Holz House: деревянному домостроению – быть!
Как организовано передовое производство клееного бруса в Кировской области
Знающие люди говорят, что Кировская область на карте России напоминает петуха с раскинутыми крыльями. Если приглядеться и включить на полную воображение, сходство с птицей есть. Столица региона занимает правильное место где-то в центре «туловища», а мой путь лежал на север, туда, где кировский кочет старательно тянет голову на длинной шее в направлении Архангельской области и Коми. По приглашению руководства компании Holz House я ехал в поселок Луза, рядом с которым расположен ее завод – одно из крупнейших предприятий отечественного деревянного домостроения.
В те дни, на которые выпала эта командировка, Луза масштабно отмечала Масленицу. Как градообразующее предприятие, компания активно участвовала в празднествах: силами Holz House из Кирова в поселок привезли целый автобус артистов (который благополучно сломался посреди совсем неблагополучной автодороги, но певцов и танцоров бросились спасать, и справились удивительно оперативно), устроили каток и крытые раздевалки с бесплатным прокатом коньков. На мероприятиях такого рода в Holz House не привыкли экономить, ведь на предприятии работают многие жители Лузы.
Завод в Лузе
На подъезде к производственной площадке оказываешься будто в зоне давних военных действий: по сторонам дороги там и сям видны руины зданий с темными провалами окон, трубы и опоры несуществующих магистралей. Во времена СССР здесь был огромный Лузский ЛПК, который в лихие «нулевые» довели до банкротства. Заняв часть принадлежавших лесопромышленному гиганту площадей, компания Holz House фактически стала его преемником и возрождает деревообработку, да и вообще полноценную жизнь монопоселка в кировской глубинке.
За декорациями военного фильма вдруг открываются возведенные с нуля аккуратные производственные корпуса, обширная биржа сырья и оригинальное здание заводоуправления: к официальному открытию завода 23 апреля 2017 года за рекордные 12 дней на территории был построен дом по традиционной брусовой технологии, который в дальнейшем, для демонстрации возможностей предприятия, дополнили еще одним модулем по технологии фахверка. Сейчас здесь размещаются офис администрации и бухгалтерия.
Лесозаготовка
«Я отвечаю за заготовку и вывозку древесины, – представился исполнительный директор завода Василий Гладышев. – Получить и освоить лесфонд – важнейшее дело, ведь без этого никакое деревообрабатывающее производство немыслимо. Арендуем участки в двух лесничествах: Лальском и Папуловском, самые дальние лесные делянки располагаются в Боровице. Максимальное плечо вывозки – 130 км. Хлысты на делянках небольшого диаметра (в среднем, 26–28 см), зато плотность насаждений большая.
Работаем в лесу уже три года. Первый год заготавливали вручную, нанимали людей со стороны – до 12 бригад. Потом приобрели три лесозаготовительных комплекса John Deere (харвестер G1270 и форвардер G1210). Их технологические возможности по сей день превышают наши потребности в заготовке, поэтому зачастую еще успеваем оказать помощь в заготовке сторонним заказчикам. Сервис машин осуществляет компания «Трактородеталь», их специалисты выезжают на делянки при необходимости.
Стараемся использовать комплексы круглый год. Заготовка идет ритмично, на сортиментных комплексах вахтами работает слаженная команда: приглашаем из Архангельской области, Республики Коми опытных знающих операторов – в месяц они вырабатывают по 10 тыс. м3 на комплекс.
На вывозке леса работают 12 длиннобазных машин Volvo и Scania с загрузкой до 60 м3, а также МАЗ и КамАЗ (восемь единиц, используемых для перевозки между делянками). Для прокладки лесных дорог используем вспомогательную технику: два бульдозера и экскаватор.
Сейчас на заводе создан достаточный на пару месяцев работы запас древесного сырья, около 45 тыс. м3. Заготовленную древесину обрабатываем сертифицированным антисептиком, защищая от паразитов и синевы.
Для проведения лесохозяйственных работ создана бригада из шести человек, которая зимой принимает участие в заготовках, а летом занимается посадками и уходом за саженцами. По договору аренды выполняется 20 видов работ: подготовка почвы, создание минерализованных полос, осветление, прореживание и т. д.
В полном объеме проводим лесовосстановление. Посадочный материал стараемся брать из местных питомников (в том числе в Лузе, где теплицы организованы на мощностях местного лесхоза), он лучше приживается.
Собственная заготовка обеспечивает только 40% потребностей завода, остальное сырье покупается в виде пиловочника и леса на корню с аукционов. Партнерские отношения связывают нас с Группой «Илим», у которой мы в основном и закупаем недостающее хвойное сырье. Необходимо искать дополнительные лесные ресурсы, увеличивать расчетную лесосеку, сейчас решаем эти вопросы, ведем переговоры. Помимо этого, надо увеличивать эффективность, глубину переработки древесины – и по большей части продавать не пиломатериалы, а клееную продукцию с высокой добавленной стоимостью».
Немного истории
«Надо заметить, леса, как и производственная площадка, достались нам в своеобразное наследство от Лузского ЛПК – те, что не успели выпилить для нужд огромного комбината из 23 цехов с потреблением 1 млн м3 в год. Он проработал больше 70 лет и закрылся в 2006 году, сейчас наш завод занимает только небольшую часть его территории. Я начинал работать еще на том комбинате, – продолжает рассказ Василий Гладышев. – После банкротства Лузского ЛПК активы были распроданы, лучшие кадры отправились искать работу в других местах, а нам достались фактически пустая площадка и отсутствие квалифицированного персонала, а те работники, что остались, утратили веру в серьезность работодателей. Доверие местных жителей Holz House пришлось долго и не всегда просто завоевывать. А сегодня у нас работает фактически вся местная молодежь».
