фасадов мебели занимают 4,9 тыс. м2. Здесь хранятся материалы, используемые при производстве мебели, в том числе профильные. На фабрике очень большая номенклатура профилей - одного из основных элементов производства мебели, это сотни разновидностей разных цветов и конфигураций. На этой площадке расположен цех деревообработки, где изготавливается определенная часть необходимого профиля, но используется продукция и от поставщиков. На складе промежуточного хранения перед отправкой в логистический центр хранятся элементы готовой продукции: фасады, детали мягкой мебели, стекло.
Площадь производственных помещений фабрики - 12,5 тыс. м2, на которой расположены участки деревообработки, отделки, изготовления фасадов (отдельное подразделение - участок изготовления фасадов, покрытых пленкой ПВХ), стеклообработки, мягкой мебели. Особое место на этой площадке занимает динамически развивающееся производство по изготовлению мебели по индивидуальным заказам.
Еще 15 лет назад все производство «Ангстрема» располагалось там, где сейчас находится один участок деревообработки. Здесь изготавливают заготовки и детали для кроватей и пуфиков, для фасадов, а также мебельный профиль. В качестве материала для производства деталей используются древесина сосны и южного бука, плитные материалы.
Плитный материал в зависимости от размеров и техзадания раскраивается на пильном центре Holzma НРР81 и двух форматно-раскроечных станках Altendorf F45. Производство профиля осуществляется на четырехстороннем станке Nortec GN - 7S23U (Тайвань): проходя через станок, напиленные в размер заготовки превращаются в готовый профиль с пазами, который затем окутывается специальной бумагой или пленкой на профилеоблицовочной установке Duspohl MultiWrap 400S (Германия), декорируется в цвет в соответствии с дизайнерским решением. На станке для продольного деления пленки Barberan TF-1300 пленку нарезают по ширине.
Часть элементов будущей мебели изготавливют на четырехстороннем станке Weinig Profimat 26 Super (Германия): черновые мебельные заготовки загружают в станок, и он их калибрует до заданного сечения. Изделия необходимого размера отправляют на дальнейшую обработку: торцовку, фрезеровку, присадку, шлифовку и сборку, если она предусмотрена в рамках техзадания цеха деревообработки. На ленточнопильном станке Griggio SNA-800 детали дорабатывают по шаблону и подготавливают для фрезеровки на копировально-фрезерном станке Pade (Италия). На вертикальных шлифовальных станках фигурные детали обрабатываются шлифовальными кругами. Присадка выполняется на трех сверлильно-присадочных станках Vitap (Италия). Обработанные детали фасадов и профили при необходимости отправляют в покрасочный цех и отгружают в цех сборки фасадов. Мебельные заготовки и собранные изделия, например, пуфики, также при необходимости доставляют сначала в покрасочный цех, а затем в цех обшивки.
Основным поставщиком оборудования для работы с ЛКМ является итальянский производитель Cefla - давний и проверенный партнер «Ангстрема».
Покрасочный цех фабрики оборудован двумя линиями отделки производства этой компании. Распылительный автомат с двумя качающимися каретками Cefla Easy 2000D позволяет обрабатывать любые декоративные элементы из профиля, древесины и стекла. На изделия наносится несколько слоев покрытия - изолирующий, грунтовочный, после чего оно подвергается сушке и шлифовке, затем наносится финишное покрытие. Кроме того, в цехе есть краскораспылительная кабина Koimpex CVAPE60 (Италия). В зависимости от типа лакокрасочного покрытия (на фабрике используют и лаки НЦ, и полиуретановые, и акриловые и др.) изделие выдерживается на этажерках в сушильных камерах Koimpex. На линии отделки Easy 2000D c вертикальной сушильной камерой FV3+TR (производитель - компания Cefla) детали в автоматическом режиме проходят все необходимые этапы: очистку от пыли, наложение изолянта, грунтовку, причем выдерживать изделия не требуется (они проходят выдержку в процессе выполнения названных выше операций), и на выходе из камеры детали можно сразу отправлять на шлифование. Шлифовка перед финишным нанесением лака в большинстве случаев на фабрике выполняется вручную, поскольку зачастую у деталей настолько глубокие выемки и такие фигурные углубления, которые невозможно обработать ни на одном станке. Машинной шлифовке на шлифовальном станке Cefla Delle Vedove 200/6 подвергаются детали, изготовленные из погонажа. На линии Cefla FlexiSprey 36QS для нанесения патины деревянные детали искусственно состариваются, а потом патина вручную растирается шерстью так, чтобы она осталась только на определенных местах поверхности изделия. После отделки лаком деталь приобретает окончательный вид.
