Как получить высокий доход при незначительных инвестициях
Переработка неиспользуемой лиственной и низкокачественной хвойной древесины на малотоннажных заводах ЭХТММ
Основной проблемой развития российского лесного комплекса является неравномерное распределение перерабатывающих предприятий по стране. Лесные ресурсы если используются, то крайне неэффективно. Из-за больших расстояний перевозки сырья и отсутствия дорог на значительной части территории лесопереработка нерентабельна.
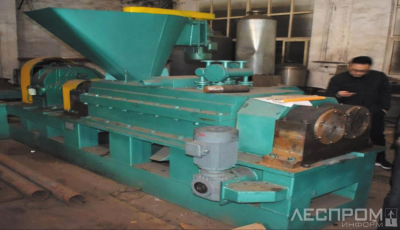
В 1989 году в СССР заготовили 350 млн м3 древесины, а спустя 40 лет, в 2019 году, – только 220 млн, при освоении экономически доступной расчетной лесосеки (550 млн м3) всего на 41%. За тот же срок в КНР, где площадь лесов 97,1 млн га (в 12 раз меньше, чем в России) и её запас – 6 млрд м3 (в 13 раз меньше, чем в России), было заготовлено 320 млн м3 древесины (в 1,5 раза больше, чем в России). В 2019 году доля лесного сектора в ВВП в Китае составляла 7%, в денежном выражении $994 млрд, а в России – $22 млрд (1,4 трлн руб.), то есть в 45 раз меньше. В 2018 году доля ВВП от переработки древесины в Китае вдвое превысила доход нефтегазового сектора России ($518 млрд)!
Сегодня для ЦБП создаются целевые лесосырьевые плантации с коротким оборотом рубки: 3–7 лет. Треть объема целлюлозы в мире производится за счет сырьевых плантаций, занимающих всего 3% площади вырубаемых лесов.
Для российских лесных предприятий характерны низкие показатели технико-экономической эффективности. Так, рентабельность лесозаготовок 1,8%, лесопиления – около 4%. Только предприятия глубокой переработки древесины (заводы по производству плит, ЦБК) характеризуются рентабельностью на уровне 10–20%. Именно они являются локомотивом развития лесной индустрии, поскольку выпускают продукцию с самой высокой добавленной стоимостью из малоценного и низкокачественного древесного сырья (балансов, технологических дров), не находящего массового спроса в остальных секторах лесопереработки.
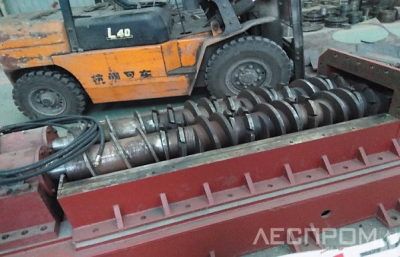
К сожалению, история развития целлюлозно-бумажной промышленности представляла собой постоянное наращивание мощности ЦБК, стоимости их строительства и увеличение продолжительности возврата вложенных в проект денежных средств. В результате все действующие предприятия-гиганты российской ЦБП работают свыше 40 лет, леса вокруг них на значительном расстоянии вырублены и возить сырье приходится издалека. Из-за постоянного повышения затрат на транспортировку сырья и российские производители целлюлозы и бумаги потеряли конкурентоспособность и были вытеснены с мировых рынков производителями из тропических стран, где лесные ресурсы возобновляются быстрее и плечо вывозки сырья увеличивается медленнее или вообще не меняется.
Особая ситуация сложилась в РФ с потреблением лиственной древесины. Почти полностью прекратилось производство тарных деревянных ящиков, бочек, лыж и катушек, уменьшился объем выпуска спичек (из осины). В 2019 году из 39 млн м3 произведенных пиломатериалов на лиственные пришлось всего 4,7%. Объем переработки лиственной древесины с 1989 года снизился на 50,2 млн м3.
При сплошных рубках смешанных древостоев со значительной долей лиственных пород у лесозаготовителей возникает проблема: как использовать низкокачественные лиственные сортименты (балансы, дрова), а зачастую и лиственную древесину вообще. Из-за отсутствия спроса лиственная древесина, как и неликвидная хвойная, как правило, оставляется на лесосеке, применяется для строительства лежневок или сжигается. Только небольшая часть реализуется с выгодой, основная масса поступает в продажу по цене ниже себестоимости. В связи с этим лесные предприятия терпят убытки, их технико-экономические показатели снижаются, нередки банкротства и закрытия.
