Veisto OY: от лесопиления к станкостроению
Лесопильное оборудование HewSaw для предприятий многих стран мира является стандартом в промышленной переработке тонкомерной древесины. За 70 лет существования компания из семейной фирмы выросла в одного из ведущих мировых производителей лесопильного оборудования.
В станкостроительной компании все новинки до запуска в серию отрабатываются на собственных лесопильных заводах, что позволяет постоянно совершенствовать оборудование.
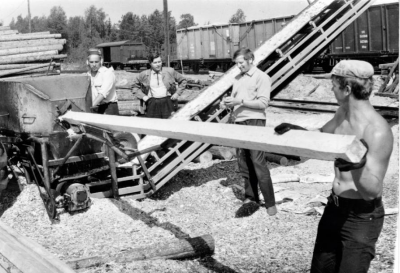
В 1950-х годах семья финских землевладельцев Раутио занималась сельским хозяйством, лесозаготовкой и обработкой древесины в Восточной Финляндии. Тогда одним из наиболее востребованных продуктов деревообработки в Финляндии был строительный конусный брус, который пользовался высоким спросом и экспортировался в Египет. Это брус традиционно обтесывался топорами вручную.
Для облегчения труда четыре брата Раутио построили механическую мастерскую, в которой проводили текущий ремонт оборудования, а в середине 1950-х, когда был накоплен опыт, наладили сборку тракторов для нужд своего предприятия и производство вспомогательного ручного инструмента.
С этой мастерской и началась история лесопильного оборудования HewSaw.
История компании
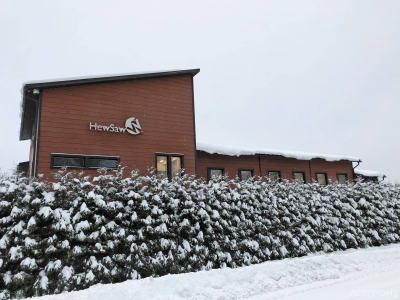
В 1964 году братья Раутио сконструировали и изготовили первый многопильный круглопильный станок для получения конусного бруса, его можно было эксплуатировать на лесных делянках. Для обеспечения станка электроэнергией была собрана генераторная станция, которая снабжала электричеством и весь рабочий поселок. Использование станка позволило значительно ускорить работу, и в том же году братья основали компанию KoneVeisto Rautio Oy, которая оказывала услуги по выпиловке бруса сторонним лесозаготовителям, но не продавала свои станки. В 1967 году в пос. Мянтюхарью построили цех по выпуску лесопильного оборудования. Было изготовлено несколько мобильных версий станка, которые монтировались на тракторные прицепы – так братья ездили по стране, выполняя подряды на распиловку. Конструкция станка постоянно совершенствовалась, и к 1970 году в Финляндии было организовано более 20 стационарных лесопильных пунктов, где использовались станки, часть которых уже работала по фрезерно-брусующей технологии. В середине 1970-х годов в Финляндии на этих станциях выпиливался почти весь объем бруса, поставлявшегося на экспорт в Египет, а их суммарная производительность позволяла выпускать до 300 тыс. м3 бруса в год.
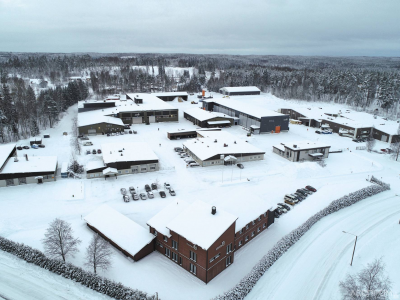
К концу 1970-х годов вследствие изменений в законодательстве и политической ситуации в Египте экспорт бруса из Финляндии туда почти прекратился, и компания оказалась в кризисном положении. Поскольку к тому моменту семья Раутио уже накопила опыт распиловки тонкомерной древесины, компания отказалась от предоставления услуг по ее раскрою и решила сфокусироваться на производстве лесопильного оборудования для обработки тонкомерного сырья. В посаженных после Второй мировой войны лесах уже наступало время рубок ухода, и на подобные станки, по мнению владельцев компании KoneVeisto Rautio Oy, ожидался высокий спрос.
