Как организовать производство оцилиндрованных бревен
В России и других северных странах строят разные виды деревянных домов: рубленые из окоренного бревна, как в старину, из окоренного и оцилиндрованного бревна, из цельного бруса, обычно четырехкантного, из клееного профильного бруса и каркасные из сухих пиломатериалов и плит с утеплителем.
Первый вид можно посчитать устаревшим, хотя по расходу материала он самый экономичный. Срубы из неоцилиндрованных бревен веками рубили наши предки. Для этого нужно подобрать прямые бревна одного диаметра, окорить их и выдержать до достижения равновесной влажности древесины 20 ± 2%. Затем можно выполнять необходимую механическую обработку бревен, не боясь изменения формы и размеров сруба при эксплуатации. При такой технологии потери древесины в отходы минимальны.
Превращение бревна в правильный цилиндр дает декоративный эффект, поэтому оцилиндрованные бревна по-прежнему популярны в деревянном строительстве, несмотря на распространение высокотехнологичных конструкционных материалов из древесины.
Оценим потери древесины при оцилиндровке.
Объем пиловочного бревна длиной 6 м и диаметром в вершинной части 24 см составляет 0,33 м3 (по таблице объемов круглых лесоматериалов в ГОСТ 2708–75). Объем цилиндра диаметром 24 см той же длины будет равен (3,14 × 0,242 × 6)/ 4 = 0,2714 м3. Следовательно, потери древесины составят 100 – (0,2714 : 0,33) х 100% = 18%. Для бревен меньшего диаметра потери будут еще больше, для минимального допустимого диаметра 18 см – почти 22%.
Полезный выход 80% является недосягаемым показателем при всех остальных вариантах деревообработки. В лесопилении обычным считается выход пиломатериалов примерно 50% (объем пиловочного бревна принимается 100%). Несколько выше выход сырого шпона из фанерного чурака – за счет безопилочного резания может доходить до 70%. То есть использовать лесоматериалы в круглом виде весьма выгодно, поскольку при минимальных затратах получается максимальная добавленная стоимость, так как по теплотехническим характеристикам стена из оцилиндрованных бревен ничем не уступает стенам из бруса или каркасных панелей. При этом для производства 1 м3 стены из оцилиндрованных бревен требуется примерно 1,2 м3 лесоматериалов, из цельного бруса – около 2 м3, а из клееного бруса – не менее 3 м3.
Товарной продукцией предприятия по изготовлению строительных деталей для бревенчатых домов является оцилиндрованное бревно заданной длины и постоянного диаметра с укладочным пазом и компенсационным пропилом для снижения внутренних напряжений при сушке древесины, а также (по согласованию с заказчиком) с поперечными чашками.
Стандартный диаметр бревен 18–32 (36) см, шаг 2 см. Бревна диаметром 18–20 см рекомендуются для строительства летних кухонь или детских домиков, диаметром 20–22 см – для бань и саун, а более толстые – для рубленых домов круглогодичного проживания. Ширина паза принимается равной половине диаметра бревна. Основные породы древесины для бревен – сосна и ель. Находят применение кедр, пихта, лиственница и даже осина.
Малому бизнесу интересна возможность организации производства при минимальных капитальных затратах. И чаще всего она появляется в местах лесозаготовок. Головным оборудованием в этом случае может быть комбинированный оцилиндровочно-фрезерно-пильный станок, на котором в позиционном режиме выполняется окорка и оцилиндровка бревен, фрезеруется укладочный паз и формируется компенсационный пропил. Многие позиционные станки за одну установку формируют также поперечный паз (чашку).
Станки токарного типа позволяют обрабатывать бревна с кривизной, хотя при этом резко увеличивается объем отходов и уменьшается диаметр готовой продукции. Минимальный диаметр согласно характеристикам станков составляет 14 см.
Рынок предлагает широкий выбор таких станков, отечественных и импортных; минимальная цена примерно 200 тыс. руб. Помимо головного станка, потребуется торцовочный круглопильный станок для бревен. Впрочем, его может заменить цепная электро- или бензопила, хотя качество поверхности торца в этом случае гораздо ниже, чем при пилении круглой пилой. Неизбежны расходы на приобретение подающего и выходного конвейера и средств механизации для снижения затрат ручного труда. Для погрузо-разгрузочных работ оптимальным может оказаться колесный погрузчик с вилочным захватом. В качестве производственного здания можно использовать ангар. Понадобятся также станок для заточки режущего инструмента, распылитель для антисептика и оборудованные площадки для хранения сырья и готовой продукции.
