«Светлица»: доступные дома из профилированного бруса
С 1998 года в г. Твери работает группа компаний «ТМК», основной продукцией которой являются пластиковые и алюминиевые окна, межкомнатные и входные двери, натяжные потолки, корпусная мебель, напольные покрытия и интерьерные системы. Под руководством бессменного генерального директора Виталия Давыденко предприятие планомерно расширяет ассортимент продукции в сегменте бюджетного строительства. В 2011 году было решено создать собственное домостроительное производство, что позволило заказчику, что называется, из одних рук приобретать полностью укомплектованные деревянные дома.
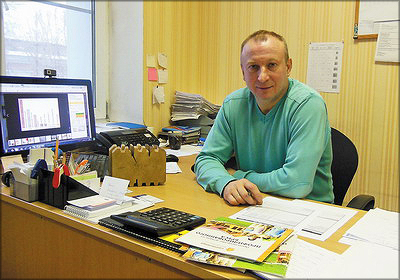
Заместитель директора компании «Светлица» Павел Беззубчак
Промышленные площадки группы компаний «ТМК» размещены на выкупленной территории бывшего Тверского завода искусственных кож. На этой же территории в 2011 году было создано подразделение, занимающееся изготовлением деревянных домокомплектов из профилированного бруса – «Светлица».
Это производство было организовано силами всего двух человек: Андрея Иванова (сегодня он руководитель направления «Дома из бруса») и Павла Беззубчака. На момент создания предприятия у этих специалистов уже был обширный опыт проектирования и строительства деревянных домов, изготовления деревообрабатывающих станков и создания деревообрабатывающих предприятий. Это и позволило довольно быстро организовать производственный процесс и вывести цех на запланированный уровень производственной мощности. На площадке около 700 м2 менее чем за год был создан новый производственный участок. Промышленное оборудование для организации технологического процесса закупалось в Европе при участии компании Eurowood Group GmbH. Парк оборудования формировался из бывших в употреблении станков, которые перед поставкой в Россию были полностью восстановлены в заводских условиях.
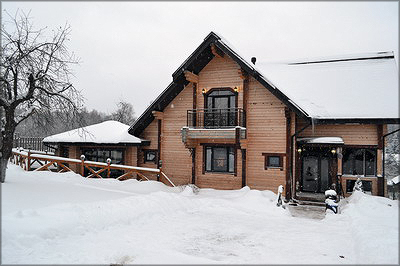
Вскоре все оборудование уже было смонтировано и введено в эксплуатацию на производственной площадке компании «Светлица». В 2012 году заказчикам уже были отгружены первые домокомплекты, изготовленные из бруса естественной влажности. Выпуск профилированного бруса камерной сушки начался в 2013 году. Помимо стеновых элементов, на предприятии изготавливают стропильные системы, оконные и дверные коробки, а также строганые пиломатериалы.
В настоящее время производственные мощности предприятия полностью загружены и позволяют ежемесячно выпускать до 1000 м3 готовой продукции. По мнению руководителей компании, именно подобные небольшие региональные производства и должны обеспечивать развитие малоэтажного деревянного домостроения в России – они ответственнее перед заказчиками, чем крупные холдинговые предприятия, что продиктовано необходимостью сохранения высокой репутации на небольших местных рынках. Кроме того, подобные компании могут не только предложить потребителю изготовление домокомплектов, но и осуществлять комплексную поддержку проекта, обладая полной информацией об особенностях эксплуатации жилых зданий в своем регионе с присущими ему температурно-климатическими условиями. Наличие производственных площадок в собственности, отсутствие кредитной нагрузки и ориентация на массового потребителя позволили обеспечить уверенную работу группы компаний «ТМК» даже в период экономических кризисов.
Продукция предприятия «Светлица»
Основной продукцией компании «Светлица» является сухой профилированный брус как элемент конструкции дома, у которого в заводских условиях сформированы все соединительные элементы. По желанию заказчика домокомплекты могут быть изготовлены из древесины двух пород: сосны и ели. Установленное оборудование позволяет обрабатывать брус естественной влажности сечением до 200х250 мм и брус камерной сушки сечением до 175х230 мм при длине продукции до шести метров.