«Когда компания Holz House заходила на эту площадку в мае 2016 года, кроме заброшенных корпусов прежнего завода, тут не было ничего, – присоединился к разговору главный инженер завода в Лузе Андрей Хаустов. – Все, что можно было, разобрали и растащили. Пространство заросло молодым березняком – и первой задачей для создания производства стало: пилить, корчевать, вывозить. А потом на площадку заехали 70 фур: 56 с оборудованием для будущего завода, плюс строительные материалы. И уже к декабрю в этом "чистом поле" выросли новые цеха с собранными технологическими линиями, две сушильные камеры, котельная с одним котлом и линия сортировки круглого леса. Всего за какие-то полгода!»
Лесопиление
В производстве используется древесина сосны и ели (попутно заготавливаемая на делянках лиственная древесина продается в круглом виде производителям фанеры и др.).
На уличной площадке завода в момент моего посещения было примерно 6–7 тыс. м3 пиломатериалов, готовых к отгрузке. Кроме того, здесь помещается до 12 тыс. м3 древесного сырья.
Кругляк с биржи сырья подается на линию сортировки с 24 карманами (производство компании «ДТМ», Киров) с помощью перегружателя Liebherr 924 сортируется по диаметрам (минимальный – 10мм) и качеству. Далее на каждый постав подается бревно определенного диаметра. Затем распиловка с получением обрезного пиломатериала и технологической щепы, которая в железнодорожных вагонах направляется на ЦБК (главным образом, на Котласский, а также на Приволжский, в Нижегородской области).
Собственно линия лесопиления начинается с окорочного станка. «Требования к щепе у покупателей очень серьезные, поэтому окорка должна выполняться очень качественно, – поясняет Андрей Хаустов. – Ни на пиломатериалах, ни на щепе коры ни в коем случае оставаться не должно. Поэтому мы вместо одного поставили последовательно два окорочных станка: Linck и Cambio». Технику компании Cambio местные инженеры модернизировали: дополнительный ротор позволяет производить доокорку для лучшей очистки от коры.
Снятая кора транспортером выводится из процесса и направляется в отвалы, еще один транспортер перемещает к ситу щепу и опилки, образующиеся при распиловке (они утилизируются в котельной, вырабатывающей тепловую энергию для нагрева сушильного комплекса и отопления цехов).
Проектирование технологической линии и инжиниринг взяла на себя австрийская компания WDT. «Наше пожелание было – сделать все как можно компактнее, – поясняет главный инженер. – Мы вместе оптимизировали классическую схему и в результате сумели расположить оборудование на минимальной площади, но с максимальным удобством пользования».
Управление всей фрезерно-пильной линией (оборудование производства EWD) и контроль за ней осуществляются из оснащенной компьютерами операторской; в смене оператор с помощником. Работа в цеху идет в трехсменном режиме. Дополнительный персонал требуется на укладке боковой доски (два человека) и подобных операциях.
При первичной фрезеровке снимается горбыль и измельчается в щепу, которая ссыпается вниз, на транспортер для сбора отходов. С первого прохода выпиливается боковая подгорбыльная доска и выводится ленточным транспортером за переделы цеха. Далее материал кантуется и по аналогичной схеме с выпиливанием боковой доски осуществляется второй проход. Полученная центральная доска направляется на штабелеформирующую машину, где в автоматическом режиме укладывается сушильный штабель 1800 х 1800 мм (В х Ш). Линию формирования штабелей обслуживают три человека в смену. Готовый штабель с помощью вилочного погрузчика транспортируется в сушильные камеры (на заводе используется сушильное оборудование итальянской компании Incoplan и кировской «Энергоавтоматики»). Сушильный комплекс состоит из 16 камер по 120 м3. Цикл сушки составляет от двух суток (для доски 14 мм) до десяти (для доски 60 мм, применяемой в домостроении) до влажности 8–10% на выходе.
После сушки производится сортировка сухих пиломатериалов на трех столах с визуальным контролем трех операторов в отдельной кабине.
В планах руководства установка на линии автоматизированного сканирующего оборудования.
Доски торцуются триммером (30 пил) в необходимую длину и раскладываются в 24 кармана по сортам/сечению/длине. Линия сортировки пиломатериалов, как и штабелеформирующая машина, от финского производителя Heinola. За смену по линии проходит от 200 до 300 м3 сухих пиломатериалов. По мере накопления пакетов карманы опускаются, пиломатериалы извлекаются, маркируются, упаковываются и передаются для отгрузки потребителям.
В котельной предприятия суммарной мощностью 7 МВт установлены три котла компании «Теплоресурс». Опил доставляется транспортером в бункеры-накопители, откуда подается в топки котлов. Контроль и регулировка режимов горения осуществляются автоматически, за процессом следит один оператор в смену. Оборудованием, по словам главного инженера, на заводе довольны: надежное и нетребовательное.
Первых операторов фрезерно-пильной линии обучал австрийский специалист, осуществлявший шеф-монтаж. Впоследствии этим занимались уже главный инженер, механик, главный энергетик и другие руководители предприятия. «С кадрами было, конечно, очень тяжело, – признает Андрей Хаустов. – Но постепенно местные жители начали откликаться на вакансии, и нам удалось сформировать костяк коллектива из тех, кто участвовал в первых работах на площадке и запуске, – с монтажа оборудования они перешли на производство, встали к станкам. Это хороший опыт, мы и теперь стараемся максимально вовлекать местных жителей, начиная с базовых позиций, позволяем им набираться опыта и учиться у знающих работников».
За цехом лесопиления находится железнодорожный тупик и погрузочная площадка, где пакеты пиломатериалов в контейнерах с помощью специального подъемного стола грузятся на ж.-д. платформы для отправки (до 12 шт. в день) в порт Петербурга, откуда морем идут на экспорт.
С завода в месяц уходит от 40 до 60 вагонов щепы для нужд ЦБК.
Чтобы организовать отправку продукции по железной дороге, компании пришлось фактически с нуля создавать свою ветку от магистрали – прежнюю дорогу к моменту основания предприятия полностью демонтировали и растащили: ни рельсов не сохранилось, ни шпал...
«За время работы завода продуктивность лесопиления повысилась на 25%. И ни одного кубометра мы не продали кругляком», – с гордостью говорит Василий Гладышев.