Ориентировочный объем капитальных затрат на такой минимальный вариант производства, по нашим прикидкам, будет 1,5–2,0 млн руб. Производительность головного станка, по данным изготовителя, колеблется от 3,5 до 6 м3 в смену, то есть примерно 70–120 м3 в месяц.
Проще всего организовать участок оцилиндровки бревен на складах сырья лесопильных комбинатов и на лесных биржах, где есть линии сортировки круглых лесоматериалов. Для нового предприятия достаточно выделить несколько карманов для бревен заданного диаметра и требуемого качества.
Из отечественного оборудования можно рекомендовать для средних предприятий проходные оцилиндровочные станки производства Sherwood, «СТИН», «Термит» (г. Киров). Предлагаются станки для диаметра бревен (на выходе) от 7 до 40 см. В комле диаметр может быть от 14 до 55 см. Припуск на обработку, например, для станков серии СК от фирмы «СТИН» составляет 60 мм (120 мм на диаметр).
Максимальная скорость подачи бревен в проходных станках 6–8 м/мин. По данным машиностроителей, производительность может достигать 650 пог. м в смену. При среднем диаметре бревен 24 см Пчас = 3,6 м3/ч, а годовая производительность станка (программа предприятия) при односменной работе составит примерно 5–6 тыс. м3.
Не менее 20–25% сырья, перерабатываемого предприятием, будет уходить в отходы (вторичное сырье). Это мелкодисперсные отходы, которые могут стать дополнительным источником дохода.
Режим работы предприятия зависит от времени года. Зимний период (октябрь – март) характеризуется очень низкой активностью строителей и, соответственно, слабым спросом на строительные материалы. В это время следует делать запасы материалов и закладывать оцилиндрованные бревна на атмосферную сушку.
На фото, взятом из архива журнала «ЛесПромИнформ», показан один из вариантов оборудования штабелей для сушки круглых лесоматериалов. Нижние ряды выложены на прокладках без обвязки, на них укладываются плотные пачки из 12 бревен. Штабель венчает съемная крыша, защищающая древесину от атмосферных осадков.
Важным вопросом является продолжительность атмосферной сушки. В ГОСТ 3808.1–80 приведены сроки сушки пиломатериалов на открытых складах. Для бруса толщиной до 75 мм это 1–2 месяца в зависимости от климатической зоны и сезона (рекомендуется только с апреля по сентябрь). Для круглых лесоматериалов продолжительность сушки немного увеличивается. Предприниматель должен иметь в виду, что для высушивания бревен до влажности не выше 22% в теплый период года потребуется не менее двух месяцев.
Равновесная влажность больше зависит от относительной влажности воздуха, нежели от его температуры. Даже при низкой температуре 0–10°С и типичной для межсезонья влажности воздуха 80–90% равновесная влажность древесины составляет 17–24%. То есть лесоматериалы более высокой влажности теряют влагу и при низкой температуре воздуха.
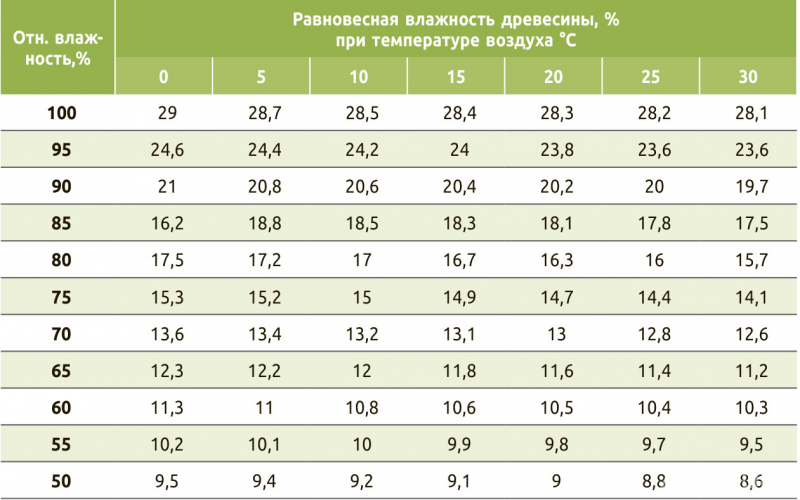
Любое производство эффективнее при круглогодичном режиме работы. Зимой предприятие по оцилиндровке бревен должно обеспечить сохранность продукции. Если продукция не реализуется, создаются большие межсезонные запасы продукции, хранящиеся примерно четыре месяца. За это время даже малое предприятие может произвести около 400 м3 оцилиндрованных бревен, для которых нужно оборудовать специальные хранилища. Склад готовой продукции должен располагаться на ровной площадке с приподнятым над землей основанием (лучше бетонным). Все это требует дополнительных затрат, которые нужно учитывать при организации нового бизнеса.