Профиль бруса выполняется в форме «гребенки» что, по мнению специалистов компании, обеспечивает хорошую ветроизоляцию и позволяет собирать дома без использования утеплителя между венцами. Утеплитель марки «Шелтер ЭкоСтрой» применяется только при сборке угловых соединений.
Сухой профилированный брус выбран в качестве основной продукции исходя из следующих соображений. В сравнении с клееным брусом, рынок которого в регионе перенасыщен, профилированный брус камерной сушки более доступный продукт, для производства которого не требуется привлечение больших инвестиций. Собственники также рассматривали вариант производства каркасных домов без использования дорогого оборудования. Однако стоимость производства подобных домов с соблюдением всех строительных норм и правил приближается к цене конструкций из клееного бруса.
Для строительства одно- и двухэтажных домов несущей способности профилированного бруса вполне достаточно. При эксплуатации домов из цельного бруса вследствие усушки древесины на стенах могут появляться трещины, но они не приводят к значительному снижению эксплуатационных свойств. Их появление – нормальное явление при использовании цельной древесины. С другой стороны, строительство дома из цельной древесины позволяет обеспечить одинаковые цвет и фактуру всей площади стены, что не всегда удается при использовании клееной древесины, особенно изготавливаемой из ламелей, сращенных по длине.
Компания «Светлица» предлагает заказчикам комплекс услуг – от создания проекта до изготовления готовых домокомплектов. Для проектирования используется специализированный программный комплекс SEMA. Наряду с домами, изготовленными из оцилиндрованных бревен, постройки из профилированного бруса экологичны, поскольку полностью изготовлены из древесины и для их обработки не используются никакие вредные вещества. Они могут эксплуатироваться без дополнительной отделки, достаточно только покрасить наружные стены.
Производство недорогих деревянных домов из сухого профилированного бруса полностью соответствует общей философии группы компаний «ТМК», ориентированной на бюджетный сегмент рынка.
Предпочтения потребителей
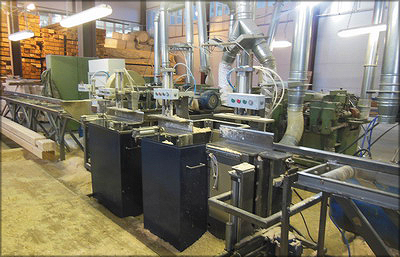
По мнению Павла Беззубчака, дом из профилированного бруса камерной сушки может позволить себе любой работающий россиянин. Наиболее востребованы двухэтажные дома площадью 120–170 м2 из профилированного бруса, прошедшего камерную сушку. Для изготовления домов указанной площади в зависимости от планировки требуется 60–80 м3 бруса. При цене домокомплекта до 1,5 млн руб. обеспечивается самая низкая стоимость квадратного метра жилой площади. Очень часто профилированный брус камерной сушки выбирается потребителями после анализа стоимости домов из клееного бруса. Возможность использования более экологичного материала, позволяющего за ту же цену построить дом большей площади, часто является решающим аргументом.
Необходимо также отметить изменение предпочтений покупателей. Если еще два года назад до 70% клиентов выбирали себе дома из древесины естественной влажности, то сегодня доля покупателей подобных домов сократилась до 30 процентов.
Все больше покупателей понимают, что ожидание окончания усушки ради экономии на строительном материале себя не оправдывает. Современный потребитель уже не готов экономить на качестве и увеличении сроков строительства, что позволяет предположить дальнейший рост доли сухого бруса в общем объеме выпускаемой продукции.