На фабрике «Ангстрем» для изготовления мебели широко используют остекленные фасады. Сначала стекло режется в размер, затем прямолинейная кромка обрабатывается по периметру на двух вертикально-шлифовальных станках Bottero Victralux 110FC и 111F (Италия), криволинейная - на станке СКС-2Т (Россия), а необходимые отверстия в стекле сверлят на станке Enkong ZJ 130 (Китай). После проверки качества операторами и итоговой протирки стекла складывают на пирамиды и перемещают в цех сборки фасадов или на склад готовой продукции - в зависимости от назначения изделия. Установлен в цехе и станок для декорирования стекла пленками - корейский рулонный ламинатор GMP Excelam m1600 combi. Часть стекол на производстве красится, но покраска стекла - очень сложный процесс, сопровождающийся большим числом отбраковок, поэтому было освоено оклеивание стекол пленками. Только специалист может визуально отличить, каким именно образом декорировано стекло. Кроме того, для декорирования стекол используется автоматическая пескоструйная камера MHG Glasmaster 1500 (Германия). Руководство фабрики отмечает, что возможности станочного парка цеха стеклообработки обеспечивают высокое качество операций, но сказываются на производительности. Поэтому планируется его дооснащение в соответствии с растущими объемами использования стекла в мебели.
Технологическая цепочка изготовления мебельных фасадов начинается с участка по работе с плитными материалами. Основной поставщик оборудования здесь тоже Homag Group. Плиты раскраивают на пильном центре Holzma Profi HPL 530/38/22 и форматно-раскроечном станке Altendorf F45. Кромкооблицовка выполняется на одностороннем станке Homag Profi KAL 310/9/A3 и двустороннем Homag Optimat KF 26/10/A6/25. Для фрезерования, пазования и присадки будущих фасадов используют: обрабатывающий центр Homag Optimat BAZ 222/60/K, обрабатывающий центр с ЧПУ Weeke Venture 211 220M, сверлильный станок Weeke BST 750 (все - Homag Group), сверлильно-присадочный станок Vitap Forma 85 (Италия) и сверлильный станок Hirzt Livra (Италия). Здесь же обкатывают плиты по периметру для фасадов под пленку ПВХ. После того как заготовки для будущего фасада готовы, они поступают на участок сборки, где к ним прикрепляют профили.
Для изготовления рамочных фасадов профиль из цеха деревообработки или со склада на паллетах доставляется в цех производства фасадов. Для начала его раскраивают при помощи маятниковой пилы Virutex TM33W (Испания) под разными углами на декоративные элементы и мелкие детали. Для изготовления рамки используется станок-автомат Koch Sprint multi (Германия), на котором распиливают профиль в нужный размер, сверлят технологические отверстия, впрыскивают клей и забивают шканты. Универсальный двусторонний станок Koch SBD 45 непрерывного действия для опиловки, сверления, впрыска клея и забивки шкантов с вращающимися рабочими станциями выполняет те же функции, но на более крупных деталях, может начинать работать с сырья - хлыста. И еще одно отличие этих станков: в первом предусмотрено нижнее позиционирование, что обеспечивает идеальную заднюю часть рамки фасада, второй станок прижимает деталь сверху, что гарантирует идеальную поверхность лицевой части заготовки.
После раскроя некоторые торцы профилей не облицовывают кромкой, а подвергают тиснению: на станке торцевого тиснения РЕ-500-100 фирмы Gierlich PE-500 KDF Kurz (Германия) к заготовке с нанесенным на нее клеем с обратной стороны прижимают кромочный материал - фольгу, которую припечатывают к поверхности торца, а по краям излишки материала просто отламывают, так как он очень тонкий. Таким образом, профиль декорируется с торцов и защищается от повреждений. В процессе изготовления рамочных фасадов используют сверлильно-присадочные станки Xettich ВММ 3-6 NH (Германия), BM 8FS и F65-4J-1C, сверлильные станки Uniholz Double Eagle (Италия), Detel Dual 21 (Словения) и Hitachi В16 RM (Япония), а также станок сверлильный и шкантозабивной Koch Sprint-PTP-2/2500.