Производство клееного бруса
Во дворе, у входа в цех клееного бруса, высится шестиметровый «миньон», знакомый всем по диснеевскому мультфильму Despicаble Me: в глазастое ярко-желтое существо работники при полной поддержке руководства превратили промышленный ресивер (емкость для воздуха под давлением). И приехавшие на церемонию пуска завода высокие гости радостно фотографировались с мультяшным исполином, сегодня видимым чуть ли не с любой точки предприятия.
«В этом цеху мы производим как стандартный клееный брус (минимальное сечение 140 х 140, чаще всего 180 х 200), так и знаменитый мегабрус – сечением до 280 х 360 мм, – рассказывает начальник цеха Артем Собенин. – В России больше нигде такой не выпускают. Производство бруса большого сечения запустили с год назад, а максимального сечения – с декабря. Первый дом из такого бруса уже построен в Подмосковье».
Изначально выстроить приобретенную линию Weinig Dimter планировалось так: первичный прострог, узел разметки, оптимизатор, затем материал сразу загружается на каретку и поступает на шипорезный станок, далее сеть транспортеров, пресс сращивания… Но опытные инженеры предприятия обнаружили в технологии несколько «узких мест», которые не позволяли разогнать производство, и решили ее изменить: заказать более производительный пресс, а также разорвать цепочку и вместо одного технологического потока пустить два. Поскольку оригинальное немецкое ПО после модернизации линии уже не годилось, к автоматизации привлекли кировскую компанию, специалисты которой установили свои контроллеры, написали все программы, и производство заработало.
Пиломатериалы поступают в цех из сушильных камер, определяется влажность каждой доски. На станке Weinig Profimat выполняется первичный прострог для обнаружения дефектов древесины, далее доски размечаются бракером для разделения на лицевые и черновые ламели.
Доски проходят через оптимизатор Dimter Grecon, раскраиваются по длине на линии оптимизации, после чего на узле разделения шипорезной линии CF300 производства WeinigGrecon параллельно происходит сращивание по отдельности лицевых и черновых ламелей. Оборудование в цеху позволяет делать сращивание как на вертикальный, так и на горизонтальный шип.
Далее ламели строгают повторно, для того чтобы получить заданные геометрические размеры и качество поверхности, необходимое для склейки. Готовые ламели накапливаются на автоматизированном складе (две буферные зоны – для черновых и лицевых). На выходе со склада оператор клееналивной машины задает в программе последовательность поступления ламелей на склеивание. В автоматизированном режиме ламели склеиваются в одинарный брус (полубрус). Через патерностер идет формирование закладки пресса, материал поступает в пресс Minda (Германия) – время склеивания составляет 40 минут для ЭПИ-системы и примерно один час для меламинового клея.
Склейка для производства клееного бруса – основной процесс, поэтому к нему здесь особое, даже трепетное отношение. Приходя на смену, мастер проверяет температуру и влажность в цехе, ведь от них зависит время и качество склеивания (температура 20–25°С поддерживается очень строго). Вообще факторов, определяющих качество склеивания, много. Это и подготовка поверхности ламели (определенное количество «волн» на 1 см, то есть качество строжки), и время выдержки, и соотношение клея и отвердителя в клеевой смеси. Мастер постоянно держит на контроле эти параметры, проверяя их ежечасно.
По завершении склеивания бруса пачка выходит из закладки на пятишпиндельный станок первичного прострога Rex (максимальное сечение при обработке: 300 х 400). После прострожки полубрус по системе транспортеров перемещается в зону накопления, откуда подается на вторую клееналивную машину, где заготовка обрабатывается клеевой смесью и закладывается в пресс для получения сложного бруса.
Прессы для склейки большеформатного (300 х 600) бруса – российского производства («Тигруп»). Клеенаносящее оборудование и меламиновые двухкомпонентные клеи – AkzoNobel. Руководство Holz House стремится к универсальности производства, поэтому для более гибкого применения клеевых систем (в зависимости от поставленных задач) в дальнейшем планируется установка дополнительных клеенаносящих узлов с использованием ЭПИ-клеев Kiilto.
Склеенный брус строгается и профилируется до окончательного профиля на втором (шестишпиндельном) станке Rex.
Готовый брус (стандартная длина – 12 м, максимальная – 13,5 м) складируется в пачки и затем подается на участок зарезки деталей домов. На станках Hundegger (сейчас на участке работают 2 станка – моделей K2i и BHM, третий станок BHM уже готовится к монтажу) по специальной программе в зависимости от проекта автоматически выполняется окончательная зарезка. Затем дефекты (сучки, смоляные карманы и т. д.) заделываются пробками или заглушками-лодочками и производится шлифовка поверхности.
«Hundegger K2i – машина большая и надежная, – поясняет Андрей Хаустов. – Самое ценное в ней – производительность, точность, универсальность и большой спектр возможностей. Станок позволяет, например, выполнять заказы в технологии фахверк, делать уникальные угловые зарезки в разных плоскостях».
Мастер оценивает полученные детали домокомплекта на соответствие проекту и подписывает готовый пакет, который направляют за пределы цеха на складирование (для перемещения пачек с линии сращивания и вывоза готовых наборов деталей домокомплектов используется четырехходовой погрузчик Combilift, с его помощью можно легко перегружать 12-метровые детали без риска их повреждений). Отгрузка потребителю – автомобильным транспортом.
Для повышения производительности цеха было принято решение о внедрении дополнительного оборудования. «Цех клееного бруса производит 1000 м3 в месяц, мы стремимся к увеличению объемов производства клееной продукции до 2000 м3 и больше. Ресурс станков это позволяет, – рассказывает Артем Собенин. – Ввод в строй дополнительного оборудования даст возможность не только нарастить объемы, но и обеспечить ритмичность производства, взаимозаменяемость участков для необходимых ремонтов, ревизий, переоснащения.
Рост мощностей в перспективе позволяет планировать и продажи клееной продукции на экспорт. Первые шаги в этом направлении уже сделаны: недавно отгрузили несколько контейнеров клееной балки в Корею. Объем контейнерных перевозок также планируем увеличивать».
