Традиции, инновации, качество
Путешествие по Финляндии в поисках России
Наш журнал посвящен российскому лесопромышленному комплексу (хотя ни для кого не секрет, что сегодня отрасль работает и развивается в основном с помощью зарубежной технологической оснастки). Поэтому, приняв любезное приглашение компании «ИмпортТехСнаб» посетить два известных в мире финских предприятия, я прежде всего подумал о том, что их связывает с нашей страной.
И этих взаимосвязей обнаружилось даже больше, чем я ожидал! Но обо всем по порядку.
День первый. TKM TTT Finland Oy
Позади остается около 600 км дороги от Санкт-Петербурга на северо-запад, до заводских корпусов компании ТТТ в городе Aкaa, где меня уже ждут представители руководства компании: директор производства Яри Хакала, менеджер по продажам в России Вейо Маттила и технический специалист Тапио Койвисто. Проведенная ими экскурсия по оснащенному современным оборудованием производству и неформальное общение позволили многое узнать о компании, ее прошлом, настоящем и даже будущем.
Начало промышленной группе, в которую сейчас входит компания ТТТ, было положено в Германии в 1908 году, когда в г. Ремшайд открылось производство рубительных ножей. Постепенно ассортимент выпускаемого инструмента расширялся за счет обращения к новым отраслям промышленности – металло- и деревообработке, ЦБП, переработке отходов. IKS – так назывался этот бизнес, пока его владелец Томас Майер не объединил все компании группы под брендом TKM, который расшифровывается как The Knife Manufacturers – в буквальном переводе: «Производители ножей». В структуре TKM Group 12 предприятий, сотрудников около 1000 человек. Филиалы или партнеры холдинга действуют более чем в 50 странах.
«TKM ТТТ Finland Oy – дочерняя компания германского холдинга ТКМ со штаб-квартирой в городе Ремшайд, – поясняет Вейо Маттила. – Также в Германии работают три предприятия группы, еще два до недавнего времени располагались в разных районах Австрии. Год назад в рамках развития холдинга было принято решение о переносе производства из австрийского города Трайсмауер (где изготавливали пилы малых диаметров) на нашу площадку – и теперь здесь, в Финляндии, сосредоточено все производство дереворежущего инструмента, все наши компетенции и ноу-хау в сфере переработки древесины. Мы работаем по трем основным направлениям: инструмент для целлюлозно-бумажной промышленности, лесопиления и фанерного производства».
«Перенос мощностей из Австрии в Финляндию позволил на единой базе выпускать наиболее полный ассортимент деревообрабатывающего инструмента, – рассказывает Яри Хакала. – А также оптимизировать логистику сырья и готовой продукции, максимально использовать наш технологический потенциал, знания и опыт. Мы внедрили в производство самое современное автоматизированное оборудование, поступившее из Австрии. В одной локации стало гораздо проще контролировать весь рабочий процесс. В результате этого слияния объем производства дисковых пил в ТТТ увеличился в 2,5 раза (в штуках)».
Финская компания ТТТ к моменту вхождения в группу (2005) была уже хорошо известна на международном рынке под названием TTT Technology Oy Ab. Основанный в 1961 году завод режущего инструмента в Акаа приобрел хорошую репутацию за счет высокого качества и широкого ассортимента продукции, например круглых пил большого (до 2,45 м) диаметра. Стоит отметить, что именно Россия, советские целлюлозно-бумажные комбинаты и лесозаводы сыграли важную роль на этапе становления предприятия. Сейчас в Россию экспортируется примерно 15% продукции.
«В России нас представляют давние и надежные партнеры: "ИмпортТехСнаб" в лесопильной промышленности, "Бум Техно" в целлюлозно-бумажной промышленности и "СФТ Сервис" – в фанерной. В них работают настоящие профессионалы, мы довольны этим долгосрочным сотрудничеством, – говорит Вейо Маттила. – Вообще у нас четыре основных рынка сбыта: домашний рынок Финляндии, Россия, Южная Америка и Центральная Европа».
На площадке в Акаа размещается производство, отдел продаж, центр инженерных разработок и администрация. Предприятие работает частично в трехсменном режиме. В двух производственных цехах работает примерно 200 станков. В одном цехе выпускаются длинные и короткие ножи для линий лущения, рубительных машин и другого назначения, а также изнашиваемые части машин с упрочняющим покрытием, в другом, на оборудовании, перевезенном из Австрии, – круглые пилы.
«Успех инструмента складывается из трех слагаемых: качественного сырья, уровня используемого оборудования и методов обработки, – считает Вейо Маттила. – Продукция компании чаще всего кастомизирована согласно потребностям клиента.