В начале 1980-х годов был разработан прототип станка HewSaw R115, конструкция которого позволяла повысить качество обработки поверхности пиломатериалов и обеспечивала возможность установки дополнительных пил для раскроя бруса на доски. В те же годы в поселках Киссакоски и Коккосенлахти были пущены собственные лесопильные заводы компании, на которых не только вырабатывалась пилопродукция, но и проходили заводские испытания оборудования. На этих заводах компания впервые применила технологию криволинейного пиления, ставшую впоследствии стандартом технологии раскроя древесины на всех моделях станков HewSaw.
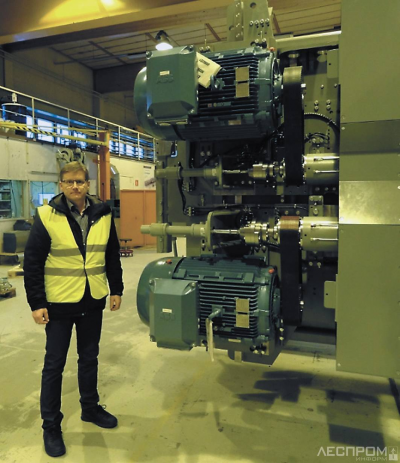
«Распиловка тонкомерного сырья –сложный процесс. В то время как конкуренты делали упор на производстве станков для переработки крупных сортиментов, в нашей компании внедрялись технологии, позволявшие сделать рентабельной переработку тонких лесоматериалов, – говорит Маркку Раутио, исполнительный директор компании Veisto Oy (в 2001 году компания KoneVeisto Rautio Oy стала называться Veisto Oy. – Прим. авт.). – Раскрой тонкомерных бревен должен выполняться на высокой скорости подачи, обеспечивающей высокую производительность, иначе стоимость пилопродукции будет неконкурентоспособной вследствие высокой себестоимости. Создание станка, на котором можно распиливать лесоматериалы на скорости более 100 м/мин, потребовало разработки большого числа вспомогательных конструкторских решений». Расчет на увеличение объемов заготавливаемой тонкомерной древесины в стране оказался верным, а высокая точность формы пиломатериалов и простота переработки круглых лесоматериалов с одновременным получением технологической щепы на высокой скорости подачи быстро привлекли к станку HewSaw R115 внимание лесопильных компаний.
В 1983 году первый станок HewSaw R115 был продан на один из лесопильных заводов в Финляндии, а с 1985 года начались продажи оборудования за рубеж: два станка были проданы в Норвегию.
В конце XX – начале XXI века сфера использования фрезерно-профилирующих станков и линий значительно расширилась. Сегодня в разных странах их применяют не только для распиловки тонкомерной древесины, но и для переработки пиловочного сырья среднего и большого диаметра.
Первые станки Veisto Oy, предназначенные для раскроя сортиментов с вершинным диаметром от 6 до 14 см, позволяли заказчикам эффективно перерабатывать молодую древесину, а также вершинные части хлыстов и выпускать тарные пиломатериалы, бруски для строительства изгородей, прокладки для штабелей пиломатериалов, а также мебельные заготовки. Ввиду малого диаметра сырья и невозможности выпиловки из тонкомерного бревна большого объема пиломатериалов для раскроя подобных сортиментов использовалось типовое оборудование, в состав которого входили фрезерно-брусующий модуль и пильный блок для распиловки бруса вразвал, дополняемый при раскрое бревен диаметром более 200 мм узлом фрезерования боковых досок. Разработанные компанией в 1990-е годы станки серии R200, конструкция которых позволяла использовать описанные выше возможности раскроя сырья, долгое время были визитной карточкой завода и завоевали репутацию универсального оборудования на тех рынках, куда поставлялась техника этого финского производителя.
Помимо HewSaw R200, в 1990 годы был создан станок HewSaw SL250; технические возможности этого оборудования позволяли перерабатывать пиловочные бревна диаметром до 420 мм, конструкция этих станков послужила основой для современных моделей техники. В те же годы фрезерно-брусующие линии стали компоноваться узлами фрезерования боковых досок, что обеспечило возможность выпиловки до четырех дополнительных обрезных досок из сбеговой зоны бревна.
Вовлечение в обработку толстомерной древесины, распиливаемой на большой скорости, потребовало модернизации фрезерно-брусующих головок для сохранения высокого качества вырабатываемой технологической щепы. Инженеры компании разработали новые фрезерные диски с четырьмя рядами спирально установленных ножей, обеспечивающих стабильность размера щепы при раскрое бревен большого диаметра.