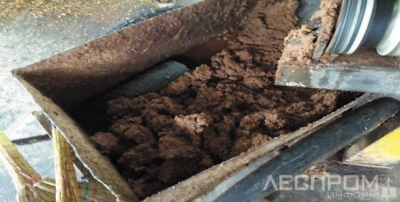
Концепция постоянного наращивания объемов производства и укрупнения лесоперерабатывающего предприятия полностью исчерпала себя. И прежний подход с перевозкой сырья на любое расстояние уже не «работает», поскольку при мощности современных предприятий дальность вывозки довольно быстро увеличивается настолько, что производство продукции становится экономически нецелесообразным. Вместо принципа «сырье – к заводу» следует ввести другой: «завод – к сырью». Для его реализации необходимы новые высокоэффективные решения по переработке лиственной древесины, неликвидной хвойной древесины и древесных отходов, поскольку невостребованность этих видов сырья в России тормозит развитие индустрии.
Какими же должны быть новые технологии переработки древесного сырья, чтобы вывести отрасль на новый уровень производства, при котором современные высокоэффективные и экологически безопасные предприятия перерабатывали бы все доступное сырье (в первую очередь не используемое сегодня) в продукцию с высокой добавленной стоимостью, предназначенную для конечного покупателя?
Прежде всего технологии должны отличаться приемлемым для малого и среднего бизнеса объемом инвестиций в строительство предприятия. Современный ЦБК идеален с точки зрения возможности использования сырья вокруг, но его невозможно построить, так как в нынешних российских экономических условиях не найти инвестора, который согласится вложить несколько миллиардов долларов на длительный срок (13–22 года в зависимости от степени освоения новой лесосырьевой базы) с неясными перспективами неистощимости лесопользования.
А для быстрой окупаемости вложенных средств технологии должны быть простыми и эффективными.
По мнению специалистов Инновационного центра инжиниринга переработки лиственной древесины, биомассы дерева, неликвидной хвойной древесины и древесных отходов Санкт-Петербургского государственного лесотехнического университета имени С. М. Кирова, наиболее перспективной для России технологией переработки малоценной древесины в товарную продукцию с высокой добавленной стоимостью может стать развитие малотоннажных заводов по выпуску экструзивной химико-термомеханической массы (ЭХТММ) – сырья для производства ряда видов бумаги, картона и изделий из них. Сегодня они широко распространены и успешно работают в Китае.
История создания этой технологии началась в 70-х годах прошлого века в Германии, где был изобретен экструдер – механизм разностороннего и многофакторного воздействия на древесину. А в 1987 году в СССР впервые в мире была построена опытно-промышленная установка по выпуску ХТММ. Экструдер стал основой технологии производства ЭХТММ и обеспечивает ее высокую эффективность за счет комплексного воздействия на древесину и возможность быстрой перенастройки на другие виды сырья. Вскоре после публикации профессором Комаровым (АрхЛТИ) технологии ЭХТММ на установке производительностью 20 т в сутки, в 90-х годах в Китае появилась промышленная установка такой же мощности для переработки рисовой соломы в ЭХТММ. Впоследствии, изменяя устройство подачи растительного сырья и конструкцию экструдера, наши восточные соседи разработали большую линейку оборудования для разных видов сырья (соломы, ненаркотической конопли, камыша, плантационной древесины тополя и других древесных пород) и разной мощности: 20 (30), 50 (60), 100 и 200 т/сут. Такое оборудование в КНР производят всего шесть заводов. В мире построено около 300 заводов по переработке сырья в ЭХТММ. Два завода, выпускающие ЭХТММ из технологической сосновой щепы, появились в 2020 году и в России.
Конструкция экструдера за сорок с лишним лет претерпела ряд изменений. Китайские специалисты рекомендуют использовать двухвинтовой экструдер – многофункциональную машину для превращения щепы в волокнистый полуфабрикат (ВПФ) для производства бумаги и отделения отходов – лигниноподобного материала. Никакая химическая технология переработки древесины не позволяет в одном аппарате получать ВПФ одновременно с выделением отходов.