Еще один плюс древесины как основного строительного материала для малоэтажных зданий – ее небольшой вес относительно веса кирпича или бетона, что обеспечивает возможность строительства домов из бруса на простых и долговечных малозаглубленных фундаментах. Некоторые потребители из экономии выбирают свайные фундаменты, которые в компании «ТМК» применять не рекомендуют, поясняя свое решение не только отсутствием точных данных о гарантированном периоде эксплуатации подобных фундаментов, но и необходимостью инвестирования дополнительных средств в отделку цоколя. Ленточный фундамент достаточно просто покрасить. Использование свайного основания влечет за собой необходимость проведения дополнительных строительных работ, что в конечном итоге оборачивается большими затратами, превышающими возможный размер экономии.
Технологический процесс
Сырьем для изготовления домокомплектов является пиленый брус естественной влажности, закупаемый на лесопильных предприятиях Тверской области. Около 65% бруса изготавливается из древесины сосны, 35% – из древесины ели. Это соотношение обусловлено параметрами лесосырьевой базы в регионе. По словам менеджеров компании, 99% клиентов при покупке домокомплектов не обращают внимания на породу древесины, из которой изготовлены элементы и конструкции. При строительстве индивидуальных одно- и двухэтажных зданий на первый план выходит качество изготовления элементов домокомплекта и сборки дома, а не различия в физико-механических свойствах древесины.
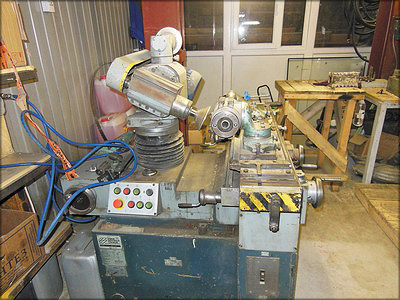
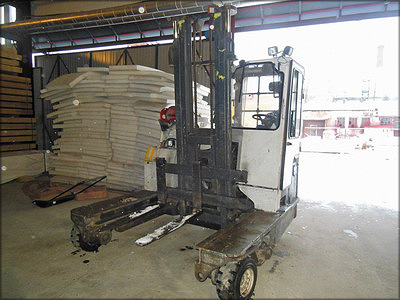
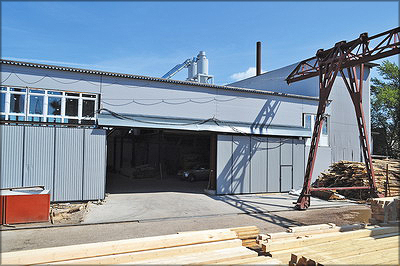
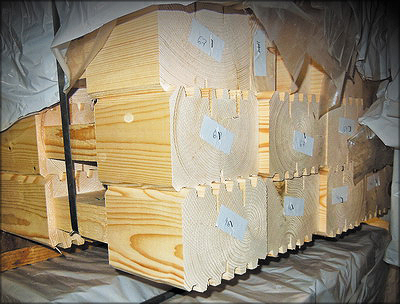
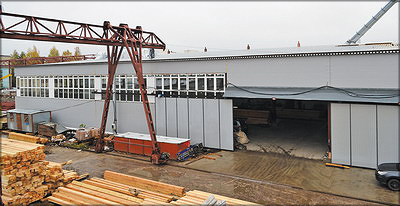
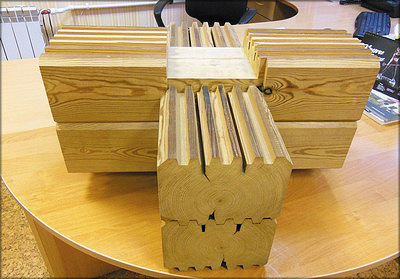
Процесс изготовления домокомплектов начинается с приемки сырья. Пиленый брус естественной влажности поставляется автотранспортом на площадку предприятия. Разгрузка машин осуществляется с помощью кранового оборудования. Все остальные транспортные операции на участке деревообработки выполняются с помощью погрузчика Combilift C4000.