С ростом популярности линий HewSaw SL, позволяющих одновременно выпускать пиломатериалы и технологическую щепу без использования обрезных систем, появился спрос на линии, обеспечивающие возможность раскроя пиловочника диаметром до 50 см в комле. Подобные линии, компонуемые из нескольких последовательно расположенных модулей, как правило, на базе станка SL250, используются для переработки древесины плантационного выращивания и востребованы в Южной Америке, Канаде, Новой Зеландии и Австралии. «В этих странах очень много толстомерной древесины, для переработки которой необходимо оборудование, позволяющее обрабатывать сырье на скорости подачи до 310 м/мин», – отмечает координатор экспорта компании Veisto Oy Лаура Нипули. Первые линии для переработки толстомерной древесины производства компании Veisto Oy были установлены на лесопильных предприятиях в Новой Зеландии еще в 2004 году.
За семь десятилетий компания из маленькой семейной фирмы превратилась в одного из ведущих мировых производителей лесопильного оборудования с оборотом 40–45 млн евро в год.
Станки, выпускаемые под торговой маркой HewSaw, работают больше чем на 350 лесопильных предприятиях мира. Объемный выход пиломатериалов на современных лесопильных фрезерно-профилирующих линиях в среднем составляет 50% объема неокоренного бревна.
Мощности завода позволяют ежегодно выпускать от 8 до 10 лесопильных линий, включая необходимые поворотные и загрузочные устройства. Средний срок изготовления лесопильной линии, состоящей из трех станков, зависит от загрузки завода и обычно не превышает шести месяцев.
Самые крупные и скоростные лесопильные заводы производства компании Veisto Oy работают в Канаде и Швеции, где ведется раскрой 6-метровых сортиментов на скорости подачи до 310 м/мин с вершинным диаметром 350 мм.
Рынки сбыта
«При создании оборудования для лесопильных предприятий разных стран используются разные конструкторские решения, что обусловлено различиями пород и условий произрастания, – говорит Маркку Раутио. – Расположение станкостроительного завода в Финляндии обеспечивает нам существенные выгоды, поскольку наше оборудование изначально было предназначено не для распиловки плотной, медленно растущей финской древесины. Поставляя станки в другие страны, где древесина менее плотная, особенно если она выращена плантационным способом, мы всегда уверены в достаточном запасе мощности оборудования.
В каждой стране свои особенности. В Северной Америке при раскрое толстомерной древесины необходимо использовать подвижные поставы пил на телескопных валах.
В Южном полушарии быстрорастущая древесина содержит смолу, свойства которой приводят к коррозии металла, что требует использования для станков толстых защитных кожухов из специальных сталей. Следует отметить разницу в объемах хлыстов, получаемых в результате заготовки деревьев одного и того же возраста в Финляндии и в странах Центральной Европы: в Центральной Европе объем хлыста в среднем на 10% больше. А если сравнивать с североамериканской древесиной, эта разница еще больше, поскольку деревья там растут быстрее. Этот фактор сокращает оборот рубки и требует использования высокоскоростного оборудования для обработки древесины. В Южной Америке заготавливают и распиливают древесину, достигшую 15 лет. Физико-механические характеристики получаемой из нее технологической щепы полностью соответствуют требованиям предприятий ЦБП, а для обеспечения распиловки большого объема тонкомерных бревен не обойтись без специализированного фрезерно-пильного оборудования. Информация об особенностях распиловки древесины в разных странах накапливается на заводе, систематизируется и используется при проектировании нового оборудования».
В основном поставки станков осуществляются в Финляндию, Швецию США и Канаду. На долю России приходится не более 15% объема оборудования, выпускаемого Veisto Oy. В последние годы растет число поставок в Южную Африку, Южную Америку, Австралию и Новую Зеландию.
Станкостроительное производство
Завод расположен на территории бывшего лесопильного предприятия, ранее также принадлежавшего компании Veisto Oy, и занимает 9 га, из которых 5 га отведены под крытые производственные помещения.
Отопление всех помещений обеспечивает котельная, в которой летом сжигают пеллеты, а зимой – топливную щепу.