Технологий сборки фасадов несколько. Есть технология сборки псевдорамочного фасада. С виду он напоминает раму, но на самом деле на плиту наклеивается аппликация. Еще один вариант сборки псевдорамочного фасада: сначала собирается рама, которая затем целиком наклеивается на фасад из ДСП. Качество фасада зависит прежде всего от профессионализма сборщика. При сборке все детали фасадов проходят неоднократный контроль обрабатывающих их лиц, потому что даже мелкие недочеты, допущенные при изготовлении фасадной части мебели, небольшие дефекты могут вызвать массу неприятностей. Именно поэтому на фабрике не стремятся механизировать этот процесс.
Участок стандартного изготовления рамочного фасада оснащен двумя ваймами для сборки фасадов V/Grum-Snhwensen (Германия).
В отличие от других производств «Ангстрема», где организована централизованная система аспирации, на участке производства фасадов установлена местная аспирация отечественного производителя «Консар». Связано это с планами компании по переносу производства фасадов на новую площадку, где будут заново спроектированы как производственные линии, так и коммуникации централизованной аспирации.
Основное оборудование, установленное в цехе производства фасадов с покрытием из пленки ПВХ, - это пресс Burkle (Германия) для покрытия гладких и объемных поверхностей деталей из плиты MDF термопластичными пленкам. Сначала выравнивают поверхность детали, с нее удаляют пыль, потом наносят клей, далее разматывается пленка (пресс оснащен устройством для обеспечения антистатики, чтобы на пленку ничего не налипало и она не притягивала пыль). Стол с деталями накрывается пленкой ПВХ, ее отрезают в необходимый размер, вакуумом убирается воздух из-под пленки, и детали загружаются в пресс при определенной температуре и на заданное программой время. Задействованы два рабочих стола - пока один заходит в пресс и происходит технологическая выдержка, на втором столе готовится к обработке очередной фасад. Таким образом изготавливают фасады с покрытием «высокий глянец» (в том числе черного и белого цвета - из числа самых сложных декоров). Этим очень гордятся на фабрике, поскольку не каждый производитель, в том числе и производитель фасадов, может добиться высочайшего качества подобных изделий. Вместе с основной пленкой на фасад наносится защитная, которая снимается только при сборке мебели у клиента.
Мягкую мебель на «Ангстреме» не производят, но есть отдельный цех, в котором изготавливают мягкие детали кроватей и пуфы. Из цеха деревообработки сюда приходят заготовки ЛДСП, ДВП, сосновый брус - материалы, из которых изготавливают каркасы. С использованием пневмопистолетов, скоб, разных крепежных элементов собирают каркасы и изголовья кроватей и в собранном виде передают на участок оклейки. Мягкие элементы кроватей изготавливают из поролона и синтепона, а спанбонд используется для того, чтобы на них легко одевались чехлы, которые кроят здесь же, рядом. На специальные столы в рулонах поступает ткань, из которой делают настил (максимум 30 слоев), при помощи лекала и электрических ножниц вырезают раскройки деталей, которые поступают на швейный участок. Cшитые чехлы отправляют на участок обивки, где их соединяют с каркасами, и на выходе получается готовое изделие. Каркасы пуфов поступают в цех мягкой мебели уже собранными и покрашенными и там оклеиваются мягкими элементами и обшиваются. С участка обивки готовые изделия отправляют на упаковку и отгружают на склад.
Производство мебели по индивидуальному заказу - это одно из наиболее активно развивающихся направлений работы фабрики «Ангстрем». Площадь цеха - 1300 м2. Для увеличения объемов заказов руководство предприятия открывает все больше точек продаж, а для обеспечения выпуска подобной мебели активно развивает цех производства нестандартной мебели - по индивидуальным заказам.