Для подготовки и реставрации режущего инструмента в цеху организован заточной участок, оснащенный станками Vollmer. «Только напайку пластин мы заказываем в Кирове, все остальные работы делаются на месте», – поясняет начальник цеха.
По запчастям компания сотрудничает с петербургской компанией «Фаэтон».
Очень большое внимание уделяется качеству работы на каждом этапе технологической цепочки. «Наше основное, неукоснительно соблюдаемое правило: с завода не должно выходить ни одной бракованной детали, – подчеркивает Андрей Хаустов. – Станочный брак, дефекты обработки у нас сведены к минимуму. Прежде чем профилер (итальянский станок Compact 600, максимальное обрабатываемое сечение 600 х 300) начнет профилировать брус, от него отрезается пробный фрагмент, оценивается симметрия профиля (отклонение не больше 0,5 мм), качество склейки и пр. После проверки мастера и необходимых корректировок начинается профилирование большой партии бруса».
Конечно, на высокотехнологичном производстве многое зависит от людей, пресловутого человеческого фактора. Профессионализм и опыт работников позволяют полностью раскрыть потенциал оборудования: если обслуживать его как положено и со знанием дела, то оно будет производительным и прослужит долго.
Если на лесопильной линии все было довольно просто и понятно, то в производстве клееного бруса, по признанию начальника цеха, многое оказалось внове: «Но ребята толковые есть, работают с желанием, учатся в процессе, стараются, интересуются новой техникой. Вообще в моногородах и поселках кадровый вопрос ключевой, решать его непросто даже с учетом того, что зарплаты на предприятии по меркам региона весьма достойные (к тому же официальные, "белые"), – рассказывает Артем Собенин. – Утолять кадровый голод можно по-разному: например, купив несколько автобусов, организовать доставку работников из других населенных пунктов, либо привлекать работников на вахтовый метод. Мы задумываемся об этом и уже начинаем строить общежитие рядом с предприятием, чтобы приезжим было где жить.
Инфраструктура цеха постоянно развивается: строим новые раздевалки, душевые, столовую – стараемся улучшать условия труда. Уделяем внимание и охране труда, обеспечению корпоративной зимней и летней спецодеждой и т. д.».
«Можно заметить, что здесь работают довольно молодые люди. Обслуживать сложную современную технику молодым неравнодушным людям интересно, они учатся и хотят развиваться дальше, – отмечает Андрей Хаустов. – Тем самым у монопоселка появилась надежда: молодежь перестает стремиться в другие регионы, убедившись, что и в родной Лузе есть ответственный работодатель, обеспечивающий возможность круглогодичной занятости: даже если производство останавливается, всегда есть необходимость ремонта и приведения линий в порядок. Тут нет сезонности, как у мелких предпринимателей области».
Оплата труда в цеху сдельная, в зависимости от выработки. Поэтому каждый сотрудник напрямую – рублем – мотивирован на максимальную выработку. И это заметно, что называется, невооруженным глазом: лишних или праздно «гуляющих» людей здесь нет, работа спорится – все четко, точно, размеренно.
География поставок Holz House обширная – от Южной Кореи и Турции до Австрии, Германии, Италии. У компании есть представительство в Китае, недавно открыли офис в Казахстане. В России пять основных офисов: в Москве, Санкт-Петербурге, Екатеринбурге, Казани и Кирове.
Всего в развитии завода были предусмотрены три этапа: лесопильное производство, производство клееного бруса и домокомплектов из него, пеллетное производство. Первые два реализованы, уже готова проектная документация для третьего, в течение полугода на заводе начнется строительство пеллетной линии, которая позволит утилизировать все отходы производства. Фактически это станет логическим завершением процесса глубокой переработки древесины на предприятии. Сердцем установки станет немецкий гранулятор Munch, вспомогательное оборудование – от компании «Механика-Транс», специалисты которой возьмут на себя и монтаж линии.
Кроме того, руководство рассматривает возможность установить линию по переработке толстомера – для распила комлевой части, которая иногда не проходит по объему на действующую линию.
«Приезжайте к нам через год, – пригласил на прощание Василий Иванович, – увидите, как изменится предприятие! Обязательно запустим пеллетное производство и уберем горы отходов, оставшиеся в наследство от советского завода. Давно пора с ними разобраться.
Компания не стоит на месте. Надо отдать должное владельцам: они безостановочно двигают и двигают предприятие вперед, это очень правильно. Нам есть куда развиваться!»
Завод в Даровском
Это предприятие компании расположено ближе к центру региона и заработало раньше, но технологический процесс в целом схож с заводом в Лузе. Впрочем, есть и отличия: например, лесопильное и деревообрабатывающее производства здесь разделяет расстояние в три километра.
Производство бруса
Обзорную экскурсию по цеху клееного бруса провел инженер цеха деревообработки Дмитрий Сыкчин: «С отдельной площадки лесопиления мы автотранспортом доставляем сюда пакеты высушенного пиломатериала. Они поднимаются подъемником и по рядам подаются на линию. При прохождении досок через влагомер производства компании Testo (Германия) осуществляется дополнительная сортировка по влажности: если содержание влаги выше 10–11%, досушиваются. Далее – предварительная острожка на четырехстороннем строгальном станке для вскрытия рисунка и возможных дефектов древесины. Согласно размещенной на участке схеме дефектов оператор отмечает их мелком и пускает пиломатериал в оптимизатор WeinigOptiCut, который по сделанным меткам вырезает нужные фрагменты в автоматическом режиме.
Затем на участке сортировки специалист-сортировщик определяет, куда пойдет доска: на лицевую ламель (если идеальная, без сучков и обзола) или черновую, внутреннюю. Доски, которые по качеству не годятся для ламелей, выбраковываются и отправляются в переработку – измельчаются в шредере для последующего изготовления пеллет.
На линии сращивания Weinig Dimter доски сращиваются на микрошип (так называемый европейский, с шагом 3,8 мм и шириной 15 мм для несущих балок, а для бруса – 11) в 12-метровые ламели для последующего склеивания. Специальные датчики в сушильных камерах и здесь, на линии, фиксируют данные для отчета в конце каждой смены о количестве досок, поступивших в работу, выбраковке и изготовленных ламелях.