На заводе изготавливаются все элементы станков за исключением электрических кабелей, автоматических датчиков, двигателей, цепей, степфидеров, подшипников и болтов. Комплектующие приобретаются только у европейских производителей, что позволяет исключить поставки контрафактной продукции. Ежегодно завод потребляет около 2 ГВт•ч электрической энергии.
Сварочный цех
Производство лесопильного оборудования начинается в сварочном цехе, где изготавливают несущие рамы. Площадь сварочного цеха, в котором принимается и хранится металл, составляет 2000 м2. Сталь для изготовления лесопильного оборудования поставляется в виде пластин стандартного размера – слэбов, а также в виде металлопроката круглого или прямоугольного сечения. Основные поставщики металла – финские и шведские сталелитейные компании. Некоторые виды стали приобретаются в Великобритании. При поступлении партии металла на завод проводится входной контроль его качества. Проверяется марка стали и ее твердость. Для слэбов и металлопроката каждого сорта предусмотрены свои места хранения.
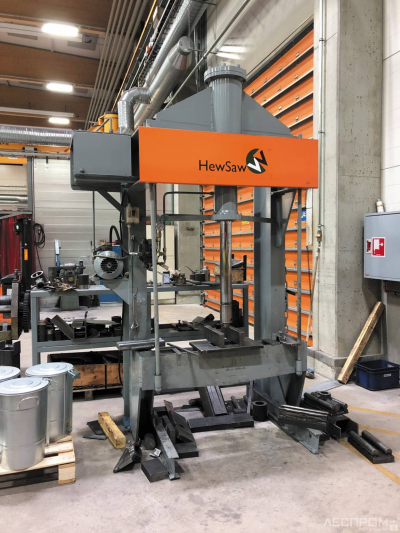
Металлопрокат распиливается по длине на двух ленточно-пильных станках: Meba и Kasto.
Резка металла осуществляется в этом же цехе с помощью гильотинных ножниц Aliko CNC 3016.
Для выполнения ряда операций, например, запрессовки подшипников и формования сложных профилей, на предприятии используются прессы собственного производства.
В цехе за каждым рабочим местом, отгороженным от других защитными шторами, закреплен свой инструмент. Все работы выполняются только в соответствии с чертежами. Для сварки стандартных изделий используются промышленные роботы производства компании ABB, программное обеспечение для которых создано специалистами Veisto Oy.
В сварочном цехе выполняется наиболее ответственная операция – изготовление рамы станка. На каркас будущей рамы устанавливаются вспомогательные микрометры, между которыми натягивается нить, указывающая центральную ось станка. На центральную ось будущего станка привариваются две пластинки, которые нельзя сдвигать и даже красить, потому что их местоположение служит ориентиром не только при установке всех компонентов на сборочных участках, но и при техническом или сервисном обслуживании станка у заказчика. Поскольку все лесопильные станки изготавливаются индивидуально, в соответствии с требованиями того или иного заказчика, запасные части для них можно изготовить только на заводе Veisto Oy.
К раме привариваются все несущие элементы, затем монтируются сборочные и сервисные люки, а также крепятся защитные кожухи, после чего она передается на следующий участок. В покрасочном цехе раму подвергают пескоструйной обработке, затем окрашивают, после чего к ней приваривают жесткий внешний каркас из металлических плит, толщина которых достигает 5 см. Каркас предназначен не только для обеспечения безопасности и защиты движущихся частей станка от пыли и инородных предметов, но и для повышения жесткости всей конструкции. Жесткий каркас обеспечивает возможность модернизации оборудования на площадке заказчика за счет установки более мощных двигателей или пильных блоков при возникновении необходимости повышения скорости подачи.
Механический участок
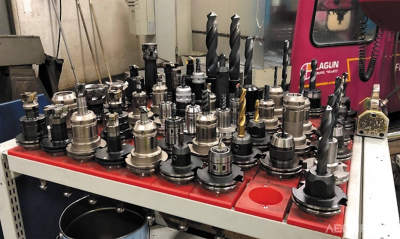
Все элементы станка изготавливаются на высокоточном оборудовании европейского производства. При выборе фрезерного и сверлильного оборудования собственники предприятия ориентировались на те модели металлообрабатывающих станков, которые используются в авиационной промышленности, поскольку их характеристики позволяют обеспечить высокую точность механической обработки, необходимую для изготовления современного высокоскоростного лесопильного оборудования.