Среди наших преимуществ не только высококачественный готовый продукт, но и большой инженерный опыт, мы знаем, как решить любую проблему, которая может возникнуть у клиента с инструментом. И прежде всего в этом мы видим свою роль. Глубокие технические знания позволяют нам быть не просто поставщиком, а еще и экспертом-консультантом для клиентов».
«Мы продаем в большей степени знания, нежели продукцию, – добавляет Тапио Койвисто. – Наши сильные стороны – это возможность быстро реагировать на любые запросы клиентов, широкий ассортимент продукции, индивидуальный подход к каждому проекту и покупателю. Сейчас заказы различаются настолько, что, наверное, уже нельзя сказать, что мы выпускаем стандартную продукцию: каждое наше изделие – кастомизированный продукт. А это диктует необходимость быть гибкими на каждом этапе работы: при планировании, инжиниринге и производстве изделий».
Поскольку инструмент изготавливается на заказ, как такового, склада продукции на заводе нет – только площадка для отгрузки. Отмечая, что продукция компании не относится к дешевому сегменту, мои собеседники не раз и не два акцентировали, что ТТТ предлагает прежде всего комплексные решения по внедрению и использованию на производстве высококлассного режущего инструмента, производя, в том числе и под заказ, самые нестандартные варианты по запросу клиента. Безусловно, это не может не сказываться на ценах, которые, впрочем, с учетом «долгожительства» и эффективности эксплуатации инструмента оказываются более чем доступными для пользователей. И это уже мнение не производителя, а клиентов ТТТ.
«Сегодня продать инструмент, даже самый высококачественный, – это лишь часть дела, – полагает Яри Хакала. – Мы должны обеспечить его максимально эффективную, долгую и безаварийную работу и помогать покупателю, используя свои знания и навыки. Мы предлагаем комплексные решения, делимся с заказчиками своими ноу-хау. С каждым годом это становится все важнее».
«Возьмем российский рынок, – предлагает Вейо Маттила. – Многим лесоперерабатывающим предприятиям приходится работать в суровых северных условиях, и это требует особого внимания к качеству оборудования и инструмента, его особым свойствам, соответствующим условиям эксплуатации. Клиент обращается к нам со своей индивидуальной задачей, и мы совместными усилиями решаем ее – от разработки проекта до его воплощения в металле».
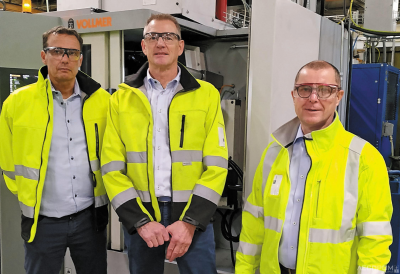
«В последние годы в нашем сегменте появляется все больше дешевой продукции – мы не можем этого не замечать, но не испытываем большого беспокойства по этому поводу, – говорит Яри Хакала. – Тут не возникает конкуренции как таковой. Ведь дешевый инструмент – он и есть дешевый, это предполагает в первую очередь его невысокое качество. А стоимость оборудования, сырья, вынужденных простоев в деревообработке настолько высокая, что рачительный хозяин просто не может позволить себе покупать некачественный инструмент, даже потратив меньше. Поэтому наш главный приоритет именно качество, отслеживаемое на каждом этапе производства. Добросовестно изготовленный из наилучших материалов инструмент прослужит верой и правдой настолько долго, что в конечном итоге его стоимость с лихвой окупится.
Мы не стремимся удешевить свою продукцию любой ценой, как это делают некоторые производители. Наши клиенты – профессионалы, и рассуждают как профессионалы. Я не припомню, чтобы покупатель интересовался исключительно ценами в прайс-листе. Ему важны функциональность, надежность, эффективность и долговечность. Именно на этих характеристиках базируется понимание конечной цены инструмента, который мы создаем.
Для изготовления инструмента мы используем высококачественную инструментальную сталь, в процессе обработки применяем прессование, лазерную резку, несколько различных методов закалки и отпуска металла, добиваясь высочайших прочностных и режущих свойств. Инструмент обязательно тестируется, в том числе с помощью электронного микроскопа. Каждое изделие проходит испытание механическими методами. Перед упаковкой супервайзеры проводят тщательный визуальный контроль. На производстве работают как классические станки с мануальным управлением, так и машины с ЧПУ. Самый современный станочный парк и высокопрофессиональные работники обеспечивают высокое качество продукции».