Многие операции, связанные с производством индивидуальной мебели, выполняют на серийном оборудовании тех цехов, где изготавливается серийная мебель. А часть технологических операций позволяет реализовывать оборудование, которым укомплектован цех. Раскрой листового материала выполняется на форматно-раскроечном станке Altendorf F45 ELMO-III, кромкооблицовка - на станках Biesse Roxyl 5,5 (Biesse, Италия) и Brandt Optimat KTD 720 (Homag Group), присадка отверстий и фрезерование - на обрабатывающем центре с ЧПУ Biesse Rover и сверлильных станках Vitap Forma 63Н и Dual. Кроме того, для раскроя профиля из плиты MDF имеются четыре маятниковые торцовочные пилы Virutex ТS 33W и маятниковая пила Dewalt. Цех активно развивается, уже в ближайшее время будет дооснащаться, сейчас ведутся переговоры с представителями компании Biesse - оборудование этой компании, по мнению руководства фабрики, больше всего подходит для производства мебели небольших серий и по индивидуальным заказам.
Кроме производства фасадов и индивидуальной мебели на этой площадке фабрики «Ангстрем» есть другие подразделения. Здесь расположен участок экспериментальной мебели, где проходят проверку новые образцы продукции и обкатываются новые технологии. Именно здесь собирают новые экземпляры мебели перед запуском в серийное производство. И здесь принимается решение: увидит свет новая серия или продукт отправится на доработку.
В основном фурнитуру на «Ангстрем» поставляет фирма Hettich (Германия). Фурнитура приходит на производство россыпью и здесь, на участке комплектации, составляются комплекты необходимых для той или иной мебели ручек, защелок, кнопок, петель, полочек и прочего, которые расфасовывают по пакетам или коробам согласно ведомости комплектации. На каждый пакет или короб наклеивают этикетку с указанием содержимого, и отсюда они попадают в пакет с основным продуктом (деталями и элементами мебели). Правильность комплектации проверяют на этапе контрольной сборки.
Гарантия качества
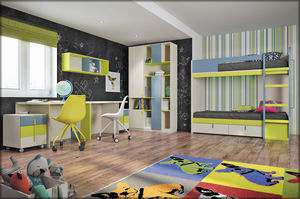
Детская «Кеноша»
Вопросам качества на фабриках «Ангстрема» уделяется огромное внимание, и тут есть чем гордиться. Производство корпусов - это полностью автоматизированный процесс, и во время обработки деталь невозможно контролировать визуально. На предмет отсутствия дефектов изделие проверяется во время контрольной сборки, и после, на этапе комплектования, идет индивидуальный осмотр каждой детали. В течение одной рабочей смены упаковывается около 2 тыс. пакетов готовой продукции; если учесть, что в каждый пакет входит не менее четырех деталей, то станет ясно, что в смену выпускается почти 8 тыс. деталей. Рекламации по вине предприятия приходят на 10-12 деталей в месяц. При изготовлении фасадов в основном осуществляется визуальный контроль на нескольких этапах производства, отдельные детали проходят проверку качества почти десятка людей, отвечающих за ту или иную операцию. Здесь принцип такой: если ты пропустил какой-то дефект с предыдущей операции и взял деталь в работу, значит дефект твой. Некоторые детали проходят до 10 раз через разные руки от начала до конца. Конечно, человеческий фактор никто не отменял, но рабочие мотивированы не пропустить брак, потому что в маршрутной карте перемещение детали по технологической цепочке отражено полностью, и можно отследить, на каком этапе и по чьей вине произошел сбой. Эти карты хранятся в течение трех лет после отгрузки заказа клиенту.