Несмотря на то что компании «Светлица» всего семь лет, парк оборудования в деревообрабатывающем цехе уже неоднократно сменялся. Первоначально предварительное калибрование бруса осуществлялось на станке REX, на котором можно было обрабатывать заготовки максимальным размером 300х500 мм. Сейчас для этой операции используются приобретенные станки Weinig, которые лучше, чем прежний станок, соответствуют поставленным задачам. Изменилось и оборудование для нарезки соединительных узлов. В начальный период производства на предприятии использовался чашкорезный фрезерный станок ВКР, но с повышением производительности он был заменен автоматизированной линией Schmidler, которая работала под управлением купленной у компании «Фаэтон» программы SEMA. Но сложности, возникавшие при техническом обслуживании линии и погрешности при позиционировании бруса, привели к тому, что от использования линии Schmidler также решили отказаться. При анализе рынка было изучено множество характеристик моделей оборудования для изготовления соединительных элементов. Высокая стоимость станков и невозможность на одной линии сверлить отверстия под нагели, выполнять торцовку по длине и изготавливать соединительные элементы подвели к решению изготовить оборудование по индивидуальному заказу. В соответствии с разработанными техническими условиями оборудование было изготовлено на Сявском экспериментально-механическом заводе. На линии установлены двигатели повышенной мощности, что важно при обработке бруса естественной влажности и большого сечения. При высоком качестве электронной начинки и металла корпуса и деталей изготовленное оборудование дешевле, чем даже бывшие в употреблении конкурентные станки известных брендов. Единственным недостатком был длительный срок изготовления, но в конечном итоге все затраты себя оправдали. В настоящее время производство деревянных домокомплектов полностью отлажено, а производительность оборудования синхронизирована.
Перед выполнением камерной сушки брусья профилируют с двух сторон на 9-шпиндельном станке Weinig с одновременным формированием компенсационных пропилов, повышающих формоустойчивость бруса в процессе эксплуатации. После выполнения указанных операций брус укладывается на прокладки и поступает в одну из двух сушильных камер Vanicek.
Емкость установленных сушильных камер обеспечивает возможность одновременной сушки до 180 м3 бруса. Влажность высушенного профилированного бруса – 18–20%. После сушки брусья погрузчиком перемещаются ко второму станку Weinig, на котором с помощью семи шпинделей выполняется профилирование бруса. Завершающими технологическими операциями являются сверление отверстий под нагели, торцовка по длине и изготовление соединительных элементов. Готовая продукция по желанию заказчика может быть антисептирована с помощью защитных составов «Неомид» или сразу упакована в транспортные пакеты. На каждый брус крепится табличка с указанием порядкового номера и его размеров, что позволяет максимально упростить сборку.
При необходимости изготовления пиломатериалов нестандартного сечения, предназначенных для изготовления оконных и дверных коробок, на заводе используется ленточнопильный станок Wood-Mizer.
Тепловую энергию предприятие получает в результате сжигания древесных отходов, закупаемых на ближайших деревообрабатывающих предприятиях. Мощность котла Kohlbach, который эксплуатируется в компании, 4 МВт. Этой мощности вполне достаточно для обеспечения работы сушильных камер и отопления производственных помещений.
Большое внимание на предприятии уделяется подготовке режущего инструмента. Организован заточной участок на базе станков Weinig Rondamat и 3Е642Е. Установленное оборудование позволяет самостоятельно готовить режущий инструмент к работе, а используемые дереворежущие инструменты Kanefusa обеспечивают высокое качество обработки поверхности.
Хранение продукции и дополнительная обработка
Изготовление профилированного бруса осуществляется только под заказ. Дата изготовления обязательно согласуется со строительными бригадами исходя из тех сроков, в какие они могут начать возведение дома. Подобный подход позволяет избежать дополнительной защиты бруса камерной сушки путем его антисептирования на предприятии, что снижает стоимость домокомплекта для заказчика.
Кроме того, при этом подходе можно обойтись без склада готовой продукции и сэкономить производственные площади, что не приводит к «замораживанию» денежных средств предприятия в виде готовой, но не реализованной продукции. Максимальный срок хранения домокомплектов не превышает трех недель. Готовая продукция с пяти сторон упаковывается в полиэтиленовую пленку.