Ламели поступают на четырехсторонний шестишпиндельный строгальный станок и после острожки через промежуточный склад (где сортируются по карманам на черновые и лицевые) подаются на узел клеенанесения и пресс. По поступившему в работу заказу оператор на компьютере задает параметры изготавливаемого бруса, исходя из которых оборудование собирает пакет на выдачу. Так, на двухсотый брус нужно пять ламелей: две лицевые и три черновые».
Узел клеенанесения от компании «Бакаут» был модернизирован инженерами предприятия: оснащен более мощными и надежными насосами. В производстве используются клеи Kiilto и AkzoNobel. Прессы позволяют склеивать детали длиной до 13,5 м, что бывает необходимо для выполнения заказов по технологии фахверка, межэтажные перекрытия могут быть сращены из балок такой длины. Производительность пресса – 2,5 т в час. Прессы и часть оборудования для цеха поставляет компания «Интервесп».
Давление в прессе устанавливается в зависимости от толщины доски, ширины штабеля и пр. У операторов перед глазами специальный расчет конфигурации и рекомендации по установке правильных параметров клеевой системы, облегчающие расчет: время выдержки, жизнеспособность клея, температура и влажность в помещении (в цехах установлена система кондиционирования, поддерживается температура воздуха 20°С и влажность 40%).
Кстати, именно в Даровском начали производить брус большого сечения, до 280 х 280 мм. Поскольку сейчас появилась потребность в еще более массивном брусе, его производство перевели в Лузу.
Полученный после склеивания брус профилируется, торцуется. Торцы обрабатываются для упрочнения специальным клеем. Древесину пропитывают защитными средствами Teknos.
Для особо точных операций (сложных зарезок, вырезания косых чаш) был приобретен шестишпиндельный строгальный станок Hundegger K2. Более современный, автоматизированный, он стал дополнением к паре работающих в цехе итальянских чашкорезов-автоматов Stromab. В компьютер станка загружается проект дома со всеми размерами деталей, выборками, присадками. При необходимости можно внести оперативные изменения в программу изготовления домокомплекта, быстро сменить обрабатывающий инструмент. Настройки обработки предустановлены, человеческий фактор фактически сведен к нулю. Специалист компании-производителя, приехавший для пусконаладки станка, неделю обучал работников завода, после чего первые операторы смогли работать самостоятельно. Но после отъезда наладчика операторы и ИТР продолжили обучение в процессе работы и сейчас могут использовать технику, что называется, с закрытыми глазами.
Профилирование бруса выполняется на четырехстороннем станке HighPoint (Корея). Крупные балки обрабатываются на классическом четырехстороннем станке компании Ledinek.
Если на финальном этапе обработки вскрываются какие-то мелкие дефекты вроде смоляного кармана, они вырезаются и заклеиваются специальными вставками-«лодочками» и пробками. После этогоготовые детали из профилированного бруса дополнительно шлифуются.
В конце технологической цепочки детали раскладываются по пакетам, и для удобства монтажа дома на месте установки в «паспорте» проекта помечается, какая из них в каком пакете. Готовые домокомплекты вывозятся с завода автотранспортом, своей ж.-д. ветки в Даровском нет.
«Бывают проекты, для которых продукция уходит с площадки в контейнерах: сюда приходят контейнеровозы, загружаются и отправляются на ж.-д. станцию», – пояснил Дмитрий Сыкчин.
На производстве бруса режим работы трехсменный – круглосуточно по рабочим дням, в субботу работает одна смена. В смену выходят 20–25 человек.
Котельная, занимающая небольшое уютное здание, работает на отходах предприятия. Два котла: итальянский на 1 мВт и российский на 1,5 мВт – отапливают производственные помещения и снабжают теплом четыре сушильных комплекса (один Incomac и три – кировского производителя «Теплар») суммарной загрузкой 1000 м3.
На лето текущего года запланирован пуск пеллетной линии – древесных топливных гранул из северной древесины уже с нетерпением ждут клиенты компании.
Лаборатория
За точным соблюдением производственных параметров следит лаборант-технолог, который проводит испытания образцов продукции в специально оборудованной лаборатории.
«Из каждой партии бруса мы произвольно делаем несколько срезов и проверяем их на механическую прочность (испытываем шиповое соединение в ламелях на изгиб и излом, готовый брус на разрыв в специальной разрывной машине), определяем уровень влажности с помощью влагомера. Берем по два-три образца в смену, – рассказывает лаборант-технолог Ирина Юсовских. – Существует целый отработанный процесс, при котором образец проходит имитацию различных воздействий при работе в агрессивной среде: он взвешивается, подвергается давлению в автоклаве, пропитывается водой, помещается в вакуум, высушивается при температуре, близкой к устанавливаемой в сушильных камерах…
По итогам смотрим, расклеился ли образец, насколько сильно, определяем причину, вызвавшую расклей, расслоение. Это может быть, например, скрытый сучок или иной порок. Часто в ходе испытаний на разрыв рвется не клеевое соединение, а древесина рядом с ним (не по шву) – вот насколько прочно она склеивается.
Специальный компьютеризированный микроскоп позволяет отслеживать и оценивать качество клеевого шва при большом увеличении, определять оптимальный расход клея.
Кроме того, в обязанности технолога входит ряд работ в цехе: периодический контроль расхода клея, оценка качества строжки и прочее. А также контроль качества работ по всему технологическому процессу, вплоть до упаковки.
Каждые полгода к нам приезжают аудиторы из Австрии, которые проверяют соответствие работы лаборатории международным стандартам, дают необходимые рекомендации. По результатам проверок они обычно отмечают стабильность качества и даже говорят, что многие крупные европейские заводы сегодня до нас не дотягивают».
Лесопильный цех
Инженер цеха лесопиления Александр Митяшин рассказал, что сырье на довольно небольшую биржу завозится с расположенных в радиусе примерно 100 км (иногда больше) лесных участков, где древесину заготавливают сортиментные комплексы Ponsse.