Вейо Маттила отмечает: «Чем дальше, тем больше производители фокусируются на перспективах, а значит, все большее значение приобретают вопросы сервиса, эксплуатации техники, послепродажного обслуживания. Движется в этом направлении и наш бизнес». Например, в Финляндии ТТТ предлагает клиентам комплексное сервисное обслуживание и в лесопильной, и в целлюлозно-бумажной, и в фанерной промышленности. Оно включает доставку инструмента от клиентов, а по завершении обслуживания отправку его назад, на место эксплуатации, заточку, шлифовку, ремонт инструмента и, если необходимо, замену.
Прощаясь, Вейо Маттила еще раз напомнил, что Россия для ТТТ – важнейший экспортный рынок, где компания хочет и считает необходимым присутствовать, предлагая производителям разнообразной продукции из древесины (и не только) лучший режущий инструмент и кастомизированные комплексные решения по его наиболее эффективной эксплуатации: «Мы давно и успешно работаем в России, стараясь быть неизменно надежным партнером, не только поставщиком, но и экспертом-консультантом для наших нынешних и потенциальных клиентов».
День второй. FB Ketju Oy
Девиз Never Stop Moving (в переводе «Никогда не прекращая движение») как нельзя лучше подходит компании FB Ketju: и бизнес этот находится в непрерывном развитии, и выпускаемые на двух финских предприятиях, которые мне довелось посетить, конвейерные цепи предназначены именно для этого – работы без остановки.
FB Ketju является частью FB Group, представленной компаниями в семи странах Европы (Швеции, Норвегии, Великобритании, Германии, Австрии, Финляндии). 170 сотрудников, годовой оборот свыше €50 млн. Выпуск продукции организован в Финляндии и Швеции, остальные подразделения занимаются продажами и подготовкой комплектующих для основного производства. Владелец FB Group и еще 120 компаний в 20 странах мира (в Финляндии 18 компаний) с персоналом 2700 человек – шведский концерн Addtech AB с годовым оборотом более одного миллиарда евро.
История компании восходит к 70-м годам XIX века, когда Адольф Фредрик Хеденгран основал в Эскильстуне, в Швеции, фабрику по производству изделий из чугуна и стали. В 1908 году компанию приобрела недавно созданная Eskilstuna Fabriks AB. Под этой маркой в 1912 году были впервые изготовлены конвейерные цепи.
А в Финляндии производство конвейерных цепей наладили в 1945 году под маркой Ammus Oy. Тогда же осуществили первые поставки в СССР. Да, собственно, именно они – сперва в рамках военной контрибуции победителям во Второй мировой войне – и положили начало этому бизнесу, помогавшему возрождать разрушенное хозяйство. С тех пор добротную продукцию FB Ketju знают в нашей стране.
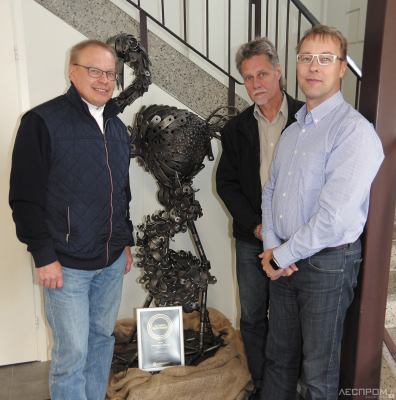
Компания работала, ее владельцы и названия менялись. В 1985 году завод в Кёйлио, принадлежавший тогда Huhtamaki, приобрела группа FB. Группа продолжала выпускать конвейерные цепи и в Швеции, и в Финляндии до конца 1990-х годов, когда все производство было окончательно перенесено на модернизированный завод в Кёйлио.
Об основных приоритетах компании говорит ее генеральный директор Матти Веккели: «Прежде всего это неизменное высочайшее качество продукции. Потом умение оперативно решать любые проблемы клиентов. И наконец, постоянные инновации, без которых невозможно развитие и движение вперед. Мы неустанно ищем новые пути для достижения лучших результатов и стремимся быть поставщиками не просто конвейерных цепей, а комплексных инжиниринговых решений».
«Еще одна характерная черта FB Ketju – гибкость, – уверен Петри Хейно, руководитель направления Восточной Европы. – Компания готова производить очень маленькие партии изделий в самые короткие сроки, чем едва ли могут похвастать конкуренты. Мы готовы принять заказ хоть на метр цепи, хоть на километр. Вообще, я обычно говорю так: цепь начинается с двух звеньев, значит, таким может быть минимальный заказ нашего клиента».