Мебель «Ангстрем» для ванн и кухонь
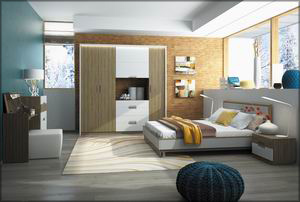
Спальня «Ноэль»
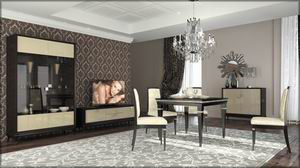
Гостинная «Брио»
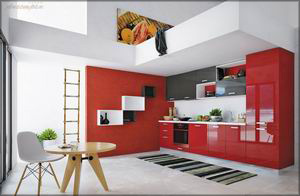
Кухня «Ниола»
Пользуется спросом и мебель «Ангстрем» для кухонь и ванных комнат. В 2009 году в состав холдинга вошла фабрика «Диана». Общая площадь ее производственно-складских помещений - 4,5 тыс. м2. Технологические процессы производства мебели для кухонь и ванных комнат схожи с технологией изготовления корпусной мебели и фасадов. Отличие лишь в использовании специальных материалов и фурнитуры. «Диана» - это отдельный, уникальный и масштабный проект, поэтому в рамках этой публикации только перечислим оборудование, составляющее основу станочного парка, который задействован на площадке. Это форматно-раскроечные станки Altendorf F45 (Германия) и Sсhelling FX-H 330/310 (Австрия), кромкооблицовочные станки Brandt KDF 770 (Homag Group, Германия), SCM Olimpic K 1000, SCM Olimpic M80 (Италия), деревообрабатывающие центры SCM Optimat BHC 250 SE и SCM Tech Z 25 (Италия), сверлильно-присадочные станки Vitap Forma 85 LCD и Vitap Alfa 21 (Италия), калибровально-шлифовальный станок SCM Sandia 5S (Италия), два фрезерных станка с ЧПУ «Артмастер» Е 2112 (Россия), заусовочный станок MHF DGS 2500 (Германия), сверлильный станок Einheell SB401 (Китай), присадочный станок под петли Hettich (Германия), шкантозабивной станок Koch Sprint-PTP-2-L (Германия), сверлильные станки Forward FDP-13/350 (Китай) и Hitachi B16RM (Германия). Для раскроя материалов и деталей используются маятниковые пилы Bosch GSM12SD, Bosch GSM10SD (Германия), Virutex TS 48L, Virutex TM 33L (Испания) и циркулярная пила DeWalt DW1501 (США). На площадке «Дианы» изготавливаются и фасады - здесь работают горячий пресс Orma NPC/Digit 6/90 AS BO (Италия) и мембранно-вакуумный пресс МВП 2512 (Россия). За чистоту воздуха в помещениях и соблюдение температурного режима отвечают аспирационные системы Bartling HRV-G-D-280-2 (Германия) и Nestro 535525 (Германия), а также пылеулавливающие агрегаты «Эковент ПФЦ-3000», «Эковент ПФЦ-8000», «Эковент ПФЦ 5000», «Консар УВП 2500», УПУ 1200 для станка «Артмастер» А и Е (все названное оборудование отечественного производства), Elmos ПП (Германия). Сжатым воздухом производство обеспечивают три компрессора: Atlas Copco GA 18 (Швеция), АВАС Genesis 15 и ABAC Genesis 11 (Италия), готовую продукцию упаковывают машины ТР-202 отечественного производства.
Непрофильные, но социально важные
Помимо прочего, руководство компании «Ангстрем» реализует еще ряд самостоятельных и не менее интересных проектов:
- гипермаркет домашнего уюта Hommy в г. Курске - большой магазин с огромным ассортиментом мебели как собственного производства, так и производства других компаний, сопутствующие товары и товары для дома, готовые интерьерные решения;
- агрохозяйственный бизнес, включающий молочный комплекс «Дон», сеть молокоматов «Наше донское» и производство экологически чистых продуктов (мяса птицы, свинины, молока);
- книжный клуб «Петровский», в составе которого книжный магазин, кафе, где проходят вечера живой музыки, встречи с писателями, презентация книг и лекции на актуальные темы;
- деловой центр «Репное» - площадка для проведения семинаров и мероприятий, включающая гостиничный комплекс для гостей, а также школа эффективных коммуникаций «Репное» - некоммерческий образовательный проект, в рамках которого творческие люди могут повысить образование, расширить кругозор, пройти обучение под руководством экспертов из разных областей бизнеса, научиться создавать и реализовывать разные социальные проекты;
- центр восточных практик Shakti - культурно-оздоровительный центр, где можно окунуться в атмосферу восточных практик, принять участие в группах по интересам, посетить концерты, мастер-классы, семинары и многое другое;
- частное охранное предприятие, действующее в рамках группы компаний ЧОП «Эгида-2»;
- подразделение по оказанию транспортных и клининговых услуг. «Ангстрем» располагает большим собственным парком спецтехники (машин для обрезки деревьев, мусоровозов и прочих), который обслуживает не только предприятия холдинга, но и помогает городу и подшефным учреждениям.
На «Ангстреме» умеют не только хорошо работать, но и отдыхать. В историко-этнографической экспедиции «Ангстрем» может принять участие любой желающий, прошедший подготовку и отбор. Два раза в год команды друзей и единомышленников осваивают разные маршруты по всей России, расширяя границы своего знания Родины и набираясь новых впечатлений.