Автоматическая линия сортировки круглого леса с 14 карманами изготовлена кировской компанией «Алмаз ДТМ». Грейфер подвозит бревна на раскатной стол, они проходят через измеритель и подаются на сортировку с помощью козлового крана. Пиловочник сортируется по диаметру и сортам и направляется на переработку.
Основная фрезерно-пильная линия – производства EWD. Работает восьмой год, распиливает в смену до 300 м3 круглого леса. Сырье подается на линию погрузчиком, окаривается, отрезается боковая доска с получением двухкантного бруса, далее проходит через фрезер. Получаемая центральная доска толщиной 50–60 мм идет на производство бруса. Рубительная машина превращает отходы лесопиления в неокоренную топливную щепу.
Укладка в сушильный транспортный пакет осуществляется в полуавтоматическом режиме с помощью штабелирующей машины. Пакеты пиломатериала для производства бруса отправляются на сушку в цех деревообработки, а боковая доска сушится здесь же и поставляется на экспорт в Китай и Иран.
Монтажом оборудования и инжинирингом в цехе занималась австрийская компания WDT, но в 2018 году при нештатной ситуации часть электроники вышла из строя. Тогда оперативно подключилась архангельская компания «Автоматика-Вектор»: ее специалисты заменили выгоревшую электронную «начинку» и поставили собственное русскоязычное ПО.
Цех работает пять дней в неделю, в одну смену. Этого достаточно, чтобы обеспечивать производство бруса, поддерживая для него месячный запас доски.
Отдельно расположен участок сортировки сухого пиломатериала, прозванный в народе «китайским цехом» (раньше здесь массово перерабатывали доску для Китая): полученные в лесопильном процессе боковые доски распределяются по сортам и длине, торцуются и укладываются в пленочные транспортные пакеты для отправки покупателям, в основном на экспорт.
В 2017 году, всего за один сезон, на площадке были установлены новый котел и сушильные камеры. Производитель сушильных установок – компания «Энергоавтоматика» (г. Киров), номинальный объем загрузки двух камер – 120 м3.
Мощность котла компании «Теплоресурс» (г. Ковров) 1,5 мВт. Механизированная топка с подвижными колосниками позволяет использовать сырое топливо. Котел работает в автоматическом режиме на отходах производства (древесной щепе и опилках), тепло идет только на обогрев производственных помещений и в сушильные камеры. Чистка и профилактика проводятся примерно раз в два месяца. «За любым оборудованием нужно ухаживать, тогда оно будет функционировать как положено и без сюрпризов», – подытожил небольшую экскурсию Александр Митяшин.
Слово директору
Несмотря на занятость, руководитель компании Holz House Николай Юферев нашел время для небольшого разговора, который и поставил смысловую точку в моем путешествии по Вятской земле.
– Прежде всего, разрешите поблагодарить вас, Николай Леонидович, за приглашение посетить производственные площадки компании.
– С вашей помощью на страницах известного отраслевого издания мы хотим показать, что деревянное домостроение живо и в стране есть предприятия, успешно работающие в этой сфере. Мы не только активно развиваемся, наращиваем объемы и строим амбициозные планы – компания социально ориентирована, мы идем к успеху вместе с жителями тех населенных пунктов, где расположены заводы, наши судьбы неразделимы. Будучи в Лузе, вы наверняка обратили внимание на объекты, созданные Holz House для жителей: это физкультурно-оздоровительный комплекс и фельдшерско-акушерские пункты, ледовая горка и каток для детей, пункт бесплатного проката коньков и т. д.
– А еще я наблюдал яркое празднование Масленицы, организованное при участии компании…
– Тесное сотрудничество с местной администрацией не исчерпывается одним этим мероприятием. Забота о людях должна быть постоянной.
В наших планах строительство оконного завода, что позволит приблизиться к решению давно поставленной задачи: делать свои дома от и до, что называется, под ключ. Чтобы клиент, заказывая у нас дом, мог быть абсолютно уверен в высоком качестве каждого его элемента.
Если еще год назад мы ориентировались на сдачу заказчику теплового контура, в который не входят окна, то теперь стремимся к такой степени готовности объекта, чтобы покупателю оставалось только завезти мебель. Конкуренция на рынке довольно жесткая, идет настоящая борьба за клиента, и не хочется терять его из-за того, что, допустим, поставщики окон не уложились в сроки или с качеством подвели, как уже бывало. Нелепая ситуация: мы полностью выполнили свою работу – сделали фундамент, возвели стены, кровлю, завершили покраску, – а потом вдруг дело встает из-за окон и это разрушает добрые отношения с клиентом… Один такой недочет способен серьезно повредить деловой репутации, которая весьма непросто заработана.
Клиенты хотят получать максимальный набор услуг от одного производителя. Компания должна делать все своими силами. И в скором времени мы начнем строительство оконного завода, сейчас определяемся с площадкой и выбираем оборудование. И, надеюсь, очень скоро, заказывая дом в нашем офисе, покупатель будет уверен, что не только стены и перекрытия, но и окна в нем будут самые лучшие – от компании Holz House.
Однако наши планы не ограничиваются только окнами, мы собираемся построить комплексный завод, который будет выпускать также широкий ассортимент столярных изделий для строительства дома: наличники и доборы, ступени лестниц и подоконники, внутренние двери и т. п.
– Сырьевое обеспечение предприятия – серьезная проблема для каждого развивающегося бизнеса в ЛПК. Как вы ее решаете?
– Аренда обеспечивает наши потребности только на 30%. Лесосырьевую базу мы получили в рамках реализации двух приоритетных инвестиционных проектов. В группу компаний Holz House сегодня входят два предприятия: головное предприятие в Лузе и «СтройЛес» в поселке Даровской. Инвестпроект в Даровском признан успешно завершенным, а завершение другого проекта мы сейчас оформляем в Минпромторге.
