Способы укрепления временных транспортных путей для трелевки и вывозки древесины
Вывозка заготовленной древесины всегда была одной из основных проблем лесозаготовительного производства в России. Не случившаяся зима 2019/2020 года в очередной раз обострила ее.
По данным Гидрометцентра России, зима 2019/20 стала самой теплой в России за 130-летнюю историю регулярных метеонаблюдений. Лишь в Магаданской области, в Камчатском крае и Чукотском АО средняя температура воздуха примерно соответствовала норме. Многие лесозаготовительные предприятия, традиционно ориентирующиеся на зимнюю вывозку заготовленной древесины, столкнулись с непреодолимыми трудностями. На Северо-Западе России некоторые стали искать для вывозки альтернативные виды транспорта, включая дирижабли и аэростаты, но до их использования дело не дошло.
Конечно, самыми дешевыми были и останутся зимние временные дороги. Но при мягкой зиме их строительство с применением стандартных технологий по стоимости и трудозатратам вполне сопоставимо со строительством временных летних дорог.
На особо влажных участках приходится делать подсыпку песчано-гравийной смесью. При наличии снега необходима стандартная для зимников процедура его укатывания на случай оттепелей. После оттепели укатанный снег покрывается ледяной коркой. Для борьбы с гололедом и обеспечения безопасности движения можно использовать подсыпку песком. Однако темный песок способствует более раннему таянию снежной дороги под действием солнечных лучей.
Обычно для организации вывозки заготовленной древесины строятся временные, со сроком эксплуатации не более года, лесовозные пути, примыкающие к ветке или магистрали лесовозной дороги и предназначенные для освоения отдельных лесосек, так называемые лесовозные усы.
Опыт показывает, что наименее затратным вариантом является одностадийная вывозка, без перегрузки с лесовоза на лесовоз у мест примыкания к магистральной лесовозной дороге. При этом необходимо строительство лесовозных усов такой конструкции, которая позволяет заезжать на погрузочный пункт тяжелым магистральным лесовозам (сортиментовозам) с прицепами. Ввиду весьма высокой стоимости таких машин, качество лесовозного уса должно обеспечивать их сохранность.
Дорожно-эксплуатационные качества уса определяются сезоном, местными грунтово-гидрологическими условиями и объемом древесины, подлежащей вывозке. Зима наиболее благоприятный период для вывозки древесины по усам, поскольку в этом случае требуется минимум дорожно-строительных работ. Выбор конструкции уса летнего действия зависит от почвенно-грунтовых условий, объема подлежащей вывозке древесины, наличия местных дорожно-строительных материалов и типа автопоезда (табл. 1).

Схема транспортного освоения лесного массива выбирается исходя из минимизации плеча вывозки заготовленной древесины. При увеличении расстояния между лесовозными дорогами уменьшается их общая протяженность, следовательно, снижается стоимость строительства дорог и их содержания. Однако при этом существенно увеличивается среднее расстояние трелевки и ее стоимость. В практике российских лесозаготовительных компаний известны примеры, когда заготовленные сортименты трелевали тяжелыми колесными форвардерами в полностью погруженном положении на расстояние 4 км и более. При этом лесозаготовители часто уверены, что хорошо сэкономили на строительстве лесовозных дорог, но забывают посчитать затраты на работу форвардера: топливо, ремонт и техническое обслуживание. Ведь форвардер конструктивно не предназначен для вывозки древесины на большие расстояния, кроме разве что форвардера Ponsse Bison. Из-за значительного увеличения среднего расстояния трелевки существенно снижается производительность форвардера, и приходится приобретать второй.
Большим достоинством усов из железобетонных плит является высокая прочность и износостойкость. Но плиты весьма дорогой материал, к тому же от завода-изготовителя их еще нужно привезти, потом разгрузить и складировать. Стоимость дорожной одежды из железобетонных плит прямо-пропорциональна расстоянию их перевозки (табл. 2). Кроме того, без подготовленного основания и правильной перевязки, дорога из бетонных плит может стать непреодолимой для автотранспорта. Большим минусом железобетонныех плит считается неремонтнопригодность.

