Производство ДСП
Все по полочкам
Для изготовления ДСП необходимо знать всю цепочку технологического процесса. При этом необходимо учитывать вид применяемого сырья, конструкции плит и требуемый тип древесных частиц (игольчатая, плоская и мелкая стружка). Только тогда в результате можно получить качественный продукт.
Итак, изготовление ДСП состоит из следующих операций: подготовка сырья, переработка сырья в древесную стружку, сушка и доизмельчение, сортировка древесной стружки, приготовление рабочего раствора связующего, дозирование и смешивание древесных частиц со связующим, формирование пакетов, подпрессовывание пакетов, горячее прессование, охлаждение, обрезка плит, их выдержка, калибрование, шлифование, сортирование и упаковка. Включение в технологический процесс ряда перечисленных операций напрямую зависит от вида применяемого сырья, конструкции плит и требуемого типа древесных частиц (игольчатая, плоская и мелкая стружка).
Характеристика древесных частиц для формирования слоев древесно-стружечных плит
Для производства древесно-стружечных плит могут использоваться древесные частицы различных видов.
По фракционному составу древесные частицы в зависимости от размеров можно разделить на четыре фракции: пылевая, мелкая, средняя и крупная. Первая содержит частицы толщиной 0,01–0,1 мм, шириной 0,01–0,5 мм, длиной 0,1–1 мм. Древесные частицы мелкой фракции имеют толщину 0,1–0,15 мм, ширину 0,3–1 мм и длину 1–10 мм. Древесные частицы пылевой и мелкой фракции применяют преимущественно для наружных слоев плит ДСП.
Средняя фракция состоит из частиц толщиной 0,15–0,25 мм, шириной 1–3 мм и длиной 10–20 мм. Крупная фракция содержит частицы толщиной 0,25–0,45 мм, шириной 3–12 мм и длиной 20–40 мм. Последние два вида древесных частиц применяют в основном для формирования внутреннего слоя.
Во внутреннем слое ее процентное содержание должно быть не более 10–20% (так как при этом увеличивается расход связующего). Однако многие производители по возможности стараются не использовать пыль при производстве плит.
Кроме пыли, до 30–40% от общей массы древесной стружки внутреннего слоя добавляют стружку-отход в средний слой древесно-стружечных плит. –
Что касается получения того или иного типа стружки, то в производстве ДСП древесные частицы изготавливают по двум основным схемам.
Схема 1. Круглые лесоматериалы и крупные отходы деревообрабатывающих производств измельчают в рубильных машинах в технологическую щепу. Затем на центробежных станках получают из щепы игольчатую стружку. Преимущественно такую стружку используют для формирования внутреннего слоя плит, а при дополнительном измельчении на зубчато-ситовых мельницах - и для наружных. Древесно-стружечные плиты из игольчатой стружки имеют рыхлые кромки, но в меньшей степени изменяют свои размеры при эксплуатации.
Схема 2. Круглые лесоматериалы и карандаши фанерного производства (остаются после разлущивания чурака) перерабатывают на стружечных станках с ножевым валом или диском. После этого стружка дополнительно измельчается, в основном по ширине, в дробилках.
Некоторые предприятия используют для производства как игольчатую, так и плоскую стружку. С учетом этого в цех ставится соответствующее оборудование. Но основной тип древесных частиц, которые широко используют плитные предприятия, – игольчатая стружка.
Современные инжиниринговые компании (например, Siempelkamp, Dieffebacher) под ключ могут поставить (в зависимости от требуемой заказчиком производственной мощности) линии для производства ДСП. Тем не менее для участка измельчения древесины клиенту следует выбрать необходимое оборудование. Что о нем следует знать?
Рубильные машины. По виду рабочего органа различают барабанные и дисковые машины. Основным рабочим органом дисковых рубильных машин является стальной диск с радиально закрепленными на нем ножами.
У дисковых машин длина щепы определяется величиной выступа ножей на ножевом диске. Эту величину можно регулировать только в небольших пределах.