На эти два инвестпроекта нам была выделена лесосека в объеме 270 тыс. м3. Объем, прямо скажем, небольшой. Притом что наши возможности по лесозаготовке значительно больше: приобретены и работают четыре сортиментных комплекса, парк лесовозных машин более 50 единиц. Стараемся восполнять недостаток сырья, участвуя в региональных лесных аукционах. По результатам таких аукционов за прошлый год в Кировской области реализовано более 2 млн м3 древесины, в областной бюджет лесные аукционы принесли более 1 млрд руб. Так вот, из этих двух миллионов компания Holz House выкупила более 150 тыс. м3, по 560 руб. за кубометр. Безусловно, это недешево. Но других вариантов у нас, к сожалению, нет, рассчитывать приходится только на собственные силы. Ведь государство сегодня, несмотря на громкие лозунги и правильные слова с трибун, недостаточно содействует развитию деревянного домостроения. Госполитика в ЛПК ориентирована на поддержку крупных промышленных холдингов, основным приоритетом которых был и остается экспорт необработанных или минимально обработанных пиломатериалов. А деревянное домостроение остается уделом энтузиастов.
– А как же официальные заявления о необходимости развития глубокой лесопереработки в стране, вплоть до запрета вывоза необработанного древесного сырья?
– На деле все совершенно не так. Ситуация, с которой мы сталкиваемся в повседневной работе, убеждает, что рассчитывать на помощь «сверху» бессмысленно. Например, существует государственная программа субсидирования логистических затрат на продукцию с высокой добавленной стоимостью, и выделяемых средств в ЛПК не хватало даже на такую продукцию глубокой переработки, как LVL или клееный брус, но в 2019 году в список субсидируемых изделий удивительным образом добавились… обыкновенные доски!
– Пиломатериалы приравняли к продукции глубокой переработки?
– И это сводит к нулю все реальные или просто заявленные усилия по развитию глубокой переработки древесины внутри страны. Зачем организовывать непростые производственные процессы, выпускать высокотехнологичную продукцию с не такой уж высокой маржинальностью, если можно без затей пилить и продавать доски в Китай?!
– Понимаю, почему вы говорите об этом с такой горечью…
– В таких условиях мы становимся неконкурентоспособными в борьбе за сырьевые ресурсы. Серьезные кредиты на развитие банки предоставляют только крупным компаниям, нам подобных программ кредитования не видать, как и необходимой для полноценной работы лесосеки.
Наш бизнес существует более 13 лет. С самого начала и по сей день мы занимаемся деревянным домостроением, таково наше предназначение. Holz House – одна из немногих компаний, последовательно работающая на этом рынке и сегодня вышедшая в лидеры по объему производства домокомплектов из клееного бруса.
- Клееный брус сам по себе недешевый материал, дома из него доступны людям с достатком много выше среднего. Получается, что для вас выход в бюджетный, то есть массовый, сегмент невозможен априори?
– Действительно, пока дома из клееного бруса – продукт нишевый, скорее премиального уровня. Однако с каждым годом ситуация меняется, и производители находят способы для массового распространения своих технологий и продукции. Такие компании, как «Терем» или «Зодчий» активно продвигают кампании недорогих изделий вроде «Дом за миллион», при этом в продуктовой линейке «Терема» до 30% занимает клееный брус. Мы ориентированы на эксклюзивные проекты и уникальные дома, поэтому идем в массы своим путем – за счет некоторого сокращения площадей: если сейчас мы почти не продаем дома меньше 300 м2, то на будущее рассматриваем варианты проектов площадью по 120–150 м2.
Нужно понимать, что деревянные дома из клееного бруса не просто стремительно набирают популярность, а фактически сменили традиционные дома из оцилиндрованного бревна, – сегодня их уже почти никто не строит в промышленных масштабах. Когда мы начинали в 2005 году, не то что сам дом, даже идею деревянного дома из клееных конструкций продать было чрезвычайно трудно – люди просто не понимали, о чем речь и зачем переплачивать за что-то непонятное, когда все кругом строят из оцилиндрованного бревна. Но за последующее десятилетие тренд сошел на нет, и большинство производителей оцилиндрованного бревна (в кризисном 2008 году только у нас в районе Даровского было около таких 50 предприятий) уже не существует. Уверен, что будущее деревянного домостроения в России – именно за клееным брусом. В ближайшие три года сегмент производства домокомплектов из клееного бруса вполне может вырасти до 500 тыс. м3.
Чтобы высококачественные дома из клееного бруса стали доступнее, необходимы простые и понятные механизмы ипотеки и кредитования. Ни для кого не секрет, что программа «деревянной» ипотеки полностью провалилась и сейчас для постройки деревянного дома заказчик вынужден обращаться за обычным потребительским кредитом под 14%. А представьте, что было бы с рынком недвижимости при отсутствии доступной ипотеки: его бы просто не существовало.
– Специалисты, с которыми мне довелось познакомиться и пообщаться на двух площадках Holz House, оставили впечатление профессионалов высочайшего класса – настоящая «соль земли». Как вам удалось собрать такую команду, и что нужно для дальнейшего развития коллектива?
– Готовых специалистов на рынке не так много, и, даже если находишь такого, не факт, что он окажется лоялен твоей компании на все сто. Поэтому единственный вариант – выращивать специалистов у себя. Нередкая у нас ситуация: человек устраивается на работу мастером и дорастает до одного из руководителей заводов. Я сам занимаюсь деревообработкой, начиная со второго курса университета, постоянно изучаю и осваиваю новое. Так и вся наша команда: пока не набили себе шишек, дело не пошло. А дальше наработанный опыт передается новым сотрудникам – так растим себе смену.
– С руководителями более или менее понятно. А производственный персонал?
– Наши производства расположены максимально близко к источникам сырья, часто в удаленных поселках, куда и добраться бывает нелегко. И квалифицированным операторам современного деревообрабатывающего оборудования там взяться неоткуда, поэтому вариант тот же: обучаем на месте. Согласно стратегии компании, мы стремимся обеспечивать работой местных жителей. А они должны прежде всего поверить вам, осознать, что вы пришли сюда надолго и хотите для них лучшего. Это приходится подтверждать делом каждый день. Я не понаслышке знаю: чем больше души вкладываешь в людей, чем серьезнее занимаешься их подготовкой, тем больше будет отдача.