Большое внимание уделяется работе с детьми и молодежью. Это и программа развития научно-технического творчества детей «Робототехника», включающая фестиваль, на котором свои работы представляют юные конструкторы (в последнем фестивале на конкурс было представлено почти 2000 работ, участие в мероприятии приняли около 10 тыс. человек со всех уголков страны). Реализуется программа профориентации для школьников «Большая игра», разработанная профильными специалистами с целью социальной адаптации и развития старшеклассников. В рамках программы проводится психологическая диагностика личностных качеств участников, двухдневный тренинг, беседа с родителями. Регулярно организуется конкурс студенческих работ «Поколение "Ангстрем"», итогом которого становится приглашение лучших участников на стажировку в компанию и предоставление возможностей для карьерного роста, а также фестиваль «История успеха» для учащихся старших классов школ. Многогранная и разноплановая деятельность мебельного холдинга «Ангстрем» социально ориентирована, в центре внимания человек с его интересами, самобытностью, нуждами, достижениями и стремлением к развитию.
Ну и, конечно же, в холдинге огромное внимание уделяется обеспечению комфортных условий работы сотрудников, их поощрению и поддержке, повышению мотивации. Как отмечают в «Ангстреме», самая большая ценность компании - это люди, работающие на предприятии и разделяющие основные принципы корпоративной политики: свобода и ответственность, эффективность, честность, доверие, командный дух, взаимоуважение, равноправие, профессионализм и стремление к высоким целям.
В компании действует много программ, цель которых - мотивация сотрудников. Бесплатные комплексные обеды в производственных столовых, спецодежда и средства индивидуальной защиты, услуги фитнес-клуба для сотрудников, поощрения за добросовестный и качественный труд (фото на доске почета и т. п.) - все это здесь само собой разумеется. Есть комнаты отдыха, где во время перерывов работники смотрят телевизор, играют в настольные игры. Здесь же проходит обучение и аттестация сотрудников на получение каких-либо разрядов (у «Ангстрема» есть право присваивать разряды своим работникам самостоятельно). Сотрудники проходят обучение и повышают квалификацию как в Германии - в системе концерна Homag, так и в России, например, в обучающем центре Homag Russland, либо непосредственно на предприятии. Люди заинтересованы в работе в такой большой компании с прекрасным соцпакетом, да и оплата труда на фабриках «Ангстрема» выше, чем в среднем по городу или на других производствах. Стаж работы сотрудников производственных цехов зачастую достигает десятков лет. Профессионалы с колоссальным опытом работы - гордость предприятия, ими дорожат, на их примере воспитывают новых специалистов. Каждый год на день рождения компании лучшие сотрудники удостаиваются знаков почета за заслуги перед «Ангстремом» и награждаются солидными денежными премиями. Раз в год, а в юбилейные годы и несколько раз, сотрудники имеют возможность приобретать в компании мебель по заводской цене. Организуются корпоративные мероприятия, экскурсии для сотрудников.
Ставя во главу угла точность, качество и профессионализм, «Ангстрем» с успехом выполняет свою миссию: быть среди первых в формировании среды обитания современного человека, постоянно развиваясь и воплощая в реальность самые яркие идеи и мечты, делать мир совершеннее, а людей - счастливее.
Ольга РЯБИНИНА
Член наблюдательного совета ГК «Ангстрем» Сергей Радченко: «Возможно, лет через 20 мебель будут печатать на принтере...»
Если говорить о развитии мебельного холдинга «Ангстрем», то в первую очередь нужно сказать о реализации большого проекта - фабрики в индустриальном парке «Масловский». Сейчас введена в эксплуатацию первая очередь - логистический центр «Ангстрем», куда свозится готовая продукция со всех производственных площадок, и откуда она отгружается клиентам. Новая фабрика - очень большой и долгосрочный проект, фактически предприятие будет спроектировано и построено с нуля. В ближайшем будущем планируется реализация второй очереди проекта - фабрики по производству фасадов. Еще одно направление, по которому мы будем продолжать активно работать, - развитие нашей торговой сети, которая требует сегодня большого внимания и вклада сил и средств. Пришла пора ребрендинга торговой сети, которым мы и будем заниматься в ближайшее время. Также в планах компании освоение новой технологии, которую в мире пока используют всего несколько предприятий, сейчас мы пытаемся адаптировать ее к нашим условиям.