Рабочим органом барабанных рубильных машин является барабан с закрепленными на его цилиндрической поверхности ножами. Такие машины применяют как для переработки крупномерного сырья, так и для переработки отходов длиной более 100 мм.
Длина древесных частиц, получаемых в барабанных рубильных машинах, определяется скоростью подачи материала, частотой вращения ротора и количеством на нем ножей. Если увеличить скорость подачи материала, на выходе из машины получаем древесные частицы большей длины, а вот с увеличением частоты вращения ротора и количества ножей на нем щепа получается меньшей длины.
На Западе древесную стружку получают путем измельчения поддонов, старой мебели, деревянной тары. Для этого используют специальное оборудование. В России исходным сырьем для производства ДСП являются технологические дрова, неделовая древесина или технологическая щепа. Именно поэтому отечественные плиты превосходят по многим физико-механическим показателям зарубежные.
При измельчении древесного сырья на рубительных машинах наряду с нормальной щепой (длиной от 5 до 40 мм), идущей в производство, образуется определенное количество мелкой и крупной щепы, которая не пригодна для дальнейшей переработки. Кроме того, вместе с кусковыми отходами и шпоном-рваниной в рубительную машину попадают опилки, кора, гниль, мусор, которые должны быть отделены от кондиционной технологической щепы. Крупная щепа и сколы забивают трубопроводы пневмотранспортных установок, приемники стружечных станков. Поэтому после изготовления щепу сортируют на три фракции: крупную, направляемую на дополнительное измельчение, кондиционную, идущую к стружечным станкам, мелкую, которая также может (после дополнительного измельчения) быть использована для формирования наружных слоев или (при большой засоренности) сжигается. Полученная щепа требует обязательной сортировки для удаления кусков коры, гнили, опилок и мусора и отделения щепы крупной фракции, которая после сортировки дополнительно измельчается. Кондиционная щепа транспортируется к стружечным станкам.
Стружечные станки. Для получения из щепы или мелких кусковых отходов древесных частиц нужного размера и формы применяют центробежные стружечные станки. Отечественным станкостроением был разработан и поставлен в цеха многих крупных заводов стружечный станок марки ДС-7. Со временем многие предприятия стали модернизировать свое производство и ставить в цеха стружечные станки компаний Pallman, Maier, Hombak.
Щепу можно измельчать и безножевым способом - путем истирания древесных частиц зубчатыми вкладышами. Например, это центробежный безножевой стружечный станок MSZ компании Maier.
Дополнительное измельчение. Необходимость в дополнительном измельчении древесной стружки возникает из-за чрезмерной ширины древесных частиц, получаемых на стружечных станках. Также получает распространение производство плит с мелкоструктурной поверхностью, в которых для формирования наружных слоев используют мельчайшие древесные частицы. Как правило, доизмельчение происходит методом ударного измельчения либо на молотковых дробилках, либо в лопастных мельницах различной конструкции. Поступающая на эту операцию древесная стружка должна быть предварительно высушена и отсортирована. Иначе при переработке влажной стружки пропускная способность машин снижается. Таким образом, на выбор оборудования для участка измельчения древесины влияет вид исходного сырья, его порода, влажность, производительность. Только с учетом вышеуказанных параметров поставленные станки будут слаженно и эффективно работать.
По фракционному составу древесные частицы в зависимости от размеров можно разделить на четыре фракции: пылевая, мелкая, средняя и крупная. Первая содержит частицы толщиной 0,01–0,1 мм, шириной 0,01–0,5 мм, длиной 0,1–1 мм. Древесные частицы мелкой фракции имеют толщину 0,1–0,15 мм, ширину 0,3–1 мм и длину 1–10 мм. Древесные частицы пылевой и мелкой фракции применяют преимущественно для наружных слоев плит ДСП.