В Лузе за довольно короткий срок мы сформировали надежный костяк коллектива из 300 человек, там много молодежи, и эти ребята верны духу компании, работают с нами на одной волне. Важно, что люди уже не стремятся уехать из родных мест куда-то за длинным рублем, а хотят развиваться вместе с Holz House у себя дома.
– На производстве я неоднократно слышал, что основополагающие принципы компании – качество и клиентоориенти- рованность…
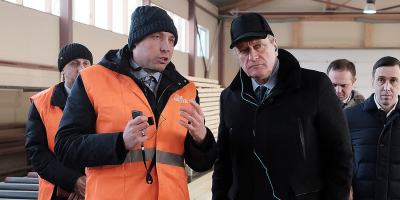
– Борьба за качество в основе нашей работы. Holz House – одна из немногих компаний в России, получившая европейские сертификаты CEEN14080, что позволяет без проблем поставлять продукцию на экспорт. Мы сотрудничаем с австрийским институтом деревообрабатывающей промышленности HolzForschung, два раза в год его аудиторы проверяют наши производства, это очень полезно для компании в целом.
Если говорить о клиентоориентированности, то отчетливо нишевая продукция предполагает единственно верный подход: каждый заказчик дорог и важен для Holz House, мы стараемся максимально удовлетворить все его пожелания и даже сверх того. Я не устаю повторять коллегам, что клиент для нас – лучший друг. И даже после того как проект завершен и дом построен, наше общение с заказчиками не прекращается.
Что нового
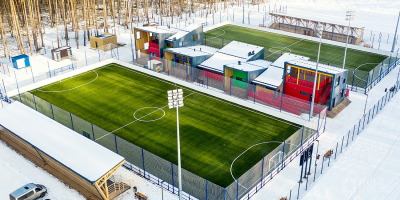
За годы работы компания Holz House построила из клееного бруса много сотен жилых домов и объектов разного назначения.
За 2019 год компания произвела более 25 тыс. м3 клееного бруса для домокомплектов, что примерно соответствует 50-60 тыс. м2 жилой площади. 70% из этого объема передано заказчикам в виде построенных домов, остальные 30% домокомплектов отгружены дилерам. В планах по выпуску на 2020 год – более 36 тыс. м3 бруса, причем 90% этого объема будет реализовано в виде готовых, построенных домов. В пересчете на площадь жилья это свыше 80 тыс. м2 – весьма серьезные цифры, в Кировской области не каждый застройщик многоэтажных жилых домов может похвастать подобным объемом вводимого жилья.
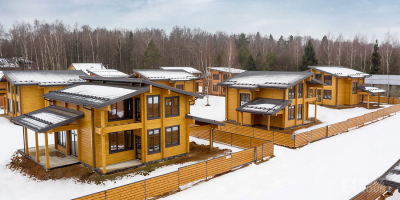
В конце января был сдан спортивно-оздоровительный комплекс площадью 600 м2 в Парке им. Малевича в Барвихе (Московская область). Его строительство продолжалось всего три месяца. Инициатором проекта стало правительство Московской области, автор архитектурной концепции Сергей Краснокутский. А в Красногорском городском округе Подмосковья построен комплекс из 22 коттеджей «Михалково Парк». В основу застройки были положены проекты двухэтажных домов «Тарту» и «Хельсингборг», разработанные в северном стиле.
Посетив в рамках рабочей поездки по Даровскому району завод Holz House, губернатор Кировской области Игорь Васильев особо отметил построенные компанией в регионе три фельдшерско-акушерских пункта из древесины: в селе Папулово Лузского района, в деревне Зайцевы Котельничского района и в селе Елгань Унинского района. Первые два возведены за счет собственных средств Holz House, третий – в рамках нацпроекта «Здравоохранение».
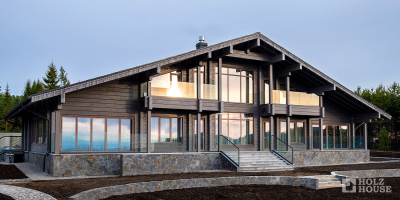
В этом году в селе Пасегово Кирово-Чепецкого района Кировской области компания планирует начать строительство школы на 250 мест площадью 3,5 тыс. м2, а в Лузском районе возвести из древесины физкультурно-оздоровительный комплекс.
В конце февраля компания Holz House был признана экспортером года по версии Российского экспортного центра и Центра поддержки экспорта Кировской области. Основанием для такой высокой оценки стала успешная работа компании на рынках стран ЕС, Южной Кореи, Японии, Ирана, Израиля, Сирии, Египта и других, а также открытие постоянных представительств в США, Казахстане, Турции и Китае.
Текст Максим Пирус
Фото: Максим Пирус, Алена Волкова
Редакция благодарит Артема Громазина и Алену Волкову (Holz House) за помощь в организации поездки.
Справка
Компания Holz House
На рынке с 1998 года. Производство расположено на трех площадках в Кировской области, в 200–450 км от столицы региона, в зоне таежных лесов. Группы продукции: круглые лесоматериалы, клееный брус (высотой 185, 250, 280 мм), клееная балка (длиной до 13,5 м, толщиной до 400 мм и высотой до 2000 мм), пиломатериалы сращенные на шип и строганые размерные, доски, топливная древесина, технологическая щепа, пеллеты.
С 2015 года производство сертифицировано по европейскому стандарту EN 14080, специалисты научно-исследовательского института древесины HolzForschung (Австрия) дважды в год проводят технический аудит на соответствие стандарту EN. Получен сертификат по стандарту FSC (FSC-C137745). Клееная продукция сертифицирована по ГОСТ 20850–2014 и ТУ 5366–001–84551923–2015. В производстве используется безформальдегидный клей AkzoNobel класса E1, имеющий санитарно-гигиенический сертификат.
Источник: holz-house.ru