Для лесозаготовительных предприятий древесина всегда была самым доступным конструктивным материалом, поэтому практически во всех случаях, когда на лесовозных дорогах надо укреплять проезжую часть и нет возможности использовать грунт, покрытие делается из лесоматериалов. Традиционно покрытия из древесины устраиваются в заболоченной местности с глинистыми грунтами. Известный в лесозаготовительном производстве лежневый настил часто может оказаться оптимальным, поскольку необходимая для его строительства древесина всегда под рукой. Но древесина имеет определенную стоимость, поэтому дорога с лежневым настилом фактически делается из товарной продукции (полуфабриката). Кроме того, стоимость такой дороги растет с ухудшением состояния мест прокладки.
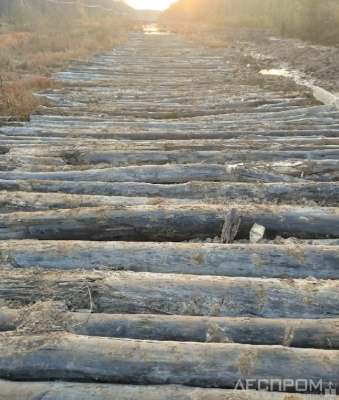
Однако древесина, уложенная в лежневую дорогу, будет безвозвратно потеряна, ее дальнейшее использование невозможно (рис. 1). А при сегодняшних ценах древесины на рынке и ее немалом расходе на километр пути такой вариант приводит к значительным финансовым потерям.
Для устройства лежневой дороги на заранее подготовленное основание раскладываются шпалы, а на них круглые лесоматериалы – плотно друг к другу в виде двух колесопроводов или в виде разреженного или сплошного настила из бревен с последующей засыпкой дренирующим грунтом.
Конструкции с колейным деревянно-лежневым покрытием применяются преимущественно на прямых участках трассы и в кривых, на которых требуется уширение не более 0,2 метра.
Колеи-колесопроводы набирают из бревен длиной 6 или 8 м. С внутренней стороны колесопроводов укладывают бревна большего диаметра. Расход деловой древесины составляет 460 800 м3/км в зависимости от почвенно-грунтовых условий.
Более просты в изготовлении сплошные лежневые покрытия, для устройства которых не нужна высокая квалификация исполнителей. Требования к качеству укладываемых в настил лесоматериалов невысокие, поэтому финансовые потери от неиспользования древесины по прямому назначению низкие. Основной недостаток сплошного лежневого покрытия – повышенный расход древесины (800–1200 м3/км) и необходимость засыпки грунтом для создания приемлемых условий движения по поперечному настилу.
В грунтово-лежневых конструкциях дорог древесина используется для основания дорожной одежды, а само покрытие отсыпается из песчано-гравийных материалов. Засыпка древесины грунтом не только обеспечивает ровную и прочную проезжую часть, но и снижает интенсивность гниения древесины.
Колейные покрытия из инвентарных деревянных щитов эффективнее лежневых ввиду возможности повторного использования. В отрасли применяли несколько щитовых конструкций, различающихся способом скрепления брусьев и соединением щитов в колесопроводе: щиты с металлическими оголовниками ЛВ-11, деревянные щиты с нагельным креплением брусьев, щиты на металлических стяжках, гибкие ленты, дорожные щиты из досок и др. По конструкции ездовой поверхности и условиям передачи нагрузки на основание из дерева выделяются два основных типа переносных покрытий: ленточные, состоящие из сравнительно коротких (по направлению оси дороги) элементов, соединенных шарнирно и образующих сплошную гибкую ленту, и щитовые, состоящие из элементов, соизмеримых по длине (по оси дороги) с базой автолесовоза. Как ленточные, так и щитовые покрытия могут быть колейными, состоящими из двух колесопроводов, и сплошными, то есть с устройством проезжей части на всю ширину дороги.
Ленточные покрытия из-за малой опорной поверхности составляющих элементов сильно давят на основание, поэтому для распределения давления на большую площадь грунтового массива в большинстве случаев требуется его подготовка. Покрытие марки ЛД-5 представляет собой два колесопровода из деревянных щитов, шарнирно соединенных в ленты. Через 20 м ленты связываются поперечным соединительным щитом для соблюдения необходимого расстояния между колесопроводами.