«В этой шутке очень большая доля правды, – кивая, соглашается директор по продажам Мика Суоми. – Мы стараемся отвечать на любые запросы и идти навстречу всем, в отличие от многих других производителей, которые могут отказать в продаже цепи короче 15 метров».
Линейка продукции предприятия – звездочки для цепей, конвейерные цепи, втулки, аттачменты, соединения, специальные изделия. В будущем планируется также реализация роликовых цепей. Конвейерные цепи предлагаются стандартного типа, специальные, а также под заказ по запросам клиента.
«Наши цепи чаще всего прибретают для цементных и металлических заводов, горнодобывающих и деревообрабатывающих предприятий, энергетических объектов, предприятий ЦБП и по переработке вторичного сырья, – рассказывает Матти Веккели. – Пожалуй, лучше всего FB Ketju известна в лесоперерабатывающем секторе, ведь там транспортные цепи нужны практически на каждом этапе – от загрузки и сортировки сырья до сушки и выгрузки готовой продукции.
А наиболее быстрорастущая в последнее время индустрия – переработка мусора, рециклинг. В ней мы тоже занимаем все более прочное положение».
Портфель заказов завода расписан на два года вперед. Обычный срок ожидания заказа 4–6 недель. В сентябре 2019 года был достигнут рекорд: самый высокий уровень производства за 75 лет работы. Прирост к норме составил 30%!
Предприятие использует исключительно европейское металлическое сырье. «Совместно с ведущими производителями стали в Скандинавии и департаментом сварки Университета Лаппеенранты мы разрабатываем спецификации материалов, из которых потом изготавливаем конвейерные цепи. Продукция выпускается с использованием автоматических сборочных машин и сварочных роботов», – поясняет Мика Суоми. Интересная особенность: для изготовления боковых пластин цепей используется немецкая сталь, для втулок – шведская, для штифтов – финская. Такая комбинация обеспечивает, по мнению Петри Хейно, наилучший результат, несмотря на то что это не самый простой и не дешевый вариант. Выбираются только те марки стали, которые оптимальны для сварки – ведь сварные цепи являются достоинством продуктов компании – а также для температурной обработки и закаливания (внешнего температурного воздействия).
За последние годы удвоился объем металлического сырья, используемого предприятием. Он мог быть еще больше, но поставщики не всегда успевают за ростом производства FB Ketju.
«Вот только в августе завершился начавшийся в апреле переезд из Кёйлио в Лаппи линии сборки компонентов, – рассказывает Мика Суоми. – Две наши производственные площадки разделяют 25 км. На "старой", в Кёйлио, осталось производство компонентов цепей и склады – как сырья, так и частично готовой продукции. Основная сборочная линия работает теперь на новом месте. И имеющиеся резервы площади позволяют и дальше расширять производство. Причем все здания не арендуются, а находятся в собственности компании».
Лаппи – небольшое поселение в 20 км от портового города Раума и примерно в 100 км от Турку. Производственные площади FB Ketju там составляют около 6 тыс. м2 (в Кёйлио – чуть более 3 тыс. м2).
В дальнейшем, по плану руководства, будут работать обе производственные площадки – переносить все производство не планируется. Логистическая цепочка отработана: основные операции металлообработки выполняются в Кёйлио, затем компоненты цепей перевозятся для сварочных, сборочных и финишных работ в Лаппи.
Моим сопровождающим по цехам обоих заводов стал Петри Хейно, представляющий компанию в странах Восточной Европы. Кроме производственных помещений и станций роботизированной сварки, мы побывали в огромном зале (назвать его складом было бы неравильно), отведенном для стандартных цепей, широкий ассортимент которых всегда стараются иметь в наличии. Но сегодня зал почти пустой!
«Бывает, тут все заполнено готовой продукцией, и меня немного беспокоит, что сегодня это не так, потому что спрос стал гораздо выше наших производственных возможностей, – делится Петри Хейно. – Это вроде бы хорошо – продукция расходится как горячие пирожки, а вместе с тем и плохо: поскольку спрос все еще превышает предложение, мы не можем удовлетворить все запросы клиентов».
Ежегодно компания производит 3–4 тыс. км цепей при полной загрузке производства. Руководство намерено в течение нескольких ближайших лет существенно нарастить объемы выпуска. Также на территории завода в Лаппи планируют выделить зону для сервиса и ремонта цепей с отдельной сварочной станцией.