Небольшие заготовки, такие как стаканы для вращающихся валов, обрабатываются на токарном станке Boehringer VDF 32 M и фрезерном станке Future 1800.
Детали большого размера и сложной формы обрабатываются на горизонтальных фрезерных станках с ЧПУ Burkhardt+Weber и роботизированных станках Fastems.
Даже если для очередного заказа необходимо изготовить всего одну деталь, на заводе их производят не менее десяти – для того чтобы снизить их себестоимость. Невостребованные для выполнения заказа элементы отправляются на склад и либо используются при сборке следующего станка, либо реализуются как запасные части.
Сборочный цех
Финишная сборка станков выполняется на специально подготовленной площадке, где исключены любые вибрации по внешним причинам. Основание площадки изготовлено из бетона, уложенного на металлическую подушку, которая, в свою очередь, опирается на заглубленные сваи, упирающиеся в скальные грунты под зданием завода.
На этой же площадке осуществляется проверка всех вращающихся элементов станка для выявления возможных вибраций в готовых изделиях.
Склад запасных частей
Площадь склада запасных частей – 1200 м2. Информация о каждом элементе, который хранится там, заносится в единую информационную складскую систему.
В зависимости от сроков службы каждой запчасти и ее востребованности лесопильными предприятиями установлено минимальное число хранящихся на складе деталей и узлов, а при сокращении этого числа до предельного автоматически формируется и передается на механический участок заказ на изготовление определенной детали. Кроме деталей собственного производства, на складе хранятся запасные части, которые поступают на завод от сторонних поставщиков и используются для производства станков и линий HewSaw. Такой подход позволяет сократить срок поставок запчастей для клиентов компании.
Технический контроль
Из каждой партии изготовленных деталей станков отбираются контрольные образцы; на трехкоординатном поверочном стенде, обеспечивающем точность измерений 0,1 мкм, осуществляется контроль их размеров и оценивается качество выполнения производственных операций.
На каждую деталь формируется паспорт качества, в котором отмечается дата ее выпуска и фиксируются данные работника, ее изготовившего, что предполагает персональную ответственность за каждую технологическую операцию. Такая система контроля полностью себя оправдала – объем брака на предприятии менее 1%.
Дереворежущий инструмент
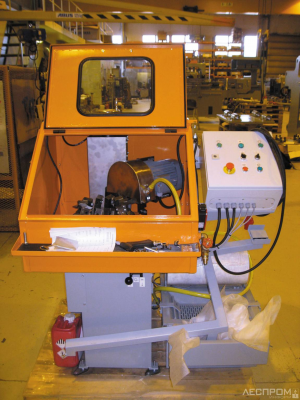
Фрезерные головки и ножи для их комплектования изготавливаются в отдельном цехе. Для производства ножей используется инструментальная сталь, поставляемая на завод из Австрии. Операции по закалке ножей полностью роботизированы. На участке используются два робота компании ABB, один из которых укладывает ножи на подающий стол линии закаливания, а другой снимает и укладывает их на подстопные места после термической обработки.
Пильный инструмент изготавливается по патентам Veisto Oy на заводах Финляндии и Канады, специализирующихся на производстве круглых пил. Все параметры инструмента: число зубьев, форму и размер их впадин, посадочные размеры и требуемую точность обработки – определяют инженеры станкостроительной компании, передавая исполнителю при заказе инструмента необходимые чертежи. Заточка комплектов ножей, поставляемых заказчикам вместе со станками, осуществляется на станке HewSaw RM12CW.
Вместе с лесопильным оборудованием обязательно поставляются станки для заточки фрезерных ножей, уже настроенные для правильной подготовки инструмента. На них можно затачивать до 12 ножей единовременно.
«Более 96% простоев или поломок оборудования так или иначе связаны с состоянием режущего инструмента, – отмечает Лаура Нипули. – Основные причины остановки оборудования: незаточенные или заточенные неверно пилы, отсутствие готовых к работе пил необходимого типоразмера, длительная замена инструмента. Эти проблемы характерны и для российских компаний и связаны с неправильной подготовкой инструмента к работе. Не на всех заводах есть современное оборудование для подготовки пил, а также квалифицированные работники. В Финляндии и странах Балтии многие заводы пользуются услугами сторонних фирм, специализирующихся на обслуживании дереворежущего инструмента, что позволяет гарантировать качество его подготовки. В России, где между заказчиком и исполнителем зачатую огромное расстояние, сегодня подобная схема невозможна.