Технологический процесс можно организовать с атмосферной или камерной сушкой лесоматериалов. По некоторым данным 2004 года, высушенные бревна почти в три раза дороже сырых. Следует иметь в виду, что во время хранения влажность лесоматериалов снижается при любых климатических условиях. Нужно только, чтобы штабели были защищены от атмосферных осадков.
Камерная сушка лесоматериалов применяется редко. Еще в 2004 году был предложен и экспериментально проверен способ сушки круглых лесоматериалов с помощью СВЧ-энергии, при котором влага изнутри бревна удаляется с помощью электродов, ориентированных по его центральной оси. Метод позволял сушить сортименты без образования торцовых трещин. Однако сегодня ничего не известно о его дальнейшей реализации.
Оптимальным оборудованием для сушки лесоматериалов могли бы быть двухкамерные проходные конвекционные сушилки. Первая камера в них высокотемпературная. Бревна в ней высушиваются до влажности примерно 30%, то есть удаляется только свободная влага и усушка древесины не происходит. После того как приборы зафиксируют снижение высоты штабеля из-за удаления связанной влаги из древесины, штабель с бревнами перемещается во вторую камеру, с мягким температурным режимом, а в первую камеру загружается новый материал.
При таком способе время сушки можно сократить до 15–20 дней. Загрузка сушильных камер зависит от времени года, то есть от влажности и температуры наружного воздуха. Также учитывается спрос на сухой материал.
Для организации производства необходим определенный набор средств производства:
- Оборудованный склад – запас сырья нужных размеров и качества.
- Оцилиндровочный станок (станки) с функцией формирования монтажного паза и компенсационного пропила и необходимой механизацией загрузки, центрирования и выгрузки бревен. Цена проходных станков отечественного производства от 1 млн до 1,5 млн рублей.
- Система удаления и складирования вторичного сырья (стружки и опилок). При норме отходов 20% от объема сырья их ежемесячный объем (на программу 500 м3 продукции) составит не менее 100 пл. м3, или 250 нас. м3. Наиболее современное решение – эксгаустерная установка с отбором в отдельный бункер стружки, которую можно использовать как топливо и для производства топливных брикетов или гранул.
- Торцовочный круглопильный станок (допустим, марки «Термит 3207» с максимальным диаметром пиления 32 см) для формирования из бревен деталей нужной длины.
- Чашкозарезной станок.
- 6Установка для антисептирования продукции методом распыления жидких антисептиков на поверхность оцилиндрованных бревен. Антисептирование продукции особенно важно в летний период.
- Станок для заточки режущих инструментов.
- Производственное закрытое неотапливаемое здание длиной 24–30 м.
- Склад готовой продукции с крышей для выдержки и атмосферной сушки (досушки) деталей.
Окупаемость немалых расходов на организацию производства зависит от качества продукции, спроса на нее и сотрудничества со строителями.
При работе с крупными домостроительными фирмами, которые имеют спецификацию всех деталей, предприятие-изготовитель выполняет заказ на комплект деталей для дома. Некоторые застройщики работают по эскизам здания и предпочитают использовать оцилиндрованные бревна максимальной длины, а распиливать их и вырезать чашки – на строительной площадке.
По данным открытых источников, сегодня цены на такую продукцию в Ленинградской области 7,1–11 тыс. руб./м3. При этом продавец иногда указывает, что продает «бревна естественной влажности». Можно сказать, что это бревна неопределенной влажности. Ведь чем дольше выдерживаются бревна до и после обработки, тем ближе их влажность к равновесной, следовательно, тем меньше времени занимает усадка сруба. Опыт показывает, что усадка бревенчатой стены высотой 2,5–3 м из сырого материала может достигать 30 см! И далеко не всегда стены сруба оседают равномерно, что неизбежно нарушает геометрию постройки. Понятно, почему оцилиндрованные бревна влажностью не выше 22–25% дороже других.
Как ни странно, в интернете нам удалось найти предложение сухих оцилиндрованных бревен только одного производителя: вологодская фирма «Воллесдом» выполняет камерную сушку бревен до влажности не выше 25% в камерах Mühlböck с объемом загрузки 70 м3. Время сушки – до трех недель. Сухие бревна в комплекте деталей на дом компания в основном экспортирует, поставляет в Германию и Венгрию.
Текст Владимир Волынский