Двухвинтовой экструдер представляет собой аппарат с двумя продольно расположенными винтами. При вращении винтов щепа одновременно подвергается скручиванию, трению, многоцикличному сжатию и саморасширению, размягчению и управляемому растворению химического вещества древесины химическими реагентами. Сложное воздействие этих факторов на увлажненную щепу по мере ее продвижения приводит к расщеплению древесной ткани и постепенной экстракции смол и лигнина. Экстрагированные отходы в виде пасты коричневого цвета (лигнина) удаляются из экструдера. Выход волокнистой костры регулируется соотношением костра/лигнин и может достигать 80–85%, содержание лигнина в ней 15–25%.
Оказалось, что ЭХТММ малотоннажного предприятия – самый конкурентоспособный древесный волокнистый полуфабрикат и экологически чистое сырье для производства бумаги, картона и изделий из них.
При производстве ЭХТММ в процессе варки древесины лигнин не переводится в растворимое состояние, как это происходит при производстве разных видов целлюлозы, а пластифицируется вследствие размола щепы в экструдере. Технология получения традиционной многотоннажной ХТММ предусматривает переход большой части лигнина в растворимую форму в результате размола щепы в рафинерах при температуре выше 100° С и высоком давлении, как и при производстве целлюлозы. Поэтому при организации производства ХТММ и целлюлозы необходимо строительство очистных сооружений с капитальными затратами до 20% стоимости завода и эксплуатационными расходами 10–15%. Для выпуска ЭХТММ стационарные очистные сооружения не требуются, по крайней мере об этом свидетельствует опыт китайцев.
Технология получения ЭХТММ состоит из нескольких этапов: подготовки и пропитки щепы химикатами, размола ее в экструдере и рафинерах, отбеливания и сортирования ЭХТММ, сушки и упаковки товарной продукции. Технология производства малотоннажной (20–200 т/сут) ЭХТММ, в отличие от производства многотоннажной (350–700 т/сут) ХТММ, предполагает замкнутый водооборот. Свежая вода нужна для компенсации потерь пара, удаляемого в виде паровоздушной смеси из реакторных бассейнов; потребность в ней – 3–5 м3 на 1 т массы может обеспечить скважина. Локальная очистка оборотной воды необходима при промывке щепы и обезвоживании массы на ленточном прессе; хозбытовые стоки направляются в действующую канализацию предприятия или города.
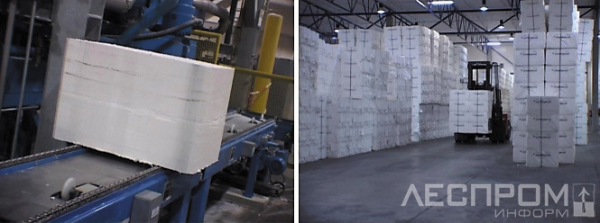
В производстве беленой ЭХТММ, как и в традиционном производстве ХТММ, для отбеливания применяется перекись водорода, а не вредные для окружающей среды соединения хлора, используемые при получении целлюлозы.
По механическим и оптическим свойствам ЭХТММ – востребованный вид ВПФ, который может использоваться в композиции около 100 видов бумаги и картона. Из небеленой ЭХТММ можно выпускать небеленый тарный картон, в том числе основу для гофротары, из беленой – санитарно-гигиенические изделия. Особый интерес представляет использование беленой и небеленой ЭХТММ для производства упаковочных бумажных пакетов, которые в ближайшем будущем должны заменить полиэтиленовые.
По технологическим и бумагообразующим свойствам малотоннажная ЭХТММ не отличается от традиционной многотоннажной ХТММ. 13-летний опыт работы Светогорского ЦБК (International Paper) – завода многотоннажной беленой ХТММ (БХТММ), выпустившего за эти годы более 2 млн т ВПФ, показал, что без беленой ХТММ недостижимы некоторые свойства конечной товарной продукции, например, жесткость картона при определенных толщине и весе одного квадратного метра. Высокая водоотдача дает возможность повысить скорость бумагоделательной машины, а значит и удельный выход готовой продукции.
Производство малотоннажной ЭХТММ и многотоннажной ХТММ позволяет снизить затраты производства за счет низкой стоимости массы в сравнении с сульфатной целлюлозой: расход древесины почти в два раза меньше, а выход продукта – почти в два раза больше. При достигаемом уровне белизны ХТММ можно добиться целевого уровня белизны бумаги, особенно при использовании осины в качестве сырья, что обуславливает преимущество БХТММ для смешивания с сульфатной целлюлозой при производстве таких видов бумаги, как офисная писче-печатная и бумага-основа для санитарно-гигиенических изделий.