Сплошное покрытие ДГС-3,25 монтируется из лент длиной 4–8 м, набранных из поперечно расположенных полубрусьев толщиной около 15 см, соединенных в звене двумя металлическими стержнями (стяжками), или стальными канатами, пропущенными в просверленные отверстия. Для придания жесткости покрытие укладывается на две нитки лежней из круглых лесоматериалов.
Щитовые переносные покрытия, в отличие от ленточных, собираются из жестких в обоих направлениях элементов и тоже выполняются как в виде колейных, так и со сплошной ездовой поверхностью. Такие покрытия создают ровную проезжую часть и оказывают меньшее удельное давление на основание, чем гибкие ленточные покрытия, то есть распределяют массу движущегося по ним автолесовоза на бóльшую опорную поверхность. Наибольшее распространение из щитовых переносных покрытий в свое время получили щиты ЛВ-11 (рис. 2).
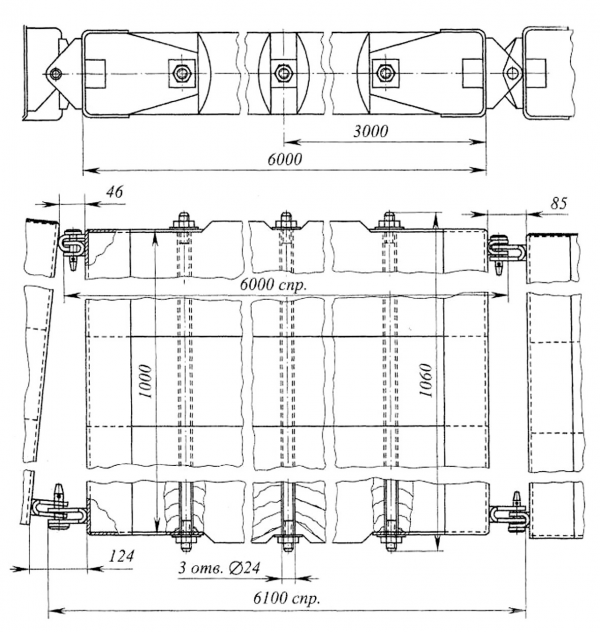
Усы с колесопроводами из щитов ЛВ-11 могут строиться на слабых почвогрунтах. При подготовке основания под щиты пни рекомендуется занижать заподлицо (спиливать или мульчировать) или выкорчевывать. Под колесопроводами недопустимы валуны, крупные корни и валеж.
Брусья для изготовления щита должны быть выполнены из бревен хвойных пород, имеющих небольшой сбег и диаметр не менее 24 см, то есть востребованных у деревопереработчиков, а потому дорогих.
Шпалы укладываются на нераскорчеванное основание или продольные лежни на расстоянии 1–1,5 м и выравнивают в горизонтальной плоскости. Чтобы предотвратить сдвиг колесопроводов на кривых, щиты укладываются в пазы в шпалах. Для укладки щитов используют краны грузоподъемностью 5–7 т с вылетом стрелы до 10 м или щитоукладчики.
Нагельные щиты изготавливаются из брусьев на специализированной линии ЛД-36-1. Поточное производство позволяло снизить затраты на него и механизировать сборку. Крепление брусьев в нагельных щитах осуществляется без использования металла, при помощи деревянных нагелей, как в деревянном кораблестроении. Но брусья щитов такой конструкции ослаблены отверстиями под нагели, поэтому требуется усиленное и тщательно выровненное основание.
Несомненным достоинством деревянных щитов для создания дорожной одежды временных дорог является значительно меньший вес, по сравнению с железобетонными плитами, а также относительная простота и низкая стоимость их производства, возможность производить их недалеко от места использования из низкотоварной древесины, которую можно предварительно модифицировать на мобильных установках для повышения стойкости к гниению.
Но у деревянных щитов есть и существенные недостатки: низкие прочность и износостойкость; часто их сколачивают на гвоздях, поскольку применение специальных клеев и систем «шип – паз» значительно удорожает конструкцию. Щиты значительно дороже лежневого настила, а возможность их повторного применения лишь гипотетическая. Как показывает практика, вдавленные тяжелыми машинами в дорогу деревянные щиты не удается вынуть из грязи, починить и использовать повторно.