Средняя фракция состоит из частиц толщиной 0,15–0,25 мм, шириной 1–3 мм и длиной 10–20 мм. Крупная фракция содержит частицы толщиной 0,25–0,45 мм, шириной 3–12 мм и длиной 20–40 мм. Последние два вида древесных частиц применяют в основном для формирования внутреннего слоя.
Специально изготовленные
древес-ные частицы:
стружка плоская (СП)
стружка игольчатая (СИ)
мелкая стружка (МС)
волокно древесное
технологическое (ВДТ)
частицы волокнистые (чВ)
Древесные частицы –
отходы деревообрабаты-
вающих производств:
стружка станочная (СС)
опилки (О)
пыль древесная
технологическая (ПДТ)
пыль шлифовальная (Пш)
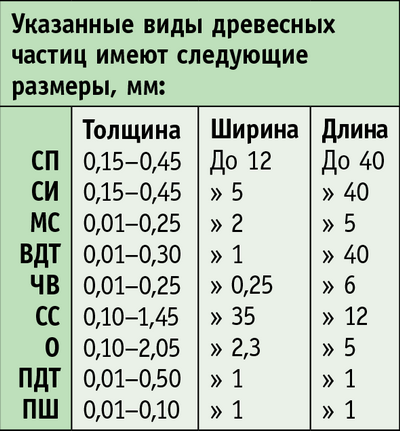
Для наружных слоев используют мелкую стружку, стружку-отход и опилки, а также шлифовальную пыль. Последняя в ограниченных количествах добавляется в наружные и внутренние слои. древес-ные частицы:
стружка плоская (СП)
стружка игольчатая (СИ)
мелкая стружка (МС)
волокно древесное
технологическое (ВДТ)
частицы волокнистые (чВ)
Древесные частицы –
отходы деревообрабаты-
вающих производств:
стружка станочная (СС)
опилки (О)
пыль древесная
технологическая (ПДТ)
пыль шлифовальная (Пш)
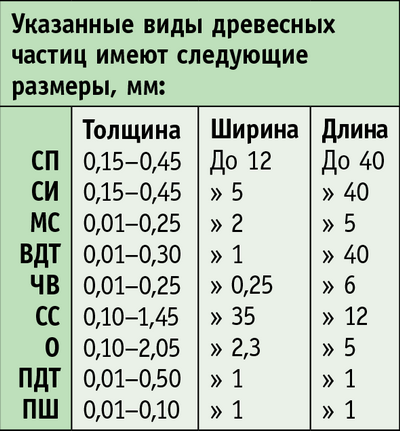
Во внутреннем слое ее процентное содержание должно быть не более 10–20% (так как при этом увеличивается расход связующего). Однако многие производители по возможности стараются не использовать пыль при производстве плит.
Кроме пыли, до 30–40% от общей массы древесной стружки внутреннего слоя добавляют стружку-отход в средний слой древесно-стружечных плит. –
Что касается получения того или иного типа стружки, то в производстве ДСП древесные частицы изготавливают по двум основным схемам.
Схема 1. Круглые лесоматериалы и крупные отходы деревообрабатывающих производств измельчают в рубильных машинах в технологическую щепу. Затем на центробежных станках получают из щепы игольчатую стружку. Преимущественно такую стружку используют для формирования внутреннего слоя плит, а при дополнительном измельчении на зубчато-ситовых мельницах - и для наружных. Древесно-стружечные плиты из игольчатой стружки имеют рыхлые кромки, но в меньшей степени изменяют свои размеры при эксплуатации.
Схема 2. Круглые лесоматериалы и карандаши фанерного производства (остаются после разлущивания чурака) перерабатывают на стружечных станках с ножевым валом или диском. После этого стружка дополнительно измельчается, в основном по ширине, в дробилках.
Схемы смотрите в PDF-версии журнала.
Некоторые предприятия используют для производства как игольчатую, так и плоскую стружку. С учетом этого в цех ставится соответствующее оборудование. Но основной тип древесных частиц, которые широко используют плитные предприятия, – игольчатая стружка.