Высокие абсорбционные свойства ХТММ позволяют снизить затраты на размол и подготовку массы. Применение ХТММ вместе с целлюлозой при подготовке массы ВПФ в композиции для бумагоделательной машины допускает подачу компонентов в машину как по отдельности, так и в смеси с целлюлозой одной линией. Причем изменения технологического процесса не требуется.
Механические и бумагообразующие свойства ХТММ зависят от продолжительности размола, концентрации массы при подаче в рафинеры и температурного режима. За счет изменения перечисленных параметров осуществляется регулирование качественных характеристик ХТММ. Качество размола в рафинерах определяет почти все качественные показатели ХТММ: степень помола, удельный объем, содержание костры и т. д.
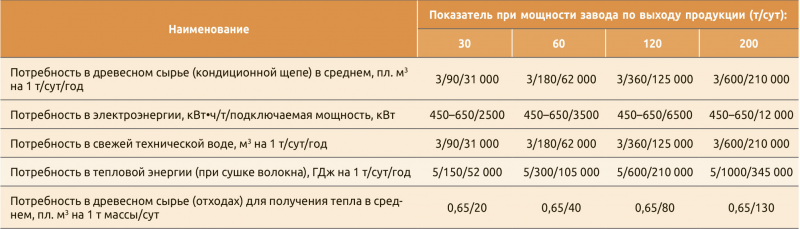
Однако свойства конечной продукции связаны и с выбранной породой древесины. Из отечественных пород оптимальны осина и ель, которые позволяют снизить расход энергии на размол и получить массу высокой (до 85%) белизны. Действует общее правило: чем длиннее древесное волокно исходного сырья (по породам), тем лучше бумагообразующие свойства получаемой ЭХТММ. От этого и от химического состава древесины зависит выбор древесной породы в качестве сырья для определенного вида бумажной товарной продукции. Для производства ЭХТММ древесина лиственницы малопригодна, поскольку содержит много смоляных и жирных кислот и таких экстрактивных веществ, как арабиногалактан и дигидрокверцетин. Переработка лиственницы возможна только с применением дополнительного оборудования для экстрагирования указанных веществ перед подачей щепы в экструдер. Базисная плотность древесины зависит от породы, например, плотность осины – 300 кг/м3, лиственницы – 540 кг/м3, и оказывает существенное влияние на производство ЭХТММ и конечные свойства массы. С одной стороны, использование неплотной древесины позволяет снизить расходы на размол и уменьшить объем каустика на пропитку, с другой – повышает удельный расход древесного сырья, а следовательно затраты на него.
Производственная линия работает по экструзивной технологии, позволяющей перерабатывать в качестве сырья раздельно щепу лиственных (осины, березы, тополя, акации и др.) и хвойных (ели, сосны) пород древесины. Допускается совместная переработка всех лиственных или всех хвойных пород, а также примесь до 15% хвойных пород к лиственным и наоборот.
Исходным видом сырья могут служить балансы и технологическая щепа. Необходимо создание лесной биржи (приемки, сортировки и складирования древесины) и древесно-подготовительного цеха с переработкой круглого леса в технологическую щепу и организацией кучевого хранения с выдержкой не менее месяца. Щепа должна отвечать требованиям ГОСТ 15815-83 Щепа технологическая, но для производства небеленой массы в ней допускается содержание коры 1–3%.
При переработке древесины в волокно на разных стадиях образуются органические древесные отходы. Большая часть отходов утилизируется путем сжигания для получения необходимого для производственного процесса тепла или органических удобрений. Все технологические приемы экологически безопасны.
Экономические преимущества производства ЭХТММ очевидны: удельные капиталовложения ниже, чем в производство сульфатной целлюлозы, в 10 раз, а традиционной ХТММ – в пять раз; срок окупаемости 1,5–3 года, тогда как в случае ХТММ – 5–7 лет, а целлюлозы – 13–17 лет. Инвестиции в строительство малотоннажных заводов ЭХТММ сопоставимы с вложениями в лесопильные заводы средней мощности и составляют $1–10 млн при годовой производительности от 7 до 70 тыс. т и потреблении древесного сырья от 30 тыс. до 210 тыс. м3.