Возможно изготовление необходимых для щитов пиломатериалов на верхнем складе, при помощи мобильных лесопильных станков. Но и в этом случае трудоемкость изготовления и себестоимость щитов очень высокие. Для устройства лесовозных усов используют и порубочные остатки уже освоенных лесосек. Порубочные остатки образуются при очистке деревьев от сучьев и обрезке вершин во время прокладки просеки, а затем при разработке лесосек. Для сбора лесосечных отходов задействуются подборщики сучьев и погрузчики с грейферными захватами.
Дорожно-строительные бригады непрерывно готовят хворостяную подушку и засыпают ее привозным дренирующим грунтом или песчано-гравийной смесью, профилируют и уплотняют. В сухих местах порубочные остатки засыпают местным грунтом из боковых резервов при помощи бульдозера, а в сырых и мокрых – из боковых канав экскаватором. Их уплотняют катками или гружеными самосвалами за 5–7 проходов. Расход хвороста на 1 км составляет 400–800 м3, расход дренирующего грунта – 680–2280 м3.
Для выравнивания и укрепления проезжей части на сухих местах при недренирующих грунтах широко используются усы на хворостяной выстилке из порубочных остатков. Толщина покрытия в уплотненном состоянии должна быть 0,2–0,3 м, ширина 4,0–4,5 м (рис. 3).
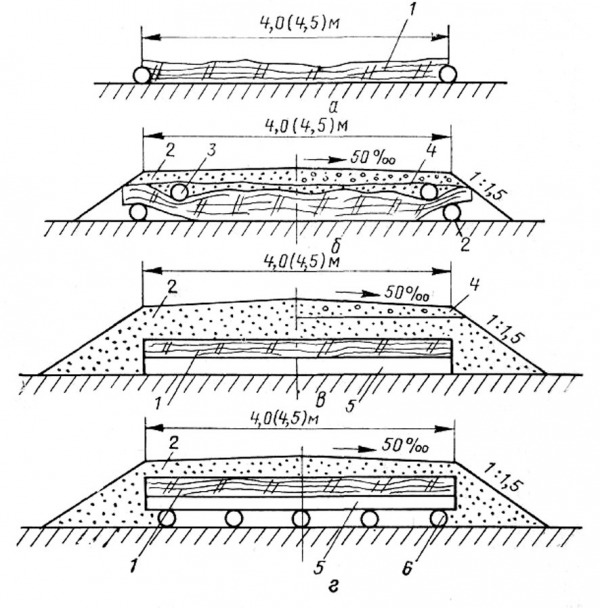
На сырых и заболоченных грунтах для повышения несущей способности устраивают хворостяную выстилку по сплошному или разряженному настилу с отсыпкой поверх хвороста слоя дренирующего грунта или гравийно-песчаной смеси толщиной 0,1–0,25 м. Средний расход древесины для устройства поперечного настила на болотах составляет 388 м3/км. Дренирующий грунт для засыпки хворостяной подушки должен обеспечивать частичное заполнение пустот между сучьями и пригрузку пружинящего слоя. Хворостяная выстилка хорошо пропускает воду и обеспечивает устойчивость отсыпанного грунта.
Еще один вариант – это грунтовые дороги с применением улучшенных дренирующих материалов: геосинтетических. При современных технологиях производства они обходятся намного дешевле. Однако никакой геотекстиль не спасет при обильных осадках. Отсыпка из инертных материалов в этом случае необходима, и, чем дальше строящаяся дорога от карьера, тем дороже она обойдется. Тогда затраты на строительство будут неоправданно высокими для временного лесовозного уса.
Весьма перспективной альтернативой рассмотренным способам строительства лесовозных усов можно считать современные дорожные маты повышенной прочности. Укладка дорожных матов позволяет обеспечить безопасный временный доступ к рабочим зонам и устойчивое дорожное покрытие как при мягком грунте, так и на твердых поверхностях. Использование современных пластиковых матов, в принципе, позволяет отказаться от перегрузки лесоматериалов при двухстадийной вывозке: по лесовозным усам лесовозами повышенной проходимости (УРАЛ, КрАЗ и др.), по магистралям – современными грузовиками (MAN, SISU и др.).