Современные инжиниринговые компании (например, Siempelkamp, Dieffebacher) под ключ могут поставить (в зависимости от требуемой заказчиком производственной мощности) линии для производства ДСП. Тем не менее для участка измельчения древесины клиенту следует выбрать необходимое оборудование. Что о нем следует знать?
Рубильные машины. По виду рабочего органа различают барабанные и дисковые машины. Основным рабочим органом дисковых рубильных машин является стальной диск с радиально закрепленными на нем ножами.
У дисковых машин длина щепы определяется величиной выступа ножей на ножевом диске. Эту величину можно регулировать только в небольших пределах.
Рабочим органом барабанных рубильных машин является барабан с закрепленными на его цилиндрической поверхности ножами. Такие машины применяют как для переработки крупномерного сырья, так и для переработки отходов длиной более 100 мм.
Длина древесных частиц, получаемых в барабанных рубильных машинах, определяется скоростью подачи материала, частотой вращения ротора и количеством на нем ножей. Если увеличить скорость подачи материала, на выходе из машины получаем древесные частицы большей длины, а вот с увеличением частоты вращения ротора и количества ножей на нем щепа получается меньшей длины.
На Западе древесную стружку получают путем измельчения поддонов, старой мебели, деревянной тары. Для этого используют специальное оборудование. В России исходным сырьем для производства ДСП являются технологические дрова, неделовая древесина или технологическая щепа. Именно поэтому отечественные плиты превосходят по многим физико-механическим показателям зарубежные.
При измельчении древесного сырья на рубительных машинах наряду с нормальной щепой (длиной от 5 до 40 мм), идущей в производство, образуется определенное количество мелкой и крупной щепы, которая не пригодна для дальнейшей переработки. Кроме того, вместе с кусковыми отходами и шпоном-рваниной в рубительную машину попадают опилки, кора, гниль, мусор, которые должны быть отделены от кондиционной технологической щепы. Крупная щепа и сколы забивают трубопроводы пневмотранспортных установок, приемники стружечных станков. Поэтому после изготовления щепу сортируют на три фракции: крупную, направляемую на дополнительное измельчение, кондиционную, идущую к стружечным станкам, мелкую, которая также может (после дополнительного измельчения) быть использована для формирования наружных слоев или (при большой засоренности) сжигается. Полученная щепа требует обязательной сортировки для удаления кусков коры, гнили, опилок и мусора и отделения щепы крупной фракции, которая после сортировки дополнительно измельчается. Кондиционная щепа транспортируется к стружечным станкам.
Стружечные станки. Для получения из щепы или мелких кусковых отходов древесных частиц нужного размера и формы применяют центробежные стружечные станки. Отечественным станкостроением был разработан и поставлен в цеха многих крупных заводов стружечный станок марки ДС-7. Со временем многие предприятия стали модернизировать свое производство и ставить в цеха стружечные станки компаний Pallman, Maier, Hombak.
Щепу можно измельчать и безножевым способом - путем истирания древесных частиц зубчатыми вкладышами. Например, это центробежный безножевой стружечный станок MSZ компании Maier.
Дополнительное измельчение. Необходимость в дополнительном измельчении древесной стружки возникает из-за чрезмерной ширины древесных частиц, получаемых на стружечных станках. Также получает распространение производство плит с мелкоструктурной поверхностью, в которых для формирования наружных слоев используют мельчайшие древесные частицы. Как правило, доизмельчение происходит методом ударного измельчения либо на молотковых дробилках, либо в лопастных мельницах различной конструкции. Поступающая на эту операцию древесная стружка должна быть предварительно высушена и отсортирована. Иначе при переработке влажной стружки пропускная способность машин снижается. Таким образом, на выбор оборудования для участка измельчения древесины влияет вид исходного сырья, его порода, влажность, производительность. Только с учетом вышеуказанных параметров поставленные станки будут слаженно и эффективно работать.
Екатерина МАТЮШЕНКОВА
Автор: Екатерина Матюшенкова