Мебельные компании все шире используют новые, революционные технологии для производства современной мебели, в конструкции которой сегодня сочетаются металл, стекло, камень, плита, натуральная древесина, например, шпон. Для того чтобы выпускать востребованную мебель, помимо процессов деревообработки надо осваивать резку и сварку металлов, стеклообработку, работу с камнем и т. д. А может, лет через 20 мебель начнут печатать на принтере? Надо быть к этому готовым, следить за тенденциями и осваивать новые технологии. Чем мы и занимаемся.
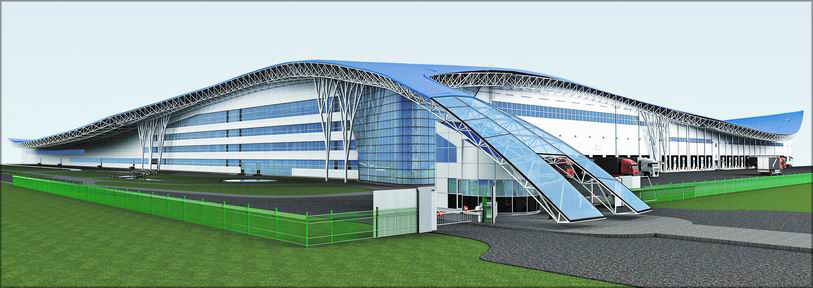
Еще одно направление, которое мы планируем активно развивать, - производство мебели по индивидуальным заказам. Удивительно, но в наше непростое время объем заказов на мебель по индивидуальным проектам растет. И наша компания сегодня занимает первое место в производстве и реализации подобной мебели в Воронеже (где мы работаем в этом сегменте рынка уже более 20 лет) и в Москве. В столице заказная мебель немало отличается по цене от типовой, стандартной серийной мебели, и тут мы берем ценой - наш прайс ниже московских компаний. В Воронеже ситуация сложнее - там очень здоровая и правильная конкурентная среда в этом сегменте, которая держит нас в тонусе, поэтому планируем расширять цех и дооснащаться, чтобы сделать нашу мебель еще более конкурентоспособной и нарастить объемы производства.
И конечно же, мы планируем запуск новых продуктов. Среднестатистический срок жизни продукта на рынке - не больше пяти лет. Конечно, есть «долгоиграющие» товары, в программе «Ангстрема» они тоже есть: одним моделям уже под 20 лет, другие 10 лет на рынке. Но это относится скорее к классическим моделям. Современные топовые модели очень ярко загораются, но так же быстро гаснут. Поэтому надо иметь возможность сменить товарную линейку тогда, когда этого требует рынок, и помнить, что разработка новых продуктов занимает около 20% рабочего времени.
Как в запуске новых продуктов, так и в работе с розничной сетью нужно уметь заглянуть за горизонт и попробовать ответить на вопросы: а что будет с рынком мебели через 5-10 лет, как может целевая аудитория измениться в ближайшее время, что будет происходить с продажами, какие будут превалировать? Многие эксперты уже говорят, что крупные мебельные центры как таковые уйдут в историю. Возможно, «Ангстрему» удается развивать свой интернет-магазин за счет того, что у него довольно разветвленная розничная сеть, во многих городах есть магазины, и потенциальный клиент может в них посмотреть образцы мебели и заказать по интернету, что ему нужно.
Сейчас много рассуждают на тему кризиса в экономике и промышленности России и выхода из него. Но мне кажется, это не кризис - это новая экономическая реальность, и она в ближайшее время не закончится. Выживет тот, кто сможет приспособиться, адаптироваться к этой реальности. Да, на внутреннем рынке спад, но он в первую очередь коснулся импорта, а это 60% рынка. Отечественным производителям 40% рынка вроде бы достаточно - теоретически, а на практике нет. Многие начали предпринимать активные действия, пытаясь адаптироваться к новым условиям. Одни производители изменили ценовой сегмент и запустили производство мебели класса эконом, другие начали заниматься той товарной группой, в которой раньше никогда не работали, третьи изменили целевую аудиторию, кто-то пытается переориентироваться на экспорт. Безусловно, и компания «Ангстрем» не может не реагировать на изменившуюся ситуацию.
Подготовила Ольга РЯБИНИНА