Современные пластиковые маты для устройства временных подъездных путей изготавливаются методом прессования или экструзии. Маты с шероховатой поверхностью сцепления применяются для автомобилей и колесных лесных машин, а с низкопрофильной поверхностью сцепления – для стальных гусениц и перемещения персонала.
Совместное российско-словенское предприятие ISOTRACK с большим опытом производства полимеров выпускает дорожные маты трех серий.
Серия L – облегченные маты, выдерживающие машины массой до 80 т. Площадь полезной поверхности мата 2,89 м2, а масса 36 кг – его могут переносить два работника. В стандартный высокий 40-футовый контейнер помещается 500 матов, в автотранспорт стандарта ЕС – 650 матов. Маты легко устанавливаются, имеют различные варианты соединения.
Серия Н – маты, выдерживающие машины массой до 150 т. Легко разгружаются с помощью подъемного оборудования или вилочного погрузчика. Просто устанавливаются, имеют различные варианты соединения. Масса одного мата 360 кг, площадь полезной поверхности 6,84 м2. В стандартный высокий 40-футовый контейнер помещается 50 матов, в автотранспорт стандарта ЕС – 80 матов.
Серия Х – маты повышенной прочности для устройства временных подъездных путей повышенной прочности на мягком грунте для эксплуатации при экстремально влажной погоде. Выдерживают машины свыше 200 т. Масса одного мата 295 кг, площадь полезной поверхности 7,5 м2. В стандартный высокий 40-футовый контейнер помещается 50 матов, в автотранспорт стандарта ЕС – 60 матов.
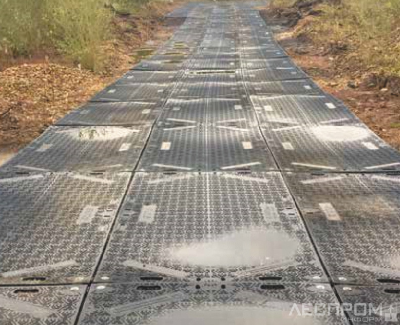
Аналогичного назначения дорожные плиты прочностью 15 МПа производит ООО «Рускомпозит». Материал плит содержит песок и переработанный пластик.
Дорожные маты легко демонтируются и переносятся на новый лесовозный ус. При правильном использовании и уходе маты обеспечивают высокие эксплуатационные показатели в течение многих лет. Все маты полностью подлежат вторичной переработке. Перед этим их чистят любым доступным способом.
Для хранения плит не требуются специальные условия и температурный режим, плиты обладают нулевым водопоглощением. Морозостойкость под ударом достигает -80 °С.
Маты слегка изгибаются в соответствии с контуром грунта, и тщательная подготовка основания не требуется (рис. 4). Кроме того, они предотвращают колееобразование, что позволяет избежать расходов на восстановление грунта. Обеспечивается безопасность движения и предотвращается застревание автотранспорта, поэтому работы не прекращаются и нет потерь рабочего времени. Материалы, применяемые при производстве матов, устойчивы к действию химических веществ и масел, защищены от воздействия УФ-лучей.
При помощи матов можно укладывать временные транспортные пути разной конструкции, колейные и сплошные (рис. 5).
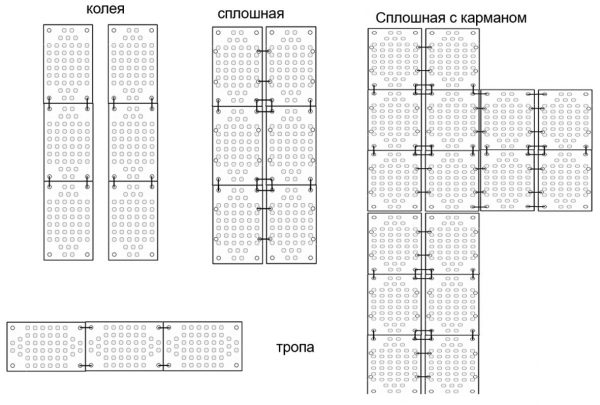
Временные транспортные пути из пластиковых матов строятся в определенной последовательности (рис. 6 и 7). Допускается укладка матов без предварительного выравнивания основания (при незначительных перепадах высоты). Выравнивание составляет от 200 до 500 мм к ширине дорожного полотна. При строительстве дороги с предварительной отсыпкой земляного полотна сначала выполняется подготовка основания земляного полотна.