Кроме того, на рынке режущего инструмента работает много компаний, которые выпускают контрафактную продукцию, не отвечающую стандартам качества и изготовленную с нарушениями технологии. Инструменты, изготовленные ими, дешевле, чем те, которые производят на предприятиях по всем правилам, но служат недолго и требуют частой заточки, что влечет остановки линий, частую смену ножей и в конечном итоге значительное снижение производительности оборудования».
Сервисное обслуживание
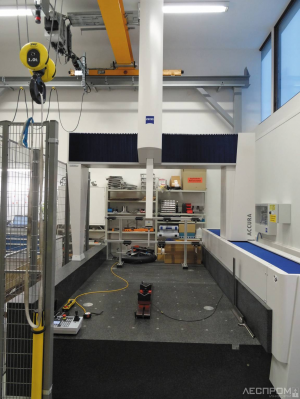
Все станки комплектуются системами телеметрии. В любой момент специалисты завода-изготовителя могут провести удаленную диагностику работы оборудования, проверить работу всех систем. Подобный подход в большинстве случаев позволяет выявить и исправить ошибки, возникающие в ходе эксплуатации оборудования, а также внести дополнения в программы управления без выезда инженеров на лесопильное предприятие, в результате чего существенно сокращаются простои. Наиболее актуально использование этой схемы при настройке измерительной системы Prologic, которой комплектуются линии HewSaw. Программа по составлению поставов, которые рассчитываются на основе результатов измерения формы бревна, разработана в Канаде. Без возможности внесения в нее через интернет необходимых заказчику доработок использование программного обеспечения стало бы невозможным.
Программное обеспечение
В современных лесопильных станках стоимость металла (хотя она довольно высока) не меняет принципиально их себестоимость. Самые большие затраты – до 50% стоимости оборудования – приходятся на программное обеспечение, системы автоматизации и электрическое оснащение.
Ключевой особенностью работы современных линий является полная автоматизация лесопиления. Оператор только контролирует производственный процесс для предотвращения внештатных ситуаций, связанных с возможным застреванием бревен в станках или падением пиломатериалов с транспортеров. Софтверное обеспечение для станков HewSaw разрабатывают штатные программисты Veisto Oy. В линейку программного обеспечения, предлагаемого заводом лесопильным предприятиям, входят программы по составлению поставов, а также решения для контроля и учета рабочего времени. Стандартные датчики, закупаемые на европейских заводах, также программируются на станкостроительном предприятии. Программы можно купить как вместе с новой линией, так и отдельно, в случае приобретения на рынке линии, бывшей в употреблении.
Поддержка б/у оборудования
Довольно часто собственники лесопильных предприятий, которые либо выработали лесосырьевую базу, либо хотят заменить технику более современной, продают на рынке оборудования станки HewSaw, бывшие в употреблении. Кроме того, многие лесозаготовители начинают организацию лесопильного производства именно с приобретения б/у оборудования, что позволяет им не только обеспечить быстрый пуск производства, но и впоследствии заменить его новым, уже зная нюансы работы машин, а также особенности сырья, которые необходимо учесть в техническом задании на изготовление нового станка. Подобные сделки проходят без участия завода-изготовителя, но о них становится известно, поскольку новые владельцы обращаются в компанию Veisto Oy за инструкциями и с просьбами об обучении персонала.
Завод, конечно, заинтересован в продаже нового оборудования, но то, что станки его производства выдерживают перемещение, установку и эксплуатацию на новых производствах, в Veisto Oy считают показателем надежности выпускаемой продукции. Компания предоставляет помощь в ревизии, пуске и модернизации подобных линий, но только при условии устранения всех неисправностей, которые выявляются при обязательном участии специалистов станкостроительного завода.
Кадровое обеспечение
Завод функционирует в круглосуточном режиме. Специалисты выходят на работу по смещенному графику, в соответствии с ходом технологического процесса. Всего на заводе работает 200 человек. Около половины – жители пос. Мянтюхарью, остальные приезжают на работу из близлежащих городов. В летний период, когда в школах и вузах каникулы, завод привлекает для выполнения разных работ более 20 детей сотрудников, а также студентов для прохождения практики, предусмотренной программами обучения в колледжах и вузах.