Прочность цепей, выпускаемых компанией FB, обеспечивается за счет свойств материала и точности штамповки пластин конвейерных цепей со строго цилиндрической формой отверстий под штифт – при выборке под прямым углом штифт точно сопрягается с боковыми пластинами, обеспечивая идеальную плотность контакта элементов цепи. В результате повышается стойкость звеньев к нагрузкам. «Конкуренты используют другие углы, это проще и дешевле, - поясняет Петри, – но именно прямой угол позволяет создать надежное и прочное соединение».
Еще один ресурс стойкости – индукционная закалка элементов конвейерных цепей. Применение такого технологического решения позволяет увеличить усилие запрессовки штифтов в пластины и повысить общую прочность цепной оснастки. Индукционная обработка вызывает так называемое сжатие поверхности и увеличение глубины твердости углеродистой стали, тогда как ядро металла воздействию индукционного тока не подвергается и внутри детали не подвергаются воздействию индукционного тока и остаются пластичными, что и обуславливает стойкость к ударам и прочим динамическим нагрузкам.
В компании FB Ketju не скрывают, что отдают предпочтение сварным соединениям. Использование конвейерной цепи со сварными штифтами уменьшает общие габариты и массу конвейера. Кроме того, сварные компоненты прочнее штампованных и обеспечивают долговечность конвейерных цепей. Преимуществом цепей со сварными штифтами является высокая устойчивость не только к ударам, но и к разрывным нагрузкам.
На заводе в Кёйлио в отдельном помещении организован испытательный стенд для тестирования изделий на разрыв и другие механические деформации. Тесты наиболее ярко демонстрируют преимущества сварных цепей перед штампованными: сварная цепь из закаленных пластин с маркировкой М630 (то есть номинально рассчитанная на усилие 630 кН) выдерживает максимальное усилие на разрыв, которое может создать оборудование (1000 кН), порвать ее так и не удалось! Штампованная цепь 315 по результатам тестов показывает запас прочности около 330 кН, тогда как сварная аналогичной модели – 475 кН...
Согласно известной поговорке, рвется, где тонко. И на продемонстрированных примерах я смог убедиться в том, что звенья рвутся в наиболее тонких местах, ломаются штифты, но сварное соединение при этом остается целым!
«Вот потому мы и рекомендуем клиентам использовать сварные цепи – они на 30–50% прочнее», – уверяет Петри.
Для контроля качества сварки в специальной лаборатории в Тампере был проведен анализ среза готового изделия, безукоризненность швов подтвердил осмотр под электронным микроскопом. Да, 75-летний опыт сварки и металлообработки – не шутка!
Но все когда-нибудь кончается. Проведя подробную экскурсию по заводам FB Ketju в Лаппи и Кёйлио, Петри Хейно, провожая меня, подытожил: «С первого взгляда можно решить, что мы здесь только соединяем тяжелые железки. И в самом деле, цепи – это всего лишь скрепленные металлические детали. Но все не так просто: важно знать, КАК их скрепить. И не забывать делать упор на качество».
TKM TTT Finland Oy производит сотни видов режущих инструментов для всех процессов деревопереработки. Производственные и складские площади – 11 900 м2. В компании работает около 150 человек. Ежегодно TKM TTT Finland выпускает и продает продукцию примерно на €15–17 млн. Потребление инструментальной стали – 500–600 т в год. ТТТ поставляет инструмент и конечным клиентам, и машиностроителям (O.E.M). Продукцию предприятия используют такие известные бренды, как HewSaw, Linck, Heinola, Söderhamn-Eriksson, AriVislanda, EWD, Raute, Plytec, Andritz, Valmet и др.
FB Ketju – крупнейший производитель конвейерных цепей в Скандинавии и ведущий производитель сварных цепей в Европе. Оборот предприятия – €12 млн. На двух заводах FB Ketju работают 70 человек. Производство сертифицировано по стандартам ISO 9001, ISO 14001.
75% продукции заводов экспортируется более чем в 30 стран мира. Самые крупные клиенты: Valmet, Andritz, Stora Enso, UPM, Arauco, Sandvik, UPM и др.
В Финляндии продается 27% продукции, а в соседнюю Швецию уходит 23%. На Россию приходится 3–4% экспорта, но руководство завода видит возможность увеличить этот показатель до 20%.
Справка
Цепи FB специально спроектированы с учетом высоких требований лесопильных заводов и широко используются в конвейерах подачи бревен, конвейерах сортировки бревен, токарных станках, системах штабелирования, сортировке по размерам, переработке древесной щепы и пиломатериалов. В биоэнергетике они применяются для транспортировки различных видов биотоплива, а также для удаления золы и коры.
Текст и фото Максим Пирус