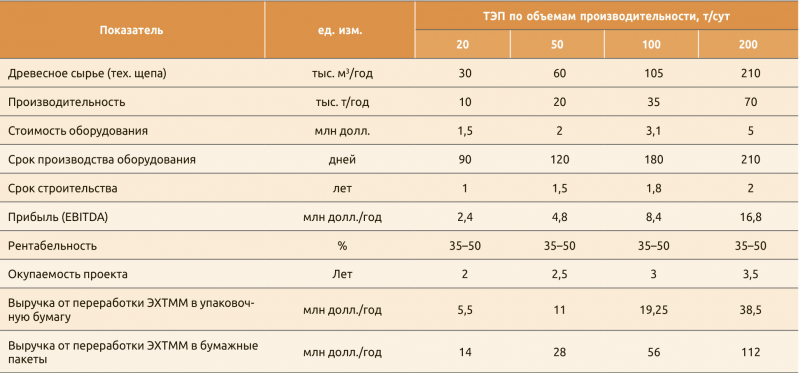
В технологии не применяются машины и аппараты, работающие при избыточном давлении и температуре выше 100 °C, следовательно, не требуется специальных разрешений на эксплуатацию такого оборудования. Для сушки массы, отопления помещений, нагрева воды, размораживания щепы в зимнее время необходимо тепло. Расчеты показывают, что древесных отходов производства ЭХТММ (коры, отходов окорки и сортирования щепы, лигниноподобных отходов экструдирования, скопа – мелкого волокна после сортирования массы) достаточно для получения необходимого количества тепловой энергии. Поэтому дополнительно к оборудованию следует закупать теплогенераторы, если ранее не были установлены утилизационные котлы, работающие на древесном топливе. При производительности оборудования от 30 до 200 т массы в сутки потребуется один и тот же удельный расход электроэнергии на 1 т ЭХТММ, но разные мощности подключения – от 2,5 до 12 мВт. Поскольку технология энергоемкая, обеспеченность электромощностью и стоимость электроэнергии являются определяющими при принятии решения о строительстве завода ЭХТММ. При нехватке электроэнергии к утилизационному котлу или теплогенератору подключают электрогенератор для производства электроэнергии за счет сжигания отходов предприятия вместе с дровами, брикетами или пеллетами. В этом случае стоимость электроэнергии будет не выше 3 руб./кВт.
И еще об особенностях технологии. Воздействие на щепу в экструдере происходит при низком гидромодуле: Г = 1,1–1,5 т воды/т а.с.д., поэтому размол костры в волокно возможен в дисковых рафинерах при высокой концентрации массы с получением на выходе пастообразного лигнина, который можно сжигать в котлах или теплогенераторах вместе с отходами окорки и сортировки щепы.
Обезвоживание полученной массы в ленточном прессе до влажности 35–45% и аэрофонтанная сушка до конечной влажности 8–10% исключают применение громоздких и сложных в эксплуатации дорогостоящих сушильных машин (пресс-патов). Запрессовка готовой массы в брикеты высокой плотности (750–800 кг/м3) существенно повышает рентабельность транспортировки ЭХТММ потребителям.
Регенерация химикатов не требуется, поэтому нет необходимости промывать массу с использованием большого объема воды и обеспечением ее очистки и сброса в водоемы.
При использовании экструзивной технологии производства ЭХТММ завод (цех) может быть построен в любом лесном регионе России, с привязкой не к лесоперерабатывающему предприятию, а к сырью – низкокачественной, прежде всего лиственной, древесине, а также к водным и энергетическим ресурсам.
Справка
Ориентировочная себестоимость производства ХТММ на примере строящегося в РФ завода (при себестоимости волокна 24 тыс. руб./т), %
Химикаты – 18,6%
Древесное сырьё (технологическая щепа из кругляка) – 17,6%
Электроэнергия для производства – 14,6%
Электроэнергия для линии – 7,4%
Коммерческие расходы – 18,1%
Зачасти и расходные материалы – 2,9%
Топливо для сушки – 0,4%
Общепроизводственные расходы – 6,4%
Общехозяйственные расходы (ФОТ управления, амортизация, налоги) – 6,5%
ФОТ производственных рабочих – 7,1%
Вода для производства – 0,3%
Офисные расходы – 0,1%.
Текст Владимир Крылов