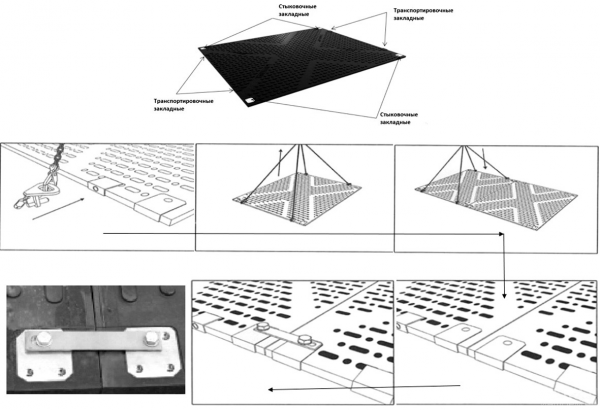

Для перевозки плит к месту строительства временной дороги можно использовать еврофуры стандарта EC80, вмещающие до 600 м2 плит формата 2500 × 3000. Перемещение вдоль строящегося пути осуществляется на любом грузовом транспорте: лесовозах, самосвалах, тралах и т. д.
Для строительства (сборки) покрытия 1 км лесовозного уса (с шириной ездовой поверхности 4,5 м), выдерживающего автолесовоз массой 40 т, потребуется 500 матов серии H 2 × 4 м. Монтаж матов на 1 км уса силами трех человек займет примерно два рабочих дня.
Маты прямоугольной формы, поэтому на кривых участках (поворотах, разворотах) их следует укладывать «лесенкой». Компания ISOTRACK прорабатывает выпуск матов другой формы, чтобы упростить укладку поворотов на кривых малого радиуса.
Гарантированный срок службы матов составляет 50 циклов (сборка-разборка).
Для укладки матов также применяются машины (рис. 8).
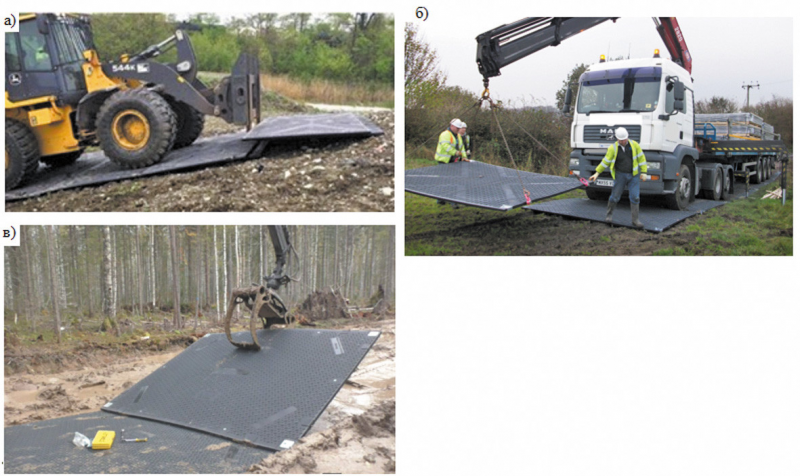
Технология создания временных транспортных путей из пластиковых матов весьма перспективна и найдет применение при освоении переувлажненных и заболоченных лесосек в теплое время года. По такому принципу можно собирать и разбирать временные покрытия на магистральном и пасечных трелевочных волоках. Это позволит в разы снизить негативные экологические последствия лесосечных работ, снизить трудоемкость лесовосстановительных мероприятий, значительно повысить эффективность работы трелевочной техники.
Текст:
Николай Тюрин, канд. техн. наук, профессор, СПбГЛТУ
Сергей Рудов, канд. техн. наук, ст. препод., ВАС им. С. М. Буденного
Ольга Куницкая, д-р техн. наук, профессор, АГАТУ
Игорь Григорьев, д-р техн. наук, профессор, АГАТУ
Максим Зорин, аспирант ВГЛТУ