Большое внимание уделяется на предприятии технике безопасности. Сотрудники обязательно используют защитные средства и спецодежду, а также периодически подтверждают аттестационной комиссии знания техники безопасности. Кроме того, в компании разработана система стимулирования соблюдения правил безопасной работы. На территории предприятия установлено специальное информационное табло, на котором указано, сколько часов прошло с момента последнего инцидента, связанного с нарушением правил безопасной работы. При достижении 100 часов безопасной работы сотрудникам предприятия предоставляются бесплатные обеды и кофе-паузы за счет компании.
Направления развития
Рост стоимости сырья требует применения на лесопильных заводах все более экономичных линий, что может быть достигнуто только за счет повышения скорости подачи, точности базирования и раскроя сортиментов с максимальным объемным выходом при распиловке сырья тонкими пилами. Лесопильное оборудование должно обеспечивать не только точность формы пиломатериалов, но и стабильность фракционного состава технологической щепы, качеству которой в Финляндии, Швеции и странах Северной Америки уделяется повышенное внимание.
Совершенствование лесопильного оборудования в компании Veisto Oy ведется в направлении повышения точности базирования сортиментов и развития программного обеспечения, позволяющего оптимизировать лесопиление.
По оценкам компании, замена лесопильного оборудования, изготовленного по технологиям 10-летней давности, современными станками, возможности которых позволяют распиливать бревна подвижными поставами на телескопных валах (плавающими поставами) и обеспечивать высокую точность базирования сортиментов, выполняемого по критерию максимального объемного выхода, позволит оправдать инвестиции менее чем за год. Подобный эффект может быть достигнут только за счет увеличения объемного выхода продукции при неизменном объеме переработки круглых лесоматериалов.
В компании Veisto Oy разработана технология, позволяющая устанавливать на каждом из двух пильных валов нескольких поставов пил, что обеспечивает возможность изменения схемы раскроя каждого бревна в зависимости от его формы. При работе жестким поставом на валах могут быть установлены несколько одинаковых поставов, чтобы при затуплении инструмента не останавливать работу, а продолжать пилить сырье другими пилами.
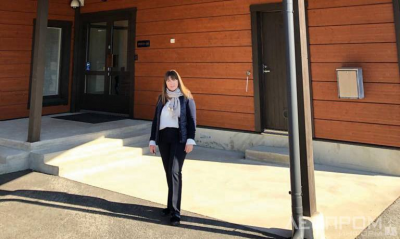
В ближайшие годы следует ожидать активного оснащения современных линий рентгеновскими установками, с помощью которых можно оценить внутреннюю структуру лесоматериалов перед раскроем и выбрать оптимальный постав для каждого бревна.
По мнению собственников завода, в скором будущем большое внимание в станкостроении и лесопилении будет уделяться развитию робототехники. На заводе уже эксплуатируют семь роботов производства компании ABB. Программированием роботов также занимаются специалисты Veisto Oy, что обеспечивает точную настройку всех выполняемых роботами операций. В настоящее время на заводе создается программное обеспечение еще для одного робота, который будет отвечать за заточку инструмента.
«По нашим данным, ни на одном лесопильном заводе в мире роботы пока не используются, хотя они уже могут выполнять большое число задач, – отмечает Лаура Нипули. – Клиенты скоро поймут, что использование роботов на некоторых операциях, в основном при подготовке дереворежущего инструмента к работе, не только выгоднее, чем привлечение квалифицированных специалистов, но и обеспечивает постоянство качества выполнения технологических операций. Компания Veisto Oy уже может предложить лесопильным компаниям роботов для выполнения целого ряда стандартных операций. Мы не только научились ими пользоваться, но и готовы их программировать в соответствии с нуждами предприятий. Мы хотим быть первыми на рынке поставок роботов для промышленных лесопильных предприятий. Компания уже заказала еще несколько роботов, которые будут использоваться для выполнения стандартных операций при сборке оборудования. Их внедрение в производственный процесс даст возможность расширить наши предложения для лесопильных заводов, а наши IT-специалисты разработают ПО еще для нескольких технологических операций».
Текст Александр Тамби, д-р техн. наук, проф. ЯГСХА
Фото: Александр Тамби, Юлия Валайне