Кадровое обеспечение
На домостроительном участке работает всего десять человек. Изначально ни у одного работника не было профильного образования. В условиях, когда наши специализированные ПТУ не оснащены современным деревообрабатывающим оборудованием, необходимую квалификацию можно получить только на действующих предприятиях. Подготовку персонала предприятие осуществляло своими силами. Павел Беззубчак и Андрей Иванов на этапе становления предприятия наравне с рабочими занимались монтажом и пуском оборудования, а также обучали работников.
Поскольку компания «Светлица» занимается только изготовлением домокомплектов, для сборки домов привлекаются подрядные организации. Партнерами фирмы в настоящее время являются 15 компаний, у которых есть опыт строительства не только в Тверской области, но и в Московской, Тульской и Калужской. Дома, изготовленные компанией «Светлица», приобретают покупатели и из других регионов. Несколько объектов возведено в Республике Беларусь, а также в Ингушетии, Ямало-Ненецком автономном округе и даже на Камчатке.
Планы развития
На текущий момент предприятие вышло на полную производственную мощность по изготовлению сухого профилированного бруса. Несмотря на рост внутреннего рынка деревянного домостроения, увеличить объем выпуска продукции довольно сложно. Сдерживающими факторами роста производительности предприятия являются сложности с поставками пиломатериалов. Появление в регионе крупных деревообрабатывающих комбинатов привело к тому, что они скупают значительные объемы древесного сырья, сушат, дорабатывают и отправляют на экспорт большую часть выпускаемых в регионе пиломатериалов.
Парадоксальный факт: пилопродукция в регионе есть, но малым предприятиям, работающим на внутреннем рынке, получить ее довольно сложно. Те же проблемы с древесиной на корню. Небольших лесосек, которые могли бы арендовать маленькие компании, по сути, не осталось. Большие участки требуют использования дорогой лесозаготовительной техники, средств на приобретение которой у малых предприятий нет, и эти участки арендуются теми же крупными экспортно ориентированными предприятиями. Создавать же собственное лесопильное производство для выпиловки бруса, работающее на покупной древесине, в текущих экономических условиях нецелесообразно.
В качестве основного направления развития руководство «Светлицы» и компании «ТМК» выбрало диверсификацию продукции. На рынок планируется вывести новый продукт – строительный брус из термомодифицированной древесины. В результате термомодификации изменяются физические и химические свойства древесины, повышается ее формоустойчивость и биостойкость. При правильно выбранных параметрах и продолжительности термообработки пиломатериалы могут использоваться в качестве строительных комплектующих, а также в качестве комплектующих для дверей и окон, производство которых дополняет ассортимент продукции группы компаний «ТМК».
Предприятие уже разработало полную техническую документацию на изготовление оборудования для термомодификации и производство домокомплектов, а также дверей и окон из модифицированной древесины. Для размещения новых производственных мощностей уже начато строительство еще одного цеха.
Небольшие домостроительные предприятия постоянно развивают производство, создают новые рабочие места и реализуют продукцию из древесины внутри страны, однако на них не распространяются государственные программы по поддержке малого бизнеса. Кроме того, подобные региональные производства, по сути, не вовлечены в деятельность Ассоциации деревянного домостроения, как сказал Павел Беззубчак: «Представители ассоциации никогда не обращались к нам с предложениями о взаимодействии или сотрудничестве, хотя мы хорошо известны в регионе и больше семи лет принимаем участие в профильных московских выставках, посвященных деревянному домостроению».
Парадоксально, но развитие и рост производственной мощности компании сдерживаются не отсутствием площадей или инвестиций для размещения дополнительного оборудования, а дефицитом основного ресурса – пиломатериалов, которые отправляют из региона на экспорт, вместо того чтобы использовать для развития деревянного домостроения внутри страны.
Что касается компании «Светлица», то она может служить примером того, как можно собственными силами, без государственной поддержки или сторонней помощи, успешно выстроить производственный процесс с большим потенциалом.
Александр ТАМБИ,
д-р техн. наук, проф. каф. «Природообустройство»
Якутской государственной сельскохозяйственной академии